材料成型设备作业.docx
《材料成型设备作业.docx》由会员分享,可在线阅读,更多相关《材料成型设备作业.docx(13页珍藏版)》请在冰豆网上搜索。
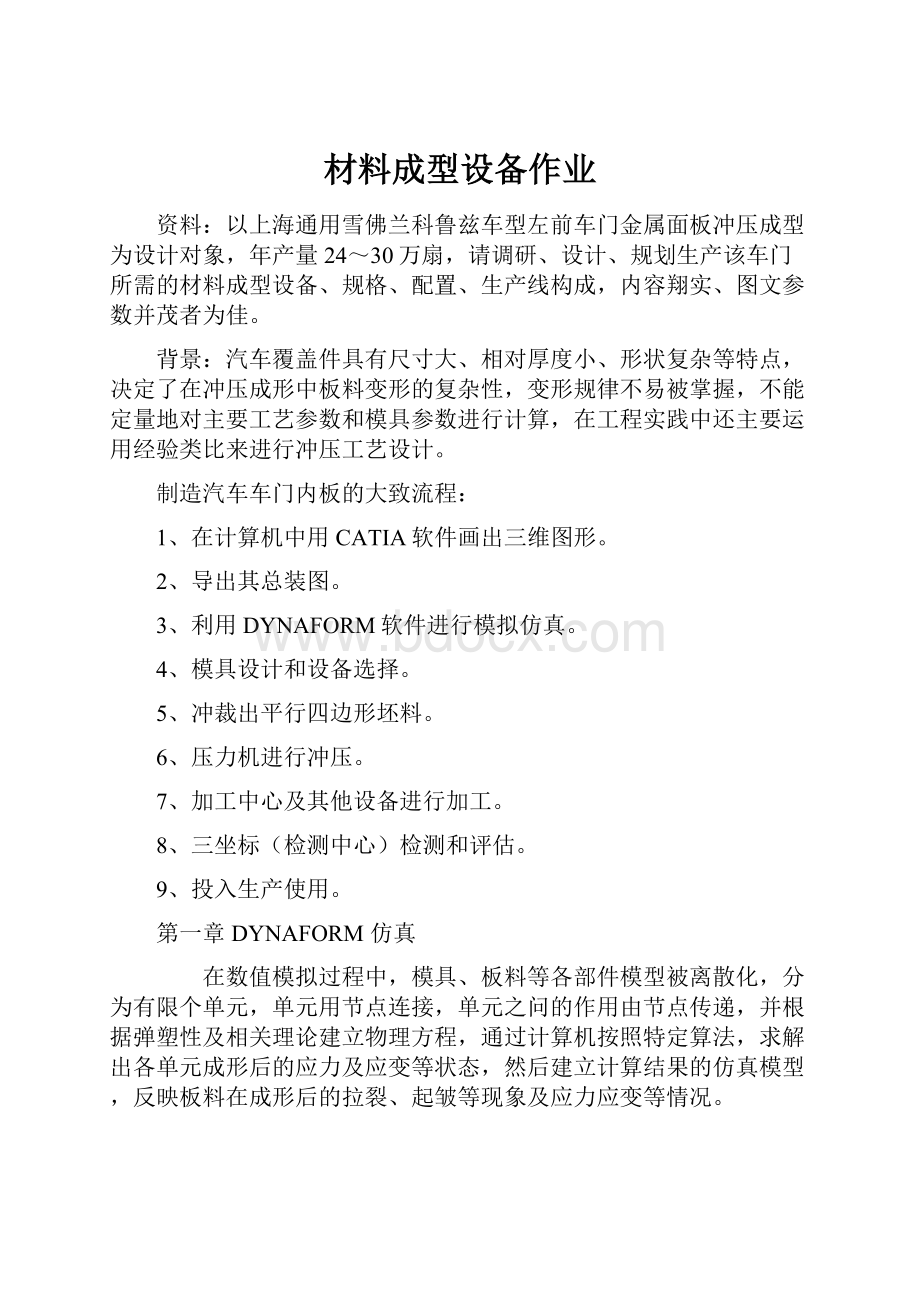
材料成型设备作业
资料:
以上海通用雪佛兰科鲁兹车型左前车门金属面板冲压成型为设计对象,年产量24~30万扇,请调研、设计、规划生产该车门所需的材料成型设备、规格、配置、生产线构成,内容翔实、图文参数并茂者为佳。
背景:
汽车覆盖件具有尺寸大、相对厚度小、形状复杂等特点,决定了在冲压成形中板料变形的复杂性,变形规律不易被掌握,不能定量地对主要工艺参数和模具参数进行计算,在工程实践中还主要运用经验类比来进行冲压工艺设计。
制造汽车车门内板的大致流程:
1、在计算机中用CATIA软件画出三维图形。
2、导出其总装图。
3、利用DYNAFORM软件进行模拟仿真。
4、模具设计和设备选择。
5、冲裁出平行四边形坯料。
6、压力机进行冲压。
7、加工中心及其他设备进行加工。
8、三坐标(检测中心)检测和评估。
9、投入生产使用。
第一章DYNAFORM仿真
在数值模拟过程中,模具、板料等各部件模型被离散化,分为有限个单元,单元用节点连接,单元之问的作用由节点传递,并根据弹塑性及相关理论建立物理方程,通过计算机按照特定算法,求解出各单元成形后的应力及应变等状态,然后建立计算结果的仿真模型,反映板料在成形后的拉裂、起皱等现象及应力应变等情况。
图1拉延成形极限图
在DYNAFORM的实际应用中,计算结果的仿真模型是确定合理的工艺参数,指导模具设计的依据。
因此,计算结果的准确性是数值模拟技术的首要问题。
而计算结果的准确性主要是由有限元模型的准确性决定的。
有限元建模过程包括选择适当的网格单元对几何模型进行离散化,以获得有限元网格模型;以合理的方式获得仿真分析中准确的材料参数、摩擦润滑参数、工艺条件和各种约束条件等,建立一个可直接用于仿真计算的完整有限元模型其中,有限元网格质量是决定计算效率和计算精度的主要因素。
网格单元小则结果精确,但单元数目越多计算量越大,浪费计算时间;网格尺寸大则计算量小,但误差较大,不能真实反映模型特征。
在实际应用中,根据模具与板料在数值模拟中的不同特点,板料网格尺寸的大小应在满足精度要求的前提下尽量大,并尽可能采用自适应网格划分。
图1为其DYNAFORM仿真图。
第二章冲压成形工艺分析
一、冲压工艺制定
1.零件工艺分析
图2车门内板零件图
图2中的a和b处,由于窗框部分进行内工艺补充后,形成了零件的反成形形状,这部分形状的成形一般不能靠外部材料进行补充,只能靠该部分板料的胀形成形来实现,胀形成形深度较深,a和b处大约有20mm左右,且转角部R较小,因此在拉延成形过程中很容易出现破裂。
在零件的c处,存在大约12mm高的台阶,此部分若在第一次拉延过程中直接成形,则压料面可能有以下两种分法:
(1)将c部分作为压边面的一部分,即将分模线分在零件侧壁圆角处,这样由于台阶对板料的进料阻力较大,易导致零件在拉延过程中可能产生破裂;
(2)将c部分作为凸模的一部分,即将分模线分在c部分外侧的法兰上,则在拉延过程中该区域的板料是悬空的,在径向拉应力和切向压应力的作用下,材料集中收缩到此处,可能导致零件的该部分起皱,甚至有迭料的可能。
由上面的工艺分析可知,该覆盖件成形难度大,成形工艺较复杂。
2.工艺方案的制定
产品冲压成形工艺的确定过程,就是分析和预测板料在变形过程中可能产生的缺陷,并采取一定的措施,以消除和防止冲压缺陷,同时考虑制造能力、冲压设备、投资成本等因素。
根据本零件的工艺性和本身的结构特点,结合实际生产情况,车门内板的工艺过程如下:
拉延+切角;二次拉延+切边+冲孔;切边+冲孔;侧切+侧冲孔翻孔+冲孔+整形;整形+冲孔。
(1)拉延工序工艺方案的制定
拉延工序是覆盖件冲压成形的关键工序,覆盖件的大部分形状是在此工序形成的,拉延成形的好坏将直接影响覆盖件质量。
该工序一方面将成形出零件的大部分形状,同时在拉延过程中还将对坯料进行切角,减少落料模具,降低成本。
结合零件的工艺性,在拉延工序中对零件的某些部分作如下处理:
在零件的a和b处可采取以下方式来消除破裂:
第一方案,增大a和b处的相应模具圆角,以减小材料流动阻力,后工序再对相应部分作整形;第二方案,利用在窗框的适当部位冲切工艺切口的方法,使容易破裂的区域从相邻区域里得到材料补充,从而改善该区域的变形情况,避免破裂的产生。
在零件的C处,为了避免一次拉延可能产生的缺陷,考虑作二次拉延,从而降低第一次拉延的难度,如图3中的局部视图F所示。
拉延工序工艺的制定包括拉深方向的选择、工艺补充和压料面的设计等。
选择合理的拉延方向应考虑以下原则:
(1)保证能将拉延件的全部空间形状一次拉出来,不产生负角;
(2)尽量使拉深深度浅且均匀;(3)保证凸模有良好的接触状态;(4)有利于防止表面缺陷;(5)同时要考虑后工序内容和模具结构。
综上所述,结合车门内板本身特点,拉延工序的冲压方向如图3所示。
合理的压料面形状应遵循以下几个主要设计原则:
(1)压料面的形状应尽量简单;
(2)在拉延过程中压料面任一断面的展开长度要小于拉延件内部相应断面的长度;(3)压料面应使成形深度小且各部分深度接近一致。
结合本零件的特点,压料面沿零件四周的变化趋势顺延成曲面,如图3所示。
在进行工艺补充时,应主要考虑以下几个原则:
(1)尽量简化拉延件结构形状;
(2)工艺补充部分尽量小,以提高材料利用率,降低成本;(3)对后工序有利原则,如定位、修边等。
根据以上原则,结合本零件的本身特点,工艺补充简图如图3所示。
如局部视图F所示,为了降低拉延的难度,避免拉延过程中产生缺陷,将如图2的C部分分两次成形。
由于后工序全部有冲孔动作,出于模具结构简单化的目的考虑,窗框型面部分采用向下整形,并保证合适的切边角度,窗框型面部分的工艺补充如图3的局部视图I所示,并将侧壁作了8°的拔模角,如局部视图E所示。
其余部分顺着产品延伸出来。
图3拉延工序及工艺补充简图
(2)其余工序工艺方案
该覆盖件部分孔和其他大部分孔的方向相差约10°,并且考虑到窗框型面弧度变化,第一工序和第二工序的冲压方向相同,后工序冲压方向与之相差10度,现将后工序进行简单介绍。
工序二,二次拉延+切边+冲孔,如图4a所示,该工序对如图2所示的C部分进行二次拉延,局部区域进行整形,切边时考虑了窗框内废料较大,将其分三块切掉,出于模具结构强度的原因本工序切出两端的两块。
工序三:
切边+冲孔,如图4b所示,将余下全周进行切边,同时冲出部分孔。
工序四:
侧切+侧冲孔翻孔+冲孔+整形,如图4c所示,窗框内边整形,侧向门锁安装孔在此工序全部完成,如SECA-A所示,此部分内容的完成也是模具结构的难点,采用双动斜楔机构。
工序五:
整形+冲孔,如图4d所示,全周法兰边整形,冲切余下孔,因为零件的法兰边要与外板进行扣合,法兰边的平展度将直接影响扣合的质量,故在此工序安排了法兰边全周的整形。
2ndDR—二次拉延;TR—切边;PI—冲孔;RST—整形;CAMTR—侧切;
CAMPI/RST—侧冲孔/翻边;FL—翻边。
图4后工序简图
三、车门内板材料和拉延数值分析
将各单元集分别定义为凹、凸模、板料和压边圈。
设置好模具、板料和压边圈之间的相对位置,并定义它们之间的接触类型、参数和运动曲线,设置必要的工艺参数。
图5实际拉延的零件
本车门材料选用材料库中的St14,料厚0.8mm。
分析材料厚度为0.8mm,考虑到材料利用,坯料设计为平行四边形,如图3所示。
材料St14,其弹性模量E=2.07×105MPa,泊松比为0.28,屈服强度σ=165MPa,各向异性指数r-0=1.87,各向异性指数r-45=1.27,各向异性指数r-90:
2.17,硬化指数n=0.2,摩擦系数为0.125,压边力为80t。
分析所得成形极限图如图1所示,由图可以看出零件拉延成形比较充分,零件部分无明显的起皱,但在窗框部分由于胀形成形深度较深而出现了破裂,即如图2的a和b处,在生产中可通过增大模具相应圆角和冲切工艺切口的方法来消除。
在试模过程中,为了降低成本,应优先考虑方案一,即通过增大模具圆角来消除破裂。
图5为实际拉延成形的零件。
第三章车门加工流水线
因为该产品属于大批量生产。
生产处理要长期处于稳定状态,形状改变可能性小,工艺难易程度困难,工艺方案要为流水线提供保证,每道工序都要使用冲模,拉延、修边冲孔和翻边模同时安装在一条冲压线上,工序间的流转,故采用全自动化加工生产。
现采用多工位压床,更加提高了生产效率和工件质量。
在冲压生产线上,一般都配有各种送料装置、取件装置、翻转装置、废料排除装置和传送带。
机器人控制冲压生产线。
压力机以单次行程规范工作,由自动化系统控制着生产线上各台压力机在什么时候冲压和各工序间的工件运动。
从整条生产线上传出的工件是按一定的节拍连续不断地运动,从而明显地提高了生产产量。
该系统还可以保证工件表面的高质量要求,大幅度减少压力操作人员,解决了安全及下料的难题,最大限度地提高了设备利用率。
第四章车门冲压成形设备
根据以上本零件的工艺性和本身的结构特点,结合实际生产情况,车门内板的工艺过程为:
拉延+切角;二次拉延+切边+冲孔;切边+冲孔;侧切+侧冲孔+翻边+冲孔+整形;整形+冲孔。
设备的选择参考《中国模具设计大典:
第三卷冲压模具设计》,第八章,汽车覆盖件冲压工艺设计:
选择冲压设备是冲压工艺设计的一项重要内容,应根据冲压零件的具体情况进行选择。
双动压力机具有行程大、压边力稳定且容易调整等特点,故覆盖件的拉深成形一般选用双动压力机。
对相对较小的零件也可选用单动压力机。
在选择双动压力机是,主要从以下几方面考虑。
1)根据工艺人员的经验估测出所需成形力,拉深成形所需的拉深力要小于双动压力机的内滑块公称力。
2)估测拉深成形所需压边力,拉深成形所需的压边力要小于外滑块公称力。
3)工作台面尺寸应大于模具外形尺寸,能方便地安装模具。
4)闭合高度、滑块行程、气垫行程及气垫压力等的确定与一般冲压工艺的设计原则相同。
在选用单动压力机是,主要考虑工作台面尺寸、闭合高度、滑块行程、气垫行程及气垫压力等。
其确定方法与一般冲压工艺设计的原则相同。
选择翻边冲压设备是,首先选择设备的台面尺寸。
因为翻边时所需的翻边力相对不大,一般只要设备的台面尺寸能够安装翻边模具,设备的能力就能满足翻边要求,可以不进行翻边力的计算。
但在水平或倾斜翻边时,要把翻边方向的行程换算成压力机滑块运动方向的行程,作为选择设备行程的依据。
同时,设备的最大闭合高度要大于(模具高度+10mm)
修边冲压设备采用单动压力机。
选择压力机参数时,首先选择设备的台面尺寸。
因为修边时所需的冲裁力相对不大,一般只要设备的台面尺寸能够安装修边模具,设备的冲裁力就能满足修边要求,可以不进行冲裁力的计算。
在水平或倾斜修边时,要把修边方向的行程换算成压力机滑块运动方向的行程,作为选择设备行程的依据。
同时,设备的最大闭合高度要大于(模具高度+10mm)
参考以上原则,选择的设备如下:
1、冲压:
JH36-630压力机。
2、修边:
J36-160B压力机
3、拉延:
双动薄板拉延液压机。
4、冲孔:
数控平板冲孔机。
5、其它:
加工中心、机械人等。
详细参数如下:
JH36-630压力机参数
序号
项目
单位
规格
JH36-630
1
公称力
kN
6300
2
公称力行程
mm
13
3
滑块行程次数
次/分
14
4
滑块行程长度
mm
500
5
最大装模高度
mm
1000
6
装模高度调节量
mm
500
7
立柱间距
mm
4350
8
工作台面尺寸
左右×前后
mm×mm
4000×1800
工作台板厚度
mm
220
工作台高度
mm
650
移出形式
前移约2500
载重量
T
20
9
滑块面积
左右×前后
mm×mm
4000×1800
10
气垫
气垫力
KN
1200
形式
单顶冠
行程
mm
15-240
11
滑块打料
形式
刚性
打料力
KN
50×8
行程
mm
180
12
主电机
功率
KW
75
转速
r/min
1500
13
装模高度
调整电机
功率
KW
5.5
转速
r/min
1500
JH36-630压力机:
J36-160B压力机:
公称力(kN)
1600
压力行程(mm)
10.8
滑块行程(mm)
315
滑块行程次数(r/min)
20
最大闭合高度(mm)
670
闭合高度/调节量(mm)
250
导轨间距离(mm)
1820
滑块地面前后尺寸(mm)
1050
工作台面尺寸(mm)
左右
2000
前后
1250
YH28系列双动薄板拉伸液压机
性能特点:
•德国引进技术,计算机优化设计,具有国际先进水平。
•框架式拉杆预紧结构,刚性好;四柱式结构简单、经济、实用。
•四角八面导轨,导向精度高,抗偏载能力强;
•新型油缸密封元件,可靠性高,寿命长。
•移动工作台,方便模具更换。
•压边滑块四角调压,易于不对称零件拉抻。
•拉伸、压边滑块可通过定位销联为一体,实现单动工艺动作。
•机、电、液一体化安全装置,如油缸下腔支承回路、油缸上下腔互锁回路等,安全性优越。
•采用PLC控制,工作灵敏可靠,柔性好。
第五章结束语
图6实际生产零件
这里的车门内板是典型的汽车覆盖件,用计算机进行仿真模拟,预测了拉延过程中可能出现的缺陷,为模具设计提供了指导,减少了模具试模次数,有效降低了设计和制造成本,缩短了生产周期,所生产的制件质量高,提高了企业的市场竞争力。
图6为按本工艺所生产的零件。