工业机器人使用及维护Word格式文档下载.docx
《工业机器人使用及维护Word格式文档下载.docx》由会员分享,可在线阅读,更多相关《工业机器人使用及维护Word格式文档下载.docx(9页珍藏版)》请在冰豆网上搜索。
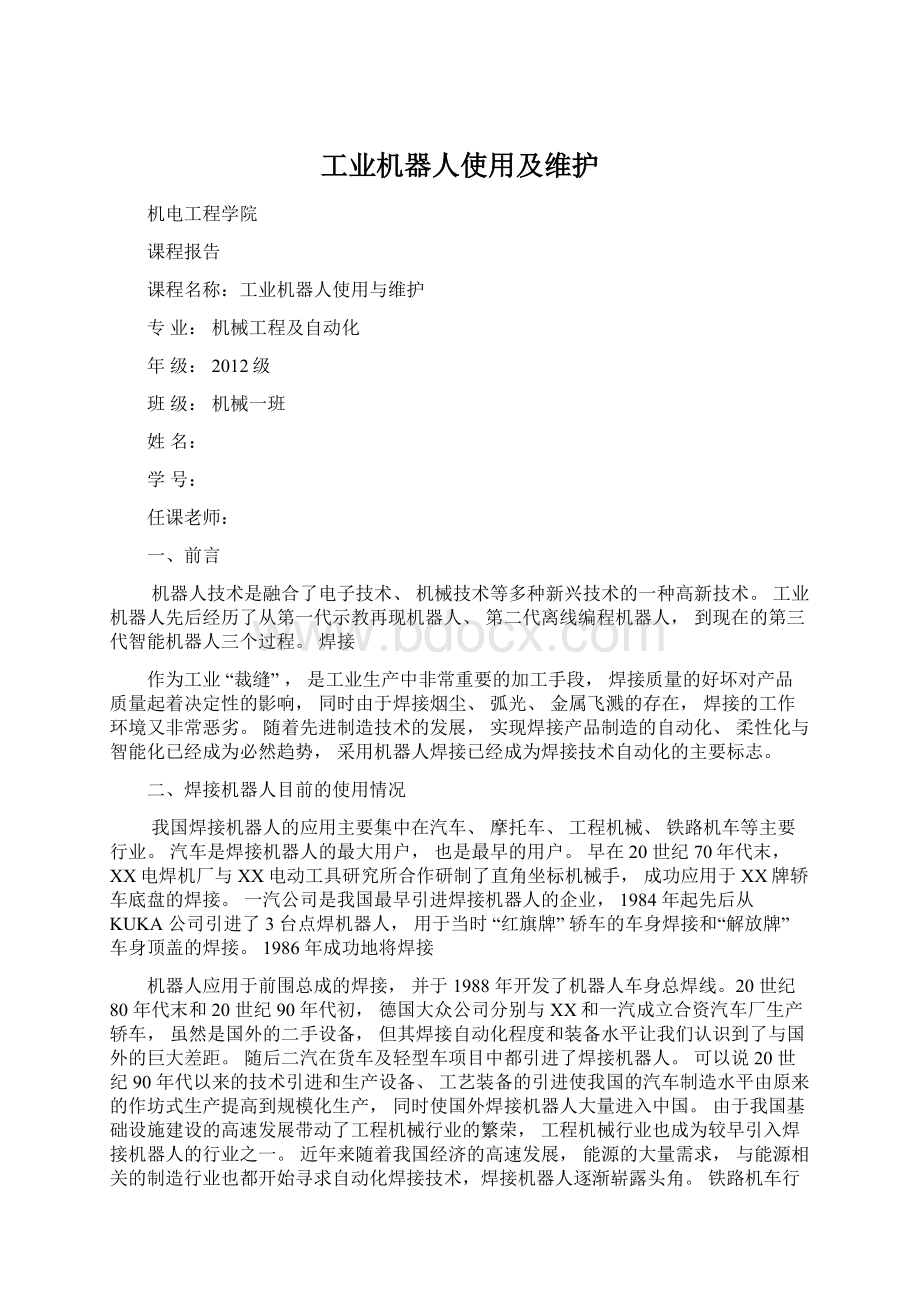
一、前言
机器人技术是融合了电子技术、机械技术等多种新兴技术的一种高新技术。
工业机器人先后经历了从第一代示教再现机器人、第二代离线编程机器人,到现在的第三代智能机器人三个过程。
焊接
作为工业“裁缝”,是工业生产中非常重要的加工手段,焊接质量的好坏对产品质量起着决定性的影响,同时由于焊接烟尘、弧光、金属飞溅的存在,焊接的工作环境又非常恶劣。
随着先进制造技术的发展,实现焊接产品制造的自动化、柔性化与智能化已经成为必然趋势,采用机器人焊接已经成为焊接技术自动化的主要标志。
二、焊接机器人目前的使用情况
我国焊接机器人的应用主要集中在汽车、摩托车、工程机械、铁路机车等主要行业。
汽车是焊接机器人的最大用户,也是最早的用户。
早在20世纪70年代末,XX电焊机厂与XX电动工具研究所合作研制了直角坐标机械手,成功应用于XX牌轿车底盘的焊接。
一汽公司是我国最早引进焊接机器人的企业,1984年起先后从KUKA公司引进了3台点焊机器人,用于当时“红旗牌”轿车的车身焊接和“解放牌”车身顶盖的焊接。
1986年成功地将焊接
机器人应用于前围总成的焊接,并于1988年开发了机器人车身总焊线。
20世纪80年代末和20世纪90年代初,德国大众公司分别与XX和一汽成立合资汽车厂生产轿车,虽然是国外的二手设备,但其焊接自动化程度和装备水平让我们认识到了与国外的巨大差距。
随后二汽在货车及轻型车项目中都引进了焊接机器人。
可以说20世纪90年代以来的技术引进和生产设备、工艺装备的引进使我国的汽车制造水平由原来的作坊式生产提高到规模化生产,同时使国外焊接机器人大量进入中国。
由于我国基础设施建设的高速发展带动了工程机械行业的繁荣,工程机械行业也成为较早引入焊接机器人的行业之一。
近年来随着我国经济的高速发展,能源的大量需求,与能源相关的制造行业也都开始寻求自动化焊接技术,焊接机器人逐渐崭露头角。
铁路机车行业由于我国货运、客运、城市地铁等需求量的不断增加以及列车提速的需求,机器人的需求一直处于稳步增长态势。
据2001年统计,全国共有各类焊接机器人1040
台,汽车制造和汽车零部件生产企业中的焊接机器人占全部焊接机器人的76%。
在汽车行业中点焊机器人与弧焊机器人的比例为3∶2,其他行业大都是以弧焊机器人为主,主要分布在工程机械(10%)、摩托车(6%)、铁路车辆(4%)、锅炉(1%)等行业。
焊接机器人也主要分布在全国几大汽车制造厂。
目前在我国应用的机器人主要分日系、欧系和国产三类。
日系中主要有安川、OTC、松下、FANUC、不二越、川崎等公司的产品。
欧系中主要有德国KUKA、CLOOS,瑞典ABB,意大利AU和奥地利IGM公司。
国产机器人主要是XX新松机器人公司产品。
目前在我国虽然已经具有自主知识产权的焊接机器人系列产品,但却不能批量生产,形成规模,究其原因有以下几点:
(1)国内机器人价格没有优势。
近十年来,进口机器人的价格大幅度降低,从7~8万美元/台降低到2~3万美元/台,使我国自行制造的普通工业机器人在价格上很难与之竞争。
特别是我国在研制机器人的初期,没有同步发展相应的零部件产业,如伺服电机、减速机等需要进口,使价格难以降低,所以机器人生产成本高;
加之我国焊接装备水平与国外还存在很大差距,也间接影响了国内机器人的发展。
对于机器人的最大用户———一汽白车身生产厂来说,几乎所有的装备都是从国外引进,国产机器人找不到表演的舞台。
(2)国产机器人无论从控制水平还是可靠性等方面与国外公司还存在一定的差距。
国外工业机器人是个非常成熟的工业产品,经历了30多年的发展历程,而且在实际生产中不断地完善和提高;
而我国尚处于单件小批量的生产状态。
(3)国内机器人生产厂家处于幼儿期还需要政府政策和资金的支持。
焊接机器人是个机电一体化的高技术产品,单靠企业的自身能力是不够的,需要政府对机器人生产企业和使用国产机器人系统的企业给予一定的政策和资金支持,加速我国国产机器人的发展。
3、焊接机器人技术的研究现状
机器人技术是综合了计算机、控制论、机构学、信息和传感技术、人工智能、仿生学等多学科而形成的高新技术。
从国内外研究现状来看,焊接机器人技术研究主要集中在焊缝跟踪技术、离线编程与路径规划技术、多机器人协调控制技术、专用弧焊电源技术、焊接机器人系统仿真技术、机器人用焊接工艺方法、遥控焊接技术七个方面。
四、组成结构
焊接机器人主要包括机器人和焊接设备两部分。
机器人由机器人本体和控制柜(硬件及软件)组成。
而焊接装备,以弧焊及点焊为例,则由焊接电源,(包括其控制系统)、送丝机(弧焊)、焊枪(钳)等部分组成。
对于智能机器人还应有传感系统,如激光或摄像传感器及其控制装置等。
图1a、b表示弧焊机器人和点焊机器人的基本组成。
世界各国生产的焊接用机器人基本上都属关节机器人,绝大部分有6个轴。
其中,1、2、3轴可将末端工具送到不同的空间位置,而4、5、6轴解决工具姿态的不同要求。
焊接机器人本体的机械结构主要有两种形式:
一种为平行四边形结构,一种为侧置式(摆式)结构,如图2a、b所示。
侧置式(摆式)结构的主要优点是上、下臂的活动范围大,使
焊接机器人示意图
机器人的工作作空间几乎能达一个球体。
因此,这种机器人可倒挂在机架上工作,以节省占地面积,方便地面物件的流动。
但是这种侧置式机器人,2、3轴为悬臂结构,降低机器人的刚度,一般适用于载较小的机器人,用于电弧焊、切割或喷涂。
平行四边形机器人其上臂是通过一根拉杆驱动的。
拉杆与下臂组成一个平行四边形的两条边。
故而得名。
早期开发的平行四边形机器人工作空间比较小(局限于机器人的前部),难以倒挂工作。
但80年代后期以来开发的新型平行四边形机器人(平行机器人),已能把工作空间扩大到机器人的顶部、背部及底部,又没有测置式机器人的刚度问题,从而得到普遍的重视。
这种结构不仅适合于轻型也适合于重型机器人。
近年来点焊用机器人(负载100~150kg)大多选用平行四边形结构形式的机器人。
上述两种机器人各个轴都是作回转运动,故采用伺服电机通过摆线针轮(RV)减速器(1~3轴)及谐波减速器(1~6轴)驱动。
在80年代中期以前,对于电驱动的机器人都是用直流伺服电机,而80年代后期以来,各国先后改用交流伺服电机。
由于交流电机没有碳刷,动特性好,使新型机器人不仅事故率低,而且免维修时间大为增长,加(减)速度也快。
一些负载16kg以下的新的轻型机器人其工具中心点(TCP)的最高速度可达3m/s以上,定位准确,振动小。
同时,机器人的控制柜也改用32位的微机和新的算法,使之具有自行优化路径的功能,运行轨迹更加贴近示教的轨迹。
五、焊接机器人的特点
点焊对焊接机器人的要求不是很高。
因为点焊只需点位控制,至于焊钳在点与点之间的移动轨迹没有严格要求,这也是机器人最早只能用于点焊的原因。
点焊用机器人不仅要有足够的负载能力,而且在点与点之间移位时速度要快捷,动作要平稳,定位要准确,以减少移位的时间,提
机械手臂
高工作效率。
点焊机器人需要有多大的负载能力,取决于所用的焊钳形式。
对于用与变压器分离的焊钳,30~45kg负载的机器人就足够了。
但是,这种焊钳一方面由于二次电缆线长,电能损耗大,也不利于机器人将焊钳伸入工件内部焊接;
另一方面电缆线随机器人运动而不停摆动,电缆的损坏较快。
因此,目前逐渐增多采用一体式焊钳。
这种焊钳连同变压器质量在70kg左右。
考虑到机器人要有足够的负载能力,能以较大的加速度将焊钳送到空间位置进行焊接,一般都选用100~150kg负载的重型机器人。
为了适应连续点焊时焊钳短距离快速移位的要求。
新的重型机器人增加了可在0.3s内完成50mm位移的功能。
这对电机的性能,微机的运算速度和算法都提出更高的要求。
六、焊接机器人系统主要由以下几个部分组成:
机械本体系统、传感系统、控制系统。
机器人系统原理图如图1所示。
机械本体系统是轮式移动机器人及其附属部件,该机器人采用两轮差速驱动,在前面增加一万向轮实现机器人本体的移动。
焊炬固定在十字滑块上,通过控制十字滑块的上下和左右运动,控制焊炬的升降和伸缩。
焊接系统包含焊接电源、送丝机、保护气,用于实现机器人的焊接作业。
传感系
统是采用旋转电弧传感器作为焊枪,结构紧凑,实时性、可达性都很好;
霍尔传感器采集焊接电流信号;
超声波传感器置于机体前端,采集障碍物的信号;
在机体底盘四角有4个光电传感器,用于检测机器人是否移动到边角,防止跌落。
控制系统用于机器人的控制,主要是实现机器人的移动跟踪、焊接的起弧与停弧等控制。
本次控制系统的设计目标是设计一个控制箱,能够达到机器人的控制要求,并且小型化,以简化机器人的尺寸和重量。
6.1机器人控制系统总体设计
控制系统实行模块化设计,分为:
电源模块、中央控制模块、驱动模块、信号采集与处理模块、旋转电弧电机调速模块、防跌落模块。
控制系统原理图如图2所示。
电源模块用于对输入电压进行转换,以提供各个模块的供电。
中央控制模块实现对系统的控制功能。
信号采集与处理模块是采集机器人的位置及焊接电流等信号,作为控制模块的输入信号。
驱动模块
根据控制信号做出相应动作,完成机器人的焊缝跟踪。
旋转电弧调速模块用于稳定旋转电弧电机的转速,减小转速偏差造成的干扰。
防跌落模块是防止机器人到达边角落时跌落而造成损失。
6.2控制系统硬件设计与选型
6.2.1电源模块
机器人输入为+24V直流稳压电源,需要设计一块电源转换板,将+24V电压转换为+5V、+12V、-12V,满足各个模块不同电压的要求。
PCM-3343采用+5V供电,步进电机是+12V供电,霍尔传感器需要+12V、-12V电压。
3.2中央控制模块采用研华PCM-3343,这是一款嵌入式工控主机,单+5V供电,功耗较低。
PCM-3343基于PC104总线,兼容能力强,尺寸小,可以显著减小设计尺寸。
PC104总线模块之间是堆栈式连接,即上下层是通
过针和孔相互咬合相连,这种层叠封装有极好的抗震性、抗冲击性能好、可靠性高,这对于采用旋转电弧的本型机器人(电机偏置旋转有一定的振动),无疑也是很重要的性能。
拥有基本工控机的资源,能够满足焊接机器人的控制要求。
6.2.2信号采集与处理模块
采用ART2932数据采集卡。
电弧旋转时,光耦得到信号,经过LM353进行电压比较,将采集的信号输入ART2932,信号处理后即可得出焊炬的位置。
水平和垂直滑块上各安装有左、中、右三个限位光耦。
这三个光耦用来限制电机防止堵转,并且测得滑块的大概位置。
机器人的头部装有超声波传感器,用于测量机器人与前面的障碍物的距离,超声传感器信号输入ART2932,经过信号处理得出机器人位置。
霍尔传感器检测焊接电流信号,根据焊炬位置的高度变化与焊接电流信号间的变换关系,可推导出焊炬相对焊缝位置,实现焊缝的跟踪。
6.2.3驱动模块
本系统采用ART1020运动控制卡,这是PC104总线四轴伺服/步进电机运动控制卡,它以高频率脉冲串形式输出,可以控制伺服/步进电机的运动。
这款控制卡能够精确控制所发出的的脉冲频率(即
电机速度)、脉冲个数(电机转角)以及脉冲频率变化率(电机加速度),能够满足步进电机的各种复杂的控制要求。
此控制卡可以独立控制4轴驱动,而本系统有左右两轮,水平、