蜗轮蜗杆减速箱设计课程设计论文.docx
《蜗轮蜗杆减速箱设计课程设计论文.docx》由会员分享,可在线阅读,更多相关《蜗轮蜗杆减速箱设计课程设计论文.docx(20页珍藏版)》请在冰豆网上搜索。
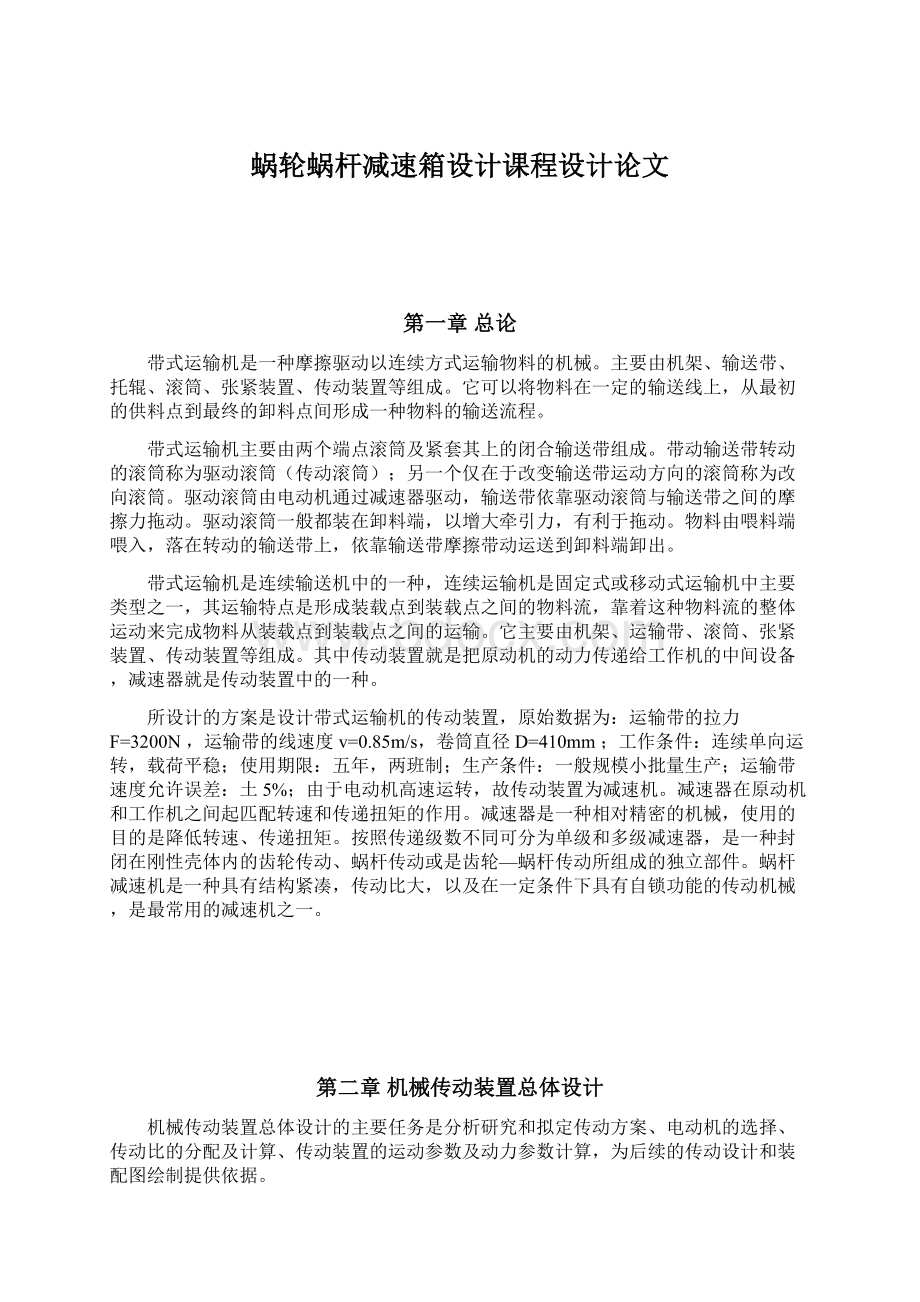
蜗轮蜗杆减速箱设计课程设计论文
第一章总论
带式运输机是一种摩擦驱动以连续方式运输物料的机械。
主要由机架、输送带、托辊、滚筒、张紧装置、传动装置等组成。
它可以将物料在一定的输送线上,从最初的供料点到最终的卸料点间形成一种物料的输送流程。
带式运输机主要由两个端点滚筒及紧套其上的闭合输送带组成。
带动输送带转动的滚筒称为驱动滚筒(传动滚筒);另一个仅在于改变输送带运动方向的滚筒称为改向滚筒。
驱动滚筒由电动机通过减速器驱动,输送带依靠驱动滚筒与输送带之间的摩擦力拖动。
驱动滚筒一般都装在卸料端,以增大牵引力,有利于拖动。
物料由喂料端喂入,落在转动的输送带上,依靠输送带摩擦带动运送到卸料端卸出。
带式运输机是连续输送机中的一种,连续运输机是固定式或移动式运输机中主要类型之一,其运输特点是形成装载点到装载点之间的物料流,靠着这种物料流的整体运动来完成物料从装载点到装载点之间的运输。
它主要由机架、运输带、滚筒、张紧装置、传动装置等组成。
其中传动装置就是把原动机的动力传递给工作机的中间设备,减速器就是传动装置中的一种。
所设计的方案是设计带式运输机的传动装置,原始数据为:
运输带的拉力F=3200N,运输带的线速度v=0.85m/s,卷筒直径D=410mm;工作条件:
连续单向运转,载荷平稳;使用期限:
五年,两班制;生产条件:
一般规模小批量生产;运输带速度允许误差:
土5%;由于电动机高速运转,故传动装置为减速机。
减速器在原动机和工作机之间起匹配转速和传递扭矩的作用。
减速器是一种相对精密的机械,使用的目的是降低转速、传递扭矩。
按照传递级数不同可分为单级和多级减速器,是一种封闭在刚性壳体内的齿轮传动、蜗杆传动或是齿轮—蜗杆传动所组成的独立部件。
蜗杆减速机是一种具有结构紧凑,传动比大,以及在一定条件下具有自锁功能的传动机械,是最常用的减速机之一。
第二章机械传动装置总体设计
机械传动装置总体设计的主要任务是分析研究和拟定传动方案、电动机的选择、传动比的分配及计算、传动装置的运动参数及动力参数计算,为后续的传动设计和装配图绘制提供依据。
2.1拟定传动方案
一个传动方案的拟定,除了应满足机器的功能要求外,还应当具备工作可靠、结构简单、尺寸紧凑、传动效率高、成本低廉以及使用维护方便等特性。
在拟定传动方案的时候,应多种传动方案进行对比,在结合具体情况进行设计,最后确定最终的方案。
一般情况下,蜗杆减速器除有第一章所述特点外还具有坚固耐用、传动平稳、承载能力大、噪音低,动力源广,可用于电机或其他动力驱动等特点。
所以根据上述数据及要求(原始数据为:
运输带的拉力F=3200N,运输带的线速度v=0.85m/s,卷筒直径D=410mm;工作条件:
连续单向运转,载荷平稳;使用期限:
五年,两班制;生产条件:
一般规模小批量生产;运输带速度允许误差:
土5%;),在以下方案中进行选择:
方案一(皮带一单级圆柱齿轮传动)、方案二(两级展开式圆柱齿轮传动)、方案三(蜗轮蜗杆传动)。
由于转速高的电动机传递到工作机时降速范围较大,故选择蜗轮蜗杆传动的结构紧凑、传动比大、坚固耐用、传动平稳等特点。
故最终确定方案为:
方案三(蜗轮蜗杆传动)。
由所选传动方案可绘制工作传动装置如下图所示:
图1-1蜗杆减速器示意图
1-电动机2、4-联轴器3一级蜗轮蜗杆减速器5-传动滚筒6-输送带
电动机与减速器相连选用凸缘联轴器,工作机与减速器相连处选用弹性联轴器。
2.2电动机的选择
根据工作机的负荷、特性和工作环境,选择电动机的类型、结构形式和转速,计算电动机功率,最后确定电动机型号。
1、选择电动机的类型
按工作要求和条件选取Y系列一般用途全封闭自扇冷鼠笼式三相异步电动机。
2、选择电动机容量
(1)工作机各传动部件的传动效率及总效率
其中弹性联轴器的传动效率=0.99;
单线蜗杆与蜗轮的传动效率=0.75;
运输机驱动轴一对滚动轴承的效率=0.99;
凸缘联轴器的传动效率=0.99
所以减速机构的总效率
=0.99×0.75×0.992×0.99=0.7203
(2)选择电动机的功率
所选电动机的额定功率应该等于或稍大于工作要求的功率。
容量小于工作要求,则不能保证工作机的正常工作,或使电动机长期过载、发热大而过早损坏;容量过大,则增加成本,并且由于效率和功率因数低而造成电能浪费。
①带式运输机所需的功率:
Pw=F·v/1000w=3200×0.85/1000×1=2.72kW(其中w为工作机传动效率且w=1);
②初步估计电动机额定功率P:
所需电机输出的功率Pd=Pw/=2.72/0.72=3.78kW;
③查《机械设计课程设计》表2.1,选取Y112M-4电动机,主要参数如下:
额定功率P=4kw
满载转速nm=1440r/min
电机轴伸出端直径:
28mm
伸出端安装长度:
60mm
2.3传动比及其分配
1、查《机械设计》书中得各级齿轮传动比如下:
;
理论总传动比:
;
运输机驱动滚筒转速nw===39.62r/min;
根据初选电机转速nm=1440r/min,计算总传动比i'=nm/nw=1440/39.62=36.35。
由工作原理图可知该传动装置为蜗轮蜗杆单级传动,即总传动比就等于蜗轮蜗杆传动比。
2、查《机械设计》表11-1,取蜗杆头数z1=1,蜗轮齿数z2=36,则实际总传动比i==36。
2.4校核转速
滚筒的实际转速nw'=nm/i=1440/36=40,
转速误差Δnw===0.97%<5%,符合要求。
2.5传动装置各参数的计算
1、各轴功率计算
蜗杆输入功率:
P1=P=4×0.99=3.96kW
蜗轮输出功率:
P2=P1=P=2.97kW
滚筒轴的传递功率:
P3=P2=2.97×0.99×0.99=2.91kW
2、各轴转速计算
由于蜗杆是通过联轴器与电机伸出轴连接在一起,故蜗杆转速等于电机转速即n1=nm=1440r/min;
涡轮轴的转速n2=n1/i=1440/36=40r/min;
滚筒轴转速n3=n2=40r/min。
3、各轴转矩计算
蜗杆传递的转矩T1=9550×P1/n1=26.26N·m
蜗轮轴传递的转矩T2=9550×P2/n2=709.09N·m
滚筒轴传递的转矩T3=9550×P3/n3=694.76N·m
第三章传动零件—蜗杆蜗轮传动的设计计算
传动装置中传动零件的参数、尺寸和结构,对其他零部、件的设计起决定性的作用,因此,应首先设计计算传动零件。
当减速器有传动件时,应先设计减速器外的传动零件。
3.1蜗轮蜗杆材料及类型选择
1、选择蜗杆传动类型
根据GB/T10085-1988的推荐,选用渐开线蜗杆(ZI)。
2、选择材料
考虑到蜗杆传动的功率不大,速度中等,故蜗杆采用45刚;而又希望效率高些,耐磨性好些,故蜗杆螺旋齿面要求淬火,硬度为45~55HRC;蜗轮选用铸锡磷青铜(ZCuSn10P1),砂模铸造;为了节约贵重有色金属,仅齿圈用青铜铸造,而轮芯用灰铸铁(HT100)制造。
3.2设计计算
1、按齿面接触强度设计
根据闭式蜗杆蜗轮的设计准则,先按齿面接触疲劳强度进行计算,再校核齿根弯曲疲劳强度。
由《机械设计》根据式子:
m2d≥KT2
(1)确定载荷系数
因工作是有轻微振动,故取载荷分布不均匀系数=1,由《机械设计》表11-5选取使用系数=1,由于转速不是很高,冲击不大,可选取动载荷系数=1.1,则K==1×1.05×1≈1.1
(2)确定弹性影响系数
因为选用的是锡磷青铜(ZCuSn10P1)的蜗轮和45刚蜗杆相配,故
(3)确定许用接触应力[]H
根据蜗轮材料为锡磷青铜(ZCuSn10P1),金属模铸造,蜗杆螺旋齿面硬度>45HRC,可从《机械设计》表11-7查得蜗轮的基本许用应力=268MPa。
应力循环次数N=60=60×1×40×(16×5×365)=7.008×,寿命系数=0.784,则==0.784268=210.1MPa
(4)计算m2d
由于z2=36,T2=709.09N·m=709.09×103N·mm,故
m2d≥KT2=1.1×709.09×103×=3144.33mm3
因z1=1,故从《机械设计》表11-2中查取模数m=6.3mm,蜗杆分度圆直径d1=112mm。
2、蜗杆与蜗轮主要参数与几何尺寸
(1)中心距a===169.4
(2)蜗杆:
轴向齿距Pa=πm=3.14×6.3=19.78mm;
直径系数q==17.78;
齿顶圆直径=d1+2ha1=d1+2ha*m=112+2×1×6.3=124.6mm;
齿根圆直径=d1-2hf1=d1-2(ha*m+c)=112-2(1×6.3+1.6)=47.88mm;
分度圆导程角=arctan=3.22°(右旋);轴向齿厚sa=πm=9.89mm。
(3)蜗轮:
蜗轮齿数:
=36;
变位系数=0;
螺旋角:
30.96°(右旋)
蜗轮分度圆直径:
=226.8mm;
蜗轮喉圆直径:
=+=239.4mm;
蜗轮齿根圆直径:
=+=211mm;
蜗轮咽喉母圆半径:
=a-=169.4-×239.4=49.7mm;
蜗轮轮缘宽度:
B=(0.67~0.7)=(83.48~87.22)mm,取B=85mm。
3、校核齿根弯曲疲劳强度
当量齿数==36.173
根据=0,=36.173,从《机械设计》图11-17中可查得齿形系数2.44
螺旋系数==0.977
许用弯曲应力=
从表11-8中查得由ZCuSn10P1制造的蜗轮的基本许用弯曲应力=56MPa
寿命系数
==560.624=34.92MPa
所以==≤56MPa
即<,弯曲强度校核满足要求。
4、验算效率
已知=3.22°,=,与相对滑移速度有关,
m/s
从《机械设计》表11-18中用插值法查得=0.0175,=1°代入上式得
≈(0.7239~0.732)大于原估计值0.7203,因此不用重算,且进一步验证了电机选择的合理性。
5、精度等级公差和表面粗糙度的确定
考虑到所涉及的蜗杆传动是动力传动,属于机械减速器。
从GB/10089-1988中,蜗轮圆周速度=n2πd2/60=0.47m/s<1.5m/s,故查《课程设计》表3.66选取蜗轮、蜗杆为9级精度,侧隙种类为f,标注为9fGB/10089-1988。
蜗杆与轴做成一体,即蜗杆轴。
蜗轮采用轮箍式,与铸造贴心采用H7/r6配合。
查《课程设计》表3.80得蜗轮、蜗杆表面粗糙度如下表:
表3—1蜗轮、蜗杆表面粗糙度
齿面
顶圆
蜗杆
6.3,3.2
6.3,3.2
蜗轮
6.3,3.2
12.5,6.3
查《课程设计》表3.69得:
蜗杆轴向齿距极限偏差fpx=±25μm;
蜗杆轴向齿距累积公差fpxl=48μm;
蜗杆齿形公差ff1=45μm;
查《课程设计》表3.70得:
蜗杆齿槽径向跳动公差fr=40μm;
查《课程设计》表3.70得:
蜗轮齿距极限偏差fpt=40μm;
蜗轮齿形公差ff2=36μm。
6、热平衡计算
(1)估算散热面积S
S=
(2)验算油的工作温度
室温,通常取。
散热系数=8.15~17.45:
取=17.5W/(㎡·℃);
啮合效率;轴承效率0.98~0.99,取轴承效率2=0.99;搅油效率0.94~0.99,搅油效率3=0.98;
=1×2×3=0.88×0.99×0.98=0.85
56.77℃<80℃油温未超过限度。
7、主要设计结论
表3—2蜗轮蜗杆主要参数
蜗杆
蜗轮
分度圆直径(