该条生产线由14组机架组成每小时生产48吨最高等级ETP铜杆CONTIROD生产线文档格式.docx
《该条生产线由14组机架组成每小时生产48吨最高等级ETP铜杆CONTIROD生产线文档格式.docx》由会员分享,可在线阅读,更多相关《该条生产线由14组机架组成每小时生产48吨最高等级ETP铜杆CONTIROD生产线文档格式.docx(15页珍藏版)》请在冰豆网上搜索。
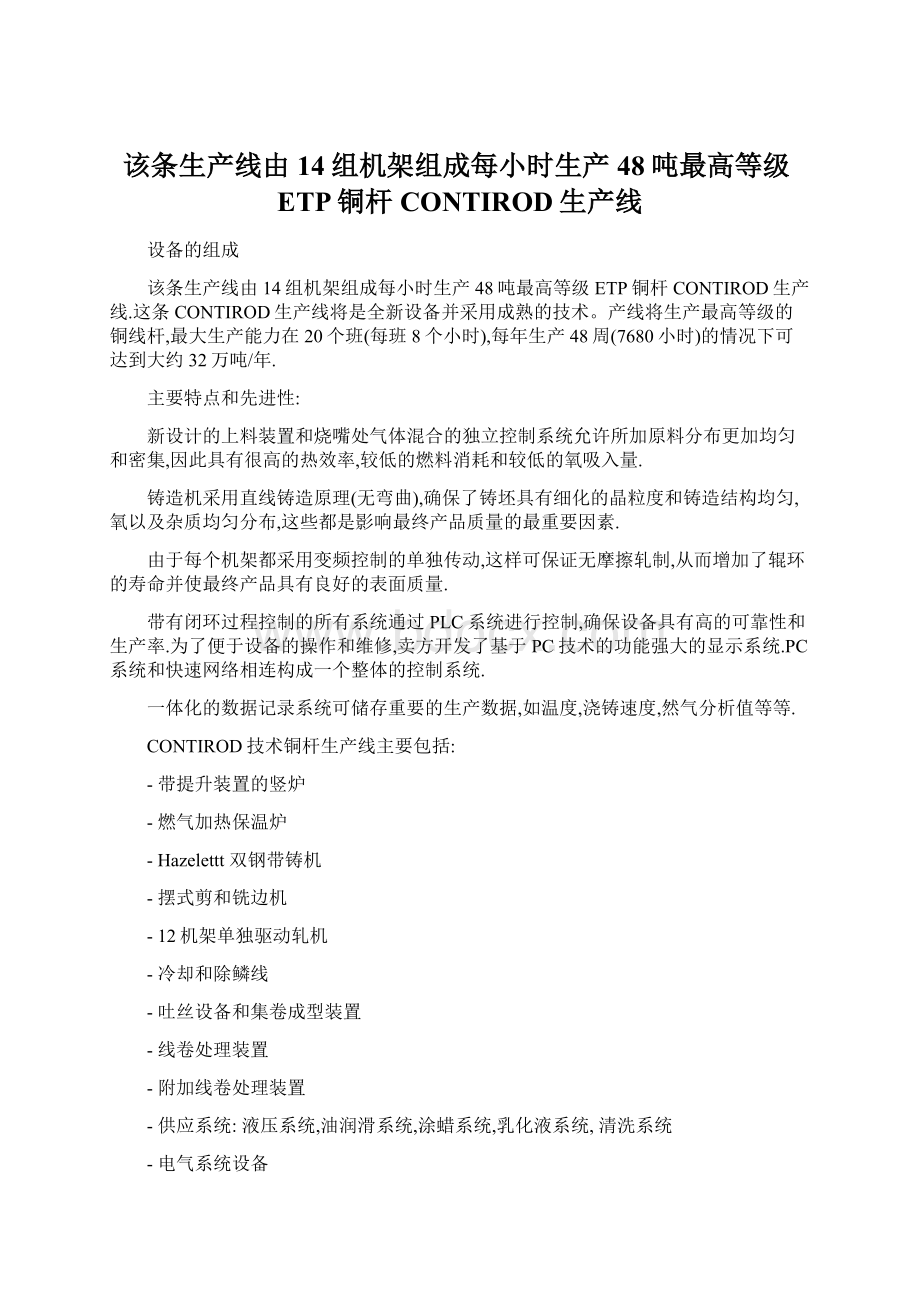
-线卷处理装置
-附加线卷处理装置
-供应系统:
液压系统,油润滑系统,涂蜡系统,乳化液系统,清洗系统
-电气系统设备
-备件和易损件
一套用于电解铜和废铜的新装料系统,装料灵活。
装料系统包括安装在平台上的卷扬机,料斗车以及控制系统。
独特的翻斗车设计合理,电解铜布料得到很大改进,废铜的装料简单易行
碎料箱
电解铜的装运
电解铜的分布
-竖炉
设有自动调节烧嘴23个,能精确控制每个烧嘴中气体的混合。
当采用电解铜和废铜混合熔炼时,应防止自由氧进入铜液
-带封罩的流槽
铜液通过燃气加热带罩盖流槽将铜液从竖炉送达保温炉
-氧的吸入量少
-保温炉
容量20吨
燃烧气体自动控制
当轧制中断时(如需更换钢带和辊环),竖炉继续熔炼,维持保温炉内液铜温度的稳定。
Hazelett双带连铸机
直线浇注,无弯曲铸造
铸件断面规格大120mmx70mm=8,400mm²
(压缩比大,从浇铸断面到轧制断面为165倍,这样可将铸造组织完全转变成良好的轧制组织).
凝固过程中液铜静压–无中心缩孔
轧机
14单独传动的机架,辊环直径480/360/220mm
(直径大–轧制效果更佳,从而有效的转变铸造结构)
机架中上下两辊对称调节
->
辊环允许25次再修磨
->
使用修磨后的轧辊仍能保证轧制中心在一条直线上
轧机单独传动,即通过14台交流变频电机驱动–实现无张力轧制,辊环寿命长
高压除鳞系统确保在轧制过程中减少氧化物形成
分为2段–时用酒精和水的混合液,先除鳞,然后冷却到最终温度.
优点:
-铜杆表面光亮,附着很薄的250Å
厚的氧化层–重要的质量因素
-集卷设备
集卷站将铜线杆以梅花型方式绕成盘卷.在集卷站下面装备有一个升降台架(对盘卷形状很重要).在这之后是一个打蜡装置用于对铜杆表面进行保护.
-灵活地按照客户要对盘卷尺寸要求进行盘卷
-满足新一代高速拉拔机快速抽线要求
乳化液系统
采用两个单独的乳化液系统,配备自动加料泵。
按轧制条件及按初轧,精轧对化学成份要求不同,将酒精,油,中和剂进行优化配比。
-按轧制要求不同,对乳化液成份做配比
-对辊环进行控制润滑,再加上单独传动使辊环寿命长,生产成本低
-铜杆表面质量好–保证产品质量的重要因素
-电气控制设备
整个CONTIROD®
生产线采用PLC-系统进行控制
轧机采用交流变频传动
整条生产线配备显示系统以及信号诊断,监控软件,
-工艺数据采集方便,易于排除故障
-生产线停机时间少
-作业率高
-交流传动维护费用低,轧制速度高
3生产工艺描述
熔化炉设备
电解铜板和废铜箱的装料系统由一个带电动卷扬机和翻斗的倾斜升降机组成,CONTIROD生产线产生的所有废铜全部由相同的废料收集箱进行收集.向炉内装料时,在母线的引导下将装料机的倾卸斗引导到卸料位置.
叉车将料放在倾卸斗上后,卷扬机驱动提升电解铜或单独的负荷,最重可达5吨(最大铜料尺寸1300mm×
1000mm).
竖炉由钢板焊接成垂直的圆柱形,外部直径约2.4米,高约12米。
竖炉壳底部留有开口用以布置三排燃气烧嘴,另外出液口用于将铜液流入流槽系统,再进入保温炉。
炉子的上部有一个水平的装料口。
竖炉设有空冷防护板,直接安装在装料部分的下部以防止装料时对炉壳和耐火材料产生机械损伤。
从底部到炉体段,炉体全部装有耐火材料衬。
竖炉上有一个烟囱用于排放热废气,废气除尘设备可以选项供货。
三台变频控制的风机和空气调节设备为烧嘴提供燃烧。
空气收集在三个空气集流腔里。
每排烧嘴所用的空气都从集流腔中提取。
燃气的供应包括来自当地气源的燃气管道以及控制装置和三个燃气集流腔。
一个电气控制屏控制炉子的操作。
通过连接流槽使熔化炉与保温炉相连,流槽有盖,流槽都砌有耐火衬和装有流槽烧嘴。
竖炉是一个熔化炉,不是冶炼炉。
它仅仅用于熔化电解铜和洁净的铜废料。
炉子的烧嘴以三排的形式设置在炉子的周围,用于连续熔化竖炉内的电解铜和废铜。
铜液通过排液孔流出,通过流槽系统流入保温炉。
在熔化过程中产生的烟气将通过烟囱排放到大气中。
烟气还用于预热上面的电解铜和废铜。
自动装料操作是通过电视系统进行监视。
全部烧嘴的空气和燃气量可以调节以达到最佳的燃烧条件,它是通过控制屏进行
连续控制。
竖炉系统的重要特性如下:
在开始点火和工作过程中的压力和流量安全措施–根据喷嘴混合原理不会有回火现象产生.
喷嘴混合系统,即燃气和空气在每一个烧嘴中均匀混合(安全、可靠)而不是采用远处的预混合。
自动调节空气和燃气的燃烧比例使其最佳化。
熔入铜液中的氧含量低。
采用变频控制风机以更好地对燃烧进行控制,并降低能源消耗。
保温炉
保温炉炉体由钢板制成,为水平的鼓形结构。
它装有两个倾斜的摆架和一个型钢结构架。
鼓形装置轻微向铸机方向倾斜并可围绕着炉子的偏心轴转动。
保温炉前后端的液态金属出入口分别设置在倾动轴线上。
在鼓形体的圆周上布置了一个通风门和一个工作门。
保温炉可以借助于液压缸倾转到每个加注位置,液压缸支撑在钢结构上并和鼓体相连。
保温炉由两个燃气烧嘴加热,烧嘴装在保温炉上。
保温炉具有一个单独的燃气供给系统。
整个保温炉全部砌有必要的耐火材料衬。
保温炉实为一个连续的保温炉。
液态金属在熔化炉中熔化后通过流槽系统进入保温炉的前端。
炉子的容量可以在总的容量范围内根据需要进行变化,并通过调节倾动角来实现。
铜水的容量通过安装在底座上的传感器来进行测量.在对面设置有管形出口喷嘴。
通过流槽液态金属流入铸机的中间包。
保温炉底部永久装有热电藕,用于连续监测铜液温度。
炉子的烧嘴将由这个热电藕控制。
铜液的流量由铸机的EMLI系统自动控制。
连铸和连轧设备
连铸机的铜液供给
在鼓形保温炉和连铸机之间设置了铜液供给系统。
装有耐火衬的流槽接收来自保温炉的铜液并将铜液送入铸机上游的中间包。
在流槽的中设有液态金属过滤砖。
中间包直接设置在流槽的下面。
通过一个通道式的浇口,铜液被引导流入由铸造钢带等形成的结晶器区域.
当浇注过程开始和结束时,中间包在液压驱动下旋入和旋出。
当中间包旋出时,流向铸机中的铜液会立刻停止,仍留在中间包里的铜液将排放到铸机对面的容器中。
当浇注开始时,铜液通过流槽流到旋出的中间包里。
中间包充满金属后,溢出的铜液流到上述的容器中,这时,中包旋入,铜液被引导流到铸机中。
这就保证了在开始浇注时铸机的起动无任何问题并不会发生冷凝的风险。
另外,浇注的浇口可确保平稳的和无湍流的铜液流动,这样就将不可避免的氧吸收限定在最可能低的范围内,并且被吸收的氧均匀分布在铜液中。
在浇注开始前,流槽和中间包由烧嘴预热。
在流槽上这些烧嘴设置在流槽的盖上并带有耐火衬。
流槽的盖上还留有开口,用于插入连续测量铜液氧含量检测装置(不在基本供货范围内),这些开口还用于铜液液位自动监控和流量调节探头的插入。
为了便于耐火衬的维护和修理,流槽和中包可以很容易地移出,分别放置在支撑架和旋转装置上。
HAZELETT双带式铸机
HAZELETT双钢带铸机结晶器是一个平直的、对称的矩形形状。
因此铸坯也具有同样的特性,即被铸成平直的、对称的矩形形状,铸坯接下来进行轧制。
结晶器由两条回转钢带构成结晶器的上下两个表面,还有两条回转的青铜挡块链形成结晶器的两个侧面。
在浇注过程中,结晶器壁与铸坯之间没有相对运动。
为了补偿铸坯在凝固过程中的收缩,钢带以及青铜挡块链都向着铸机出口方向调节,这样,铸坯和结晶器之间的接触面在结晶器区域就没有脱开现象。
来自铸坯的热量主要通过浇注钢带和和青铜挡块带走,也将有部分热量由浇注钢带吸收。
在青铜块中的残留的热量在特殊冷却装置中通过喷水被带走。
为了达到这个目的,我们使用一个特殊的冷却水供给装置,它能使铸机钢带在结晶器的全部长度范围内保持均匀的温度。
这样不仅使在浇注钢带之间形成的铸坯均匀和对称的冷却,并且还能延长浇铸钢带的寿命。
为了能够实现给浇铸钢带和青铜挡块链喷涂润滑涂层,配有自动分配器喷嘴。
温度的测量仪器主要用于下列各项:
在中间包里的铜液温度
进入结晶器之前的青铜挡块的温度,包括记录器
冷却水温度
再者,冷却水的进给压力也要进行测量。
铸机由电机驱动。
上下钢带通过人字齿轮箱和万向传动轴同步传动上下钢带。
青铜挡块链由于它们与下浇铸钢带的接触而实现同步传动。
铸机区域还包括一个辊式导位来引导铸坯以与水平线15度的角度离开铸机,这样大的弯曲直径防止了铸坯产生有害弯曲缺陷。
在出口部位,铸坯已经处于水平位置,并处于轧制线上,在那里设置了一组夹送辊。
下部的夹送辊设计为固定辊,而上部的夹送辊的位置可以借助于液压缸进行调节。
夹送辊由一台电机驱动,并与铸机的传动同步。
从后轴的末端,速度参考值被采集供后续线轧机传动装置使用。
铸机的维修很简单,可以在短时间内完成,这是因为上下铸机钢带的导向装置可以吊起放置在铸机的主框架上。
在移走挡水板后,两个钢带可以很容易地从操作员一侧移出。
另外,上钢带可以略向上旋转,这样青铜块链可以简单地从下钢带中移出。
经过训练的人员大约需要20分钟的时间就可以更换完铸机的所有的钢带和青铜块链。
目前铸机钢带须在6个班次后更换,青铜块链大约在160个班次后更换。
正是因为HAZELETT双钢带铸机结晶器的独特设计,就铸机的浇铸断面而言,能够灵活地更换到另一种浇铸断面。
通过增加或减少了青铜块链之间的距离,铸坯的宽度可以在不做大的改动的情况下进行变换。
铸坯的高度变化可以通过使用高的或低的青铜块来实现。
借助于液压调节,上钢带的导向装置可以自动地适配于不同高度的青铜挡块链。
这种灵活性可使我们的铜杆设备生产除了铜杆以外的厚带材和扁材产品。
铸机和轧机之间的设备
这些设备主要用于:
1.在铸造开始阶段和在出现故障的情况下切断铸坯
2.以45°
角对铸坯铣边
切断铸坯使用一个液压驱动的摆式剪。
在剪切时,剪子以摆动的方式移动,这个移动是借助铸坯的前进而产生的。
摆动的优点表现于在切断过