年产量65万吨高速线材车间设计工艺设计剖析Word文档格式.docx
《年产量65万吨高速线材车间设计工艺设计剖析Word文档格式.docx》由会员分享,可在线阅读,更多相关《年产量65万吨高速线材车间设计工艺设计剖析Word文档格式.docx(9页珍藏版)》请在冰豆网上搜索。
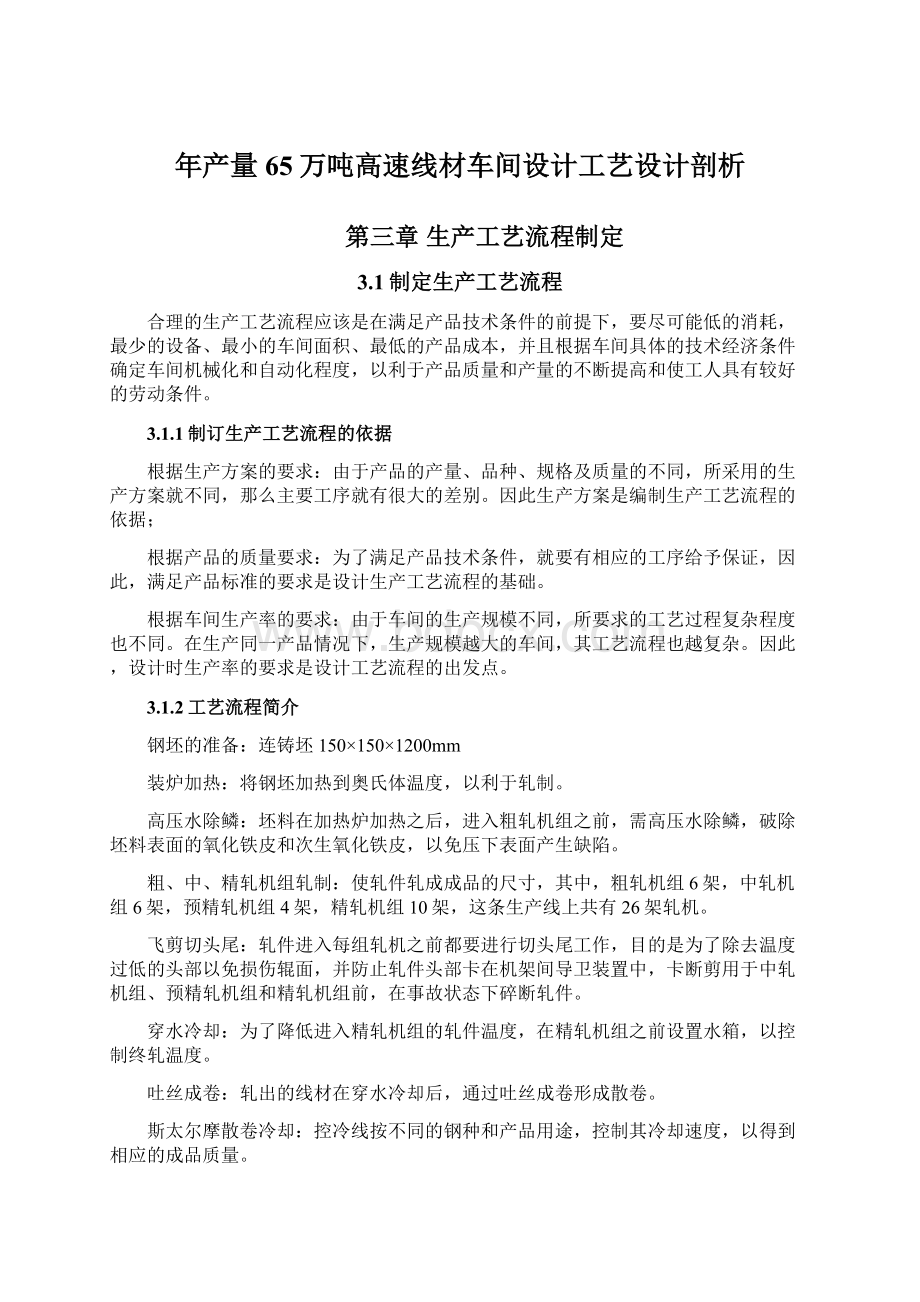
高压水除鳞:
坯料在加热炉加热之后,进入粗轧机组之前,需高压水除鳞,破除坯料表面的氧化铁皮和次生氧化铁皮,以免压下表面产生缺陷。
粗、中、精轧机组轧制:
使轧件轧成成品的尺寸,其中,粗轧机组6架,中轧机组6架,预精轧机组4架,精轧机组10架,这条生产线上共有26架轧机。
飞剪切头尾:
轧件进入每组轧机之前都要进行切头尾工作,目的是为了除去温度过低的头部以免损伤辊面,并防止轧件头部卡在机架间导卫装置中,卡断剪用于中轧机组、预精轧机组和精轧机组前,在事故状态下碎断轧件。
穿水冷却:
为了降低进入精轧机组的轧件温度,在精轧机组之前设置水箱,以控制终轧温度。
吐丝成卷:
轧出的线材在穿水冷却后,通过吐丝成卷形成散卷。
斯太尔摩散卷冷却:
控冷线按不同的钢种和产品用途,控制其冷却速度,以得到相应的成品质量。
精整与运输:
包括集卷、修整、检查、取样、捆轧、称重挂标牌,用集卷装置收集散卷,并将其挂到P-S运输线上的C形钩上,依次完成集卷、修整、检查、取样、捆轧、称重挂标牌等工序,之后卸卷入库。
3.2坯料选择
连铸坯是用钢水直接浇铸而成的。
连铸工艺与模铸开坯相比具有减少钢锭再加热的切头切尾、金属回收率高、能源消耗少、产品成本低、基建投资和生产费用少、劳动定员少、劳动条件好等一系列优点,使连铸坯成为轧钢生产的主要供坯方式。
3.2.1坯料规格
(1)连铸坯尺寸的边长和允许偏差:
连铸坯断面尺寸150×
150mm;
连铸坯长度12000mm
边长公差±
4mm;
对角线长度偏差≤6mm;
圆角半径R>8mm;
连铸坯单根重约为2.3t吨。
连铸方坯和矩形坯标准:
GB2011-98;
(2)钢坯标准长度为12000mm;
短尺钢坯最短长度为10000mm;
每批(炉)短尺钢坯重量不大于全部钢坯重量的10%。
(3)钢坯的弯曲度在12000mm内不大于100mm;
但不允许在钢坯两端,两端最大50mm.
(4)钢坯扭转在12000mm内为6°
.
(5)钢坯端部因剪切变形而造成的局部宽度不大于边长的10%.切头毛刺应清除.端部因剪切变形而造成的局部弯曲不得大于20mm.剪切端面应与钢坯长度方向轴线垂直;
端面弯斜量不得大于边长的6%.
3.2.2对连铸坯表面质量要求
(1)连铸坯表面缺陷最为常见的是表面氧化结疤和针孔。
严重时报废。
(2)严格控制冶炼及浇铸过程,消除表面缺陷,得到符合生产要求的连铸坯。
3.2.3对连铸坯内部质量要求
(1)减少连铸坯的偏析现象。
偏析是连铸坯的一个重要的质量问题,连铸坯尺寸越小则偏析越严重。
(2)控制中心偏析。
中心偏析是连铸小方坯的代表性缺陷。
其控制方法主要有:
1)扩大连铸坯尺寸。
2)严格控制钢水的过热度,防止产生严重的中心偏析。
3)降低钢种设计中的磷、锰、硫含量,以减少高碳钢盘条的中心偏析。
4)采用电磁搅拌技术,有助于减低固液界面与心部区域的温度梯度,从而减少合金成分的中心偏析。
(3)控制裂纹的产生。
3.3确定加热温度
钢的加热温度是指钢加热终了时出路的温度。
不同碳素钢的加热温度见表3-1.
表3-1不同碳钢的加热温度和过烧温度
钢种
加热温度/C°
过烧温度/C°
碳素钢1.5%C
1050
1140
碳素钢1.1%C
1080
1180
碳素钢0.9%C
1120
1220
碳素钢0.7%C
1280
碳素钢0.5%C
1250
1350
碳素钢0.2%C
1320
1470
碳素钢0.1%C
1490
每单位时间的板坯加热速率一般铸坯表面温度的上升速度,单位℃/h时,在实际生产中,钢坯的厚度被加热到所需的时间温度(min/cm)的每单位时间或加热一预定单元钢坯的厚度(cm/min)来表示。
由大小和传热条件加热炉的热负荷速度,钢坯尺寸和热扩散系数的大小的影响。
加热速度大时,炉内的全部加热容量可以是短的时间在炉中,钢坯的燃烧速率。
因此,在可能的条件和内部产生过大的温差,否则钢坯将会产生弯曲和由热应力引起的内裂。
碳素结构钢和低合金钢一般不限制加热速度,加热时间越短。
但大截面钢坯和高碳,高合金钢,必须控制升温速度,以免造成铸坯内部缺陷。
线材所用的中型钢坯在步进式加热炉中加热时,情况得到很大改善,步进式加热炉可以使钢坯得到全方位上的加热。
各钢种在步进式加热炉中平均加热速度的经验数据如表2
表3-2在步进式加热炉中各钢种的平均加热速度
低碳钢
低合金钢
高碳钢
高合金钢
平均加热速度/min/cm
6-9
9-12
12-18
18-24
3.4加热时间确定
加热时间指金属装炉后加热到加工要求温度所需要的时间。
加热时间同钢种、坯料尺寸与形状、坯料在炉中的方法、炉形结构及装炉温度等因素有关。
连续式加热炉:
式中T-加热时间,time
D-钢坯厚度或钢坯直径,cm
取T=2h
3.5钢材的冷却与精整
1、钢材的冷却
经热轧成形的钢材仍处在一个较高的温度范围,尚有800~900℃的温度,需要经过冷却使钢材温度降至常温。
由于钢在热轧后冷却到常温,钢材经历相变和再结晶的过程;
在应力作用下可能出现内部裂纹和外部裂纹,得采取缓冷等措施。
另外还可利用轧件扎后的余热进行控制冷却,以获得所需要的金相组织和力学性能,这就是钢材的冷却制度。
冷却方法分为自然冷却和控制冷却:
自然冷却是把轧后的钢材在冷床上自然冷却。
对组织及性能无特殊要求的钢材,可采用这种冷却方式。
控制冷却是把轧后的轧件进行冷却过程进行有目的人为控制,使产品达到预期的内部组织和力学性能。
2、其它精整工序
除了上述各工序外,精整内容还包括成品的热处理、各种涂层和表面精加工及成品检验等内容,成品的质量检验内容包括化学成分分析、低倍组织及显微组织、机械性能检验等。
第四章车间工艺设计
4.1确定轧机类型及布置形式
轧钢机是完成金属轧制变形的主要设备,是代表车间生产技术水平。
因此,选择的是否合理对车间生产具有非常重要的影响。
4.1.1轧钢机选择原则
轧钢机选择的主要依据是车间生产的钢材的钢种、产品品种和规格、生产规模的大小以及由此确定的产品生产工艺过程。
在选择轧钢机时一般要注意考虑下列原则;
(1)满足产品方案的前提下,使轧机组成合理,布置紧凑;
有较高的生产效率和设备利用系数;
有利于轧机机械化、自动化的实现,有助于工人劳动条件的改善;
(2保证获得质量良好的产品,并考虑到生产新产品的可能;
轧机结构型式先进合理,制造容易,操作简单,维修方便;
由于采用的生产方案就不同,所以产品的产量、品种、规格及质量的不同,那么主要工序就有很大差距。
因此生产方案是编制生产工艺流程的依据。
(1)生产规模大小
由于车间生产规模不同,所要求的工艺过程复杂程度也不同。
在同一生产产品情况下,生产规模越大的车间,其工艺过程也越复杂。
设计时生产率的要求是设计工艺过程的出发点。
(2)产品成本
成品是生产效果的综合反映,是各种因素影响的结果。
一般钢的加工工艺性能愈差,产品的技术要求愈高,其生产工艺过程就愈复杂,生产过程中金属、燃料、电力、劳动力等各种消耗也愈高,产品成本必然会相应提高。
反之,则产品成本下降。
工艺过程中采用的工序必须保证生产安全,不危及劳动者的身体健康,不造成环境污染。
否则,应采取妥善的防护措施。
选择轧钢机时除遵循上述的一般原则之外,要从产品的工艺要求出发,根据不同产品的生产特点和具体要求来确定轧机的结构型式、主要技术参数和它们的布置形式
4.1.2轧钢机类型
线材轧机多为二辊式,布置形式很多,主要有横列式、连续式、高速无扭整体式由于设计产量较高可采用45°
全程无扭轧机,例如美国摩根公司的高速无扭线材精轧机其特点是:
(1)工艺布置优化,全线18架轧机呈平立轧制交替布置,轧件在整个轧制过程中无扭转;
(2)高速轧制,成品轧机的最高轧制速度为120米/秒;
(3)引进新一代超重型V型轧机,轧机的功率、负荷、刚度都优于标准型轧机;
(4)产品的高化,可生产直径5.5~20毫米规格线材;
(5)产品盘重大,利用一锭一坯一成品,成品每盘单重达2.2吨;
(6)产品性能优质化,采用美国摩根公司最新开发的大风量斯太尔摩控制冷却设备,成品线材可以直接拉成高强度钢丝;
(7)自动控制系统数字化提高了轧制过程的控制精度、可靠性和易操作性。
轧机布置形式、轧机布置形式可采用摩根式45°
无扭整体机座的高速线材轧机为二辊式,辊轴中心线与水平成45°
角,而相邻轧辊轴线成90°
角交替配置,轧制中轧件没有扭转,轧机集体传动,一般简称为45°
无扭线材轧机。
4.1.3轧机数量的确定
本设计产品的最小规格为Φ5.5mm,故在确定轧机数目时,以最小直径Φ5.5坯料规格为150×
12000mm连铸坯计算得:
F0=150×
150=22500mm2
Fn=π(D/2)2=23.75mm2
上式中:
F0——连铸坯料原始面积
Fn——成品断面面积
则总延伸系数:
μz=F0/Fc=22500/23.75=947.3
取平均延伸系数:
μc=1.28
则轧机数:
N=㏑μz/㏑μc=27.61
取N=28
4.1.4轧机的组成
(1)粗轧机组的选择
粗轧机是使坯料得到初步的压缩和延伸,得到温度合适、断面形状正确、尺寸合格、表面质量良好、长度合适的工艺要求的轧件。
本设计选用6架平-立辊交替布置的二辊无牌坊式粗轧机组,采用上传动和下传动方式。
(2)中轧机组的选择
中轧机组的作用是继续缩减从粗轧机组的轧件断面,为精轧提供形状正确、尺寸精确的中间料为保证足够的压下量。
本设计采用6架平-立交替布置的、双支点、长辊身、多孔型无牌坊轧机。
(3)预精轧机组的选择
预精轧机组继续缩减从中轧机组轧出来的轧件断面,为后来的精轧机组轧机提供尺寸精确和形状正确的轧件。
本设计前两2选用无牌坊轧机,后4架选用悬臂轧机。
属于平-立悬臂式轧机交替配置。
(4)精轧机组的选择
高速线材轧机的精轧机组是最具特色的关键设备,它的水平决定整套线材轧机的水平。
在此基础上,产生了许多不同型式的高速机组,并各具特点,其中摩根高速无扭机组的优势更多一些,应用也更广泛些。
本设计采用精轧机组为10架,且均为摩根45°
悬臂式无扭轧机机组。
之所以选择悬臂式精轧机组,是因为悬臂式精轧机组不仅换辊、换槽方便,同时安装和调整也比较便利,而且结构比框架式简单、轧辊直径小,故而选用悬臂式而不用框架式。
悬臂式精轧机组由一台交流电机传动,轧辊布置形式为顶交45°
,相邻机架互成90°
。
4.2轧辊技术参数
表4-1轧辊计算参数
机架
轧辊最大直径(MM)
轧辊最小直径(MM)
轧辊长度(