红参工艺验证质量风险评估表文档格式.doc
《红参工艺验证质量风险评估表文档格式.doc》由会员分享,可在线阅读,更多相关《红参工艺验证质量风险评估表文档格式.doc(9页珍藏版)》请在冰豆网上搜索。
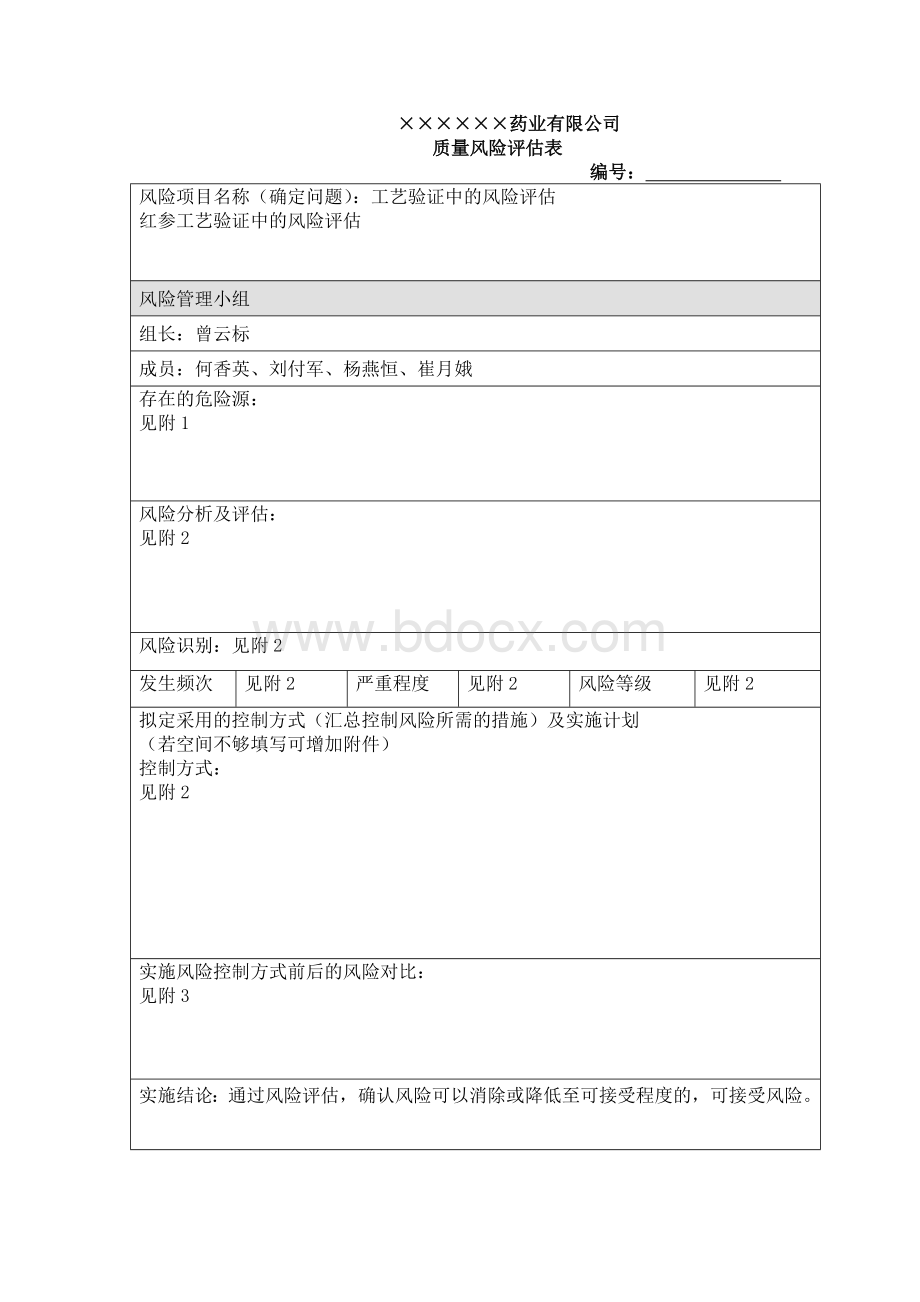
(若空间不够填写可增加附件)
控制方式:
实施风险控制方式前后的风险对比:
见附3
实施结论:
通过风险评估,确认风险可以消除或降低至可接受程度的,可接受风险。
附件1
安全性特征问题清单及可能危害分析表:
序号
问题内容
特征判定
可能的危害
1
不按规定进入生产区
不按规定进入生产区,污染饮片
给使用者带来危害
2
容器已清洁,是否在效期内
容器污染,造成污染或混药事故
产生杂质超标或混药事故
3
洁具污染
洁具污染,污染饮片
4
红参领料复核
领料没复核,称量不准
计算不准,带来偏差
5
操作人员技术不熟练
操作不到位,造成违规操作
质量不合格
6
未培训或培训不到位
想当然操作,造成违规操作
7
无工艺规程
无工艺规程,无法指导生产
质量不可控
8
无SOP等或操作性差
无SOP等或操作性差,无法指导生产
9
净制间有无清场合格证,与本批产品不相符合的物料、文件
产生污染
10
净度不够
挑选不够仔细,造成净度不符合要求;
违反SOP,质量不合格
11
润制间有无清场合格证,与本批产品不相符合的物料、文件
12
润制的时间不够或超长
润制时间加长,造成松软膨胀,时间不够,温度太低,导致润制不透心,影响切片;
13
润制的温度不够
温度不够,润制不透心,
14
润制铺参的厚度
平铺一层,太多,润制不透心
15
切制间有无清场合格证,与本批产品不相符合的物料、文件
16
切刀钝化
厚薄不均
17
切片厚度不符合
太薄或太厚
18
干燥间有无清场合格证,与本批产品不相符合的物料、文件
19
干燥过头或不到位
干燥时间过长,影响有效成分;
干燥时间不够,水分太高
20
干燥的温度
干燥温度过高,影响有效成分;
干燥温度不够,水分太高
21
铺盘的厚度
铺盘太厚,影响干燥效果
22
监控不力
生产部监控不正常或发现问题不制止,造成失控
QA监控不正常或发现问题不制止,造成失控
违反GMP,质量不合格
23
无监控
生产部不到现场监控
QA不到现场监控
24
记录不及时或伪造
预报性或回忆性记录,记录不及时,内容失真,无法追溯;
伪造记录,严重违反GMP,诚信缺失。
严重违反GMP,诚信缺失,质量无法追溯
25
伪造批记录
伪造批记录,严重违反GMP,诚信缺失。
26
记录等未审核或审核不严
未审核,胡乱签名,违反GMP,过程失控
审核不严,胡乱签名,违反GMP,过程失控
27
检验仪器未校正
造成检测数据失准,带来工艺失控,饮片质量不合格
质量合格成为不合格,质量不合格变为合格
28
没按要求检验或没检
29
质量限度标准不合理
因质量限度标准太低,造成实物质量低于法定标准;
或质量限度标准太高,造成实物质量不合格;
质量不合格成为合格,质量合格变为不合格
30
不按规定清场
不按规定清场,造成污染或混药事故
31
未清场
未清场,造成污染或混药事故
32
包装装量
装量不合格
附件2
危害判断及风险控制措施表:
对每一项可能失败因素、严重性、发生的可能性进行等级划分并评定,以及采取的控制措施,具体记录如下表:
可能失败因素
措施
按规定进入生产区,并安装监控装置,发现违规者按规定处理
按规定清洗容器,并在有效期内,超有效期,使用前按规定重新清洁
按规定保管好洁具,防止污染,一旦发现立即清洗
百合领料复核
双人复核,确保称量准确
开展针对性培训和师带徒活动,提高技术水平
按规定培训,并做好师带徒工作
按规定编制完善工艺规程
按规定编制完善SOP,提高可操作性
生产前检查生产操作间有无清场合格证,及与本批产品不相符合的物料、文件
按《红参净制标准操作程序》进行净制
按规定控制润制时间
按规定控制润制温度
按规定控制铺参的厚度
及时磨刀,保持锋利
按规定控制切制厚度
干燥时间过头或不到
按规定控制干燥时间
按规定控制干燥温度
按规定控制铺盘的厚度
加强监控人员的管理,按规定做好现场监控
加强对相关人员的管理,按规定做好现场监控
记录不即时或伪造
按规定即时记录,强化监控,杜绝伪造,发现即扣奖
加强对QA的管理,按规定做好记录审核
仪器未校正
按规定使用前进行校正
没按要求检验或未检
加强管理,严格按检验SOP进行
严格按药典等法定标准执行
按规定做好清场,并加强QA监控
按规定进行装量
附件3
控制方式实施后的风险结果、实施风险控制方式前后的风险对比:
潜在失
效模式
效后果
严重度
等
级
潜在失效的
原因、机理
发生
频率
现行设计控制
负责
部门
措施结果
风险
等级
采取的措施
严重
度
给生产环境带来污染
加强教育
强化管理
生产科
产生产品污染
容器清洁不在有效期内,造成污染
加强管理
给产品带来污染
完善洁具清洁规程
完善人员培训教育管理规程
综合科
编制完善工艺规程
编制完善SOP
可能出污染
生产前检查
挑选不够仔细,造成杂质过多;
完善工艺规程和SOP
按规定控制净度
润制时间不符
润制温度不够
温度太低,导致润制不透心,影响切片;
放参太多,导致润制不透心,影响切片;
按规定控制润制铺参厚度
切药刀片钝
性状不合格
片形差,连刀片
完善相关SOP
切制厚度不符合