焦油加工实用实用工艺.docx
《焦油加工实用实用工艺.docx》由会员分享,可在线阅读,更多相关《焦油加工实用实用工艺.docx(13页珍藏版)》请在冰豆网上搜索。
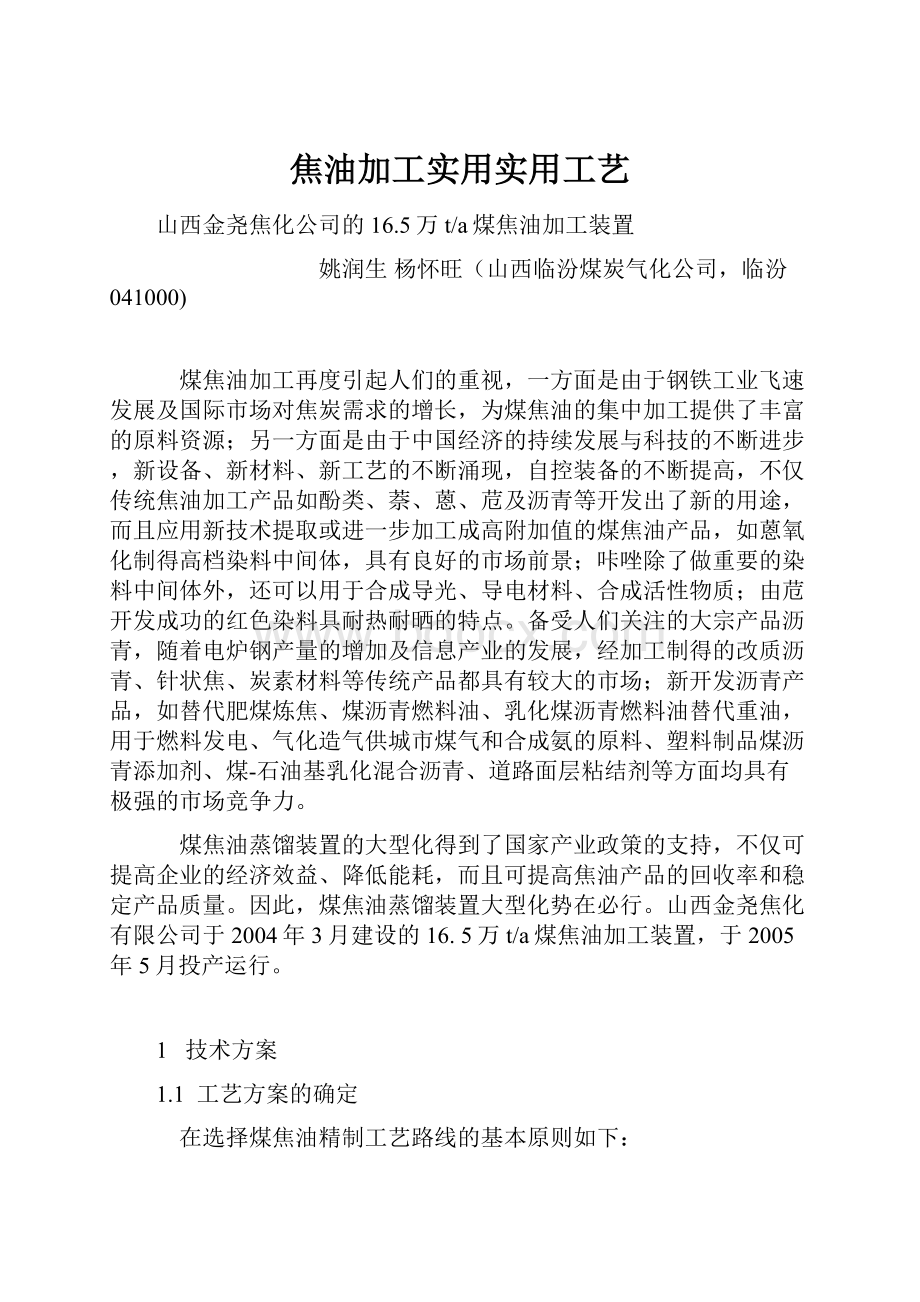
焦油加工实用实用工艺
山西金尧焦化公司的16.5万t/a煤焦油加工装置
姚润生杨怀旺(山西临汾煤炭气化公司,临汾041000)
煤焦油加工再度引起人们的重视,一方面是由于钢铁工业飞速发展及国际市场对焦炭需求的增长,为煤焦油的集中加工提供了丰富的原料资源;另一方面是由于中国经济的持续发展与科技的不断进步,新设备、新材料、新工艺的不断涌现,自控装备的不断提高,不仅传统焦油加工产品如酚类、萘、蒽、苊及沥青等开发出了新的用途,而且应用新技术提取或进一步加工成高附加值的煤焦油产品,如蒽氧化制得高档染料中间体,具有良好的市场前景;咔唑除了做重要的染料中间体外,还可以用于合成导光、导电材料、合成活性物质;由苊开发成功的红色染料具耐热耐晒的特点。
备受人们关注的大宗产品沥青,随着电炉钢产量的增加及信息产业的发展,经加工制得的改质沥青、针状焦、炭素材料等传统产品都具有较大的市场;新开发沥青产品,如替代肥煤炼焦、煤沥青燃料油、乳化煤沥青燃料油替代重油,用于燃料发电、气化造气供城市煤气和合成氨的原料、塑料制品煤沥青添加剂、煤-石油基乳化混合沥青、道路面层粘结剂等方面均具有极强的市场竞争力。
煤焦油蒸馏装置的大型化得到了国家产业政策的支持,不仅可提高企业的经济效益、降低能耗,而且可提高焦油产品的回收率和稳定产品质量。
因此,煤焦油蒸馏装置大型化势在必行。
山西金尧焦化有限公司于2004年3月建设的16.5万t/a煤焦油加工装置,于2005年5月投产运行。
1 技术方案
1.1 工艺方案的确定
在选择煤焦油精制工艺路线的基本原则如下:
(1)在保证产品质量、产量和提高产品附加值的前提下,尽量采用先进的工艺设备与材料。
通过提高自动化水平和精馏设备的技术进步,确保生产操作的稳定性和灵活性;
(2)采用先进有效的环保措施,减少环境污染,满足环境标准的要求;
(3)充分利用工艺余热,以减少工艺能耗,尽可能做到节能降耗。
遵循上述基本原则,16.5万t/a煤焦油加工装置选择了沥青循环的单炉单塔切取三混馏分的焦油蒸馏工艺。
洗涤采用碱洗脱酚流程,酚盐采用间歇硫酸分解工艺,工业萘采用双炉双塔制取95%工业萘及含萘低于3%的低萘洗油工艺,I蒽油采用机械化结晶机间接冷却制取粗蒽技术。
1.2 工艺流程
(1)焦油蒸馏的工艺流程。
焦油蒸馏为沥青循环一塔式切取三混馏分流程,其工艺流程示意图见图1。
图1 焦油蒸馏的工艺流程示意图
1-碱液高位槽;2-焦油大槽;3-原料焦油泵;4-管式炉;5-II蒽油槽;6-II蒽油冷却器;7-沥青冷却器;8-一次轻油冷却器;9-油水分离器;10-无水焦油泵;11-一段、二段蒸发器;12-I蒽油回流泵;13-I蒽油槽;14-II蒽油换热器;15-I蒽油换热器;16-I蒽油冷却器;17-I蒽油抽出泵;18-焦油蒸汽换热器;19-精馏塔;20-轻油冷却器;21-油水分离器;22-轻油回流泵;23-轻油接收槽;24-三混馏分冷却器;25-三混馏分槽;26-轻油槽。
如图1所示,原料焦油在油库被加热脱水、并与蒽油换热后送入一段蒸发器进行再脱水,塔顶逸出轻油与水,脱水后的无水焦油用泵送入煤气管式炉,在此加热到330~400℃后进入二段蒸发器闪蒸,沥青自二段蒸发器底部自流到沥青冷却装置,生产低、中、高温沥青及配制油等。
侧线切取II蒽油,塔顶的馏分蒸汽进入馏分塔,馏分塔底的I蒽油送入结晶工段生产粗蒽,侧线切取酚、萘、洗油三混馏分,塔顶逸出的轻油送粗苯原料槽。
(2)馏分洗涤及工业萘蒸馏。
含酚5%~7%的三混馏分进行二段间歇洗涤,其工艺流程示意图见图2。
图2 三混馏分的洗涤分解工艺流程图
1-引风机;2-洗净循环槽;3-排气洗净塔;4-碱性酚钠高位槽;5-稀碱高位槽;6-洗涤器;7-碱性酚钠槽;8-中性酚钠槽;9-蒸吹塔;10-换热器;11-蒸吹冷却器;12-净酚钠冷却器;13-分离器;14-油收集槽;15-净酚钠槽;16-硫酸高位槽;17-分解器;18-硫酸钠槽;19-粗酚槽。
如图2所示,一段用碱性酚盐洗涤脱酚得中性酚盐,二段用稀碱液洗涤脱酚得碱性酚盐,中性酚盐在蒸吹釜中蒸吹得净酚盐,然后用稀硫酸分解得粗酚。
工业萘蒸馏采用双炉双塔流程,其工艺流程示意图见图3。
图3 工业萘蒸馏工艺流程图
1-酚油冷凝器;2-油水分离器;3-酚油回流槽;4-酚油槽;5-酚油回流泵;6-初馏塔;7-初馏炉;8-初馏塔热油循环泵;9-精馏塔;10-精馏炉;11-精馏塔热油循环泵;12-洗油冷却器;13-洗油槽;
14-工业萘回流泵;15-原料预热器;16-工业萘汽化冷凝冷却器;17-工业萘回流槽;18-工业萘槽;19-原料泵;20-原料槽;21-工业萘结晶机。
如图3所示,脱酚后的已洗三混馏分,由原料泵将其送往换热器与工业萘油换热后送入初馏塔,塔顶采出脱酚酚油,塔底采出低萘洗油,用热油循环泵一部分送初馏管式炉,加热到260~270℃后再返回塔内供热;另一部分送精馏塔作为原料,塔顶馏出萘油,经冷却结晶生产工业萘。
塔底为含萘<3%的低萘洗油。
2 焦油蒸馏工程主、辅装置的构成
焦油蒸馏工程由焦油蒸馏、洗涤分解、工业萘、沥青成型、粗蒽和油库等6套主生产装置构成。
辅助装置由60t/h反渗透和钠离子型水处理系统、3台25t/h燃料为劣质煤的流化床锅炉和两个变配电所组成。
3 焦油蒸馏装置的特点
该工艺属于国内常见的常压蒸馏-三混馏分切取流程,但与国内其他焦油加工装置的不同的是在新材料、新设备、节能环保、自控水平方面有质的突破。
3.1 工艺特点
切取三混馏分的焦油蒸馏工艺能最大限度地提高高附加值产品(萘、洗油、粗酚)的集中度,提高粗酚、工业萘、洗油的产量与质量。
使洗涤分解工艺和工业萘蒸馏工艺的流程变短,无需重复加热冷却,系统运行稳定可靠,节约能耗。
整体投入与产出经济比合理,可灵活生产低温沥青、中温沥青及燃料油,较好地解决了沥青产品品种少和销售难的问题,增强了市场竞争力,使工艺技术与市场相结合,确保了生产的稳定运行。
3.2 先进的自控水平
本工程采用PLC集散控制技术,可对油库、焦油蒸馏、洗涤分解、工业萘蒸馏等生产装置进行监控,便于数据的采集、显示、调节、报警、联锁和记录等,实现了现场运转设备在集控室内的远程控制和操作。
自控水平的提高可精确控制各段的温度,确保了产品的质量和数量。
变频调速装置在电机自控系统的应用,取消了节流阀的调节,既节省了系统能耗,又控制了系统的灵活性和稳定性,实现了生产系统的柔性调节,节能降耗与控制系统的配合,以实现装置的多样化生产。
3.3 新材料及精馏设备的采用
馏分塔、工业萘初馏塔和精馏塔是煤焦油加工装置的核心设备,连续、安全、稳定运行是保证焦油蒸馏系统正常运行的关键。
国内常规焦油蒸馏装置多为泡罩塔和浮阀塔,一般为40~60块塔盘。
此工程设计采用了新型浮阀塔盘,浮阀材质全部选用316L,彻底解决了馏分对塔盘浮阀的腐蚀,不仅能够提高分离效果,而且能确保设备的长期稳定运行,16.5万t/a焦油蒸馏装置的馏分塔的塔径仅为2m。
实际运行表明,该装置的焦油处理量可高达23~25万t/a。
3.4 直接生产低萘洗油
国内焦油加工工艺所产洗油的含萘量通常在7%~10%,有的甚至在15%以上,含萘量高的洗油洗苯效果差、消耗大,另外,工业萘收率也低,经济效益差。
该工艺采用高效分离塔板,辅以计算机模拟控制,塔顶可产出结晶点>77.8℃的优质工业萘,塔底产出含萘量<3%的优质低萘洗油,同时,也提高了萘的收率及质量。
由于精馏效率高,洗油及蒽油中的含萘量较低,萘的回收率可提高10%~15%。
4 生产指标
4.1 各项能耗指标的比较
将我公司的16.5万t/a的新建焦油蒸馏装置与山西宏特焦化有限公司的15万t/a和山西焦化有限公司从国外引进的30万t/a焦油蒸馏装置进行能耗比较(水、电、蒸汽和煤气),其结果见表1。
表1 三套焦油蒸馏装置的能耗比较
装置规模
焦油处理量
t/h
新水
m3/h
循环水m3/h
电
kW/h
蒸汽
t/h
煤气
m3/h
自产蒸汽
t/h
30万t/a
36~38
20
-
500
2.0
3000
-
15万t/a
18
115
-
150
3.0
1400
-
16.5万t/a
20~30
20~30
300~400
110
2.5~3.0
1500~1600
1.0~1.5
从表1可看出,因新建16.5万t/a装置的换热和沥青冷却均采用了废热锅炉,综合能耗大为降低。
由于液体输送采用了变频调速装置,使电耗也极大为降低。
4.2 产品收率与质量
煤焦油蒸馏装置为系统工程,不应该将焦油馏分、洗涤分解、工业萘蒸馏看做各自独立的系统,而应该将三者有机地统一起来,以提高高附加值产品的集中度,切取三混馏分能极大地提高粗酚和萘的集中度,从而也提高了其他馏分的质量。
产品收率及质量的对比结果见表2。
表2 不同焦油蒸馏工艺的产品收率与质量
馏分
30万t/a
15万t/a
16.5万t/a
馏分
产率
%
关键组
分含量
%
馏分
产率
%
关键组
分含量
%
馏分
产率
%
工业萘分离
轻油
0.3~0.5
酚<0.2
0.3~0.5
酚<0.2
0.3~0.5
-
酚油
2~3
-
2~3
-
三混馏分
酚油2~3
萘油
10.5
萘80~90
9.0
萘70~80
17.0~20.0
工业萘产率9.5%~10.0%,萘集中度95%~98%
洗油
7~8
萘<2
7~8
萘<10
-
含萘≤3%
I蒽油
8.5
蒽10
15.0~16.0
蒽4~7
20.0~25.0
-
II蒽油
12
-
8~10
-
2~5
-
沥青
58
软化点90℃
Na+<10×10-6
55
软化点80℃
53~55
软化点45~105℃
从表2可看出,采用沥青循环切取三混组分的16.5万t/a焦油蒸馏工艺较其他工艺具有如下优势。
(1)切取三混馏分可最大限度地提高萘的集中度和收率,使洗涤分解、工业萘蒸馏流程更加简捷。
(2)洗油的产品质量高于国内旧工艺的产品质量。
(3) I蒽油的收率可大幅度提高,沥青量可适度减少。
(4)沥青产品采用柔性化生产工艺,可生产低温沥青、中温沥青、高温沥青及油品混合生产燃料油,品种多,提高了产品的附加值
1、间歇式焦油蒸馏
间歇式焦油蒸馏的生产工艺流程,如图3--1所示。
焦油间歇蒸馏有常压蒸馏和减压蒸馏两种流程,为装料、加热、分馏和排放沥青等操作依次周期性进行的蒸馏过程。
脱水焦油装入蒸馏釜,缓慢加热升温,依次从蒸馏柱顶切取各种馏分油,釜底残渣为沥青。
间歇蒸馏由于物料保温时间长,生产的中温沥青比连续蒸馏的中温沥青具有较高的β--树脂,沥青产率也高,可达60%。
间歇蒸馏结束后,可对蒸馏釜残渣(中温沥青)继续进行加热处理,直接得到软化点100--115℃的改质沥青。
间歇焦油蒸馏设备比较简单,投资少。
由于间歇焦油蒸馏存在各馏分质量不易控制,酚和萘的提取率低;能耗高;劳动条件差,难以采用自动控制及自动调节装置等缺点,已很少采用。
2、 连续式焦油蒸馏
2.1 一次汽化过程及一次汽化温度
2.1.1 焦油在管式炉中的一次汽化过程
在工业生产上液体混合物的蒸发(指部分汽化),原则上可以用2种不同的方法来实现:
一种是微分蒸馏方法,即将产生的蒸气随时从被蒸馏的物料分离出来;另一种是不将所产生的蒸气随时引出,而使其与液体密切接触,直到达到指定的温度时,才将蒸气一次引出(此时气、液两相达到平衡),即一次汽化(或平衡蒸馏)的方法。
煤焦油连续蒸馏的加热过程是在管式炉中实现的,煤焦油的蒸发就是以一次汽化(或称为一次蒸发)的方法来完成的。
脱水焦油采用泵压送到管式炉炉管内,迅速把焦油加热到指定温度,在整个加热过程中所形成的馏分蒸气,一直与液体密切接触,相互达到平衡。
当气、液混合物从管式炉进入二段蒸发器后,由于压力急剧降低,馏分蒸气立即一次汽化,并与残液分离,完成一次汽化过程。
2.1.2 一次汽化温度
管式炉连续蒸馏过程要求二蒽油以前的全部馏分都在二段蒸发器内一次蒸发出来。
欲使各馏分产率及沥青质量都符合工艺要求,就须合理确定一次蒸发温度。
一次蒸发温度是指焦油气、液两相混合物进入二段蒸发器闪蒸后气、液两相达到平衡的温度。
由于换热损失和闪蒸需要的汽化潜热,焦油气、液混合物进入二段蒸发器闪蒸后,温度要降低一些,故一次蒸发温度低于管式炉二段出口焦油温度,而略高于二段蒸发器的沥青排出温度。
最适宜的一次蒸发温度应保证从焦油中蒸出的酚和萘最多,并得到软化点满足要求的沥青。
显然,当焦油的组成不同或对沥青的软化点要求不同时,最适宜的一次蒸发器温度也不同。
焦油的一次蒸发温度与馏出物的产率、二段蒸发器压力、二段蒸发器内过热蒸汽用量等因素有关。
2.2 一次汽化所有馏分的焦油蒸馏流程
这是国内最常采用的一种焦油蒸馏工艺,将脱水焦油在管式炉里加热至380~400℃后进入二段蒸发器。
高温焦油在二段蒸发器内进行一次汽化,中温沥青与所有馏分分离。
馏分油气自二段蒸发器顶部进入下一个塔进行蒸馏,由二段蒸发器底部排除沥青。
根据生产规模和技术装置水平情况,按着一次汽化所有馏分,然后逐渐冷凝馏分的原则建立焦油蒸馏流程,依精馏塔台数不同,分为一塔式、二塔式和多塔式流程;依据操作压力不同,分为常压、常减压和减压蒸馏流程;依据馏分的切取数量不同,分为切取窄馏分和切取混合分流程。
2.2.1 二塔式和一塔式焦油蒸馏流程
以上两种工艺为切取窄馏分工艺。
两塔式焦油蒸馏工艺中,在馏分塔将萘油馏分和洗油馏分合并在一起切取称作二混馏分,此时塔底油苊含量大于25%,称作苊馏分;一塔式焦油蒸馏工艺中,馏分塔可以开一个侧线,将酚油馏分、萘油馏分和洗油馏分合并在一起切取称作三混馏分。
这两种切取馏分的方法,可使萘集中度提高,从而提高了工业萘产率。
这种工艺沥青在二次蒸发器内停留时间比较短,一般约在15~17min排出系统,沥青保温时间短,中温沥青甲苯不溶物(TI)增长幅度不大,很难达到优质电极沥青的质量要求。
我国较普通采用二塔式和一塔式焦油蒸馏流程,生产规模小的装置切取混合分(三混馏分或二混馏分),生产规模大的装置一般切取窄馏分。
根据对产品种类和质量要求的不同,焦油蒸馏的工艺路线也有所不同。
2.2.2 多塔式焦油蒸馏流程
无水焦油经管式炉加热后进入蒸发器。
在蒸发器汽化的所有馏分气依次进入4个精馏塔,各塔均采用热回流(后一个塔底油不经冷却作为前一个塔塔顶回流)。
得到的馏分馏程为:
酚油馏分175~210℃,萘油馏分209~230℃,洗油馏分220~300℃,蒽油馏分240~350℃。
3.3.2.3 减压焦油蒸馏流程
减压焦油蒸馏流程的显著特点是节能。
减压操作可以降低蒸馏温度。
采用换热流程,回收余热对原料焦油进行脱水,脱水后焦油在管式炉加热后进入主塔。
从主塔侧线切取萘油、洗油和蒽油;主塔顶部得到酚油;主塔底部为软沥青产品。
在蒸汽发生器内,利用洗油和蒽油的热量产生0.3MPa蒸气,供装置加热用。
根据一次汽化所有馏分,然后逐渐冷却分离馏分的原则建立的焦油连续蒸馏流程在我国和东欧各国应用普遍。
这种类型流程的优点是工艺过程简单、便于操作等。
但同时也存在以下不足:
(1)由于精馏所需的热量是由焦油在管式炉被加热一次供给的,所以精馏条件受到严格限制,几乎不可能用改变塔板回流量的方法调节馏分组成。
(2)轻油、酚油、萘油和洗油组分毫无意义地通过蒽塔,轻组分经过所有塔板后分离出来,由于在塔板上的气、液相平衡,不可避免地导致所切取的馏分中含有轻组分。
如萘,在蒽油中有一定数量的萘,而萘油馏分本身又被酚油和轻油组分所污染。
(3)所有馏分通过二次蒸发器和蒽塔,致使设备负荷增大,效率降低。
(4)常压焦油蒸馏为了降低一次汽化温度,在蒸发器和精馏塔内通入占焦油量0.5%的过热蒸汽,不但降低了设备的生产能力,而且还恶化馏分蒸馏的精确性,废水量增加。
(5)加热制度不合理,能耗高。
减压焦油蒸馏降低了焦油在管式炉的加热温度和一次汽化温度,可防止焦油组分加氢、分解和聚合,焦油组分稳定,馏分产率提高3%~5%。
另外,还能提高各组分的相对挥发度,可向系统中不通或少通直接蒸汽,这不仅使分离效率有所提高,能耗和废水量也有所降低。
2.3 逐渐加热焦油的连续蒸馏
根据逐渐加热焦油,使组分蒸发而分离的原则建立的焦油蒸馏流程,逐塔对焦油由轻至重分离出各馏分。
根据切取产品数量不同,蒸馏塔数量也不同,采用这种工艺的主要有吕特格式焦油连续蒸馏和考伯斯式焦油连续蒸馏。
现介绍吕特格式典型逐塔加热焦油蒸馏流程,见图3--4。
其特点是:
热能利用合理,馏分分馏精细,沥青在较高温度下保温时间较长,能生产具有较高β--树脂的沥青。
轻组分在沸点温度下首先被分离出来,不受高温作用,所得到的轻质馏分质量好。
如,经过高温作用的酚油馏分脱酚后生产古马隆树脂时,质量明显下降。
2.4 带有沥青循环的焦油蒸馏流程
带有沥青循环的焦油蒸馏工艺在美国、法国和英国都有装置在运行。
带有沥青循环的焦油蒸馏装置具有一个共同的特点:
较高温度的循环沥青直接与焦油混合,来完成焦油的加热或脱水。
同时这种流程广泛利用二次能源,能耗低,沥青和各馏分质量得到改善。
2.5 煤焦油改质处理生产优质沥青
煤焦油改质处理方法目的是简化工艺,降低操作费用,获得物化性质不同的多用途沥青。
典型的方法是切里--特(Cherry--T)法。
原料焦油在脱水塔脱水后,再进入低压脱水塔,脱除残余水和轻油,而后经管式炉加热至400~420℃后进入反应器。
反应器设有搅拌装置,焦油在0.9MPa压力及约400~410℃条件下保温5h,使不稳定组分发生缩合聚合,然后进入闪蒸塔闪蒸,直接得到优质的F沥青。
焦油在反应器内经过较长时间的热作用后,结果增加了沥青产率和馏分的稳定性。
闪蒸塔内的馏分油气经该塔顶部的精馏段分成闪蒸油和重油。
闪蒸油直接冷凝冷却后,作为产品。
也可直接引入二段反应器(图3-5中未表示),二段反应器温度为450℃,物料停留时间为10h。
由二次反应器排出来的沥青为S沥青。
这种方法生产的两种沥青性质对比见表3--1。
表3--1 沥青的性质对比
沥青名称 软化点/℃ QI/% BI/% 产率/%
F沥青 80~100 8~14 31~38 60
S沥青 70~90 0~2 23~31 45
该流程的特点是煤焦油直接加热处理,油分和沥青产生热分解和热聚合反应,沥青收率高,而且进行了沥青的改质。
改质后的沥青性能得到很好的改善。
特别是β树脂含量高,F沥青适用于作为石墨电极和铝用炭素制品的黏结剂,特别是S沥青几乎不含喹啉不溶物,是优质的浸渍剂沥青,也可作为针状焦和碳纤维的原料