过程控制系统与装置综合实训Word格式.doc
《过程控制系统与装置综合实训Word格式.doc》由会员分享,可在线阅读,更多相关《过程控制系统与装置综合实训Word格式.doc(20页珍藏版)》请在冰豆网上搜索。
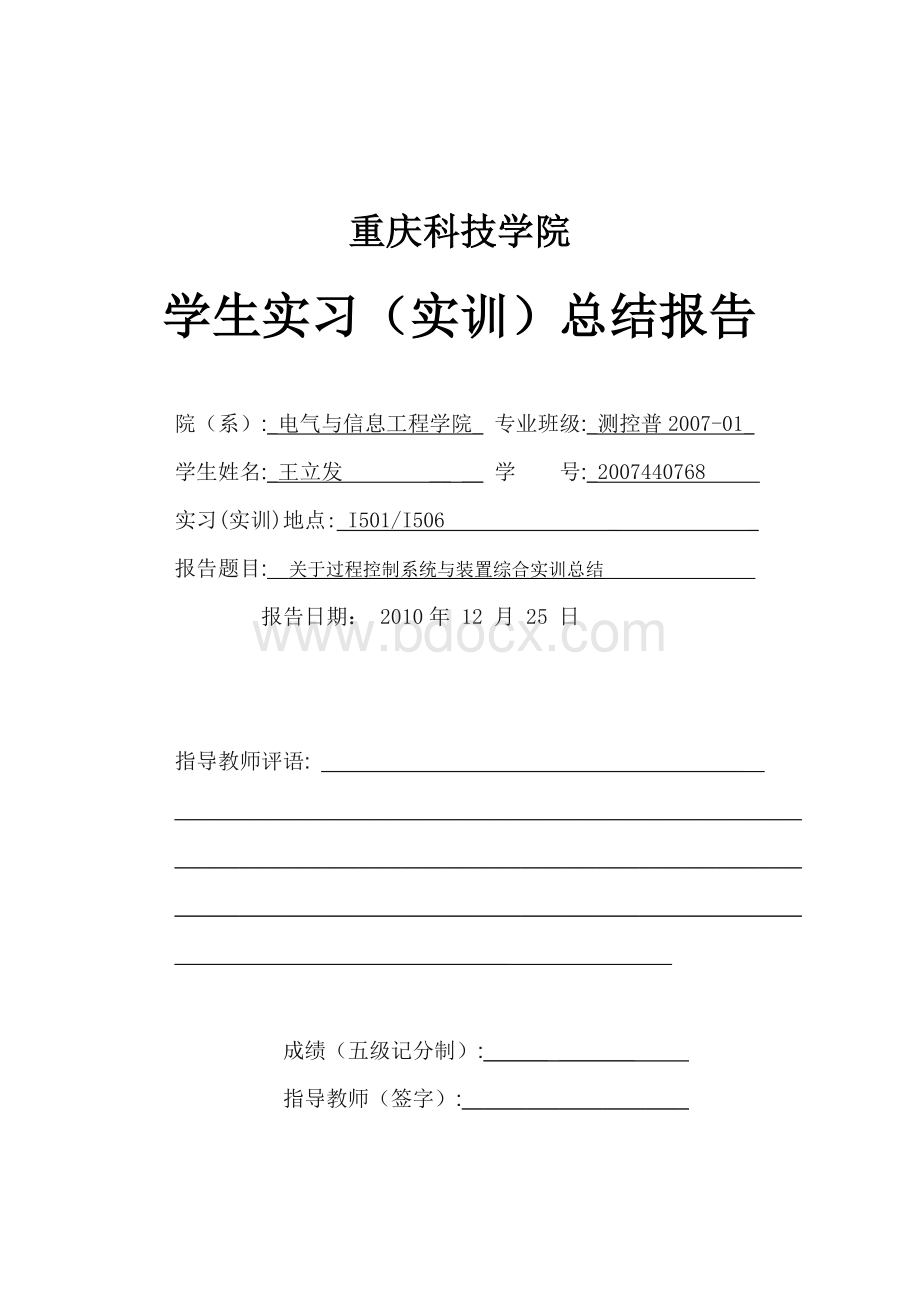
指导教师(签字):
_____________________
目录
1实验任务书 1
2温度单回路控制系统 2
2.1温度单回路控制系统 2
2.2温度检测设备 2
2.3执行机构 3
2.4智能仪表 3
3复杂控制系统的组成 4
3.1液位-流量的串级控制系统 4
3.11液位-流量的串级控制系统原理 4
3.12液位-流量的串级控制系统试验结果 5
3.2下水箱液位的前馈-反馈控制系统 6
3.21下水箱液位的前馈-反馈控制系统试验原理 7
3.22下水箱液位的前馈-反馈控制系统试验结果 8
3.3单闭环流量比值控制系统 9
3.31单闭环流量比值控制系统试验原理 9
3.32单闭环流量比值控制系统试验结果 11
4对象传递函数测试 11
4.1单容水箱特性的测试 11
4.11单容水箱特性的测试试验原理 12
4.12单容水箱特性的测试试验结果 12
4.2双容水箱特性的测试 14
4.21双容水箱特性的测试试验原理 14
4.22双容水箱特性的测试测试结果 15
5心得体会 16
I
1实验任务书
报告题目:
关于过程控制系统与装置综合实训总结
学生姓名
王立发
课程名称
过程控制系统综合实训
专业班级
测控普2007
地点
I501/I506
起止时间
10.12.13~10.12.24
设计内容及要求
过程控制系统与装置综合实训内容有4类。
内容及要求如下:
1.用protel绘制实验平台的电气接线图,对每个部分的I/O端子进行标注。
2.对象传递函数测试
(1)单容水箱特性的测试
(2)双容水箱特性的测试
3.复杂控制系统的组成,干扰源的加入,参数整定。
(1)液位-流量的串级控制系统
(2)单闭环流量比值控制系统
(3)下水箱液位的前馈-反馈控制系统
4.典型过程控制系统的投运、关闭操作
(1)间歇反应过程
(2)连续反应过程
(3)热交换过程
进度
要求
第1天:
讲解任务;
第2天:
温度单回路控制系统电气连接原理图;
第3天:
串级控制系统;
第4天:
前馈控制系统;
第5天:
比值控制系统;
第6天:
单容双容水箱模型建立;
第7天:
间接反应的过程与操作;
第8天:
连续反应过的;
第9天:
热交换系统的的过程投运与交换;
第10天:
撰写设计报告.
教研室主任:
指导教师:
唐德东、彭宇兴
2010年12月13日
17
2温度单回路控制系统
2.1温度单回路控制系统
温度单回路控制系统由温度传感器、智能仪表(AS3010)、调压模块、三项加热炉、PC机组成。
温度传感器将温度信号转换成4~20mADC电流信号。
传给智能仪表,智能仪表经过运算后,送出控制信号控制调压模块,改变加热器的电压。
其系统框图如图2.10所示。
系统的电气接线图如图2.11所示。
智能仪表
调压模块
加热器
PC机
温度传感器
+
-
给定值
T温度
锅炉
图2.10系统框图
图2.11系统电气接线图
2.2温度检测设备
温度传感器为PT100,Pt100传感器精度高,热补偿性较好。
如图2.2所示。
图2.2温度传感器为PT100
温度变送器为两线制,24V直流供电。
经过调节器的温度变送器,可将温度信号转换成4~20mADC电流信号。
2.3执行机构
1)调压模块
调压模块是根据控制信号来控制加热器的电压。
电流控制信号为4-20mA,调压器到加热管采用380V三相交流供电。
如图2.3所示。
图2.3调压模块
如果采用电压控制,则从2号端子的CON端输入2-10V。
如果采用电流控制则从3号端子输入4-20mA。
调压器到加热管采用380V三相交流供电。
2.4智能仪表
智能仪表是整个系统的重要部分,它是控制中心,它将测量信号运算后,得出控制信号并传给控制器。
仪表的测量信号为传感器的输出信号,此处经过电阻将电流信号转换成1—5V(0.2—1V)的电压信号,即AI0+、AI0-为1—5V信号输入;
AI1+、AI1-为0.2—1V信号输入。
AO0+(AO1+)、AO0-(AO1-)为仪表的控制信号输出端,4—20mA的电流控制执行器的输出。
如图2.4所示。
仪表外给定是通过外部输入的1—5V电压信号来设定仪表设定值的。
其它报警等端子为扩展备用。
图2.4智能仪表
3复杂控制系统的组成
3.1液位-流量的串级控制系统
液位-流量的串级控制系统采用了液位变送器、流量变送器、电动调节器、智能仪表。
其实验线路按照图3.10接好。
将下水箱液位变送器的输出端接到智能仪表一的模拟输入端,智能仪表一的模拟输出端接智能仪表二的外给定端,流量变速器的输出端接到智能仪表二的输入端,智能仪表二的模拟输出端接到电动调节阀。
下水箱液位变送器将测的信号传送给智能仪表一,智能仪表一经过运算后,输出调节信号作为智能仪表二的给定值,智能仪表二将流量值和给定值结合运算后,输出控制信号传给调节阀。
控制电动调节阀开度,控制下水箱的进水量,达到或保持给定的液位。
智能仪表通过RS485与PC机通信,将液位值和调节阀的开度传送给PC机,PC机实时显示数据。
操作人员可以在PC机上实时修改各个参数。
3.11液位-流量的串级控制系统原理
本实验系统的主控量为下水箱的液位高度H,副控量为电动调节阀支路流量Q,它是一个辅助的控制变量。
系统由主、副两个回路所组成。
主回路是一个恒值控制系统,使系统的主控制量H等于给定值;
副回路是一个随动系统,要求副回路的输出能正确、快速地复现主调节器输出的变化规律,以达到对主控制量H的控制目的。
图3.10液位-流量串级控制系统的结构图
不难看出,由于主对象下水箱的时间常数较大于副对象管道的时间常数,因而当主扰动(二次扰动)作用于副回路时,在主对象未受到影响前,通过副回路的快速调节作用已消除了扰动的影响。
图3.10为实验系统的结构图,图3.11为该控制系统的方框图。
图3.11液位-流量串级控制系统的方框图
3.12液位-流量的串级控制系统试验结果
液位-流量的串级控制系统的参数整定方法有逐步逼近法、两步整定法和一步整定法。
本实验采用的是两步整定法。
在工况稳定,主、副控制器都在纯比例作用运行的条件下,将主控制器的比例度先固定在100%的刻度上,逐渐减小副控制器的比例度,求取副回路在满足某种衰减比(如4∶1)过渡过程下的副控制器比例度和操作周期,分别用δ2s和T2s表示。
在副控制器比例度等于δ2s的条件下,逐步减小主控制器的比例度,直至得到同样衰减比下的过渡过程,记下此时主控制器的比例度δ1s和操作周期T1s。
按查表所得的PI参数对主调节器的参数进行整定。
副回路PID参数比例带为10.0%,积分时间为999S,微分时间为0S,副回路调节好后,不改变参数。
调节主回路,经调节后主回路PID参数的比例带为10.0%,积分时间为50S,微分时间为0.0S。
对进入副回路的干扰有很强的克服能力;
改善了被控过程的动态特性,提高了系统的工作频率;
对进入主回路的干扰控制效果也有改善;
对负荷或操作条件的变化有一定自适应能力。
图3.120串级控制系统图
图3.121串级控制系统图
3.2下水箱液位的前馈-反馈控制系统
下水箱液位的前馈-反馈控制系统主要用了液位变送器、流量变送器、电动调节阀、智能仪表。
其实验线路按照图3.20接好。
将流量变送器一的输出端接到智能仪表一的模拟输入端,流量变速器二的输出端接到智能仪表二的输入端,智能仪表二的模拟输出端接到电动调节阀。
流量变送器一将测的信号传送给智能仪表一,智能仪表二将流量变送器一的值按比值运算后,输出控制信号传给调节阀。
控制电动调节阀开度,控制进水流量,达到或保持给定的流量。
3.21下水箱液位的前馈-反馈控制系统试验原理
图3.20前馈-反馈控制系统的结构图
反馈控制是按照被控参数与给定值之差进行控制的。
它的特点是,调节器必须在被控参数出现偏差后才能对它进行调节,补偿干扰对被控参数的影响。
基于过程控制系统总具有滞后特性,因而从干扰的产生到被控参数的变化,需要一定长的时间后,才能使调节器产生对它进行调节作用,从而对干扰产生的影响得不到及时地抑止。
为了解决这个问题,提出一种与反馈控制在原理上完全不同的控制方法。
由于这种方法是一种开环控制,因而它只对干扰进行及时地补偿,而不会影响控制系统的动态品质。
即当扰动一产生,补偿器立即根据扰动的性质和大小,改变执行器的输入信号,从而消除干扰对被控量的影响。
由于这种控制是在扰动发生的瞬时,而不是在被控制量产生变化后进行的,故称其为前馈控制。
前馈-反馈控制系统中的主要扰动由前馈部分进行补偿,这种扰动能测定,其它所有扰动对被控制量所产生的影响均由负反馈系统来消除。
这样就能使系统的动态误差大大减小。
图3.20为本实验的系统结构图,被控制量是下水箱的液位,扰动为流量F。
图3.21为该控制系统的方框图。
图3.21控制系统的方框图
图中GC(S)-调节器 G0(S)-电动调节阀、中水箱与下水箱
Gf(S)-干扰通道的传递函数 GB(S)-前馈补偿器H(S)-液位变送器
由图3.21可知,扰动F(S)得到全补偿的条件为
F(S)Gf(S)+F(S)GB(S)G0(S)=0
GB(S)=-(3.21)
上式给出的条件由于受到物理实现条件的限制,显然只能近似地得到满足,即前馈控制不能全部消除扰动对被控制量的影响,但如果它能去掉扰动对被控制量的大部分影响,则认为前馈控制已起到了应有的作用。
为使补偿器简单起见,GB(S)用比例器(KB)来实现,则:
由式(13)可知,
KB=(3.22)
式中Kf-干扰通道的静态放大倍数
K0-控制通道的静态放大倍数
3.22下水箱液位的前馈-反馈控制系统试验结果
下水箱液位的前馈-反馈控制系统经过调节后,其PID参数的比例带为5