射频溅射PPT课件下载推荐.ppt
《射频溅射PPT课件下载推荐.ppt》由会员分享,可在线阅读,更多相关《射频溅射PPT课件下载推荐.ppt(22页珍藏版)》请在冰豆网上搜索。
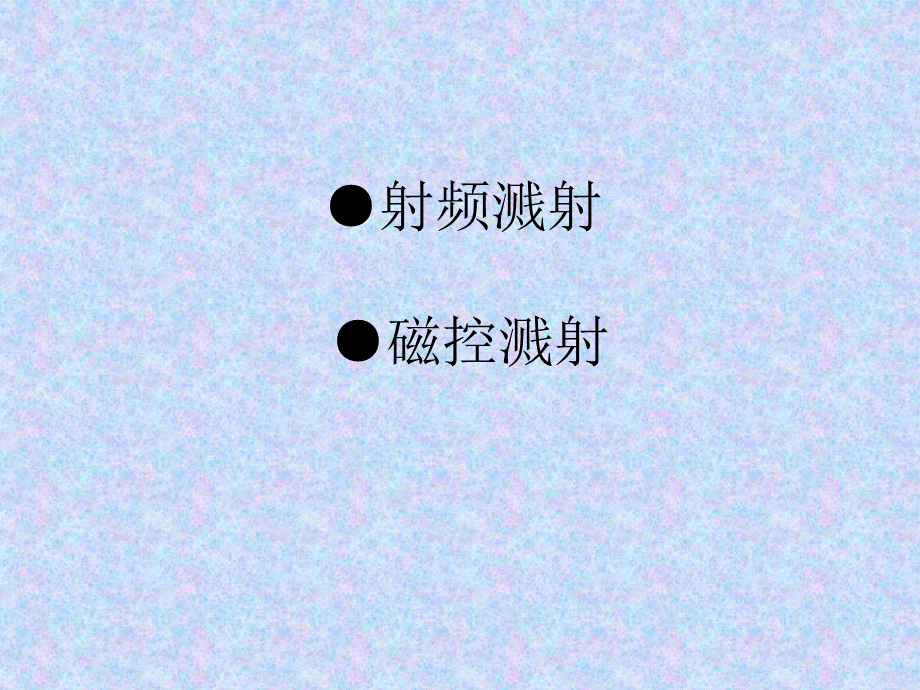
,两极间接上射频(530MHz,国际上多采用13.56MHz)电源后,两极间等离子体中不断振荡运动的电子从高频电场中获得足够的能量,并更有效地与气体分子发生碰撞,并使后者电离,产生大量的离子和电子,此时不再需要在高压下(10Pa左右)产生二次电子来维持放电过程,射频溅射可以在低压(1Pa左右)下进行,沉积速率也因此时气体散射少而较二极溅射为高;
高频电场可以经由其他阻抗形式耦合进入沉积室,而不必再要求电极一定要是导体;
由于射频方法可以在靶材上产生自偏压效应,即在射频电场作用的同时,靶材会自动处于一个较大的负电位下,从而导致气体离子对其产生自发的轰击和溅射,而在衬底上自偏压效应很小,气体离子对其产生的轰击和溅射可以忽略,主要是沉积过程。
射频溅射的基本原理,射频溅射装置示意图,射频电场对于靶材的自偏压效应:
由于电子的运动速度比离子的速度大得多,因而相对于等离子体来说,等离子体近旁的任何部位都处于负电位。
设想一个电极上开始并没有任何电荷积累。
在射频电压的驱动下,它既可作为阳极接受电子,又可作为阴极接受离子。
在一个正半周期中,电极将接受大量电子,并使其自身带有负电荷。
在紧接着的负半周期中,它又将接受少量运动速度较慢的离子,使其所带负电荷被中和一部分。
经过这样几个周期后,电极上将带有一定数量的负电荷而对等离子体呈现一定的负电位。
(此负电位对电子产生排斥作用,使电极此后接受的正负电荷数目相等)设等离子电位为Vp(为正值),则接地的真空室(包含衬底)电极(电位为0)对等离子的电位差为-Vp,设靶电极的电位为Vc(是一个负值),则靶电极相对于等离子体的电位差为Vc-Vp。
|Vc-Vp|幅值要远大于|-Vp|。
因此,这一较大的电位差使靶电极实际上处在一个负偏压之下,它驱使等离子体在加速后撞击靶电极,从而对靶材形成持续的溅射。
(1)射频溅射条件:
工作气压1.0Pa,溅射电压1000V,靶电流密度1.0mA/cm2,薄膜沉积速率低于0.5m/min。
(2)射频溅射法的特点能够产生自偏压效应,达到对靶材的轰击溅射,并沉积在衬底上;
自发产生负偏压的过程与所用靶材是否是导体无关。
但是,在靶材是金属导体的情况下,电源须经电容耦合至靶材,以隔绝电荷流通的路径,从而形成自偏压;
与直流溅射时的情况相比,射频溅射法由于可以将能量直接耦合给等离子体中的电子,因而其工作气压和对应的靶电压较低。
相对于蒸发沉积来说,一般的溅射沉积方法具有的两个缺点:
a、沉积速率较蒸发法低;
b、所需工作气压较高,否则电子的平均自由程太长,放电现象不易维持。
从而导致薄膜被污染的可能性较高。
磁控溅射法则因为其沉积速率较高(比其他溅射法高出一个数量级),工作气体压力较低而具有独特的优越性。
(1)磁控溅射的基本原理磁控溅射的基本原理,就是以磁场来改变电子的运动方向,并束缚和延长电子的运动轨迹,从而提高了电子对工作气体的电离几率和有效地利用了电子的能量。
因此,使正离子对靶材轰击所引起的靶材溅射更加有效。
同时,受正交电磁场束缚的电子,又只能在其能量要耗尽时才沉积在基片上。
这就是磁控溅射具有“低温”,“高速”两大特点的道理。
磁控溅射,磁控溅射设备简要模型:
电子在交互电场与磁场EB作用下将气体电离后撞击靶材表面,使靶材原子或分子等溅射出来并在管面经过吸附、凝结、表面扩散迁移、碰撞结合形成稳定晶核。
然后再通过吸附使晶核长大成小岛,岛长大后互相联结聚结,最后形成连续状薄膜。
磁控溅射的工作原理如上图所示;
电子在电场E作用下,在飞向基板过程中与氩原子发生碰撞,使其电离出Ar+和一个新的电子,电子飞向基片,Ar+在电场作用下加速飞向阴极靶,并以高能量轰击靶表面,使靶材发生溅射。
在溅射粒子中,中性的靶原子或分子则淀积在基片上形成薄膜。
二次电子el一旦离开靶面,就同时受到电场和磁场的作用。
为了便于说明电子的运动情况,可以近似认为:
二次电子在阴极暗区时,只受电场作用;
一旦进入负辉区就只受磁场作用。
于是,从靶面发出的二次电子,首先在阴极暗区受到电场加速,飞向负辉区。
进入负辉区的电子具有一定速度,并且是垂直于磁力线运动的。
在这种情况下,电子由于受到磁场B洛仑兹力的作用,而绕磁力线旋转。
电子旋转半圈之后,重新进入阴极暗区,受到电场减速。
当电子接近靶面时,速度即可降到零。
以后,电子又在电场的作用下,再次飞离靶面,开始一个新的运动周期。
电子就这样周而复始,跳跃式地朝着E(电场)B(磁场)所指的方向漂移。
磁控溅射靶在镀膜过程中的重要作用,磁控溅射靶是真空磁控溅射镀膜的核心部件,它的重要作用主要表现在以下两个方面:
(1)对于大面积表面的镀膜,磁控溅射靶影响着膜层的均匀性与重复性;
(2)当膜层材料为贵金属时,靶的结构决定着靶材的利用率。
(2)常用磁控溅射设备根据靶材形状不同,磁控溅射可以有许多形式,常用的主要有:
平面磁控靶、圆柱磁控靶。
a、平面磁控靶,特点:
在靶材的部分表面上方使磁场与电场方向相垂直,从而将电子的轨迹限制到了靶面附件,提高了电子碰撞和电离的效率,减少电子轰击作为阳极的衬底、抑制衬底温度升高的作用。
b、圆柱磁控靶电子约束在靶的表面附近,靶材的利用率高。
(1)磁控溅射的特点a、工作气压低,沉积速率高,且降低了薄膜污染的可能性;
b、维持放电所需的靶电压低;
c、电子对衬底的轰击能量小,可以减少衬底损伤,降低沉积温度;
d、空易实现在塑料等衬底上的薄膜低温沉积。
(2)磁控溅射缺点:
a、对靶材的溅射不均匀;
b、不适合铁磁材料的溅射,如果铁磁材料,则少有漏磁,等离子体内无磁力线通过;
磁控溅射法的改进非平衡磁控溅射法,普通的磁控溅射阴极的磁场集中于靶面附近的有限的区域内,基片表面没有磁场,称平衡磁控溅射阴极磁控溅射具有将等离子体约束于靶附近,对衬底的轰击作用小的特点。
这对于希望减少对衬底损伤,降低沉积温度的应用场合是有利的。
但是,某些情况下,希望保持适度的离子对衬底的轰击效应,这就是非平衡磁控溅射法提出的背景。
1985年Window提出增大普通的磁控溅射阴极的杂散磁场,从而使等离子体范围扩展到基片表面附近的非平衡磁控溅射阴极。
如果通过阴极的内外两个磁极端面的磁通量不等,则为非平衡磁控溅射阴极,非平衡磁控溅射阴极磁场大量向靶外发散采用非平衡磁控溅射法,有意识地增大(或减小)靶中心的磁体体积,造成部分磁力线发散至距靶较远的衬底附近,这时等离子体的作用扩展到了衬底附近,而部分电子被加速射向衬底,同时在此过程中造成气体分子电离和部分离子轰击衬底,保持适度的离子对衬底的轰击效应,以提高薄膜的质量:
附着力、致密度等。
普通平衡磁控靶示意图,平衡磁控阴极内外磁钢的磁通量大致相等,两极磁力线闭合于靶面,很好地将电子/等离子体约束在靶面附近,增加碰撞几率,提高了离化效率,因而在较低的工作气压和电压下就能起辉并维持辉光放电,靶材利用率相对较高,但由于电子沿磁力线运动主要闭合于靶面,基片区域所受离子轰击较小。
平衡磁控溅射阴极的磁场将等离子体约束在靶面附近,基片表面附近的等离子体很弱,只受轻微的离子和电子轰击。
平衡式靶源镀膜均匀,多用于半导体光学膜。
平衡磁控溅射,非平衡磁控溅射技术,即让磁控阴极外磁极磁通大于内磁极,两极磁力线在靶面不完全闭合,部分磁力线可沿靶的边缘延伸到基片区域,从而部分电子可以沿着磁力线扩展到基片,增加基片磁控溅射区域的等离子体密度和气体电离率.非平衡磁控溅射阴极磁场可将等离子体扩展到远离靶面的基片,使基片浸没其中,因此又称“闭合磁场非平衡溅射”,可以以高速率沉积出多种材料的、附着力强的高质量薄膜。
这有利于以磁控溅射为基础实现离子镀,有可能使磁控溅射离子镀与阴极电弧蒸发离子镀处于竞争地位。
非平衡磁控溅射,磁控溅射膜常见故障排除,膜层灰暗及发黑
(1)真空度低于0.67Pa,应将真空度提高到0.130.4Pa;
(2)氩气纯度低于99.9%,应换用纯度为99.99%的氩气;
(3)充气系统漏气,应检查充气系统,排除漏气现象;
(4)底漆未充分固化,应适当延长底漆的固化时间;
(5)镀件放气量太大,应进行干燥和封孔处理。
膜层表面光泽暗淡
(1)底漆固化不良或贬值,应适当延长底漆的固化时间或更换底漆;
(2)溅射时间太长,应适当缩短;
(3)溅射成膜速度太快,应适当降低溅射电流或电压,膜层色泽不均
(1)底漆喷涂不均匀,应改进底漆的施涂方法;
(2)膜层太薄,应适当提高溅射速度或延长溅射时间;
(3)夹具设计不合理,应改进夹具的设计;
(4)镀件的几何形状太复杂,应适当提高镀件的旋转速度。
膜层发皱、龟裂
(1)底漆喷涂太厚,应控制厚度范围;
(2)涂料的粘度太高,应适当降低;
(3)蒸发速度太快,应适当减慢;
(4)膜层太厚,应适当缩短溅射时间;
(5)镀件温度太高,应适当缩短对镀件的加温时间。
膜层表面有水迹、指纹及灰粒
(1)镀件清洗后未充分干燥,应加强镀前处理;
(2)涂底漆后手接触过镀件,表面留下指纹,应严禁用手接触镀件表面;
(3)涂料中有颗粒物,应过滤涂料或更换涂料;
膜层附着力不良
(1)镀件除油脱脂不彻底,应加强镀前处理;
(2)真空室内不清洁,应清晰真空室;
(3)夹具不清洁,应清洗夹具;
(4)溅射工艺条件控制不当,应改进溅射工艺条件。