连杆机械加工工艺说明书Word格式文档下载.doc
《连杆机械加工工艺说明书Word格式文档下载.doc》由会员分享,可在线阅读,更多相关《连杆机械加工工艺说明书Word格式文档下载.doc(25页珍藏版)》请在冰豆网上搜索。
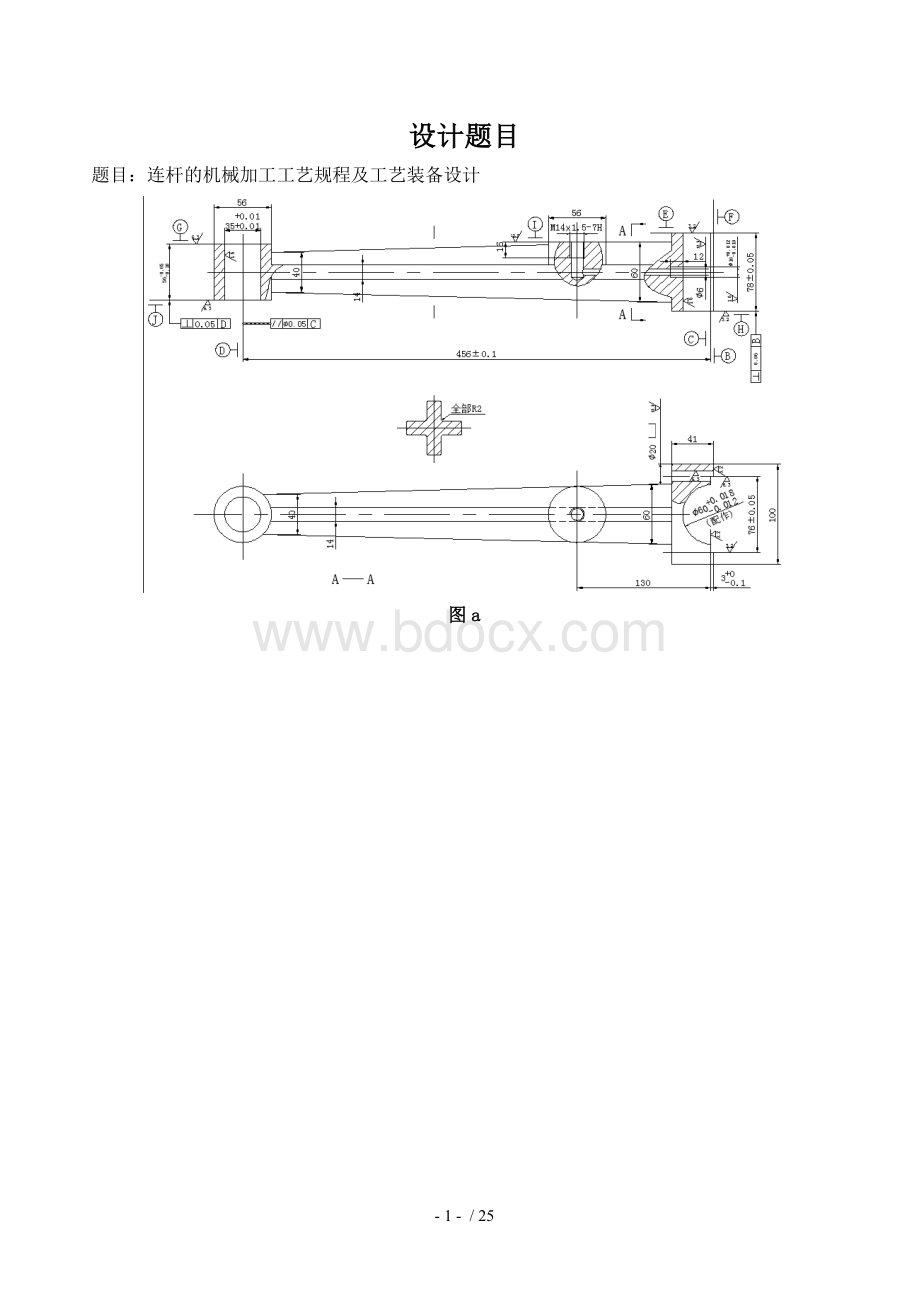
4-ø
10.5的孔虽然尺寸精度为自由公差,要求不高,但是其表面粗糙度为Ra3.2,所以要对其进行精加工;
而ø
6的孔为自由公差,且表面质量为Ra12.5,故只用粗加工就可以了。
1.3凸台的加工
该零件中凸台在ø
60的孔的两侧,表面粗糙度要求为Ra3.2,是故应进行精加工。
1.4螺纹的加工
该零件中油孔的位置有螺纹配合的要求,且孔底与ø
6的孔相通,在加工时应注意螺纹底孔的深度。
综合以上分析,可得出该零件的加工路线为:
粗铣面G、E、I;
粗铣、精铣面J、H、F;
精加工面G、E;
钻ø
35的孔;
加工螺纹M14;
10.5、ø
6的孔。
二、确定毛胚、画毛胚——零件合图
根据零件的材料确定为铸件。
又由题目已给定零件为大批量生产。
毛胚的铸造方法选用砂型机器造型。
为了减少机加工的加工量,ø
60mm、ø
35mm在铸造时就铸造出来,所以还应该安放型芯。
此外,为消除残余应力,铸造后应安排人工时效。
参考文献[1]表2.2—3,该种零件的尺寸公差等级CT为8—10级,加工余量等级MA为G级。
故取CT为10级,MA为G级。
铸件的分型面选择通过ø
6的孔的中心轴线,且平行与面H的平面,浇冒口位置分别位于ø
35的孔的中心。
参考文献[1]表2.2-4,用查表法确定各表面的总余量如表2-1
表2-1各加工表面总余量
加工表面
基本尺寸
(mm)
加工余量等级
加工余量数值
说明
E面
F面
G面
H面
I面
J面
Ø
35
60
41
78
56
H
G
4
3.5
顶面降一级
侧面,单侧加工(取上行数据)
孔降一级,双侧加工
由参考文献[1]表2.3-5,用查表法可得铸件主要的尺寸公差,如表2-2所示。
2表-2主要毛胚尺寸及公差
主要面尺寸
零件尺寸
总余量
毛胚尺寸
公差CT
G—J两面间距
7.5
63.5
2.8
E—H两面间距
85.5
3.2
I面距中心线高度
30
34
2.6
F面尺寸
44.5
27
52
毛胚图如下:
图b
三、工艺规程设计
3.1定位基准的选择
粗基准的选择:
选择H面和J面作为粗基准。
精基准的选择:
选择加工好后的H面和J面作为零件上其他的表面和孔的精基准,能够实现通过一个基准对多个表面进行精加工,也就是实现基准重合。
且对于该类零件来说,若只是单个端面来定位,其定位效果极差,可以等同认为是两个点的定位,是故用两个阶梯面来定位,其定位效果较单个面来说好得多。
且便于夹紧。
3.2制定工艺路线
根据各表面加工要求和各种加工方法能达到的经济精度,确定各表面加工方法如下:
E面、H面、F面:
粗铣——精铣;
G面、J面、I面:
粗铣;
ø
35的孔:
扩——铰;
螺纹G14:
钻孔——攻螺纹;
零件中的ø
35有较高的平行度要求,故它们的加工宜采用工序集中的原则,即分别在一次装夹下将两孔同时加工出来,以保证其加工精度。
根据先面后孔、现主要表面后次要表面和先粗加工后粗加工的原则,将面E、F、G、H、J,孔ø
35mm和ø
10的粗加工放在前面,精加工放在后面,每一阶段中又先加工面F、H,然后加工G、E、J面和钻扩铰孔ø
10mm和ø
35mm。
然后铣凹台面B。
孔4-ø
6面I和其上的螺纹孔M14最后加工。
精加工也是按如此顺序加工。
初步拟定加工工艺路线如下:
序号
工序内容
10
20
40
50
70
80
90
100
110
120
130
140
150
铸造
退火(人工时效)
涂漆
粗铣G面及E面
粗铣H面及J面
粗铣ø
60mm和ø
35mm的孔(ø
60mm的孔与配件配作)
10mm的孔
精铣E面
精铣H面
精铣ø
60mm的孔(ø
粗铣凸台面B面、F面
精铣凸台面B面、F面
粗铣I面
锪平ø
20mm的孔,钻4-ø
10.5mm的孔(配作)
粗铰4-ø
10.5mm的孔
6mm的孔,铣ø
钻M14的底孔,攻M14的螺纹
去毛刺(所有锐角)
检验
入库
上述方案遵循了工艺路线拟定的一般原则,但某些工序有些问题还值得进一步讨论。
如:
在第10道工序中,加工时应该同时粗铣I面,因为I面的要求不高,同时加工能减少反复装夹次数,提高加工效率。
在第70和80道工序中粗铣凸台面B面、F面精铣凸台面B面、F面,为保证配作时故应将凹台B面的加工放在孔ø
60mm之前。
在铣削加工孔ø
60mm,应将粗、精加工放在相连的两道工序中。
修改后的工艺路线如下:
工艺内容
简要说明
涂底漆
粗铣G、I、E面
粗铣H、J面
精铣G、E面,精铣H、J面
粗铣凸台B、F面
精铣凸台B、F面
精铣孔ø
60mm(ø
10.5mm的孔(留有粗铰余量)孔口倒角1×
45˚,粗铰4-ø
消除残余应力
防止生锈
先加工基准面
粗加工面
精加工面
加工接合面,为配作准备
粗加工孔
精加工孔
配作加工孔
钻油孔
加工凹台
加工螺纹
3.3选择加工设备及刀、夹、量具
由于生产类型为大批量生产,所以加工设备宜以通用机床为主,辅以少量的专用机床。
其生产方式为以通用机床家专用夹具为主,辅以少量专用机床的流水生产线。
工件在各机床上的装卸及各机床之间的传送均由人工完成。
粗铣G、I、E面和粗铣H、J、F面。
考虑到工件的定位夹紧方案及夹具设计的问题,都采用立铣。
选择X52K立式铣床。
选择直径为80mm的材料为YG6硬质合金可转位锥柄面铣刀(如下表4-41所示)、专用夹具和游标卡尺。
精铣E面和粗铣H面。
加工设备仍选用X52K型立式铣床。
刀具选用同上的直径为80mm的可转位锥柄面铣刀,专用夹具和游标卡尺。
粗铣ø
35mm的孔。
由于铣孔是属于曲线插补加工,所以要求用数控铣床。
故对孔ø
35mm的加工设备选用型号为XK6330的数控铣床。
刀具选用直径为25mm和16mm的材料为硬质合金中齿莫氏锥柄立铣刀,专用夹具、游标卡尺。
加工设备还是XK6330型号的数控铣床。
刀具选用直径为16mm和20mm的材料为硬质合金细齿莫氏锥炳立铣刀。
专用夹具,量具选用塞规。
锪平ø
10.5mm的孔(留有粗铰余量),孔口倒角1×
45˚。
10.5mm的孔。
选用型号为Z3025的摇臂钻床。
锪平ø
20mm的孔选用锪钻。
10.5mm的孔选用直径为10的钻头和直径为10.5mm的铰刀。
钻ø
10mm的孔。
选用专用的机床。
刀具选用直径为ø
6mm的加长型钻头和直径为10mm的材料为硬质合金立铣刀。
专用夹具。
粗铣凸台B、F面。
机床选用卧式铣床,型号为X6030。
12mm中齿的材料为硬质合金立铣刀。
精铣凸台B、F面。
机床还是选用卧式铣床,型号为X6030。
10mm的材料为硬质合金细齿立铣刀。
钻M14的底孔,攻M14的螺纹。
参考文献[1]中表3.1-6、3.1-48。
加工M14的螺纹底孔选用直径为12.5mm的锥柄麻花钻。
攻螺纹时选用代号为M14×
1.5的机用丝锥。
专用夹具、机用丝锥夹头、螺纹塞规。
3.4加工工序设计
1.工序10粗铣G、I、E及工序30精铣E、G面工序。
查文献[1]表2.3-21平面加工余量,为1mm。
已知E面总余量为4mm。
故粗加工余量为3mm。
查文献[2]表2.6-6,得粗铣的加工公差等级为IT9—IT11级,取IT=10,E面公差为0.12mm,G面公差为0.12mm。
所以=82.5±
0.06,=60.5±
0.06mm。
校核E面精铣余量:
=(82.5-0.06)-(81.5+0.05)
=0.89mm
=(60.5-0.06)-(59.5-0.05)
=0.89mm
故余量足够。
切削参数的选择:
查表3-16取粗铣每齿进给量为0.13mm/z;
取精铣每转进给量为=0.5mm/r。
粗铣走刀一次,=3mm;
精铣走刀一次,=1mm。
表3-16,取粗铣主轴转速为380r/min;
取精铣主轴转速为700r/min。
2.工序20粗铣H、J面和工序40精铣H、J面。
查文献[1]表2.