年产280万吨热轧带钢车间设计Word文档下载推荐.doc
《年产280万吨热轧带钢车间设计Word文档下载推荐.doc》由会员分享,可在线阅读,更多相关《年产280万吨热轧带钢车间设计Word文档下载推荐.doc(8页珍藏版)》请在冰豆网上搜索。
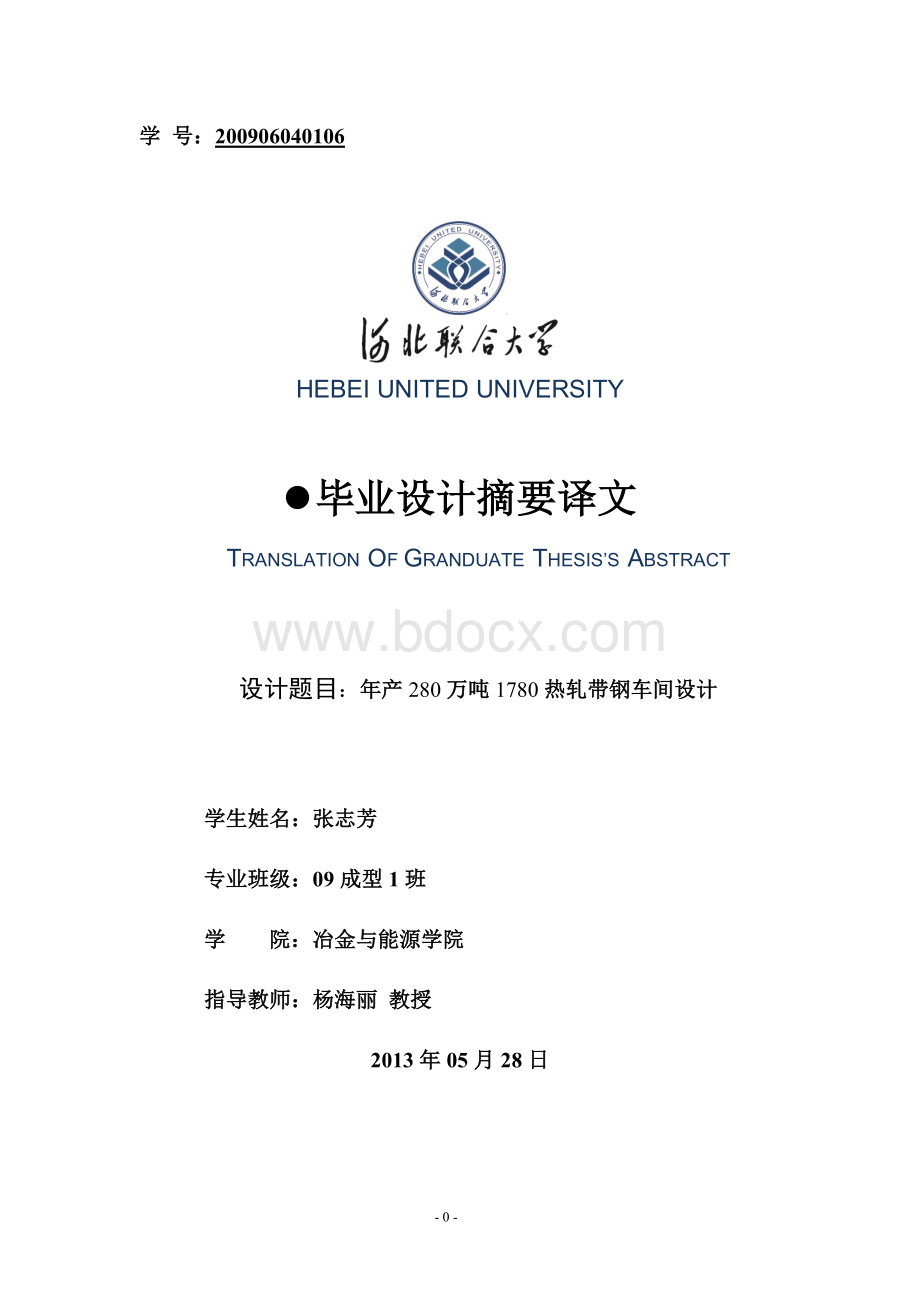
学生姓名:
张志芳
专业班级:
09成型1班
学院:
冶金与能源学院
指导教师:
杨海丽教授
2013年05月28日
摘要
板带材生产技术水平不仅是冶金工业生产发展水平的重要标志,也反映了一个国家工业与科学技术发展的水平。
建设现代化的热轧宽带钢轧机要满足现代工业对热轧板品种质量的要求。
最终产品的质量取决于连铸坯的质量,传统厚度的板坯连铸工艺明显优于薄板坯连铸工艺。
薄板坯连铸连轧更适于生产中低档板材品种,在薄规格产品生产方面具有明显优势。
为了满足高质量和高性能板材要求,采用厚板坯常规连轧生产方式更合理。
本设计为年产280万吨1780热轧带钢车间设计,典型产品厚度为3.0mm。
为了满足高质量和高性能板材要求,本次设计结合唐钢1700mm、宁钢1780mm、鞍钢1780mm热轧车间设计了年产280万吨的1780mm常规热轧车间。
设计采用两架四辊可逆粗轧机,轧制六道次,精轧机选用六架非可逆轧机轧制六道次,通过采用CVC轧机、PC轧机和厚度自动控制(AGC)等技术相结合来控制板型和厚度,在精轧前采用无芯轴隔热屏热卷箱。
本设计粗轧机组选用两架独立的可逆轧机,两架带立棍的强力四辊可逆轧机,共完成6个道次粗轧,不但解决了粗轧轧制时间过长、与精轧机不匹配的问题,还能保证中间坯厚度及凸度的稳定性。
精轧选用6机架连轧,前四架采用板型控制良好的CVC技术。
全线采用许多新技术来保证稳定生产。
产品在质量、精度等各方面居于先进水平。
热轧板带机轧制连铸坯,生产厚度为1.5~12.0mm的带钢。
板坯在加热炉中加热到1200℃左右,由两架粗轧机将板坯轧到30mm左右。
粗轧后,由飞剪切头,进入精轧。
带钢经过由六架组成的精轧机组轧制。
然后,再经过层流冷却进行冷却,最后由地下卷取机卷取。
最终产品可经过冷轧进行再加工。
轧制前先除鳞,除鳞的方法有多种,而现代工厂只采用投资很少的高压水除鳞箱及轧机前后的高压水喷头即可满足除鳞要求,其水压过去为12MPa左右,嫌低,现已采用15~25MPa以上,合金钢则需更高的水压值。
考虑到缩短车间长度和粗轧时奥氏体回复再结晶程度以适应给冷轧薄板供坯的工艺需求,本次设计采用了两架独立的粗轧机,板坯在粗轧机上共轧制六道次,如果板坯厚度小,粗轧还可以分配空轧道次,同样可达到节能效果。
根据产品大纲要求,生产薄规格为6.0~15.0mm带钢要占40%以上,为提高精轧入口温度,减少中间坯头尾温差,提高终轧温度(绝大部分要在850℃以上),保证带钢应有的质量、内部组织性能,粗、精轧间采用保温设施是必要的。
热卷取箱保温效果较好,一次性设备投资虽高一些,但技术成熟,设备运转可靠,生产、维护费用较低,所以本设计选用它。
精轧机组的布置为六机架连轧。
带坯在进入精轧机之前,首先要进行测温、测厚并接着用飞剪切去头部和尾部。
切头的目的是为了除去温度过低的头部以免损伤辊面,并防止“舌头”、“鱼尾”卡在机架间的导卫装置或辊道缝隙中。
有时还要把轧件的后端切去,以防后端的“鱼尾”或“舌头”给卷取及其后的精整工序带来困难。
现代的切头飞剪机一般装置有两对刀刃,一对为弧形刀,用以切头,这有利于减小轧机咬人时的冲击负荷也有利于咬钢和减小剪切力。
飞剪设备主要用于切头、切尾、事故剪断及成品倍尺剪切,它在消除开花头子、减少头尾翘皮、倍尺优化和事故剪断等方面有着十分重要的作用。
由于飞剪是在轧件运行中进行剪切的,这就必须满足剪刃在水平方向上的分速度与轧件的运动速度同步的要求。
生产线上共设两处剪,即精轧入口与卷曲机前面,由于剪切过程是在轧件运动的同时完成的,故均选择飞剪。
活套对产品的质量起到了积极的作用。
通过活套可以调节带钢速度来保证稳定轧制。
例如,若张力较低,增加活套角,增大张力,使轧制稳定。
若张力较大,减小活套角,减小张力。
更全面的说,为了减小张力波动,活套角应保持在一定的角度。
为了在非稳定轧制时调节大的速度波动,活套角需有一个比较大的变化范围。
为了保证热轧中带钢的质量和速度,可以采用同时控制活套角和张力的方法。
在传统方式中,通过改变电机的速度来控制活套角,但没有张力反馈控制,这是因为在机架内部安装和固定张力测量装置有一定的困难。
传统的PI控制就是依据这种原理,这种控制在工业中曾被广泛应用。
为了满足产品大纲的所有产品的力学性能,机械性能和金属组织,终轧后选择层流冷却方式对带钢进行冷却,层流冷却采用恒定压力的低压水进行冷却,形成柱状水流,而且有比喷射多的动能冲击在板面上,击破板面的蒸气膜,形成核沸腾,整个冷却段大约27米,分为6段控制,其中最后1段可以实现水量微调控制以满足卷取温度误差控制,冷却水量6000立方米每小时,为了方便维修,上面的喷水横梁设计成为液压缸驱动的可以开闭式。
层流冷却系统的设计适用于全厚度范围,每一段的压力是通过调节喷水横梁上面的开口度来控制的,同时保持高水位水箱的水在一定的范围内测喷设备,通过向带钢的表面积喷射水压约为10千克力每毫米的水来吹走钢表面的冷却水,其目的是防止带钢冷却温度的弥散,它安装在精轧机核每段冷却段的后面,高压喷水由气动控制阀门来打开或者关闭。
地下式卷取机布置在热连轧机输出辊道。
由于它位于辊道标高之下,所以被成为地下式卷取机。
在整个连轧机组中,卷取机的工作条件最为恶劣,也是最易出故障的环节之一。
为了保持连轧机组的生产节奏,本设计采用两台卷取机,两台交替使用。
另外该设计附有车间平面布置图,以供参考。
关键词:
半连轧工艺;
步进式加热炉;
热卷箱;
液压AGC系统
Abstract
Thehotstripproductiontechniquelevelisnotonlyaimportantmarkingofthemetallurgyindustryproducedevelopmentlevel,butalsoreflectsalevelofthenationalindustryandsciencetechnique.Thenewmodernhotwiderollingmillsshouldsatisfytherequestofmodernindustrytohotstripspeciesquality.Thequalityofendproductisbyallmeansdecidedbyqualityofcontinuouscastingslab.Thecontinuouscastingslaboftraditionalthicknessisobviouslybetterthanthinslabcontinuouscastingandrolling.Thinslabcontinuouscastingandrollingissuitabletoproducemediumlowfiletimeplankmaterialspeciesandhaveobviousadvantageatthethinspecificationproduct.Forsatisfyingtherequestofobtainingthehighqualityandhighperformancestrip,thickslabcontinuouscastingproducemethodisconsideredmorereasonable.
The1780isdesignedtoproduce2.8milliontonsofhotrolledstripplantdesign,atypicalproductthickness3.0mm.Tomeettherequirementsofhighqualityandhighperformanceboards,thisdesigncombinestheTangshanIronandSteel1700mm,Ningsteel1780mm,AnshanIronandSteel1780mmhotrollingworkshopdesignedannualoutputof2.8milliontonsof1780mmconventionalhotrollingworkshop.Designusestwofour-highreversingroughingmill,rollingsixtimes,finishingmillselectedsixnon-reversiblerollingmillsixtimes,throughtheuseofCVCmill,PCmillandthicknesscontrol(AGC)tocontrolpanelsandothertechnology-basedcombinationandthickness,intheno-mandrelbeforefinishingtheheatshieldcoilbox.
Inthedesign,theroughmillsuseonetwo-highun-reversiblemillandonefour-highreversiblestrongmillwithverticalrollcompleting6passrough.ItnotonlysolvestheproblemthatthetimeoftheroughrollingistoolongandtheFinishingmilldoesnotmatchwithroughmill,butalsoensuresstabilityofthemiddlebilletthicknessandthecrown.The6standscontinuousrollingisusedinthefinishingmill,theformerthreestandusinggoodcrowncontroloftheCVCtechnology.Alladoptsmanynewtechnologiestoensurestableproduction.Inquality,precision,andotheraspects,theproductionoccupiedtheadvancedlevel.
Hotrollingplateandstriprollingcontinuouscastingmachine,theproductionof1.5~12.0mmthicknessofthestrip.Slabinthefurnaceheatedto1200℃inabouttworoughslabrollingmillwillbearoundto30mm.Afterroughing,thefirstcut