气瓶应力分析和强度计算.docx
《气瓶应力分析和强度计算.docx》由会员分享,可在线阅读,更多相关《气瓶应力分析和强度计算.docx(40页珍藏版)》请在冰豆网上搜索。
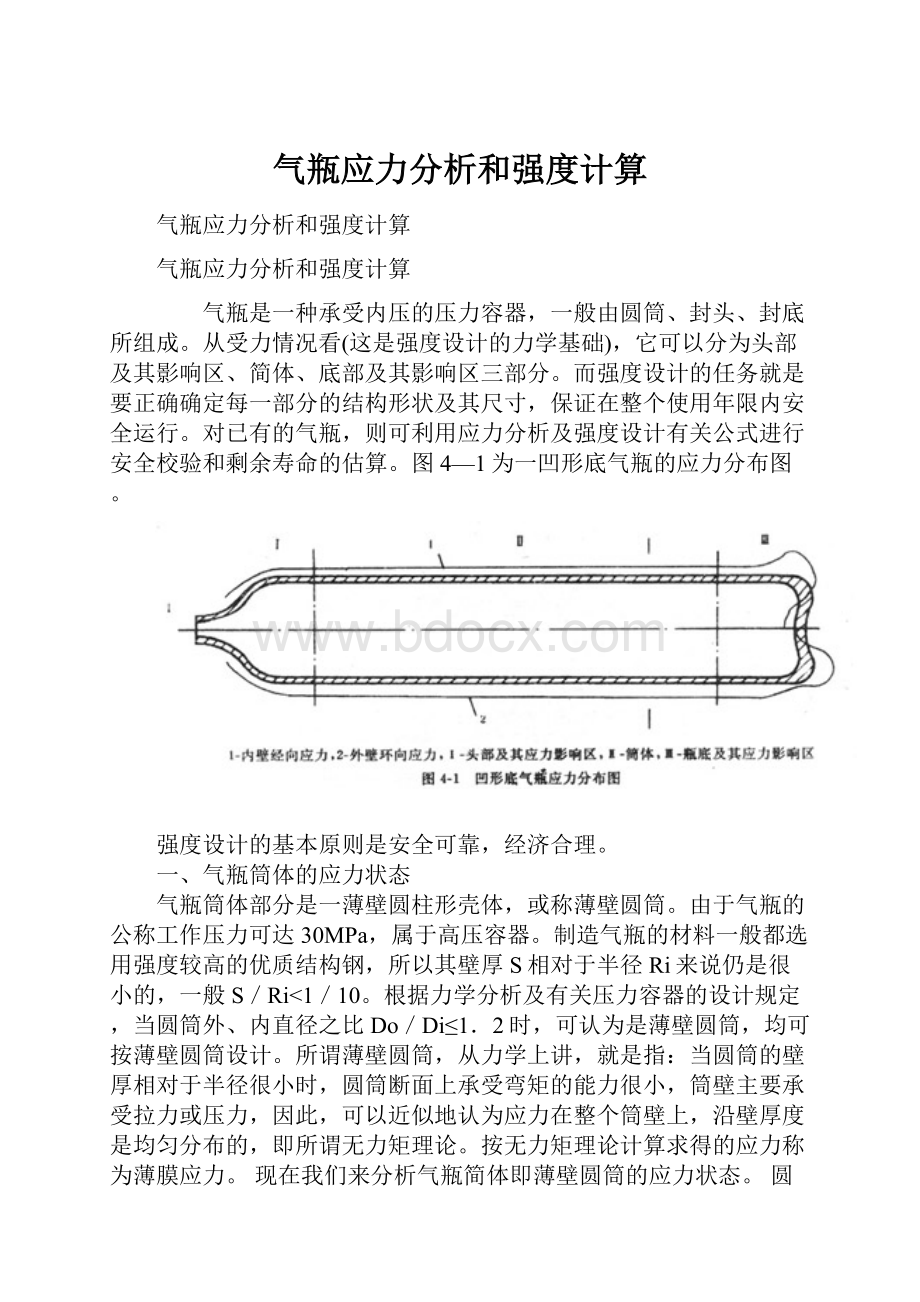
气瓶应力分析和强度计算
气瓶应力分析和强度计算
气瓶应力分析和强度计算
气瓶是一种承受内压的压力容器,一般由圆筒、封头、封底所组成。
从受力情况看(这是强度设计的力学基础),它可以分为头部及其影响区、简体、底部及其影响区三部分。
而强度设计的任务就是要正确确定每一部分的结构形状及其尺寸,保证在整个使用年限内安全运行。
对已有的气瓶,则可利用应力分析及强度设计有关公式进行安全校验和剩余寿命的估算。
图4—1为一凹形底气瓶的应力分布图。
强度设计的基本原则是安全可靠,经济合理。
一、气瓶筒体的应力状态
气瓶筒体部分是一薄壁圆柱形壳体,或称薄壁圆筒。
由于气瓶的公称工作压力可达30MPa,属于高压容器。
制造气瓶的材料一般都选用强度较高的优质结构钢,所以其壁厚S相对于半径Ri来说仍是很小的,一般S/Ri<1/10。
根据力学分析及有关压力容器的设计规定,当圆筒外、内直径之比Do/Di≤1.2时,可认为是薄壁圆筒,均可按薄壁圆筒设计。
所谓薄壁圆筒,从力学上讲,就是指:
当圆筒的壁厚相对于半径很小时,圆筒断面上承受弯矩的能力很小,筒壁主要承受拉力或压力,因此,可以近似地认为应力在整个筒壁上,沿壁厚度是均匀分布的,即所谓无力矩理论。
按无力矩理论计算求得的应力称为薄膜应力。
现在我们来分析气瓶简体即薄壁圆筒的应力状态。
圆筒是最简单的一种回转壳体,也是压力容器中最基本的部分。
薄壁圆筒的无力矩理论应力状态可以用分析回转壳体应力状态的一般方法求解,也可以更简单的从静力平衡方程式直接求得。
以图4—2为例,如果我们在气瓶中部以垂直于轴线的平面(横截面)将气瓶截为上下二段,则作用在环断面的经向应力(亦称轴向应力)的合力为πDSo经,此力应与由内压P作用在气瓶底端的总轴向力(不管封头形状如何,均为π/4D2ip)相平衡,
即
因系薄壁圆筒,故内径D”可近似地等于平均直径Di.即D1≈D,由此,可求得作用于圆筒横截面上的经向应力。
为了求得环向应力(亦称周向应力或切向应力),则可取长度为L的一段圆筒,并以通过轴线的纵向截面将此圆环沿轴线切开,如图4—3所示,一辟两半,并沿Y--Y方向列静力平衡方程式,由于内压P引起的Y方向的合力为P·Di·L此合力应与作用在二块长为L宽为S的纵向断面上的环向应力的合力2·L·S·σ环相平衡,因此,
公式(4.1)及(4.2)中圆筒的直径均为内径,所以有时亦称内径公式。
如果式(4.1),(4.2)中Di近似地用平均直径D,则得中径公式:
对比式(4.1)及(4.2)可知:
气瓶简体的环向应力较经佝应力为大,σ环=2σ径。
所以环向是薄弱环节,这与如图(4—1)所示的气瓶实测应力分布曲线是一致的。
气瓶爆破试验或气瓶爆破事故实例一般也是瓶身纵向开裂爆破,即是由于作用在气瓶筒体轴向断面上的环向应力达到材料抗拉强度所引起的。
故焊接气瓶(如液化石油气钢瓶)尽量不用或少用纵向焊缝,也就是这个道理。
如果爆破试验或气瓶爆破事故中发生环向断裂,则应分析出现轴向强度低于环向强度的具体原因。
有些特殊用途的气瓶,例如飞机上用的灭火瓶,为了降低气瓶的重容比,针对简体强度是薄弱环节这一特点,就采用绕丝式结构,即在气瓶的外壁再缠绕上几层超高强度钢丝以增加简体承受环向载荷的能力。
采用这种结构,即保证了气瓶环向强度,又可充分发挥轴向强度的潜力,这种设计称为等强度设计。
也有一些航空用气瓶,外形象'糖葫芦”,相当于几个球壳串联在一起,这是因为球壳的轴向应力和环向应力是相等的,所以它也是一种等强度壳体。
在我国发射的某宇宙卫星上,即使用球形气瓶,在简体上,如需要开孔时,应尽量开成椭圆形,且使椭圆之短轴平行于筒体轴线,以尽量减小纵截面的削弱程度,从而使环向应力少增加一些。
前面在分析薄壁圆筒的应力状态时,我们曾假定由于壁厚相对于半径来说很小,就像薄膜气球一样,只能承受拉力,不能承受弯矩,因此应力沿壁厚方向是均匀分布的,也就是圆筒外表面上的应力和内表面上的应力是一样的,因此,如果我们从气瓶瓶体上用二个通过主轴并互成。
角的纵截面和二个垂直于主轴的横截面割出一小块来看(如图4—2)只在二个方向受力,即环向力和轴向力,半径方向没有受力,这在力学上叫做二向应力状态(或称平面应力状态)。
如果我们观察得更细一点,在外壁表面上是不受力的(除了大气压力以外,既没有东西压在它上面,也没有东西去拉它),但在内壁上则承受瓶内介质的压力。
如果瓶内装的是15MPa的气体,那么,在内壁表面就受到数值为15MPa压力。
因此,就内壁表面来说,除微块的环向和轴向出现拉应力σ环,σ经以外,在半径方向还出现径向应力σ径,σ径=-P,(此处负号表示在内表面上受的压力)。
这三个正应力互相垂直,由于它们各自所在的平面上无剪应力,这种无剪应力的平面称为主平面。
主平面仅有的正应力称主应力。
根据三个主应力代数值的大小顺序,依次称为第一主应力,第二主应力,第三主应力。
分别以σ1,σ2,σ3表示之(有关概念可参阅材料力学教材)。
所以,实际上内壁表面是处于三向应力状态,而只在外表面上,由于σ径=0才是二向应力状态,为了有一个量的概念。
我们计算一个实例:
有一个气瓶,外径φ=219mm,壁厚s=7.Omm,试计算内压p=15MPa时的应力。
由以上实例可以看出,气瓶简体上的经向应力确实较环向应力小得多,其绝对值只有后者的s/R:
倍,相差一个数量级,所以在强度设计时,忽略径向应力,把气瓶筒体作为薄壁圆筒,按二向应力来考虑是完全可以的,关于壁薄不能承受弯矩的假定也是近似的。
实际上,只要有厚度就有一定的承受弯矩的能力,即抗弯刚度。
气瓶受内压直径要增大,也就是曲率半径要变大。
曲率半径改变,就意味着存在弯矩,计算结果表明:
由于环向弯矩引起的内外表面上的弯曲应力为土专,因而导致环向应力沿壁厚方向的分布不均匀,使内壁表面的环向应力较外壁表面大一个P值。
这个数值相对于环向应力也是不大的,所以不考虑弯曲力矩的影响和应力均匀分布的假定是可以的。
圆筒应力的精确解,可以应用通常所谓的厚壁圆筒公式(或称拉美公式)计算:
式中:
k=Da/Di
表(4—1)列出了上面的气瓶实例按厚壁圆筒公式、中径公式和内径公式的计算结果。
表4-1
压力(MPa)
内壁表面
厚壁公式
内径公式
中径公式
厚壁公式
内径公式
厚壁公式
σ环(=σ1)
223.00
215.35
222.71
208.29
215.35
222.71
σ经(=σ2)
104.15
107.67
111.40
104.15
107.67
111.40
σ径(=σ3)
-14.71
0
0
0
0
0
由以上计算可知,气瓶简体内壁上的环向应力按厚壁圆筒公式计算的精确解为223.OOMPa,如按薄壁内径公式求得的近似解为215.35MPa,较小3.43%,按薄壁中径公式计算则为222.71MPa,甚为接近。
外壁环向应力按厚壁圆筒公式计算的精确解为208.29MPa,如按薄壁内径公式计算则大3.39%,按薄壁中径公式计算则大6.92%,可见用内径公式计算求得的环向应力相当于内外壁环向应力的平均值,略为偏大。
而用中径公式求得的环向应力则接近内壁上的环向应力的精确解。
由于内壁上的环向应力较外壁为大,是危险应力,所以气瓶简体强度计算公式也和一般薄壁圆筒计算公式一样,用的是中径公式。
如若计算经向应力,则薄壁公式计算所得的值均较厚壁公式所得的精确解为大,内径公式较接近,中径公式更大,这从公式(4.1)的推导过程即可看出:
用中径代替内径,必然导致TONG体断面上所受的轴向力的增加。
因而也就增加了经向应力。
按薄壁中径公式求得的内外壁环向应力及轴向应力与按厚壁公式求得的相应应力之比值,亦即薄壁中径公式的准确性与k值有关。
如表4—2所示。
表4-2
由上面分析可知,气瓶简体应力状态按薄壁圆筒公式计算是近似的。
用来计算内壁环向应力可以满足工程计算的精度要求。
应该注意的是计算应力时,要根据要求解决什么问题,达到什么精度,选用什么公式。
二、气瓶筒体的壁厚计算
气瓶酮体强度设计主要任务就是要确定气瓶简体所需的最小壁厚。
对已有的气瓶也可以运用强度计算公式进行强度校核或最高允许充装压力的计算。
要计算气瓶简体壁厚,就需要有强度计算公式,而强度计算公式则是根据简体受力情况所确定的应力状态,然后应用一定的强度理论制定的。
前面我们分析了气瓶简体的应力状态,怎样根据气瓶简体所受的应力计算筒体的壁厚呢?
这里首先要回答二个问题;一、简体所受的应力达到什么极限数值,因为什么原因就要破坏失效了;二、为了使气瓶在使用中安全可靠,并留有必要的安全裕度,气瓶简体允许达到的应力值又是多少?
前者就是强度理论问题,后者就是许用应力亦即安全系数的选用问题。
气瓶在内压作用下,简体处于近似的二向应力状态。
一般工程构件则应力状态更为复杂。
例如厚壁圆筒,除环向应力,经向应力以外,径向应力亦不可忽视。
而一般材料的机械性能',如抗拉强度,屈服点则是用试件在单向拉伸试验下测得的。
要运用材料在简单受力状态下所测得的机械性能去判定在复杂应力状态下的工程构件将在什么条件下开始破坏,就必须寻找并建立这二者之间的联系,这种联系的建立即形成所谓强度理论。
显然,建立联系首先需要找出材料开始破坏的真实原因,以及把复杂应力综合起来变成一个相当于简单应力状态下的应力(即相当应力),然后把相当应力与材料单向拉伸试验所得的机械性能作比较。
因此,强度理论的实质就是关于构件材料破坏内在原因的解释及表达。
强度理论一般有四种。
关于强度理论的完整概念在材料力学或材料强度等书中都有详细阐述。
这里只简单介绍强度理论在气瓶简体强度设计中的应用。
(一)第一强度理论(最大主应力理论)
最大主应力理论认为材料的破坏是由于最大正应力引起的,就是说,某一材料不论受有几向应力,只要其中最大的一向主应力(即第一主应力σ1)达到材料在简单拉伸(或压缩)被破坏时的极限数值σo时,它就开始破坏,而其他两个方向的主应力则不起作用。
因此,按第一强度理论校核气瓶的强度是否足够时,只要设法求出气瓶内部的最大主应力,并测试出材料的极限应力σo就够了。
第一强度理论的一般表达式为:
(二)第二强度理论(最大主应变理论)
最大主应变理论认为材料的破坏不决定于最大的主应力,而决定于最大主应变,即某二材料不论它的受力状态如何,只要其中一个方向的单位伸长或缩短达到该气瓶材料在单向拉压而破坏的相应数值εo时,它就开始破坏,因此,按第二强度理论设计时,应使:
对于气瓶筒体:
(三)第三强度理论(最大剪应力理论)
最大剪应力理论认为材料破坏的主要原因是剪应力,不管材料受力状态如何,只要最大剪应力达到该材料在单向拉压破坏时的剪应力数值i,材料就开始破坏.按照第三强度理论,强度检验的,条件不是最大正应力,而是最大剪应力,即;
此式与(4.8)式相同,因此,在第三主应力口σ3=0的特定情况下,最大剪应力理论的强度条件表达式与最大主应力理论的强度条件表达式在形式上是一致的。
但是,对破坏原因的解释是不同的。
前者认为是最大剪应力i最大大引起的,而后者则认为是最大主应力σ1起作用。
(四)第四强度理论(最大变形能理论)
最大变形能理论,或简称能量理论认为材料的破坏并不决定于单独的应力或应变,而是决定于它的综合,即决定于改变其形状的单位体积的变形能。
材料在三向受力状态下单位体积的变形能为
由上可知,各种强度理论对材料破坏原因的解释是各不相同,它的适应范围也不同。
一般认为第一强度理论只对脆性材料在拉伸情况下与实验结果比较符合;第二强度理论对脆性材料的实验结果比较一致,第三强度理论则和实验结果相当接近,特别对塑性材料,且偏于安全;第四强度理论也得到塑性材料实验结果的证实。
但是,所有强度理论也各有缺点和矛盾,实际上也很难找到一种强度理论它能适应所有的材料、各种不同的应力状态和破坏形式。
对于气瓶筒体这一特定构件的应力状态来说,当采用第一和第三强度理论时,其结果是一致的,第二和第四强度理论结果只是很接近的。
目前在气瓶设计或压力容器设计中用得最多的是第一或第三强度理论公式。
即:
对实际气瓶一度曾考虑腐蚀裕度,焊接气瓶还要考虑焊缝对简体的削弱,因此
如果气瓶的公称工作压力尹用p表示,材料的许用应力[σ]则以kgf/mm2表示,壁厚S、内径Di、外径Do,以及腐蚀裕度C均以mm2表示,则上式应为
这就是1979年颁布的《气瓶安全监察规程》(以下简称《79瓶规》)中气瓶筒体最小壁厚的计算公式。
1985年4月22日我国同时发布,GB5099—85钢质无缝气瓶和GB5100一85钢质焊接气瓶;1986年2月6日公布了GB5824—86液化石油气钢瓶。
为了使我国气瓶有利于扩大出口,同时公制单位改为法定计量单位。
为此,简体壁厚计算公式均等效采用下ISO的计算式
(用于新制焊接气瓶筒体最小壁厚的计算公式)
(用于无缝气瓶筒体最小壁厚的计算公式)
公式中ph为水压试验压力,单位为MPa,符合国际上公式的传统。
同时也解决了采用4.14和4.14,公式进行气瓶设计,在使用中长期以采存在的气瓶最高工作压力超过气瓶设计压力的矛盾。
水压试验压力为公称工作压力的1.5倍。
为了方便设计,标准中以表的形式,列出了常用气体的公称工作压力及充装系数,表中未列的气体如需要装瓶时,其公称工作压力或充装系数则采用该气体在60℃时的饱和蒸气压来设计。
计算低压液化气体充装系数时,还应考虑留有2%的安全空间。
4.15式同时适用钢质焊接气瓶和液化石油气钢瓶,如设计溶解乙炔气瓶时,4.15式中的ph=5.2MPa,这是因为如采用GB5100的pn=5.88MPa(60kgf/cm2G)计算简体壁厚时,其最小壁厚比按ISO3807溶解乙炔气瓶基本要求的设计最小壁厚大11%以上,这无疑增加了钢材的消耗,减少了乙炔气瓶的有效装载率(乙炔充装量与乙炔气瓶总重的百分比)。
4.15'公式中的σe为屈服应力,单位为N/mm2,是指在材料试件拉伸试验时,呈明显屈服现象的,取屈服点或下屈服点:
无明显屈服现象时取规定残余伸长应力(σro.2)。
公式中采用了对屈服应力(屈服点σs)取安全系数的方法,有利于气瓶制造厂采用新材料和新工艺。
提高经济效益。
但为了防止片面追求屈服应力(屈服点),减薄钢瓶简体壁厚,降低钢瓶的安全储备,标准中对气瓶主体材料的屈强比也作了规定。
ISO气瓶标准,以及英国、西德、法国等国的气瓶标准,其简体壁厚计算公式也都是第一或第三强度理论公式,只是表示符号、所用单位不同,因此公式的具体形式略有差异而已。
日本JISB8241—1976,美国ICC一3A,以及意大利、加拿大等国标准使用巴赫公式计算简体壁厚,实际上它是以第二强度理论为基础的,采用厚壁圆筒公式进行计算的,因此,所得公式与式(4.9)有所不同。
按最大主应变理论:
σ当=σ1-μ(σ2+σ3)≤[σ].
这就是日本工业标准JISB8241—1976钢质无缝气瓶简体最小壁厚的计算公式。
我国1961年颁布《气瓶安气管理规定》(试行)(以下简称《61规定》,以及1965年修订公布的《气瓶安全监察规程》(以下简称《65瓶规》)所用的简体最小壁厚计算公式都是以第四强度理论为基础的。
参照式(4.14)的推导方法,可由第四强度理论的强度条件表达式(4.11)直接推得:
(《61规定》及《65瓶规》中内径以Do表示,《79瓶规》则以D。
表示外径,同一符号含义不同)。
气瓶简体壁厚的计算公式由原规程的第四强度理论公式改为第三强度理论公式主要是考虑:
从国内外的气瓶及压力容器的试验结果看,试验所得的屈服压力及爆破压力比较接近于第三强度理论推导的计算值,并略偏安全。
破坏形式也符合第三强度理论的假设,而按第四强度理论计算所得的屈服压力以及爆破压力则偏大约10%,实际达不到。
目前国内外压力容器及锅炉规范都趋向于采用第三强度理论公式。
ISO气瓶标准,亦采用第三强度理论公式。
(国外有些原来按第四强度理论公式计算的规定现在也改用第三强度理论公式了)。
因此,气瓶简体壁厚计算公式的这一修改是合理的。
和国外气瓶规范相比,各国气瓶设计目前仍按弹性失效准则设计,这是相同的。
但强度设计公式中压力参数多数国家采用试验压力,并按在试验压力下的应力水平不超过σs/NS(较多)或σb/Nb(较少)进行控制,并通过对不同热处理状态限制一定的σs/σb数值,以达到按抗拉强度与屈服应力共同控制许用应力的目的。
式中:
s——瓶壁许用应力;
p——水压试验压力,对压缩气体为工作压力的5/3倍;
d,D——简体内、外直径。
前已说明,此式是以第二强度理论为基础的,并采用厚壁圆筒公式计算壁厚。
此公式本身偏不安全,与第一、第三强度理论的计算公式相比,相差约17—18%左右。
JIS标准对瓶体在水压试验压力下的许用应力是按气瓶的种类(根据所用材料及热处理方法分类)分别确定的。
例如,对正火处理的锰钢气瓶取5/9σ(相当于nb=1.8),为了避免片面提高σs,因此对正火处理的锰钢限定σs≯0.75σb。
(即使实际上已达到或超过,也只能按σs≤0.75σb取)因此在试验压力下的许用应力为σr≤0.75σs如按公称工作压力计算,则nb=1.8×5/3=3.0,ns≤3.0×0.75=2.25,采用在试验压力下各种气瓶规定的瓶体许用应力及由此推算求出的在试验压力、工作压力下的nb、ns。
,以及如按第一、第三强度理论公式计算时,在工作压力下相应的nb、ns列于表4—3。
表4-3
标准规定:
设计气瓶时,选用σs值,对正火处理气瓶σs≯0.75σb对淬火十回火处理的σs≯0.85σb,这里是分别按0.75及0.85计算的。
焊缝是影响焊接气瓶质量比较关键的因素,也是气瓶强度的薄弱环节,尤其是纵向焊缝。
焊缝(包括热影响区)强度的降低一方面是由于在焊接时可能出现缺陷。
如气孔、夹渣、未焊透、未熔合、裂纹等,另一方面则是焊接过程中可能使焊缝边缘晶粒长大,热影响区被淬硬,塑性降低,以及引起内应力等。
所以焊缝系数的大小不但与焊缝结构和焊接工艺(包括焊后是否进行消除残余应力热处理等)有关,而且还与焊缝的检验方法及受检程度有关。
《79瓶规》规定根据焊接形式及检查等级选取焊缝系数,这是参照我国有关焊接标准和容器设计规定确定的,并无特殊考虑。
焊接气瓶的焊缝系数如下表:
表4-4
焊接型式
焊缝系数
全部无损探伤检查
局部无损探伤检查
双面对接焊缝
1.0
0.9
有垫板的单面对焊接缝
0.9
0.8
GB5100—85和GB5842—86两项标准,针对焊接型式较为单一的现实情况,只规定根据无损探伤等级选取ω值。
即纵环焊缝全部射线照相检验的ω取1,对于只有一条环焊缝按生产顺序每50只抽取一只进行焊缝全长的射线照相检验的甲取0.9,对于有一条纵焊缝,两条环焊缝的,每只钢瓶应进行不少于其纵、环焊缝总长的20%的射线照相检验,这样钢瓶的焊缝系数也取0.9。
进行强度核算时,气瓶简体最小壁厚应是不包括制造工艺造成的减薄量或管材、板材的负偏差的,这是与一般压力容器相同的。
但腐蚀裕度在钢质无缝气瓶,钢质焊接气瓶,液化石油气钢瓶三项气瓶国标中均取消了。
气瓶的介质腐蚀是实际存在的,腐蚀程度与介质及气瓶材料等因素有关。
我国以及许多国外气瓶设计标准(规程)中未另加腐蚀裕度,这是因为腐蚀裕度已在安全系数中包括进去了,可以不必再加的缘故。
考虑各种气体标准对含水量均有严格规定,含水超标属暂时非正常状态,况且国标采用了ISO壁厚计算式后,对于目前国内锰钢气瓶、壁厚比加腐蚀裕度的《?
9瓶规》计算结果还需增加0.2~0.4mm,因此c值也就没有必要存在了。
三、气瓶筒体屈服压力和爆破压力的计算
简体是气瓶的主体,因此气瓶封头和瓶底的强度应等于或略大于筒体,以便充分利用筒体材料的强度,所以气瓶的屈服压力及爆破压力实际上就是简体的屈服压力及爆破压力。
根据弹性失效准则,气瓶筒体屈服就意味着气瓶失效。
水压试验中测定残余变形率的目的就是以此来判定气瓶是否已经产生屈服,并进而确定气瓶仍可继续使用或需降级、报废。
但是从气瓶失效所造成的后果看,即从安全的角度看,爆破压力具有更重要的意义。
气瓶简体受内压后内壁应力较外壁为大,所以当内压力升到某一数值时,内壁表层材料首先开始屈服,这个压力叫做简体的屈服压力。
但此时简体外壁尚处于弹性状态,尚未达到屈服的外层弹性区域将阻止内壁的塑性变形。
因此简体也还有继续承受内压的能力。
当内压继续增加时,已经屈服的内层材料由于塑性流动不能承受这种继续增加的外载,得由外层弹性区来承受,并使塑性区逐渐由内向外扩展,而外层弹性区则逐渐缩小。
当内压增至某一值时,简体外表面也达到屈服,这个使简体整个壁厚达到屈服的压力称为简体的极限压力。
整体屈服后材料不会无限制地塑性流动,而只有继续增大内压,克服整体屈服后塑性强化的能力,才能使筒体继续变形,直到最后破坏,因此,对气瓶材料的简体,在整体屈服以后尚有一定的承受内压的能力。
因此气瓶爆破时的压力——进水量曲线与材料试验时的拉伸曲线也相类似。
既然简体屈服压力是指筒体内壁表层材料开始出现屈服时所能承受的压力,此时简体整个壁厚尚处于弹性变形状态(或者说是弹性状态的结束和弹——塑状态的开始)。
因此屈服压力仍可以用弹性理论为基础的公式进行计算,即取内壁的当量应力和等于材料的屈服应力,以此作为计算屈服压力的条件。
而简体的极限压力或整体屈服压力则是指简体外壁也达到屈服时所能承受的压力。
这时简体已全部进入塑性状态。
因此极限压力要比屈服压力为高,而且由于筒体内部不仅出现应力的重新分布,对非理想塑性的气瓶材料还有塑性强化,所以原则上就不能采用弹性理论公式了。
但是对于薄壁圆筒,既然已经假定应力沿壁厚是均匀分布的,即内外壁应力甚为接近,因此极限压力和屈服压力实际上很接近(这个压力就是通常所说的气瓶简体屈服压力或整体屈服压力)。
所以,对于薄壁圆筒仍可以认为当简体强度理论表达式(4.8)~(4.11)中的当量应力达到材料屈服应力时,筒壁就整体屈服,与此相应的压力就是筒体的屈服压力,即按第一强度理论计算:
当筒体壁厚较小时,即k≤1.5时,上述公式(4.26)、(4.27)即可近似地简化为公式(4.18)及(4.21)的形式。
如前所说,非理想塑性的气瓶材料简体的爆破是筒壁塑性变形不断发展的结果。
由于要考虑塑性强化的影响。
因此爆破压力的理论计算比较复杂,作为工程计算,对于薄壁圆筒也可以筒体强度理论表达式为基础.近似地认为当简体的当量应力达到抗拉强度时,筒体即导致爆破,因此:
由于第一和第二强度理论一般只适用于脆性材料,所以计算塑性材料筒体的屈服压力及爆破压力原则上只有第三强度理论和第四强度理论才能适用。
有些作者以式(4.26)或(4.27)为基础,考虑塑性强化或不同屈强比对爆破压力的影响,进行了一定的修正,提出