顺丁橡胶合成工艺设计.docx
《顺丁橡胶合成工艺设计.docx》由会员分享,可在线阅读,更多相关《顺丁橡胶合成工艺设计.docx(12页珍藏版)》请在冰豆网上搜索。
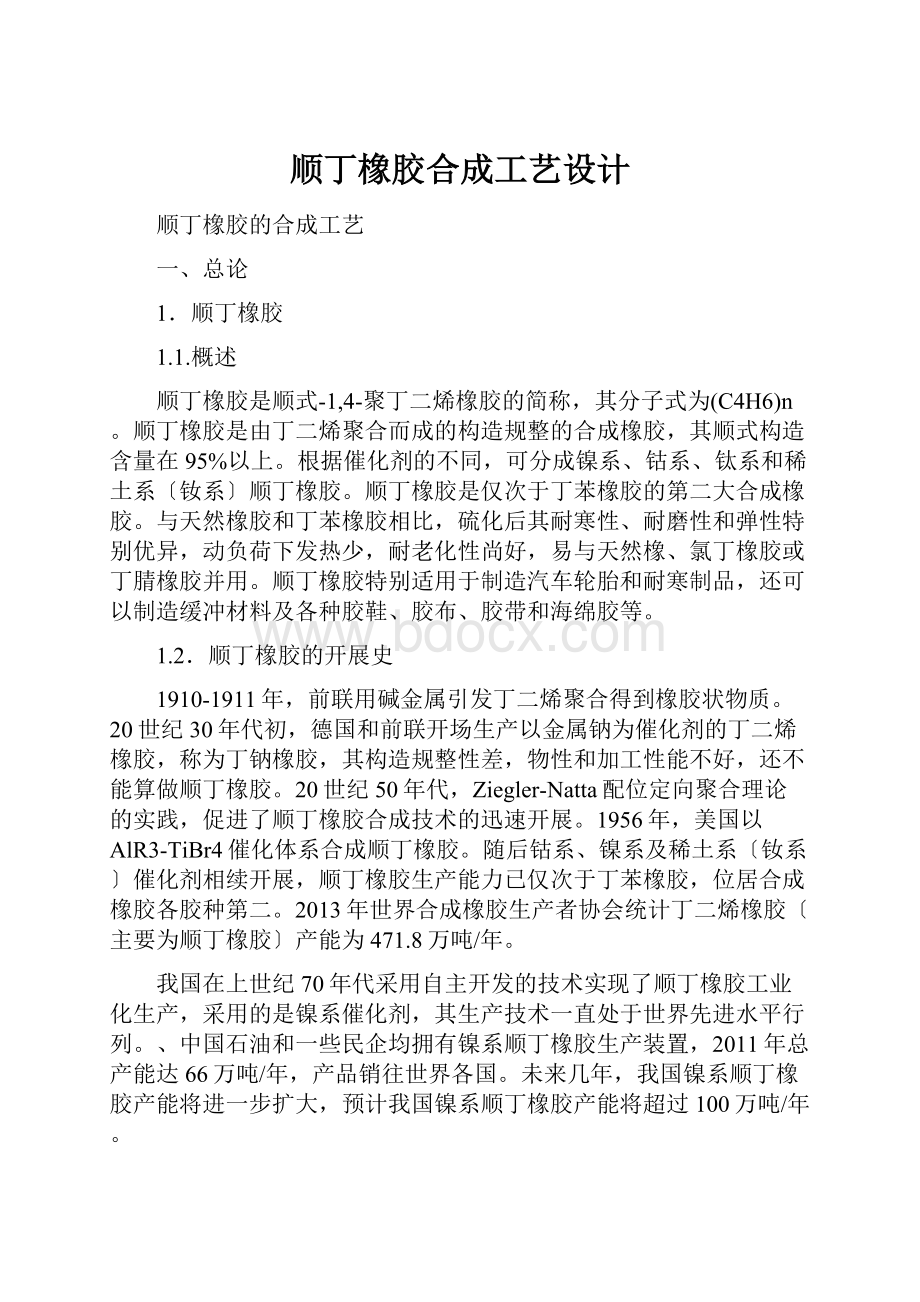
顺丁橡胶合成工艺设计
顺丁橡胶的合成工艺
一、总论
1.顺丁橡胶
1.1.概述
顺丁橡胶是顺式-1,4-聚丁二烯橡胶的简称,其分子式为(C4H6)n。
顺丁橡胶是由丁二烯聚合而成的构造规整的合成橡胶,其顺式构造含量在95%以上。
根据催化剂的不同,可分成镍系、钴系、钛系和稀土系〔钕系〕顺丁橡胶。
顺丁橡胶是仅次于丁苯橡胶的第二大合成橡胶。
与天然橡胶和丁苯橡胶相比,硫化后其耐寒性、耐磨性和弹性特别优异,动负荷下发热少,耐老化性尚好,易与天然橡、氯丁橡胶或丁腈橡胶并用。
顺丁橡胶特别适用于制造汽车轮胎和耐寒制品,还可以制造缓冲材料及各种胶鞋、胶布、胶带和海绵胶等。
1.2.顺丁橡胶的开展史
1910-1911年,前联用碱金属引发丁二烯聚合得到橡胶状物质。
20世纪30年代初,德国和前联开场生产以金属钠为催化剂的丁二烯橡胶,称为丁钠橡胶,其构造规整性差,物性和加工性能不好,还不能算做顺丁橡胶。
20世纪50年代,Ziegler-Natta配位定向聚合理论的实践,促进了顺丁橡胶合成技术的迅速开展。
1956年,美国以AlR3-TiBr4催化体系合成顺丁橡胶。
随后钴系、镍系及稀土系〔钕系〕催化剂相续开展,顺丁橡胶生产能力已仅次于丁苯橡胶,位居合成橡胶各胶种第二。
2013年世界合成橡胶生产者协会统计丁二烯橡胶〔主要为顺丁橡胶〕产能为471.8万吨/年。
我国在上世纪70年代采用自主开发的技术实现了顺丁橡胶工业化生产,采用的是镍系催化剂,其生产技术一直处于世界先进水平行列。
、中国石油和一些民企均拥有镍系顺丁橡胶生产装置,2011年总产能达66万吨/年,产品销往世界各国。
未来几年,我国镍系顺丁橡胶产能将进一步扩大,预计我国镍系顺丁橡胶产能将超过100万吨/年。
稀土顺丁橡胶因其优异的性能被视为镍系顺丁橡胶的升级品种,逐渐被工业界所重视。
稀土顺丁橡胶与镍系顺丁橡胶相比具有较高的弹性、较好的拉伸性能、较低的生热和滚动阻力以及优异的耐磨耗和抗疲劳等物理机械性能,符合高性能轮胎在高速、节能、平安、环保等方面开展的需要,常用于高性能绿色轮胎。
中国早在上世纪60年代就开场了稀土催化丁二烯聚合的研究,由于当时经济开展落后,未能实现工业化生产。
1998年在国家863方案的支持下,中国石油石化公司在镍系万吨级顺丁橡胶生产装置上成功地生产出了稀土顺丁橡胶。
2011年,中国石油独山子石化公司稀土顺丁橡胶生产装置投产,中国稀土顺丁橡胶生产装置实现了零突破。
2012年,燕山分公司3万吨/年稀土顺丁橡胶生产装置也投产。
未来几年,我国将新增20多万吨/年稀土顺丁橡胶的产能,届时中国稀土顺丁橡胶总产能达30万吨/年以上,成为稀土顺丁橡胶第一大生产大国。
2.溶液聚合
2.1.概述
将聚合单体溶解于溶剂中,然后在催化剂的催化下进展的聚合反响。
在溶液聚合中溶剂起到传热介质的作用。
溶液聚合分为均相和非均相聚合两种情况。
2.2.聚合方式
溶液聚合可以采用自由基、阴离子和配位阴离子等方式进展引发反响。
2.3.溶液聚合的根本配方
溶液聚合的根本配方为:
单体+溶剂+催化剂
二、顺丁橡胶的生产工艺
1.概述
丁二烯在配位络合催化剂存在下,其反响为:
丁二烯分子含有共轭双键,按照聚合条件不同,所得大分子的立体构造有顺式-1,4聚丁二烯、反式-1,4聚丁二烯和1,2-聚丁二烯三种产品。
其中,顺式-1,4聚丁二烯具有弹性高、耐低温性能好、耐磨性佳和耐老化等很多的优异性能,因此成为聚丁二烯的主要产品。
其分子构造式如下:
工业品的顺丁橡胶含有96-98%的顺式-1,4聚丁二烯,采用配位溶液聚合法生产。
2.主要生产原辅材料
顺丁橡胶生产的主要生产原辅材料为五大类:
单体;溶剂;引发剂;终止剂;防老剂。
1〕单体
采用纯度≥99%的工业品丁二烯,其具体质量规格可以通过查询相关
化工产品手册得到。
2〕溶剂
各种溶剂对反响原料、产物及反响所用各种引发剂的溶解能力不同。
从溶解度参数、体系粘度、工程上传热与搅拌、生产能力提高、回收难易、毒性大小、来源、输送等几个方面对苯、甲苯、甲苯-庚烷、溶剂油等,进展综合比拟,确定选择溶剂油。
3〕催化剂
A催化剂体系的选择原那么
定向能力高:
顺式-1,4聚丁二烯含量在97%以上。
稳定:
在贮藏和聚合过程中很少变化。
活性高:
少量使用就可获得较高的聚合速率和较多的聚合物。
易别离:
聚合后,催化剂易从聚合物中别离出来,且残留的催化剂对聚合物的性能无不良影响。
B催化剂体系的比拟
丁二烯聚合采用的引发剂主要有Li系、Ti系、Co系、Ni系等很多种类
型,它们的典型组成如下:
a〕Li系:
丁基锂
b〕Ti系:
三烷基铝-四碘化钛-碘-氯化钛
c〕Co系:
一氯二烷基钼-二氯化钴
d〕Ni系:
环烷酸镍-三异丁基铝-三氟化硼乙醚络合物
目前,国工业上采用的是Ni系催化剂体系,本次课程设计也采用该催化剂体系。
Ni系催化剂体系有如下特点:
催化剂活性高;
顺式含量在97%以上;
产品质量均匀,产物的综合物理机械性能较好,分子量较易控制,易
于加工,冷流倾向小,便于连续生产;
改变条件〔温度,单体浓度〕对聚合物的性能无影响。
CNi催化剂体系的组成
根本组成:
环烷酸镍-三异丁基铝-三氟化硼乙醚络合物
a)环烷酸镍〔主引发剂〕
其中n=12-14,绿色膏状液体,易溶于苯和加氢汽油,使用时先用溶
剂稀释后再用。
其组成为:
镍含量:
>7-8%;水份:
<0.1%;不皂化物:
无
b〕三异丁基铝〔助引发剂,Al(i-C4H9)3M=129〕M=198
无色或微黄色透明液体,化学性质极为活波,使用时稀释到平安浓度以下〔<20g/L-溶剂〕。
生产、使用及贮存都必须与空气及水分隔绝用氮气保护。
其组成为:
活性铝含量:
≥50%;外观浅黄透明;无悬浮物
c〕氟化硼乙醚络合物〔第三组分,BF3O(C2H5)2,M=142〕
无色透明液体,有刺激性,有腐蚀性,易溶于苯,较难溶于加氢汽油。
其组成为:
BF3含量:
>46%;沸点:
124.5-126℃
使用时溶于溶剂油中,配比为:
溶剂油/三氟化硼乙醚=250/1。
D催化剂的化
a〕什么是化
把催化剂的各组份按一定配比,在一定条件下混合,形成催化剂的活性中心,这种方式工业上称之为化。
Ni催化剂的化有三元化、双二元化和稀硼单加化三种方法。
b〕稀硼单加化
这是目前顺丁橡胶工业制备中普遍采用的催化剂化方法,该法特点是催化剂活性最高。
C〕稀硼单加化工艺
化温度:
通常为-50~80℃,而以-5~40℃为宜;
化时间:
通常为0.5~7hr,最宜为1hr;
催化剂浓度:
Al/Ni=3~8、Al/B=0.3~0.7时,催化剂活性最高;
在生产中,可变更B用量来控制产品的门尼粘度。
4〕终止剂:
乙醇
采用纯度为95%的工业品乙醇,其具体质量规格可以通过查询相关化工产品手册得到。
5〕防老剂:
2,6-二叔丁基-4-甲基苯酚〔简称264〕熔点69-71℃,游离甲酚<0.04%,灰分<0.03%,油溶性:
合格。
3.生产工艺概况
1〕工艺流程
催化剂配置→聚合→单体回收→凝聚→脱水枯燥
2〕工艺流程简述
溶液聚合生产顺丁橡胶工艺过程包括原料精制、引发剂配制、聚合、回收、凝聚、后处理等工序。
聚合级丁二烯由泵经流量控制与由泵经流量控制送来的溶液油在文氏管中混合后,再经丁油预热〔冷〕器进展预热〔冷〕后,与分别由计量泵送出的Ni组分、Al组分经文氏管混合后的混合物混合,连续送入聚合釜首釜底入口;
B组分由计量泵送出与稀释油在文氏管中混合后直接送入聚合釜首釜底入口;
聚合釜为不锈钢制并装有双螺带式搅拌器;
物料在首釜反响一定时间后,从釜顶出来进入第二釜、第三釜等连续进展聚合反响;
当到达规定门尼粘度后,进入终止釜用乙醇破坏引发剂使反响终止;
从终止釜出来的胶液经过滤器进入胶液罐,回收局部未反响的单体送单体回收罐区,再经精制处理循环使用;胶液在胶液罐中被混配成优级品的门尼粘度,然后经胶液泵送入凝聚釜用0.9MPa水蒸汽在搅拌下於热水中进展凝聚。
从凝聚釜顶出来的单体和水蒸汽经冷凝器冷凝,入油水别离罐别离出溶剂油和少量单体送回收精制后循环使用;水经液面调节阀控制排出,经二次净化处理排入地沟;
从凝聚釜底出来的胶粒与循环热水颗粒泵送入缓冲罐,经1号经振动筛别离出胶料去洗胶罐。
在洗胶罐中,用40~60℃热水对胶粒进展洗涤,洗涤后的胶粒经2号振
动筛别离后,含水量约为40%~60%的胶粒送入挤压机挤压脱水。
经挤压脱水后,胶粒含水量为8%~15%。
将其切成细条形,并进入膨胀枯燥机加热、加压,到达膨胀和蒸,进一步除去所含的大局部水分,再送入水平红外枯燥箱中枯燥,使胶条的含水量降到0.75%以下;
枯燥合格的胶条经提升机送入自动称量秤,按每块25kg进展压块,并用塑料薄膜包好,装袋封口入库。
3〕聚合工艺
A反响机理
丁二烯的采用配位聚合法〔双烯烃定向聚合〕,生产采用连续式溶液聚合法。
B典型生产配方
工程
控制指标
工程
控制指标
丁油浓度
12-15g/ml
镍/丁
≤2.0×10-5
铝/丁
≤1.0×10-4
硼/丁
≤2.0×10-4
铝/硼
>0.25
醇/铝
6
铝/镍
3-8
防老剂/丁
0.79-1.0%
聚合压力
<0.45MPa
丁二烯单耗
1.045t/t-p
收率
>95%
转化率
>83%
聚合温度
首釜<95℃;末釜<100℃
C传热与搅拌
丁二烯的聚合反响热约为325k/kg,反响过程中必须及时排除反响热。
为改善传热效果,可采用传热面积大的反响釜和特种类型的搅拌器。
搅拌器常选用螺带式,有的还带有刮刀,以强化搅拌。
a〕传热方法
夹套通冷冻盐水,仅移出反响热的10%;
首釜冷进料法,平衡反响热;
次釜补充冷溶剂,平衡反响热。
b〕搅拌器
双螺带式搅拌器,径向和轴向均有较大的搅动,适用于高粘度流体的搅拌。
D反响体系的粘度问题
溶液聚合制造高顺丁橡胶时,聚合体系的粘度问题随着聚合反响的进展而剧烈上升,这给搅拌和除去反响热造成严重困难,即难得到高分子量,又难到高转化率。
E主要分析控制指标
物料名称
采样地点
分析工程
控制指标
分析时间
丁二烯
丁二烯总管线
组成
水值
杂质
胺值
>99%
<20mg/kg
乙腈检不出
<1mg/kg
每班一次
每班一次
溶剂油
溶剂油总管
水值
胺值
<20mg/kg
<0.2mg/
浓镍
浓镍高位槽
浓度
稀镍
镍配制槽
浓度
(1.0+0.05)g/L
稀铝
浓度
防老剂
配制釜
浓度
丁油
丁油管线
水值
丁浓
<20mg/kg
12~/L
胶液
末釜出口
胶含量
转化率
≥100g/L
≥83%
胶液
首釜出口
末釜出口
门尼黏度
门尼黏度
50
45
4〕凝聚工艺
A凝聚目的:
脱除溶剂,使橡胶颗粒分散在水中;
B常用方法:
盐析法、蒸发法、冷冻法和水析法
C水析凝聚枯燥法:
将胶液注入热水中,用水蒸汽汽提,脱除溶剂及未反响的单体,橡胶凝聚成小颗粒,然后再经脱水枯燥而成产品,称为水析凝聚枯燥法。
工业上主要用此法:
第一过程—水蒸汽蒸馏过程
第二过程—扩散过程
降低胶粒中残留溶剂比拟困难,所以起控制作用的是扩散过程。
D凝聚结果的评价指标
水蒸汽的耗量;
胶粒中溶剂含量〔胶中含油量〕
三、后处理单元
1、后处理单元生产原理及工艺流程
后处理单元分为四个局部,分别为洗胶局部、枯燥局部、压块局部、包装局部。
1.1洗胶局部
用水洗涤除去凝聚后的胶粒外表杂质,调节胶粒温度,控制胶粒密度和流量,给挤压脱水机供料脱水。
1.2枯燥局部
将含水量为40~60%的橡胶粒投入挤压脱水机。
经挤压脱水,切成含水量在5-12%的胶片原料进入膨胀枯燥机J-0805。
膨胀枯燥机通过无级变速器和驱动马达将橡胶在膨胀机升温、造压,到达必要的枯燥目的,在螺桶切入膨胀机出料端形成硬质物的同时,由双螺旋片抽送胶料固体物,转化为机械能,来增加模孔的热胶料流量,以保持膨胀枯燥机的温度。
1.3压块局部
橡胶经过振动枯燥流化床进一步枯燥后,经称量后压块。
1.4包装局部
由压块机送来的橡胶块经包装后成为成品橡胶。
四、回收单元
1.装置的作用
聚合胶液除了含有溶剂和聚丁二烯外,尚含有未反响的丁二烯,每生产1t顺丁橡胶,约有0.25t的回收丁二烯和4.5t左右的溶剂需要进展回收处理。
回收装置的任务是,将回收粗溶剂〔丁二烯与溶剂的混合物〕进展别离、精制,使回收溶剂和丁二烯符合聚合要求,返回聚合使用。
由于本装置所用丁二烯和溶剂全部外购,回收装置还担负着对外购丁二烯和溶剂精制的任务。
本装置生产过程是一系列的精馏操作过程,利用混合物中各组分的挥发度不同,在一定温度压力下在塔中进展气液接触,通过屡次局部汽化和局部冷凝,到达轻重组分别离的目的。
回收装置是顺丁橡胶生产过程最大的“毒〞〔脱出水和轻、重组分杂质〕系统。
回收装置操作水平关系着聚合单元生产的稳定性和产品质量。
2.料和产品
原料:
凝聚来粗溶剂、外购溶剂、外购丁二烯、阻聚剂TBC
产品:
溶剂,供聚合循环使用,供催化剂配制使用,丁二烯,供聚合使用。
3.塔操作参数及影响
精馏塔的主要工艺参数有进料量、进料组成、进料温度、操作压力、精制温度及回流比等。
实际精馏过程的每一个精馏塔都是针对完成某一生产任务而设计,即按一定生产能力和别离要求而设计,因此,影响精馏效果的主要操作参数有操作压力、塔顶温度、塔釜温度回流比和进料组分的变化等。
3.1操作压力的影响
操作压力主要由被精馏物料的组成决定,由塔顶冷凝器和不凝气出料量控制。
在操作中,操作压力由下而上逐板降低,一般选择控制塔顶压力来控制塔的操作压力。
在一定塔顶温度、塔釜温度及回流比的精馏过程中,改变操作压力,每一层塔板上的汽液传质都会发生变化。
提高操作压力,气相中的重组分浓度减少,轻组分浓度增加,有利于提高塔顶产品的纯度,塔顶采出量减少,而塔釜液中轻组分浓度增加,塔底产品质量下降,塔釜采出量增加。
同理,降低操作压力,精馏效果将向相反方向变化。
3.2精馏温度的影响
在精馏操作中,塔温度沿塔高而变化,由下而上温度逐板降低,塔顶温度最低,塔釜温度最高。
塔顶、塔釜温度由进料组成和操作压力决定,由塔底再沸器控制。
在一定操作压力下,汽、液平衡与温度有密切关系。
不同的温度对应着不同的汽、液平衡组成。
塔顶、塔釜的汽、液平衡组成反映产品的质量状况,它所对应的平衡温度就是塔顶、塔釜的温度控制指标。
因此,在精馏过程中,塔顶、塔釜温度反映了精馏效果。
当操作压力一定时,塔顶温度、塔釜温度要保持相对稳定。
在一定操作压力和回流比的精馏过程,改变塔顶温度、塔釜温度,每一层塔板上的温度都会改变,每一层塔板上的汽液传热、传质都会发生变化。
提高塔顶温度、塔釜温度,液相中的重组分浓度增加,轻组分浓度减少,有利于提高塔釜产品的纯度,塔釜采出量减少;塔顶产品重组分增加,塔顶产品质量下降,塔顶采出量增加。
同理,降低塔顶、塔釜温度,精馏效果将向相反方向变化。
3.3回流比的影响
精馏塔顶回流液与采出量之比称为回流比。
在精馏塔操作中,改变回流比对精馏效果有明显影响。
正常操作,回流比一般保持不变,产品不合格时,才作适当调节。
在一定操作压力和一定塔顶温度、塔釜温度的精馏过程中,提高回流比能提高塔顶产品的纯度,但回流比的增加,却增加了精馏塔的负荷,降低了生产能力,并增加了精馏过程的能量消耗。
因此,在确保精馏塔采出合格产品的前提下,应尽量降低回流比。
值得注意是,对于物料中具有特殊物理化学性质的某些组分的别离如脱水过程,如果提高回流比,反而会降低其别离效果。
在精馏过程,操作压力、塔顶温度、塔釜温度和回流比是影响精馏效果的主要参数,针对以较低的能耗物耗完成某一物料的别离过程,必须进展工艺条件优化,才能到达理想的精馏效果。
3.4进料组分的影响
在精馏塔操作中塔釜、塔顶温度和压力不变,回流比不变的情况下,当进料组分发生变化时,可以通过改变塔体进料口的位置来相应加以解决
组分变轻时可以把进料口位置相应的向上移动,以增加提馏段的塔板数来保证塔釜组分的合格组分变重时可以把进料口位置相应的向下移动,以增加精馏段的塔板数来保证塔顶组分的合格。