仓库风险评估方案Word文档下载推荐.doc
《仓库风险评估方案Word文档下载推荐.doc》由会员分享,可在线阅读,更多相关《仓库风险评估方案Word文档下载推荐.doc(14页珍藏版)》请在冰豆网上搜索。
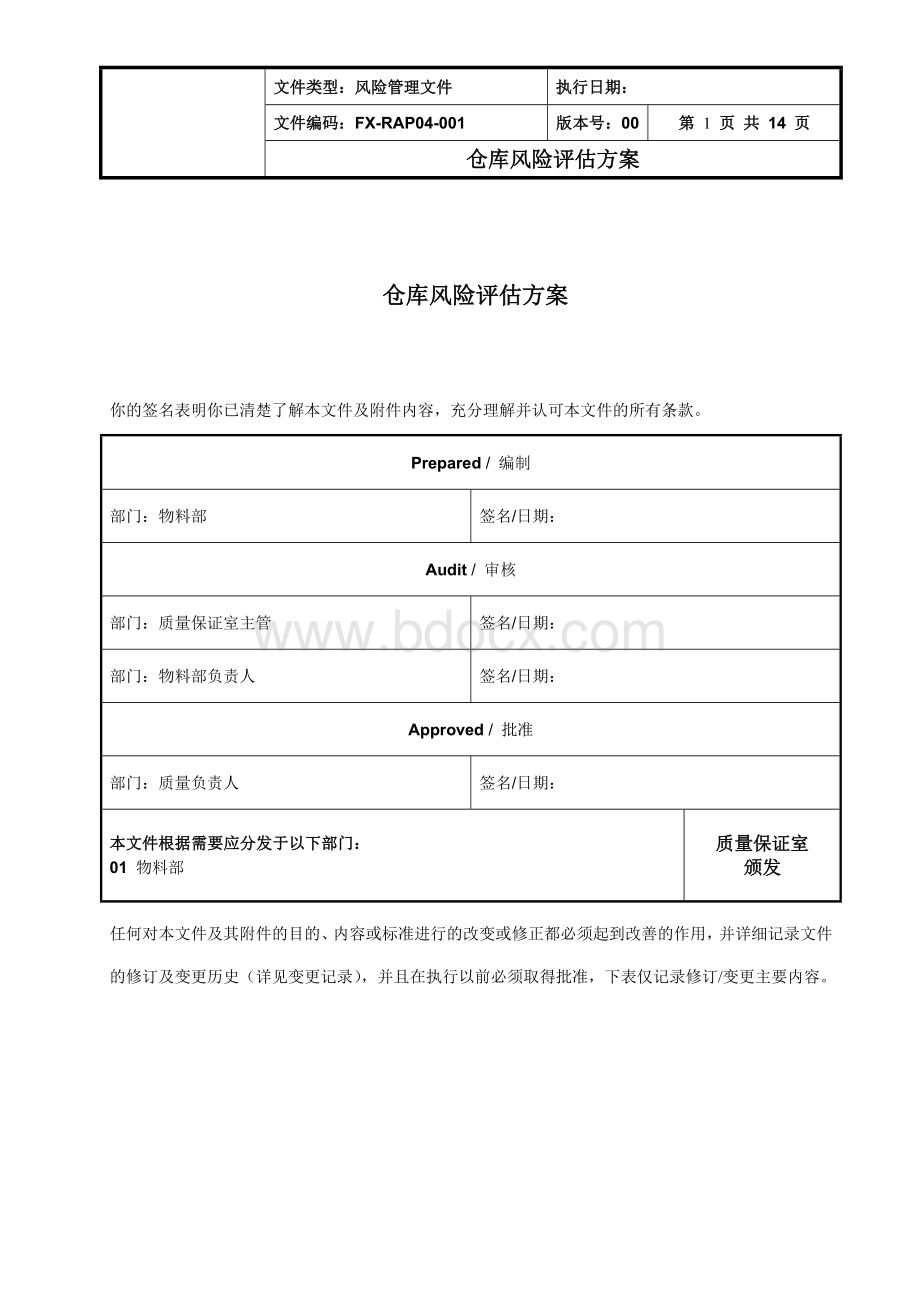
01物料部
质量保证室
颁发
任何对本文件及其附件的目的、内容或标准进行的改变或修正都必须起到改善的作用,并详细记录文件
的修订及变更历史(详见变更记录),并且在执行以前必须取得批准,下表仅记录修订/变更主要内容。
目录
1.目的 3
2.范围 3
3.术语或定义 3
4.引用资料 3
5.使用的风险工具 3
6.风险评价准则 3
6.1严重性(S) 3
6.2可能性(P) 4
6.3可检测性(D) 4
6.4风险级别评判标准 4
7.本项目风险评估管理过程 4
7.1概述 5
7.2风险管理小组成员及其职责分工 5
7.3风险评估流程及日程安排 5
7.4确定风险源,对风险源存在的相关风险进行预估和分析 6
7.5风险评价 8
7.6风险控制 11
7.7风险评价总结 13
7.8总结和结论 15
7.9风险再评估 15
7.10附件 15
1.目的
制定公司仓库风险评估方案,为了识别仓库可能存在的风险,并对该风险进行科学的、系统的评估,采取适当的方法对风险进行控制、消减、规避等系统活动,旨在最大程度上降低仓库在使用的过程中带来的风险。
2.范围
适用于同溢堂药业有限公司规范仓库风险管理工作
3.术语或定义
3.1GMP:
药品生产质量管理规范(GoodManufacturingPractice)的英文简称。
3.2SOP:
标准操作规程(StandardOperatingProcedure),用于指导如何完成一项工作的文件。
3.3质量风险管理:
在整个产品生产周期中采用前瞻性或回顾性的方式,对质量风险进行评估、控制、沟通、审核的系统过程。
3.4风险评估:
是指对风险进行识别、分析、评价,确定风险事件、风险类别、类型,辨识风险的来源和风险特点,以及预测风险带来的伤害、影响模式。
3.5失效模式和效果分析(FMEA):
是一种用来确定潜在失效模式及其原因的分析方法。
3.6CAPA:
纠正与预防措施的英文缩写。
4.引用资料
4.1《药品生产质量管理规范》2010年版
4.2《中国药典》2010年版
4.3ISO31000《风险管理原则及实施指南》
4.4ICHQ9
5.使用的风险工具
5.1FMEA
6.风险评价准则
风险级别由三个因素组成:
风险的严重性(S)、风险的发生可能性(P)、风险的可检测性(D)。
6.1严重性(S)主要针对可能危害产品质量数据完整性的影响,严重程度分为以下三个等级:
严重性(S)
风险系数
风险评价标准
高
3
直接影响产量要素或工艺与质量数据的可靠性、完整性、可跟踪性。
此风险可导致产品召回或退回;
不符合GMP原则,可能引起检查或审计中产生偏差。
中
2
尽管不存在对产品或数据的影响,但仍间接影响产品质量要素或工艺与质量数据的可靠性、完整性、可跟踪性;
此风险可能造成资源的浪费。
低
1
尽管此类风险不对产品或数据产生最终影响,但对产品或可跟踪性仍产生较小影响。
6.2可能性(P)测定风险产生的可能性,为建立统一基线,建立以下等级
可能性(P)
偶尔发生
很少发生
发生可能性很低
6.3可检测性(D)在潜在风险造成危害前,检测发现的可能性
可检测性(D)
自动控制装置到位,检测错误
通过应用于每批常规的手动控制或分析可检测到错误
通过周期性控制可检测到错误
6.4风险级别评判标准
风险优先数(RPN)计算公式:
RPN=风险的严重性(S)x风险发生的可能性(P)x风险的可检测性(D)
6.4.1风险水平等级:
风险系数RPN
风险水平
19≤RPN≤27
此为不可接受风险,必须尽快采取控制措施,通过提高可检测性及降低风险产生的可能性来降低最终风险水平。
对此类风险如无管理制度得建立管理制度,如有,则需进行改进,加强培训、考核、监控、验证。
10≤RPN≤18
此风险要求采用控制措施,通过提高可检测性及(或)降低风险产生的可能性来降低最终风险水平。
所采用的措施可以是规程或技术措施,但均应经过验证。
1≤RPN≤9
此风险水平为可接受水平,无需采用额外的控制措施。
对此类风险本公司继续维持现行的管理规程及操作规程。
7.本项目风险评估管理过程
7.1概述
我公司物料部仓库分为危险品库、中药材仓库、综合仓库(综合仓库用于存放辅、包装材料、成品、劳保用品),仓储空间充足、设施完善。
仓库主要负责公司成品、半成品、原辅料、包装材料、五金备品、劳保用品的接收、储存、发放的管理。
物料部共5人,其中物料部副经理1人,仓库主管1人,中药材仓管员1人,辅料、包材仓管员1人,五金备品、劳保用品仓管员1人。
为进一步提高仓库的管理水平,发现并尽可能消除一些潜在的风险对物料造成的影响,根据公司《风险管理管理规程》文件中的有关规定,物料部特组织相关人员开展了对仓库的风险评估。
此次风险评估从2014年4月22日开始,至4月25日结束。
7.2风险管理小组成员及其职责分工
7.3风险评估流程及日程安排
物料系统风险评估小组在4月22日召开了首次会议,确定了本次仓库风险分析的活动流程及日程安排。
7.3.1风险活动流程
7.3.1.1风险活动流程图
7.3.1.1.1风险识别:
根据仓库的实际情况,分析仓库可能出现的失效模式,从人、机、料、法、环、五方面进行风险源的识别,确定风险源。
7.3.1.1.2风险分析:
针对风险等级为高、中、低级的失效模式分析失效原因,对失效原因发生的可能性、可检测性进行调查、评估,制作失效原因的风险指数排序表,对失效原因进行风险分级。
7.3.1.1.3风险评价:
针对风险分析的结果,利用FMEA对风险发生的严重性、可能性、可检测性进行风险赋值,评定风险等级。
7.3.1.1.4风险控制:
对于经风险评价为不可接受的风险,针对失效原因制定改进措施,对改进措施实施后仍残留的风险进行预评估。
应将所有失效原因的风险指数(RPN值)降至可接受水平,否则需重新进行风险分析、评价、控制的循环。
7.3.1.1.5总结报告:
当风险降至可接受水平后,对风险分析全过程进行总结,形成书面报告。
7.3.1.1.6风险审核:
当采取系列措施控制了已知风险后,应对该方法进行必要的评价及审核,证明所采取的风险控制手段确实有效地把风险等级降低到了可接受的标准及以下,同时没有引出新的风险。
7.3.1.1.7风险回顾:
应定期回顾风险评估过程的有效性和适用性,即时调整、增加或降低风险控制的力度。
7.3.1.2评估日程
星期一
星期二
星期三
星期四
4月22日
4月23日
4月24日
4月25日
1.首次会议
2.风险识别、分析
3.风险评价
4.风险控制、总结报告
7.4确定风险源,对风险源存在的相关风险进行预估和分析
物料系统风险评估小组召开第二次会议,依据各库特点,以及GMP对仓库的要求,风险管理小组成员使用头脑风暴法,结合FMEA(失效模式与影响分析),从人、机、料、法、环五方面对仓库进行了风险源预估确定,并分析仓库可能出现的各种偏离正常的偏差,即潜在的失效模式、失效模式可能造成的影响,将本次的仓库风险源及风险影响结果汇总如下:
序
风险源
可能的风险
人
管理者资质不能满足要求
人员数量不够,超负荷工作
中药材仓管人员未经过培训,不具备初步判断药材真假伪劣能力,不具备仓库管理知识;
仓管人员未经过培训,不具备仓库管理知识;
培训考核未通过,未进行再培训
没有能替代人员
仓管人员操作、复核意识不强,责任心不够;
物料现场QA监控力度不够
未经健康体检或有健康体检,但体检报告有误
机
冷库机组不能正常运行
空调不能正常运行;
衡器、温湿度计未经计量部门检定
秤的量程选择不正确
叉车及附属设施未检查
仓库设备设施没有进行保养维护
没有文件规定维护保养设施、设备
料
供应商未经评估
原药材、原辅料质量不符合标准规定,数量不准确
包装材质、印刷质量不符合标准规定,数量不准确;
印字包材没有设置专库
各物料以及成品分区不明确;
特殊物料、贵细药材没有设置专库或专柜
物料未按贮存要求存放
物料没有按要求接收与验收
物料没有按要求发放
没有按照有效期与复验期管理
没有安全库存
4
法
未制定相应的管理规程
未制定相应的操作规程;
文件操作性差
没有相应的状态标识卡
没有相应货位卡以及记录
没有必要的验证报告和记录
安全告知卡、应急处理装置、安全标志不醒目
5
环
仓库设施不能够保证药材在存放期间的质量稳定
仓库储存区域未能足够容纳物料;
物料摆放未按要求分区、未定置管理,易产生混淆
特殊物料、易串味、贵细药材、印字包材是否设置专库或专柜
是否有相应的措施控制温湿度
防虫鼠设施不完善
没有按照规定对物料进行养护
没有按照要求进行清洁
7.5风险评价
2014年04月24日,物料系统风险评估小组针对风险分析的结果,利用FMEA对人、机、料、法、环五方面风险发生的严重性、可能性、可检测性进行风险赋值,评定风险等级。
7.5.1仓库潜在失效模式分析评价表:
风险点
风险识别
风险影响
现有控制措施
严重性
可
能
性
可检测性
风险
指示值
风险等级
1.人
2.机
没有文件规定维护保养设备
3.料