未来坦克弹药装填系统共12页文档Word文档格式.docx
《未来坦克弹药装填系统共12页文档Word文档格式.docx》由会员分享,可在线阅读,更多相关《未来坦克弹药装填系统共12页文档Word文档格式.docx(6页珍藏版)》请在冰豆网上搜索。
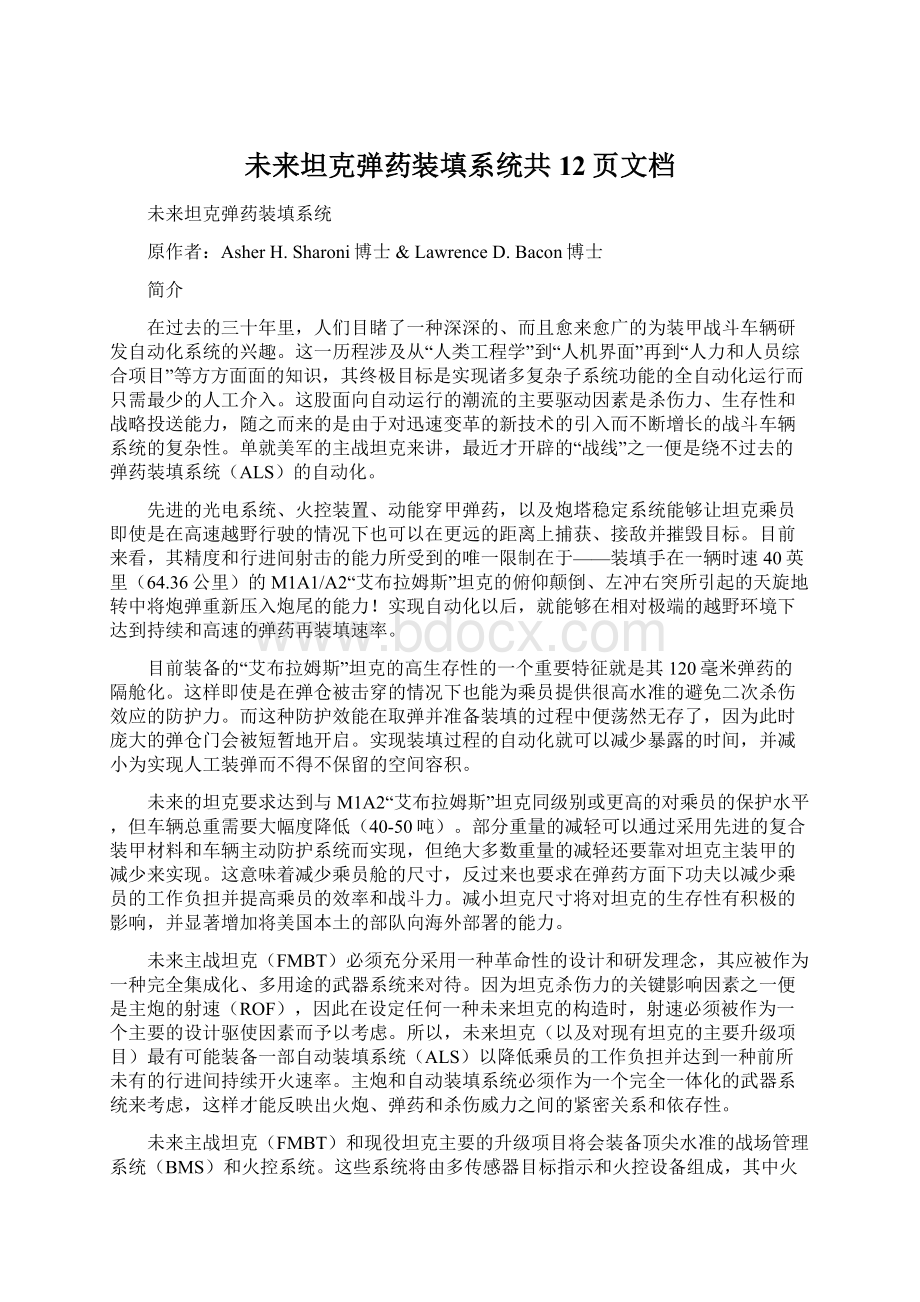
先进的光电系统、火控装置、动能穿甲弹药,以及炮塔稳定系统能够让坦克乘员即使是在高速越野行驶的情况下也可以在更远的距离上捕获、接敌并摧毁目标。
目前来看,其精度和行进间射击的能力所受到的唯一限制在于——装填手在一辆时速40英里(64.36公里)的M1A1/A2“艾布拉姆斯”坦克的俯仰颠倒、左冲右突所引起的天旋地转中将炮弹重新压入炮尾的能力!
实现自动化以后,就能够在相对极端的越野环境下达到持续和高速的弹药再装填速率。
目前装备的“艾布拉姆斯”坦克的高生存性的一个重要特征就是其120毫米弹药的隔舱化。
这样即使是在弹仓被击穿的情况下也能为乘员提供很高水准的避免二次杀伤效应的防护力。
而这种防护效能在取弹并准备装填的过程中便荡然无存了,因为此时庞大的弹仓门会被短暂地开启。
实现装填过程的自动化就可以减少暴露的时间,并减小为实现人工装弹而不得不保留的空间容积。
未来的坦克要求达到与M1A2“艾布拉姆斯”坦克同级别或更高的对乘员的保护水平,但车辆总重需要大幅度降低(40-50吨)。
部分重量的减轻可以通过采用先进的复合装甲材料和车辆主动防护系统而实现,但绝大多数重量的减轻还要靠对坦克主装甲的减少来实现。
这意味着减少乘员舱的尺寸,反过来也要求在弹药方面下功夫以减少乘员的工作负担并提高乘员的效率和战斗力。
减小坦克尺寸将对坦克的生存性有积极的影响,并显著增加将美国本土的部队向海外部署的能力。
未来主战坦克(FMBT)必须充分采用一种革命性的设计和研发理念,其应被作为一种完全集成化、多用途的武器系统来对待。
因为坦克杀伤力的关键影响因素之一便是主炮的射速(ROF),因此在设定任何一种未来坦克的构造时,射速必须被作为一个主要的设计驱使因素而予以考虑。
所以,未来坦克(以及对现有坦克的主要升级项目)最有可能装备一部自动装填系统(ALS)以降低乘员的工作负担并达到一种前所未有的行进间持续开火速率。
主炮和自动装填系统必须作为一个完全一体化的武器系统来考虑,这样才能反映出火炮、弹药和杀伤威力之间的紧密关系和依存性。
未来主战坦克(FMBT)和现役坦克主要的升级项目将会装备顶尖水准的战场管理系统(BMS)和火控系统。
这些系统将由多传感器目标指示和火控设备组成,其中火控设备将装有空中/地面目标自动捕获装置,该装置通过热成像仪和/或毫米波雷达实现对目标的搜索及跟踪。
战场管理系统(BMS)将为坦克的昼/夜间一体化军械系统提供自动与多目标交战的能力,并带有“无人工介入”的全自动选项。
必须配备高速自动装弹机以充分利用现代战场管理系统和颇具杀伤威力的“行进间射击”的能力。
自动化减轻了乘员的工作负担,并使得考虑采用新的坦克构造及更少的坦克乘员成为可能。
在采用自动装填系统的基础上,可以考虑开发无人炮塔,这也使得减少四人乘员组变得顺理成章。
它将大大提高坦克在各种环境下的射速,为坦克提供迅速与多目标接战的能力,并最终有助于坦克整体生存性能的提高。
无人炮塔可以显著地减少其体积和质量,使坦克更轻、正面投影面积更小。
如果传统的有人炮塔布局在未来仍然得以保留,或者在现有的坦克炮塔上加装了自动装填系统,那么坦克车组的第四名乘员的职能将会扩展到数据管理和目标捕获方面,或者干脆取消第四名成员。
举例来讲,如果在M1A2坦克上引入战场管理系统的话,那么需要一位“全职”的数据管理员才能使其良好地运作。
在确定车组乘员的人数方面,坦克的维护保养、周界安全和24小时连续不断的战场部署是另外需要考虑的问题。
(三人车组与四人车组的比较是一个涉及军事条令方面的问题,不应该只作工程技术方面的考虑。
)
尽管杀伤威力是坦克设计的根本性考虑要素之一,但对一款未来的主战坦克而言,任何开始着手的理性设计路线都应当含有对军械系统的选择,包括主炮和自动装填系统(ALS),继之以对常规或无人炮塔的选择,最终结果是有关坦克杀伤威力的其余方面要围绕着高度集成化的武器系统来构建。
本文的意图是探讨自动装填系统(ALS)的不同设计方案,并勾勒出它们对坦克整体性能参数的可能影响及其作战效能。
我们的评论将基于我们在过去16年里所参与的多个美军弹药装填系统研发工程中所积累的设计经验,而且凭借我们的专业知识经验,本文笔者在有关欧洲、美国及苏联的主战坦克设计研究方面多有建树。
通过对不同设计路线的探讨,我们将为读者提供一份有关之前不同的自动装填系统(ALS)设计经验及美军实施过的相关研究计划的简要概述。
通用动力公司坦克测试平台演示车
1983年,美国陆军坦克及机动车辆司令部(TACOM)签署了一份合同,要求设计、制造并演示一款“实验性的”120毫米自动装弹机输弹机构。
该设备被要求能够循环地从指定的储弹位置提取炮弹并输弹至模拟的炮尾,然后归位。
速率为12发/分钟,同时在完成每轮20次的重复装填动作后不能在较脆的可燃药筒上留下肉眼可见的痕迹。
在对这一“原理论证”的设备进行成功的演示后,TACOM又签订了一份后续合同,要求设计、建造并在坦克测试平台炮塔上测试全尺寸的自动装弹机。
正如图1至图3所展示的那样(展示了自动装弹机的主要部件,特别是输弹机构),坦克测试平台(TTB)自动装弹机是一款引人注目的成功设计。
该系统由一个位于无人炮塔吊篮内的弹容量44发的旋转式机械弹仓、一部位于炮塔尾舱内M256型120毫米加农炮尾的全铰接的输弹机构(包括一根推弹杆)、以及一台以微处理器为基础的电子控制单元(ECU)所构成。
该系统由电-液压驱动,可由现有的炮塔电力设备供电,并为迄今为止仍少有建树的自动装填系统(ALS)研究领域奠定了新的性能基准。
坦克测试平台(TTB)自动装弹机成功地展现出了全部所要求的设计功能,这些功能都是一款“通用的”主战坦克自动装弹机所要求具有的有代表性的指标:
●实现M256加农炮开火后的迅速再装填,最高速率12发/分钟。
●通过炮塔后方的小型开口实现发射后药筒的自动抛出。
●哑弹的排出。
●遇停止射击及更改开火命令的情况下在旋转弹仓上对未发射弹药的归位及优化调整(按一定目次)。
●操作过程的“软复位”模式,即允许车组乘员方便安全地通过炮塔后方的抛壳开口从车外武器站向车内补充弹药。
●“上传”模式,同样是通过炮塔后方进行,速率为6到8发/分钟。
图1:
坦克测试平台(TTB)自动装弹机系统概观及主要部件。
控制系统能够发挥存弹管理功能,这使得自动装弹机能够迅速移动到位置最接近的一发可用的、符合预先选定弹种的炮弹上,同时最大限度地减少重心偏移的距离及对电力消耗的大幅度波动。
该系统的动作机构实现了完全的冗余设计,以确保即使是在动作机构的某一“点”发生故障的情况下,自动装弹机也能够以较低的装填速率实现持续不断地运行。
这一额外的可靠性特点证明采用远距离遥控操纵的武器系统是可行的,这也使得考虑采用三人制车组乘员成为可能。
系统循环测试一共进行了超过66000次以上的整装弹药装填,结果极为成功。
测试包括在坦克及机动车辆司令部(TACOM)的车辆运动模拟器上完成的长时期的演示,在演示期内弹药不断地进行装填循环,同时武器站也在进行实时的“振动”以模拟真实的行进间射击状况,正如图4所示。
坦克测试平台系统由两个主要的机械子系统组成:
(1)位于炮塔座圈下方的旋转式弹仓,存放有44枚弹药;
(2)输弹机构总成,可提供装弹、退弹、准备射击、补充弹药、弹药卸载、以及迅速处置发射过后的药筒及哑弹等所要求的一切功能。
图2:
位于装填位置的坦克测试平台(TTB)120毫米自动装弹机输弹机构。
图3:
自动装弹机输弹机构。
自动装弹机被设计成能够在长时间维持10发/分钟的射速下正常工作(最高射速12发/分钟),并且其空重应低于1400磅(约635千克)。
贮存在弹仓中的44发弹药分别受到单独的保护、支持,并通过可容纳射弹全长的包装罐(能够将炮弹整个地支持包绕起来)使弹药
相互分离。
弹仓的设计要求预留能够在需要的情况下将弹容量扩大到48发的潜力,且高达60发的补充弹容量也是可行的。
图4:
坦克及机动车辆司令部(TACOM)车辆运动模拟器上的坦克测试平台炮塔。
电力的消耗可以忽略不计,受此限制需要车长手动操纵伺服阀门及低功耗传感器。
该系统的独特之处在于其“无弹簧”设计,即其并不依赖其他任何种类的自动装弹机运行时所需要的弹簧承载部件。
输弹机构的特征是一部液压驱动的推弹杆系统,该系统的设计限制推力载荷(药筒)最大为110磅(约49.896千克,加速度大小约为2g,包括重力),设计限制压力负荷最大为220磅(约99.792千克,加速度大小约为4g)。
发射后的药筒和哑弹以大约11英尺/秒(约为3.35米/秒)的速度抛出车外。
抛壳窗位于炮塔尾部,水平抛出,抛壳窗与弹药补充门共用一处开口。
FASTDRAW机械化弹仓
1980年代中期,美国陆军考虑为M1A1主战坦克引入一款备选的弹药装卸系统,该系统耦合有一种机械化旋转式弹仓,如图6和图7所示。
该系统为美国陆军与通用动力公司共同研发,FASTDRAW是一款高度轻量化、坚固耐用、可靠的系统,与“传统的”固定架类型的弹药储存系统相比,该系统拥有许多重要的优势。
该系统弹容量36发,存放在两部一模一样的弹仓中,专为装备120毫米火炮的M1系列坦克而设计,但也可以通过修改尺寸减少弹容量而应用在轻型车辆上,或采用口径更小的弹药(105毫米)。
FASTDRAW方案在坦克弹药贮存方面最重要和直接的特征是:
●明显降低了防爆门的复杂性,也降低了对密封性的要求,结果是提高了车组乘员的安全性和生存性。
●用一堵固体装甲隔板墙隔开的两处完全分立的弹药室,这使得车辆的生存性有所提高,且在一处弹药室被击穿的情况下仍具有战斗力。
●自动将预选的弹种与装弹机“适配”,而不再需要装弹机在弹药架上寻找所需要的弹种。
●降低了炮塔尾舱的结构重量和复杂性。
就M1A1坦克而言,可减重350磅(约158.76千克)。
●迅速获取所贮存的所有弹药,不需要“拆开”弹药架以获取位于尾舱角落里的弹药。
●完全避免了两处弹药室互相殉爆的保护措施。
图5:
所示为未来主战坦克的机器人化弹药装填系统(RALS)和备用弹仓。
FASTDRAW应该会采用电动或液压驱动的方式,通过一种简洁、精确的十字轮驱动机构工作。
由于采用了蜂窝状的结构总成,即弹药架炮弹包装罐之间相互支持并导致了结构的紧凑,这使得FASTDRAW的重量颇具优势,且取消了设置厚重的前后结构支撑板的需要。
FASTDRAW方案还提供了内置的增长期权这一固有优势,或者说是预先计划的产品改进。
旋转弹仓具备将弹药旋转至某一单独的抽提位置的功能,这使得其更有希望用一部机器人式的弹药输送装置取代车组的第四名乘员。
这一输弹装置的工作方式与坦克测试平台(TTB)上的对应设备基本一致,唯一的不同之处是在炮塔两侧各增加了一部动作机构,以便将输弹装置从弹仓提弹的水平位转换至与坦克主炮炮管和炮尾完全对准的装填位。
图6:
FASTDRAW弹仓的组成。
图7:
在M1A1主战坦克上应用FASTDRAW方案的概念图。
第三批次的坦克自动装弹机
由食品机械化学公司(FMC)和通用动力公司地面系统分部组成的联合探索小组AVTA被授予了一份对下一代主战坦克进行设计、发展、原型车制造和测试的合同,下一代主战坦克安装有140