薄膜与涂层现代表面技术Word文件下载.docx
《薄膜与涂层现代表面技术Word文件下载.docx》由会员分享,可在线阅读,更多相关《薄膜与涂层现代表面技术Word文件下载.docx(20页珍藏版)》请在冰豆网上搜索。
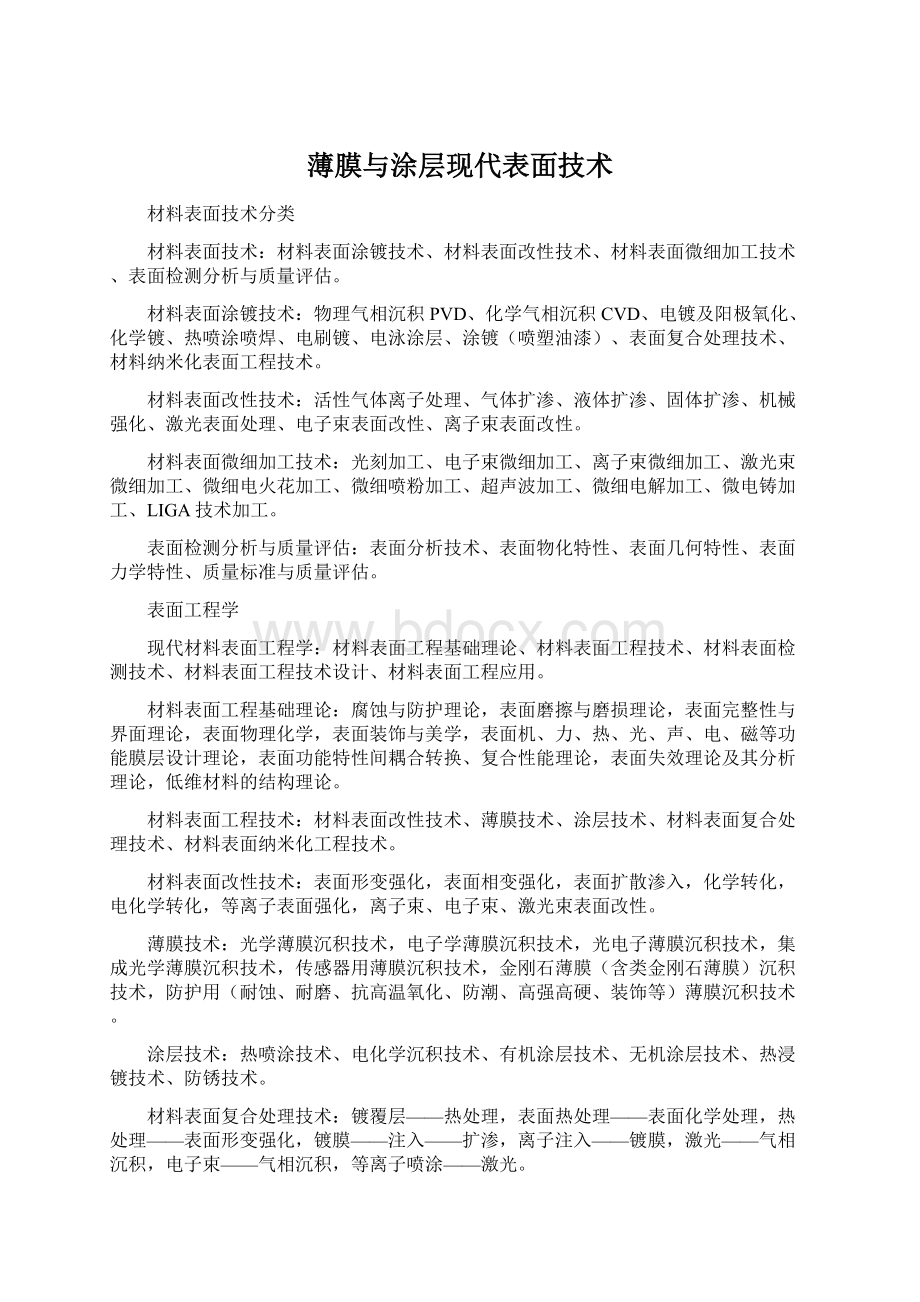
材料表面工程基础理论:
腐蚀与防护理论,表面磨擦与磨损理论,表面完整性与界面理论,表面物理化学,表面装饰与美学,表面机、力、热、光、声、电、磁等功能膜层设计理论,表面功能特性间耦合转换、复合性能理论,表面失效理论及其分析理论,低维材料的结构理论。
材料表面工程技术:
材料表面改性技术、薄膜技术、涂层技术、材料表面复合处理技术、材料表面纳米化工程技术。
表面形变强化,表面相变强化,表面扩散渗入,化学转化,电化学转化,等离子表面强化,离子束、电子束、激光束表面改性。
薄膜技术:
光学薄膜沉积技术,电子学薄膜沉积技术,光电子薄膜沉积技术,集成光学薄膜沉积技术,传感器用薄膜沉积技术,金刚石薄膜(含类金刚石薄膜)沉积技术,防护用(耐蚀、耐磨、抗高温氧化、防潮、高强高硬、装饰等)薄膜沉积技术。
涂层技术:
热喷涂技术、电化学沉积技术、有机涂层技术、无机涂层技术、热浸镀技术、防锈技术。
材料表面复合处理技术:
镀覆层——热处理,表面热处理——表面化学处理,热处理——表面形变强化,镀膜——注入——扩渗,离子注入——镀膜,激光——气相沉积,电子束——气相沉积,等离子喷涂——激光。
材料表面纳米化工程技术:
纳米颗粒复合电刷镀技术,纳米热喷涂技术,纳米涂装技术,纳米减摩自修复添加剂技术,纳米固体润滑干膜技术,纳米粘涂技术,纳米薄膜沉积技术。
材料表面检测技术:
表面微观结构分析技术,表面化学分析技术,表面物理性能测试技术,表面力学性能测试技术,表面几何特性测试技术,表面无损检测技术。
材料表面工程技术设计:
表面层成分结构设计,表面复合功能层设计,表面选择与应用设计,表面涂镀层制备工艺设计,表面工程施工设计,表面工程设备与工艺流程设计,表面工程车间设计。
材料表面工程应用:
表面层特性及其综合利用,表面层原料及加工技术,表面层标准及检验,表面界面维修与再造,表面质量与工艺过程控制,表面工程管理与经济分析。
薄膜功能分类
装饰功能薄膜、物理功能薄膜、机械功能薄膜、特殊功能薄膜。
装饰功能薄膜:
各种色调的彩色膜,幕墙玻璃用装饰膜,塑料金属化装饰膜,包装装潢及装饰薄膜,镀铝纸。
物理功能薄膜:
光学薄膜、微电子学薄膜、光电子学薄膜、集成光学薄膜、信息存储膜。
光学薄膜:
阳光控制膜,低辐射系数膜,防激光致盲膜——Al2O3、SiO2、TiO2、Cr2O3、Ta2O5、NiAi、金刚石和类金刚石薄膜Au、Ag、Cu、Al,反射膜,增反膜,选择性反射膜,窗口薄膜。
微电子学薄膜:
电极膜,电器元件膜——Si、GaAs、GeSi,传感器膜——Sb2O3、SiO、SiO2、TiO2、ZnO、AlN、Se、Ge、SiC、PbTiO3、Al2O3,超导元件膜——YBaCuO、BiSrCaCuO、Nb3Al、Nb3Ge,微波声学器件膜,晶体管薄膜,集成电路基片膜——Al、Au、Ag、Cu、Pt、NiCr、W,热沉或散射片膜。
光电子学薄膜:
探测器膜——HF/DFCL、COIL、Na3+、YAG、HgCdTe,光敏电阻膜——InSb、PtSi/Si、GeSi/Si,光导摄像靶膜——PbO、PbTiO3、(Pb、L)TiO3、LiTaO3。
集成光学薄膜:
光波导膜,光开关膜,光调制膜——Al2O3、Nb2O5、LiNbO3、Li、Ta2O5,光偏转膜——LiTaO3、Pb(Zr、Ti)O3、BaTiO3,激光器薄膜。
信息存储膜:
磁记录膜——磁带、硬磁盘、软磁盘、磁卡、磁鼓等用:
γ-(Fe2O3)、Co-Fe2O3、CrO2、FeCo、Co-Ni,光盘存储膜——CD-ROM、VCD、DVD、CD-E、GdTbFe、CdCo、InSb膜,铁电存储膜——Sr-TiO2,(Ba、Sr)TiO3、DZT、CoNiP、CoCr。
机械功能薄膜:
耐腐蚀膜——TiN、CrN、SiO2、Cr7C3、NbC、TaC、ZrO2、MCrAlY、Co+Cr、ZrO2+Y2O3,耐冲刷膜——TiN、TaN、ZrN、TiC、TaC、SiC、BN,耐高温氧化膜——TiCN、金刚石和类金刚石薄膜、TiSiN、TiAlSiN、TiSiCN,防潮放热膜——Al、Zn、Cr、Ti、Ni、AlZn、NiCrAl,高强度高硬度膜——CoCrAlY、NiCoCrAlYHf、NiCoCrAlYTa,润滑与自润滑——MoS2,成型加工(防咬合、裂纹、耐磨损)——TiC、TiCN、TiSiCN。
特殊功能薄膜:
真空下的干磨擦——DLC、金刚石;
辐射下的润滑与耐磨——MoS2;
高温耐磨与透光——金刚石;
具某方面特殊功能的纳米薄膜——单层:
金属、半导体、绝缘体、高分子,复合膜(包括纳米复合结构与复合功能):
金属——半导体、半导体——绝缘体、金属——绝缘体、金属——高分子、半导体——高分子。
表面改性技术
表面形变强化、表面相变强化、离子注入、表面扩散渗入、化学转化、电化学转化。
表面形变强化:
喷丸强化;
辊压强化——在金属表面、亚表面形成压应力区;
孔挤压强化。
表面相变强化:
感应加热表面淬火;
激光表面淬火——在金属表面、亚表面形成新的相变区,形成硬化层;
电子束表面淬火;
流态床表面硬化。
离子注入:
非金属离子注入——硼、氮、磷;
金属离子注入——铬、金旦、银、铅、锡;
复合离子注入——钛+碳、铬+碳、铬+钼、铬+磷;
离子混合——钛+氮、钼+硅、钛+钯。
表面扩散渗入:
非金属元素表面扩散——渗碳、氮、硼、硅、碳氮共渗;
金属元素表面扩散——渗锌、锡、铍、铝、铬、钨、钼、钒;
复合元素表面扩散——渗铝铬、铝硅、铝钛、铜铟、铝铬硅、钨钼硼硅。
化学转化:
化学氧化——在铝、镁、钢、铜表面形成氧化膜;
钝化——在钢、铜、锌、镉、铝、镁、钛上形成钝化膜;
磷化——在钢铁上形成磷化膜;
草酸盐处理——在钢铁上形成草酸盐膜;
着色——在钢、铜、不锈钢、钛、铬形成颜色;
钢件的发蓝——在钢件上形成黑色氧化膜;
磨光、滚光、抛光——提高表面完整性和光洁度。
电化学转化:
耐蚀阳极氧化——在铝、镁、钛表面形成耐腐蚀氧化膜;
粘结阳极氧化——在铝、镁表面形成易于粘结的氧化膜;
瓷质阳极氧化——在铝表面上形成瓷釉状氧化膜;
硬质阳极氧化——在铝表面上形成高耐磨的硬氧化膜;
微弧等离子体阳极氧化——在铝表面上形成超高硬度层或新型彩色装饰;
阳极氧化原位合成——在铝表面上形成多种铝质功能材料膜。
第二章热喷涂涂层技术
热喷涂涂层形成原理:
热喷涂用火焰、等离子射流、电弧等某种热源将涂层材料(丝、棒、粉)加热到熔融或半熔融状态,借助焰流或高手气体将其雾化,并加速把这些雾化后的粒子形成的高速熔滴喷射到基体表面,经扁平化,快速冷却凝固沉积成具有某种功能的涂层技术。
热喷涂可分为气体燃烧火焰喷涂(线材棒材火焰喷涂、粉末火焰喷涂、爆炸喷涂、高速火焰喷涂、塑料喷涂)、电弧喷涂(常规电弧喷涂、高速电弧喷涂)、等离子喷涂(微等离子喷涂、大气等离子喷涂、低压等离子喷涂、水稳等离子喷涂、三阴极等离子喷涂)、激光喷涂和电热热源喷涂(冷喷、线材电爆喷涂)。
热喷涂涂层形成过程及其结构
整个热喷涂涂层形成的过程有三步:
1喷涂粒子的产生;
2喷涂材料粒子与热源的相互作用,在热源作用下,喷涂材料被加热,熔化加速,同时还发生高温高速粒子与环境气氛的作用过程:
3高温高速熔融粒子与基体(或已沉积形成的涂层)作用,包括熔融粒子与基体的碰撞,与此同时伴随着横向流动扁平化,急速冷却凝固。
(加热、加速、碰撞、变形扁平化、冷却凝固与吸附沉积)
结构:
层状结构,其中存在着孔隙夹杂(粒子间互相熔融区、氧化膜、不完全熔融粒子、气孔)。
涂层与基体的结合机理:
1机械结合;
2物理结合,范德瓦尔力;
3冶金结合,互扩散。
热喷涂涂层的制备工艺
基体表面预处理:
要求表面必须清洁,并要有一定的粗糙度。
因此喷涂前,基体一定要进行表面净化和粗化的加工处理。
净化处理:
溶剂清洗、碱液清洗、加热脱脂、喷砂净化。
粗化处理:
增加涂层与基体的结合面,产生更多的表面“抛锚效应”点,并使涂层产生压应力,减少残余宏观应力。
使涂层和基体产生更强的结合,喷砂、电拉毛、机械加工。
喷涂工艺:
热源参数、喷涂材料的送进量、雾化参数、操作参数(喷涂距离、喷涂角度、喷枪和工件的相对移动速度)、工件的温度控制(防止基体及涂层过热,控制基体和涂层的相对膨胀而引起的热应力)、喷涂气氛的控制、涂层的后处理(封孔处理(提高涂层抗蚀性)、扩散处理(提高涂层与基体的结合强度,提高涂层的致密度和耐蚀性)、涂层的重熔处理(提高致密度,使合金成分组织更加均匀,进一步消除残余应力,使涂层与基体产生良好的冶金结合))。
涂层精加工:
切削、磨削。
第三章材料线道表面改性技术
金属材料表面改性主要是指金属表面形变强化,表面相变硬化,金属表面扩渗,等离子表面处理,电子束表面处理,激光束表面处理,离子注入技术等。
等离子体可提高反应气体分子的能量、离化率和相互间的化学反应程度。
等离子体的材料表面改性技术:
是辉光放电、等离子体在低于0.1Mpa的特定气氛中,用工件作阴极在和阳极之间产生的辉光放电所进行的一种使金属表面改性的处理工艺。
等离子渗氮原理:
第一阶段活性氮原子的产生;
第二阶段活性氮原子从介质中迁移到工件表面;
第三阶段氮原子从工件表面转移到心部(扩散控制)。
离子渗氮的理论:
溅射沉积理论,渗氮层是通过反应阴极溅射形成的。
等离子渗氮的工艺
离子渗氮的渗层有化合物层和扩散层组成。
扩散层的基体是氮在铁中的固溶体,其上弥散分布着细小的合金及铁的氮化物,依靠弥散强化,使渗层扩散区的硬度得到提高。
离子渗氮的主要工艺参数包括气体成分、处理温度和保温时间。
其他的参数有工作压力、工作电压及电流密度等。
温度和时间对渗层深度和厚度有影响的同时,也改变了渗层内残余应力的大小和分布。
气体压力影响到氮向工件表面的迁移速率及化合物层得增长速率,因此对扩散层的厚度有影响。
等离子渗硫:
在表面生产一层多孔的松软的由FeS、FeS2、Fe3S4所组成的波波的硫化物,起减摩润滑作用,提高钢制部件的耐磨性、抗咬合性,达到提高部件的使用寿命。
等离子硫氮共渗,硫碳氮共渗:
在离子渗氮时,添加含硫的H2S气氛,就可实现离子硫氮共渗,其渗层具有硫化物的减摩性及渗氮层的耐磨性的综合效果。
电子束与材料表面改性技术:
利用电子束对材料表面0.01~0.2mm范围作用的能量加热、熔化,实现对材料表面硬化(淬火),表面熔凝,熔覆,合金化和非晶化等材料表面改性。
材料的加热是因材料晶格的电子弹性和非弹性碰撞所产生的,是材料吸收电子束能量的结果。
电子束与材料表面改性工艺
1电子束表面硬化(即相变硬化,表面淬火):
由于电子束加热能量利用率高,速度快,温度梯度大,冷却速度快,材料的相变过程时间短,奥氏体晶粒来不及长大,可获得超细晶粒的组织,而使材料表层具有较高的强硬性和耐磨性。
适合于碳钢、中碳低合金钢、铸铁等材料的表面强化。
2电子束表面熔凝:
用高能量密度的电子束轰击工件表面,使表面产生局部