机械制造工艺学填空题.docx
《机械制造工艺学填空题.docx》由会员分享,可在线阅读,更多相关《机械制造工艺学填空题.docx(12页珍藏版)》请在冰豆网上搜索。
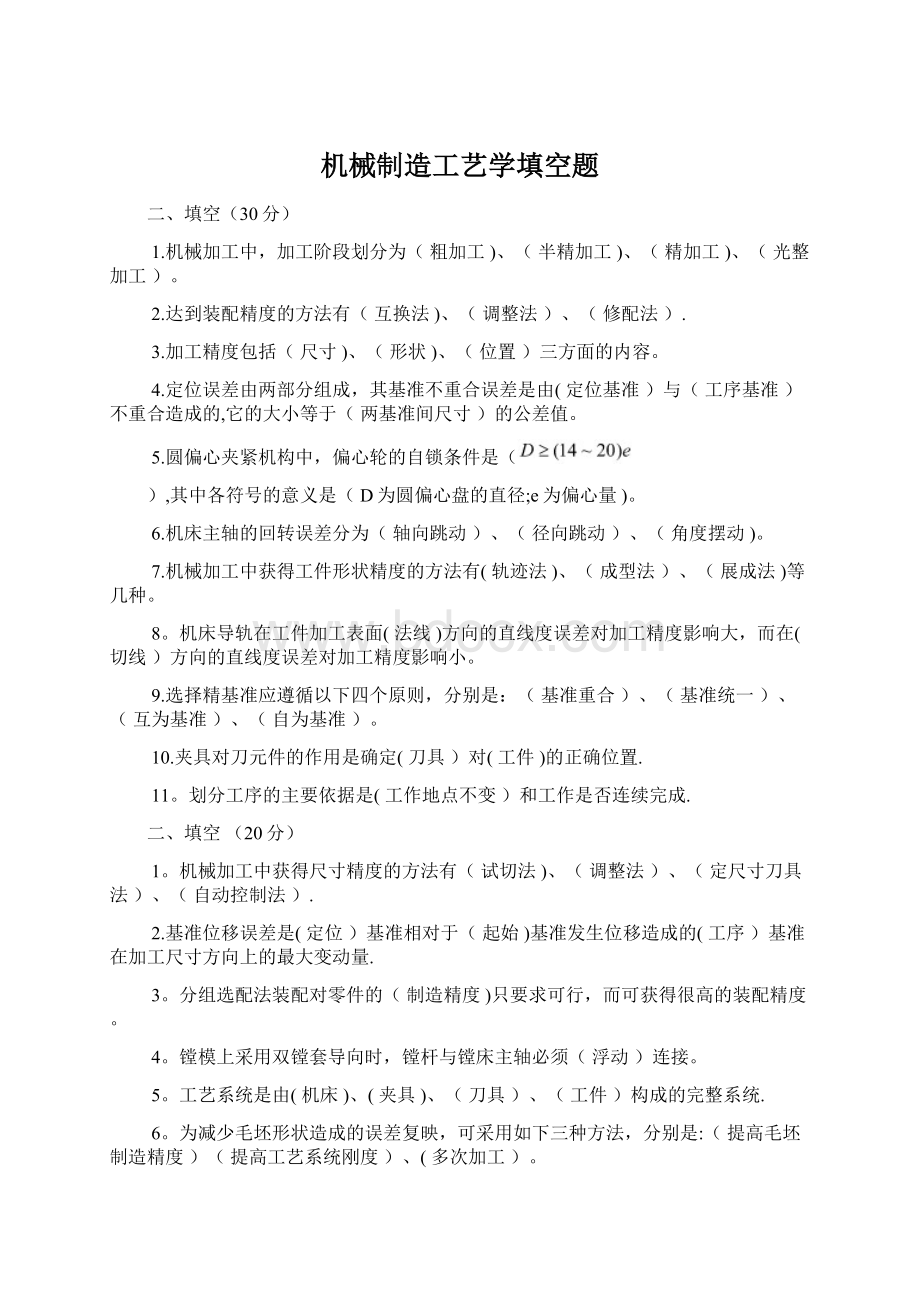
机械制造工艺学填空题
二、填空(30分)
1.机械加工中,加工阶段划分为(粗加工)、(半精加工)、(精加工)、(光整加工)。
2.达到装配精度的方法有(互换法)、(调整法)、(修配法).
3.加工精度包括(尺寸)、(形状)、(位置)三方面的内容。
4.定位误差由两部分组成,其基准不重合误差是由(定位基准)与(工序基准)不重合造成的,它的大小等于(两基准间尺寸)的公差值。
5.圆偏心夹紧机构中,偏心轮的自锁条件是(
),其中各符号的意义是(D为圆偏心盘的直径;e为偏心量)。
6.机床主轴的回转误差分为(轴向跳动)、(径向跳动)、(角度摆动)。
7.机械加工中获得工件形状精度的方法有(轨迹法)、(成型法)、(展成法)等几种。
8。
机床导轨在工件加工表面(法线)方向的直线度误差对加工精度影响大,而在(切线)方向的直线度误差对加工精度影响小。
9.选择精基准应遵循以下四个原则,分别是:
(基准重合)、(基准统一)、(互为基准)、(自为基准)。
10.夹具对刀元件的作用是确定(刀具)对(工件)的正确位置.
11。
划分工序的主要依据是(工作地点不变)和工作是否连续完成.
二、填空(20分)
1。
机械加工中获得尺寸精度的方法有(试切法)、(调整法)、(定尺寸刀具法)、(自动控制法).
2.基准位移误差是(定位)基准相对于(起始)基准发生位移造成的(工序)基准在加工尺寸方向上的最大变动量.
3。
分组选配法装配对零件的(制造精度)只要求可行,而可获得很高的装配精度。
4。
镗模上采用双镗套导向时,镗杆与镗床主轴必须(浮动)连接。
5。
工艺系统是由(机床)、(夹具)、(刀具)、(工件)构成的完整系统.
6。
为减少毛坯形状造成的误差复映,可采用如下三种方法,分别是:
(提高毛坯制造精度)(提高工艺系统刚度)、(多次加工)。
7.生产类型为(单件小批量)生产时,极少采用夹具,一般用划线及试切法达到加工精度要求。
8。
工艺系统热变形和刀具磨损都属于工艺系统的(动态)误差,对工件加工误差而言,造成(变值)系统性误差。
9。
工件上用来确定工件在夹具中位置的点、线、面称为(定位基准).
二、填空(30分)
1。
为减少误差复映,通常采用的方法有:
(提高毛坯制造精度),(提高工艺系统刚度),(多次加工)。
2.达到装配精度的方法有(互换法),(调整法),(修配法)。
3.表面质量中机械物理性能的变化包括(加工表面的冷却硬化),(金相组织变化),(残余应力)。
4.机床主轴的回转误差分为(轴向跳动),(径向跳动),(角度摆动)。
5。
机械加工中获得工件形状精度的方法有(轨迹法),(成型法),(展成法)。
6。
机床导轨在工件加工表面(法线)方向的直线度误差对加工精度影响大,而在(切线)方向的直线度误差影响小。
7。
选择精基准应遵循以下四个原则,分别是(重合基准),(统一基准),(自为基准),(互为基准)。
8。
夹具对刀元件的作用是确定(刀具)对(工件)的正确加工位置。
9。
应用点图进行误差分析时
和R的波动反映的是(变值性误差的变化)和(随机性误差)的分散程度。
10。
工艺系统是由(机床),(夹具),(刀具),(工件)构成的完整系统。
11.划分工序的主要依据是工作地点是否改变和(工件是否连续完成)。
二、填空(20分)
1。
轴类零件、盘类零件和箱体类零件加工时,其常见的统一基准分别为:
(两中心孔连线)、(圆孔、端面)、(一面双孔).
2.各种钻夹具中,以(固定)式钻模加工精度最高,各种钻套中以(固定)式钻套加工精度最高。
3.分组选配法装配对零件的(制造精度)要求不高,而可获得较高的装配精度.
4。
机床导轨在加工表面(垂直)方向的直线度误差对加工精度影响大,而在(切线)方向上的直线度误差影响小.
5。
应用点图进行误差分析时,
和R的波动反映的是(系统性误差的变化)和(随机性误差)的分散程度。
6.工艺系统是由(机床)、(夹具)、(刀具)、(工件)构成的完整系统。
7。
为减少毛坯形状造成的误差复映,可用如下三种方法,分别是:
(减小毛坯制造误差)、(提高工艺系统刚度)、(多次加工)。
8.生产类型为(单件小批)生产时,极少采用夹具,一般用划线及试切法达到精度要求。
9.工艺系统热变形和刀具磨损都属于工艺系统的(动态)误差,对工件加工误差而言,造成(变值性)系统性误差。
二、填空(30分)
1.一般机械零件的加工顺序为:
(先粗后精)、(先主后次)、(先基面后其他)、(先面后孔)。
2.达到装配精度的方法有(互换法)、(调整法)、(修配法)。
3。
加工精度包括(尺寸)、(位置)、(形状)三方面的内容。
4.基准位移误差是(定位)基准相对于(起始)基准发生位移造成的(工序)基准在加工尺寸方向上的最大变动量。
5.分组选配法装配对零件的(制造精度)要求可行,而可获得很高的装配精度。
6。
工艺系统是由(机床)、(夹具)、(刀具)、(工件)构成的完整系统。
7.为减少毛坯形状造成的误差复映,可用如下三种方法,分别是:
(减小毛坯制造误差)、(提高工艺系统刚度)、(多次加工)。
8.生产类型为(单件小批)生产时,极少采用夹具,一般用划线及试切法达到精度要求。
9.工艺系统热变形和刀具磨损都属于工艺系统的(动态)误差,对工件加工误差而言,造成(变值)系统性误差。
10.工件上用来确定工件在夹具中位置的点、线、面称为(定位基准)。
11。
选择精基准应遵循以下四个原则,分别是:
(基准重合)、(基准统一)、(互为基准)、(自为基准)。
12.为了提高生产率,用几把刀具同时加工几个表面的工步,称为(复合工步).
二、填空(30分)
1.机械加工中,加工阶段划分为(粗加工)、(半精加工)、(精加工)、(光整加工).
2.选择精基准应遵循以下四个原则,分别是:
(基准重合)、(基准统一)、(互为基准)、(自为基准).
3。
达到装配精度的方法有(互换法)、(概率法)、(选配法)、(调整法)、(修配法)。
4.表面粗糙度的影响因素有(刀具几何度数)、(切削用量)、(充分冷却)、(工艺系统抗振性).
5。
为减少毛坯形状造成的误差复映,常采用的方法有:
(提高毛坯制造精度)、(提高工艺系刚度)、(多次加工)。
6。
加工精度包括(尺寸)、(形状)、(位置)三方面的内容。
7.基准位移误差是(定位)基准相对于(起始)基准发生位移造成的(工序)基准在加工尺寸方向上的最大变动量。
8.生产类型为(单件小批)生产时,极少采用夹具,一般用划线及试切法达到精度要求.
9。
工艺系统热变形和刀具磨损都属于工艺系统的(动态)误差,对工件加工误差而言,造成(变值)系统性误差。
10。
工件上用来确定工件在夹具中位置的点、线、面称为(基准)。
11。
在平面磨床上磨削平面时,若机床导轨在水平面内有直线度误差δ1,垂直面内有直线度误差δ2,则工件表面产生的形状误差大小为(δ2)。
12.分组互换法装配对零件的(制造精度)要求可行,而可获得很高的装配精度。
二、填空(20分)
1.获得零件尺寸精度的方法有(试切法)、(调整法)、(定尺寸刀具法)、(自动控制法).
2.磨削淬火钢时,影响工件金相组织变化的主要因素是(磨削温度),所以通常分为(回火)烧伤、(退火)烧伤和(淬火)烧伤.
3.由于工件材料硬度不均匀而引起的加工误差其性质是(随机性误差).
4。
不完全互换法适用于(2、5),修配法适用于(3、4),固定调节法适用于(1、5)。
①大批大量生产;②成批生产;③单件小批生产;④多环装配尺寸链;⑤少环装配尺寸链
5。
应用点图进行误差分析时,
和R的波动反映的是(工件平均值的变化趋势)和(随机误差)的分散程度。
6.工艺系统是由(机床)、(刀具)、(夹具)、(工件)构成的完整系统.
7.分组选配法装配对零件的(加工精度)要求不高,而可获得较高的装配精度。
8。
机床导轨在加工表面(法线)方向的直线度误差对加工精度影响大,而在(切线)方向上的直线度误差影响小。
二、填空(20分)
1.获得零件尺寸精度的方法有(试切法)、(调整法)、(定尺寸刀具法)、(自动控制法)。
2。
加工细长轴时,由刀具热变形引起的工件误差属于(变值系统性误差)。
3。
在选择精基准时,应遵循的原则有(基准统一)、(基准重合)、(互为基准)、(自为基准)。
4。
在平面磨床上磨削平面时,若机床导轨在水平面内有直线度误差δ1,垂直面内有直线度误差δ2,则工件表面产生的形状误差是(δ2)。
5.基准位移误差是(定位)基准相对于(起始)基准发生位移造成的(工序)基准在加工尺寸方向上的最大变动量。
6。
工序尺寸的公差带一般取(入体)方向,而毛坯尺寸的公差带一般取(双向)分布。
7.为减少毛坯形状造成的误差复映,可用如下三种方法,分别是:
(增大系统刚度)、(减小毛坯误差)、(多次加工)。
8。
安装是指(定位)和(夹紧)过程的总和。
二、填空(30分)
1。
为了提高生产率,用几把刀具同时加工几个表面的工步,称为(复合工步)。
2.加工细长轴时,由刀具热变形引起的工件误差属于(变值系统性误差)。
3。
在选择精基准时,应遵循的原则有(基准重合)、(基准统一)、(互为基准、反复加工)、(自为基准)。
4。
在平面磨床上磨削平面时,若机床导轨在水平面内有直线度误差δ1,垂直面内有直线度误差δ2,则工件表面产生的形状误差是(δ2).
5.基准位移误差是(定位)基准相对于(调刀)基准发生位移造成的(定位)基准在加工尺寸方向上的最大变动量。
6.工序尺寸的公差带一般取(入体)方向,而毛坯尺寸的公差带一般取(对称)分布。
7.为减少毛坯形状造成的误差复映,可用如下三种方法,分别是:
(增加机床刚度)、(减小)、(减小)。
8.工艺系统是指机械加工中由(机床)、(夹具)、(刀具)和(工件)构成的一个完整系统.
9.当装配精度要求很高、大批量生产、组成环数又很少时,可采用(选配法)进行装配;而当装配精度要求高、单件小批生产、组成环数又较多时,应采用(调整法)进行装配;
10.点图法能将(常值系统性)误差和(变值系统性)误差分开,并能看出(工件平均尺寸)和(随机误差)的变化趋势。
11.获得零件尺寸精度的方法有(试切法)、(调整法)、(定尺寸刀具法)、(自动控制法)。
二、填空(30分)
1.镗模上采用双镗套导向时,镗杆与镗床主轴必须(浮动)连接。
2。
为了提高生产率,用几把刀具同时加工几个表面的工步,称为(复合工步).
3.加工细长轴时,由刀具热变形引起的工件误差属于(变值系统性误差)。
4.在选择精基准时,应遵循的原则有(基准统一)、(基准重合)、(互为基准反复加工)、(自为基准)。
5.工序尺寸的公差带一般取(入体)方向,而毛坯尺寸的公差带一般取(对称)分布。
6。
为减少毛坯形状造成的误差复映,可用如下三种方法,分别是:
(增大工艺系统刚度)、(提高毛坯精度)、(多次加工)。
7。
工艺系统是指机械加工中由(机床)、(刀具)、(夹具)和(工件)构成的一个完整系统。
8.分组选配法装配对零件的(加工精度)要求不高,而可获得很高的装配精度.
9。
生产类型分为(单件生产)、(成批生产)、(大量生产)。
10.点图法能将(系统性)误差和(随机性)误差分开,并能看出(平均尺寸)和(随机误差)的变化趋势。
11。
获得零件尺寸精度的方法有(试切法)、(调整法)、(定尺寸刀具法)、(自动控制法)。
二、填空(30分)
1。
生产类型分为(单件生产)、(批量生产)、(大量生产)。
2。
保证装配精度的方法通常有(互换法)、(选配法)、(修配法)、(调整法).
3。
工艺系统中的各种误差称之为(原始误差)。
4。
在选择精基准时,应遵循的原则有(基准统一)、(基准重合)、(互为基准反复加工)、(自为基准).
5。
工序尺寸的公差带一般取(入体)方向,而毛坯尺寸的公差带一般取(对称)分布。
6。
为减少毛坯形状造成的误差复映,可用如下三种方法,分别是:
(提高工艺系统刚度)、(提高毛坯精度)、(多次走刀).
7.工艺系统是指机械加工中由(机床)、(夹具)、(刀具)和(工件)构成的一个封闭系统。
8.分组选配法装配对零件的(加工制造精度)要求不高,而可获得很高的装配精度。
9。
在正态分布曲线中,参数
表征整个曲线所在的位置,它的变化是由(常值系统性误差)引起的。
的变化只影响整个曲线在水平方向上的位置,而不改变(曲线形状)。
10。
获得零件尺寸精度的方法有(试切法)、(调整法)、(定尺寸刀具法)、(自动控制法).
11。
为了提高生产率,用几把刀具同时加工几个表面的工步,称为(复合工步).
二、填空(30分)
1.磨削烧伤的形式主要有:
(回火烧伤)、(退火烧伤)和(淬火烧伤)。
2。
生产类型分为(单件生产)、(成批生产)、(大量生产).
3。
利用分布曲线研究一批工件的加工精度时,最主要的二个参数是(尺寸平均值)和(分散范围).
4.保证装配精度的方法通常有(互换法)、(修配法)、(调整法)。
5。
在选择精基准时,应遵循的原则有(基准重合)、(基准统一)、(互为基准)、(自为基准)。
6.工序尺寸的公差带一般取(入体)方向,而毛坯尺寸的公差带一般取(双向)分布.
7。
为减少毛坯形状造成的误差复映,可用如下三种方法,分别是:
(提高系统刚度)、(提高毛坯质量)、(多次走刀)。
8。
工艺系统是指机械加工中由(机床)、(夹具)、(刀具)和(工件)构成的一个完整系统。
9.分组选配法装配对零件的(加工精度)要求不高,而可获得很高的装配精度。
10.。
为了提高生产率,用几把刀具同时加工几个表面的工步,称为(复合工步)。
11.机床导轨在工件加工表面(法线)方向的直线度误差对加工精度影响大,而在(切线)方向的直线度误差对加工精度影响小。
二、填空(30分)
1.划分工序的主要依据是(工作地点是否变动)和(工作是否连续)。
2.达到装配精度的方法有(互换法)、(修配法)和(调整法).
3.加工精度包括(形状精度)、(尺寸精度)、(位置精度)三方面的内容。
4.基准位移误差是(定位)基准相对于(起始)基准发生位移造成的(工序)基准在加工尺寸方向上的最大变动量。
5.分组选配法装配对零件的(加工精度)要求不高,而可获得较高的装配精度。
6.工艺系统是由(机床)、(夹具)、(刀具)、(工件)构成的完整系统。
7。
为减少毛坯形状造成的误差复映,可用如下三种方法,分别是:
(提高毛坯精度)、(提高工艺系统刚度)、(多次走刀)。
8。
生产类型为(单件小批)生产时,极少采用夹具,一般用划线及试切法达到精度要求.
9.工件上用来确定工件在夹具中位置的点、线、面称为(定位基准)。
10。
为了提高生产率,用几把刀具同时加工几个表面的工步,称为(复合工步)。
11。
镗模上采用双镗套导向时,镗杆与镗床主轴必须(浮动连接)连接.
12.利用分布曲线法研究一批工件的加工精度时,最主要的两个参数是:
(均方根差)和(平均尺寸).
13。
表面质量的主要内容是:
①表面的几何形状特征,主要有(表面粗糙度)和(波度);②表面层的物理、机械性能的变化,主要有以下三方面:
(表面层的硬度)、(表面层的组织)和(表面层的残余应力).
二、填空(30分)
1。
划分工序的主要依据是工作地点是否变动和(加工过程是否连续)。
2.为了提高生产率,用几把刀具同时加工几个表面的工步,称为(复合工步)。
3。
在选择精基准时,应遵循的原则有(基准重合)、(统一基准)、(互为基准)、(自为基准)。
4.在平面磨床上磨削平面时,若机床导轨在水平面内有直线度误差δ1,垂直面内有直线度误差δ2,则工件表面产生的形状误差是(δ2)。
5。
基准位移误差是(定位)基准相对于(起始)基准发生位移造成的(工序)基准在加工尺寸方向上的最大变动量。
6.用调整法磨削一批轴的外圆时,砂轮磨损过程会使工件直径产生(变值系统性误差)。
7.工序尺寸的公差带一般取(入体)方向,而毛坯尺寸的公差一般取(双向)分布。
8.为减少毛坯形状造成的误差复映,可用如下三种方法,分别是:
(提高毛坯精度)、(提高工艺系统刚度)、(多次走刀)。
8。
工艺系统是指机械加工中由(机床)、(夹具)、(工件)和(刀具)构成的一个完整系统.
9.当装配精度要求很高、大批量生产、组成环数又很少时,可采用(分组互换法)进行装配;而当装配精度要求高、单件小批生产、组成环数又较多时,应采用(修配法)进行装配.
10.点图法能将(随机)误差和(系统)误差分开,并能看出(加工误差)和(平均尺寸)的变化趋势.
11。
获得零件尺寸精度的方法有(试切法)、(调整法)、(定尺寸刀具法)、(自动控制法)。
1。
采用修配法保证装配精度时,对于修配环的选择应注意(结构简单,便于加工)、(便于拆装)和(对其他尺寸无影响)。
2。
磨削烧伤的形式主要有:
(退火烧伤)、(淬火烧伤)和(回火烧伤).
3.生产类型分为(大量生产)、(成批生产)、(单件小批生产)。
4。
利用分布曲线研究一批工件的加工精度时,最主要的二个参数是(均方根差)和(平均值)。
5.保证装配精度的方法通常有(调整法)、(互换法)、(修配法).
6.在选择精基准时,应遵循的原则有(基准重合)、(基准统一)、(互为基准)、(自为基准)。
7.机械加工中,加工阶段划分为(粗加工阶段)、(半精加工阶段)、(精加工阶段)、(光整加工阶段)。
8.为减少毛坯形状造成的误差复映,常见的方法有:
(提高毛坯精度)、(提高工艺系统刚度)、(多次走刀).
9.生产类型为(单件小批)生产时,极少采用夹具,一般用划线及试切法达到精度要求.
10。
夹具对刀元件的作用是确定(刀具)对(工件)的正确位置。
11.工序尺寸的公差带一般取(入体)方向,而毛坯尺寸的公差带一般取(双向)分布.
二、填空(30分)
1.若封闭环公差为0.12、组成环有6个、单件生产,则合适的装配方法为(修配法);
若封闭环公差为0。
10、组成环有2个、大量生产,则合适的装配方法又为(完全互换法)。
2.生产类型分为(大量生产)、(成批生产)、(单件小批生产)。
3。
工艺系统中的各种误差称之为(原始误差)。
4。
在选择粗基准时,应遵循的原则有(选重要表面)、(不加工表面或与加工面位置要求较高的表面)、(加工余量较小的表面)、(同一方向只能使用一次)。
5.工序尺寸的公差带一般取(入体)方向,而毛坯尺寸的公差带一般取(双向)分布。
6.为减少毛坯形状造成的误差复映,可用如下三种方法,分别是:
(提高毛坯精度)、(提高系统刚度)、(多次走刀)。
7.工艺系统是指机械加工中由(机床)、(刀具)、(夹具)和(工件)构成的一个完整系统。
9。
划分工序的主要依据是(工作地点是否变动)和(加工过程是否连续)。
10。
在正态分布曲线中,参数
表征整个曲线所在的位置,它的变化是由(系统性误差)引起的;
的变化只影响整个曲线在水平方向上的位置,而不改变(曲线的形状)。
11.获得零件尺寸精度的方法有(试切法)、(调整法)、(定尺寸刀具法)、(自动控制法)。
12。
为了提高生产率,用几把刀具同时加工几个表面的工步,称为(复合工步)。
13.生产类型为(单件小批)生产时,极少采用夹具,一般用(试切法)达到精度要求。
二、填空(30分)
1.各种钻夹具中,以(固定)式钻模加工精度最高,各种钻套中以(固定)式钻套加工精度最高。
2。
获得零件尺寸精度的方法有(试切法)、(调整法)、(定尺寸刀具法)、(自动控制法).
3。
轴类零件、盘类零件和箱体类零件加工时,其常见的统一基准分别为:
(两顶尖孔)、(端面及与其垂直的孔)、(一面双孔、两面一孔或三面)。
4.在选择精基准时,应遵循的原则有(基准重合)、(统一基准)、(自为基准)、(互为基准)。
5。
基准位移误差是(定位)基准相对于(起始)基准发生位移造成的(工序)基准在加工尺寸方向上的最大变动量。
6。
工序尺寸的公差带一般取(入体)方向,而毛坯尺寸的公差带一般取(双向)分布。
7。
为减少毛坯形状造成的误差复映,可用如下三种方法,分别是:
(提高工艺系统刚度)、(提高毛坯精度)、(多次走刀)。
8.安装是指(定位)和(夹紧)过程的总和。
9.分组选配法装配对零件的(加工精度)要求不高,而可获得较高的装配精度。
10.机床导轨在加工表面(法线)方向的直线度误差对加工精度影响大,而在(切线)方向上的直线度误差影响小.
11。
工艺系统是由(机床)、(刀具)、(夹具)、(工件)构成的完整系统。
二、填空(每空1分共30分)
1.在安排机械加工顺序时,需要遵循的原则是:
(先基面后其他)、(先面后孔)、(先主后次)。
2.机械加工中,加工阶段划分为(粗加工)、(半精加工)、(精加工)、(光整加工)。
3.保证装配精度的方法有(互换法)、(调整法)和(修配法)。
4.机械加工中获得工件形状精度的方法有(轨迹法)、(范成法)、(成形刀具法)三种。
5.磨削淬火钢时,最常出现(淬火烧伤)、(回火烧伤)和(退火烧伤),其主要原因是由于(磨削热使金属温度超过相变温度)。
6.机床主轴的回转误差分为(纯径向跳动)、(角度摆动)、(轴向窜动).
7.选择精基准应遵循以下四个原则,分别是:
(基准重合)、(统一基准)、(自为基准)、(互为基准)。
8。
表面质量的主要内容是:
1)表面的几何形状特征,主要有(粗糙度)和(波度);2)表面层的物理、机械性能的变化,主要有以下三方面:
(加