交流伺服电机PLC控制系统设计说明书Word格式文档下载.docx
《交流伺服电机PLC控制系统设计说明书Word格式文档下载.docx》由会员分享,可在线阅读,更多相关《交流伺服电机PLC控制系统设计说明书Word格式文档下载.docx(18页珍藏版)》请在冰豆网上搜索。
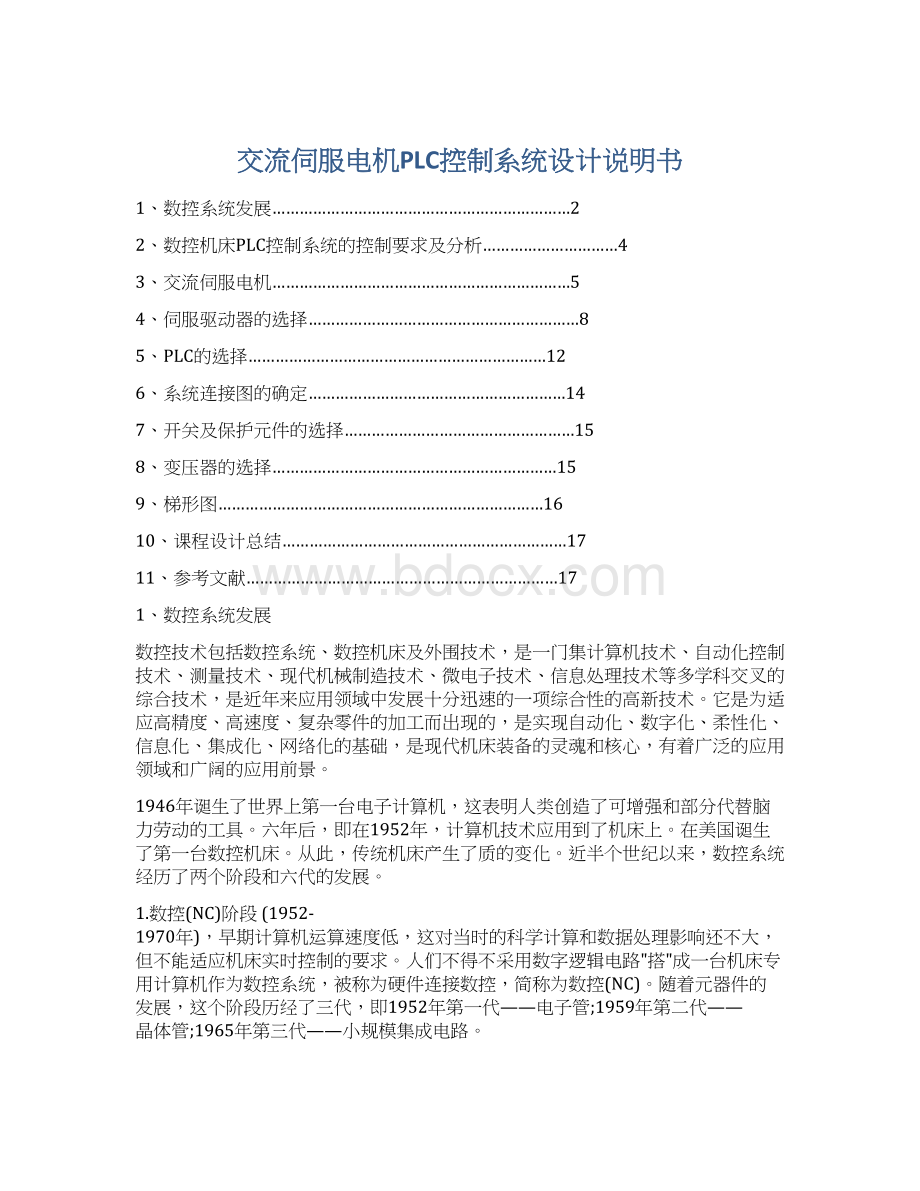
在美国诞生了第一台数控机床。
从此,传统机床产生了质的变化。
近半个世纪以来,数控系统经历了两个阶段和六代的发展。
1.数控(NC)阶段(1952-1970年),早期计算机运算速度低,这对当时的科学计算和数据处理影响还不大,但不能适应机床实时控制的要求。
人们不得不采用数字逻辑电路"
搭"
成一台机床专用计算机作为数控系统,被称为硬件连接数控,简称为数控(NC)。
随着元器件的发展,这个阶段历经了三代,即1952年第一代——电子管;
1959年第二代——晶体管;
1965年第三代——小规模集成电路。
2.计算机数控(CNC)阶段(1970——现在)到1970年,通用小型计算机业已出现并成批生产。
其运算速度比五、六十年代有了大幅度的提高,这比专门"
成的专用计算机成本低、可靠性高。
于是将它移植过来作为数控系统的核心部件,从此进入了计算机数控(CNC)阶段。
到1971年美国lintel公司在世界上第一次将计算机的两个核心的部件——运算器和控制器,采用大规模集成电路技术集成在一块芯片上,称之为微处器,又可称中央处理单元(简称CPU)。
到1974年微处理器被应用于数控系统。
由于微处理器是通用计算机的核心部件,故仍称为仿计算机数控。
到了1990年,PC机的性能已发展到很高的阶段,可满足作为数控系统核心部件的要求,而且PC机生产批量很大,价格便宜,可靠性高。
数控系统从此进入了基于PC的阶段。
总之,计算机数控阶段也经历了三代。
即1970年第四代——小型计算机;
1974年第五代——微处理器和1990年第六代——基于PC的阶段。
必须指出,数控系统近五十年来经历了两个阶段六代的发展,只是发展到了第五代以后,才从根本上解决了可靠性低,价格极为昂贵,应用很不方便等极为关键的问题。
因此,即使在工业发达国家,数控机床大规模地得到应用和普及,是在七十年代未八十年代初以后的事情,也即数控技术经过近三十年的发展才走向普及应用的。
还要指出的是,虽然国外早已改称为计算机数控(即CNC)了,而我国仍习称数控(NC)。
所以我们日常讲的"
数控"
实质上已是指"
计算机数控"
了。
智能化、开放式、网络化成为当代数控系统发展的主要趋势。
21世纪的数控装备将是具有一定智能化的系统,智能化的内容包括在数控系统中的各个方面:
为追求加工效率和加工质量方面的智能化,如加工过程的自适应控制,工艺参数自动生成;
为提高驱动性能及使用连接方便的智能化,如前馈控制、电机参数的自适应运算、自动识别负自动选定模型、自整定等;
简化编程、简化操作方面的智能化,如智能化的自动编程、智能化的人机界面等;
还有智能诊断、智能监控方面的内容、方便系统的诊断及维修等。
为解决传统的数控系统封闭性和数控应用软件的产业化生产存在的问题。
目前许多国家对开放式数控系统进行研究,数控系统开放化已经成为数控系统的未来之路。
所谓开放式数控系统就是数控系统的开发可以在统一的运行平台上,面向机床厂家和最终用户,通过改变、增加或剪裁结构对象(数控功能),形成系列化,并可方便地将用户的特殊应用和技术诀窍集成到控制系统中,快速实现不同品种、不同档次的开放式数控系统,形成具有鲜明个性的名牌产品。
目前开放式数控系统的体系结构规范、通信规范、配置规范、运行平台、数控系统功能库以及数控系统功能软件开发工具等是当前研究的核心。
网络化数控装备是近两年国际著名机床博览会的一个新亮点。
数控装备的网络化将极大地满足生产线、制造系统、制造企业对信息集成的需求,也是实现新的制造模式如敏捷制造、虚拟企业、全球制造的基础单元。
国内外一些著名数控机床和数控系统制造公司都在近两年推出了相关的新概念和样机,反映了数控机床加工向网络化方向发展的趋势。
2、数控机床PLC控制系统的控制要求及分析
PLC应用系统设计的内容:
数控技术课程设计交流伺服电机PLC控制系统设计,它是利用数字化的信息对机床运动及工作过程进行控制的一种方法。
课题采用PLC来控制这些器件,实现工业控制。
以可编程控制器(简称PLC)作为控元件,替代机床继电器连接触器组成的电气控制部分,是为了提高机床电气控制系统的可靠性,这种方法主用于组合机床以及生产线上的专用机床用数控技术实施加工控制的机床,或者说装备了数控系统的机床称为数控(NC)机床。
要实现对机床的控制,需要用几何信息描述刀具和工件间的相对运动以及用工艺信息来描述机床加工必须具备的一些工艺参数。
某机床进给电机采用交流伺服电动机,型号为ASD-B2-1521-B,丝杠螺距6mm。
驱动器电源为三相220V,功率为1.5KW。
需要控制伺服电机的正反转,采用位置控制模式Y0脉冲输出,Y1方向控制,反转时Y1要先输出,丝杠螺距为6MM其螺杆正转一圈前进6MM,反转一圈后退6MM,丝杆两头需要安装极限开关如行程开关或者光电开关/接近开关。
计算电机旋转一周需要多少脉冲,用6MM除以一周脉冲得到最小单位"
脉冲当量"
即一个脉冲到应多少距离,然后根据需求来计算脉冲的数量和方向,脉冲的速度决定电机的转速。
1、减速比=伺服的转数/丝杠的转数;
2、工件平移的距离=螺距×
丝杠的转数;
3、工件平移的距离=螺距×
伺服的转数/减速比
4、伺服的转数=伺服输入的驱动脉冲/伺服每转一周的驱动脉冲数;
5、工件平移的距离/伺服输入的驱动脉冲=螺距/(减速比×
伺服每转一周的驱动脉冲数);
6、脉冲当量=螺距/(减速比×
伺服每转一周的驱动脉冲数)
3、伺服电动机的选择
机床进给电机采用交流伺服电动机,伺服驱动器型号为ASD-B2-1521-B,丝杠螺距6mm。
参考下表1选择对应的伺服电机。
表1伺服驱动器与电机机种名称对应参照表
上表以伺服电机的额定电流的三倍来设计伺服驱动器的规格。
根据设计内容要求,所选择的伺服电机为ECMA-E21315S(S=22mm)
图1电机的外型尺寸
伺服驱动器电源接线法分为单相与三相两种,单相仅允许用于1.5kW与1.5kW以下机种,而三相电源接线法全系列皆适用。
图中,PowerOn为a接点,PowerOff与ALRM_RY为b接点。
MC为电磁接触器线圈及自保持电源,与主回路电源接点。
图2三相电源接线法
表2电机U、V、W引出线的连接头规格
表3端子定义
4、伺服驱动器的选择
4.1伺服驱动器
伺服驱动器,又称为,伺服电机驱动器,伺服马达驱动器全数字交流伺服驱动器。
随着全数字式交流伺服系统的出现,交流伺服电机也越来越多地应用于数字控制系统中。
如果对电机的速度、位置都没有要求,只要输出一个恒转矩,当然是用转矩模式。
如果对位置和速度有一定的精度要求,而对实时转矩不是很关心,用转矩模式不太方便,用速度或位置模式比较好。
如果上位控制器有比较好的闭环控制功能,用速度控制效果会好一点。
如果本身要求不是很高,或者,基本没有实时性的要求,用位置控制方式对上位控制器没有很高的要求。
就伺服驱动器的响应速度来看,转矩模式运算量最小,驱动器对控制信号的响应最快,位置模式运算量最大,驱动器对控制信号的响应最慢。
关于伺服的三种控制方式,一般伺服都有三种控制方式:
速度控制方式,转矩控制方式,位置控制方式。
速度控制和转矩控制都是用模拟量来控制的。
位置控制是通过发脉冲来控制的。
1、转矩控制:
转矩控制方式是通过外部模拟量的输入或直接的地址的赋值来设定电机轴对外的输出转矩的大小,
2、位置控制:
位置控制模式一般是通过外部输入的脉冲的频率来确定转动速度的大小,通过脉冲的个数来确定转动的角度,也有些伺服可以通过通讯方式直接对速度和位移进行赋值。
由于位置模式可以对速度和位置都有很严格的控制,所以一般应用于定位装置。
3、速度模式:
通过模拟量的输入或脉冲的频率都可以进行转动速度的控制,在有上位控制装置的外环PID控制时速度模式也可以进行定位,但必须把电机的位置信号或直接负载的位置信号给上位反馈以做运算用。
位置模式也支持直接负载外环检测位置信号,此时的电机轴端的编码器只检测电机转速,位置信号就由直接的最终负载端的检测装置来提供了,这样的优点在于可以减少中间传动过程中的误差,增加了整个系统的定位精度。
4.2伺服驱动器的选择
采用交流伺服电动机,伺服驱动器选择型号为ASD-B2-1521-B。
图3伺服驱动器各部名称及作用
4.3驱动器各端口的连接
表4驱动器各端口的连接
4.4伺服系统基本方块图
图4伺服系统基本方块图
表5位置脉冲指令
4.5位置(Pt)模式标准接线
图5位置(Pt)模式标准接线
5、PLC的选择
5.1分析工艺流程及控制要求
由数控机床的进给系统中,传动件要快速移动到加工位置、以加工速度进行加工、快速退回原来位置等要求,那么对应的传动轴传动伺服电机则要求快速正转,以加工速度正转、以加工速度反转、快速反转等。
一次,PLC指要控制伺服电机以一定的速度精确地正、反转一定圈数来控制传动件的位置和移动速度。
5.2分析输入输出信号的性质
由机床进给系统动作的分析得:
输入信号有:
A相脉冲,B相脉冲,正转按钮SB1,反转按钮SB2,增速按钮SB3,减速按钮SB4,停止按钮SB5,停止按钮SB6。
输出信号:
正转Y0反转Y1。
表6PLCI/O口分配表
X0
启动
Y0
正转启动
X1
反转
Y1
X2
增速
Y2
始能
X3
减速
X4
停止
5.3选择PLC
高功能主机DVP32EH00T著脱端子台,16点DC24V输入,16点数为输出,6点单相高速计数器,1組AB相高速计数器,最高输入频率总和达60KHz,2点高速脉波输出共100KHz,内建RS232通讯埠,晶体管输出。
图6DVP32EH00T外形图
图7DVP32EH00T引脚图
控制要求:
由台达PLC和台达伺服组成一个简单的进给控制演示系统。
通过PLC发送脉冲控制伺服,实现机床的前进、后退、快进和快退以及暂停功能,并对速度和位置进行简单控制。
6、系统连接图的确定
图8PLC控制器与驱动器的连接图
7、开关及保护元件的选择
正转启动按钮:
SB1;
反转启动按钮:
SB2;
增速按钮SB3:
减速按钮SB4;
熔断器(保险丝):
FU;
热继电器:
FR;
电磁式继电器:
KM。
7.1开关保护元件的