管板式换热器设计说明书Word下载.doc
《管板式换热器设计说明书Word下载.doc》由会员分享,可在线阅读,更多相关《管板式换热器设计说明书Word下载.doc(25页珍藏版)》请在冰豆网上搜索。
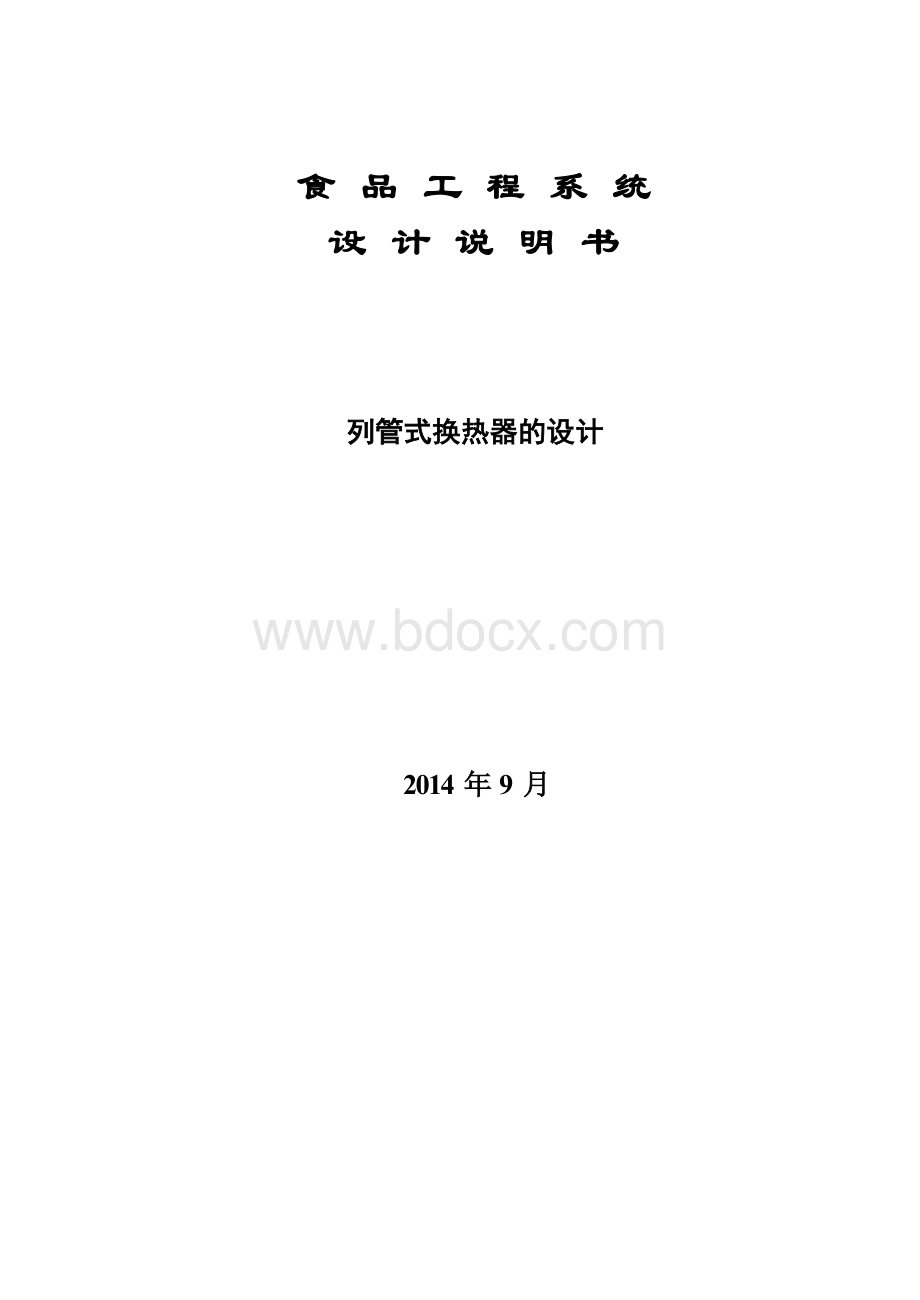
3.2平均传热温差 7
3.3稀盐水用量 7
3.4传热面积A的计算 7
4结构设计 8
4.1管径和管内流速 8
4.2管程数和传热管数 8
4.3传热管的排列和分程方法 8
4.4壳体内径 9
4.5折流板 9
4.6接管 10
4.7法兰 10
4.8支座 11
4.9垫片 11
4.10换热器主要传热参数计算 12
5强度计算 15
5.1筒体壁厚计算 15
5.2管箱短节、封头厚度的计算 16
5.3壳体接管开孔补强校核 17
5.4管板设计及校核 18
6总结 21
参考文献 23
1绪论
1.1课程设计提出的背景及应用价值
化工生产离不开化工设备,化工设备是化工生产必不可少的物质技术基础,是生产力的主要因素,是化工产品质量保证体系的重要组成部分[1]。
然而在化工设备中化工容器占据着举足轻重的地位,由于化工生产中,介质通常具有较高的压力,化工容器一般有筒体、封头、支座、法兰及各种容器开孔接管所组成,通常为压力容器,因为压力容器是化工设备的主体,对其化工生产过程极其重要,国家对其每一步都有具的标准对其进行规范,如:
中国《压力容器安全技术监察规程》、GB150—1998《钢制压力容器》、GB151—1999《管壳式换热器》等。
在其中能根据不通的操作环境选出不同的材料,查出计其允许的工作压力,工作温度等[2]。
1.2研究和使用现状
不同温度的流体间传递热能的装置称为热交换器,简称为换热器。
简单说是具有不同温度的两种或两种以上流体之间传递热量的设备。
在工业生产过程中,进行着各种不同的热交换过程,其主要作用是使热量由温度较高的流体向温度较低的流体传递,使流体温度达到工艺的指标,以满足生产过程的需要。
此外,换热设备也是回收余热,废热,特别是低品位热能的有效装置[3]。
在化工生产中换热器的使用十分普遍,由于物料的性质、要求各不相同,换热器的种类很多。
了解各种换热器的特点,根据工艺要求正确选用适当类型的换热器是非常重要的。
按照热量交换的方法不同,分为间壁式换热器、直接接触式换热器、蓄热式换热器三种。
化工生产中绝大多数情况下不允许冷、热两流体在传热过程中发生混合,所以,间壁式换热器的应用最广泛。
在换热器中至少要有两种温度不同的流体,一种流体温度较高,放出热量:
另一种流体温度较低,吸收热量。
换热器在化工、石油、动力、制冷、食品等行业中都有广泛应用,且它们是上述这些行业的通用设备,并占有十分重要的地位。
1.2.1管壳式换热器的分类
换热器的种类划分方法很多,方法也各不相同。
按其用途:
可将换热器分为加热器、冷却器、冷凝器、蒸发器、再沸器[4]。
按其传热方式和作用原理:
可分为混合式换热器、蓄热式换热器、间壁式换热器等。
其中间壁式换热器为工业应用最为广泛的一种换热器。
它按传热面形状可分为管式换热器、板面式换热器、扩展表面换热器等。
这其中又以管壳式换热器应用最为广泛,它通过换热管的管壁进行传热。
具有结构简单牢固、制造简便、使用材料范围广、可靠程度高等优点,是目前应用最为广泛的一种换热器。
根据管壳式换热器的结构特点,常将其分为固定管板式、浮头式、U型管式、填料函式、滑动管板式、双管式等[5]。
1)固定管板式换热器
固定管板式换热器主要是由筒体、封头、管板、换热管、管箱、折流板及法兰等组成,管束两端固定在管板上,管板和筒体之间焊接,相互之间无相对移动,换热器结构简单、制造方便、紧凑、能承受较高的压力,造价较低;
在相同直径的壳体内可排列较多的换热管,而且每根换热管都可单独进行更换和管内清洗;
但管外壁清洗较困难。
当两种流体的温差较大时,会在壳壁和管壁中产生温差应力,一般当温差大于50摄氏度时就应考虑在壳体上设置膨胀节以减小温差应力。
但当管、壳温差大于70摄氏度时,壳程压力超过0.6Mpa时,导致膨胀节过厚失去温差补偿作用。
因此,固定管板式换热器适用于壳测介质清洁且不易结垢、并能进行清洗、管程与壳程两侧温差不大或温差较大但壳测压力不高的场合[6]。
2)浮头式换热器
浮头式换热器的两端管板中只有一端与壳体固定,另一端可相对壳体自由移动,称浮头。
浮头由浮头管板、钩圈和浮头端盖组成,是可拆连接,管束可从壳体内抽出。
管束与壳体的热变形互不约束,因而不会产生热应力[7]。
浮头换热器的特点是管间与管内清洗方便,不会产生热应力;
但其结构复杂,造价比固定管板式换热器高,设备笨重,材料消耗大,且浮头端小盖在操作中无法检验,制造时对密封要求较高。
适用于壳体与管束之间壁温差较大或壳程介质易结垢的场合。
3)U形管换热器
U形管式换热器的结构特点是,只有一块管板,管束由多根U形管组成,管的两端固定在同一根管板上管子可自由伸缩,其管程至少为两程。
当壳体与U形换热管有温差时,不会产生热应力[8]。
U型管式换热器的优点是结构简单,密封面少,运行可靠;
管束可以抽出,管间清洗方便。
价格便宜、承压能力强。
特别适用于管内走清洁而不易结垢的高温、高压、腐蚀性大的物料。
其缺点是管内清洗困难;
由于管子需要一定的弯曲半径,故管板的利用率较低;
管束最内程管间距大,壳程易短路,对传热不利;
内程管子损坏不能更换,因而报废率较高。
此外,其造价比管定管板式高10%左右。
4)填料函式换热器
填料函式换热器的结构特点与浮头式换热器相类似,浮头部分露在壳体以外,在浮头与壳体的滑动接触面处采用填料函式密封结构。
由于采用填料函式密封结构,使得管束在壳体轴向可自由伸缩,壳壁与管壁不会产生热变形差,从而避免可热应力。
其结构较浮头式换热器简单,加工制造方便,节省材料,造价比较低廉,且管束从壳体内可以抽出你,管内,管间都能清洗,维修方便[9]。
1.2.2管壳式换热器结构
管壳式换热器的主要零部件有壳体、接管、封头、管板、换热管、折流元件等,对于温差较大的固定管板式换热器,还应包括膨胀节。
管壳式换热器的结构应该保证冷、热两种流体分走管程和壳程,同时还要承受一定温度和压力的能力[10]。
(1)管板:
管板是换热器的重要元件,主要是用来连接换热器,同时将管程和壳程分隔,避免冷热流体相混合。
当介质无腐蚀或有轻微腐蚀时,一般采用碳素钢、低合金钢板或其锻件制造。
(2)管子与管板的连接:
管子与管板的连接必须牢固,不泄漏。
既要满足其密封性能,又要有足够的抗拉强度。
其连接形式主要有强度胀接、强度焊接、胀焊结合等[11]。
(3)管箱:
其作用是把管道中来的流体均匀分布到各换热管中,将换热管内流体汇集在一起送出换热器[12]。
(4)折流板和支承板:
壳程内侧装设折流板或支承板,折流板的作用是组壳间流道,使流体以适当的流速冲刷管束,提高传热系数,改善传热效果,以达到一定的传热强度。
常用的折流板有弓形和圆环形两种,弓形折流板又分为单弓形、双弓形和三弓形[13]。
(5)拉杆和定距管:
折流板的安装一般是用拉杆和定距管组合并与管板固定在一起。
拉杆与管板连接的一端可用焊接或螺纹连接,另一端也用焊接或螺纹固定。
一般拉杆的直径不得小于10mm、数量不得小于4根[14]。
(6)管板与壳体的连接:
其连接型式可分为不可拆式和可拆式。
1.2.3换热器的发展趋势
管壳式换热器具有结构坚固、弹性大和使用范围广等独特优点,一直被广泛应用。
尤其在高温高压和大型化的场合下,以及制造工艺上的进一步自动化和机械化,管壳式换热器今后将在广泛的领域内得到继续发展。
目前各国为提高这类换热器性能进行的研究主要是强化传热,促进设备结构的紧凑性,加强生产制造成本的标准系列化,并在广泛的范围内继续向大型化发展,并CDF模型化技术、强化传热技术及新型换热器开发等形成一个高技术体系[15]。
强化传热的主要途径有提高传热系数、扩大传热面积和增大传热温差等方式,其中提高传热系数是强化传热的重点,主要是通过强化管程传热和壳程传热两个方面得以实现。
目前,管壳式换热器强化传热方法主要有:
采用改变传热元件本身的表面形状及其表面处理方法,以获得粗糙的表面和扩展表面;
用添加内插物的方法以增加流体本身的绕流;
将传热管的内外表面轧制成各种不同的表面形状,使管内外流体同时产生湍流并达到同时扩大管内外有效传热面积的目的,提高传热管的传热性能;
将传热管表面制成多孔状,使气泡核心的数量大幅度增加,从而提高总传热系数并可增加其抗污垢能力;
改变管束支撑形式以获得良好的流动分布,充分利用传热面积等。
换热器相关技术的发展主要表现在以下几发面:
防腐技术,大型化与小型化并重,强化技术,抗振技术,防结垢技术,制造技术,研究手段。
随着工业中经济效益与社会环境保护的要求,制造水平的不断提高,新能源的逐渐开发,研究手段的日益发展,各种新思路的与新结构的涌现,换热器将朝着更高效、经济、环保的方向发展。
1.3本设计的内容
本设计主要研究的是固定管板式换热器,查阅换热器相关标准,分析固定管板式各部分性能影响,并进行了换热器的热工计算、结构计算和强度计算[16]。
换热器的应用广泛,日常生活中取暖用的暖气散热片、汽轮机装置中的凝汽器和航天火箭上的油冷却器等,都是换热器。
它还广泛应用于化工、石油、动力和原子能等工业部门。
近年来,随着制造技术的进步,强化换热元件的开发,使得新型高效换热器的研究有了较大的发展,根据不同的工艺条件与工况设计制造了不同结构形式的新型换热器,也取得了较大的经济效益。
故我们在选择换热设备时一定要根据不同的工艺、工况要求选择。
换热器的作用可以是以热量交换为目的。
在即定的流体之间,在一定时间内交换一定数量的热量;
也可以是以回收热量为目的,用于余热利用;
也可以是以保证安全为目的,即防止温度升高而引起压力升高造成某些设备被破坏[17]。
本设计的内容是:
总体方案的选择、管板式换热器的设计计算、结构设计。
2总体方案的选择
首先对固定管板式换热器进行热工设计的计算,它的设计程序或步骤随着设计任务数和原始数据的不同而不同,要尽可能的使已知数据和要设计计算的项目顺次编排,但由于许多项目之间互相关联,无法排定顺序,故往往先根据经验选定一个数据使计算进行下去,通过计算得到结果后再与初始假定的数据进行比较,知道达到规定的偏差要求,试算才告结束。
一般换热器的设计程序如下:
(1)根据生产任务和有关要求确定设计方案;
(2)确定换热器类型和主要结构;
(3)根据换热量要求,计算换热面积,确定换热管与壳体尺寸;
(4)核算换热器的传热能力及流动阻力;
(5)确定换热器的工艺结构,形成工艺简图。
2.1换热器类型的选择
按照设计的要求,热流体物料入口温度95℃,出口温度45℃,冷流体物料,入口温度30℃,出口40℃,操作压力小于0.6MPa,因此初步确定选用固定管板式换热器。
2.2材料选择及流速确定
稀盐水易结垢,为便于清洗,应该走管程,牛奶为粘度较大的流体走壳程。
冷却稀盐水与牛奶在设计的换热器中进行热交换,牛奶由95℃冷却到45℃。
冷却稀盐水由初温30℃升温至40℃。
按照一般情况,选用规格为25*2.5mm的碳素钢无缝管(换热管标准:
GB8163)。
当冷、热流体的进出口温度相同时,逆流操作的平均推动力大于并流,因而传递同样的热流体,所需的传热面积较小。
逆流操作时,冷却介质温升可选择得较大因而冷却介质用量可以较小。
显然在一般情况下,逆流操作总是优于并流。
2.3