数控车床自动回转刀架的控制设计Word格式文档下载.docx
《数控车床自动回转刀架的控制设计Word格式文档下载.docx》由会员分享,可在线阅读,更多相关《数控车床自动回转刀架的控制设计Word格式文档下载.docx(27页珍藏版)》请在冰豆网上搜索。
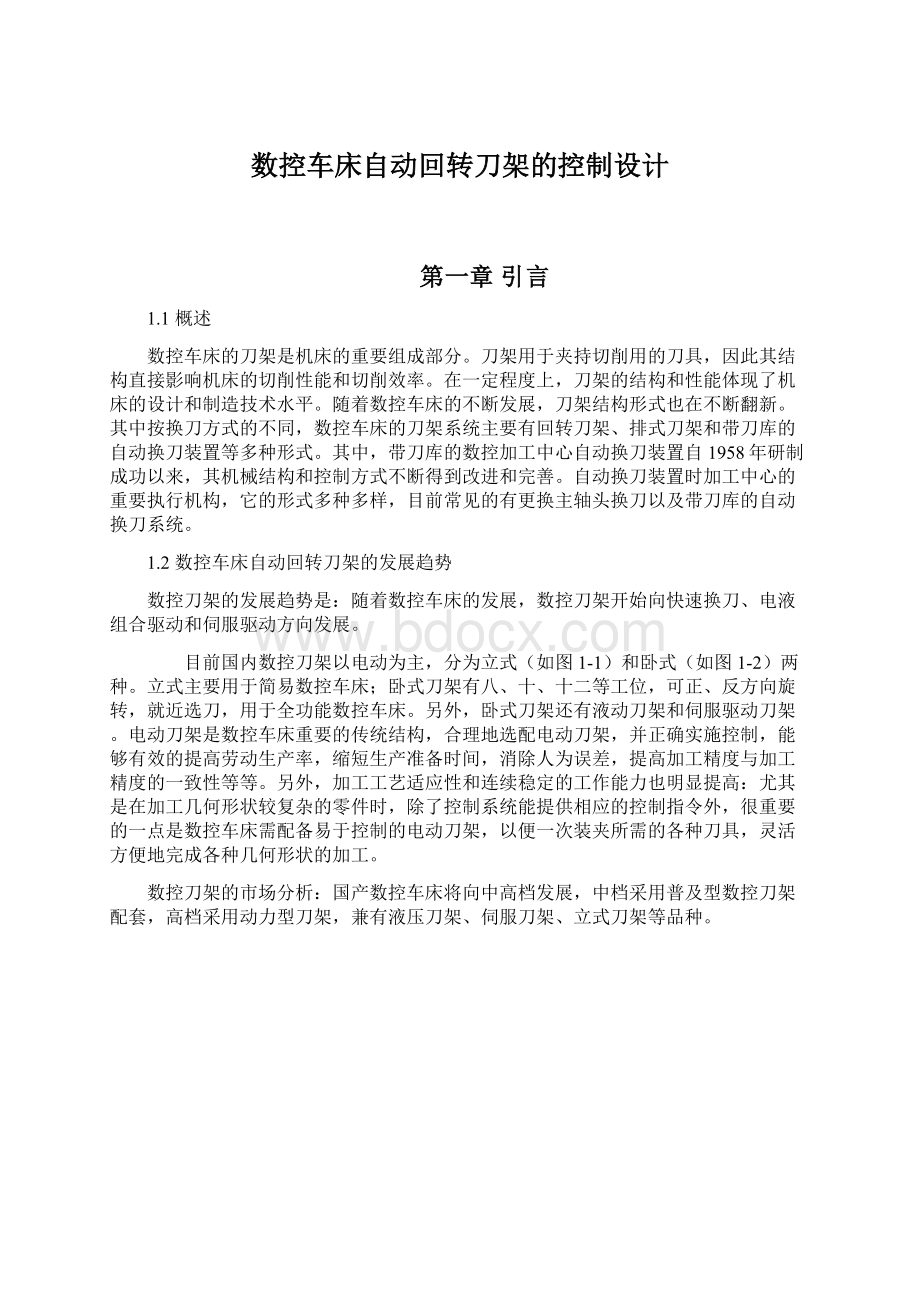
卧式刀架有八、十、十二等工位,可正、反方向旋转,就近选刀,用于全功能数控车床。
另外,卧式刀架还有液动刀架和伺服驱动刀架。
电动刀架是数控车床重要的传统结构,合理地选配电动刀架,并正确实施控制,能够有效的提高劳动生产率,缩短生产准备时间,消除人为误差,提高加工精度与加工精度的一致性等等。
另外,加工工艺适应性和连续稳定的工作能力也明显提高:
尤其是在加工几何形状较复杂的零件时,除了控制系统能提供相应的控制指令外,很重要的一点是数控车床需配备易于控制的电动刀架,以便一次装夹所需的各种刀具,灵活方便地完成各种几何形状的加工。
数控刀架的市场分析:
国产数控车床将向中高档发展,中档采用普及型数控刀架配套,高档采用动力型刀架,兼有液压刀架、伺服刀架、立式刀架等品种。
图1-1立式回转刀架图1-2卧式回转刀架
1.3刀架的设计准则
我们设计主过程,本着以下几条设计准则:
1)创造性的利用所需要的物理性能和控制;
2)预测意外载荷;
3)创造有利的载荷条件;
4)提高合理的应力分布和刚度面;
5)辨别功能载荷及其意义;
6)重量尽量轻;
7)应用基本公式求相称尺寸和最佳尺寸;
8)根据性能组合选择材料;
9)在储备零件与整体零件之间进行选择;
10)进行功能设计以适应制造工艺和降低成本的要求。
第二章数控车床自动回转刀架的设计
2.1数控车床刀架应满足的要求
1)满足工艺过程所提出的要求。
机床依靠刀具和工件间相对运动形成工件表面,而工件的表面形状和表面位置的不同,要求刀架能够布置足够多的刀具,而且能够方便而正确地加工各工件表面,为了实现在工件的一次安装中完成多工序加工,所以要求刀架可以方便地转位。
2)在刀架以要能牢固地安装刀具,在刀架上安装刀具进还应能精确地调整刀具的位置,采用自动交换刀具时,应能保证刀具交换前后都能处于正确位置。
以保证刀具和工件间准确的相对位置。
刀架的运动精度将直接反映到加工工件的几何形状精度和表面粗糙度上,为此,刀架的运动轨迹必须准确,运动应平稳,刀架运转的终点到位应准确。
面且这种精度保持性要好,以便长期保持刀具的正确位置。
3)刀架应具有足够的刚度。
由于刀具的类型、尺寸各异,重量相差很大,刀具在自动转换过程中方向变换较复杂,而且有些刀架还直接承受切削力。
考虑到采用新型刀具材料和先进的切削用量,所以刀架必须具有足够的刚度,以使切削过程和换刀过程平稳。
4)可靠性高。
由于刀架在机床工作过程中,使用次数很多,而且使用频率也高,所以必须充分重视它的可靠性。
5)刀架是为了提高机床自动化而出现的,因而它的换刀时间应尽可能缩短,以利于提高生产率。
目前自动换刀装置的换刀时间在0.8—6秒之间不等。
而且还在进一步缩短。
6)操作方便和安全。
刀架是工人经常操作的机床部件之一,因此它的操作是否方便和安全,往往是评价刀架设计好坏的指标。
刀架上应便于工人装刀和调刀,切屑流出方向不能朝向工人,而且操作调整刀架的手柄(或手轮)要省力,应尽量设置在便于操作的地方。
2.1.1动力刀架的整体方案设计
刀架是车床的重要组成部分,加工中心的动力刀架可安装各种非动力辅助刀夹和动力刀夹进行加工,用于夹持加工用的刀具,因此其结构直接影响到车床的加工性能和加工效率。
刀架采用端齿分度,转位由步进电动机驱动,刀位由二进制绝对编码器识别,动力刀具由变频电机驱动,通过同步齿形带等将动力传递到刀夹。
各类数控机床的自动换到装置的结构取决于机床的类型、工艺范围、使用刀具种类和数量。
数控机床常用的自动换刀装置的类型、特点、适用范围见表2-1
表2-1
类别型式
特点
适用范围
转塔式
回转刀架
多为顺序换刀,换刀时间短、结构简单紧凑、容纳刀具较少
各种数控车床,数控车削加工中心
转塔头
顺序换刀,换刀时间短,刀具主轴都集中在转塔头上,结构紧凑。
但刚性较差,刀具主轴数受限制
数控钻、镗、铣床
刀库式
刀具与主轴之间直接换刀
换刀运动集中,运动不见少。
但刀库容量受限
各种类型的自动换刀数控机床。
尤其是对使用回转类刀具的数控镗、铣床类立式、卧式加工中心机床
要根据工艺范围和机床特点,确定刀库容量和自动换刀装置类型
用机械手配合刀库进行换刀
刀库只有选刀运动,机械手进行换刀运动,刀库容量大
2.1.2数控机床刀架的类型选择
按换刀方式的不同,数控车床的刀架系统主要有回转刀架、排式刀架和带刀库的自动换刀装置等多种形式,下面对这三种形式的刀架作简单的介绍。
1)排式刀架:
排式刀架一般用于小规格数控车床,以加工棒料或盘类零件为主。
其结构形式为:
夹持着各种不同用途刀具的刀夹沿着机床的X坐标轴方向排列在横向滑板上。
刀具的典型布置方式如下图所示。
这种刀架在刀具布置和机床调整等方面都较为方便,可以根据具体工件的车削工艺要求,任意组合各种不同用途的刀具,一把刀具完成车削任务后,横向滑板只要按程序沿X轴移动预先设定的距离后,第二把刀就到达加工位置,这样就完成了机床的换刀动作。
这种换刀方式迅速省时,有利于提高机床的生产效率。
宝鸡机床厂生产的CK7620P全功能数控车床配置的就是排式刀架。
2)回转刀架:
回转刀架是数控车床最常用的一种典型换刀刀架,一般通过液压系统或电气来实现机床的自动换刀动作,根据加工要求可设计成四方、六方刀架或圆盘式刀架,并相应地安装4把、6把或更多的刀具。
回转刀架的换刀动作可分为刀架抬起、刀架转位和刀架锁紧等几个步骤。
它的动作是由数控系统发出指令完成的。
回转刀架根据刀架回转轴与安装底面的相对位置,分为立式刀架和卧式刀架两种。
3)带刀库的自动换刀装置:
上述排式刀架和回转刀架所安装的刀具都不可能太多,即使是装备两个刀架,对刀具的数目也有一定限制。
当由于某种原因需要数量较多的刀具时,应采用带刀库的自动换刀装置。
带刀库的自动换刀装置由刀库和刀具交换机构组成。
排式刀架回转刀架
本次设计的刀架是四工位刀架,刀位较少,且要求精度较高,所以可以选择回转刀架和排式刀架,且一次装夹中完成多工序加工,缩短辅助时间,减少多次安装所引起的加工误差保证转位具有高的重复定位精度具有转位快,定位精度高,切向扭矩大的特点。
而电动机最低转速为35r/min,最高转速为4000r/min,额定转速为ne=2000r/min刀具顺利换刀,因此需要很高的稳定性。
对于以上三种刀架,排式刀架加工棒料或盘类零件为主,局限性较大,同时定位精度不高,况且排式刀架往复运动幅度较大,占用空间多。
综上,本次设计选用回转刀架作为设计对象,其具有换刀时间短、结构简单紧凑、容纳刀具较少的特点,所以较为合适,对于回转刀架根据安装方式的不同可分为立式和卧式两种根据机械定位方式的不同,自动回转刀架又可分为端齿盘定位型和三齿盘定位型等。
其中断齿盘定位型换刀时刀架需抬起,换刀速度较慢且密封性较差,但其结构较简单。
三齿盘定位型又叫免抬型,其特点是换刀时刀架不抬起,因此换刀时速度快且密封性好,但其结构较复杂。
由于本人初次设计数控刀架,所以选择较为简单的端齿盘定位,结构简单。
同时,自动回转刀架在结构上必须具有良好的强度和刚性,以承受粗加工时的切削抗力。
为了保证转位具有高的重复定位精度,自动回转刀架还要选择可靠的定位方案和合理的定位结构。
自动回转刀架的自动换刀时由控制系统和驱动电路来实现的。
发信转位采用霍尔元件,使用寿命长。
根据以上对机床刀架类型、性能及其使用场合的综合比较,并结合现有数控车床的实例,本次设计的动力刀架为伺服电机驱动的转塔式自动回转刀架。
2.2刀架的工作原理
回转刀架的工作原理为机械螺纹升降转位式。
工作过程可分为刀架抬起、刀架转位、刀架定位并压紧等几个步骤。
图2.1为自动回转刀架,其工作过程如下:
1)刀架抬起当数控系统发出换刀指令后,通过接口电路使电机正转,经传动装置驱动蜗杆蜗轮机构3、蜗轮螺纹即螺母机构延逆时针旋转,此时由于上下齿盘40、6处于啮合状态,在丝杆螺母机构转动时,使上刀架体产生向上的轴向力将上齿盘40松开并抬起,直至两定位齿盘40、6脱离啮合状态,从而带动上刀架和齿盘产生“上台”动作。
2)刀架转位当圆套13逆时针转过150°
时,齿盘40、6完全脱开,此时销钉准确进入圆套13中的凹槽中,带动刀架体转位。
3)刀架定位当上刀架转到需要到位后(旋转90°
、180°
或270°
),数控装置发出的换刀指令使霍尔开关19中的某一个选通,当磁性板18与被选通的霍尔开关对齐后,霍尔开关反馈信号使电机反转,插销39在弹簧力作用下进入反靠盘7地槽中进行粗定位,上刀架体停止转动,电机继续反转,使其在该位置落下,通过螺母丝杆机构使上刀架移到齿盘40、6重新啮合,实现精确定位。
4)刀架压紧刀架精确定位后,电机及许反转,夹紧刀架,当两齿盘增加到一定夹紧力时,电机由数控装置停止反转,防止电机不停反转而过载毁坏,从而完成一次换刀过程。
图2.1
2.3步进电机的选用
动力刀架的转位需要涡轮蜗杆机构来实现,而驱动蜗轮轴旋转是由电机来实现的,电机的选择要满足所需负载和转矩。
从而需要我们对电机进一步的选择。
许多机械加工需要微量进给。
要实现微量进给,步进电机、直流伺服交流伺服电机都可作为驱动元件。
对于后两者,必须使用精密的传感器并构成闭环系统,才能实现微量进给。
在开环系统中,广泛采用步进电机作为执行单元。
这是因为步进电机具有以下优点:
1)直接采用数字量进行控制;
2)转动惯量小,启动、停止方便;
3)成本低;
4)无误差积累;
5)定位准确;
6)低频率特性比较好;
7)调速范围较宽;
采用步进电机作为驱动单元,其机构也比较简单,主要是变速齿轮副、滚珠丝杠副,以克服爬行和间隙等不足。
通常步进电机每加一个脉冲转过一个脉冲当量;
但由于其脉冲当量一般较大,如0.01mm,在数控系统中为了保证加工精度,广泛采用步进电机的细分驱动技术。
由于课题要求电动机最低转速为35r/min,最高转速为4000r/min,额定转速为ne=2000r/min。
要求4把刀更换。
因为刀架上升、下降各转150°
,刀架转位至少需90°
,所以蜗轮转的角度a=390°
。
考虑刀架只需小功率驱动,为减少生产成本,选用JD60电动机,其转速为1400r/min,额定功率为60W。
2.4蜗杆及蜗轮的选用与校核
2.4.1选择传动的类型
考虑到传递的功率不大,转速较低,选用2A蜗杆,精度8级,GB10089-88
2.4.2选择材料和确定许用应力
由《机械设计》表6-7查得蜗杆选用45钢,表面淬火,硬度为45~55HRC,蜗轮齿圈用ZCuSn10P1砂模铸造,为了节约贵重的有色金属,仅齿圈用青铜制造,而轮芯用灰铸铁HT150制造。
得到[ð
]H=200MPa,[ð
]f=500MPa
2.4.3按接触强度确定主要参