轴承加工工艺Word文档格式.docx
《轴承加工工艺Word文档格式.docx》由会员分享,可在线阅读,更多相关《轴承加工工艺Word文档格式.docx(10页珍藏版)》请在冰豆网上搜索。
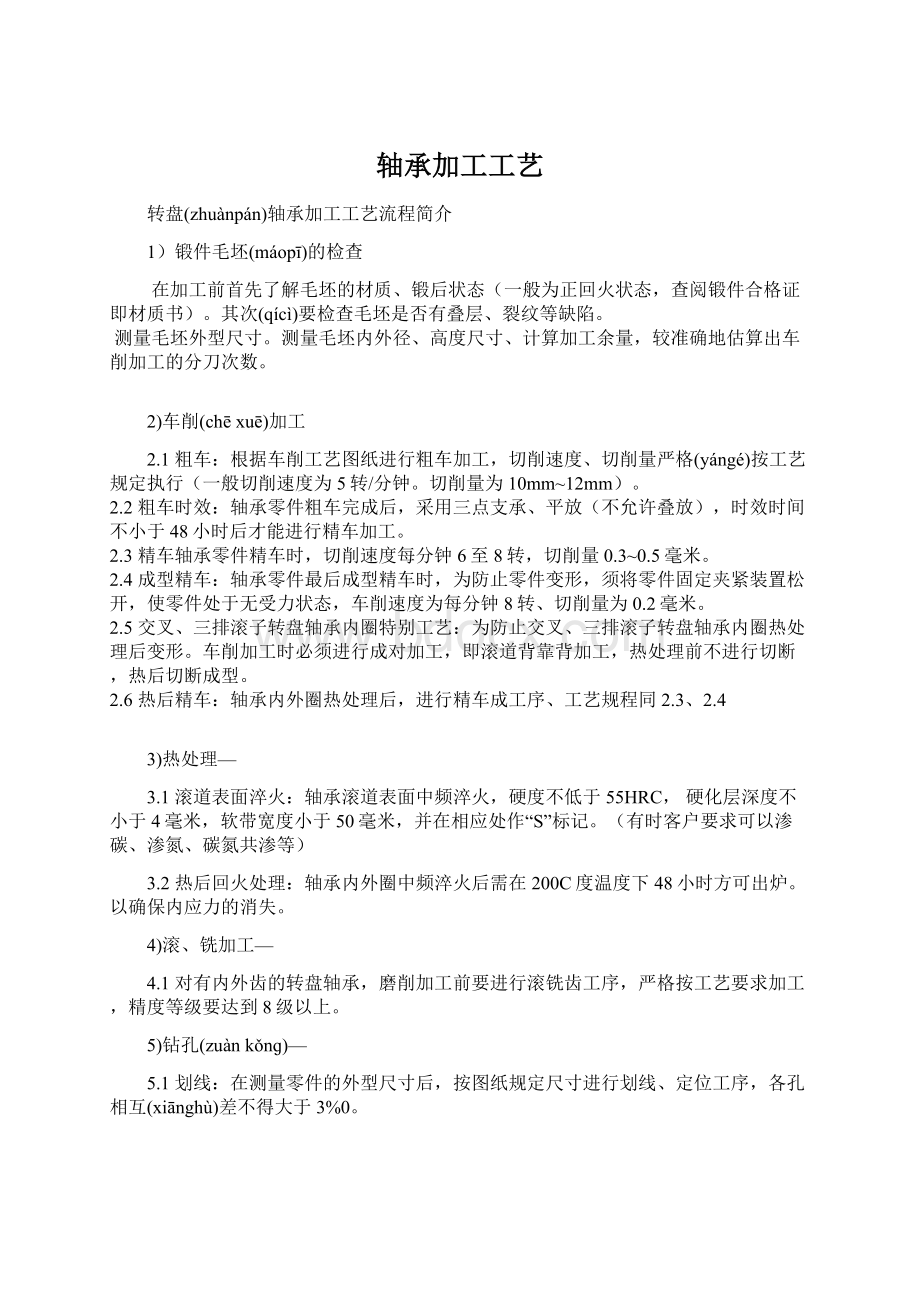
)按工艺规定执行(一般切削速度为5转/分钟。
切削量为10mm~12mm)。
2.2粗车时效:
轴承零件粗车完成后,采用三点支承、平放(不允许叠放),时效时间不小于48小时后才能进行精车加工。
2.3精车轴承零件精车时,切削速度每分钟6至8转,切削量0.3~0.5毫米。
2.4成型精车:
轴承零件最后成型精车时,为防止零件变形,须将零件固定夹紧装置松开,使零件处于无受力状态,车削速度为每分钟8转、切削量为0.2毫米。
2.5交叉、三排滚子转盘轴承内圈特别工艺:
为防止交叉、三排滚子转盘轴承内圈热处理后变形。
车削加工时必须进行成对加工,即滚道背靠背加工,热处理前不进行切断,热后切断成型。
2.6热后精车:
轴承内外圈热处理后,进行精车成工序、工艺规程同2.3、2.4
3)热处理—
3.1滚道表面淬火:
轴承滚道表面中频淬火,硬度不低于55HRC,硬化层深度不小于4毫米,软带宽度小于50毫米,并在相应处作“S”标记。
(有时客户要求可以渗碳、渗氮、碳氮共渗等)
3.2热后回火处理:
轴承内外圈中频淬火后需在200C度温度下48小时方可出炉。
以确保内应力的消失。
4)滚、铣加工—
4.1对有内外齿的转盘轴承,磨削加工前要进行滚铣齿工序,严格按工艺要求加工,精度等级要达到8级以上。
5)钻孔(zuà
nkǒnɡ)—
5.1划线:
在测量零件的外型尺寸后,按图纸规定尺寸进行划线、定位工序,各孔相互(xiānghù
)差不得大于3%0。
5.2钻孔:
对照图纸检测划线尺寸,确保尺寸正确无误后再进行钻孔工序,分体内套转盘轴承安装孔应组合加工,并使软带相间180C度各孔距误差(wù
chā)不得大于5%0
6)磨削(mó
xiāo)加工—
6.1粗磨:
采用中刚玉、软三颗粒度为36度,大气孔树脂砂轮进行磨削,线速度控制在1500转/分钟,防止滚道烧伤。
最大磨削深度不得超过1毫米。
6.2精磨:
采用颗粒度46度或60度树脂砂轮磨削,磨削量要小于粗磨加工(jiāgōng),光洁度要达到图纸规定等级
7)其他零件—
7.1滚动体:
自行加工或采用定点厂家的钢球滚子,精度等级要符合图纸要求,滚动体相互差小于5%0,轴承装配前要进行表面磁粉探伤和超声波探伤,出具探伤报告。
7.2保持器:
采用定点厂家生产的保持器,采用材料符合图纸要求,装配使用前要进行严格检测,出具检测报告。
7.3密封圈:
采用定点厂家生产的密封条。
装配前要进行严格检测,并出具检测记录。
8)装配—
8.1配制游隙:
磨削加工后要进行试装配,以便测出初步游隙,根据计算数据及试装游隙,再进行最后磨削加工,配出最终图纸规定游隙。
8.2零件检测:
游隙配制完成后,要再进行最后的零件检测,并作相应记录。
8.3退磁、清洗、包装并出具合格证。
9)交验文件(wé
njià
n)—
为了使用户更好地了解转盘轴承的内在质量及材料来源(lá
iyuá
n)等技术参数,提供以下技术资料:
(1)转盘轴承合格证。
(2)转盘轴承安装(ānzhuāng)使用说明书。
(3)轴承(zhó
uché
ng)零件材料合格证(材质书)。
(4)滚动(gǔndò
ng)体探伤报告。
(5)轴承热处理合格证
10)附件—
(1)转盘轴承合格证样本。
(2)转盘轴承各零件检测记录表(略)。
(3)转盘轴承成品检测记录表。
轴承套圈锻造CAPP系统的研究
刘军薛进学
[1]河南农业大学450002[2]河南科技大学机电工程系
文章摘要:
对锻造CAPP系统进行了研究,叙述了锻造工艺过程的设计,研制开发了BFCAPP系统,该系统能自动生成轴承套圈的锻造工艺过程文件。
文章主题:
CAPP锻造工艺轴承套圈过程文件计算机辅助工艺过程设计
文章内容:
锻压技术2003年第3期轴承套圈锻造系统的研究河南农业大学(450002)刘军河南科技大学机电工程系薛进学摘要对锻造系统进行了研究,叙述了锻造工艺过程的设计,研制开发了系统,该系统能自动生成轴承套圈的锻造工艺过程文件.关键词锻造工艺轴承套圈,,—,,..一,引言计算机辅助工艺过程设计()是与之间的重要桥梁,是实现的关键技术.长时期以来,的研究都集中在金属切削加工方面,但在机械制造中的其它许多领域还很少使用计算机来完成工艺过程设计.锻压加工工艺属金属塑性成形加工领域,它的工艺过程设计不同于金属切削加工工艺过程设计,尤其是在工艺方案的确定和工序尺寸的计算上,具有自己的特点.我们研究开发了轴承套圈锻造系统——℃系统.二,锻造工艺过程设计的原始资料轴承套圈锻造工艺过程设计需要确定锻件的形状,尺寸,公差,技术要求,原材料种类,重量规格以及锻压设备,工模具尺寸,劳动组织,劳动定额等一系列内容.设计结果可以用图示表格和文字*男,5岁,副教授收稿日期:
2002—05—174说明等多种形式表达.轴承套圈锻造工艺过程设计的原始资料有:
轴承套圈零件图;
车加工的工艺方法;
锻件的余量,公差标准和技术检查条件;
模具设计标准;
锻件的生产纲领.三,锻造工艺过程设计步骤轴承套圈锻造工艺过程设计的步骤与一般金属切削加工工艺过程设计的步骤有相似之处,图1是系统的流程图.图1系统的流程图1.轴承套圈锻件图的绘制首先根据轴承零件图绘制锻件图.轴承套圈一般是回转体,有以下几种形式:
圆筒形,内沟形,外沟形,内锥形,外梯形和圆盘形等.为了节省原材料,在绘制锻件图时要求使锻件的形状与产品的形状尽可能接近,但也要考虑加工工艺的可行性.对于一般的中小型深沟球轴承采用圆筒墅的锻件图.锻件形状确定以后,再加上机械加工余量,就可以得到锻件的外形尺寸.系统中锻件图的绘制分两步:
一是根据轴承成品形状和加工工艺性确定锻件形状,用绘制出来;
二是计算锻件外形尺寸,连同产品外形尺寸一起标注在锻件图中.2.轴承套圈锻造工艺方案的确定因为轴承套圈锻造生产的专业化程度高,工艺的通用性较大,本文总结了现场生产情况和各型号轴承套圈的特点,设计了工艺知识库.在设计锻造工艺时,通过调用工艺决策模块来完成轴承套圈工序方案的设计,即用零件信息与工艺要求和知识库中的条件相匹配,得出合理的工艺方案.3.轴承套圈锻件余量和公差的确定轴承套圈要经过车,磨,热处理等多道切削与非切削加工工序的加工,锻件余量与公差的确定必须保证锻件经多道工序加工后,不能存在任何表面缺陷和软点.本系统相对于不同的工艺方案,将余量和公差数据库划分成多块,每个不同的余量数据库的检索条件各不相同.这样,一旦工序方案确定下来,系统就以不同的检索条件到对应的余量数据库中找到正确的余量和公差.这种设计方法快捷准确,符合工艺习惯,有利于利用现有的工艺数据库.4.锻件重量的计算锻件重量可按体积不变定律来计算,如圆筒型轴承套圈锻件的重量计算公式为:
一6165410一.(--)式中——重量,——外圆直径,——内圆直径,-——宽度,本系统将工艺过程设计中所用到的设计规则和各种工况下相应的工艺参数选择方法进行归纳总结,建立了工艺参数知识库.这样,整个计算过程中各个计算公式所用的参数会根据工况的不同,选取不同的数值.考虑到拔模斜度所形成的余量和锻造圆角使锻件的实际重量大于理论计算重量,本系统采用锻件的最大尺寸来计算锻件的重量.
(1)下料重量和规格的确定公式如下—+3+4一(+3)(1+)式中一下料重量,——锻件重量,——工艺耗损,即料心重量,——加热烧损,——火耗系数(一般,一火火耗系数为3,二火火耗系数为2)锻造轴承套圈的原材料大多是圆棒料,由体积不变定律,料段重量应与套圈的下料重量相等,即:
一6.17×
10-()最后是确定长径比,计算并选取标准直径,计算出料段长度.
(2)材料消耗定额的确定材料消耗定额是指材料在下料重量的基础上,考虑到下料损耗(热剪切下料时的加热烧损,锯切下料时的锯缝损耗等)和料头料尾的损耗.它是投产前材料供应与成本核算的依据.可以按下式计算:
材料的工艺消耗定额一下料重量+分摊在每段坯料上的所有损耗(3)工艺材料利用率工艺材料利用率是用来表示在不计废品损失的条件下钢材的有效利用率.计算公式如下:
工艺材料利用率一(成品套圈重量/材料的工艺消耗定额)1005.变形力的计算变形力的计算为正确地选择设备和工模具提供了科学的依据.可以采用经验公式:
一0.01()式中——应力状态,摩擦,坯料尺寸对单位变形抗力影响的系数叫——变形速度对单位变形抗力影响的系数——变形温度下的强度极限——工件与坯料的接触面积6.轴承套圈锻件的技术条件及其检查方法轴承套圈锻件的技术条件表达了锻件要求达到的外观质量和内部质量.技术条件中所要求的形位公差允许值与机械加工余量有关,一般由机械加工余量计算而得.各种锻造工艺所产生的形位误差是不同的.系统设置了专门的数据库,用于存放不同锻造工艺所需检验的形位公差项目,以及计算此形位公差允许值所需用到的机械加工余量和计算系数.在计算形位公差允许值时,用锻造工艺代号为关键字,5锻压技术2003年第3期气门变体积镦粗过程的有限元模拟技术*华南理工大学机械学院(510641)邝卫华一阮锋广东工业大学材料与能源学院肖小亭孙友松摘要针对电镦成形工艺,提出了一种变体积镦粗的网格再划分算法,并就电镦有限元模拟技术中的网格畸变,节点优化及新旧网格场量传递等问题,提出了自己的见解.关键词电镦成形变体积网格再划分网格畸变节点优化场量传递.2一.,,.—一,引言发动机气门是典型的带盘细杆类零件,由于头部与杆部横截面积相差甚大,长径比超过了常规镦*广东省自然科学基金资助项目(990141)**男,27岁,博士研究生收稿日期:
2002-12-02粗工艺的允许范围(如发动机气门镦粗部位长径比/达10以上,常规镦粗不超过3),不能直接进行镦粗.终成形前必须使用特殊的方法制坯聚料,电镦是实际中常用的一种方法.电镦时,在毛坯的局部连续进行加热与镦粗,因此毛坯的长度
一、轴承(zhó
ng)外圈加工
1、轴承外圈加工(jiāgōng)工艺流程:
轴承钢——>
锻造(duà
nzà
o)——>
退火(tuì
huǒ)——>
车加工(jiāgōng)——>
热处理——>
磨加工——>
装配——>
检验——>
包装入库
2、锻造工艺的目的
1、成形:
控制合理的车削留量。
2、获得高寿命的锻造流线分布,确保轴承寿命。
3、获得理想的金相组织,为退火、淬火做准备。
3、退火工艺的目的
1、降低(jià
ngdī)硬度,为车加工做好准备。
2、获得理想的金相(jīnxiānɡ)组织,为淬火做好准备。
3、为成品零件提供均匀分布的残留(cá
nliú
)碳化物,确保轴承的耐磨性。
4、车加工(jiāgōng)的目的
1、成形(ché
nɡxí
nɡ)
2、减少留量,为磨加工做准备。
3、去除脱碳层,确保成品零件硬度。
5、热处理---淬火、回火
1、提高零件硬度,确保零件强度和耐磨性。
2、获得理想的金相组织,提高零件寿命。
6、磨加工的目的
1、提高零件精度(尺寸和形位精度)。
2、提高零件表面质量(粗糙度)。
7、轴承检验(径向游隙、轴承游隙、振动值、旋转灵活性、残磁等)
二、轴承磙子加工工艺、
1、工艺流程:
钢丝、棒料——>
下料——>
圆头/倒角加工——>
包装
类型代号(用数字或字母表示)如下表:
代号
轴承类型
原代号
双列角接触球轴承
6
深沟球轴