管壳式换热器的设计论文设计Word文件下载.docx
《管壳式换热器的设计论文设计Word文件下载.docx》由会员分享,可在线阅读,更多相关《管壳式换热器的设计论文设计Word文件下载.docx(21页珍藏版)》请在冰豆网上搜索。
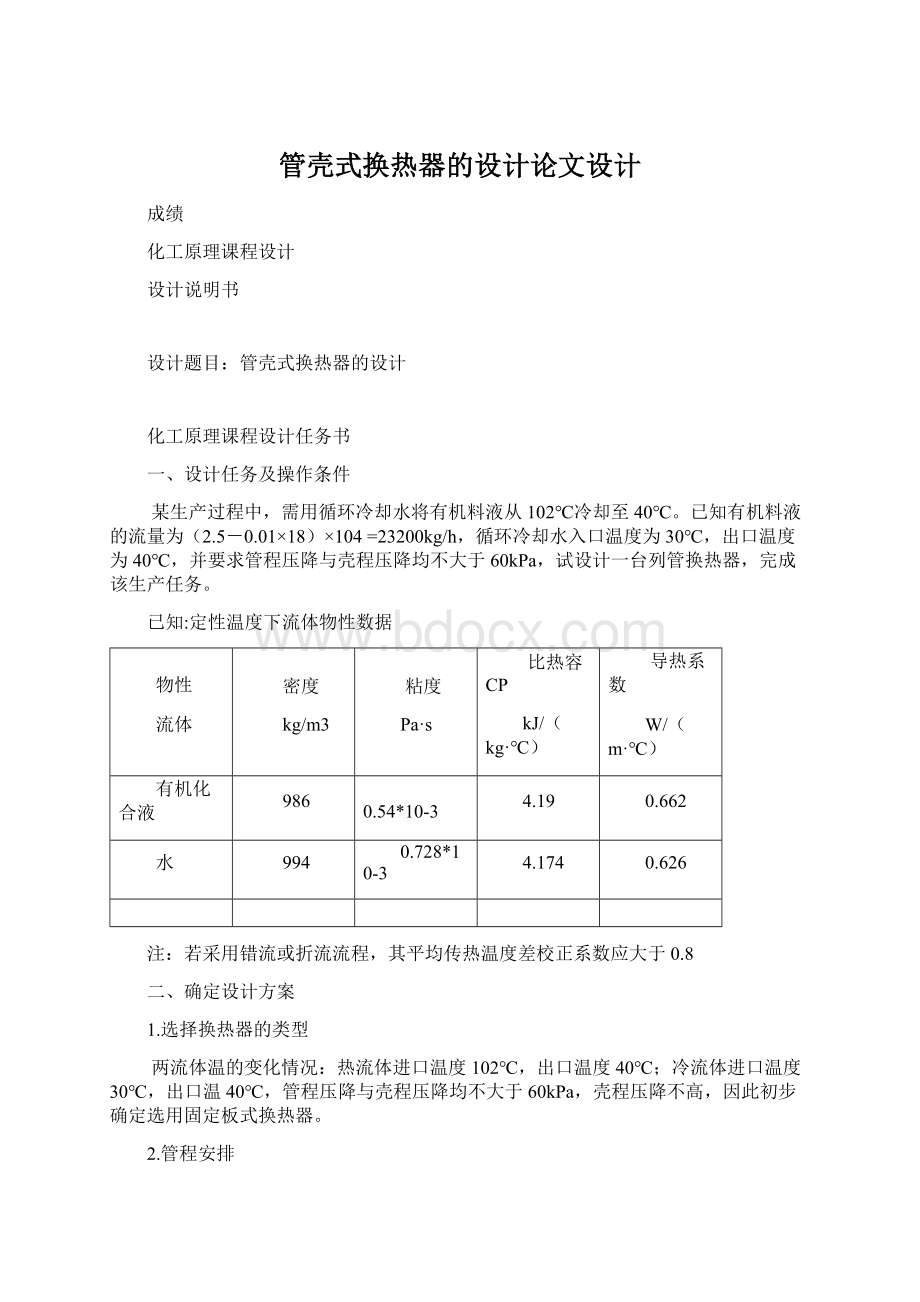
0.626
注:
若采用错流或折流流程,其平均传热温度差校正系数应大于0.8
二、确定设计方案
1.选择换热器的类型
两流体温的变化情况:
热流体进口温度102℃,出口温度40℃;
冷流体进口温度30℃,出口温40℃,管程压降与壳程压降均不大于60kPa,壳程压降不高,因此初步确定选用固定板式换热器。
2.管程安排
由于循环冷却水较易结垢,若其流速太低,将会加快污垢增长速度,使换热器的热流量下降,所以从总体考虑,应使循环水走管程,有机化合液走壳程。
三、确定物性数据
定性温度:
对于一般气体和水等低粘度立体,其定性温度可取流体进出口温度的平均值。
故壳程的有机化合液的定性温度为
T
管程流体的定性温度为
t=
根据定性温度分别查取壳程流体和管程流体的有关物性数据。
有机化合液的有关物性数据如下:
密度
粘度
0.54*10-3Pa·
比热容
=4.19kJ/(kg·
导热系数
λ=0.662W/(m·
循环水的有关物性数据如下:
粘度
0.728*10-3Pa·
=4.174kJ/(kg·
λ=0.626W/(m·
四、估算传热面积
1、热流量
Q1=
=23200×
4.19×
(102-40)=6.03×
106kj/h=1675.00kw
2、平均传热温差
先按照纯逆流计算,得
3、传热面积
由于有机化合液的粘度为
s,假定总传热系数
K=300W/(
.℃),则传热面积为
A=
4、冷却水用水量
m=
=
五、工艺结构尺寸
1、管径和管流速选用Φ25×
2.5较高级冷拔传热管(碳钢),取管流速
=1.5m/s。
2、管程数和传热管数可依靠传热管径和流速确定单程传热管数
Ns=
按单程管计算,所需的传热管长度为
=28m
按单程管设计,宜采用多管程结构。
现取传热管长l=7m,则该换热器的管程数为
传热管总根数Nt=346
3、传热温差校平均正及壳程数
平均温差校正系数:
按单壳程,双壳程结构,查得温差修正系数得
平均传热温差
由于平均传热温差校正系数大于0.8,同时壳程流体流量较大,故取单壳程合适。
4、传热管排列和分程方法
采用组合排列法,即每程均按正三角形排列,隔板两侧采用正方形排列。
取管心距t=1.25
,则t=1.25*25=31.35=32mm
隔板中心到离其最近一排管中心距离:
S=t/2+6=32/2+6=22mm
各程相邻管的管心距为44mm。
管数的分程方法,每程各有传热管90根。
5、壳体径采用多管程结构,进行壳体径估算。
取管板利用率
=0.75,则壳体径为:
D=
按卷制壳体的进级档,可取D=800mm
筒体直径校核计算:
壳体的径
应等于或大于管板的直径,所以管板直径的计算可以决定壳体的径,其表达式为:
=t(
-1)+2e
因为管子安正三角形排列:
取e=1.2*20=24mm
所以
=32*(20-1)+2*34=676mm按壳体直径标准系列尺寸进行圆整:
=800mm
6、折流挡板采用圆缺形折流挡板,去折流板圆缺高度为壳体径的25%,则切去的圆缺高度为h=0.25*800=200
取折流板间距B=0.3D,则B=0.3*800=240mm,可取B为240mm。
折流板数目N=传热管长/折流板间距-1=7000/240-1=27
7、其他附件
拉杆数量与直径选取,本换热器壳体径为800mm,故其拉杆直径为12mm最少拉杆数6。
8、接管
壳程流体进出口接管:
取接管液体流速为u=0.2m/s,则接管径为
圆整后可取管径为210mm
管程流体进出口接管:
取接管液体流体u=1m/s,则接管径为
圆整后可取管径为220mm
六、换热器核算
1、热流量核算
(1)壳程表面传热系数用克恩法计算
当量直径
壳程流通截面积:
壳程立体流速及其雷诺数分别为
普朗特数
粘度校正
(2)管表面传热系数:
管程流体流通截面积:
管程流体流速:
雷诺数:
普朗特数:
(3)污垢热阻和管壁热阻:
管外侧污垢热阻
管侧污垢热阻
管壁热按查得碳钢在该条
件下的热导率为50w/(m·
K)。
(4)传热系数
有:
(5)传热面积裕度:
计算传热面积Ac:
该换热器的实际传热面积为:
该换热器的面积裕度为
传热面积裕度合适,该换热器能够完成生产任务。
2.壁温计算
因为管壁很薄,而且壁热阻很小,故管壁温度可按式
计算。
由于该
式中液体的平均温度
和气体的平均温度分别计算为
0.4×
40+0.6×
30=34℃
(102+40)/2=71℃
6629w/㎡·
K
3046w/㎡·
传热管平均壁温
℃
壳体壁温,可近似取为壳程流体的平均温度,即T=71℃。
壳体壁温和传热管壁温之差为
℃。
因此,需选用固定板式换热器较为适宜。
3.换热器流体的流动阻力
(1)管程流体阻力
由Re=40691,传热管对粗糙度0.01,查图得
,流速=1.5m/s,
所以:
管程流体阻力在允许围之。
(2)壳程阻力:
按式计算
流体流经管束的阻力
F=0.5
0.5×
0.2419×
39×
(29+1)×
=6188.7Pa
流体流过折流板缺口的阻力
B=0.21m,D=0.7m
总阻力
6188.7+3984.4=10173.1Pa
所以壳程流体的阻力适宜。
3)换热器主要结构尺寸和计算结果见下表:
参数
管程
壳程
流率
1675.00
23200
进/出口温度/℃
40/30
102/40
压力/kPa
<
60
定性温度/℃
35
71
密度/(kg/m3)
994
986
定压比热容/[kj/(kg•K)]
粘度/(Pa•s)
0.728×
0.54×
热导率(W/m•K)
0.624
普朗特数
4.85
3.42
设备结构参数
形式
固定板式
壳程数
1
壳体径/㎜
800
台数
管径/㎜
Φ25×
2.5
管心距/㎜
32
管长/㎜
7000
管子排列
正三角形排列
管数目/根
340
折流板数/个
27
传热面积/㎡
.91
折流板间距/㎜
240
管程数
4
材质
碳钢
主要计算结果
流速/(m/s)
1.5
0.2
表面传热系数/[W/(㎡•K)]
6629
3046.3
污垢热阻/(㎡•K/W)
0.0006
0.0004
阻力/Pa
57030.75
10173.1
热流量/KW
传热温差/℃
25
传热系数/[W/(㎡•K)]
400
裕度/%
28%
七、结构设计
1、固定管板及法兰结构设计:
由于换热器的径已确定,采用标准径、固定定管板外径及各结构尺寸,结构尺寸为:
公称直径
D
b
c
d
螺栓孔数
930
890
798
843
40
10
23
36
2、管板与壳体的连接
在固定管板式换热器中,管板与壳体的连接均采用焊接的方法。
由于管板兼作法兰与不兼作法兰的区别因而结构各异,前者的结构是在管板上开槽,壳体嵌入后进行焊接,壳体对中容易,施焊方便,适合于压力不高、物料危害性不高的场合。
3、管子与管板的连接
管子与管板的连接是管壳式换热器制造中最主要的问题。
对于固定管板换热器,除要求连接处保证良好的密封性外,还要求接合处能承受一定的轴向力,避免管子从管板中拉脱。
管子与管板的连接方法主要是胀接和焊接。
胀接是靠管子的变形来达到密封和压紧的一种机械连接方法,如图1-13所示。
当温度升高时,材料的刚性下降,热膨胀应力增大,可能引起接头的脱落或松动,发生泄露。
一般认为焊接比胀接更能保证严密性。
对于碳钢或低合金钢,温度在300℃以上,蠕变会造成胀接残余应力减小,一般采用焊接。
焊接接口的形式见图1-14。
图1-14(a)的结构是常用的一种;
为了减少管口处的流体阻力或避免立式换热器在管板上方滞留的液体,可采用图1-14(b)的结构;
为了不使小直径管子被熔融的金属堵住管口,则可改成图1-14(c)的结构;
图1-14(d)的形式适用于易产生热裂纹的材料,但加工量大。
胀接和焊接方法各有优缺点,在有些情况下,如对高温高压换热器,管子与管板的连接处,在操作时受到反复热变形、热冲击、腐蚀与流体压力的作用,很容易遭到破坏,仅单独采用胀接或焊接都难以解决问题,如果采用胀焊结合的方法,不仅能提高连接处的抗疲劳性能,还可消除应力腐蚀和间隙腐蚀,提高使用寿命。
目前胀焊结合的方法已得到比较广泛的。
八、强度设计计算
1、筒体壁厚计算:
由工艺设计给定设计温度71
,设计压力等于工作压力为6.9M
,选低合金结构钢板16
卷制,查得材料85
时许用应力
计算厚度:
mm
设计厚度:
名义厚度:
圆整取
有效厚度:
水压试验压力:
所选材料的屈服应力
水式实验应力校核:
水压强度满足
气密试验压力:
2、外头盖短节、封头厚度计算:
外头盖径
=1500mm,其余参数同筒体:
短节计算壁厚:
S=
短节设计壁厚:
短节名义厚度:
=40mm
有效厚度:
压力试验应力校核:
压力试验满足试验要求。
外头盖封头选用标准椭圆封头:
封头计算壁厚:
封头名义厚度:
取名义厚度与短节等厚:
3、管箱短节、封头厚度计算:
由工艺设计结构设计参数为:
设计温度为34
,设计压力为0.4M
,选用16MnR钢板,材料许用应力
,屈服强度
,取焊缝系数
=0.85,腐蚀裕度
=2mm
计算厚度:
设计厚度:
名义厚度:
结合考虑开孔补强及结构需要取
压力试验强度在这种情况下一定满足。
管箱封头取用厚度与短节相同,取
4、管箱