冲孔落料压弯复合模设计学士学位论文Word文件下载.docx
《冲孔落料压弯复合模设计学士学位论文Word文件下载.docx》由会员分享,可在线阅读,更多相关《冲孔落料压弯复合模设计学士学位论文Word文件下载.docx(42页珍藏版)》请在冰豆网上搜索。
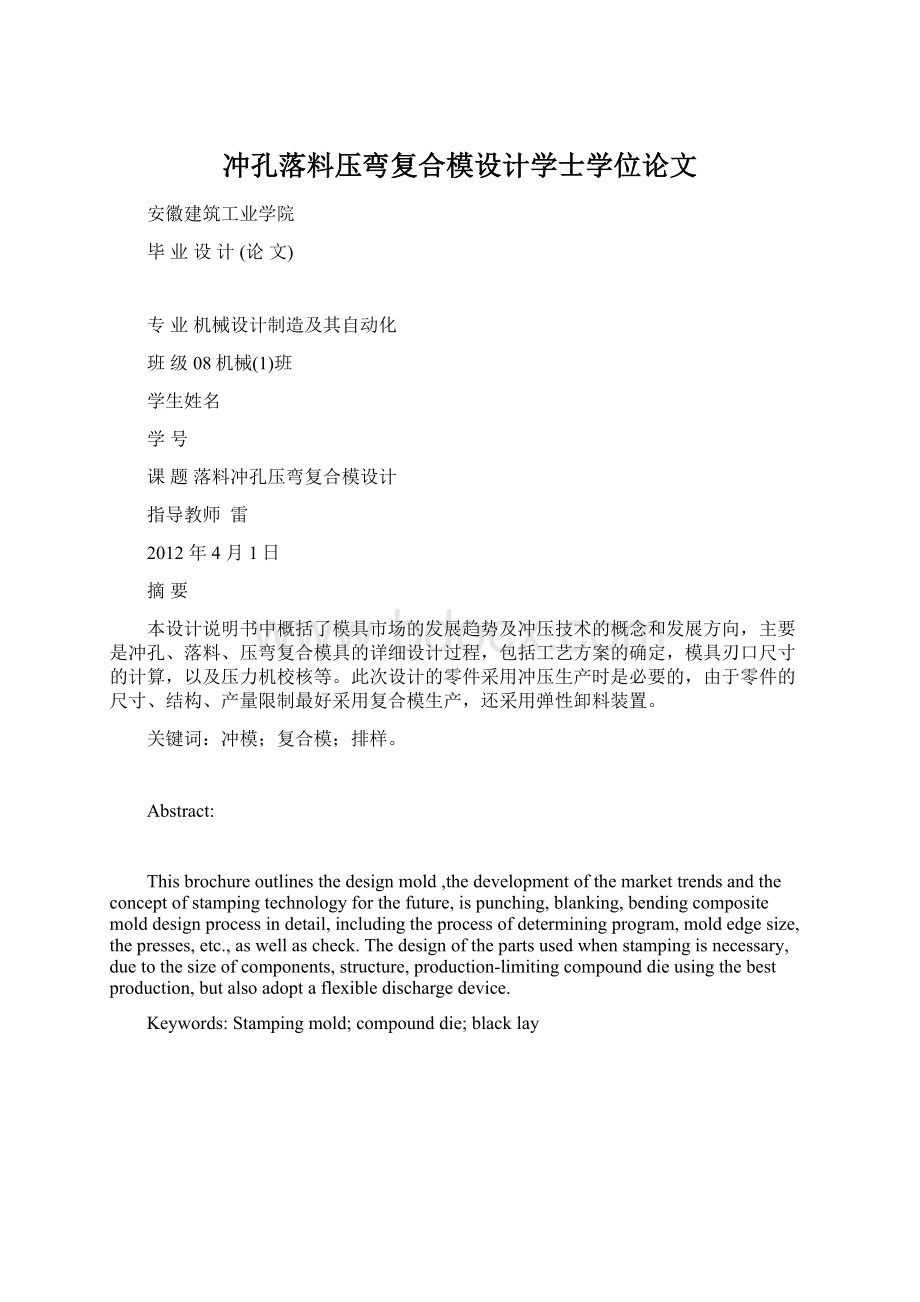
Abstract:
Thisbrochureoutlinesthedesignmold,thedevelopmentofthemarkettrendsandtheconceptofstampingtechnologyforthefuture,ispunching,blanking,bendingcompositemolddesignprocessindetail,includingtheprocessofdeterminingprogram,moldedgesize,thepresses,etc.,aswellascheck.Thedesignofthepartsusedwhenstampingisnecessary,duetothesizeofcomponents,structure,production-limitingcompounddieusingthebestproduction,butalsoadoptaflexibledischargedevice.
Keywords:
Stampingmold;
compounddie;
blacklay
第1章绪论
1.1模具在工业生产中的重要地位
模具是工业产品使用的重要工艺装备,它以其自身的特殊形状通过一定的方式使原材料成型。
现代工业生产中,由于模具的加工效率高,互换性好,节省原材料。
生产成本低。
所以得到广泛应用。
模具技术已成为衡量一个国家制造水平的重要标志之一。
模具技术能促进工业产品的发展和质量的提高,并能获得极大的经济效益。
模具是效益放大器,用模具生产的产品的价值往往是模具价值的几十倍、上百倍。
在美国模具被称为点铁成金的磁力工业,德国则认为其是所有工业中的关键工业;
日本认为模具是促进社会繁荣富裕的动力。
模具工业在我国已经成为国民经济发展的重要基础工业之一。
国民经济五大支柱产业——机械、电子、汽车、石油化工和建筑都要求模具工业的发展与之相适应,都需要大量模具,特别是汽车、电动机、电器、家电和通信等类产品中60%~80%的零部件要依靠模具成型。
1.2现代模具工业的发展方向
模具的出现可以追溯到几千年前的陶器和青铜器铸造,但其大规模使用却是随着现代工业的崛起而发展起来的。
19世纪,随着军火工业(枪炮的弹壳)、钟表工业、无线电工业的发展,冲模得到广泛使用。
第二次世界大战后,随着世界经济的飞速发展,它又成了大量生产家用电器、汽车、电子仪器、照相机、钟表等零件的最佳方式。
从世界范围看,当时美国的冲压技术走在最前列一一许多模具先进技术,如简易模具、高效率模具、高寿命模具和冲压自动化技术,大多起源于美国;
而瑞士的精冲、德国的冷挤压技术、前苏联对塑性加工的研究也处于世界先进行列。
20世纪50年代,模具行业工作重点是根据订户的要求,制作能满足产品要求的模具。
模具设计多凭经验,参考已有图纸和感性认识,对所设计模具零件的机能缺乏真实了解。
从1955年到1965年,是压力加工的探索和开发时代一对模具主要零部件的机能和受力状态进行了数学分析,对金属塑性加工工艺及原理也进行了深入探讨(如对薄板成形性能的探讨),并把这些知识不断应用于实际,使得冲压技术在各方面有了飞跃的发展。
其结果是归纳出模具设计原则,并使得压力机械、冲压材料、加工方法、模具结构、模具材料、模具制造方法、自动化装置等领域面貌一新,并向实用化的方向推进,从而使冲压加工从仅能生产优良产品的第一阶段,进入20世纪70年代向高速化、自动化、精密化、安全化发展的第二阶段。
在这个过程中不断涌现各种高效率、高寿命、高精度的多功能自动模具。
1.3模具发展趋势
一、充分运用IT技术发展模具设计、制造。
用户对压力机速度、精度、换模效率等方面不断提高的要求,促进了模具的发展。
外形车身和发动机是汽车的两个关键部件,汽车车身模具特别是大中型覆盖件模具,其技术密集,体现当代模具技术水平,是车身制造技术的重要组成部分。
车身模具设计和制造约占汽车开发周期三之二的时间、成为汽车换型的主要制约因素。
目前,世界上汽车的改型换代—般约需
48个月,而美国仅需30个月,这车要得益于在模具业中应用了CAD/CAE/CAM技术和三维实体汽年覆盖件模具结构设计软件。
另外,网络技术的广泛应用提供了可靠的信息载体、实现了异地设计和异地制造。
同时,虚拟制造等IT技术的应用,也将推动模具工业的发展。
二、缩短金属成形模具的试模时间。
当前,主要发展液压高速试验压力机和拉伸机械压力机,特别是在机械压力机上的模具试验时间可减少80%、具有巨大的节省潜力。
这种试模机械压力机的发展趋势是采用多连杆拉伸压力机,它配备数控液压拉伸垫,具有参数设置和状态记忆功能。
三、车身制造中的级进冲模发展迅速。
在自动冲床上用级进冲裁模或组合冲模加工转子、定子板,或者应用于插接件作业,都是众所周知的冲压技术,近些年来,级进组合冲裁模在车身制造中开始得到越来越广泛的应用,用级进模直接把卷材加工为成型零件和拉伸件。
加工的零件也越来越大,省去了用多工位压力机和成套模具生产所必需串接的板材剪切、涂油、板坯运输等后续工序。
级进组合冲模已在美国汽车工业中普遍应用,其优点是生产率高,模具成本低,不需要板料剪切,与多工位压力机上使用的阶梯模相比,节约30%。
但是级进组合冲模技术的应用受拉伸深度、导向和传输的带材边缘材料表面硬化的限制,主要用于拉伸深度比较浅的简单零件,因此不能完全替代多工位压力机,绝大多数零件应优生考虑在多工位压力机上加工。
第2章弯曲变形过程及变形特点
2.1弯曲变形的过程及变形特点
2.1.1弯曲变形过程
弯曲变形过程:
如图1-1所示V形件的弯曲,随着凸模进
入凹模深度的增大,凹模与板料的接触处位置发生变化,支点
B沿凹模斜面不断下移,弯曲力臂l逐渐减小,接近行程终了,
弯曲半径r继续减小,而直边部分反而向凹模方向变形,直至板
料与凸、凹模完全贴合。
1-2板料弯曲变形特点
通过网格试验观察弯曲变形特点(如图1-1)。
图2-1v型零件弯曲变形过程
图2-2弯曲前后坐标网络的变化
1.弯曲圆角部分是弯曲变形的主要变形区
变形区的材料外侧伸长,内侧缩短,中性层长度不变。
2.弯曲变形区存在应变中性层
应变中型层是指在变形前后金属纤维的长度没有发生改
变的那一层金属纤维。
3.变形区材料厚度变薄的现象
变形程度愈大,变薄现象愈严重。
4.变形区横断面的变形
变形区横断面形状尺寸发生改变称为畸变。
主要影响因
素为板料的相对宽度。
t/b>
3(宽板)横断面几乎不变;
t/b<
3(窄板)断面变成了内宽外窄的扇形。
2.2弯曲变形区的应力和应变
板料在塑性弯曲时,变形区内的应力应变状态取决于弯曲毛坯的想对宽度以及弯曲变形程度。
窄板弯曲的应力状态是平面的,应变状态是立体的。
宽板弯曲的应力状态是立体的,应变状态是平面的。
图2-3弯曲应力
第3章工艺及方案分析
3.1工艺分析
冲裁件的工艺性是指冲裁件对冲裁工艺的适应性。
因此,冲裁件的结构形状、尺寸大小、精度等级、材料及厚度等是否符合冲裁的工艺要求,对冲裁件质量、模具寿命和生产率有很大影响。
冲裁件应满足如下要求:
(1)冲裁件形状
冲裁件的形状应力求简单、对称,有利于材料的合理利用。
(2)冲裁件内形及外形的转角
冲裁件内形及外形的转角处要尽量避免尖角,应以圆弧过渡,以便于模具加工,减少热处理开裂,减少冲裁时尖角处的崩刃和过快磨损。
圆角半径R的最小值,参照表3-1选取。
表3-1冲裁件最小圆角半径R(t—料厚)
冲裁件类型
黄铜、铝
合金钢
软钢
备注
落料
α
≥90°
0.18t
0.35t
0.25t
≥0.25mm
﹤90°
0.70t
0.50t
≥0.50mm
冲孔
0.20t
0.45t
0.30t
≥0.30mm
0.40t
0.90t
0.60t
≥0.60mm
(3)冲裁件上凸出的悬臂和凹槽
尽量避免冲裁件上的凸出悬臂和凹槽,悬臂和凹槽宽度也不宜过小。
(4)冲裁件的最小孔径
冲件孔径太小时,凸模容易折断。
冲孔的最小尺寸取决于材料的机械性能、孔的形状及模具结构。
如果对冲头采用导向套保护,则可以提高冲头的稳定性,最小冲孔尺寸还可以减小,见表3-2。
表3-2冲裁件最小孔径
材料种类
冲头无保护套
冲头有保护套
圆孔直径
矩形孔最小边长
硬钢
≥(1.3-1.5)t
≥(1.2-1.35)t
0.5t
0.4t
软钢及黄铜
≥(0.9-1.0)t
≥(0.8-0.9)t
0.3t
铝、布胶板、纸胶
0.8t
0.7t
0.28t
(5)孔边距与孔间距
为避免工件变形和保证模具强度,孔边距和孔间距不能过小否则会产生孔间材料扭曲,或者使边缘变形。
一般不小于1.5t。
图3.1
此汽车钣金件为汽车连接定位零件,生产批量较大,采用厚2mm的碳素钢Q235A钢板制成,其外形图如图3.1所示。
用一副磨具同时完成落料冲孔压弯三道工序。
该冲压件为冲孔、落料、弯曲的复合件,形状较为简单且对称,尺寸精度要求不高,材料Q235A冲压性
能较好,零件弯曲直边为18mm(计算:
20-r=20-3=18),大于资料要求的2t=2x2mm=4mm,故弯曲工艺性较好;
而各孔与零件外形边缘的距离均大于复合模中凸凹模的最小壁厚4.9mm要求,因此,冲孔及落料复合时,凸凹模的强度足够。
加之零件弯曲直边有18mm,在模具上设置活动凸模结构也较易实现。
综合上述分析,可选用冲孔、落料、弯曲复合模。
有以下两种不同的工艺方案:
(1)先落料,然后冲孔和弯曲在同一工步。
(2)落料、冲孔为同一工步首先完成,然后进行弯曲。
采用方案
(1)加工工件,不易保证长度尺寸的精度要求,而且易使内孔冲头磨磨降低模具寿命。
经分析、比较,确定采用方案
(2),即设计一套冲孔—落料—弯曲复合模,该模具划分两个工步完成上述三道工序,在压力机上一次性实现零件的加工成形。
3.2工艺方案的确定
3.2.1方案的拟定及分析比较
1)先落料,再钻孔,后钳工压弯,只需1副落料模、2副夹具可以完成,其优点是模具简单,易制造,冲床占用少,但零件2孔的孔径大小与位置要求难以保证,且生产效率低,只适合小批量试制。
2)先落料,后冲孔,最后压弯,用3副简单模完成,其优点是模具简单,易制造,冲件质量好,但冲床占用相对较多,生产工序多,生产效率低,不适合大批量生产。
3)落料、冲孔、压弯一次成形完成,采用1副复合模完成,其优点是冲件质量好,冲床占用少,生产效率高,只是模具相对复杂,适合冲件的大