齐鲁石化催化操作规程.docx
《齐鲁石化催化操作规程.docx》由会员分享,可在线阅读,更多相关《齐鲁石化催化操作规程.docx(118页珍藏版)》请在冰豆网上搜索。
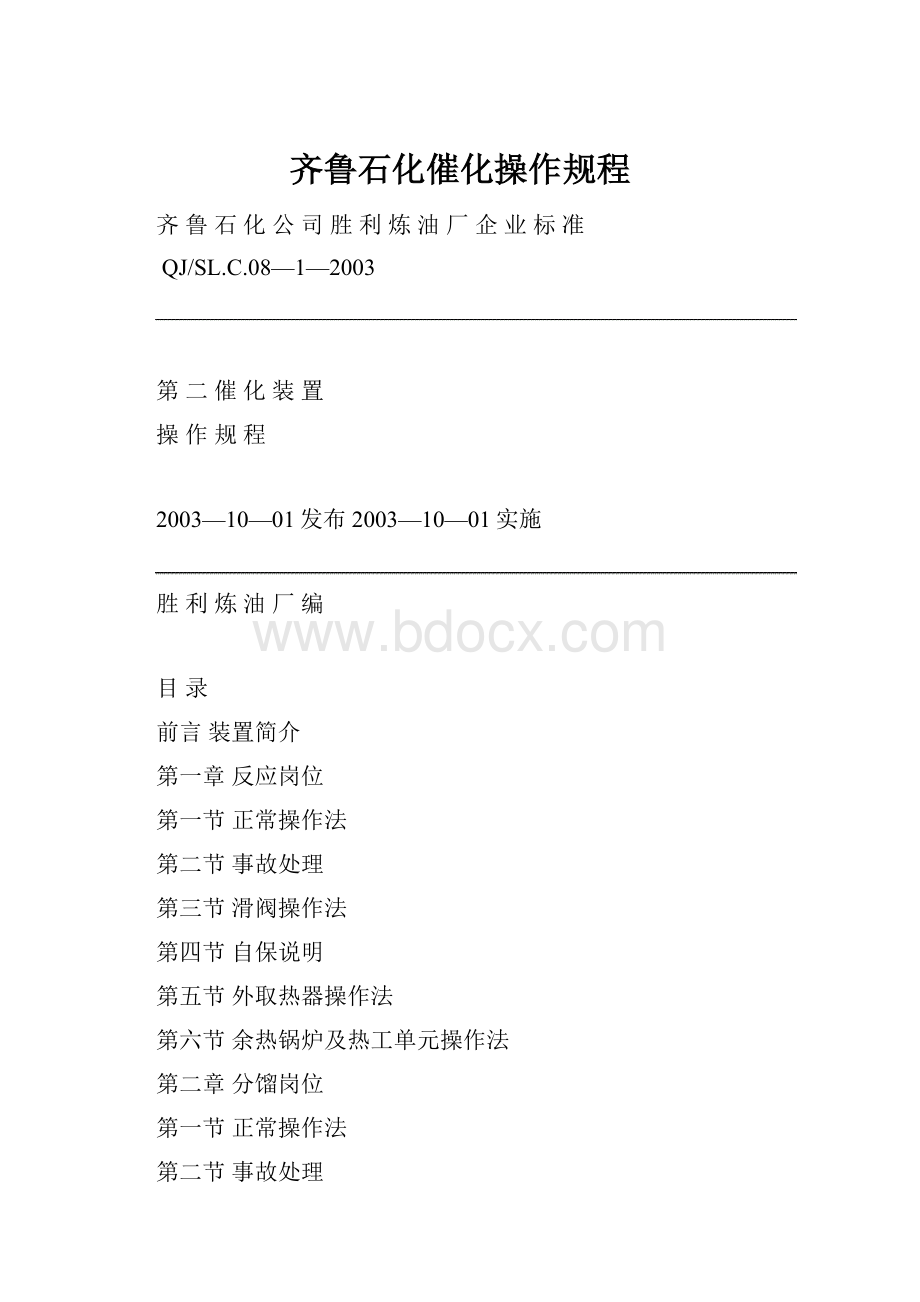
齐鲁石化催化操作规程
齐鲁石化公司胜利炼油厂企业标准
QJ/SL.C.08—1—2003
第二催化装置
操作规程
2003—10—01发布2003—10—01实施
胜利炼油厂编
目录
前言装置简介
第一章反应岗位
第一节正常操作法
第二节事故处理
第三节滑阀操作法
第四节自保说明
第五节外取热器操作法
第六节余热锅炉及热工单元操作法
第二章分馏岗位
第一节正常操作法
第二节事故处理
附分馏塔总图
第三章稳脱岗位
第一节稳定单元正常操作法
第二节脱硫单元正常操作法
第三节稳脱单元事故处理
附录装置仪表参数汇总
简介
工艺流程简要说明
反应-再生部分
装置新鲜进料一部分由罐区送入,一部分由泵404/1,2抽入与罐区送入的原料经管道混合一并至装置容203。
由原料油泵201/1,2原料-一中换热器(换201/5,6)换热至140℃,然后进入原料-油浆换热器(换201/1-4)升温至180-240℃进入提升管。
提升管自下而上设有原料油喷嘴、回炼油喷嘴、油浆喷嘴、终止剂喷嘴。
各进料油在高效喷嘴混合室内和雾化蒸汽混合后,被雾化成小油滴进入提升管。
提升管底部设有汽油回炼分布器,在分布器中,汽油和蒸汽混合后经喷淋式喷头进入提升管。
回炼的稳定汽油或粗汽油约6~10吨/小时与来自再生器(塔102)的高温催化剂(~700℃)接触后立即汽化,发生高温短接触时间迭合反应。
保持中等密度的催化剂沿提升管匀速上升。
雾化后的新鲜原料油与之接触,立即汽化、反应,产生的反应油气携带催化剂以活塞流沿提升管向上流动,为控制反应温度,在提升管中部分别注入回炼油、回炼油浆、提升管上部注入终止剂。
在提升管出口设有粗旋,使催化剂与油气迅速分离,减少二次反应。
提升管出口温度为500-510℃,油气及携带的少量催化剂经3组单级旋风分离器,分离出来的油气去分馏塔。
回收下来的催化剂经料腿流入汽提段上部,向下与汽提蒸逆流接触,脱除催化剂上吸附的油气。
汽提段设有8层盘形挡板,为确保催化剂与汽提蒸汽良好接触,本次改造在汽提段增加汽提蒸汽分布环,分层汽提。
脱除绝大部分油气的催化剂通过待生斜管进入烧焦罐内进行高效、快速烧焦。
在再生器中,催化剂分为三路:
一路经再生斜管进入提升管反应器,完成反再系统的催化剂循环,该路催化剂循环量的大小,由提升管出口温度控制再生滑阀的开度进行控制。
一路经外取热上斜管进入外取热器,降温后的催化剂通过外取热下斜管返回烧焦罐,该路催化剂循环量,由烧焦罐床层温度控制外取热下滑阀的开度进行控制。
另一路,经循环斜管、滑阀进入烧焦罐,以提高烧焦罐内的起始温度。
再生烟气经再生器内6组两级旋风分离器回收烟气携带的催化剂细粉后,进入三旋。
为维持两器热平衡,增加操作灵活性,在再生器旁设置可调热量的外取热器,由再生器床层引出高温催化剂(700℃)流入外取热器后,经取热列管间自上向下流动,取热管浸没在流化床内,管内走水,取热器底部通人流化空气增压风以维持良好流化,造成流化催化剂对直立浸没管的良好传热,经换热后的催化剂温降100℃左右,通过斜管及外取热器下滑阀流入烧焦罐。
外取热器用的脱氧水自余热锅炉来,进入汽包,与外取热器换热出来的汽-水混合物混合,传热并进行汽、液分离后产生的4.3MPA(表)饱和蒸汽送至余热锅炉过热,并入装置中压蒸汽管网。
汽包中的饱和水由循环热水泵101/1~3抽出,形成强制循环,进入外取热器取热管。
再生器和烧焦罐烧焦用的主风由主风机供给,主风机出口分出一股主风经增压机升压后(0.42MPA(表)流量200立方米/分钟),作为外取热器流化风。
因调节取热量需要,同时满足增压防喘振的需要,增压风过剩时,可将部分增压风并入主风管线。
自动控制部分
再生器操作压力由三旋后的烟气双动滑阀或烟机入口蝶阀控制。
提升管出口温度由再生滑阀控制。
待生滑阀用来控制汽提段催化剂料位高度,要求保证最低料位高度以确保良好的汽提,同时也要防止料位过高,而使催化剂从料腿中重新被携带。
再生器床层料位由循环滑阀控制,但在料位规定范围内可以不加控制,只要严密监视。
烧焦罐温度可调节外取热器下滑阀开度或调节外取热器流化风量来调整取热量,使进入烧焦罐的催化剂流量或温度变化,从而控制了烧焦罐温度。
开工用新鲜及平衡催化剂由汽车从厂内仓库运送至装置内新鲜催化剂储罐和平衡剂催化剂储罐,用系统来的非净化风(压力0.5MPA(表)温度40℃)输送至再生器和烧焦罐,正常补充催化剂用小型加料,用非净化风送到再生器。
为保持催化剂比表面和重金属含量不超过允许值需从再生器定期卸出催化剂至废催化剂罐。
废催化剂储罐考虑了催化剂卸除装运设施。
钝化剂系统为桶装的钝化剂溶液用泵抽至钝化剂罐,然后由钝化剂注入泵压送至提升管进料总管与原料油混合后进入提升管进料喷嘴。
钝化剂用轻柴油稀释,轻柴油与钝化剂比例按10:
1考虑。
由反应沉降器出来的反应油气进入分馏塔(塔-201)
烟气能量回收系统
来自再生器的具有压力的高温(670℃)含催化剂(1克/标准立方米)烟气首先进入一台多管式三级旋风分离器,分离出其中大部分催化剂,使烟气中催化剂含量降到0.2克/标准立方米以下,大于10μ的颗粒基本除去,以保证烟气透平叶片常周期运转,净化了的烟气从三级旋分器出来分为两路,一路经切断闸阀和调节蝶阀轴向进入烟气透平膨胀做功,驱动主风机回收烟气中压力能,做功的烟气压力从约0.3MPA(表)降至0.108MPA(表),温度由670℃降至~503℃,经水封罐和另一旁路经双动滑阀调节放空的烟气汇合后进入余热锅炉回收烟气显热发生3.82MPA(表)420℃过热蒸汽,烟气经余热锅炉后温度下降至~200℃最后排入烟囱。
在烟气透平前的水平管道上装有高温平板闸阀及高温蝶阀,高温平板闸阀是在事故状态下紧急切断烟气进入透平之用,调节蝶阀及副线上双动滑阀具有相同功能,均可对再生器压力起调节作用。
从三旋分离出来的催化剂细粉主要是小于30μ的,连续排入细粉收集罐,然后进入细粉储罐,设计考虑在细粉储罐下方将催化剂装车外送,或回用一部分催化剂。
从三旋排出的细粉夹带约2~5%的烟气要连续从细粉收集罐顶部排出,为维持整个系统压力,从放空线上装有临界流速喷嘴,此喷嘴已接近临界状态下操作,改造后设计上考虑了耐磨措施。
此放空管为衬里管。
在烟机入口管道上,高温平板闸阀前设计一根放空线,该线是烟机未开时放空用,以防管线中积凝液腐蚀管线。
在水封罐设有常流水的小水封,作用其一是起密封作用防止烟气漏出,其二是置换酸性水的作用,因烟气与水接触后,有部分NOX、SOX溶于水,使水PH值下降而腐蚀水封罐,所以说水封罐的小水封需要常流水。
4.2分馏部分
分馏塔(塔201)共32层塔盘,塔底部装有8层人字挡板。
来自沉降器的高温油气经大油气线进入分馏塔人字挡板底部,与人字挡板顶部返回的275℃循环油浆逆流接触,油气自下而上被冷却洗涤。
油气经分馏后得到气体、粗汽油、轻柴油、回炼油、油浆,为提供足够的内部回流并使塔负荷分配均匀,分馏塔设有四个循环回流:
顶循回流、一中回流、二中回流、塔底油浆回流。
1)分馏塔顶油气
分馏塔顶油气自塔顶进入空气冷却器(空冷201/1~8)冷却至60~80℃,
再进入分馏塔顶后冷器(水冷202/1~4)冷至40℃,进入油气分离器容-201分离。
容201中的富气(40℃、0.18MPA)进入气体压缩机,冷凝的粗汽油用泵202/1,2加压后送往吸收稳定部分的吸收塔顶,分出的污水经泵213/1,2加压后分为两路,一路出装置,另一路作为急冷水去提升管。
2)顶循环回流
顶循环油自分馏塔第29层下部集油箱用泵203/1,2抽出,温度为140~160℃,首先至换203/1,2(顶循-除盐水换热器)与除盐水换热,温度降至121℃,除盐水换热后的温度为90℃左右,顶循环经空冷-203/1,2可冷至60~80℃直接返塔第32层塔盘。
冷-203/3、4(顶循环-循环水冷却器)可作为备用。
分馏塔的操作中考虑了打冷回流,当冷回流量为5350公斤/小时时,冷回流的取热量占顶循环回流取热负荷的10%,塔顶温度为114℃,塔顶压力下水蒸汽的露点温度103~108℃,温度相差5℃,能满足操作控制要求,因此在操作中应该控制冷回流的量大于5000公斤/小时。
3)轻柴油
为了多出柴油,分馏塔第17、21层开有抽出口,第17层为全抽出斗,自流至上部轻柴油汽提塔;第21层为部分抽出斗,自流至下部轻柴油汽提塔,均经水蒸汽汽提后,用泵204/1~3分别从汽提塔底部抽出,并在各抽出泵的出口装有调节阀,上汽提塔泵出口调节阀控制上汽提塔液面,下汽提塔泵出口调节阀为流量控制,两股柴油经过调节阀后合并,首先进入换-204与富吸收油换热,然后经空冷204/1,2、冷204/3,4冷却至40℃,一路作为产品出装置,另一路作为贫吸收油至再吸收塔,吸收后的富吸收油又返回经换204换热至140℃进分馏塔第18层、22层塔盘。
当不需要时,可停用第21层抽出,此时柴油收率要底一些。
4)一中系统
一中自分馏塔第13层下部抽出斗抽出,温度230~260℃,经泵205/1,2先作为解析塔底重沸器换301的热源,温度降为190℃,再去原料一中换热器换201/5,6给原料换热,温度降至171℃,后进冷206/1,2用循环水冷却至160℃返塔第16层。
由于重柴油进UFR/VRDS做稀释油组合工艺的要求,为了防止分馏塔第11、12层塔盘干板,一中从泵205/1,2出来后新增一根一中回流直接返塔线,至分馏塔第12层,作为内回流。
5)重柴油系统
根据胜利炼油厂提出重柴油进UFR/VDRS做稀释油组合工艺的要求,为了减少重柴油中的催化剂含量,重柴油自分馏塔第8、10层抽出,温度335℃,进新增的重柴油泵214/1,2,升压后至VRDS装置,为了保证输送过程中的安全,重柴油管线至冷207、冷208冷却后,再进VRDS装置。
6)二中系统
自分馏塔第三层下部集油箱自流入容202馏分,温度335~350℃,用泵207/1,2抽出后分为三路,第一路作为回炼油进提升管,第二路作为内回流直接返回分馏塔第2层,作为调节回炼油,第三路油为二中回流,做稳定塔底重沸器换303的热源,换热至250~260℃返分馏塔第5层。
7)油浆系统
循环油浆由泵208/1~3从分馏塔底抽出,温度340-350℃,一路直接进提升管回炼,另一路进换201/1~4(油浆原料换热器)换热至332.7℃,再进换202/1,2(油浆蒸汽发生器)发生4.2MPA的中压蒸汽,出口温度275℃从人字挡板上下返塔,其中分出一路油浆作为产品经冷207、冷208水箱冷却至100℃出装置。
由于掺炼渣油后,为了防止分馏塔底结焦,控制分馏塔底处于过冷状态,塔底温度不大于350℃,循环油浆上下返塔控制方案与改造前有所不同,油浆上返塔由一层板下的气相温度和流量串级控制,以保证油浆比重和洗涤催化剂,防止结焦,为此需要有足够的流量。
油浆下返塔为流量控制,维持塔底温度,防止结焦。
本次改造将油浆蒸汽发生器汽包、换热器更换,压力等级由2.5MPA更改为6.4MPA的设备,可产生4.2MPA的中压饱和蒸汽。
4.3吸收稳定部分
从分馏部分(容201)出来的富气被富气压缩机(机301)压缩至1.4~1.6MPA,压缩气体与脱吸塔顶气体混合经空冷器(空冷301/1~4)冷却至60℃,再与吸收塔底油混合,混合后用冷301/5,6冷凝冷却到40℃,进入油气分离器(容301)。
为了防止设备腐蚀,在空冷301/1~4前注入水洗水,容301分离出来的污水去容201。
吸收塔/解析塔(塔301/1,2)改造中更换。
吸收塔的操作压力为1.25~1.45MPA,操作吸收温度为46~47℃,从容301来的富气进入吸收塔下部,从分馏部分来的粗汽油及补充吸收剂分别由第27、30层和32、35层打入,与富气逆流接触。
为了取走吸收过程中放出的热量,在吸收塔中部设有2个中段回流,分别从第26层和15层用泵302/1~3抽出,分别经吸收塔中段冷却器冷302/1~4冷却至40℃,然后返回塔的第25层和14层。
吸收塔底的饱和吸收油进入冷301/5、6前与压缩富气混合。
从吸收塔顶出来的贫气进入再吸收塔(塔302)底部,与贫吸收油逆向接触,以吸收贫气中的>C3组分,再吸收塔顶压力为1.20~1.40MPA(A),平均温度为45℃,从再吸收塔顶出来的干气分为两路,一路送往脱硫装置脱硫,新增一路进提升管作为提升干气,塔底富吸收油返回分馏塔。
自容301出来的凝缩油经泵301/1,2加压与稳定汽油换热(换304)到70℃,进入塔301/2上部,塔底温度约为140℃,塔顶压力1.45~1.65MPA(A),解析塔底重沸器换301由分馏一中换热,解析塔顶气体至空冷301/1~4前与压缩富气混合,解析塔底的脱乙烷油与稳定汽油换热(换302)至140~145℃进入稳定塔303。
塔303顶的操作压力为1.10MPA,塔底温度为~180℃。
塔底重沸器的热源由分馏二中供给。
液化气从稳定塔顶馏出,经空冷304/1~4、冷304/5,6冷凝冷却至40℃,进入容303稳定塔顶回流罐。
液化气用泵304/1,2加压,一路作为塔顶回流,另一路作为产品出装置。
塔底的稳定汽油先与脱乙烷油换热后一部分去反应提升管,剩余再与凝缩油换热后,再经冷305/1,2冷却至40℃,一路作为产品出装置,另一路经泵305/1,2加压后作为补充吸收剂进吸收塔。
第一章反应岗位
第一节正常操作法
一、正常操作
产品收率和产品质量首先取决于反应岗位的操作,要掌握好如下八大平衡关系:
即两器压力平衡、氧平衡、热平衡、生焦和烧焦平衡、转化率和反应深度平衡、催化剂与进料量的平衡、催化剂损耗与补充量的平衡、气体产量与气压机及吸收塔能力的平衡,以达到:
⑴既有足够的反应深度,又减少了二次反应,确保装置的处理能力和轻油收率。
⑵在减少汽油中烯烃含量的同时增加气体中烯烃的含量,以满足化工原料的要求。
⑶在保证装置热平衡的前提下,尽量减少焦炭产率。
反应深度可由转化率表现,主要由平衡剂活性、剂油比、反应温度、反应时间、回炼比和终止剂量决定,压力也有一定的影响。
1、反应温度的控制:
反应温度的高低,直接影响到反应深度的大小,从而影响到产品的分布。
正常操作中,反应温度(TIC101)直接控制再生单动滑阀开度(ZI103),实现自动控制。
影响因素
⑴进料预热温度的影响。
⑵催化剂循环量的变化,循环量增加,反应温度上升;反之下降。
在循环推动力不变的情况下,再生滑阀开度增加,催化剂循环量增加;反之下降。
⑶提升管总进料量的变化,进料量下降,反应温度上升;反之下降。
⑷再生温度的变化,再生温度上升,反应温度上升。
⑸进料带水,反应温度发生大幅度的波动。
⑹再生斜管推动力的变化。
⑺启用终止剂喷嘴,反应温度下降。
(但实际提升管中温度上升)
⑻仪表失灵,再生单动滑阀故障,催化剂循环量发生变化。
调节方法
⑴调节再生滑阀的开度,增加或减少催化剂的循环量,控制反应温度。
滑阀开度增大,反应温度提高。
⑵调节掺渣量及外取热器取热量,通过再生温度变化,控制好两器的热平衡,保持再生床温平稳。
⑶原料带水,及时联系调度和罐区,脱水换罐,停炼带水原料。
⑷控制好终止剂量。
⑸原料预热温度提高,反应温度提高;反之下降。
⑹控制好进料量和合适的掺炼比。
⑺再生单动滑阀故障,改手动控制,马上联系钳工和仪表处理。
⑻仪表故障及时联系处理,此时应参考提升管中下部温度及反应压力判断反应温度的变化。
⑼调节再生斜管推动力,主要通过调节再生器料位和松动点,提高推动力。
后一种方法要在车间指导下进行。
(10)平稳两器差压,保证循环量平稳。
2、沉降器料位的控制
沉降器料位指示的是料位测量点间压力降和仪表量程的比值,其大小一方面影响待生斜管的流化情况,另一方面影响待生剂的汽提效果。
正常操作中,沉降器料位(WICA101)用待生滑阀开度(ZI104)来自动调节。
影响因素;
⑴两器压力差的变化。
⑵待生滑阀故障或再生滑阀故障;仪表失灵。
⑶待生滑开度变化。
⑷催化剂循环量的变化。
⑸汽提蒸汽流量的变化,流量增大,沉降器料位上升。
⑹待生斜管推动力的影响。
⑺其他条件的改变,引起催化剂循环量的变化。
调节方法:
⑴调节待生滑阀开度。
开度增大,沉降器料位降低。
沉降器料位控制范围一般30~60%。
⑵调节两器压力差。
⑶调节汽提蒸汽量。
蒸汽量增大,沉降器料位提高。
一般不作为调节料位手段。
⑷催化剂循环量增加,沉降器料位提高。
根据循环量、系统藏量、汽提段密度等变化判断料位准确与否。
如待生斜管下料不畅,应通过调整松动点、调整反再差压、蒸汽反顶等方法,保证催化剂循环顺畅。
4、沉降器压力控制
沉降器压力是从沉降器顶部到气压机入口或到低压放火炬管网这段管路设备阻力情况的反应,它的变化直接影响到催化剂的正常流化循环,影响产品分布。
反应压力失控的情况的出现是十分危险的。
正常操作中,沉降器压力是由气压机转速维持机入口压力恒定来控制的,提高和降低沉降器压力可以通过提高和降低机入口压力来实现。
影响因素:
⑴提升管总进料量变化。
⑵反应温度变化。
⑶反应进汽总量上升,沉降器压力上升。
⑷原料油带水。
⑸催化剂中毒,产氢量增加。
⑹气压机反飞动量的变化;气压机转速变化。
⑺终止剂量和介质变化。
⑻分馏操作变化:
中段回流中断;容201液面、塔201底液面超高;冷202冷后温度高;冷回流量增加;不合格汽油回炼量大等,均可导致反应压力升高。
⑼富吸收油返塔302操作不正常,干气串入分馏塔。
⑽容301、303脱水未看住,将大量汽油和液化气送往空冷201。
容404和气压机压油过快,大量气体进入容201。
⑾塔301/1携带或冲塔,塔302富吸收油携带大量汽油组分返回塔201,使沉降器压力升高。
⑿预提升干气量变化。
⒀三常、北常等瓦斯来量变化。
调节方法:
沉降器压力(PICA102)由气压机转速及反飞动量控制。
⑴气压机转速提高,沉降器压力降低;反之升高。
⑵气压机反飞动量提高,沉降器压力提高。
⑶控制好提升管进料量,原料带水应及时向调度汇报并查清原因,防止大量的水带入系统。
⑷提升管进料量增加,沉降器压力增加;反之下降。
⑸反应温度上升,沉降器压力上升;反之下降。
⑹如富气量过小,可提大反飞动量、停空冷201、容201充瓦斯,还可适当提大反应深度和处理量。
如富气量过大,可关反飞动、开空冷201、降低反应深度和处理量,如压力继续上升,可启用DG300、DG400放火炬,如压力控制不住,应及时切断进料。
⑺终止剂调节时应缓慢进行,防止沉降器压力突然上升。
⑻空冷运行台数增加及水冷202冷后温度降低,沉降器压力降低。
⑼平稳分馏塔的操作。
调整冷回流时要缓慢,和反应岗位搞好联系,冷回流量增加,沉降器压力上升。
⑽当发现干气中氢产率明显上升时,沉降器压力将上升,可适当加大硫转移剂(金属钝化剂)的注入量,同时增大催化剂的置换速率。
⑾反应用汽量减少,沉降器压力降低;反之增加。
⑿控制平稳塔201、容201、容202液面,避免出现液面超高,造成液封而影响反应压力的情况。
⒀后部岗位影响压力变化,应及时联系并向班长汇报,协助处理。
⒁粗汽油回炼量增加,沉降器压力上升;反之下降。
5、提升管总进料量的控制
正常操作中提升管进料量由操作员根据每班生产任务及反应深度通过进料控制阀进行控制。
影响因素:
⑴原料油泵及回炼油泵故障。
⑵反应深度变化,回炼油量变化。
⑶原料带水。
⑷油浆泵的故障。
⑸原料、回炼油调节阀控制失灵或仪表故障。
⑹原料进装置量减少。
调节方法
⑴根据原料性质,控制反应深度,保证容202的液位,控制回炼油量的相对稳定。
⑵泵发生故障,及时处理,或者切换泵。
⑶根据原料性质及反应深度、反再热平衡等因素,通过蜡油进料控制阀、渣油进料控制阀调节装置掺渣比率。
⑷调节进料喷嘴阀时应确保进料平稳。
⑸喷嘴预热线关小,进料量增加。
⑹原料带水,联系调度罐区和有关单位进行处理。
⑺油浆尽量不回炼,如回炼,回炼量不可大幅度调节。
⑻仪表故障,改手动或付线控制,联系处理。
6、进料预热温度
保证合适的原料预热温度可提高雾化效果,改善产品分布。
原料预热温度过低,原料油的粘度增大,雾化不好遇高温催化剂急剧反应,产焦率升高,轻油收率降低。
预热温度过高会在管线中发生热裂化反应,结焦堵塞管线,同时造成循环量降低,剂油比降低,影响产品分布。
应根据实际情况选择适宜的温度,以使操作达到最佳状态。
原料预热温度控制是通过三通阀TIC210来调节。
7、汽提蒸汽量的控制
汽提蒸汽的主要作用是用水蒸汽将催化剂颗粒之间和颗粒的孔隙内吸附的油气分子置换出来,以减少焦炭产率,提高油品收率。
影响因素:
⑴蒸汽压力波动。
⑵催化剂循环量及沉将器料位变化。
⑶汽提蒸汽喷嘴故障。
⑷仪表和控制阀失灵。
调节方法:
⑴正常情况下,汽提蒸汽量为催化剂循环量的0.3%w以上。
开大控制阀,流量增加。
⑵反应温度低,催化剂带油时,要增大蒸汽量。
⑶提高装置内低压汽压力,汽提蒸汽量增加;反之下降。
⑷注意控制三路汽提蒸汽的比例.
⑸仪表及控制阀失灵时,改手动或付线控制,联系抢修。
⑹焦碳中氢含量增大时,提高汽提蒸汽流量。
8、反应深度的控制
反应深度的调节,最明显将体现为生焦量及再生温度的变化,同时伴有分馏塔底及回炼油罐液面的变化。
影响因素:
⑴反应温度变化。
⑵原料油预热温度变化。
⑶剂油比变化。
⑷再生温度及再生催化剂含炭高低的影响。
⑸催化剂活性变化。
⑹催化剂上重金属的污染程度。
污染严重,深度下降。
⑺提升管各路进料的比例。
⑻反应压力。
⑼终止剂作用强弱的变化。
调节方法:
⑴在催化剂循环量不变的情况下,提高原料预热温度,反应温度提高,深度增大。
⑵在反应温度不变的情况下,提高剂油比,反应深度提高。
⑶提高反应温度,反应深度大。
⑷再生催化剂含炭高于0.1w%时,反应深度会发生明显下降,此时需降低再生催化剂的含炭。
⑸提高催化剂活性,反应深度增加,调节催化剂的置换速率。
⑹催化剂重金属污染,反应深度低,控制好金属钝化剂(硫转移剂)的加注量。
⑺提高终止剂喷嘴流量,提升管底部温度提高,反应深度加大;反之下降。
⑻粗汽油回炼量增加,反应深度下降;反之上升。
⑼终止剂进上口比进下口时原料反应时间长,反应深度大。
9、催化剂循环量的控制
催化剂循环量的大小直接影响两器热平衡和产品分布,是一个受多参数综合影响的重要参数,以下调节方法多指固定其它参数,单独调整某一项参数时的变化情况。
实际操作中要区分影响循环量变化的关键因素。
影响因素:
⑴再生和待生滑阀的开度:
开度大,循环量大。
⑵两器压力变化。
⑶进料雾化蒸汽量。
预提升蒸汽(干气或粗汽油)量的变化。
⑷各松动流化点压力、流量的变化及再生斜管流化推动力的变化。
⑸提升管总进料量的变化。
⑹反应温度的变化。
⑺再生温度的影响。
⑻原料预热温度的变化
调节方法:
正常操作中,用反应温度(TIC101)控制再生单动滑阀开度来调节催化剂的循环量,随滑阀开度的增加,催化剂的循环量也增加,而滑阀压降减少。
当滑阀的压力降减少到某一限度时,继续开大滑阀,催化剂循环量就不一定会继续再有显著变化,而大的滑阀开度和小的滑阀压降将成为一种造成催化剂倒流的潜在危险,调节再生滑阀时要注意两器料位的变化和滑阀压力降的变化。
⑴调节再生、待生滑阀开度。
开大再生滑阀,循环量上升,同时待生滑阀也将相应开大。
⑵保持平稳的两器压力在控制指标内。
两器差压的变化对