钢铁企业能耗分析与未来节能对策研究.docx
《钢铁企业能耗分析与未来节能对策研究.docx》由会员分享,可在线阅读,更多相关《钢铁企业能耗分析与未来节能对策研究.docx(7页珍藏版)》请在冰豆网上搜索。
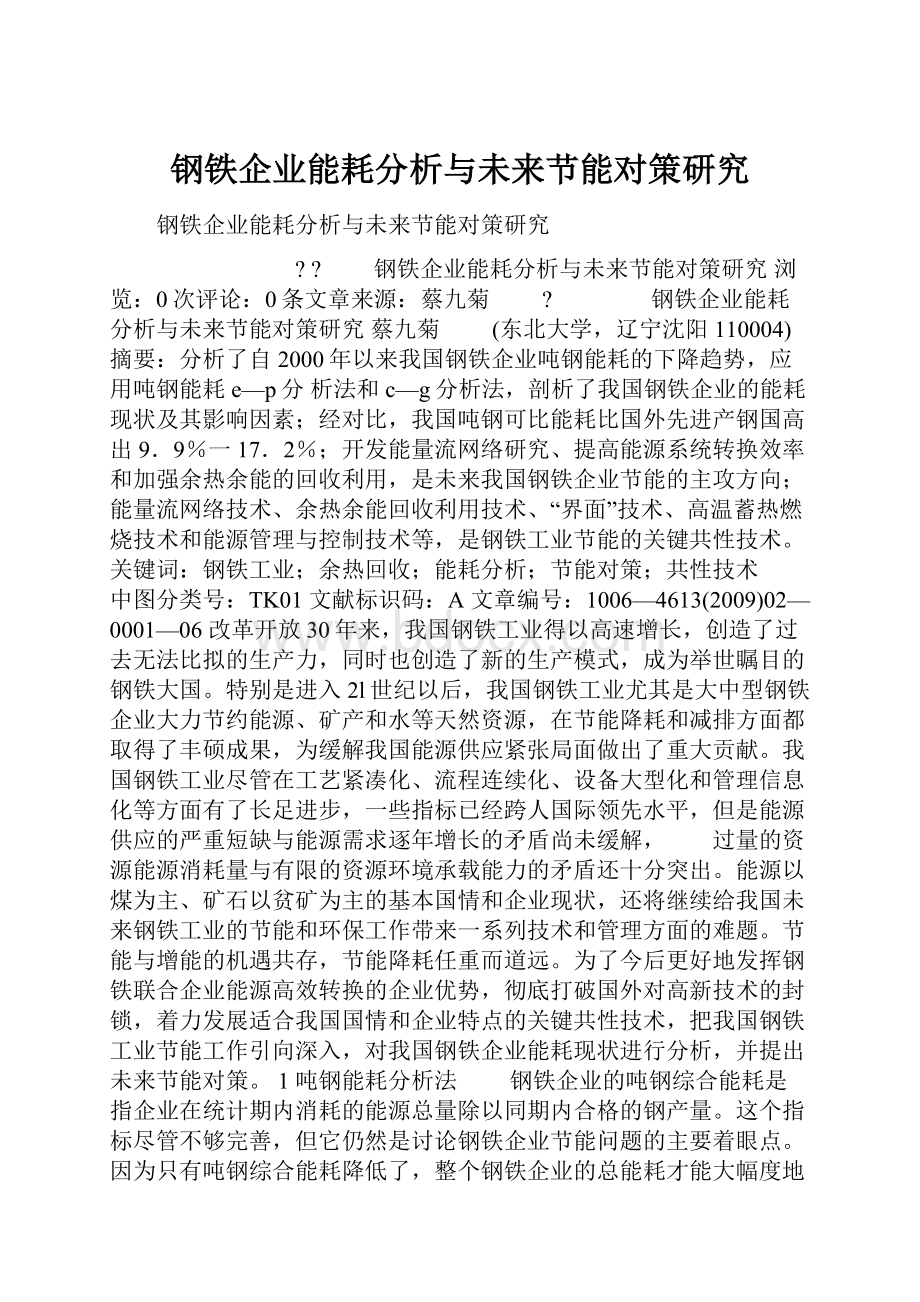
钢铁企业能耗分析与未来节能对策研究
钢铁企业能耗分析与未来节能对策研究
?
?
钢铁企业能耗分析与未来节能对策研究浏览:
0次评论:
0条文章来源:
蔡九菊 ?
钢铁企业能耗分析与未来节能对策研究蔡九菊 (东北大学,辽宁沈阳110004) 摘要:
分析了自2000年以来我国钢铁企业吨钢能耗的下降趋势,应用吨钢能耗e—p分析法和c—g分析法,剖析了我国钢铁企业的能耗现状及其影响因素;经对比,我国吨钢可比能耗比国外先进产钢国高出9.9%一17.2%;开发能量流网络研究、提高能源系统转换效率和加强余热余能的回收利用,是未来我国钢铁企业节能的主攻方向;能量流网络技术、余热余能回收利用技术、“界面”技术、高温蓄热燃烧技术和能源管理与控制技术等,是钢铁工业节能的关键共性技术。
关键词:
钢铁工业;余热回收;能耗分析;节能对策;共性技术 中图分类号:
TK01文献标识码:
A文章编号:
1006—4613(2009)02—0001—06改革开放30年来,我国钢铁工业得以高速增长,创造了过去无法比拟的生产力,同时也创造了新的生产模式,成为举世瞩目的钢铁大国。
特别是进入2l世纪以后,我国钢铁工业尤其是大中型钢铁企业大力节约能源、矿产和水等天然资源,在节能降耗和减排方面都取得了丰硕成果,为缓解我国能源供应紧张局面做出了重大贡献。
我国钢铁工业尽管在工艺紧凑化、流程连续化、设备大型化和管理信息化等方面有了长足进步,一些指标已经跨人国际领先水平,但是能源供应的严重短缺与能源需求逐年增长的矛盾尚未缓解, 过量的资源能源消耗量与有限的资源环境承载能力的矛盾还十分突出。
能源以煤为主、矿石以贫矿为主的基本国情和企业现状,还将继续给我国未来钢铁工业的节能和环保工作带来一系列技术和管理方面的难题。
节能与增能的机遇共存,节能降耗任重而道远。
为了今后更好地发挥钢铁联合企业能源高效转换的企业优势,彻底打破国外对高新技术的封锁,着力发展适合我国国情和企业特点的关键共性技术,把我国钢铁工业节能工作引向深入,对我国钢铁企业能耗现状进行分析,并提出未来节能对策。
1吨钢能耗分析法 钢铁企业的吨钢综合能耗是指企业在统计期内消耗的能源总量除以同期内合格的钢产量。
这个指标尽管不够完善,但它仍然是讨论钢铁企业节能问题的主要着眼点。
因为只有吨钢综合能耗降低了,整个钢铁企业的总能耗才能大幅度地降下来。
吨钢综合能耗的计算式过于简单,有些复杂因素没有包括进来,所以从中不易了解钢铁制造流程的各个环节和各种因素对它的影响,也不便于分析整个钢铁企业的节能潜力、方向和途径所在。
为了弥补吨钢能耗指标的这些缺陷,有必要对吨钢能耗的计算式作进一步解析,使它成为既是评价钢铁企业能耗水平的一个指标,又是用来分析其主要影响因素的数学表达式。
像这样以吨钢能耗为研究对象的分析方法可分为两种:
吨钢能耗e—p分析法[1]和吨钢能耗c—g分析法。
前者是能耗分析常用的方法,它以构成钢铁制造流程的各道生产工序为分析对象,重点研究钢铁企业中物质流的变化过程及其各组成环节对能源的消耗,不同种类的能源消耗量均以标准煤计,不去分门别类地研究与能源介质的转换、分配、使用和缓冲等问题;后者是能耗分析的新方法,它以企业能源结构中各种能源介质为分析对象,重点研究钢铁企业中能量流的变化过程以及能量流网络问题,包括每种能源介质的生产、转换、存储、分配、缓冲、使用和放散等。
1.1吨钢能耗e—p分析法 按吨钢综合能耗所包含的具体内容,可将吨钢综合能耗E0的计算式解析为各生产工序的工序能耗与钢比系数乘积的代数和,即:
式中:
ei为统计期内各道生产工序的工序能耗,tce/t实物;Pi为统计期内各道生产工序的实物产量与钢产量之比,统称为某道工序的钢比系数,t/t,它是对企业生产(产品)结构的定量描述。
为了分析某时期的节能效果,可将统计期始末吨钢能耗指标的改变量hE分解为:
式中:
两组括弧内的差值分别代表统计期始末某工序的钢比系数、工序能耗的改变量。
等式右侧的第一项是因钢比系数变化(企业结构调整)获得的节能量,称为间接节能量;第二项是因工序能耗变化(各工序节能)获得的节能量,称为直接节能量。
式
(2)可见,影响吨钢综合能耗的直接因素有两个方面,一方面是对应每吨钢产量的各工序的实物产量,即各工序的“钢比系数”;另一方面是各工序生产每吨实物量的能耗,即各工序的“工序能耗”。
为了降低吨钢综合能耗,一要改善企业生产结构,即降低各工序的钢比系数;二要降低各工序生产单位产品所直接消耗的燃料量及各种动力,即各工序的工序能耗,两者缺一不可。
1.2吨钢能耗c—g分析法 按吨钢综合能耗所包含的能源种类和数量等具体内容,还可将吨钢综合能耗E0的计算式解析为每吨钢所消耗各种能源介质的数量与该种能源介质在生产、转换或改制过程中所消耗能量的乘积之和,即:
式中,cj为统计期内第j种能源介质的化学能再加上它在加工、改制和输运过程中所消耗的能量,即这种能源介质的能值,习惯上称它折算成标煤的系数,简称折标系数,kgce/实物;gj为统计期内对应每吨钢所消耗第j种能源介质的实物量,实物/t钢。
为了分析某个时期的节能效果,可将统计期始末吨钢综合能耗指标的改变量分解为:
公式右侧两组括弧内的差值,分别代表统计期始末每吨钢所消耗的各种能源介质的改变量以及这些能源介质的折标系数的变化量。
其中,第一项是因每吨钢所消耗的能源介质的种类和数量发生变化而获得的节能量,简称为钢铁制造过程节能量;第二项是因能源介质的折标系数发生变化而获得的节能量,称为能源转换过程节能量。
进一步解析式(3)可知,影响吨钢综合能耗的直接因素有三:
一是各种能源介质在生产和转换过程中所消耗能量的多少;二是对应每吨钢所消耗各种能源介质的实际消耗量和放散量;三是对应每吨钢余热余能的回收利用量。
2我国钢铁工业能耗现状与分析2.1我国钢铁工业能耗现状 1980年我国钢产量3712万t,能源消耗总量7573万t标准煤,大中型钢铁企业的吨钢综合能耗为1.646tce/t钢,吨钢可比能耗1.285tce/t钢;到2005年,钢产量达到34900万t,总能耗上升到25861万t标准煤,吨钢综合能耗0.741tce/t钢,吨钢可比能耗0.714tce/t,钢。
25年间,我国的钢产量增加了9倍,但总能耗只增加了3倍。
2005年以后,国家统计局重新调整了电力折标系数,规定用电热当量值(即1kWh=0.1229kgce)替换冶金工业一直沿用的供电煤耗等价值(即1kWh=0.404kgce)。
粗略核算,如果电力采用国家统计局规定的新折标系数,将使我国钢铁工业的平均吨钢综合能耗指标大约下降100kgce/t.钢,参见图l。
图l可见,如果考虑电力的新老折标系数之间的差异,用老折标系数重新核算2006年以后我国钢铁工业的能耗数据,或许会发现近几年吨钢能耗指标变化并不大,继续节能的难度在逐年增加,吨钢能耗下降趋势变缓。
考虑现有数据的完备情况和分析结果的可比性, 以2005年的实际生产数据为基准,代表我国钢铁工业现有的能耗水平并与国外先进产钢国家作对比。
2.2我国吨钢能耗与先进产钢国的比较 2005年,我国大中型钢铁企业的吨钢可比能耗是714tce/t钢(电的折标系数取0.404kgce/kWh)。
进入21世纪,国际钢铁协会曾报告其会员单位的吨钢综合能耗2004年为19.1GJ(折合652kgce/t钢)[2]。
最近几年,受环境保护、产品深加工以及电炉钢比下降等增能因素的影响,这些国家的吨钢能耗都有不同程度的回升。
表l为2005年我国大中型钢铁企业吨钢可比能耗数据与先进产钢国家的对照表,其中国外吨钢能耗为550kgce/t钢,平均电炉钢比取0.30[3]。
若不考虑国内外轧钢系统在加工深度、工序能耗和成材率等方面的差异,现阶段我国大中型钢铁企业的吨钢可比能耗至少要比先进产钢国家高出9.9%, 即64kgce/t钢;若考虑两者的差异并取我国轧钢工序与国外相同的水平,则我国吨钢可比能耗要比先进产钢国高达17.2%,即112kgce/t钢。
其中:
①因钢比系数(生产结构)落后,使我国吨钢能耗高出国外55.1kgce/t钢,主要原因有我国的铁钢比高、矿钢比高、而电炉钢比低,折合每吨钢我国的铁水消耗量要比先进产钢国家高出130kg,铁矿石消耗量高出294㎏,电炉钢比却低14.2个百分点;②因工序能耗和“其它”环节能耗高,使我国吨钢能耗高出外国56.9kgce/t钢,主要原因有:
转炉、电炉工序能耗高出国外20.5kgce/t钢(折合吨钢转炉、电炉工序能耗高出13.3kgce/t钢);烧结和球团工序能耗高出8.0kgce/t矿(折合吨钢烧结、球团工序能耗高出8.3kgce/t钢);高炉炼铁工序能耗低7.0kgce/t铁(折合吨钢高炉工序能耗低5.1kgce/t钢);“其它”环节于装备、技术和管理落后,折合每吨钢高出国外能耗40.4kgce。
3未来节能对策及关键技术研究 总而言之,现阶段我国重点钢铁联合企业跻身于世界钢铁强国行列的最大障碍,不是生产工艺、装备和产品不先进,而是能源消耗和环境质量尚不能满足钢铁强国之要求。
钢铁工业是典型的流程制造业,上系天然资源(矿产、能源、水),下系自然环境(固、液、 气体废弃物),对全社会资源、能源、环境的影响举足轻重。
所以,钢铁企业作为循环经济产业链条的重要成员,理应具备三大功能H]:
钢铁产品制造功能、能源高效转换功能、废弃物消纳处理功能。
在这方面做得最好的是日本钢铁界,我国钢铁企业必须虚心向其学习,把节能 减排作为我国建设强大钢铁工业和走新型工业化道路的优先切人点。
3.1未来钢铁企业的节能方向与途径 为了节能,必须既要节约能源又要节约非能源;既要研究钢铁生产流程和它的表现形式——物质流,又要研究能源转换过程及其表现形式——能量流和能量流网络。
只有整个钢铁企业的物质流和能量流都能实现连续化、紧凑化和高效化,才会收到良好的节能效果。
我国钢铁企业节能必须沿着以下四个方向展开:
(1)降低各生产工序原料、溶剂料、零部件和耐火材料等非能源物质的单耗及其载能量。
各生产工序一定要重视本工序的原料消耗,尤其是主要原料——铁水、烧结矿的消耗,这是节能工作的基础。
对于钢铁企业而言,铁钢比是影响吨钢能耗的一个重要因素。
铁钢比高(即电炉钢比低)的企业,吨钢能耗一定高。
然而,降低铁钢比(即增加电炉钢比例)不是企业自身所能决定的,它与社会上存储的废钢资源有关。
有理论研究表明[5],一个国家废钢资源是否充足,不仅取决于这个国家的折旧废钢与加工废钢的总量,而且还与这个国家的钢产量及其变化程度密切相关。
在钢产量持续高速增长的情况下,废钢资源十分短缺,价格亦较高。
一些企业试图扩大电炉钢比例,不是明智之举。
相反,实施精料方针,提高烧结矿和球团矿品位,才是降低原料消耗的有效途径。
(2)提高能源系统生产、转换、加工等环节的能源转换效率,是钢铁企业节能的重点。
能源高效转换是钢铁联合企业的三大功能之一,本应发挥得很好。
相反,它却成了现阶段我国钢铁企业与国际先进水平的主要差距之一。
原因是焦炭、电力、蒸汽、氧气、鼓风等二次能源在生产、加工、运输过程中的能耗过高,耗损或放散严重。
今后,必须加强对钢铁联合企业“能量流”运行规律的研究和“能量流网络”的建设,通过转换、改制、优化、缓冲、调控等手段,提高能源系统转换效率,使能量耗散最少。
(3)降低各生产环节燃料、电力、氧气、蒸汽和工业水等能源动力的单耗及其载能量,是钢铁企业节能的重要方向。
当前的问题是一些生产环节的燃料和动力消耗过高,与国外先进水平相比,差距很大。
不设法降低这些能源介质的单耗,吨钢能耗是降不下来的。
(4)回收生产过程中散失的各种余热、余能和废弃物等。
调查研究结果表明∞0,我国钢铁企业余热资源的回收利用率,落后国外近20个百分点。
今后,要更多地依靠技术进步,深入研究余热余能资源的回收利用理论、技术和装备,将以往余热资源的单一间接回收方式改变为间接和直接联合回收;将单纯的热回收改变为热电联产。
3.2若干关键共性节能技术研究
(1)能量流网络技术 在研究钢铁企业节能问题时,不能只停留在有关物料平衡和能量平衡的基础上,还要进一步建立起动态的能量输入一输出、能量流和“能量流网络”的概念。
将钢铁联合企业抽象为铁素物质流的输入一输出过程、能量流的输入一输出过程,以及铁素流一能量流相互作用过程,有利于剖析物质流、能量流在钢铁生产过程中的动态行为,提高能源系统的转换效率,为钢铁企业进一步节能减排寻求新的突破口。
能源系统网络化,是以信息化改造传统产业的需要,是研究钢铁联合企业能源高效转换、储存、分配、使用、回收、缓冲和优化调控的重要方法。
(2)余热余能资源的回收利用技术 据调查统计,目前我国生产lt钢产生的余热资源量平均为8.44GJ/t钢。
其中,产品或中间产品显热为3.35GJ/t钢,占余热资源总量的39%;渣显热为0.74GJ/t钢,占9%;废(烟)气显热为3.10GJ/t钢,占37%;冷却水显热约为1.24GJ/t钢,占15%。
2005年,我国钢铁工业余热资源的平均回收率只有25.8%。
其中,以回收高温余热居多,回收率为44.4%;其次是中温余热,回收率为30.2%;低温余热回收率还不足1%。
随着钢 铁工业生产流程的逐步优化和工序能耗的不断降低,科学地回收利用各生产工序产生的余热余能资源,是未来钢铁工业节能的主攻方向。
今后,要以热力学第一、第二两大定
律为指导,根据余热余能的数量、质量以及用户对能量的需求,确定余热余能的最佳回收方式和优先使用顺序,做到“按质用能,温度对口,有序利用”。
高温余热应首先用于动力回收;低温余热应首选直接热利用。
(3)“界面”热衔接技术 “界面”是相对于钢铁生产流程中烧结、炼铁、炼钢、连铸和轧钢等主体工序而言的,指的是两相邻工序(或区段)之间的连接部分或过度过程。
“界面技术”是指相邻工序之间的衔接一匹配、协调一缓冲技术、物质流的物理和化学性质调控技术及其相关装置。
钢铁生产流程的重要界面有:
原燃料一烧结界面、原燃料一焦化界面、烧结一高炉界面、高炉一转炉界面、连铸一加热炉界面等。
其中以高炉一转炉、连铸一加热炉界面最为重要。
发展界面技术可实现生产过程中物质流、能量流、温度、时间等基本参数的衔接(尤其是热衔接)、匹配、协调、稳定,极大地促进生产流程整体运行的稳定、协调,实现紧凑化、连续化和高效化。
(4)高温蓄热燃烧技术 高温蓄热燃烧技术(HighTemperatureAirCombustion)是在传统蓄热室换热技术的基础上 (如高炉热风炉、炼钢平炉、焦炉等)形成和发展的,是蓄热室设计结构、热工操作以及火焰炉燃烧方法和燃气显热回收方式的一次重大革新。
以烧纯高炉煤气为特色的蓄热式加热炉,利用与炉体或烧嘴紧密结合的内置式、外置式和蓄热式燃烧器等蓄热室换热技术充分地回收烟气余热,将高炉煤气和助燃空气双预热至1000℃左右,既满足了加热炉加热工艺和炉温制度的要求,又解决了部分企业高炉煤气严重放散问题,具有显著的节能效果和大幅度降低烟气中NOx排放的双重优越性。
目前,应着重研究大型蓄热式加热 炉的结构、操作和控制等,重点解决炉压波动大、冒火现象严重、炉子投资高、维修频繁和使用寿命短等问题。
(5)能源管理与控制技术 能源管控系统(EMS)是一个集冶金过程监视、控制、能源调度、能源管理为一体的计算机网络系统,对全公司的能源设备和能源介质具有遥控、遥测、计算、预测、事故预警等功能,对能量流和能量流网络实施数据采集、动态预测、离线决策、实时调度和优化运行,从而实现全厂的能源节约和近“零”放散。
它不是单纯的职能管理部门,而是能源调控系统的实体,即能源管理控制指挥中心。
进入21世纪以后,我国部分钢铁企业的能源管控中心已经建成或正在建设之中,其建设水平多数处于能源计量网和能源管理系统的建设阶段,少数进入离线决策和优化运行的开发阶段。
今后,必须用“非平衡”的观点和能量流网络技术,重新认识钢铁企业中能源供需关系的变化规律,科学规划并制定能源供应与使用间的“不平衡” 策略,特别是富余煤气、氧气、热力的缓冲和使用问题,把钢铁企业节能工作推向新阶段。
4结论
(1)改革开放30年来,我国钢铁工业节能工作取得巨大成绩,其中一半靠直接节能,一半靠问接节能。
开展能量流网络研究、提高能源系统转换效率、加强余热余能资源的回收与利用,是今后我国钢铁工业节能的主要方向。
(2)吨钢能耗e—p分析法和c—g分析法是全面分析钢铁企业能耗现状及其影响因素的科学方法,前者以物质流分析为主,后者以能量流分析为主。
钢铁工业既要节约用能,更要科学用能,必须更多地依靠科技进步和自主创新,把我国钢铁工业的节能工作推向新阶段。
(3)统计分析结果表明,现阶段我国大中型钢铁企业的吨钢可比能耗比先进产钢国家高出9.9%~17.2%。
我国与钢铁强国的最大差距不是生产工艺、装备和产品不先进,而是能源消耗和环境质量尚不能满足钢铁强国的要求。
节能减排是我国建设强大钢铁工业的当务之急。
(4)能量流网络技术、余热余能回收利用技术、“界面”技术、高温蓄热燃烧技术、能源管理与控制技术,是未来我国钢铁工业节能的关键共性技术。