高速线材工艺技术操作要求示例Word下载.docx
《高速线材工艺技术操作要求示例Word下载.docx》由会员分享,可在线阅读,更多相关《高速线材工艺技术操作要求示例Word下载.docx(10页珍藏版)》请在冰豆网上搜索。
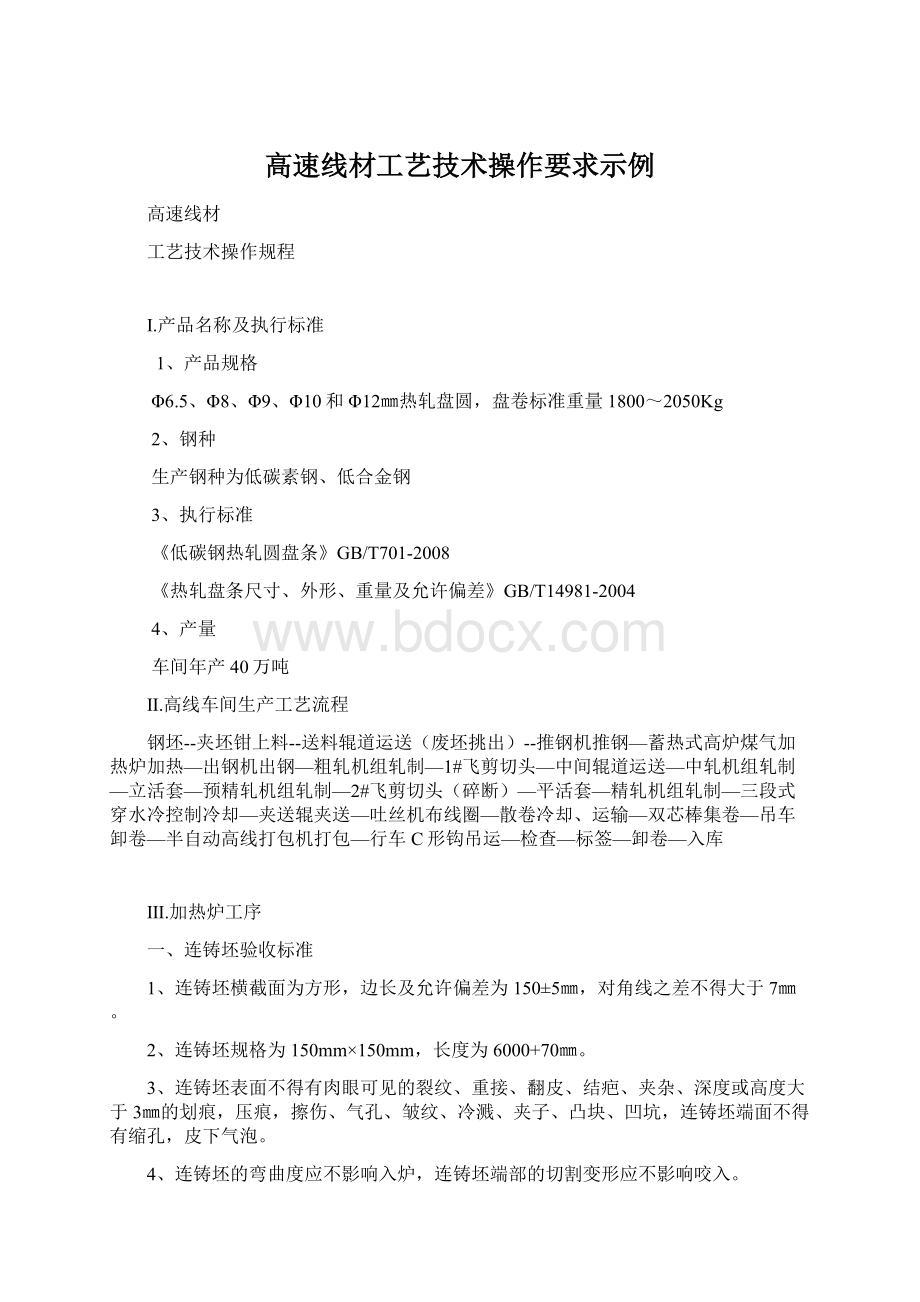
Ⅲ.加热炉工序
一、连铸坯验收标准
1、连铸坯横截面为方形,边长及允许偏差为150±
5㎜,对角线之差不得大于7㎜。
2、连铸坯规格为150mm×
150mm,长度为6000+70㎜。
3、连铸坯表面不得有肉眼可见的裂纹、重接、翻皮、结疤、夹杂、深度或高度大于3㎜的划痕,压痕,擦伤、气孔、皱纹、冷溅、夹子、凸块、凹坑,连铸坯端面不得有缩孔,皮下气泡。
4、连铸坯的弯曲度应不影响入炉,连铸坯端部的切割变形应不影响咬入。
5、连铸坯的化学成分应符合现行国家标准或内控标准规定。
6、连铸坯的其它技术要求执行YB2011-83《连铸方坯和矩形坯》现行标准。
二、钢坯入炉规程
1、操作人员提前15分钟到岗,了解上班的投料,卸车等情况,检查吊具是否完好,确认安全后方可使用。
2、钢坯到原料场后,应先检查《按炉送钢卡片》与钢坯的炉号,钢号(涂色标识),支数是否相符,钢坯的表面质量,弯曲度,定尺长度等质量要求,按连铸坯验收技术标准检查验收,验收合格后,方可装料。
3、验收时发现物卡不符,标识不清或连铸坯质量不符合标准要求时不得装料应另行堆放,同时通知工段长与质检直接联系。
4、钢坯投料前应根据《按炉送钢卡片》核对入炉连铸坯的炉号,支数及表面质量,并按批号顺序入炉。
5、在送料辊道上,将不合格坯挑出,吊至指定地点,并在不合格坯上标明钢号,炉号同时做好记录。
6、换批号时,两批号之间要有明显的标识(耐火砖),标识放在批号的首支坯上。
7、更换品种时要有调度指令,并及时向调度汇报更换品种的准确时间。
8、对于退回的回炉坯应标写炉号后放到回炉区,并及时与质检员联系组批。
9、上料操作与质检工应紧密配合,杜绝混炉、混号事故发生。
10、推钢操作当听到要钢铃声应立即推钢。
11、推钢时应将钢坯摆放在纵滑道正中,推钢过程中要密切观察炉内钢坯运行情况,当发现钢坯推斜,拱钢时要及时处理。
12、根据钢坯定尺长度调整入炉挡板。
三、加热炉操作规程
1、加热炉开炉时首先要检查炉体,烟道,冷却水系统,供风系统,煤气管路,汽化冷却系统,确认符合要求后,才允许点火升温。
2、加热炉点火前首先开启煤气盲板阀和煤气点火阀,然后打开点火烧嘴的嘴前空气调节阀后打开点火嘴前的嘴前煤气调节阀,点燃该点火烧嘴。
3、所有点火烧嘴稳定燃烧后,按需要进行烘炉或升温。
4、当炉温升到600℃左右时,启动换向程序,依次点燃蓄热箱烧嘴。
5、加热炉在加热钢坯时,要根据炉温情况,认真执行“勤观察,勤联系,勤调整”的“三勤”操作,及时调整空燃比及烟道闸板,严禁钢坯发生粘钢,脱碳等事故,出炉钢坯应符合开轧温度的要求,并掌握好出钢速度。
6、温度制度见表2
(表2)单位:
℃
均热段
加热段
预热段
1150~1200
1150~1250
≤750
7、保持微正压操作,以出钢口炉门微冒火为宜。
8、钢坯加热要均匀,同支钢坯温差不能超过50℃。
9、煤气分上、下供热,控温工可通过控制各种阀门对加热段,均热段分段调节。
四、钢坯出炉操作规程
1、炉内钢坯温度,符合轧制工艺要求时,方可出钢,发现钢坯温度低或温差大应通知控温工。
2、根据出钢信号,每次推出一支,严禁推偏和带出钢坯。
3、出钢速度应视轧制节奏,均衡出钢,出炉待轧钢坯不得超过一支。
4、当听到故障信号时,应停止出钢。
五、加热炉维护规程
1、烘炉时必须按烘炉曲线制度进行,以防损坏炉子。
2、炉子检修时,应将烟道闸板,炉门打开缓慢降温,严禁向炉底,炉墙,炉顶打水进行强制冷却。
3、不允许炉子超高温操作,炉温控制在1350℃以下。
4、随时检查堵塞砌体的冒火部分,确保钢结构处于完好状态。
5、炉子保温时,应放下炉门。
6、检查各水冷件水量是否充足,畅通,且使水温保持在60℃以下。
7、在检修,换辊等停产情况下,应调节供气压力,保证炉温不低于750℃。
8、要保持炉区周围卫生,严禁将油等易燃物品放置到炉体周围。
9、当炉温降到室温时,方可关闭冷却水。
10、冬季停炉时要排除管内积水,防止冻裂。
11、要按时清除均热床(实坑)下的氧化铁皮。
六、热送热装加热制度
1、冷热交替
先冷坯后热坯装炉时,视加热炉各段情况,即从均热段到加热段,依次减少烧嘴煤气流量或关闭加热段部分烧嘴,以增加预段长度。
2、热装
热坯装炉时,炉子需加强动态管理,视热坯温度的差别,炉内气氛及仪表显示数据对炉子的煤气量,空气量进行调整,严防粘钢和过烧。
3、热冷交替
先热坯后冷坯装炉时,从均热段到加热段依次增加烧嘴煤气流量,直到冷热交替完毕,为了杜绝热冷交替时热坯易过热,过烧及冷坯烧不透问题,采用保证热坯加热速度方法,待热坯出完均为冷坯时,将坯在炉内待温10~30分钟再出炉开轧。
Ⅳ.轧制工序
一、轧机换辊、倒槽操作规程
粗轧七连轧机的倒槽操作
1、松开或拆除导卫后,调整好新轧槽的尺寸,包括轴向和径向调整,必要时用样板检验。
2、换上合格的进出口导卫装置,按要求对正孔型并紧固。
3、新槽开轧时,关闭冷却水,待轧件头部咬入后,再送足冷却水。
粗轧七连轧的换辊操作
A、拆辊——将需要更换的辊系从轧机机架中移出。
1、将进出口导卫松开,平放于横梁上,位置以不影响辊系运行为准。
2、将轧机固定斜铁打下。
3、将万向接轴轴头与轧辊扁头的连接退出。
4、用吊具将辊系吊走,拆卸结束。
B、装辊——将预装或检修好的辊系装入机架中。
1、将预装或检修好的辊系吊放在机架上,轧辊的传动端扁头应处于特定的换辊位置。
2、紧固好轧机固定斜铁。
3、连接万向接轴与轧辊传动端扁头。
4、装辊结束后,进行导卫安装、调整、紧固。
中轧机更换轧机及倒槽技术操作规程
1、中轧机列导槽与换辊的步骤与粗轧机列相同。
2、集体传动的机组要按配辊要求更换。
以确保连轧关系不被破坏。
3、更换轧机时,要先把轧机传动端与连接轴松开,然后松开轧机固定斜铁,之后把轧机吊放在现场指定地点,再把预装好的新轧机吊到相应的轧机底座上。
4、换好轧机以后,要先紧固轧机,使轧机固定,然后按工艺要求调平辊缝,对过孔型后,再安装并紧固导卫。
5、更换下来的轧机要吊运到预装组。
6、各机组倒孔型时,为确保轧制线的一致,必须使一个机组的两架轧机同时倒孔型,机组之间尽量使轧制线一致。
7、倒完孔型后要试小料,试小料前要先磨孔型,试小料时先不开冷却水,待试小料成功后再开冷却水。
预精轧、精轧、夹送辊辊环装配
1、预精轧、精轧、夹送辊辊环装配必须由专人负责、未经培训不允许对辊环进行装配。
2、辊环装配前必须对辊环、锥套、轧辊轴三者接触面进行认真的清洗、研磨,确保三者装配后接触面在80%以上。
3、锥套打压时,打紧压力在16~20Mpa。
4、锥套必须定期更换,正常情况下,锥套使用周期为10次。
5、冬季装配时须将辊环加温至25~30℃。
6、应时刻检查冷却水是否充足。
二、轧机的调整
粗轧机的调整
1、在轧机停稳之前,严禁检查转动部位及更换检查导卫。
2、开机5—10分钟,再次检查琐紧装置和进固件,确认无隐患后,方可过钢。
3、各架轧机的孔型中心线应在同一轧制中心线上,偏差不得大于1㎜。
4、严格控制开轧温度,开轧温度为1050~1150℃。
5、严禁轧制黑头钢,阴阳面太大的钢,夹生钢及局部黑印严重的钢坯。
6、严格按照轧制图表的要求调整尺寸,做到及时倒槽换辊或换导卫。
7、正常轧制过程中,要经常检查冷却水的供应情况,以确保孔型和导卫的冷却效果。
8、正常轧制过程中,要经常检查钢的轧制情况,发现问题要及时调整轧机或换槽换辊。
9、机架间保持微张力轧制,发现异常情况及时做出判断,并调整相关的要素。
10、处理事故时,要保护轧槽和导卫装置。
11、处理完故障后,要认真检查各工艺装置是否恢复原位,轧制线是否有异物,确认无误后,方可要钢。
12、导卫装置要正确安装,保证水平线及轧制中心线一致,出口导卫要紧帖轧辊。
并紧固压紧导卫紧固件,进口导卫及出口盒的紧固件必须紧死。
13、使用的导卫经检查合格后方可使用。
中轧机的调整
1、在轧机停稳之前严禁检查转动部位及更换检查导卫。
2、调整轧机必须按轧制图表调整,以确保各道次的实料尺
寸。
3、轴向调整应保证每组轧机的各架轧槽在一条直线上,即
对正轧制线,并以光源透光检查。
4、接班检查开车后,要先试小料,确认连轧关系调整好以后,方可开轧。
5、在正常轧制过程中,要经常观察钢的轧制情况,发现问题及时调整轧机或更换导卫。
6、要随时观察冷却水的使用情况,保证孔型及导卫的冷却水的充足供应。
7、严禁贴辊轧制。
8、每架轧机的实料,必须严格按轧制图表给定的公差尺寸来调整。
9、严格控制各道次红坯尺寸,做到及时换辊或倒槽。
10、导卫装置要正确安装,保持水平。
入口导板要与轧槽保持2~3㎜的距离,并低于轧槽2~3㎜,出口管则要与轧槽紧贴,对正孔型,并低于轧槽2~4㎜。
11、各轧机的转速及实料的调整原则是保证最小的拉钢值,并要严格控制中轧末架出料尺寸。
12、轧槽缺水时严禁轧钢,如发现冷却水中断,应立即停止轧钢,待轧槽冷却后(以不烫手为准),送上冷却水后,方可轧钢,绝对不允许用冷却水浇发红的轧槽,以防发生炸裂轧槽或断辊事故。
13、为防止发生断辊事故,并保证产品质量,防止其它事故的发生,严禁轧制冷头钢,低温钢和黑钢。
14、为减少金属消耗,飞剪切头应控制在1#剪100~150㎜;
2#剪200~250㎜之间。
15、轧制过程中如果发现炸槽影响产品质量的情况,应立即倒孔型。
三、轧制图表(见附表)
四、样板的制作,使用,保管,修改规程
A、样板的制作规程
1、样板应线切割样板工制作,样板包括孔型样板,划线样板,砂轮修磨样板,检验样板。
2、样板应按技术部门提供的图纸进行。
3、公、母样板相互对在一起时,两者对合部位均应达密合,其间隙不得超过0.02㎜。
4、制作样板的钢板材质为中碳钢材质为中碳钢和结构钢,孔型检验样板用1.5~2㎜钢板制作。
5、样板表示符号在加工前按要求刻印好,不许在加工后刻印,以防变形。
6、样板做完后,必须经过三级检验,(自检,设计人员检验,质检人员检验)完全合格后,方可送交使用。
7、样板制作要“公”、“母”样板一次成套制作。
B、样板的保管
1、检验合格的样板应成套地由专人负责妥善保管。
2、建立样板管理办法,对样板的制作,使用,修复,修改跟踪记录。
3、使用过后的样板暂不使用时交回有关技术部门,经检验后,说明该样板“可再用”、“修复”或“报废”,报废的样板应及时补充。
C、样板的使用
1、根据工作指令,车工组负责人到保管处领用样板。
2、样板使用者在使用样板前应