连铸技术发展.docx
《连铸技术发展.docx》由会员分享,可在线阅读,更多相关《连铸技术发展.docx(22页珍藏版)》请在冰豆网上搜索。
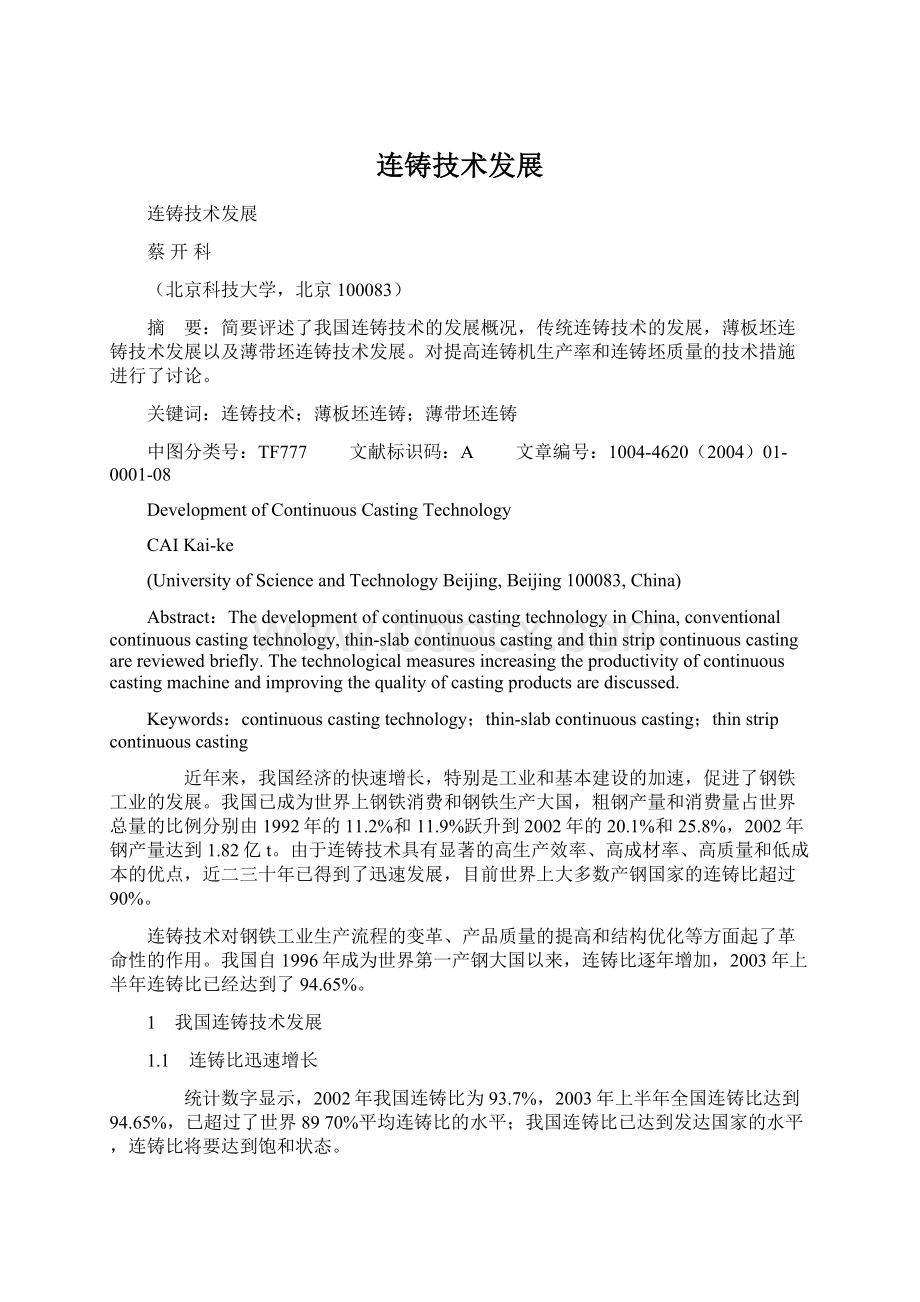
连铸技术发展
连铸技术发展
蔡开科
(北京科技大学,北京100083)
摘 要:
简要评述了我国连铸技术的发展概况,传统连铸技术的发展,薄板坯连铸技术发展以及薄带坯连铸技术发展。
对提高连铸机生产率和连铸坯质量的技术措施进行了讨论。
关键词:
连铸技术;薄板坯连铸;薄带坯连铸
中图分类号:
TF777 文献标识码:
A 文章编号:
1004-4620(2004)01-0001-08
DevelopmentofContinuousCastingTechnology
CAIKai-ke
(UniversityofScienceandTechnologyBeijing,Beijing100083,China)
Abstract:
ThedevelopmentofcontinuouscastingtechnologyinChina,conventionalcontinuouscastingtechnology,thin-slabcontinuouscastingandthinstripcontinuouscastingarereviewedbriefly.Thetechnologicalmeasuresincreasingtheproductivityofcontinuouscastingmachineandimprovingthequalityofcastingproductsarediscussed.
Keywords:
continuouscastingtechnology;thin-slabcontinuouscasting;thinstripcontinuouscasting
近年来,我国经济的快速增长,特别是工业和基本建设的加速,促进了钢铁工业的发展。
我国已成为世界上钢铁消费和钢铁生产大国,粗钢产量和消费量占世界总量的比例分别由1992年的11.2%和11.9%跃升到2002年的20.1%和25.8%,2002年钢产量达到1.82亿t。
由于连铸技术具有显著的高生产效率、高成材率、高质量和低成本的优点,近二三十年已得到了迅速发展,目前世界上大多数产钢国家的连铸比超过90%。
连铸技术对钢铁工业生产流程的变革、产品质量的提高和结构优化等方面起了革命性的作用。
我国自1996年成为世界第一产钢大国以来,连铸比逐年增加,2003年上半年连铸比已经达到了94.65%。
1 我国连铸技术发展
1.1 连铸比迅速增长
统计数字显示,2002年我国连铸比为93.7%,2003年上半年全国连铸比达到94.65%,已超过了世界8970%平均连铸比的水平;我国连铸比已达到发达国家的水平,连铸比将要达到饱和状态。
1.2 连铸机数量增长较快
我国连铸机的数量如表1所示(统计到2002年12月)。
由表1可知:
与工业发达国家相比,我国连铸机的台数最多;现有连铸机年生产能力可达29亿t,实际连铸机产能还大有潜力。
表1国内连铸机统计
机型
台数/台
流数/流
年产能/万t
说明
小方坯
211
783
8983.50
≤150mm×150mm
方、矩坯
218
781
9902
>150mm×150mm
板坯
91
120
8383
板方兼用者按板坯计
薄板坯
10
10
1262
薄板坯连铸连轧
圆坯
20
52
511.25
以生产圆坯为主者按圆坯
异型坯
1
3
63
合计
551
1749
29204.75
有几家方案未确定者(如广东、福建等)尚未计入
1.3 高效连铸技术普遍应用
采用了高拉速、高作业率、高连铸炉数、高质量的连铸技术,40%~50%小方坯连铸机进行了高效化改造,流产量达到15~20万t/a,7~10天连浇生产,铸坯无清理率达95%以上,做到了产量与质量的统一和炉机匹配统一。
1.4 薄板坯连铸-连轧流程应用(TSCR)
全球已建成54流连铸-连轧生产线,年生产能力为5500万t;我国已建和在建13流生产线,年生产能力达到1400万t(见表2),占全球总产量的1/4;中国CSP钢产量(1050万t)与美国CSP产量(1000万t)相当。
表2我国薄板坯连铸连轧生产装备一览
企业
炼钢炉
连铸机
板坯尺寸/mm
年设计能力/万t
轧机
最终产品尺寸/mm
均热炉
投产日期
珠钢
150t电炉
1流立弯型CSP
50×950~1350
80
6机架CSP
1.27
辊底炉191.8m
1998.11
邯钢
100t转炉
1流立弯型CSP
50~70×980~1560
123
1+6机架CSP
1.2
辊底炉191.8m
1999.12
包钢
210t转炉
2流立弯型CSP
70×900~1680
200
6机架CSP
1.2
辊底炉200.8m×2,摆动联接
2001.4
唐钢
150t转炉
1流直弧型TSR
90~70、65×850~1680
120
2+5机架达涅利/三菱
0.8~6
辊底炉187.8m
2002.12
马钢
100t转炉
2流立弯型CSP
90~70、65×900~1600
220
7机架CSP
0.8~8
辊底炉270m×2,摆动联接
2003.12
涟源
90t转炉
1流立弯型CSP
70、65×900~1600
130
7机架CSP
0.8~12.7
辊底炉291.8m
2004.4
本钢
1流直弧型FTSR
90~85×850~1750
150
2005.5
2 传统连铸技术的发展
2.1 提高连铸机生产率的途径
提高连铸机产量,主要是从提高连铸机拉速和提高连铸机作业率两方面着手。
2.1.1 提高连铸机拉速连铸机拉速的提高受出结晶器坯壳厚度、液相穴长度(冶金长度)、二次冷却强度等因素的限制。
要针对连铸机的不同情况,对连铸机进行高效化改造。
小方坯连铸机高效化改造的核心就是提高拉速。
拉速提高后,为了保证出结晶器坯壳不漏钢,其核心技术就是优化结晶器锥度,开发新型结晶器,包括:
Concast的凸模结晶器(CONVEXMOLD);Danieli自适应结晶器(DANAM);VAI的钻石结晶器(DIAMOLD);PaulWurth的多锥度结晶器。
虽然结晶器名称不相同,但其实质就是使结晶器锥度与坯壳收缩相一致,不致于产生气隙而减慢传热,影响坯壳均匀性生长。
目前,国际上小方坯铸机拉速达到的水平见图1和表3。
图1方坯尺寸与拉速关系
表3小方坯铸机拉速
名称
断面/mm×mm
拉速/m.min-1
结晶器型式
德马克
130×130
4.0-4.3
抛物线
康卡斯特
150×150
3.5
凸型
丹尼立
130×130
4.3
自适应
VAI
115×115
5.1
钻石
155×155
2.9
钻石
小方坯铸机拉速的提高,表现为单流产量的提高。
从世界连铸发展的历程来看,20世纪70、80、90年代连铸机的单流年产量分别为5~6、8~10、15~16万t。
我国钢材生产结构是长型材较多,板材比较低(约40%),反映在连铸机建设上是中小型钢厂建设小方坯连铸机较多。
据统计,我国共建小方坯连铸机280台978流,年产量近6000万t,平均单流年产量约为6万t。
与国外比较,连铸机生产率还较低。
为提高连铸机生产率,从20世纪90年代以来,我国对旧有小方坯连铸机进行了高效化改造,如120mm×120mm方坯拉速由2.0m/min提高到3.0~4.0m/min,150mm×150mm方坯拉速由1.5m/min提高到2.5~3.0m/min。
目前,我国不少钢厂的小方坯连铸机经过高效化改造后,单流年产量已达到15~20万t的国际水平。
板坯连铸机拉速的水平如表4所示。
目前板坯厚度为200~250mm的拉速在1.6~2.0m/min左右,单流年产量达到200万t。
如果说提高拉速是小方坯连铸机高效化的核心,那么板坯连铸机高效化的核心就是提高连铸机作业率。
这是因为板坯连铸机的拉速受炉机匹配条件及铸机本身冶金长度的限制不可能有较大的变化,以及由于过高拉速所造成的漏钢危害,对板坯连铸机的影响远远高于小方坯连铸机。
从原则上讲,连铸机提高拉速措施有:
结晶器优化技术;结晶器液面波动检测控制技术;结晶器振动技术;结晶器保护渣技术;铸坯出结晶器后的支掌技术;二冷强化冷却技术;铸坯矫直技术;过程自动化控制技术。
拉速提高了,铸坯内部疏松、偏析缺陷加重,夹杂物增加。
高拉速与高质量是相互矛盾的,因此应根据钢种和产品用途,采取相应的技术措施,把高拉速和高质量的矛盾统一起来,以获得最佳经济效益。
2.1.2 提高连铸机作业率表5为20世纪连铸机世界平均水平指标。
由表5可知,连铸机的作业率和浇注率逐年提高。
但是我国连铸机作业率行业内差距较大。
据统计,我国连铸机平均作业率2000年为63%,2001年为64.8%,2002年为63.8%,与世界平均水平差距较大。
国外有不少钢厂板坯连铸机拉速不高,而单流产量却很高,如美国A.K.Ashland钢厂的板坯铸机,浇240mm×1160~1750mm板坯,工作拉速为1.78m/min,单流年产量达到220万t,连铸机有钢作业率为98%。
这说明对板坯连铸机高效化改造核心不是提高拉速,而是要设法提高铸机作业率以提高连铸机的生产率。
表4高效板坯连铸技术经济指标
厂家
板坯尺寸/mm×mm
拉速/m.min-1
作业率/%
漏钢率/%
年产量/万t
日本住友公司鹿岛厂3号板坯连铸机
270×1450
>2.0
>90
<0.02
>300
日本钢管公司福山厂5号连铸机
220×700~1650
2.5
93
<0.02
>300
美国阿姆科公司阿什兰厂连铸机
240×965~1727
2.0
>90
<0.05
200
美国国家钢铁公司格拉尼特厂连铸机
220×900~2040
1.65
90
<0.05
160
德国克虏伯公司莱茵豪森厂连铸机
260×850~1650
1.6
>85
<0.03
>200
中国上海宝山钢铁公司1号、2号连铸机
210~250×900~1930
>1.4
>80
<0.12
>230
美国钢铁公司蒙瓦利厂连铸机
210~250×700~1050
2.0
>90
<0.05
260
表520世纪连铸机指标(1世界平均水平1)
年代
铸机作业率/%
浇注速率/t(流.min)-1
板坯
大方坯
小方坯
70年代中期
35~38
1.7
0.25
0.18
80年代末
~60
1.86
0.35
0.18
90年代
>90
2~3
0.4
0.60
提高连铸机作业率的技术有:
(1)长时间浇注多炉连浇技术:
异钢种多炉连浇;快速更换长水口;在线调宽;结晶器在线快速调厚度(只需25~30min);在线更换结晶器(小方坯);中间包热循环使用技术;防止浸入式水口堵塞技术。
(2)长时间浇注连铸机设备长寿命技术:
长寿命结晶器,每次镀层的浇钢量为20~30万t;长寿命的扇形段,上部扇形段每次维修的浇钢量100万t,下部扇形段每次维修的浇钢量300~400万t。
(3)防漏钢的稳定化操作技术:
结晶器防漏钢预报系统;结晶器漏钢报警系统;结晶器热状态运行检测系统。
(4)缩短非浇注时间维护操作技术:
上装引锭杆;扇形段自动调宽和调厚技术;铸机设备的快速更换技术;采用各种自动检测装置;连铸机设备自动控制水平。
提高板坯连铸机设备坚固性、可靠性和自动化水平,达到长时间的无故障在线作业,是提高板坯连铸机作业率水平的关键。
2.2 提高连铸坯质量技术
连铸坯的质量概念包括:
铸坯洁净度(钢中非金属夹杂物数量,类型,尺寸,分布,形态);铸坯表面缺陷(纵裂纹,横裂纹,星形裂纹,夹渣);铸坯内部缺陷(中间裂纹,角部裂纹,中心线裂纹,疏松,缩孔,偏析)。
连铸坯质量控制战略是:
铸坯洁净度决定于钢水进入结晶器之前的各工序;铸坯表面质量决定于钢水在结晶器的凝固过程;铸坯内部质量决定于钢水在二冷区的凝固过程。
2.2.1 提高连铸坯洁净度技术
(1)连铸坯洁净度评价包括:
钢总氧量T[O];钢中微观夹杂物(<50μm);钢中大颗粒夹杂物量(>50μm)。
不同产品对钢中洁净度要求如表6所示。
(2)连铸坯洁净度是一个系统工程。
就连铸过程而言,要得到洁净的连铸坯,其任务是:
炉外精炼获得的“干净”钢水,在连铸过程中不再污染;连铸过程中应创造条件在中间包和结晶器中使夹杂物进一步上浮去除。
连铸过程钢水再污染,主要决定于钢水二次氧化、钢水与环境(空气、渣、包衬)相互作用、钢水流动的稳定性、钢渣乳化卷渣。
表6高级钢材对洁净度的要求
产品分类
钢种
代表规格
产品材质特性要求
清洁度要求
薄板
DI罐
低碳铝镇静钢
0.2~0.3mm
飞边裂纹
T[O]<20×10-6,D<20μm
深冲钢
超低碳铝镇静钢
0.2~0.6mm
超深冲,非时效性表面线状缺陷
[C]<20×10-6,[N]<20×10-6,T[O]<20×10-6,D<100μm
荫罩钢
低碳铝镇静钢
0.1~0.2mm
防止图像侵蚀
D<100μm,低硫化
导架结构材
13%Cr
0.15~0.25mm
打眼加工时的裂纹
D<100μm
42Ni
D<5μm,[N]<50×10-6
中厚板
管线钢
X52~70级低合金钢
10~40mm
氢引起的裂纹
夹杂物形态控制
低硫化,S<10×10-6
低温用钢
9%Ni
10~40mm
低温脆化
P<0.003%,S<0.001%
抗层状撕裂钢
结构高强钢
10~40mm
层状撕裂
低磷化、低硫化
无缝管
座圈材
轴承钢
Φ50~300mm
转动疲劳寿命
T[O]<10×10-6,[Ti]<20×10-6
净化管
不锈钢
Φ10mm
电解浸蚀时的
表面光洁度
T[O]<20×10-6,[N]<50×10-6,D<5μm
棒材
轴承
轴承钢
Φ30~65mm
转动疲劳特性
T[O]<10×10-6,[Ti]<15×10-6
D<15μm
渗碳钢
SCM432、420
疲劳特性、加工性
T[O]<15×10-6,P<0.005%
线材
轮胎钢丝
SWRH72、82B
Φ0.1~0.4mm
冷拔断裂
非塑性夹杂D<20μm
弹簧钢
SWRS
Si-Cr钢
Φ1.6~10mm
Φ0.1~0.15mm
疲劳特性、
残余应变性
非塑性夹杂D<20μm
(3)连铸过程控制钢洁净度对策:
保护浇注;中间包冶金技术,钢水流动控制;中间包材质碱性化(碱性复盖剂,碱性包衬);中间包电磁离心分离技术;中间包热循环操作技术;中间包的稳定浇注技术;防止下渣和卷渣技术;结晶器流动控制技术;结晶器EMBR技术。
2.2.2 提高铸坯表面质量的控制技术铸坯表面质量好坏是热送热装和直接轧制的前提条件。
铸坯表面缺陷的产生主要决定于钢水在结晶器的凝固过程。
要清除铸坯表面缺陷,应采用以下技术:
结晶器钢液面稳定性控制;结晶器振动技术;结晶器内凝固坯壳生长均匀性控制技术;结晶器钢液流动状况合理控制技术;结晶器保护渣技术。
2.2.3 提高连铸坯内部质量的控制技术连铸坯内部缺陷一般情况在轧制时能焊合消除,但严重时会使中厚板力学性能恶化,使管线钢氢脆和高碳硬线脆断。
铸坯内部缺陷的产生主要决定带液芯的铸坯在二冷区的凝固过程。
要消除铸坯内部缺陷,可采用以下技术措施:
低温浇注技术;铸坯均匀冷却技术;防止铸坯鼓肚变形技术;轻压下技术;电磁搅拌技术;凝固末端强冷技术;多点或连续矫直技术;压缩铸造技术。
3 薄板坯连铸技术的发展
3.1 板坯连铸工艺的发展
供热连轧生产线坯料的发展经历了钢绽→厚板坯连铸→薄板坯连铸/连轧→薄带坯连铸等几个阶段。
市场竞争要求连铸机生产率高,产品质量好,产品规格具有潜力,投资合理和操作成本低等。
对于现代化热轧带钢生产线,浇注板坯厚度对达到这些基本要求有重要影响。
因此要选择综合优势生产方案。
通常,厚板坯:
200~250mm,单流年产量200万t;薄板坯40~70mm,单流年产量50~70万t;中薄板坯90~120mm,单流年产量100~150万t;中厚板坯130~150mm,单流年产量150~200万t。
最终产品质量取决于连铸板坯质量。
就产品质量而言,传统厚度的板坯明显优于连铸薄板坯。
而中等厚度板坯质量与传统厚度板坯质量十分接近。
厚板坯、薄板坯、中等厚度板坯连铸的优点比较如表7所示。
从生产率、质量、投资和操作成本比较来看,中等厚度板坯连铸综合了传统板坯和薄板坯连铸的优点,是两者中的一种折衷方案。
短流程钢厂建设薄板坯连铸机和中等厚度板坯连铸机已成为联合企业的竞争对手,现在世界上钢铁企业几乎不再建设长流程的厚板坯连铸机。
表7厚板坯、薄板坯、中等厚度板坯连铸的优点比较
传统板坯(200~250mm厚)
中厚板连铸机(90~150mm)
薄板坯(50~70mm厚)
高生产率、高质量、高的灵活性
高生产率、高质量、高灵活性、较低投资、较短生产周期、热装连铸轧制
较低投资成本、较低操作成本、较短生产周期、连铸连轧(直接轧制)
3.2 薄板坯连铸的发展与应用
3.2.1 薄板坯连铸的发展自1989年6月20日NucorSteel的Crawfordsville厂第一条CSP生产线投产以来,随着市场和用户需求,CSP得到了快速发展。
目前世界上已有25座钢厂建立了39流CSP连铸/连轧生产线,薄板坯厚度40~70mm,宽度900~1680mm,热轧带钢厚度0.8~25mm。
第一代CSP工厂,双流连铸机年产180万t,第二代双流连铸机CSP工厂年产可达250~300万t。
3.2.2 薄板坯连铸工艺多样化薄板坯连铸连轧生产线是以薄板坯连铸机开发商而命名的:
CSP:
西马克(SMS)开发;ISP:
德马克(Demag)开发,现与SMS合并为SMS-Demag,并称今后不再有ISP;FTSR:
达涅利(Danieli)开发;QSP:
住友金属(SMI)开发;CONROLL:
奥钢联(VAI)开发。
五种工艺的生产线统计如表8所示。
经过十多年的发展,全世界已建成薄板坯连铸/连轧生产线达32条44流连铸机,形成每年约4630万t/流的生产能力。
表8薄板坯连铸工艺生产统计
工艺
开发商
已投产项目
在建项目
合计
生产线
流数
年生产能力/万t
生产线
流数
生产能力万t/a
生产线
流数
年生产能力/万t
CSP
西马克
16
22
2230
3
5
520
19
27
2750
ISP
德马克
4
5
565
1
2
200
5
7
765
FTSR
达涅利
1
2
200
2
2
200
3
4
400
QSP
住友金属住友重工
3
4
500
-
-
-
3
4
500
CONROLL
奥钢联
1
1
70
1
1
145
2
2
215
合计
25
34
3565
7
10
1065
32
44
4630
注:
其中7套生产线建在转炉钢厂,其它均建在电炉钢厂。
3.2.3 薄板坯连铸工艺优点与传统厚薄板坯连铸相比,薄板坯连铸技术的优势如表9所示。
表9薄板坯连铸工艺优点
项目
短流程连铸连轧
常规流程连铸热轧
生产规模/万t.a-1
80~150(一流)、160~250(二流)
300~500
吨钢投资/%
~40
100
能源消耗/%
25~35
100
金属收得率/%
102~103
100
生产成本/%
80
100
劳动生产率/人.h.t-1
0.5
3~4
生产周期
~2h
>2天
产品覆盖面/%
50~70
100
3.3 薄板坯连铸凝固特点
3.3.1 凝固速度快,液芯长度短厚板坯、薄板坯、薄带坯的凝固特点如表10所示。
传统厚板坯完全凝固需10min以上,而薄板坯仅需1min左右,因此厚板坯液芯长度一般为20~25m,而薄板坯液芯长度仅为5~6m。
液芯长度短,减轻了设备重量,铸机结构简化,这是一个很重要的优点。
薄板坯散热面积增加约4倍,拉速快约5倍,使铸坯表面温度更高进入精轧机组,有利于减小轧制变形抗力。
薄板坯纵向温度均恒,铸坯横向表面温度高且中心和边部温差小,不会产生质点(如AlN)沉淀,不需再加热到高温溶解AlN,仅需均热就可直接轧制有利节能。
这是薄板坯快速凝固的一个很大优点。
表10不同类型连铸凝固特点
项目
厚板坯
薄板坯
薄带坯
尺度/mm
150~300
20~70
2~4
拉速/m.min-1
1.0~2.5
4~6
30~90
完全凝固时间t/s
>600
60
<1
结晶器热流/MW.m-2
1~3
2~3
8~10
液相穴长度,m
>10
>5
<0.5
3.3.2 铸坯热履程平稳,铸坯表面温度高且分布均匀铸坯凝固冷却参数比较见表11。
表11铸坯冷却参数比较
铸坯尺寸/mm×mm
比表面/m2.t-1
冷却速度/℃.s-1
凝固终点温度/℃
250×1500
1.5
0.15
900~1000
50×1500
5.3
2.0
1150~1200
3.3.3 铸坯内部结构致密,偏析小250mm×1500mm铸坯,晶粒尺寸60μm;50mm×1500mm铸坯,晶粒尺寸40μm。
3.3.4 铸坯表面质量控制难度加大厚板坯、薄板坯、薄带其表面积/体积(单位长度)分别为0.225~0.263、1.03~1.06、10~15。
表面积/体积比增加,在相同钢水洁净度条件下,夹杂物易集中在铸坯皮下,影响冷轧板的表面质量。
因此,对薄板坯连铸来说,提高钢水