阶梯轴加工工艺过程设计说明书Word文档格式.doc
《阶梯轴加工工艺过程设计说明书Word文档格式.doc》由会员分享,可在线阅读,更多相关《阶梯轴加工工艺过程设计说明书Word文档格式.doc(22页珍藏版)》请在冰豆网上搜索。
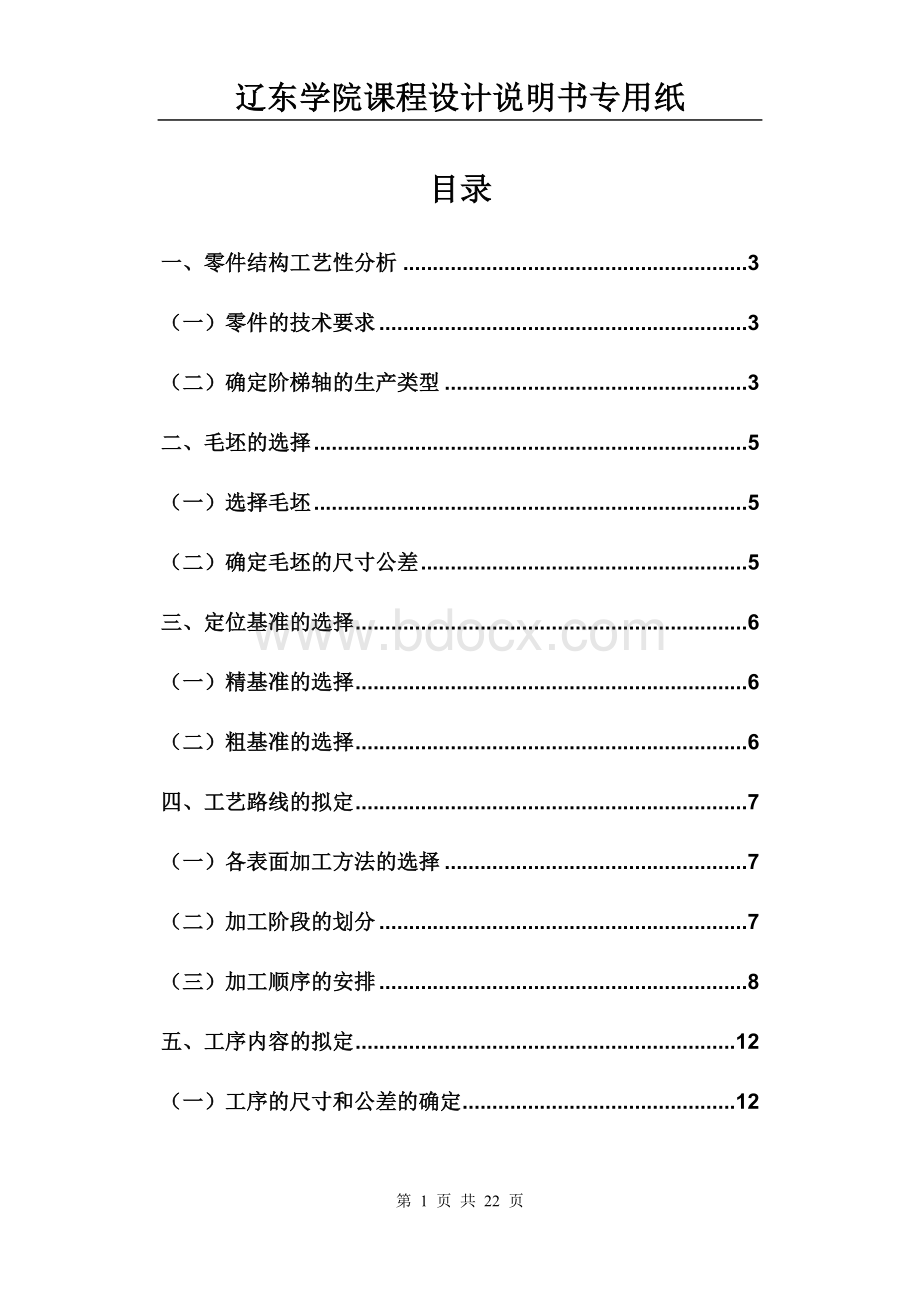
参考文献 21
一、零件结构工艺性分析
(一)零件的技术要求
1、轴类零件,材料为45钢,具有较高的硬度、耐磨性。
2、零件的技术要求表
加工表面
尺寸及偏差/mm
公差/mm及精度等级
表面粗糙度/μm
形位公差/mm
轴左右端面
154±
1
IT10
6.3
阶梯轴外圆表面
φ30h9
IT9
3.2
φ22h9
φ20h9
IT9
3.2
φ17h7
IT7
1.6
φ15h7
IT7
1.6
车
槽
φ14h10
φ15h10
φ18h10
φ20h10
铣
键
φ20
φ15
(二)确定阶梯轴的生产类型
根据设计题目年产量为10万件,因此该阶梯轴的生产类型为大批生产。
二、毛坯的选择
(一)选择毛坯
由于阶梯轴类零件工作时,某些部位如轴颈(主要是与滑动轴承配合的轴颈)往往要承受摩擦、磨损,严重时可能发生咬死(又称抱轴)现象,使轴类零件运转精度下降。
有时还需要承受多种载荷的作用,为增强阶梯轴的强度和冲击韧度,获得纤维组织,毛坯选用锻件。
为增强阶梯轴的强度和冲击韧度,获得纤维组织,毛坯选用锻件。
(二)确定毛坯的尺寸公差
1.公差等级:
由阶梯轴的功能和技术要求,确定该零件的公差等级为普通级。
2.锻件材质系数:
由于该阶梯轴材料为45钢,是碳的质量分数小于0.65%的碳素钢,故该锻件的材质系数为M级。
3.锻件分模线形状:
根据该阶梯轴的形位特点,选择零件方向的对称平面为分模面,属于平直分模线。
4.零件表面粗糙度:
由零件图可知,该阶梯轴的各加工表面粗糙度Ra均大于等于1.6μm。
三、定位基准的选择
(一)精基准的选择
根据该阶梯轴零件的技术要求和装配要求,选择该阶梯轴轴线作为精基准,零件上的很多表面都可以采用它们作基准进行加工,即遵循了“基准统一”的原则。
阶梯轴设计基准是轴线,选用其作精基准定位加工轴的外圆表面,实现了设计基准和工艺基准的重合,保证了被加工表面的垂直度要求。
选用阶梯轴轴线作为精基准,利用双顶尖进行夹持,夹紧稳定可靠。
(二)粗基准的选择
作为粗基准的表面应平整,没有飞边、毛刺或其他表面缺欠,该阶梯轴的外圆表面和左、右端面互为基准作为粗基准,以保证为后序准备好精基准。
四、工艺路线的拟定
(一)各表面加工方法的选择
加工方案
轴左、右端面
粗车-半精车
轴
外
圆
表
面
粗车-半精车
粗车-半精车-磨削
一次行程
6.3
粗铣
(二)加工阶段的划分
该阶梯轴加工质量要求较高,可将加工阶段划分为粗加工、半精加工和精加工几个阶段。
在粗加工阶段,首先将精基准准备好,使后序都可以采用精基准定位加工,保证其他加工表面的精度要求。
(三)加工顺序的安排
1.机械加工工序:
(1)遵循“先基准后其它”原则,首先加工精基准-阶梯轴左、右端面互为基准原则
(2)遵循“先粗后精”原则,先安排粗加工工序,后安排精加工工序。
2.具体方案:
方案一:
1.锻造、调质处理
2.粗车轴两端面162至,打A型中心孔
3.粗车外圆φ37至φ、φ29至φ
φ至φ
4.粗车外圆φ29至φ、φ23至φ
5.半精车φ至φ
φ至、φ至φ
φ至φ倒角
6.半精车φ至
φ至φ、φ至
倒角
7.切槽2*φ15、2*φ20、2*φ18、2*φ14
8.φ、表面淬火
9.磨削φ至φ、至
10.铣键槽17*3.5、25*3.5
11.检验、入库
方案二:
2.粗车轴两端面162至,打A型中心孔
3.粗车外圆φ37至φ、φ29至φ
φ至φ、φ至φ
4.粗车外圆φ29至φ、φ23至φ
5.半精车φ至φ
φ至、φ至φ
φ至
6.半精车φ至、φ至φ
7.铣键槽17*3.5、25*3.5
8.φ、表面淬火
9.磨削φ至φ、至
10.切槽2*φ15、2*φ20、2*φ18、2*φ14
11.检验、入库
方案三:
6.半精车φ至φ至φ
7.切槽2*φ15、2*φ20、2*φ18、2*φ14
8.铣键槽17*3.5、25*3.5
9.φ、表面淬火
10.磨削φ至φ、至
11.检验、入库
论证:
为使加工出一个符合零件的技术要求和装配要求选取一个最为合适的方案作出下列论证:
先加工出零件的基准,可同时加工出阶梯轴其他各部位,且精度能达到零件要求,但铣键槽放在了精加工之前,影响主要表面精加工表面的粗糙度,使零件在使用过程中达不到零件的技术要求。
所以,此方案设计不合理。
为了使零件各个部位达到精度要求,先进行基准加工,然后对工件进行粗加工、精加工,但这样在对零件整体进行加工时,由于零件的结构比较复杂,使加工变得更加复杂化,且浪费时间,而且不能达到要求大京都要求。
因此,此方案设计不合理。
此方案在同时进行粗加工后,进行半精加工,在切槽、铣键槽,最后进行精加工,即满足了设计要求又节省了时间。
因此,此方案为最佳方案。
3.工序的集中与分散:
该阶梯轴的生产类型为大批生产,可以采用万用型机床配以专用工、夹具,以提高生产率;
而且运用工序集中原则使工件的装夹次数少,不但可缩短辅助时间,而且由于在一次装夹中加工了许多表面,有利于保证各加工表面之间的相对位置精度要求。
五、工序内容的拟定
(一)工序的尺寸和公差的确定
加工余量
精度等级
尺寸及精度
阶
梯
粗
2
φ32.60-0.1
φ24.60-0.084
φ22.60-0.084
1.5
φ19.40-0.07
φ17.40-0.07
半
精
1.3
φ300-0.052
φ220-0.052
φ200-0.052
1.0
φ17.40-0.043
φ15.40-0.043
切
φ140-0.11
φ180-0.11
φ200-0.13
φ150-0.11
磨
削
0.2
φ170-0.018
φ150-0.018
铣键槽
φ220-0.043
φ150-0.043
(二)设备及工艺装备的选择
1.设备:
C6140立式铣床
2.工艺装备:
通用、专用车刀、专用铣刀、专用夹具等等。
(三)切削用量的选择及工序时间计算
工序Ⅰ粗车轴两端面
1.加工条件
工件材料:
45号刚,σb=170~240MPa,锻造;
工件尺寸:
aemax=37mm,162mm
加工要求:
粗车轴两端面,加工余量4mm;
机床:
C6140车床
确定粗车端面刀具类型:
YT15硬质合金焊接式车刀;
刀具耐用度T=240min;
刀杆尺寸25mm25mm;
刀片厚度6mm;
γ0=10°
后角α0=6°
,副后角α0’=6°
,刃倾角λs=0°
主偏角Kr=75°
副偏角Kr’=15°
。
2.切削用量
(1)确定切削深度ap
因为余量较小,故选择ap=4.0mm。
(2)确定每次进给量fz
由于本工序为粗加工,尺寸精度和表面质量可不考虑,从而可采用不对称端车,以提高进给量提高加工效率。
根据《切削手册》表3.5,使用YT15硬质合金端车刀加工,机床功率为7.5kw(据《简明手册》表1.27,C6140车床)
f〈0.7mm/min
故选择:
f=0.51mm/min
(3)计算切削速度vc
根据《机械制造工艺与装备》表2-20,查得各修正系数为:
切削速度计算公式为:
将以上数据代入公式:
确定机床主轴转速:
。
最终确定主轴转速为:
400r/min
3.计算基本工时
查《机械加工工序设计》指导书表3.9得,
=4/400=0.04min。
(车实体端面时,=0)
工序Ⅱ粗车阶梯轴外圆
1.选择刀具:
确定粗车外圆刀具类型:
副偏角Kr’=0°
2.确定切削用量
(1)确定背吃刀量
粗车外圆,加工余量为4mm,一次走刀,则单边吃刀量为asp=4/2=2mm。
(2)确定进给量
由《切削用量简明手册》HT200,刀杆尺寸2525,工件直径为32mm,则f=0.4~0.5。
再由《简明手册》表4.2—3查取f=0.45。
(3)选择刀具磨钝标准及耐用度
由《切削用量简明手册》表1.9查取后刀面磨损最大限度为0.8~1