江苏省高速公路水泥稳定碎石基层Word文档格式.docx
《江苏省高速公路水泥稳定碎石基层Word文档格式.docx》由会员分享,可在线阅读,更多相关《江苏省高速公路水泥稳定碎石基层Word文档格式.docx(11页珍藏版)》请在冰豆网上搜索。
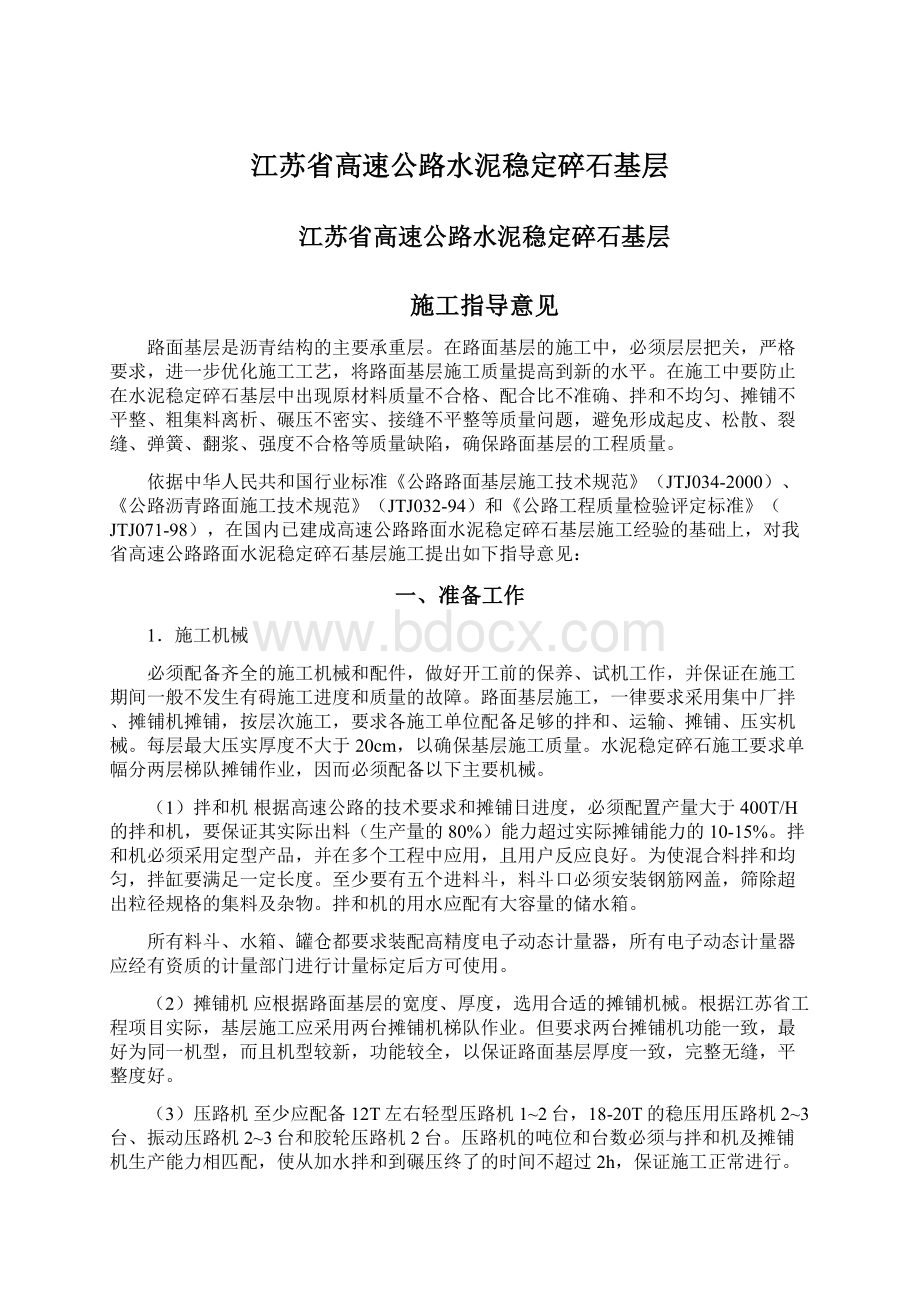
拌和机的用水应配有大容量的储水箱。
所有料斗、水箱、罐仓都要求装配高精度电子动态计量器,所有电子动态计量器应经有资质的计量部门进行计量标定后方可使用。
(2)摊铺机应根据路面基层的宽度、厚度,选用合适的摊铺机械。
根据江苏省工程项目实际,基层施工应采用两台摊铺机梯队作业。
但要求两台摊铺机功能一致,最好为同一机型,而且机型较新,功能较全,以保证路面基层厚度一致,完整无缝,平整度好。
(3)压路机至少应配备12T左右轻型压路机1~2台,18-20T的稳压用压路机2~3台、振动压路机2~3台和胶轮压路机2台。
压路机的吨位和台数必须与拌和机及摊铺机生产能力相匹配,使从加水拌和到碾压终了的时间不超过2h,保证施工正常进行。
(4)自卸汽车数量应与拌和设备、摊铺设备、压路机相匹配。
(5)装载机
(6)洒水车
(7)水泥钢制罐仓可视摊铺能力决定其容量,可用2个50T的,也可用一个80-100T,罐仓内应配有水泥破拱器,以免水泥起拱停流。
以上机械数量至少应满足每个工点,每日连续正常生产及工期要求。
2.质量检测仪器
(1)水泥胶砂强度、水泥凝结时间、安定性检验仪器
(2)水泥剂量测定设备
(3)重型击实仪
(4)水泥稳定碎石抗压试件制备与抗压强度测定设备
(5)标准养护室
(6)基层密度测定设备
(7)标准筛(方孔)
(8)土壤液、塑限联合测定仪
(9)压碎值仪
(10)针片状测定仪器
3.底基层的检查与验收
(1)底基层外形检查
底基层外形检查内容有高程、中线偏位、宽度、横坡度和平整度。
(2)底基层压实度检查、修补与验收
底基层应进行压实度检查,凡不符合要求的路段,应分别采用补充碾压、填换好的材料等,并按附表一的规定进行检查与验收。
(3)底基层沉降检查
底基层的表面沉降速率应达到连续两个月小于5mm/月才可铺筑基层。
二、混合料组成设计
水泥稳定碎石是由几种材料混合而成,为了确定各种材料组成比例,充分发挥各种材料的特性,获得性能优良的稳定材料,必须进行混合料的组成设计。
水泥稳定材料的组成设计包括:
根据规定的材料指标要求,通过试验选取合适的集料和水泥;
确定合理的集料配合比例,水泥剂量和混合料的最佳含水量。
合理的水泥稳定碎石组成必须达到强度要求,具有较小的温缩和干缩系数(现场裂缝较少),施工和易性好(粗集料离析较小)。
1.材料要求
(1)水泥
普通硅酸盐水泥、矿渣硅酸盐水泥、火山灰质硅酸盐水泥都可以用于水泥稳定碎石路面基层施工,禁止使用快硬水泥、早强水泥以及其它受外界影响而变质的水泥。
路面基层宜采用强度等级较低的水泥;
水泥各龄期强度、安定性等应达到相应指标要求;
要求水泥初凝时间3小时以上、终凝时间不小于6个小时。
如采用散装水泥,在水泥进场入罐时,要了解其出炉天数。
刚出炉的水泥,要停放七天,且安定性合格后才能使用,夏季高温作业时,散装水泥入罐温度不能高于50℃,高于这个温度,若必须使用时,应采用降温措施。
(2)碎石
碎石的最大粒径为31.5mm,轧石场轧制的材料应按不同粒径分类堆放,以利施工时掺配方便,采用的套筛应与规定要求一致。
基层用级配碎石备料建议按粒径9.5-31.5mm、粒径4.75-9.5mm、粒径2.36-4.75mm和粒径2.36mm以下四种规格筛分加工出料。
水泥稳定碎石混合料中碎石压碎值应不大于28%,针片状含量宜不大于15%,集料中小于0.6mm的颗粒必须做液限和塑性指数试验,要求液限小于28%,塑性指数<
9。
集料的颗粒组成应符合表1的规定。
表1水泥稳定碎石混合料中集料的颗粒组成
级配
通过下列筛孔(mm)的重量百分率(%)
31.5
26.5
19
9.5
4.75
2.36
0.6
0.075
范围
100
90~100
72~89
47~67
29~49
17~35
8~22
0~7
(3)水凡饮用水皆可使用,遇到可疑水源,应委托有关部门化验鉴定。
2.混合料组成设计
(1)取工地实际使用的集料,分别进行筛分,按颗粒组成进行计算,确定各种集料的组成比例。
要求组成混合料的级配应符合表1的规定,且4.75mm、0.075mm的通过量应接近级配范围的中值。
(2)取工地使用的水泥,按不同水泥剂量分组试验。
一般建议水泥剂量按4%、4.5%、5%、5.5%四种比例进行试验(水泥:
集料=4:
100、4.5:
100、5:
100、5.5:
100)。
制备不同比例的混合料(每组试件个数为:
偏差系数10%~15%时9个,偏差系数15%~20%时13个),用重型击实法确定各组混合料的最佳含水量和最大干密度。
(3)为减少基层裂缝,必须做到三个限制:
在满足设计强度的基础上限制水泥用量;
在减少含泥量的同时,限制细集料、粉料用量;
根据施工时气候条件限制含水量。
具体要求水泥剂量不应大于5.5%、集料级配中0.075mm以下颗粒含量不宜大于5%、含水量不宜超过最佳含水量的1%。
(4)根据确定的最佳含水量,拌制水泥稳定碎石混合料,按要求压实度(重型击实标准,98%)制备混合料试件,在标准条件下养护6天,浸水一天后取出,做无侧限抗压强度。
(5)水泥稳定碎石试件的标准养护条件是:
将制好的试件脱模称重后,应立即放到相对湿度95%的养护室内养生,养护温度淮安以南为25℃±
2℃,淮安以北为20℃±
2℃。
养生期的最后一天(第七天)将试件浸泡在水中,在浸泡水之前,应再次称试件的质量,水的深度应使水面在试件顶上约2.5cm,浸水的水温应与养护温度相同。
将已浸水一昼夜的试件从水中取出,用软的旧布吸去试件表面的可见自由水,并称试件的质量。
前六天养生期间试件质量损失(指含水量的减少)应不超过10g,质量损失超过此规定的试件,应予作废。
(6)水泥稳定碎石7天浸水无侧限抗压强度代表值应满足≥3.0MPa~5.0MPa。
设计累计标准轴次小于12*106的高速公路用低限值;
设计累计标准轴次大于12*106的高速公路用中值;
主要行驶重载车辆的高速公路应用高限值。
某一高速公路应采用一个值,而不是一个范围,具体用值由设计单位确定。
(7)试件室内试验结果抗压强度的代表值按下式计算:
式中:
-抗压强度代表值,MPa;
-该组试件抗压强度的平均值,MPa;
-保证率系数,高速公路保证率95%,此时=1.645;
-试验结果的偏差系数(以小数计)。
(8)取符合强度要求的最佳配合比作为水泥稳定碎石的生产配合比,用重型击实法求得最佳含水量和最大干密度,经总监代表、助理确认,报总监批准,以指导施工。
三、试铺
正式开工之前,应进行试铺。
试铺段应选择在经验收合格的底基层上进行,其长度为300~600m左右,每一种方案试验100m-200m。
水泥稳定碎石混合料采用中心站集中拌和(厂拌)法施工,由两台摊铺机梯队摊铺作业,应避免纵向接缝。
试铺路段的拌和、摊铺、碾压各道工序按现行路面基层施工技术规范(JTJ034-2000)进行。
试铺段要决定的主要内容如下:
(1)验证用于施工的集料配合比例
1)调试拌和机,分别称出拌缸中不同规格的碎石、水泥、水的重量,测量其计量的准确性
2)调整拌和时间,保证混合料均匀性
3)检查混合料含水量、集料级配、水泥剂量、7天无侧限抗压强度
(2)确定一次铺筑的合适厚度和松铺系数(约为1.20~1.30)
(3)确定标准施工方法
①混合料配比的控制
②混合料摊铺方法和适用机具(包括摊铺机的行进速度、摊铺厚度的控制方式、梯队作业时摊铺机的间隔距离,一般5-8m)
③含水量的增加和控制方法
④压实机械的选择和组合,压实的顺序,速度和遍数
建议:
12-15t双钢轮压路机静压1遍(速度1.5-1.7km/h);
18-20t双钢轮压路机静压1遍(速度1.5-1.7km/h);
激振力20-25t三轮或双钢轮压路机振动碾压2遍(速度1.8-2.2km/h);
激振力大于40t三轮或双钢轮压路机振动碾压2-3遍(速度1.8-2.2km/h);
轮胎压路机碾压1-2遍(速度1.5-1.7km/h)。
⑤拌和、运输、摊铺和碾压机械的协调和配合
(4)确定每一作业段的合适长度(一般建议50m-80m)
(5)严密组织拌和、运输、碾压等工序,缩短延迟时间
检验标准见附表二,其中试铺段的检验频率应是标准中规定正式路面的2-3倍。
当使用的原材料和混合料、施工机械、施工方法及试铺路面各检验项目的检测结果都符合规定,可按以上内容编写《试铺总结》,经驻地监理工程师审查、报总监代表和总监助理确认后,经总监批准,即可作为申报正式路面施工开工的依据。
四、施工
1.一般要求
(1)清除作业面表面的浮土、积水等。
并将作业面表面洒水湿润。
(2)开始摊铺的前一天要进行测量放样,按摊铺机宽度与传感器间距,一般在直线上间隔为10m,在平曲线上为5m,做出标记,并打好导向控制线支架,根据松铺系数算出松铺厚度,决定导向控制线高度,挂好导向控制线,(测量精度按部颁标准控制)。
用于控制摊铺机摊铺厚度的控制线的钢丝拉力应不小于800N。
(3)水泥稳定碎石基层的施工期为淮安以南在10月30日前,淮安以北在10月20前结束施工。
(4)下层水泥稳定碎石施工结束7天后即可进行上层水泥稳定碎石的施工。
建议两层水泥稳定碎石施工间隔不宜长于30天。
2.混合料的拌和
(1)开始拌和前,拌和场的备料应能满足3-5天的摊铺用料。
(2)每天开始搅拌前,应检查场内各处集料的含水量,计算当天的配合比,外加水与天然含水量的总和要比最佳含水量略高。
实际的水泥剂量可以大于混合料组成设计时确定的水泥剂量约0.5%,但是,实际采用的水泥剂量和现场抽检的实际水泥剂量应小于5.5%。
同时,在充分估计施工富余强度时要从缩小施工偏差入手,不得以提高水泥用量的方式提高路面基层强度。
(3)每天开始搅拌之后,出料时要取样检查是否符合设计的配合比,进行正式生产之后,每1-2小时检查一次拌和情况,抽检其配比、含水量是否变化。
高温作业时,早晚与中午的含水量要有区别,要按温度变化及时调整。
(4)