高速切割的关键技术Word格式.docx
《高速切割的关键技术Word格式.docx》由会员分享,可在线阅读,更多相关《高速切割的关键技术Word格式.docx(5页珍藏版)》请在冰豆网上搜索。
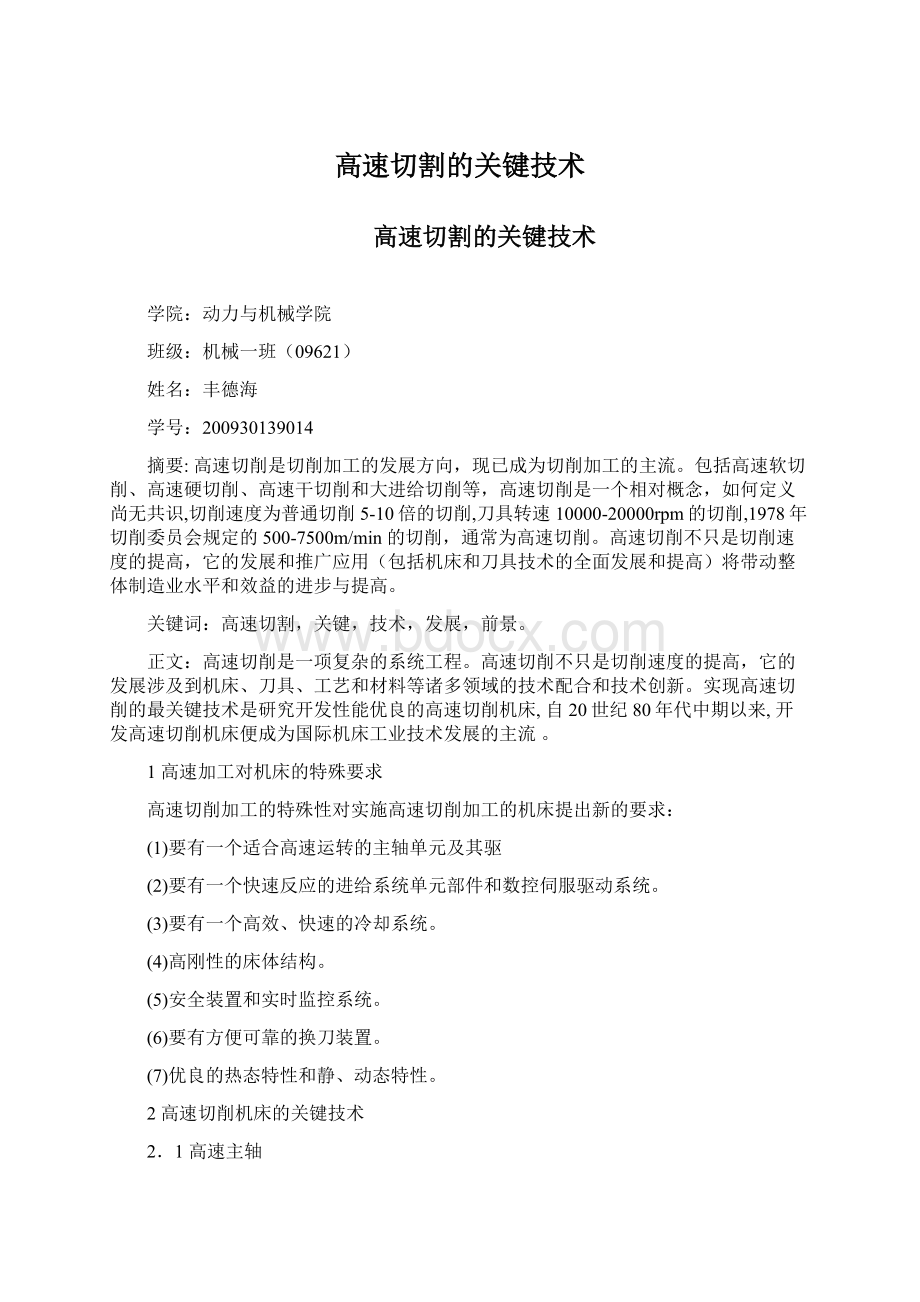
包括高速软切削、高速硬切削、高速干切削和大进给切削等,高速切削是一个相对概念,如何定义尚无共识,切削速度为普通切削5-10倍的切削,刀具转速10000-20000rpm的切削,1978年切削委员会规定的500-7500m/min的切削,通常为高速切削。
高速切削不只是切削速度的提高,它的发展和推广应用(包括机床和刀具技术的全面发展和提高)将带动整体制造业水平和效益的进步与提高。
关键词:
高速切割,关键,技术,发展,前景。
正文:
高速切削是一项复杂的系统工程。
高速切削不只是切削速度的提高,它的发展涉及到机床、刀具、工艺和材料等诸多领域的技术配合和技术创新。
实现高速切削的最关键技术是研究开发性能优良的高速切削机床,自20世纪80年代中期以来,开发高速切削机床便成为国际机床工业技术发展的主流。
1高速加工对机床的特殊要求
高速切削加工的特殊性对实施高速切削加工的机床提出新的要求:
(1)要有一个适合高速运转的主轴单元及其驱
(2)要有一个快速反应的进给系统单元部件和数控伺服驱动系统。
(3)要有一个高效、快速的冷却系统。
(4)高刚性的床体结构。
(5)安全装置和实时监控系统。
(6)要有方便可靠的换刀装置。
(7)优良的热态特性和静、动态特性。
2高速切削机床的关键技术
2.1高速主轴
高速数控机床的工作性能,首先取决于高速主轴的性能。
数控机床的高速主轴单元包括主轴动力源、主轴、轴承和机架等几个部分,它影响加工系统的精度、稳定性及应用范围,其动力性能及稳定性对高速加工起着关键的作用。
目前高速切削机床的主轴主要为陶瓷滚珠轴承电动主轴。
机床主轴由内装式电动机直接驱动,从而把机床主传动链的长度缩短为零,实现机床的“零传动”,俗称“电主轴”。
电主轴是一种智能型功能部件,不但转速高、功率大,还有一系列控制主轴温升与振动等机床运行参数的功能,以确保其高速运转的可靠性与安全性。
目前电主轴主要采用交流异步感应电动机(高频),国内外专业的电主轴制造厂已可供应几百种规格的电主轴。
其套筒直径从32mm至320mm、转速从10000r/min到150000r/min,功率从0.5kW到80kW、转矩从0.1N•m到300N•m。
2.2 高速精密轴承
高速轴承是高速切削机床的核心,是决定高速主轴寿命和负载容量的最关键部件。
2.2.1 磁悬浮轴承
它是用电磁力将主轴无机械接触地悬浮起来,其转速可达45000rPmin,功率为20kW,精度高,易实现实时诊断和在线监控,是理想的支承元件,但其价格较高。
2.2.2 液体动静压轴承
采用流体动、静力相结合的办法,使主轴在油膜支撑中旋转,具有径、轴向跳动小、刚性好、阻尼特性好,适于粗、精加工,寿命长的优点。
但其无通用性,维护保养较困难。
2.2.3 混合陶瓷轴承
用氮化硅制的滚珠与钢制轨道相组合,是目前在高速切削机床主轴上使用最多的支承元件,在高速转动时离心力小,刚性好,温度低,寿命长,功率可达80kW,转速高达150000rPmin,它的标准化程度高,便于维护,价格低。
2.3高精度快速进给系统
高速切削是高切削速度、高进给率和小切削量的组合,进给速度为传统的5~10倍。
这就要求机床进给系统高进给速度、良好的加减速特性、高精度、快响应、宽调速范围、低速大转矩。
要实行这样并准确控制这样高的进给速度,对机床导轨、滚珠丝杠、伺服系统、工作台结构提出了新的要求。
高速机床普通采用线性滚动导轨代替了传统的滑动导轨,其移动速度、摩擦阻力、动态响应特性和阻尼效果都不同于传统的滑动导轨,其特有的双V型导轨结构大大提高了机床的抗扭能力,同时其磨损近乎为零,导轨精度和寿命都比以往提高几倍,配合以数字伺服电机,其进给和快速进给从过去的6m/min提高到了现在的20~60m/min。
传统的直线电动机驱动机构,由旋转电动机、齿轮箱或联轴器、丝杠和驱动螺母、丝杠支座轴承等构成的驱动系统,影响和限制了机床的性能。
例如:
电动机最大转速的限制;
高加速度下电动机轴产生的扭曲变形和位置误差;
丝杠本身受临界转速、间隙、扭曲、螺距误差、摩擦等影响,且其振动衰减时间很长;
齿轮箱增加系统惯性,产生间隙。
而直线电动机。
驱动机构则没有上述缺点,能达到快速移动(可以达到120m/min甚至200m/min的速度)和较短的位置稳定时间,且能进一步减少机床不进行实际切削加工的非生产时间。
由于直线电动机驱动机构仅由两个互不接触部件组成,没有低效率的中间传动部件,也无机械滞后以及螺距误差,从而可达到高的效率,且其精度完全取决于反馈系统和轴承。
当用全数字伺服系统驱动直线电动机时,可达到高刚度和高固有频率,从而达到极好的伺服性能。
高速伺服系统已经发展成数字化、智能化,软件化,高速切削机床已开始使用全数字交流伺服电机和控制技术。
2.4 高速伺服系统
为了实现高速切削加工,机床不但要有高速主轴,还要有高速的伺服系统,这不仅是为了提高生产效率,也是维持高速切削中刀具正常工作的必要条件,否则会造成刀个的急剧磨损与升温,破坏工件加工的表面质量。
2.4.1 直线电机伺服系统
直线电机是使电能直接转变成直线机械运动的一种推力装置,将机床进给传动链的长度缩短为零,它的动态响应性能敏捷、传动刚度高、精度高、加减速度大,行程不受限制、噪音低、成本较高,在加速度大于1g的情况下,是伺服系统的唯一选择。
2.4.2 滚珠丝杠驱动装置
滚珠丝杠仍是高速伺服系统的主要驱动装置,用AC伺服电机直接驱动,并采用液压轴承,进给速度可达40~60m/min,其加速度可超过0.6g,成本较低,仅为直线电机的1/2.5。
2.5高性能的数控系统
数控系统的选用要注意是否具有如下的高速加工功能:
①进给速度、加减速度的控制,前馈控制,前瞻控制,冲击控制;
②各种螺距补偿、反向间隙补偿、弯曲度补偿、温度补偿、跨象限补偿等;
③大容量存储器,以适应复杂形状加工的需要;
④程序的快速输入和处理。
高性能的数控系统组成目前常用的高性能数控系统有FANUC的16i、SIEMENS的840D和HEIDENHAIN的TNC430等,它们的脉冲当量已达纳米级。
2.6高速切削机床本体结构的要求
高速切削机床要求机床本体具有很好的静刚度、动刚度和热刚度特性等,尤其对动态特性有很高的要求。
在设计时,从机床结构动态特性、固有频率的角度,进行有限元分析或利用"
多体系统"
进行动态仿真,设计出最优的床身结构。
目前大多采用落地式床身,整体铸铁结构,龙门框架的主轴立柱,并在立柱上增加适当的加强筋,使机床结构具有良好的静、动态刚度和稳定性,且有很好的吸振性。
也可采用基于Stewart平台的并联机床的床身结构,以减轻重量,增加刚度。
近年来高速机床的床身和立柱材料采用了聚合物混凝土或称人造花岗石,这种材料的阻尼特性为铸铁的7~10倍,而比重只有铸铁的三分之一,是制造高速机床支承件较为适宜的材料。
3高速切削机床发展历史与现状
3.1国外
20世纪80年代,世界机床制造强国德国、日本就在政府强有力的资助下,联合众多机床制造企业,共同攻关,进行高速切削机床各相关硬件与软件的开发,并迅速实现高速切削机床的商品化。
1993年,汉诺威国际机床博览会上展出了德国制造的世界上第一台用直线电动机驱动工作台的高速加工中心,由此拉开了高速进给的序幕,高速切削技术从此快速走向成熟应用阶段。
目前,德国的高速立式铣削加工中心实用化的主轴转速已经达到60000r/min,快速进给速度X、Y、Z轴均为60m/min,加速度为2.5g,重复定位精度±
1μm。
在研制高速切削机床的同时,德国还在高速切削工艺方面进行深入研究,在有色金属、复合材料、铸铁及模具钢等高速切削机理研究方面形成系统理论,以加工效率、加工精度和加工零件表面完整性为目标,对高速切削工艺进行优化,对指导高速切削生产起到很大作用。
日本于1996年研制出第一台卧式高速切削加工中心,主轴转速30000r/min,最大进给速度80m/min,加速度为2g,重复定位精度±
同时在高速切削工艺方面进行了深入研究,包括高速切削工艺数据库、高速切削刀具磨损破损机理、切屑控制、高速切削过程CAD/CAM系统开发及质量控制等,从而加速高速切削技术产业化进程,在国际机床界产生重大影响。
近几年国外高速加工机床发展迅速,美国、法国、瑞士、英国、加拿大、意大利等国家相继开发出了各自的高速切削机床。
3.2国内
我国在20世纪90年代初开始有关高速切削机床及工艺的研究。
研究内容包括水泥床身、超高速主轴系统、全陶瓷轴承及磁悬浮轴承、快速进给系统、有色金属及铸铁超高速切削机理与适应刀具等方面。
通过科技工作者的艰苦工作,各项关键技术都取得了显著进展。
然而,由于种种原因,一些高速加工技术基础共性技术研究没有得到优化、集成和推广应用,未能形成系统理论,与国外发达国家差距明显。
在市场经济引进技术设备的带动下,我国高速机床技术有了长足进步。
现在国内10000~15000r/min的立式加工中心、18000r/min的卧式加工中心、3500~4000r/min的数控车床和车削中心已批量生产,切削速度达8000r/min的数控车床也已问世。
高速机床的高档数控系统和开放式数控系统正在深入研究中,但目前主要还是依赖进口。
目前国内正逐步开始推广应用高速切削技术,主要是应用在航空航天、模具和汽车工业,加工铝合金和铸铁较多,采用的刀具以进口为主。
我国现在的国情是,在航空、汽车和模具等生产部门,已进口相当规模的高速切削机床,而且进口高速切削机床数量还在进一步上升。
4结束语
高速切削加工技术是一项全新的、正在发展中的先进实用技术,在理论和技术各方面还有大量研究、开发工作要做。
我国高速切削加工技术的开发和应用还处于初步阶段,但国内已进口了大批高速加工设备,也开发了多种高速加工机床,只要我们充分认识高速切削加工技术的优越性,完全有可能把我国切削加工水平推进到一个新高度。
参考文献
[1]张伯霖.高速切削技术及应用.机械工业出版社,2003.4
[2]艾兴,刘战强,赵军,邓建新,宋世学.高速切削刀具材料的进展和未来.制造技术与机床,2001.8
[3]刘文化.高速加工机床的发展历史与现状.金属加工,2010.12
[4]王正君,史津平,周小玉.高速超高速切削及高速机床.
机床与液压,2001.1
[5]胡秋.高速机床关键技术及其发展趋势.机床与液压,2001.8
[6]徐彪,李长光.高速切削的技术装备.电子机械工程,2002.Vol.18No.6
[7]孙全平,廖文和.高速切削的现状及其关键技术.淮阴工学院学报,Feb.2002 Vol.11No.1
[8]吴明友.高速切削机床.煤矿机械,2006.6
[9]张宁菊.高速切削机床的关键技术.机床与液压,2005.11
[10]周华,石彦华.高速切削机床的关键技术及其应用.现代制造工程,2008.8
[11]朱从容,顾平灿.高速切削技术及高速切削机床.精密制造与自动化,2002.3