SIP封装工艺流程Word下载.docx
《SIP封装工艺流程Word下载.docx》由会员分享,可在线阅读,更多相关《SIP封装工艺流程Word下载.docx(25页珍藏版)》请在冰豆网上搜索。
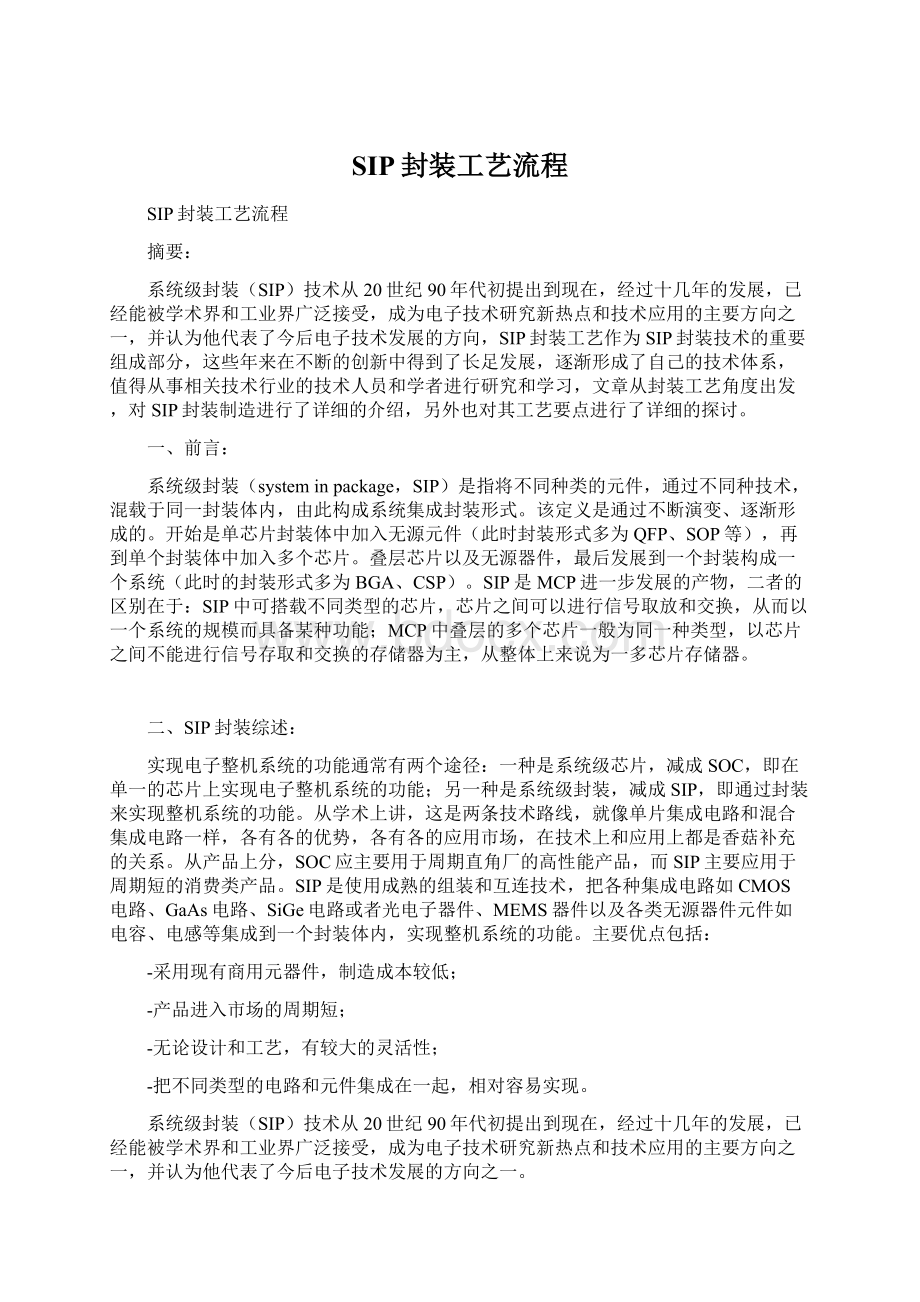
另一种是系统级封装,减成SIP,即通过封装来实现整机系统的功能。
从学术上讲,这是两条技术路线,就像单片集成电路和混合集成电路一样,各有各的优势,各有各的应用市场,在技术上和应用上都是香菇补充的关系。
从产品上分,SOC应主要用于周期直角厂的高性能产品,而SIP主要应用于周期短的消费类产品。
SIP是使用成熟的组装和互连技术,把各种集成电路如CMOS电路、GaAs电路、SiGe电路或者光电子器件、MEMS器件以及各类无源器件元件如电容、电感等集成到一个封装体内,实现整机系统的功能。
主要优点包括:
-采用现有商用元器件,制造成本较低;
-产品进入市场的周期短;
-无论设计和工艺,有较大的灵活性;
-把不同类型的电路和元件集成在一起,相对容易实现。
系统级封装(SIP)技术从20世纪90年代初提出到现在,经过十几年的发展,已经能被学术界和工业界广泛接受,成为电子技术研究新热点和技术应用的主要方向之一,并认为他代表了今后电子技术发展的方向之一。
三、SIP封装类型:
从目前业界SIP的设计类型和结构区分,SIP可分为三类。
3.12DSIP
此类封装是在同一个封装基板上将芯片一个挨一个的排列以二维的模式封装在一个封装体内。
3.2
堆叠SIP
此类封装是在一个封装中采用物理的方法将两个或多个芯片堆叠整合起来进行封装。
3.33DSIP
此类封装是在2D封装的基础上,把多个罗芯片、封装芯片、多芯片甚至圆片进行叠层互联,构成立体封装,这种结构也称作叠层型3D封装。
四、SIP封装的制程工艺:
SIP封装制程按照芯片与基板的连接方式可分为引线键合封装和倒装焊两种。
4.1引线键合封装工艺
圆片→圆片减薄→圆片切割→芯片粘结→引线键合→等离子清洗→液态密封剂灌封→装配焊料球→回流焊→表面打标→分离→最终检查→测试→包装。
4.1.1圆片减薄
圆片减薄是指从圆片背面采用机械或化学机械(CMP)方式进行研磨,将圆片减薄到适合封装的程度。
由于圆片的尺寸越来越大,为了增加圆片的机械强度,防止在加工过程中发生变形、开裂,其厚度也一直在增加。
但是随着系统朝轻薄短小的方向发展,芯片封装后模块的厚度变得越来越薄,因此在封装之前一定要将圆片的厚度减薄到可以接受的程度,以满足芯片装配的要求。
4.1.2圆片切割
圆片减薄后,可以进行划片。
较老式的划片机是手动操作的,现在一般的划片机都已实现全自动化。
无论是部分划线还是完全分割硅片,目前均采用锯刀,因为它划出的边缘整齐,很少有碎屑和裂口产生。
4.1.3芯片粘结
已切割下来的芯片要贴装到框架的中间焊盘上。
焊盘的尺寸要和芯片大小相匹配,若焊盘尺寸太大,则会导致引线跨度太大,在转移成型过程中会由于流动产生的应力而造成引线弯曲及芯片位移现象。
贴装的方式可以是用软焊料(指
Pb-Sn
合金,尤其是含
Sn
的合金)、Au-Si
低共熔合金等焊接到基板上,在塑料封装中最常用的方法是使用聚合物粘结剂粘贴到金属框架上。
4.1.4引线键合
在塑料封装中使用的引线主要是金线,其直径一般为0.025mm~0.032mm。
引线的长度常在1.5mm~3mm之间,而弧圈的高度可比芯片所在平面高
0.75mm。
键合技术有热压焊、热超声焊等。
这些技术优点是容易形成球形(即焊球技术),并防止金线氧化。
为了降低成本,也在研究用其他金属丝,如铝、铜、银、钯等来替代金丝键合。
热压焊的条件是两种金属表面紧紧接触,控制时间、温度、压力,使得两种金属发生连接。
表面粗糙(不平整)、有氧化层形成或是有化学沾污、吸潮等都会影响到键合效果,降低键合强度。
热压焊的温度在
300℃~400℃,时间一般为
40ms(通常,加上寻找键合位置等程序,键合速度是每秒二线)。
超声焊的优点是可避免高温,因为它用20kHz~60kHz的超声振动提供焊接所需的能量,所以焊接温度可以降低一些。
将热和超声能量同时用于键合,就是所谓的热超声焊。
与热压焊相比,热超声焊最大的优点是将键合温度从
350℃降到250℃左右(也有人认为可以用100℃~150℃的条件),这可以大大降低在铝焊盘上形成
Au-Al
金属间化合物的可能性,延长器件寿命,同时降低了电路参数的漂移。
在引线键合方面的改进主要是因为需要越来越薄的封装,有些超薄封装的厚度仅有0.4mm
左右。
所以引线环(loop)从一般的200
μ
m~300
m减小到100μm~125μm,这样引线张力就很大,绷得很紧。
另外,在基片上的引线焊盘外围通常有两条环状电源
/
地线,键合时要防止金线与其短路,其最小间隙必须>
625
m,要求键合引线必须具有高的线性度和良好的弧形。
4.1.5等离子清洗
清洗的重要作用之一是提高膜的附着力,如在Si
衬底上沉积
Au
膜,经
Ar
等离子体处理掉表面的碳氢化合物和其他污染物,明显改善了Au
的附着力。
等离子体处理后的基体表面,会留下一层含氟化物的灰色物质,可用溶液去掉。
同时清洗也有利于改善表面黏着性和润湿性。
4.1.6液态密封剂灌封
将已贴装好芯片并完成引线键合的框架带置于模具中,将塑封料的预成型块在预热炉中加热(预热温度在
90℃~95℃之间),然后放进转移成型机的转移罐中。
在转移成型活塞的压力之下,塑封料被挤压到浇道中,并经过浇口注入模腔(在整个过程中,模具温度保持在
170℃~175℃左右)。
塑封料在模具中快速固化,经过一段时间的保压,使得模块达到一定的硬度,然后用顶杆顶出模块,成型过程就完成了。
对于大多数塑封料来说,在模具中保压几分钟后,模块的硬度足可以达到允许顶出的程度,但是聚合物的固化(聚合)并未全部完成。
由于材料的聚合度(固化程度)强烈影响材料的玻璃化转变温度及热应力,所以促使材料全部固化以达到一个稳定的状态,对于提高器件可靠性是十分重要的,后固化就是为了提高塑封料的聚合度而必需的工艺步骤,一般后固化条件为
170℃~175℃,2h~4h。
4.1.7装配焊料球
目前业内采用的植球方法有两种:
“锡膏”+“锡球”和“助焊膏”+
“锡球”。
“锡膏”+“锡球”植球方法是业界公认的最好标准的植球法,用这种方法植出的球焊接性好、光泽好,熔锡过程不会出现焊球偏置现象,较易控制,具体做法就是先把锡膏印刷到
BGA
的焊盘上,再用植球机或丝网印刷在上面加上一定大小的锡球,这时锡膏起的作用就是粘住锡球,并在加温的时候让锡球的接触面更大,使锡球的受热更快更全面,使锡球熔锡后与焊盘焊接性更好并减少虚焊的可能。
4.1.8表面打标
打标就是在封装模块的顶表面印上去不掉的、字迹清楚的字母和标识,包括制造商的信息、国家、器件代码等,主要是为了识别并可跟踪。
打码的方法有多种,其中最常用的是印码方法,而它又包括油墨印码和激光印码二种。
4.1.9分离工艺
为了提高生产效率和节约材料,大多数
SIP
的组装工作都是以阵列组合的方式进行,在完成模塑与测试工序以后进行划分,分割成为单个的器件。
划分分割可以采用锯开或者冲压工艺,锯开工艺灵活性比较强,也不需要多少专用工具,冲压工艺则生产效率比较高、成本较低,但是需要使用专门的工具。
4.2倒装焊
和引线键合工艺相比较倒装焊工艺具有以下几个优点:
(1)倒装焊技术克服了引线键合焊盘中心距极限的问题;
(2)在芯片的电源
/地线分布设计上给电子设计师提供了更多的便利;
(3)通过缩短互联长度,减小
RC
延迟,为高频率、大功率器件提供更完善的信号;
(4)热性能优良,芯片背面可安装散热器;
(5)可靠性高,由于芯片下填料的作用,使封装抗疲劳寿命增强;
(6)便于返修。
以下是倒装焊的工艺流程(与引线键合相同的工序部分不再进行单独说明):
圆片→焊盘再分布→圆片减薄、制作凸点→圆片切割→倒装键合、下填充→包封→装配焊料球→回流焊→表面打标→分离→最终检查→测试→包装。
4.2.1焊盘再分布
为了增加引线间距并满足倒装焊工艺的要求,需要对芯片的引线进行再分布。
4.2.2制作凸点
焊盘再分布完成之后,需要在芯片上的焊盘添加凸点,焊料凸点制作技术可采用电镀法、化学镀法、蒸发法、置球法和焊膏印刷法。
目前仍以电镀法最为广泛,其次是焊膏印刷法。
4.2.3倒装键合、下填充
在整个芯片键合表面按栅阵形状布置好焊料凸点后,芯片以倒扣方式安装在封装基板上,通过凸点与基板上的焊盘实现电气连接,取代了WB和TAB
在周边布置端子的连接方式。
倒装键合完毕后,在芯片与基板间用环氧树脂进行填充,可以减少施加在凸点上的热应力和机械应力,比不进行填充的可靠性提高了1到2个数量级。
五、封装的基板
封装基板是封装的重要组成部分,在封装中实现搭载器件和电气连同的作用,随着封装技术的发展,封装基板的设计、制造技术有了长足的进步。
2001年国际半导体技术发展预测机构(ITRS)设定半导体芯片尺寸为310mm2,但随着元件IO数目的不断增加,就必须增加基板上的端子数量,对封装基板有了更精细化的要求,从而对封装基板的加工和设计有了更严格要求。
5.1封装几班的分类
封装基板的分类有很多种,目前业界比较认可的是从增强材料和结构两方面进行分类。
从结构方面来说,基板材料可分为两大类:
刚性基板材料和柔性基板材料。
刚性基板材料使用较为广泛,一般的刚性基板材料主要为覆铜板。
它是用增强材料,浸以树脂胶黏剂,通过烘干、裁剪、叠合成坯料,然后覆上一层导电率较高、焊接性良好的纯铜箔,用钢板作为模具,在热压机中经高温高压成型加工而制成。
从增强材料方面分类,基板可以分为有有机系(树脂系)、无机系(陶瓷系、金属系)和复合系,前两种材料在性能上各有优缺点,而复合机系的出现综合了两者的优点,很快成为基板的发展方向。
目前基板多采用有机系材料,也就是统称的BT树脂,改材料可分为CCL-H810、CCl-H870、CCL-HL870、CCL-HL950,介电常数在3.5
~4.5(1MHz)之间,介电损耗为0.001~0.005(1MHz),玻璃转化温度为180~230℃。
5.2封装基板的设计规则
从封装基板常规制程来看,封装基板的生产与常规的PCB加工很类似,只是在要求上更为严格,规则的要求更为具体,需要更薄的叠层,更细的线宽线距以及更小的孔,具体参数各个板厂略有差异。
5.3封装基板的制程
常规的封装基板的制程与普通PCB的加工方法大体一致,但是目前为了满足封装基板的精细化要求出现了减成