建筑陶瓷工业热工设备节能技术发展现状_Word文档下载推荐.doc
《建筑陶瓷工业热工设备节能技术发展现状_Word文档下载推荐.doc》由会员分享,可在线阅读,更多相关《建筑陶瓷工业热工设备节能技术发展现状_Word文档下载推荐.doc(11页珍藏版)》请在冰豆网上搜索。
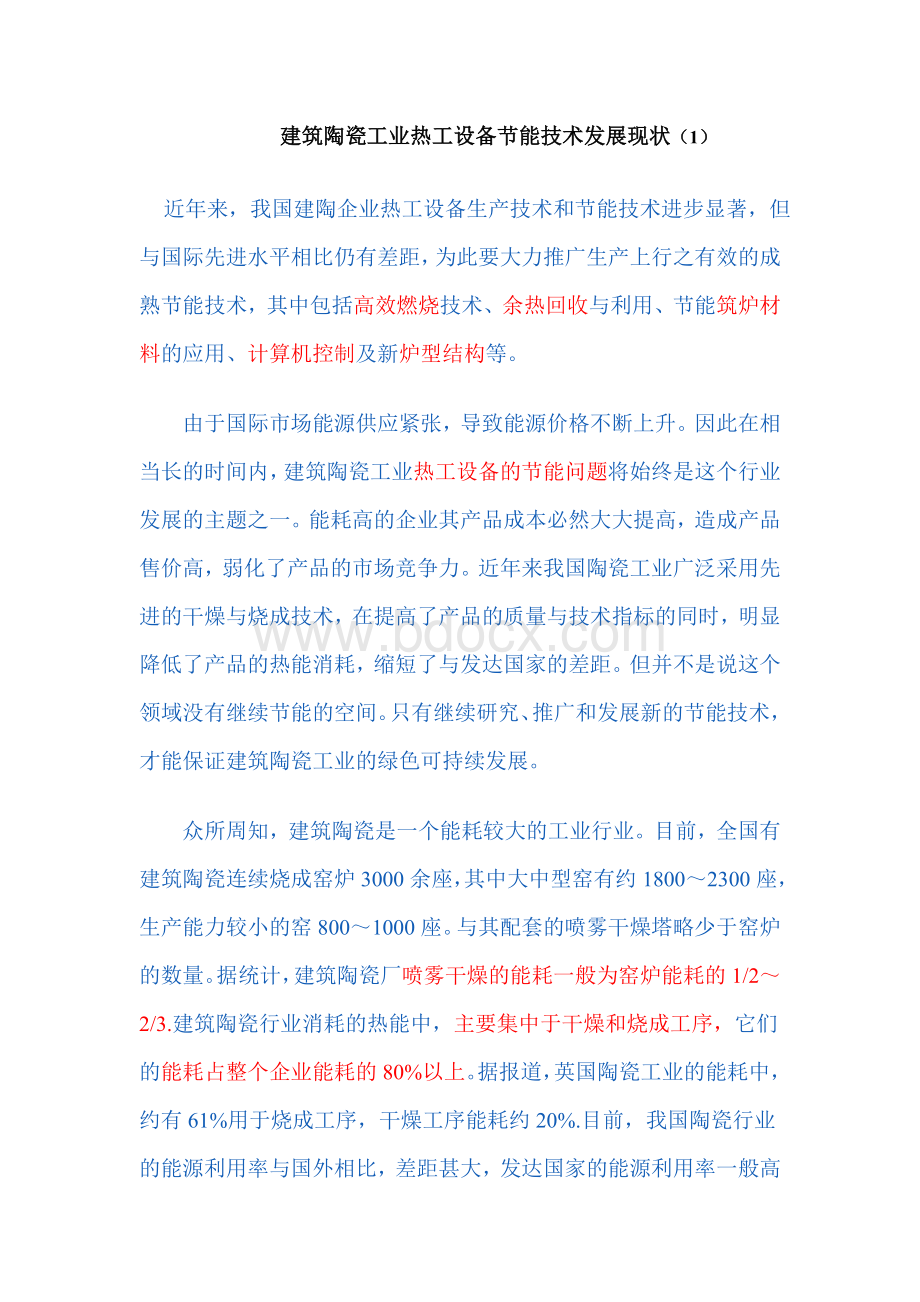
据统计,建筑陶瓷厂喷雾干燥的能耗一般为窑炉能耗的1/2~2/3.建筑陶瓷行业消耗的热能中,主要集中于干燥和烧成工序,它们的能耗占整个企业能耗的80%以上。
据报道,英国陶瓷工业的能耗中,约有61%用于烧成工序,干燥工序能耗约20%.目前,我国陶瓷行业的能源利用率与国外相比,差距甚大,发达国家的能源利用率一般高达50%以上,美国达57%,而我国仅达到28%~30%左右。
因此,如何降低陶瓷工业的能耗,特别是热工设备的能耗,提高能源利用率,是摆在建筑陶瓷行业面前的迫切任务。
基本情况窑炉:
国内广东产区陶瓷生产厂的典型数据:
生产外墙砖企业的产品单位烧成热耗在2200kj/kg~6000kj/kg;
生产仿古砖企业的产品单位烧成热耗在2000kj/kg~3000kj/kg;
生产抛光砖的产品单位烧成热耗在2200kj/kg~3300kj/kg.髙的单位烧成热耗值主要是由以下原因造成的:
(1)各个企业产品品种不同和对产品质量的要求不同,有的产品需要二次烧成。
(2)窑炉结构和工艺制度不合理。
(3)窑炉排烟损失大。
(4)产品出窑温度和排烟温度偏高。
(5)窑体散热损失较大。
(6)部分窑炉使用垫板。
喷雾干燥塔:
喷雾干燥塔的产品干粉单位热耗在2000kj/kg~4000kj/kg;
髙的热耗值主要是由以下原因造成的:
(1)制浆工艺未严格控制,对外加剂的选择和质量控制不严格,造成进入喷雾塔泥浆水分偏高。
(2)喷雾塔结构不合理,如塔身较短、内径较小、喷枪与塔体不匹配,造成大量物料互相粘连和粘壁。
降低了塔的产量,增加了热耗。
(3)喷雾塔所使用的各种材料特别是保温隔热材料低劣,使用时间稍长,发生变形和收缩,造成塔体散热损失比较大。
(4)操作工艺不合理,对进塔风温、排风温度、塔内压力、喷浆压力和喷片孔大小之间的相互影响关系不了解,工艺参数选择不够优化,造成干粉单位热耗偏高。
节能措施:
从节能角度出发,建立整厂节能系统化、统一化的观点。
衡量1座窑炉或喷雾塔是否先进,其重要的指标之一是单位产品的能耗指标。
衡量1家陶瓷生产企业是否能完全、合理地利用能源,则要从整个陶瓷生产工序方面进行考虑。
陶瓷生产企业设计建造时,由于种种原因往往不进行全厂的热平衡设计、核算。
例如:
烧成工序要建多少条窑,窑炉余热供给干燥后是否足够或剩余,多余的热量用于何处,干燥坯体后排出的废气余热能否利用等,都未进行认真的考虑,没有一整套的全厂热平衡数据。
如果我们能够从喷雾塔干燥、窑炉烧成供入的燃料所产生的热能开始,从窑炉-坯体干燥-粉料干燥-厂区暖通-发电等,逐级利用热能,就可做到高效地利用能源。
窑炉结构的优化炉型结构的改进:
窑炉的各种节能措施最终都要综合地体现在炉型结构上,每次炉型的变化都带来了能耗的降低,如:
明焰裸烧宽体隧道窑逐步取代了隔焰隧道窑;
梭式窑、钟罩窑和升降窑相继出现并逐渐占领了间歇式窑的领域,取代倒焰窑;
上世纪70年代末出现了辊道窑以后,就逐步占领了陶瓷砖烧成连续式窑炉领域。
各种类型的现代化陶瓷窑炉采用高速烧嘴,采用全轻质化装配式窑体,使得窑体质量大为减小,并使得窑体蓄热减至旧结构窑体的1/3~1/6,以致使连续式窑也变得灵活起来,可以在周末假日停窑,大大方便了生产。
以上各项窑炉结构的变化,大大降低了产品的能耗,使得产品的烧成热耗由30~40mj/kg降为2~6kj/kg左右。
因此,炉型的改变是节能突破性的进展,首先应注重炉型的改变。
高效燃烧技术:
对燃料炉来说,燃料燃烧过程必须满足炉子的工艺要求,如炉温、火焰形状、炉内气氛等,否则将会影响炉子的产量、能耗及产品的质量。
近年来已开发并推广应用的燃烧装置有:
调焰烧嘴、平焰烧嘴、高速烧嘴、亚高速烧嘴、自身预热烧嘴、油气两用烧嘴、预热式(低NOx)烧嘴。
正确地使用高效燃烧装置,可使窑炉节能5%.在燃烧装置的制造质量方面,各燃烧设备制造厂应建立健全产品出厂的性能检验制度,使燃烧装置规格、型号标准化系列化,一些附属装置如管路阀件、风机、油泵、自动点火和火焰监测等配套供应以满足炉窑的需要。
在使用前,使用厂家对燃烧装置的选择要紧密结合工艺过程的要求,选择与燃料相适应的燃烧装置并采用合理的布置方式。
在使用中,要经常检查燃烧系统的完善性和性能的稳定性,保证燃烧系统在设计参数范围内工作。
改善燃料燃烧状态,降低燃料的不完全燃烧损失,减少燃料的使用量,提高燃烧效率,达到降低燃料能耗的目的。
节能长寿筑炉材料的使用:
热工设备尽量使用导热系数小、热容小的耐火材料。
耐火纤维的导热系数小,可使炉体散热损失减少50%左右,而且热容量小,炉温的升降快,炉体的热损失小,如果炉子全部用耐火纤维作炉衬,炉体重量显著减轻,则炉体钢架等结构都可以轻量化,炉窑设计将有很大变化。
为提高陶瓷纤维抗粉化能力,增加窑炉内传热效率,节能降耗。
使用热辐射涂料材料,可以强化炉内的辐射传热,有助于热能的充分利用,其节能效果为3%~5%.如热辐射涂料HRC,在高温段,将其涂在窑壁耐火材料上,材料的辐射率由0.7上升为0.96,可节能183.3mj/(m2·
h);
而在低温段涂上HRC后,窑壁辐射率从0.7上升为0.97,可节能19.0mj/(m2·
h)。
推广和扩大使用不定型耐火材料是筑炉技术的发展方向,近年来广泛应用的耐火可塑料、耐火浇注料等均属于不定型耐火材料范畴,与耐火砖相比,节省了制砖烧成等工序,节省了能耗。
用不定型耐火材料筑炉,炉窑的整体性能好,严密、结实、寿命长,从而提高了炉窑的作业率,因此可以全面改善炉子的技术经济指标。
一般而言,可使炉窑节能4%.由于延长炉体寿命提高了炉子作业率,所带来的设备高产的效益尤为显著。
计算机控制:
陶瓷热工设备计算机控制是提高加热质量、减少环境污染、改善劳动条件、节约能耗、提高生产管理和自动化水平的有效措施之一。
目前国内有数以千计的窑炉使用计算机控制。
陶瓷热工设备进行计算机控制的第一步是实现燃烧控制,即实现炉温、供燃料量、燃料量与空气量的配比及炉压的控制,其中核心为燃料配比控制。
最简单的办法是按流量测量值控制配比,生产中由于存在设备漏风、燃料热值和压力波动及计量不准等问题,使配比失真。
可用测量烟气中的含氧量来控制配比,即掺氧分析法,它不受漏风、热值、压力波动及计量不准的影响,但氧化锆探头是消耗件,寿命短且价格昂贵,限制了该法的推广和应用。
在实现燃烧控制的基础上,应进一步提高控制水平,进行数学模型优化控制,其主要内容为优化炉窑的热制度,即炉温制度和供热制度。
数模优化控制在燃烧控制基础上可进一步达到节能10%的效果。
陶瓷热工设备是陶瓷厂整体中的一个局部,其工作应放到整体中加以衡量,而热工设备自身的燃烧控制、数模优化控制从局部看可能是最佳效果,放到整体中来衡量,则不一定是最优,这当中涉及各设备的协调、调度和管理等问题。
因此若想再提高一个层次就要进行管理优化控制,该管理优化控制的效果在单纯数模控制的基础上可再节能约5%.余热回收和利用:
首先,应该建立一种概念,就是把热工设备的余热当作一种资源,即余热资源。
陶瓷热工设备余热资源主要包括气态余热资源,即烟气余热;
固态余热资源,即产品和燃烧废渣的显热和潜热;
液态余热资源,主要是热水和热水汽。
对于陶瓷行业,主要是气态余热资源。
即使是固态余热资源,也很容易转化为气态余热资源。
建筑陶瓷企业的窑炉所产生的烟气带走的热量是巨大的,而且温度较高可达400℃~500℃,占窑炉总热量的25%~35%.喷雾塔所产生的烟气和水汽热能,热量巨大,但温度较低,仅为80℃~120℃。
若将这部分余热利用起来,其经济效益相当可观。
但是,由于人们的节能观念不足及技术水平的落后,致使我国陶瓷行业余热的利用率非常低,一般只有3%~8%,而国外的余热利用率一般都在15%左右。
可见,我国陶瓷热工设备的余热利用还有很大的开发空间。
现有工业余热利用方式:
直接利用窑炉余热;
在换热器中用烟气余热加热助燃空气和煤气;
设置预热段,用烟气余热加热坯体或喷雾泥浆;
设置余热锅炉,用烟气热量生产蒸汽并用产生的蒸汽来发电;
利用烟气余热产生的蒸汽来制冷和供暖。
直接利用窑炉余热干燥坯体:
窑炉缓冷段的冷却换热风就是干净空气通过窑内换热器,所以很洁净且温度较高,一般可以直接使用,将其作助燃风、搅拌风及坯体干燥等。
建筑陶瓷工业热工设备节能技术发展现状
(2)
换热器中用烟气余热加热助燃空气和气态燃料。
窑头排烟气主要是燃料燃烧后的烟气,还有坯釉料反应所产生的废气,其中含氟等有害物质,所以不能直接利用(如用于干燥坯体、做助燃风等)。
另外,环保处理也要求烟气温度低于200℃,这样如果采用换热器就可以一举两得。
一般可回收总热量的10%左右。
对窑头这部分烟气的利用是非常有价值的。
经换热器获得的热风可以直接送至燃烧器做助燃空气,也可以将热风经稀释输送到干燥窑做干燥介质或者它用。
采用换热器预热助燃空气或预热气态燃料,可以提高窑的热效率、降低燃料消耗,达到节能效果。
在进行高温燃烧时可提高火焰的温度,增加供热效率,缩短加热时间(烧成周期)。
而且因热风体积膨胀,致使燃烧器喷出口流速增大,加速了窑内气体循环,有助于窑内温度均匀。
有关资料表明:
当预热空气温度达到220~250℃时,可降低燃料消耗6%~8%.同时不同的助燃风温度,对火焰温度的影响非常大。
即使在煤气不预热的情况下,燃料的燃烧温度随着助燃空气的预热温度升高而显著提高。
这不仅可以解决烧成温度偏低的问题,还为企业节能降耗起着重要作用。
用余热加热坯体或喷雾泥浆。
陶瓷坯体在入烧成窑之前,由于施釉、印花等工序,会造成坯体温度较低,且含有0.5%~2%左右的水分,坯体无法快速升温。
如用余热低温加热坯体,既可使坯体温度升高至100℃以上,又可除去坯体中的水分。
便于坯体进入烧成窑后快速升温,提高烧成窑的产量。
利用余热对进喷雾塔泥浆进行预热也可取得较好的节能效果。
随着进浆温度的提高,喷雾塔的热效率可提高3%~8%.同时由于进浆温度的提高,造成浆料的粘度降低,对泥浆的雾化状况会有较大的改善。
但由于工艺布置的问题,窑炉一般与喷雾塔距离较远,影响了窑炉余热的利用。
最好在新厂设计或旧线改造时就考虑余热利用问题,这样才能有效地利用窑炉余热。
设置余热锅炉,用烟气热量生产蒸汽并用蒸汽发电。
利用余热产生低压蒸汽和利用蒸汽发电在水泥和玻璃行业已得到极大的发展,国内已有近60条生产线在正常运行,取得了极大的成效。
但水泥生产线余热量大,适合投入巨资安装低压锅炉产生蒸汽来发电。
陶瓷行业由于规模较小,余热量也较小,一次投入较大的资金来安装发电设备困难较大。
但随着技术的发展,国外已开发出一些新型的非常规余热发电系统,具有发电机组可大可小,余热温度低达100℃以下也可