数控铣床毕业论文设计曲振文档格式.docx
《数控铣床毕业论文设计曲振文档格式.docx》由会员分享,可在线阅读,更多相关《数控铣床毕业论文设计曲振文档格式.docx(17页珍藏版)》请在冰豆网上搜索。
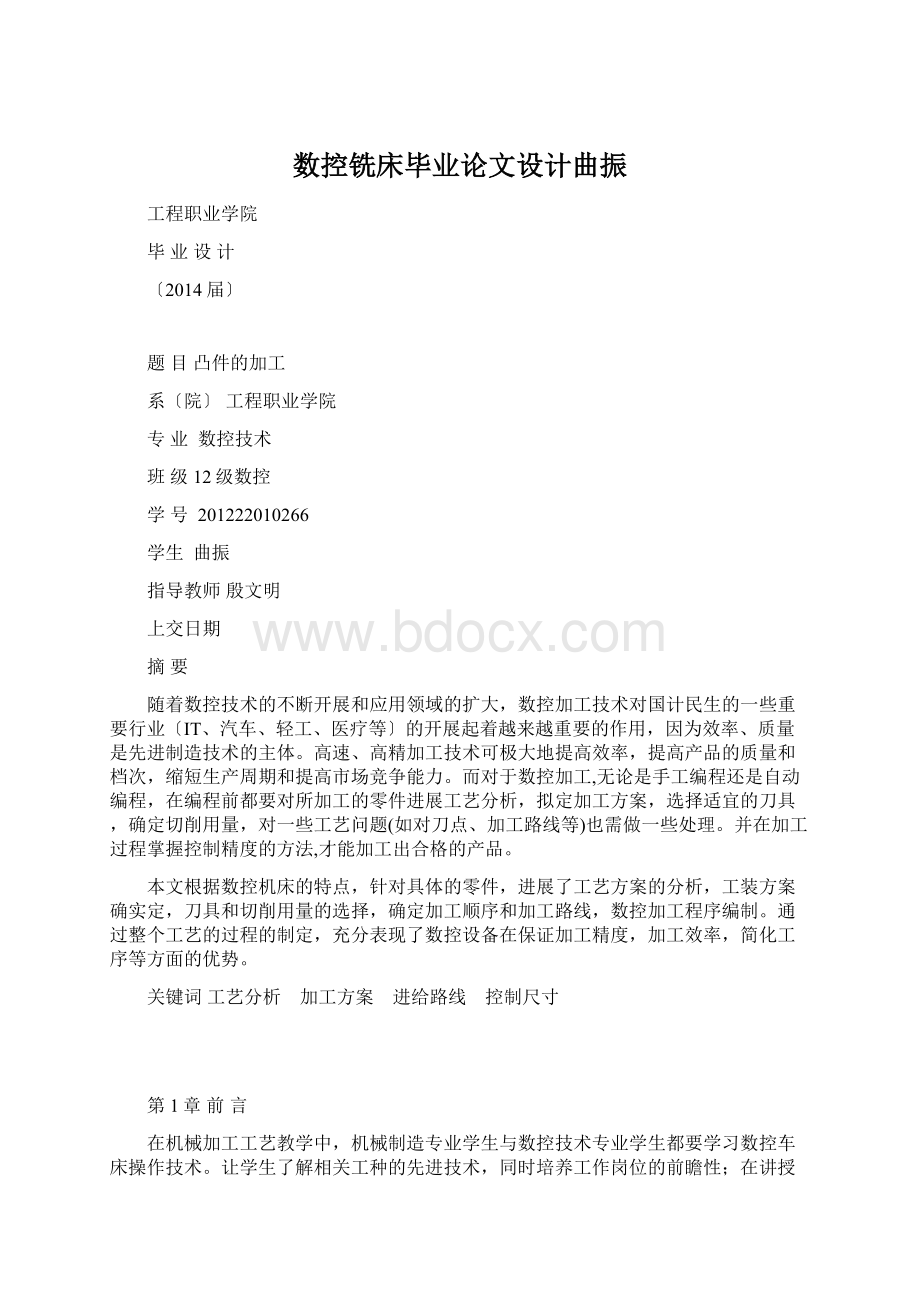
而对于数控加工,无论是手工编程还是自动编程,在编程前都要对所加工的零件进展工艺分析,拟定加工方案,选择适宜的刀具,确定切削用量,对一些工艺问题(如对刀点、加工路线等)也需做一些处理。
并在加工过程掌握控制精度的方法,才能加工出合格的产品。
本文根据数控机床的特点,针对具体的零件,进展了工艺方案的分析,工装方案确实定,刀具和切削用量的选择,确定加工顺序和加工路线,数控加工程序编制。
通过整个工艺的过程的制定,充分表现了数控设备在保证加工精度,加工效率,简化工序等方面的优势。
关键词工艺分析 加工方案 进给路线 控制尺寸
第1章前言
在机械加工工艺教学中,机械制造专业学生与数控技术专业学生都要学习数控车床操作技术。
让学生了解相关工种的先进技术,同时培养工作岗位的前瞻性;
在讲授数控知识的同时,必须要求学生掌握根本的机械加工工艺,增强系统意识,理解手动操作与自动操作之间的联系,真正把学生培养成为适应各种工作环境和岗位的多面手。
数控车工根底工艺理论与技能有机融合,包括夹具的使用、量具的识读和使用、刃具的刃磨与使用、基准定位等,分类表示了车床操作、数控车床自动编程仿真操作、数控车床编程与操作的初、中级容。
以机械加工中车工工艺学与数控车床技能训练密切结合为主线,常用量具识读与工件测量、刀具与安装、工件定位与安装、金属切削过程与精加工,较清晰地展示了数控车工必须掌握的知识和技能的训练途径。
对涉与与数控专业相关的根底知识、专业计算,都进展了有针对性的论述,目的在于塑造理论充实、技能扎实的专业技能型人才。
本文以与切削用量的选择,工件的定位装夹,加工顺序和典型零件为例,结合数控加工的特点,分别进展工艺方案分析,机床的选择,刀具加工路线确实定,数控程序的编制,最终形成可以指导生产的工艺文件。
在整个工艺过程的设计过程中,要通过分析,确定最优的工艺方案,使得零件的加工本钱最低,合理的选用定位夹紧方式,使得零件加工方便、定位精准、刚性好,合理选用刀具和切削参数,使得零件的加工在保证零件精度的情况下,加工效率最高、刀具消耗最低。
最终形成的工艺文件要完整,并能指导实际生产。
第2章工艺方案分析
2.1零件图
凸件
备件编号
技术要求
1去除毛刺尖角倒钝
3无热处理和硬度要求
4五边形尺寸自定义
2.2零件图分析
该零件外表由五边形、倒角四边形、四个盲孔、一个圆槽等外表组成。
尺寸标注完整,选用毛坯为45锻件96mm×
96mm,无热处理和硬度要求。
2.3确定加工方法
加工方法的选择原如此是保证加工外表的加工精度和外表粗糙度的要求。
由于获得同一级精度与外表粗糙度的加工方法一般有许多,因而在实际选择时,要结合零件的形状、尺寸大小和形位公差要求等全面考虑。
通过以上图形数据分析,考虑加工的效率和加工的经济性,最理想的加工方式为铣削,采用数控铣床。
2.4确定加工方案
零件上比拟精细外表的加工,铣床常常是通过粗加工、精加工逐步达到的。
对这些外表仅仅根据质量要求选择相应的最终加工方法是不够的,还应正确地确定从毛坯到最终成形的加工方案。
用虎钳夹住底部,开粗到96mmX96mm高50mm的尺寸,加工外表,加工96mmx96mm四边形外形,加工90mmX90mm外形,加工五边形,加工槽,加工盲孔
该凸件加工顺序为:
预备加工---开粗96mmX96mm高50mm---铣面---粗铣96mmX96mm轮廓---粗铣五边形---粗铣槽---精铣床96mmX96mm轮廓---粗铣90mmX90mm轮廓---精铣五边形轮廓---精铣槽---钻盲孔。
第3章工件的装夹
3.1定位基准的选择
在制定零件加工的工艺规程时,正确地选择工件的定位基准有着十分重要的意义。
定位基准选择的好坏,不仅影响零件加工的位置精度,而且对零件各外表的加工顺序也有很大的影响。
合理选择定位基准是保证零件加工精度的前提,还能简化加工工序,提高加工效率。
3.2 定位基准选择的原如此
1〕基准重合原如此。
为了防止基准不重合误差,方便编程,应选用工序基准作为定位基准,尽量使工序基准、定位基准、编程原点三者统一。
2〕便于装夹的原如此。
所选择的定位基准应能保证定位准确、可靠,定位、夹紧机构简单、易操作,敞开性好,能够加工尽可能多的外表。
3.3 确定零件的定位基准
以底面为定位基准
装夹方式的选择
为了工件不致于在切削力的作用下发生位移,使其在加工过程始终保持正确的位置,需将工件压紧夹牢。
合理的选择夹紧方式十分重要,工件的装夹不仅影响加工质量,而且对生产率,加工本钱与操作安全都有直接影响。
数控铣床常用的装夹方式
采用虎钳装夹,因为虎钳滑动面与底面,经过精细研磨,平行度精准,虎钳本体使用球墨铸铁FCD60制造,抗力强,耐磨性高,不易变形。
虎钳滑动面热处理HRC45°
以上,保持长久耐磨精度最适合于普通铣床,C数控铣床,机械加工,模具制造业使用。
3.6确定合理的装夹方式
本次采用的是一次性装夹,用虎钳夹住20mm-30mm,合理的控制自由度。
第4章刀具与切削用量
4.1选择数控刀具的原如此
刀具寿命与切削用量有密切关系。
在制定切削用量时,应首先选择合理的刀具寿命,而合理的刀具寿命如此应根据优化的目标而定。
一般分最高生产率刀具寿命和最低本钱刀具寿命两种,前者根据单件工时最少的目标确定,后者根据工序本钱最低的目标确定。
选择刀具寿命时可考虑如下几点根据刀具复杂程度、制造和磨刀本钱来选择。
复杂和精度高的刀具寿命应选得比单刃刀具高些。
对于机夹可转位刀具,由于换刀时间短,为了充分发挥其切削性能,提高生产效率,刀具寿命可选得低些,一般取15-30min。
对于装刀、换刀和调刀比拟复杂的多刀机床、组合机床与自动化加工刀具,刀具寿命应选得高些,尤应保证刀具可靠性。
车间某一工序的生产率限制了整个车间的生产率的提高时,该工序的刀具寿命要选得低些当某工序单位时间所分担到的全厂开支M较大时,刀具寿命也应选得低些。
大件精加工时,为保证至少完成一次走刀,防止切削时中途换刀,刀具寿命应按零件精度和外表粗糙度来确定。
与普通机床加工方法相比,数控加工对刀具提出了更高的要求,不仅需要冈牲好、精度高,而且要求尺寸稳定,耐用度高,断和排性能坛同时要求安装调整方便,这样来满足数控机床高效率的要求。
数控机床上所选用的刀具常采用适应高速切削的刀具材料(如高速钢、超细粒度硬质合金)并使用可转位刀片。
4.2选择数控铣削用刀具
本次铣削采用机架刀与钨钢到配合使用,这样能提高效率。
4.3设置刀点和换刀点
铣床一般采用的是中心对刀,以工件正100mm处作为换刀点
4.4确定切削用量
数控编程时,编程人员必须确定每道工序的切削用量,并以指令的形式写人程序中。
切削用量包括主轴转速、背吃刀量与进给速度等。
对于不同的加工方法,需要选用不同的切削用量。
切削用量的选择原如此是:
保证零件加工精度和外表粗糙度,充分发挥刀具切削性能,保证合理的刀具耐用度,并充分发挥机床的性能,最大限度提高生产率,降低本钱。
第5章零件的加工
5.1凸件的工艺分析
(1)技术要求图为一个凸件,精度要求不高,只有外表粗糙度有要求,还有就是槽必须保证在正负0.02之间,其余精度为自由公差
(2)毛坯选择本次的毛坯选用100mmX100mm高55的45锻件作为毛坯,比图片尺寸稍大一点,这样以便于更好的报图片的要求
(3)定位基准选择在铣床上面一般以一个面作为定位基准,本次图形我们采用的是把底面作为定位基准。
(4)热处理工序铸、锻件毛坯在粗车前应根据材质和技术要求安排正火火退火处理,以消除应力,改善组织和切削性能。
性能要求较高的毛坯在粗加工后、精加工前应安排调质处理,以提高零件的综合机械性能;
对于硬度和耐磨性要求不高的零件,调质也常作为最终热处理。
相对运动的外表需在精加工前或后进展外表淬火处理或进展化学热处理,以提高其耐磨性。
加工工序的划分一般可按如下方法进展:
①刀具集中分序法就是按所用刀具划分工序,用同一把刀具加工完零件上所有可以完成的部位。
再用第二把刀、第三把完成它们可以完成的其它部位。
这样可减少换刀次数,压缩空程时间,减少不必要的定位误差。
②以加工部位分序法对于加工容很多的零件,可按其结构特点将加工局局部成几个局部,如形、外形、曲面或平面等。
一般先加工平面、定位面,后加工孔;
先加工简单的几何形状,再加工复杂的几何形状;
先加工精度较低的部位,再加工精度要求较高的部位。
③以粗、精加工分序法对于易发生加工变形的零件,由于粗加工后可能发生的变形而需要进展校形,故一般来说凡要进展粗、精加工的都要将工序分开。
综上所述,在划分工序时,一定要视零件的结构与工艺性,机床的功能,零件数控加工容的多少,安装次数与本单位生产组织状况灵活掌握。
另建议采用工序集中的原如此还是采用工序分散的原如此,要根据实际情况来确定,但一定力求合理。
(5)走刀路线和对刀点选择走刀路线包括切削加工轨迹,刀具运动到切削起始点、刀具切入、切出并返回切削起始点或对刀点等非切削空行程轨迹。
由于半精加工和精加工的走刀路线是沿其零件轮廓顺序进展的,所以确定走刀路线主要在于规划好粗加工与空行程的走刀路线。
合理确定对刀点,对刀点可以设在被加工零件上,但注意对刀点必须是基准位或已精加工过的部位,有时在第一道工序后对刀点被加工毁坏,会导致第二道工序和之后的对刀点无从查找,因此在第一道工序对刀时注意要在与定位基准有相对固定尺寸关系的地方设立一个相对对刀位置,这样可以根据它们之间的相对位置关系找回原对刀点。
这个相对对对刀位置通常设在机床工作台或夹具上
5.2凸件加工工艺
〔1〕确定加工顺序与进给路线
加工顺序按粗到精、由近到远的原如此确定。
工是一个凸件,所以对其进展外形的排料粗加工〔留0.5的加工余量〕让后对槽进展粗加工,最后,精加工外形、精加工槽、钻孔。
(2)选择刀具
1〕整体开粗选用φ80的面铣刀进展开粗
2〕铣外形粗加工选用φ16的硬质合金机夹刀进展外形的开粗
3)槽的粗铣选用φ10的硬质合金到进展开粗
4)外形与槽的精加工选用φ10的硬质合金到进展精加工
5)盲孔的加工选用φ10的麻花钻进展加工
〔3〕选择切削用量
工序容〔走刀路线〕
工序号
工序名称
切削用量
设备
T刀具
转速r/min
进给速度mm/r
背吃刀量mm
1
铣床
整体开粗
Φ80盘铣刀
400
20%
2
外形开粗
Φ16机夹刀
2000
3
槽开粗
Φ10硬质合金刀
1600
4
外形精加工
1700
5
槽精加工
6
钻孔
Φ10的麻花钻
800
本次加工我选用的是华中铣床
(1