毕业设计浮钳盘式制动器范文Word文档下载推荐.docx
《毕业设计浮钳盘式制动器范文Word文档下载推荐.docx》由会员分享,可在线阅读,更多相关《毕业设计浮钳盘式制动器范文Word文档下载推荐.docx(9页珍藏版)》请在冰豆网上搜索。
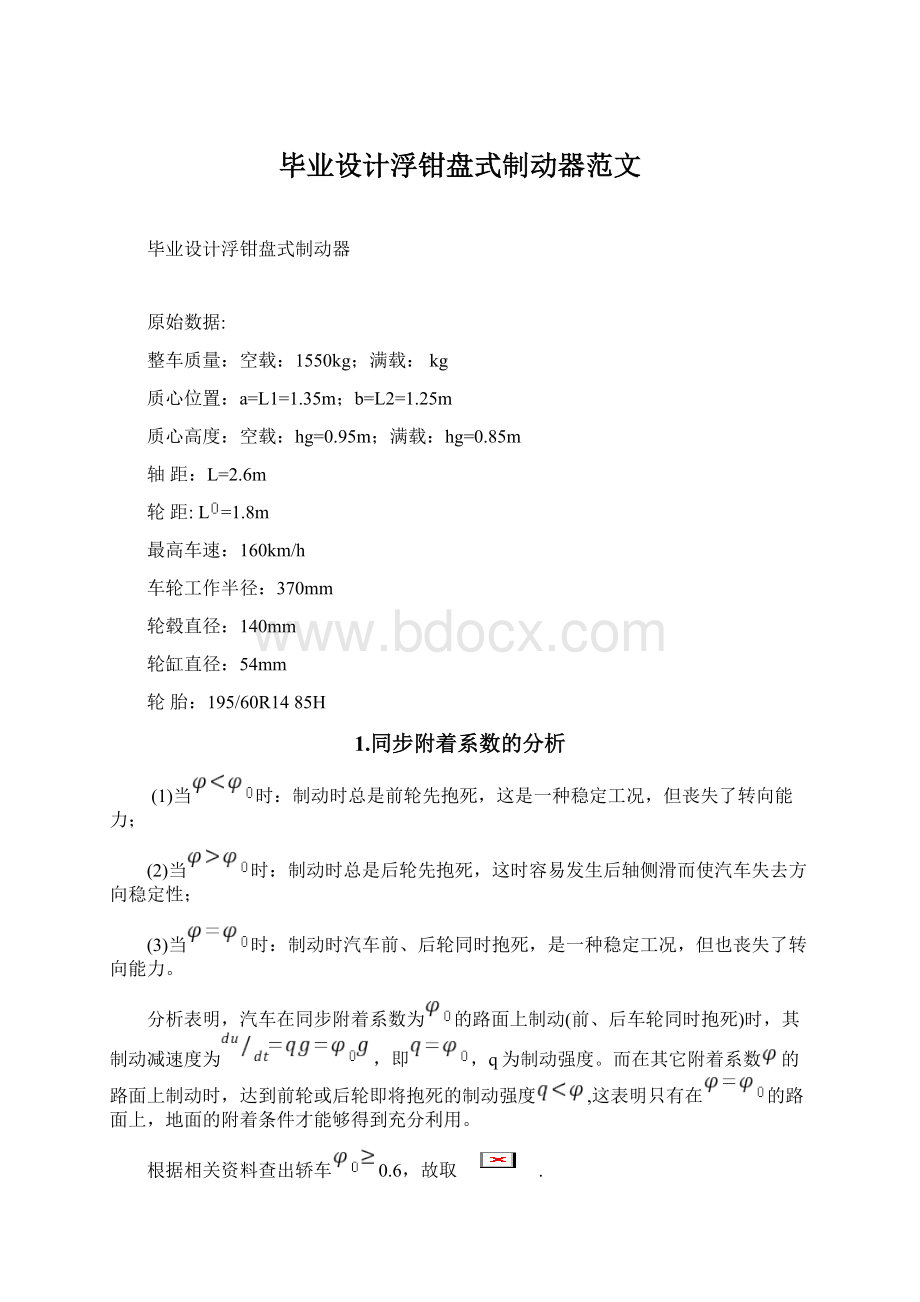
轮胎:
195/60R1485H
1.同步附着系数的分析
(1)当时:
制动时总是前轮先抱死,这是一种稳定工况,但丧失了转向能力;
(2)当时:
制动时总是后轮先抱死,这时容易发生后轴侧滑而使汽车失去方向稳定性;
(3)当时:
制动时汽车前、后轮同时抱死,是一种稳定工况,但也丧失了转向能力。
分析表明,汽车在同步附着系数为的路面上制动(前、后车轮同时抱死)时,其制动减速度为,即,q为制动强度。
而在其它附着系数的路面上制动时,达到前轮或后轮即将抱死的制动强度,这表明只有在的路面上,地面的附着条件才能够得到充分利用。
根据相关资料查出轿车0.6,故取.
同步附着系数:
0.6
2.确定前后轴制动力矩分配系数
常见前制动器制动力与汽车总制动力之比来表明分配的比例,称为制动器制动力分配系数,用表示,即:
,
式中,:
前制动器制动力;
:
后制动器制动力;
制动器总制动力。
由于已经确定同步附着系数,则分配系数可由下式得到:
根据公式:
得:
3.制动器制动力矩的确定
为了保证汽车有良好的制动效能,要求合理地确定前,后轮制动器的制动力矩。
根据汽车满载在沥青,混凝土路面上紧急制动到前轮抱死拖滑,计算出后轮制动器的最大制动力矩
由轮胎与路面附着系数所决定的前后轴最大附着力矩:
式中:
该车所能遇到的最大附着系数;
q:
制动强度;
:
车轮有效半径;
后轴最大制动力矩;
G:
汽车满载质量;
L:
汽车轴距;
其中q===0.66
故后轴==1.57Nmm
后轮的制动力矩为=0.785Nmm
前轴=T==0.67/(1-0.67)1.57=3.2Nmm
前轮的制动力矩为3.2/2=1.6Nmm
2.浮钳盘式制动器主要结构参数的确定
2.1制动盘直径D
制动盘直径D希望尽量大些,这时制动盘的有效半径得以增大,就能够降低制动钳的夹紧力,降低摩擦衬块的单位压力和工作温度。
但制动盘直径D受轮毅直径的限制一般,制动盘的直径D选择为轮毅直径的70%~90%,总质量大于2t的车辆应取其上限。
一般,制造商在保持有效的制动性能的情况下,尽可能将零件做的小些,轻些。
轮辋直径为14英寸(1英寸=2.54cm),又因为M=kg,取其上限。
在本设计中:
取D=256mm。
2.2制动盘厚度h
制动盘厚度h直接影响着制动盘质量和工作时的温升。
为使质量不致太大,制动盘厚度应取得适当小些;
为了降低制动工作时的温升,制动盘厚度又不宜过小。
制动盘能够制成实心的,而为了通风散热,能够在制动盘的两工作面之间铸出通风孔道。
通风的制动盘在两个制动表面之间铸有冷却叶片。
这种结构使制动盘铸件显著的增加了冷却面积。
车轮转动时,盘内扇形叶片的选择了空气循环,有效的冷却制动。
一般,实心制动盘厚度为l0mm~20mm,具有通风孔道的制动盘厚度取为20mm~50mm,但多采用20mm~30mm。
在本设计中选用通风式制动盘,h取20mm。
2.3摩擦衬块外半径R2与内半径R1
推荐摩擦衬块外半径R2与内半径R1的比值不大于1.5。
若比值偏大,工作时衬块的外缘与内侧圆周速度相差较多,磨损不均匀,接触面积减少,最终将导致制动力矩变化大。
在本设计中取外半径R2=104mm,,则内半径R1=80mm。
2.4摩擦衬块工作面积A
摩擦衬块单位面积占有的车辆质量在1.6kg/~3.5kg/范围内选取。
汽车空载质量为1550kg,前轮空载时地载荷为852.5kg,因此852.5/(3.5*4)<
A<
852.5/(1.6*4),即60.89<
110.7。
在本设计中取衬块的夹角为50°
。
摩擦衬块的工作面积A:
A取76㎝²
经过计算最终确定前轮制动器的参数如下:
制动盘直径D=256mm;
取制动盘厚度h=20mm;
摩擦衬片外半径R2=104mm,内半径=80mm;
制动衬块工作面积A=76cm2;
活塞直径=轮缸直径=54mm
3.制动效能分析
3.1制动减速度
制动系的作用效果,能够用最大制动减速度及最小制动距离来评价。
假设汽车是在水平的,坚硬的道路上行驶,而且不考虑路面附着条件,因此制动力是由制动器产生。
此时
式中——汽车前、后轮制动力矩的总合。
==785+1600=2385Nm
=370mm=0.37m
m——汽车总重m=kg
代入数据得=(785+1600)/0.37×
=6.16m/s
轿车制动减速度应在5.8~7m/s,因此符合要求。
3.2制动距离S
在匀减速度制动时,制动距离S为
S=1/3.6(t1+t2/2)V+V2/254
式中,t1——消除制动盘与衬块间隙时间,取0.1s
t2——制动力增长过程所需时间,取0.2s
V=30km/h
故S=1/3.6(0.1+0.2/2)30+30/254×
0.7=7.2m
轿车的最大制动距离为:
S=0.1V+V/150
S=0.130+30/150=9m
S<
S
因此符合要求。
3.3摩擦衬片的磨损特性计算
摩擦衬片的磨损与摩擦副的材质,表面加工情况、温度、压力以及相对滑磨速度等多种因素有关,因此在理论上要精确计算磨损性能是困难的。
但试验表明,摩擦表面的温度、压力、摩擦系数和表面状态等是影响磨损的重要因素。
汽车的制动过程,是将其机械能(动能、势能)的一部分转变为热量而耗散的过程。
在制动强度很大的紧急制动过程中,制动器几乎承担了耗散汽车全部动力的任务。
此时由于在短时间内制动摩擦产生的热量来不及逸散到大气中,致使制动器温度升高。
此即所谓制动器的能量负荷。
能量负荷愈大,则摩擦衬片(衬块)的磨损亦愈严重。
双轴汽车的单个前轮制动器的比能量耗散率为:
汽车回转质量换算系数,紧急制动时,;
汽车总质量;
,:
汽车制动初速度与终速度(/);
计算时轿车取27.8/;
制动时间,;
按下式计算
制动减速度,,;
前轮制动器衬片的摩擦面积;
=7600mm
制动力分配系数。
则=5.7
轿车盘式制动器的比能量耗散率应不大于6.0,故符合要求。
若摩擦衬片压力与制动盘面接触良好,且各处单位压力分布均匀,则在钳盘式制动器扇形摩擦衬面上任取一微小面积:
dA=RdRdθ,在这微小面积上产生的微摩擦力矩为:
dM=qRµ
dA=µ
qR²
dRdθ,式中q为摩擦片与制动盘之间的单位面积上的压力,µ
为摩擦片的摩擦系数,则单侧摩擦片作用于制动盘上的制动力矩为可由下式积分求得:
M'
=µ
pR²
dRdθ=θµ
dR=µ
p(R23-R13)(N.m)
则盘式制动器的总制动力矩为:
M=µ
q(R23-R13)
4.性能约束
(1)制动力矩约束:
汽车制动器制动力矩应该小于地面的摩擦力矩,否则会发生车轮抱死现象而产生侧滑,从而失去稳定性,即:
MG
路面附着系数;
G:
整车重量(N);
制动力分配系数;
车轮有效半径。
(2)摩擦片压力约束:
摩擦片应达到要求的耐磨性或使用寿命,对于摩擦片最大许用单位压力[P],一般按经验取值,因此,摩擦片单位面积压力不得超过许用单位压力[P],即:
<
[P]
(3)比能量耗散率约束:
如果比能量耗散率过高,不但会加快制动摩擦片的磨损,而且可能引起制动盘的龟裂,因此所施加的约束为:
[e](W/mm)
m:
整车质量(kg);
[e]:
盘式制动器时,取6.0W/mm;
T:
为制动时间。
(4)制动盘一次制动的温升:
△T=GV2/254C1M1[△t]
式中M1:
制动盘的质量(Kg)M1=,其中为制动盘的密度7900㎏/m3
C1:
制动盘的热容量J/(Kg·
K)对钢和铸铁取C=523J/(Kg.K);
V:
制动初速度(Km/h)取30Km/h
[△t]一次制动最大允许温升,一般不大于15℃即288.15K
(5)摩擦衬块面积:
由于摩擦衬块单位面积占有的车辆质量在1.6kg/~-3.5kg/范围内选取。
110.7于是6089<
11070。
(6)结构约束
1)D0.77Dh
2)R2+△lD/2
3)Dg/2+△2R1
4)1.27R2/Rl1.63
其中:
Dh:
轮辋直径(mm);
Dg:
轮毂直径(mm);
△1、△2:
分别为结构设计空间裕量(mm)。
浮钳盘式制动器主要部件结构的确定
制动盘
盘式制动器的制动盘有两个主要部分:
轮毂和制动表面。
轮毂是安装车轮的部位,内装有轴承。
制动表面是制动盘两侧的加工表面。
它被加工得很仔细,为制动摩擦块提供摩擦接触面。
整个制动盘一般由铸铁铸成。
铸铁能提供优良的摩擦面。
制动盘装车轮的一侧称为外侧,另一侧朝向车轮中心,称为内侧。
按轮毂结构分类,制动盘有两种常见型式。
带毂的制动盘有个整体式毂。
在这种结构中,轮毂与制动盘的其余部分铸成单体件。
另一种型式轮毂与盘侧制成两个独立件。
轮毂用轴承装到车轴上。
车论凸耳螺栓经过轮毂,再经过制动盘毂法兰配装。
这种型式制动盘称为无毂制动盘。
这种型式的优点是制动盘便宜些。
制动面磨损超过加工极限时能很容易更换。
本设计采用的是第二种型式。
制动盘一般用珠光体灰铸铁制成,或用添加Cr,Ni等的合金铸铁制成。
制动盘在工作时不但承受着制动块作用的法向力和切向力,而且承受着热负荷。
为了改进冷却效果,钳盘式制动器的制动盘有的铸成中间有径向通风槽的双层盘这样可大大地增加散热面积,降低温升约20%~30%,但盘的整体厚度较厚。
而一般不带通风槽的轿车制动盘,其厚度约在l0m~13mm之间。
本次设计采用的材料为HT250。
制动盘的工作表面应光洁平整,制造时应严格控制表面的跳动量,两侧表面的平行度(厚度差)及制动盘的不平衡量。
根据有关文献规定:
制动盘两侧表面不平行度不应大于0.008mm,盘的表面摆差不应大于0.1mm;
制动盘表面粗糙度不应大于0.06mm。
制动钳
制动钳由可锻铸铁KTH370-12或球墨铸铁QT400-18制造,也有用轻合金制造的,例如用铝合金压铸。
可做成整体的,也可做成两半并由螺栓连接。
其外缘留有开口,以便不必拆下制动钳便可检查或更换制动块。
制动钳体应有高的强度和刚度。
在钳体中加工出制动油缸。
为了减少传给制动液的热量,将活塞的开口端顶靠制动块的背板。
活塞由铸铝合金制造,为了提高耐磨损性能,活塞的工作表面进行镀铬处理。
为了解决因制动钳体由铝合金制造而减少传给制动液的热量的问题,应减小活塞与制动块背板的接触面积。
制动钳在汽车上的安装位置可在车轴的前方或后方。
制动钳位于车轴前可避免轮胎甩出来的泥,水进入制动钳,位于车轴后则可减小制动时轮毂轴承的合成载荷。
制动块
制动块由背板和摩擦衬块构成,两者直接牢固地压嵌或铆接或粘接在一起。
衬块多为扇面形,也有矩形、正方形或长圆形的。
活塞应能压住尽量多的制动块面积,以免衬块发生卷角而引起尖叫声。
制动块背板由钢板制成。
为了避免制动时产生的热量传给制动钳而引起制动液汽化和减小制动噪声,可在摩擦衬块与背板之间或在背板后粘(或喷涂)一层隔热减震垫。
由于单位压力大和工作温度高等原因,摩擦衬块的磨损较快,因此其厚度较大。
许多盘式制动器装有衬块磨损达极限时的警报装置,以便及时更换摩擦衬片。
摩擦材料
制动摩擦材料应具有高而稳定的摩擦系数,抗热衰退性能好,不能在温度升到某一数值后摩擦系数突然