白车身焊装工艺设计概述Word格式.docx
《白车身焊装工艺设计概述Word格式.docx》由会员分享,可在线阅读,更多相关《白车身焊装工艺设计概述Word格式.docx(14页珍藏版)》请在冰豆网上搜索。
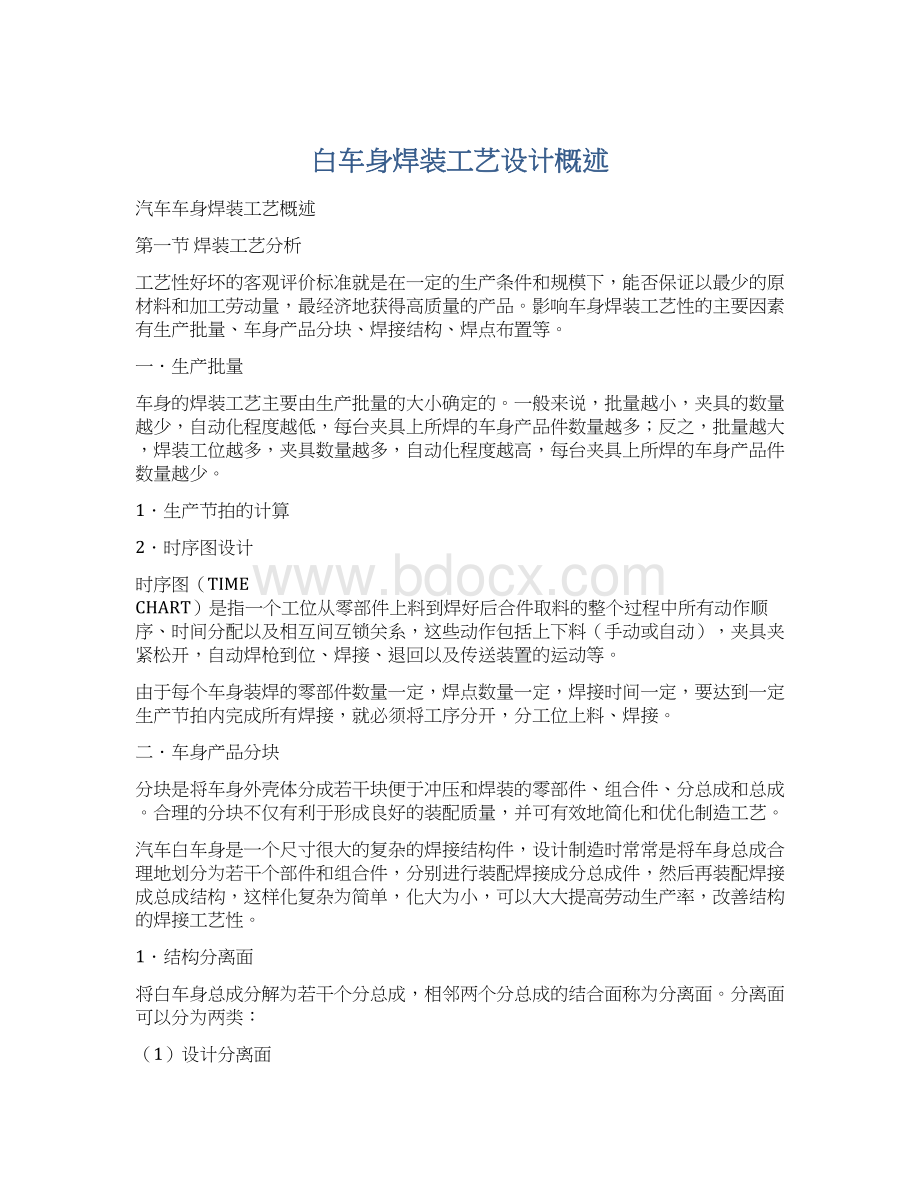
由于每个车身装焊的零部件数量一定,焊点数量一定,焊接时间一定,要达到一定生产节拍内完成所有焊接,就必须将工序分开,分工位上料、焊接。
二.车身产品分块
分块是将车身外壳体分成若干块便于冲压和焊装的零部件、组合件、分总成和总成。
合理的分块不仅有利于形成良好的装配质量,并可有效地简化和优化制造工艺。
汽车白车身是一个尺寸很大的复杂的焊接结构件,设计制造时常常是将车身总成合理地划分为若干个部件和组合件,分别进行装配焊接成分总成件,然后再装配焊接成总成结构,这样化复杂为简单,化大为小,可以大大提高劳动生产率,改善结构的焊接工艺性。
1.结构分离面
将白车身总成分解为若干个分总成,相邻两个分总成的结合面称为分离面。
分离面可以分为两类:
(1)设计分离面
根据使用上和构造上的特点,将汽车车身分成为可以单独进行装配的分总成,如发动机罩、行李厢盖、车门、车身本体等,这些分总成之间的结合面,称为设计分离面。
设计分离面一般采用可拆卸的连接,如铰链连接,以便在使用和维修过程中迅速拆卸和重新安装,而不损坏整体结构。
(2)工艺分离面
在生产制造过程中,为了适应制造装配的工艺要求,需要进一步将上级分总成分解为下一级分总成,甚至小组件,进行单独装配焊接,这些下一级分总成或组件之间的结合面,称为工艺分离面。
例如车身本体总成分解为前围、后围、地板、左/右侧围、顶盖六大分总成,这六大分总成分别平行进行单独装焊,而后总装在一起进行焊接,这些分总成之间的结合面就是工艺分离面。
工艺分离面一般采用不可拆卸的连接方法,如焊接、铆接等。
它们最终构成一个统一的刚性整体。
三.焊接结构
由于汽车车身除某些加强构件外,主要都是由低碳钢薄板冲压零件焊接而成,其厚度在0.6mm~1.5mm范围之内。
采用最多的焊接方法是电阻点焊,它将工件(PANEL)以200~300kgf程度加压至焊枪的铜电极,并瞬间(0.16~0.2秒)通过大约1万安培的高电流,以电极接触点发生的电阻热熔融结合的焊接方法。
在一辆小车的车体中大约有3000个焊点,其大部分为两层焊,根据结构也有3~4层焊。
当生产批量不大和具有密封要求的连接处,以及开敞性差的焊缝,一般采用二氧化碳气体保护焊。
1.焊接接头型式
焊接连接处称为焊接接头。
因电阻点焊的要求,车身结构的基本焊接接头型式主要是搭接接头和弯边接头。
弯边接头的焊点操作性优于搭接接头,因为弯边接头焊点直接暴露在操作台面一侧,选用小型“X”型焊钳就能很方便地进行焊接。
考虑焊接强度,弯边接头起到相当于加强梁的作用,可增大结构强度,但翻边因受冲压工艺的限制,导致贴合不理想,易产生焊接缺陷,而且弯边接头的焊点抗正应力能力比抗剪切能力差,总的对焊接强度增大不大。
考虑焊接精度,搭接接头焊点质量主要决定于工装的精度。
而弯边接头焊接质量除了与工装精度有关外,还与零件翻边精度有关,而受冲压工艺和储运方式的影响,翻边是零件质量最不稳定的地方,它容易导致两零件因贴合不好产生焊接变形,而且弯边接头的零件不利于利用工艺孔对零件作精确定位。
2.接头开敞性
封闭接头是不可能用作点焊的,半封闭接头如车身底部和内部接头也会给制造带来一定麻烦。
由于车身各连接部位不同,组成零件的形状不一样,虽然都采用搭接或弯边接头,但其结构的断面形状有很大差别。
冲压件结构型式要考虑点焊工艺性。
由于电阻点焊方法本身可达性差,在车身结构设计时,应尽量避免采用狭窄而深的或上、下电极难以接近的焊接结构和焊接接头。
3.接头的强度
点焊焊缝适宜在剪切力下工作,而不适宜在拉伸力下工作。
设计汽车车身点焊焊接结构时,应尽量使焊缝在剪切力而不是在拉力下工作。
点焊焊缝的强度与母材的种类及焊接工艺有关。
焊点受力状态:
尽量避免焊点密集布置或交汇在一起,否则金属易由于过热而产生严重应力集中及变形,影响焊接质量。
车身外板的焊接,由于焊接热应力会使表面局部变形而影响外观质量,这时可通过改变车身零件形状来消除或减轻这类缺陷。
4.焊接厚度
点焊通常用于两层薄板之间的连接,有时也用于连接叠在一起的三层薄板。
为了保证焊点的焊透率,两层焊件厚度宜相等或相近,厚度相差应不大于3倍。
连接三层板时,如板厚有差别,厚板应置于中间,有利于熔核在三层板上形成。
四.焊点布置
车身焊接中焊点的数量以及焊点间距的确定是焊装工艺性的一项重要内容。
焊点间距越小,焊点数越多,焊接强度也就越高,但分流越大,它会给产品的强度带来不利影响。
焊接质量也会因分流的影响而不易保证。
根据车身焊接接头的特点以及车身结构设计时接头的搭边宽度和焊点布置等
第二节焊装夹具的工艺方案设计
轿车车身是由上千个冲压件、近5000个焊点焊装成一个整体,每个零件之间的连接必须在三维空间中依靠焊装夹具定位,零件与零件连接形成一个整体车身。
每一个零件的连接精度,都是由焊装夹具来保证,它直接影响到功能部件,如发动机、转向器、变速器等的安装精度和性能。
重要的外形部件,如保险杠、车门、发动机盖、后箱盖、前后灯等的安装平顺性,都与车身焊装形位精度有直接的关系。
在进行焊装夹具设计之前,首先需要根据车身零件的形状、焊装工艺、焊点位置及数量来设计夹具的工艺方案,即设定焊装过程中夹具的定位基准及定位基准的形态。
一.定位基准的基本概念
基准是指某些特定(参考)点、线、面的组合,借以确定零部件中相关点、线、面的位置。
按其用途不同,可分为设计基准和工艺基准。
设计基准是指在产品图样上,设计者所选定的参考点、线、面的组合,用以确定零件轮廓、尺寸及形位公差等。
工艺基准是指在加工过程中,直接用于测量、定位、安装零部件时的实际点、线、面的组合,它分为定位基准、装配基准和测量基准。
夹具的定位基准是为了使焊好的车身组件、分总成件、总成件的位置与车身产品设计图纸、冲压成形零件的形状尺寸、车身测量数据在X、Y、Z方向上一致,所设定的焊装夹具的位置。
合理选择夹具的定位基准,可以简化焊接工艺和夹具结构,并且容易保证车身零件的装配焊接精度和质量。
选择夹具定位基准时,应尽量使其与车身零件设计基准相统一,减少因基准不重合带来的误差。
1.定位基准的种类和功能
(1)定位基准面
定位基准面有主基准和副基准两种。
主基准面是为了保证被焊零件的准确定位。
主基准面应该尽量设定在保证零件形状精度和刚性的位置上,而且数量尽可能少,一般主基准面为不可调整的形式。
副基准面是为了校正零件、辅助焊接过程或辅助焊接设备而设定的,它能约束零件的扭曲和回弹、使零件保持形状不变、校正和约束焊接变形,是焊接工装结构上必要的基准,它设计成可调整的形式。
(2)定位基准孔
定位基准孔也有主基准和副基准两种。
主基准孔的作用是固定被焊零件,它用圆柱销约束零件的两个方向,在保证可靠定位的前提下主基准孔的数量应尽可能少。
副基准孔的作用是防止被焊零件的回转,它可以用圆柱销或菱形销定位,一般选择零件上的长孔作为副基准孔,用菱形销约束零件的一个方向。
(3)定位基准端
定位基准端也有主基准和副基准两种。
主基准端使被焊零件准确定位,它确定一个方向的位置,不可调整。
副基准端是为了辅助焊接过程或焊接设备而设定的,它是约束焊接变形和焊接时两个零件错位的基准,设计成可调整的形式。
2.定位基准选择的优先顺序
(1)考虑车身零件的制造工艺,定位基准确定的先后顺序为总成、分总成、组件、零件。
因为如果装配件的定位基准不确定,则不可能对零部件的精度确定及正确评价,也无法决定零部件的准确修正方向。
同时为了使车身零件在制造过程中的变化要素最小,需要把含有更多变化要素的装配件上的定位基准首先确定。
(2)为了确定车身零部件的位置,需要基准孔、基准面和基准端的组合,但是在同一方向上约束时,采用基准面、孔、端的顺序不同。
考虑车身零件的形状,定位基准选择的先后顺序为基准面基准孔基准端。
这与冲压零件的成形顺序一致,即先拉延后冲孔。
优先选用基准面可以使相邻零件的贴合面累积误差最小,也容易补偿刚性不足的零件形状,而且如果基准孔的位置和孔间距不准确会造成被焊零件的位置不稳定。
3.定位基准位置的选定方法
夹具定位基准的选定必须以冲压件零件图、装配焊接后的组件图、车身焊装工艺流程和工艺方案、车身装配公差要求以及基本车型的相关资料为依据。
其选用方法为:
(1)夹具定位基准面的厚度一般为16mm,只有地板框架处夹具定位基准面的厚度选为19mm。
为了便于夹具设计与检测,定位基准面尽量选在与车线平行的位置,且与车线之间的距离为整数;
若定位基准的位置与车线倾斜,则从车线处标注尺寸和角度。
(2)定位基准面要尽可能选在断面形状一致的位置,尽量避免断面发生变化的位置。
因为断面发生变化的位置容易造成零件变形,很难精确定位。
(3)定位基准孔要尽可能与定位基准面不重合。
这是因为基准孔与基准面的定位方向不同,当零件定位基准面发生变化时,定位基准孔的位置也发生变化。
(4)分析整条生产线上各工位零件的构成以及各构成零件的位置,使定位基准的位置尽量选在能贯穿整条生产线的位置上,即生产线上各工位的定位基准尽量保持一致,以减小工位间的定位偏差。
(5)定位基准尽量选在被焊零件有贴合要求或功能要求的位置,如有装配关系要求的面或孔,有位置尺寸要求的端部或孔等。
(6)定位基准尽量选在容易上件取料的位置,容易实现焊装自动化的位置,以及使装配累积误差最小化的位置上。
(7)对于相同零件的定位,其定位基准位置尽量要统一。
(8)定位基准要选在可以减小焊接变形的位置上。
当焊接面的长度足够时,可以将定位基准面直接选在焊接面上。
(9)各被焊零件要尽可能单独定位,不能只依靠相邻零件型面的贴合来定位。
第三节车身焊装生产线
一.车身焊装生产线的组成
车身焊装生产线是轿车、微型客车等车型生产过程中的几个主要生产线之一,其空间作业内容复杂且自动化程度较高。
车身焊装生产线是汽车白车身(BODYINWHITE)全部成型工位的总称,它由车身总成线和许多分总成线组成。
1.车身完成线(SLATLINE)
车身完成线是一条车身装配生产线,它通过铰链连接方式分别将焊装好的前后车门,翼子板,发动机罩,行李厢盖或背门与车身本体连接装配,形成白车身(BodyInWhite),同时对车身焊接质量进行检测和修磨。
车身完成线的特点是整条生产线不需要焊接,是机械铰链连接,属于可拆卸连接,无任何焊接设备;
基本上是手工作业;
是整个车身焊装生产线的最后一道工序,完成后的产品即为白车身,将输送到涂装车间进行表面处理。
2.主焊线(MAINLINE)
主焊线是车身焊装车间最重要的一条焊装生产线,它完成车身六大分总成(地板,左右侧围,顶盖,通风罩及仪表板,后行李台)的焊接,有时也叫车身总成生产线。
车身总成工位是主焊线上的一个核心工位,在这个工位上,实现六大总成的装配。
其中地板总成的上料是通过地板传送机构(UNDERSHUTTLE)直接传送到总成工位;
侧围总成的自动上料方式有移动式、旋转式、移动翻转式和2-4位翻转基座式;
顶盖、通风罩、后行李台是利用自动