SiC陶瓷的高压烧结工艺及性能本科毕业设计Word文件下载.docx
《SiC陶瓷的高压烧结工艺及性能本科毕业设计Word文件下载.docx》由会员分享,可在线阅读,更多相关《SiC陶瓷的高压烧结工艺及性能本科毕业设计Word文件下载.docx(24页珍藏版)》请在冰豆网上搜索。
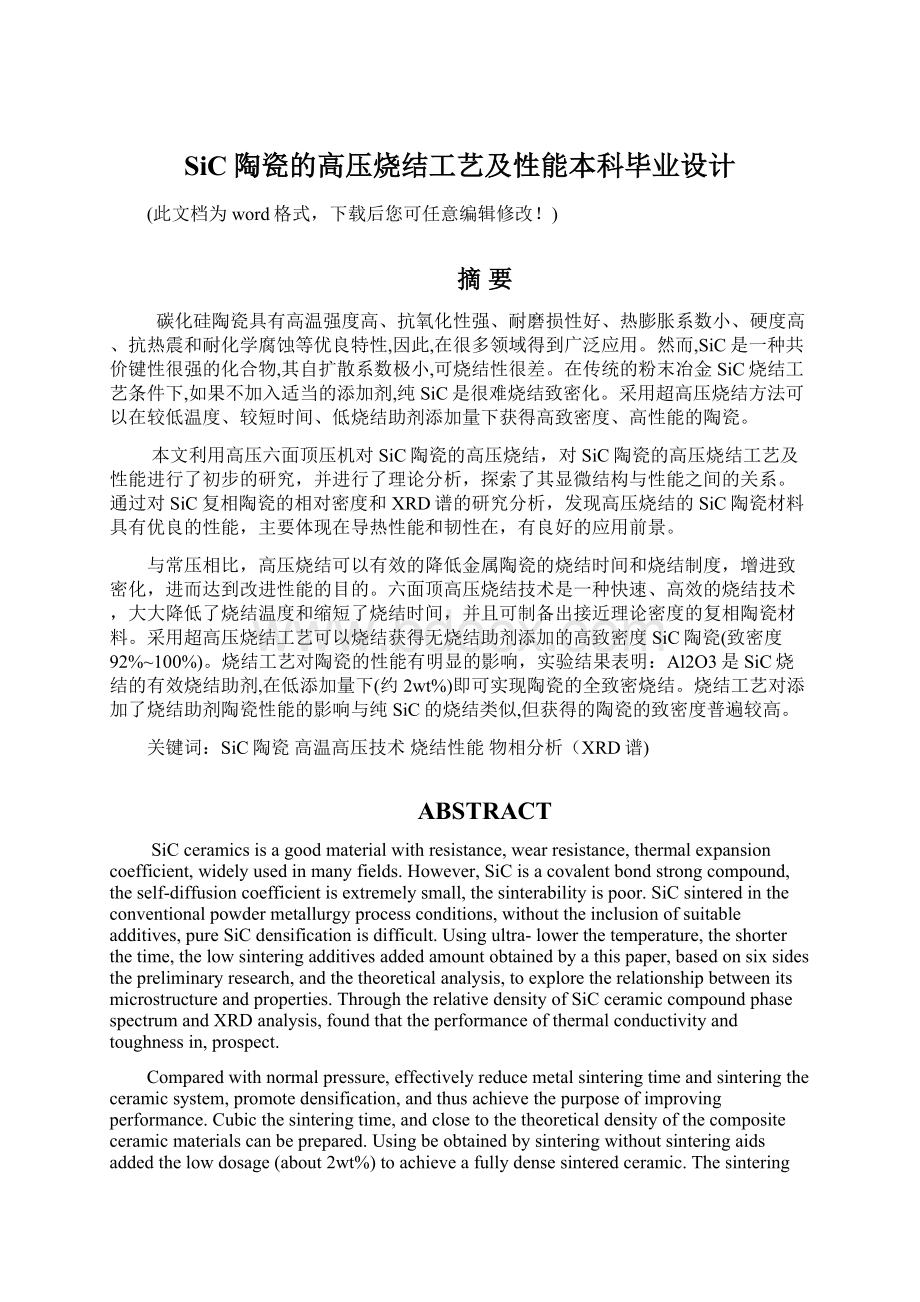
通过对SiC复相陶瓷的相对密度和XRD谱的研究分析,发现高压烧结的SiC陶瓷材料具有优良的性能,主要体现在导热性能和韧性在,有良好的应用前景。
与常压相比,高压烧结可以有效的降低金属陶瓷的烧结时间和烧结制度,增进致密化,进而达到改进性能的目的。
六面顶高压烧结技术是一种快速、高效的烧结技术,大大降低了烧结温度和缩短了烧结时间,并且可制备出接近理论密度的复相陶瓷材料。
采用超高压烧结工艺可以烧结获得无烧结助剂添加的高致密度SiC陶瓷(致密度92%~100%)。
烧结工艺对陶瓷的性能有明显的影响,实验结果表明:
Al2O3是SiC烧结的有效烧结助剂,在低添加量下(约2wt%)即可实现陶瓷的全致密烧结。
烧结工艺对添加了烧结助剂陶瓷性能的影响与纯SiC的烧结类似,但获得的陶瓷的致密度普遍较高。
关键词:
SiC陶瓷高温高压技术烧结性能物相分析(XRD谱)
ABSTRACT
SiCceramicsisagoodmaterialwithresistance,wearresistance,thermalexpansioncoefficient,widelyusedinmanyfields.However,SiCisacovalentbondstrongcompound,theself-diffusioncoefficientisextremelysmall,thesinterabilityispoor.SiCsinteredintheconventionalpowdermetallurgyprocessconditions,withouttheinclusionofsuitableadditives,pureSiCdensificationisdifficult.Usingultra-lowerthetemperature,theshorterthetime,thelowsinteringadditivesaddedamountobtainedbyathispaper,basedonsixsidesthepreliminaryresearch,andthetheoreticalanalysis,toexploretherelationshipbetweenitsmicrostructureandproperties.ThroughtherelativedensityofSiCceramiccompoundphasespectrumandXRDanalysis,foundthattheperformanceofthermalconductivityandtoughnessin,prospect.
Comparedwithnormalpressure,effectivelyreducemetalsinteringtimeandsinteringtheceramicsystem,promotedensification,andthusachievethepurposeofimprovingperformance.Cubicthesinteringtime,andclosetothetheoreticaldensityofthecompositeceramicmaterialscanbeprepared.Usingbeobtainedbysinteringwithoutsinteringaidsaddedthelowdosage(about2wt%)toachieveafullydensesinteredceramic.ThesinteringprocessissimilarwithaddedthesinteringaidsCeramicspureSiCsinteredsimilar,butthedensityoftheceramicisgenerallyV等以四乙氧基硅烷、甲基三乙氧基硅烷作硅源,以酚醛树脂、淀粉等为碳源,形成的凝胶在氮气中于800℃炭化得到SiC前驱体,再于氩气中1550℃加热,得到了5~20nm的SiC。
Narisaw等通过冷凝乙基硅酸脂、硼酸脂、酚醛树脂的混合物得到有机-无机混合前驱体,于1237K减压裂解得到含Si和C的前驱体,再由碳还原法得到SiC,过量C和B的加入有助于获得细小规则的产品。
液相反应法可制备高纯度、纳米级的SiC微粉,而且产品均匀性好,是一种具有良好发展前景的方法。
液相反应法制备SiC微粉主要分为溶胶-凝胶法和聚合物热分解法等。
溶胶-凝胶法制备SiC微粉的核心是通过溶胶-凝胶反应过程,形成Si和C在分子水平上均匀分布的混合物或聚合物固体,升温过程中,首先形成SiO2和C的均匀混合物,然后在1400~1600℃温度下发生碳热还原反应生成SiC。
聚合物热分解法主要是指加热聚硅烷等聚合物,放出小单体,形成Si-C骨架。
由热解法制备的SiC均为β-SiC。
如果热解温度低于1100℃,则为无定形SiC。
控制溶胶-凝胶化的主要参数有溶液的pH值、溶液浓度、反应温度和时间等。
该法在工艺操作过程中易于实现各种微量成份的添加,混合均匀性好;
但工艺产物中常残留羟基、有机溶剂对人的身体有害、原料成本高且处理过程中收缩量大是其不足。
固相法还包括聚合物热分解法。
有机聚合物的高温分解是制备碳化硅的有效技术:
一类是加热凝胶聚硅氧烷,发生分解反应放出小单体,最终形成SiO2和C,再由碳还原反应制得SiC粉。
另一类是加热聚硅烷或聚碳硅烷放出小单体后生成骨架,最终形成SiC粉末。
MitchellBrianS等用含氯的聚碳硅烷前驱体合成了SiC。
谢凯等报道了以低分子聚碳硅烷为原料,用气相热裂解工艺制备了SiC粉体,反应在常压和1150℃下进行,便于控制、重现性好,适于扩大再生产。
气相反应沉积法简称CVD,包括等离子体法和激光诱导气相法。
该法是在80年代后期发展起来的,是在远大于理论反应温度时,使反应产物蒸汽形成很高饱和蒸气压,导致其自动凝聚成晶核,而后聚集成颗粒。
常用硅烷和烃类为原料,采用电炉或火焰加热,可合成纯度高、粒径10~100nm的均匀的微粒。
具有操作容易、过程可控、易于连续化生产、投资小等特点,是一种比较有前途的方法。
但缺点是要求原料纯度高、加热温度低、反应器内温度梯度小、产品粒度大易团聚和烧结,产率也不高。
等离子体法(PlasmaInducedCVD)始于80年代,是利用等离子体产生的超高温激发气体发生反应,等离子体高温区域周围形成巨大的温度梯度,通过急冷作用得到纳米颗粒。
具有反应时间短,高温、高能量密度和高冷却速度的优点,易于批量生产。
缺点是等离子枪寿短、功率小、热效率低、气体效果差。
此法可分为直流电弧等离子法(direct-currentarcplasma)、高频等离子体法(radio-frequencyplasma)、微波等离子体法等,见表1-2。
表1-2等离子体发生法及其参数
电子浓度
cm-3
气体压力
kPa
电子温度
K
气体温度
K
直流辉电
<13.3
~106
~700
光晕放电
<106
>133
<104
~400
高频放电
102~1010
<133
微波放电
1011
~100
近年来关于微波等离子体化学反应的研究在国际上明显呈上升趋势,与电弧等离子体技术相比,为无极放电,可获得纯净的且密度较高的粉体;
与直流电弧或高频等离子体技术相比,微波等离体温度较低,在热解过程中不致引起致密化或晶粒过大。
如欧阳世翕等在高纯石墨衬底上用微波等离子体(MPECVD)法低温沉积β-SiC膜获得成功,在沉积室内体压力大于13.3KPa时,等离子体区变窄,功率集中,基本温度升高,沉积速率加快而形成超细粉末。
激光诱导气相法是用激光法合成高纯超细粉末最先由麻省理工学院倡导,以激光为快速加热热源,使气相反应物分子内部快速地吸收和传递能量,在瞬时完成气相反应的成核、长大。
常用大功率CO2激光,由于反应核心区与反应器之间被原料气所隔离,污染极小,是当前能稳定获得高纯超细粉体的重要方法。
但激光器效率低、电能消耗大、投资大而难以规模化生产,并且其详细化学和晶体学过程也有待于深入研究。
目前,用激光法制SiC所用原料一直限于成本较高的硅烷类气体,寻求廉价的新反应物是实现工业生产亟待解决的研究课题,李亚利等在实验室中用激光热解廉价、无毒、无腐蚀性的二甲基二乙氧基硅烷制得了SiC微粉。
除上述制备方法外,还有人报道过低温液相合成法:
在110~160℃反应得到的非晶态产物在1500℃下煅烧得到结晶态SiC粉,副产物NaCl也同时被除去。
1.3碳化硅烧结方法
SiC不同的烧结方法可以导致不同的显微力学结构性能,而这些对于材料的特殊应用特别重要。
目前主要的SiC材料烧结方法主要有:
反应烧结法、再结晶烧结法、渗硅烧结法、化学气相沉积法、无压烧结法、等离子体电火花(SPS)烧结、正压烧结。
1.3.1反应烧结
反应烧结SiC又称自结合SiC。
SiC的反应烧结技术是20世纪50年代开始研究的课题,SiC硬度大、熔点高,用一般方法难以烧结成型,故采用反应烧结是一个很好的方法,此法己经在工业中获得应用。
将α-SiC粉和石墨粉按一定比例混合压成坯块,加热到1650℃左右,熔渗硅或通过气相与C反应生成β-SiC,把原先的α-SiC结合起来。
用溶渗硅的办法可以获得致密产品但产品中含有8%~10%未与C反应的Si。
反应烧结的陶瓷一般可以分为三类:
SiC-Si陶瓷、耐高温反应烧结陶瓷、金属增韧反应烧结陶瓷。
这种工艺具有处理温度低,可以制备大尺寸、形状复杂的制品,样品处理过程中尺寸变化小且制品完全致密,制品处理时间短,不需特殊、昂贵的设备等特点。
1.3.2再结晶烧结法
早在19世纪末就已经有了再结晶碳化硅(RSiC)的专利,但其大规模应用20世纪末才发展起来,可能是因为到那时才使用了大生产能力的高温烧结窑的缘故。
RSiC具有较高的稳定性、良好的导热性和较高的强度,主要应用在陶瓷炉窑等耐高温设备中。
RSiC烧结模型为汽化凝结机理。
由于气体相里只有极少量的SiC分子,所以这里并不是指简单的汽化(或称作升华)。
而是指在SiO2的参与下SiC晶格分解。
原则上讲,在每个SiC晶粒上都有一层氧化产品,即SiO2薄层,这种SiO2薄层在温度升高时如下挥发,这样,表面的露出的SiC和Si进行反应。
再结晶烧结法并不能提高材料的烧结致密度,要求起始粉末有高致密度,烧结材料的耐高温性能不错,但由于有SiO2玻璃相的存在其耐高温性能及力学