橡胶注射成型机设备行业应用项目可行性研究报告Word格式文档下载.docx
《橡胶注射成型机设备行业应用项目可行性研究报告Word格式文档下载.docx》由会员分享,可在线阅读,更多相关《橡胶注射成型机设备行业应用项目可行性研究报告Word格式文档下载.docx(14页珍藏版)》请在冰豆网上搜索。
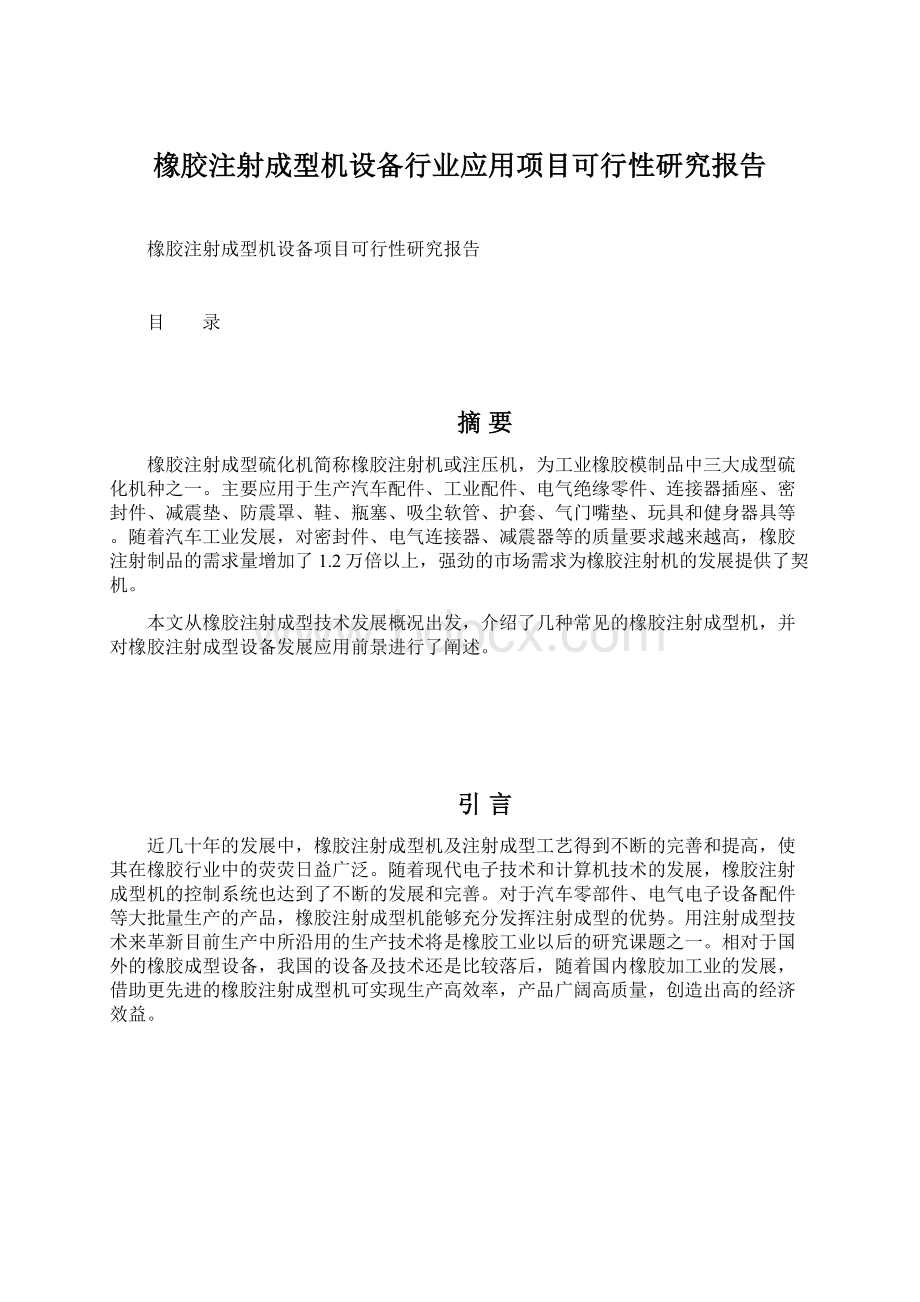
随着现代电子技术和计算机技术的发展,橡胶注射成型机的控制系统也达到了不断的发展和完善。
对于汽车零部件、电气电子设备配件等大批量生产的产品,橡胶注射成型机能够充分发挥注射成型的优势。
用注射成型技术来革新目前生产中所沿用的生产技术将是橡胶工业以后的研究课题之一。
相对于国外的橡胶成型设备,我国的设备及技术还是比较落后,随着国内橡胶加工业的发展,借助更先进的橡胶注射成型机可实现生产高效率,产品广阔高质量,创造出高的经济效益。
1橡胶注射成型技术发展概况
1.1橡胶注射成型简介
注射成型又称注射模型或注塑,就是通过塑化缸的加温和塑化螺杆的搅拌、剪切,将胶料温度升高到其流动性最好的状态,再通过较高的注射压力,将此状态的胶料注射到锁模(抽真空)的模腔中,进行加压和加温,使橡胶进行硫化,在整个过程中,时间、压力和温度三要素决定了生产的效率和质量。
是橡胶加工中重要的成型方法之一,其技术已发展得相当成熟,且应用非常普遍,注塑制品已占橡胶制品总量的30%以上,在国民经济的许多领域有着广泛的应用。
就橡胶本身的特性来说,注射成型以其独有的优势目前已经成为橡胶制品成型的主流方式[1]。
首先,注射成型能够提高制品质量。
通过先锁模后注射并进行保压,可以持续稳定的传递制品成型所需要的压力,使制品能够在可控的压力、温度和时间下进行硫化。
注射成型能够提高制品的致密性和功能性(尤其是减震制品的功能性)。
其次,注射成型可大幅提高生产效率。
通过注射单元的塑化功能,大幅度提高胶料的流动性,使其以比较高的温度充满模腔并立刻开始硫化,通过合理的参数设置,注射工艺可比模压工艺缩短30~50%的硫化时间。
再次,注射成型工艺能够大幅度降低工人劳动强度、减少胶料浪费和电力消耗等
1.2橡胶注射成型发展历史
注射成型机是随着PMMA(聚甲基丙烯酸甲酯)塑料工业的发展而兴起的,最初的注射成型机是参照金属压铸机的原理设计的,直到1932年才由德国布劳恩厂生产出第一台全自动柱塞式注射成型机。
随着塑料工业的发展,注射成型机的新产品也在不断出现。
橡胶注射机概念在20世纪40年代中期被提出,1948年.注射成型机的塑化装置开始使用螺杆;
1959年,第一台螺杆式注射成型机问世,这是塑料工业的一大突破,推动了注射成型的广泛应用。
70年代初,橡胶冷喂料注射开始在工业中得到实际应用。
由于它能实现高温快速硫化、胶料进入模腔前经过预热和塑化,制品在密封高压的模腔内成型硫化,产品质量均匀稳定,尺寸准确、可以实现全自动操作,与传统的模压法相比生产效率可提高十倍以上,因此用橡胶冷喂料注射机生产模压制品的技术得到日益广泛的应用。
随着电子工业的飞速发展,注射成型机也随之发展,其性能得到了迅速提高。
很多新技术,如集成电路、电脑控制等被引入注射成型机的控制系统中.动作的准确性已达到很高的水平,对注射模的保护有了很大的提高,塑件的质量也有了可靠保证。
随着机械工业的发展,各种新型注射成型机正陆续被研制出来,超大容量的注射成型机也随之出现,它的一次注射量可达几十万克,大大拓宽了注射产品的应用范围,也推动了塑料工业的发展。
而在橡胶机械中,注射成型机要占到橡胶机械的一半。
目前,在国际上生产橡胶注射机的主要厂家有:
法国的REP公司、奥地利MAPLAN公司、德国WP公司、STEINL公司和DESMA、日本松田制作所、神户机械株式会社、三友株式会社、日本制钢所,意大利RUTIL公司等。
70年代初期,北京化工大学与上海某厂合作,开发研制成功XZL-200螺杆预塑一线式橡胶注射成型硫化机。
注射成型机是橡胶成型设备中产量最多、增长最快、应用最广的机种,为注射制品的广泛应用打下了坚实的基础.而注射技术经历了移植、技术成熟、发展创新几个阶段[2]。
1.2.1技术移植阶段
1920年以前,早期的橡胶注射成型技术是从其它材料的加工方法(如铸造、热成型)中借鉴过来的,成型技术主要是移植改造,使粘弹性高的胶料熔体成型。
而最初的注射成型机是参照金属压铸机的原理设计的。
1.2.2技术成熟阶段
1920-1970年,聚碳酸酯(PC)、聚甲醛(PCM)、聚苯醚(PPO)、聚砜(PSU)、聚酰亚胺(PI)、环氧树脂(EP)、不饱和聚酯(LP)等一大批高性能塑料的出现,要求注射成型加工技术向更高的阶段发展。
同时,随着橡胶成型设备设计和制造技术的不断进步,以及橡胶成型加工理论研究的不断深入,为橡胶成型加工技术的提高创新提供了条件;
往复式螺杆注塑机、双螺杆挤出机的出现,使热敏性和高熔体粘度的热塑性、热固性橡胶都采用高效的成型技术生产出高质量的制品。
反应注塑技术使一些特殊的液态单体或低聚物的聚合成型成为可能。
这一切标志着橡胶成型加工已从改造、移植为主的时期过渡到了技术成熟时期。
1.2.3发展创新阶段
1970年以后,随着科技的发展,控制技术、计算机技术的引入,促使橡胶制品的生产过程从机械化、自动化进一步向连续化、程序化和自适应控制的方向发展。
此阶段的橡胶成型加工技术与前一时期相比,在可加工原材料的范围、制品的范围和制品质量等方面均有重林突破,不仅以往难以成型的热敏性、高熔体粘度的原料能方便地加工成制品,而且长纤维增强橡胶、片状和团状模橡胶也被用作高效成型技术的原材料。
2几种常见的橡胶注射成型设备
2.1橡胶注射成型机种类及成型方法
橡胶注射成型机按排列方式分类可分为:
立式注射机,卧式注射机,全电式注塑机;
按塑化方式分类可分为:
柱塞式注射成型机,螺杆往复式注射成型机,螺杆柱塞式注射成型机;
按合模机构特征分类可分为:
机械式注射成型机,液压式注射成型机,液压机械式注射成型机。
虽然橡胶注射成型机的种类繁多,但到目前为止,橡胶注射成型的经历可归为3个阶段:
柱塞式注射、螺杆往复式注射和螺杆柱塞式注射。
本章节主要介绍这三个阶段的橡胶注射成型机的结构和成型方法。
2.1.1柱塞式注射成型机
柱塞式注射成型机是最早的橡胶注射成型设备。
如图1柱塞式注射成型机
1-机身2-电动机及液压泵3-注射液压缸4-加料调节装置5-注射柱塞
6-加料杆7-料斗8-料筒9-分流梭10-定模固定板(安装板)11-模具12-拉杆
13-动模固定板14-合模机构15-合模液压缸16-喷嘴17-加热器18-油箱
图1柱塞式注射成型机
注射成型方法是:
将胶料从喂料口喂入料筒后,由料筒外部的加热器对胶料进行加热、塑化,使胶料达到易于注射而又不会焦烧的温度为止。
最后由柱塞将已塑化胶料高压注入模具中。
实际上,这种注射方法料筒主要起注射作用,辅以加热塑化作用。
因为橡胶为热的不良导体,传热效率低,如果仅仅通过热传导来加热胶料,胶料温度上升太慢,而且塑化的不均匀。
因此需要将胶料先在热炼机中热炼,热炼到一定程度后再喂入注射机中。
因此这种注射成型法虽然注射机本身结构简单,成本低,但是需要配置热炼机和炼胶工人,从而增加了设备成本和工人劳动强度,最重要的是这种注射成型方法生产效率低,塑化不均匀,从而影响到制品的质量。
2.1.2螺杆往复式注射成型机
为了提高产品效率和制品质量,人们又发明了另一种橡胶注射成型设备。
即在挤出机的基础上加以改进,将螺杆的纯转动改成既能转动以进行胶料的塑化,又可以进行轴向移动以将胶料注入到模腔中。
这就是往复式螺杆注射成型机。
如图2往复式螺杆注射成型机。
1-机身2-电动机及液压泵3-注射液压缸4-齿轮箱5-齿轮传动电动机6-料斗7-螺杆
8-加热器9-料筒10-喷嘴11-定模固定板12-模具13-拉杆14-动模固定板
15-合模机构16-合模液压缸17-螺杆转动齿轮18-螺杆花键19-油箱
图2螺杆往复式注射成型机
胶料从喂料口进入注射机后,在螺杆的旋转作用下受到强烈的剪切,胶温很快升高。
当胶料沿螺杆移动到螺杆的前端时,已得到充分而均匀的塑化。
螺杆一边旋转一边向后移动,当螺杆前端积聚的胶料达到所需要的注射量时,轴向动力机构以强大的推力推动螺杆向前移动,从而将胶料注入模腔。
这种往复式注射成型方法,胶料的塑化是通过机械剪切获得,因而胶料升温快,塑化均匀,这样一来生产效率和制品质量都得到提高。
另外由于这种注射成型方法可以直接将冷胶料喂入注射机中,从而省去了热炼工序,减少了设备投资和设备占地面积,同时提高了生产效率,降低了劳动强度。
然而在生产大型制品时,螺杆后移量过大,胶料的塑化受到限制,另外这种机器的螺杆棱峰与机筒内壁之间间隙较大,注射时易导致逆流和漏流现象,致使部分胶料反覆停留,易产生焦烧,从而注射压力也受到限制,所以往复式螺杆注射机只能用于低粘度胶料,小体积制品的生产中。
2.1.3螺杆柱塞式注射成型机
为了解决以上两种注射机的不足,人们将这两种注射机结合起来,取长补短,这就是目前应用较多的螺杆—柱塞式注射成型机。
这种机器的注射部分主要由螺杆塑化系统和柱塞注射系统组成。
如图3螺杆—柱塞式注射成型机。
1-喷嘴2-机筒3-加料装置4-螺杆驱动装置5-注射油缸
6-注射柱塞7-螺杆
图3螺杆柱塞式注射成型机
注射成型工艺过程为:
首先将冷胶料喂入螺杆塑化系统,胶料经螺杆塑化后,挤入到柱塞注射系统中,最后由柱塞将胶料注射到模腔中。
为了使胶料按照一定的顺序流动,在螺杆挤出机的端部安装一个止逆阀,胶料塑化后通过止逆阀进入注射系统中并将柱塞顶起,这时胶料不会从喷嘴出去,因为喷嘴通道狭窄,阻力大。
当柱塞将胶料以高压从喷嘴注入模腔时,因为止逆阀的作用,胶料不会倒流进入注射机中。
由于这种注射成型方法结合了柱塞式注射机和螺杆式注射机的优点,因此它可以生产大型、高质量的橡胶制品。
塑化系统与注射系统安装方式,有时可能会出现一些缺陷,因为最先注入注射室的胶料最后注射到模腔中,这样可能会使与柱塞端面接触的胶料停留时间太长而导致硫化,从而出现废品等问题。
大型设备更容易出现这种情况。
工作顺序为先进先出的注射机可以解决这一问题。
先进先出注射机虽然也分成螺杆塑化和柱塞注射两部分,但这两部分是安装在一条直线上的,工作开始时,柱塞位于前面位置上,当已塑化的胶料从螺杆前端,通过柱塞进入注射室后,柱塞在胶料压力作用下开始向后退,一直到注射室充满所需注射量为止,柱塞停止向后移动。
接着动力部分驱动柱塞向前移动,进行高压注射,另外,胶料在进入模具之前通过一个球型分流梭时,得到进一步塑化,胶料温度更加均匀一致。
2.2螺杆柱塞式注射机主要装置结构和性能特点
本节结合自己的实习工作情况,主要以螺杆—柱塞式注射机为例讲述橡胶注射成型设备的主要装置结构和一些性能特点。
2.2.1预塑注射装置
预塑注射装置由塑化和注射部件组成,通常分为螺杆挤出式、柱塞式、螺杆往复式和带预塑螺杆的柱塞式数种。
它的作用是均匀地加热和塑化胶料,通过喷嘴将塑化好的胶料注入模腔,注射完毕进行保压,使模腔内的胶料在设定的压力下保持一定时间,以防止胶料逆流而造成制品组织疏松和表面不平整。
保压的压力一般为80-120MPa,高者可达60%-80%的实