光伏质量知识题库.docx
《光伏质量知识题库.docx》由会员分享,可在线阅读,更多相关《光伏质量知识题库.docx(12页珍藏版)》请在冰豆网上搜索。
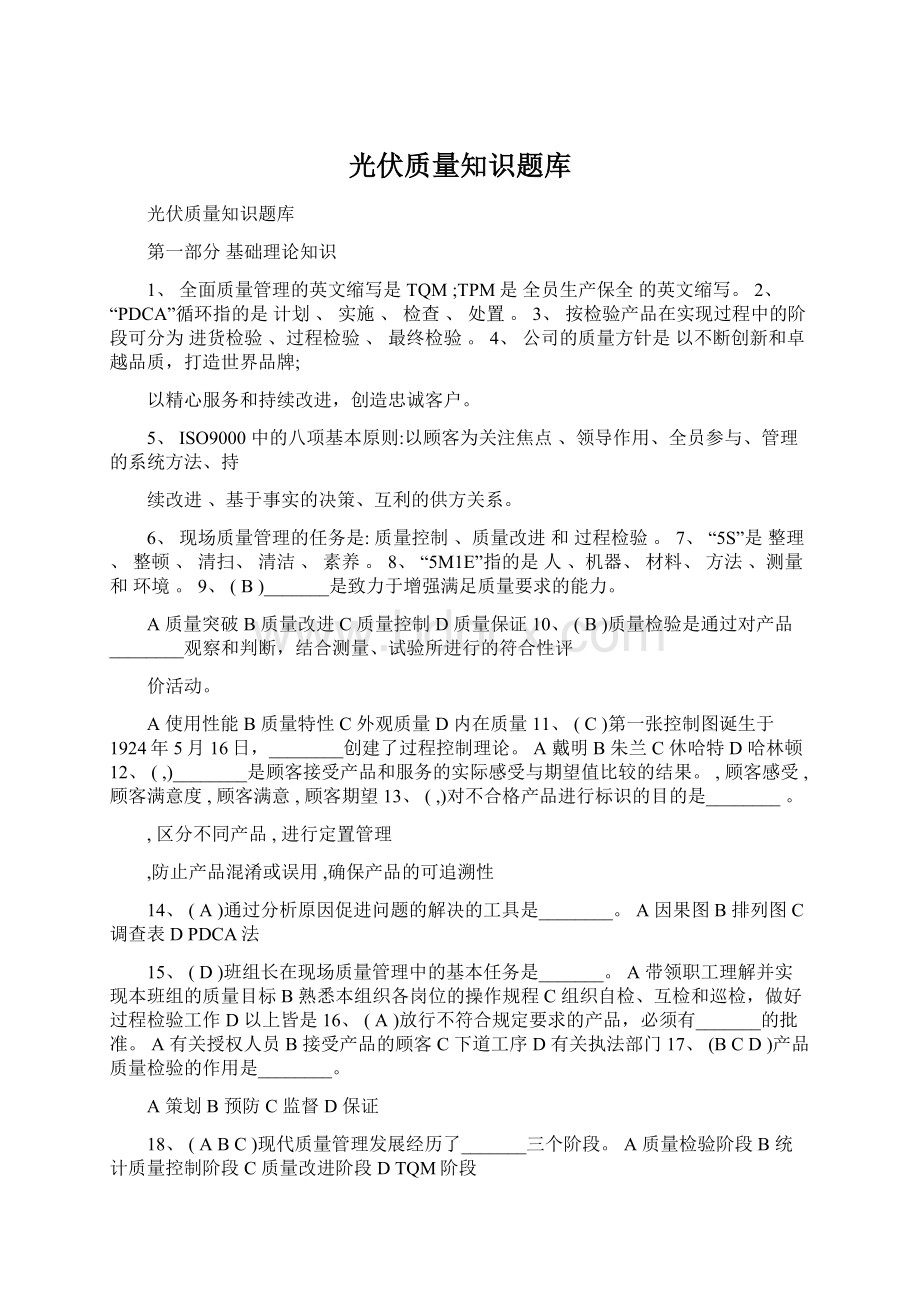
光伏质量知识题库
光伏质量知识题库
第一部分基础理论知识
1、全面质量管理的英文缩写是TQM;TPM是全员生产保全的英文缩写。
2、“PDCA”循环指的是计划、实施、检查、处置。
3、按检验产品在实现过程中的阶段可分为进货检验、过程检验、最终检验。
4、公司的质量方针是以不断创新和卓越品质,打造世界品牌;
以精心服务和持续改进,创造忠诚客户。
5、ISO9000中的八项基本原则:
以顾客为关注焦点、领导作用、全员参与、管理的系统方法、持
续改进、基于事实的决策、互利的供方关系。
6、现场质量管理的任务是:
质量控制、质量改进和过程检验。
7、“5S”是整理、整顿、清扫、清洁、素养。
8、“5M1E”指的是人、机器、材料、方法、测量和环境。
9、(B)_______是致力于增强满足质量要求的能力。
A质量突破B质量改进C质量控制D质量保证10、(B)质量检验是通过对产品________观察和判断,结合测量、试验所进行的符合性评
价活动。
A使用性能B质量特性C外观质量D内在质量11、(C)第一张控制图诞生于1924年5月16日,________创建了过程控制理论。
A戴明B朱兰C休哈特D哈林顿12、(,)________是顾客接受产品和服务的实际感受与期望值比较的结果。
顾客感受,顾客满意度,顾客满意,顾客期望13、(,)对不合格产品进行标识的目的是________。
区分不同产品,进行定置管理
防止产品混淆或误用,确保产品的可追溯性
14、(A)通过分析原因促进问题的解决的工具是________。
A因果图B排列图C调查表DPDCA法
15、(D)班组长在现场质量管理中的基本任务是_______。
A带领职工理解并实现本班组的质量目标B熟悉本组织各岗位的操作规程C组织自检、互检和巡检,做好过程检验工作D以上皆是16、(A)放行不符合规定要求的产品,必须有_______的批准。
A有关授权人员B接受产品的顾客C下道工序D有关执法部门17、(BCD)产品质量检验的作用是________。
A策划B预防C监督D保证
18、(ABC)现代质量管理发展经历了_______三个阶段。
A质量检验阶段B统计质量控制阶段C质量改进阶段DTQM阶段
19、(ACD)生产现场管理应做到__________“三按”进行生产。
A按图样B按规划C按操作规程D按工艺
20、(ABD)全面质量管理的基本要求是__________。
A全过程的质量管理B全员的质量管理
C全方位的质量管理D全企业的质量管理
21、(AB)2000版ISO9000族标准规定的以过程为基础的质量管理体系包括__________
等过程。
A管理职责B资源管理C产品制造D质量监督
22、(BCD)朱兰质量管理三部曲包括________。
A质量保证B质量控制C质量改进D质量策划
23、谈谈对关键质控点的理解:
生产现场在一定的期间内、一定的条件下对需要重点控制的质量特性、关键部位、薄弱环节,以及主导因素等采取特殊的措施和方法,实行强化管理,使工序处于良好控制状态,保证达到规定的质量要求。
它具有动态特性。
24、TPM其具体含义有哪几个方面:
英文TotalProductiveMaintenance的缩略语,中文译名叫全面生产维修,又译为全员生产保全。
以提高设备综合效率为目标,以全系统的预防维修为过程,全体人员参与为基础的设备保养和维修管理体系。
1.以追求生产系统效率(综合效率)的极限为目标;
2.从意识改变到使用各种有效的手段,构筑能防止所有灾害、不良、浪费的体系,最终构成“零”灾害、“零”不良、“零”浪费的体系;
3.从生产部门开始实施,逐渐发展到开发、管理等所有部门;
4.从最高领导到第一线作业者全员参与。
25、TPM活动由哪几个方面组成:
“设备保全”、“质量保全”、“个别改进”、“事务改进”、“环境保全”、“人才培养”这6个方面组成,对企业进行全方位的改进。
26、精益生产原则之消除八大浪费是指哪些:
生产中普遍存在的八大浪费涉及:
过量生产、等待时间、运输、库存、过程(工序)、动作、产品缺陷以及忽视员工创造力。
27、精益生产原则之"自我反省"和"现地现物"
精益文化里有两个突出的特点:
"自我反省"和"现地现物".
"自我反省"的目的是要找出自己的错误,不断地自我改进。
丰田认为"问题即是机会"-当错误发生时,并不责罚个人,而是采取改正行动,并在企业内广泛传播从每个体验中学到的知识。
这与很多国内企业动不动就罚款的做法是完全不同的-绝大部分问题是由于制度流程本身造成的,惩罚个人只会使大家千方百计掩盖问题,对于问题的解决没有任何帮助。
"现地现物"则倡导无论职位高低,每个人都要深入现场,彻底了解事情发生的真实情况,基于事实进行管理。
这种"现地现物"的工作作风可以有效避免"官僚主义".
28、精益生产原则之标准化与工作创新
标准化的作用是不言而喻的,但标准化并不是一种限制和束缚,而是将企业中最优秀的做法固定下来,使得不同的人来做都可以做得最好,发挥最大成效和效率。
而且,标准化也不是僵化、一成不变的,标准需要不断地创新和改进。
第二部分现场质量知识务实
29、我司常规电阻率1,3Ω.?
的多晶硅片扩散后的方块电阻值必须控制在(38-45)Ω/
?
之间;且同一炉扩散方块电阻不均匀度(?
10%),同一硅片扩散方块电阻不均匀度(?
5%)。
若超出以上标准范围,视为工艺异常,必须及时知会值班工艺工程师;R口小于
(30)Ω/?
或者大于(50)Ω/?
视为扩散质量不合格片,即必须返工。
30、电池片成品检验以《CSG太阳电池产品详细规范》为标准。
31、我司扩散车间洁净度要求(A3000级)
A3000级B5000级
C1万级D十万级
32、单晶单面扩散后少子寿命要求(B6μs),双面扩散后少子寿命要求(C10μs)。
多晶单面扩散后少子寿命要求(D4μs),双面扩散后少子寿命要求(A7μs)33、我司一线硅片经等离子体刻蚀后要求:
BC
A导电类型为N型B白色痕宽度正常为?
0.5mm、灰白色痕宽度?
2mm
C导电类型为P型D白色痕宽度正常为?
0.2mm、灰白色痕宽度?
1.5mm34、我司电池表面减反射膜是什么材料(C)
AAlOBSiO232
CSiNxDTiO2
35、我司单晶PECVD减反射膜有哪些质量要求(A膜厚76?
5nm,D折射率2.1?
0.1)
A膜厚76?
5nmB膜厚78?
5nm
C折射率2.05?
0.1D折射率2.1?
0.1
36、丝网印刷质量主要控制哪些:
印刷图案外观、印刷栅线高宽及比例、印刷重量37、电池片测试分选仪测试光强和温度分别控制在那个范围内(A)W/?
、(D)?
。
A1000?
50B1000?
30
ooooC20C?
-3CD25C?
3C
38、影响一次清洗外观不良主要因素有:
硅片来料脏污如油污、硅酸钠残留、出制绒槽后在空气中滞留时间过长、操作过程引入如手指印
39、影响制绒后少子寿命不合格的主要因素有:
纯水污染电阻率不达标、槽体、花篮等清洁不到位、化学药品(如添加剂)等引入杂质40、影响扩散外观不良原因主要有:
偏磷酸污染、一洗后甩干不净致药液残留、操作过程引入如手套不干净、手接触污染硅
片
41、扩散少子寿命不合格的主要原因有哪些:
炉管污染,清洁不及时;来料不良如黑心片;裸手接触污染硅片;环境洁净度不达标等42、我司造成单晶板式PECVD反射膜色差的主要原因有哪些:
微波源功率不均匀;温度场不均匀;操作放片未放水平;石墨舟载板凹凸不平;.特气管路气孔堵塞等
43、丝网印刷的主要不良有哪些:
印刷缺失;断栅;虚印;印刷偏移;漏浆;印刷脏污44、如何减少丝网印刷过程中的不良:
及时发现断栅、漏浆及时擦拭网版;2.发现脏污,浆料污染及时擦拭印刷台面如有破洞更换网版;发现印刷偏移、虚印及时通知工艺调整改善
45、电池片测试仪日常维护保养注意事项:
参考电池上是否有碎硅片或灰尘;探针的接触是否良好或已达使用寿命;测试仪周围环境清洁;光强是否能够达到测试要求;暗箱内是否有卡片;遮光布是否遮光良好等46、焊接有哪些不良,分别会导致什么后果,
答:
焊接的主要不良有虚焊、溢锡、偏移(主栅线)、锡渣、高点、焊疤等。
其中虚焊会导致组件串联电阻增加,降低组件功率输出,并且组件在使用过程中虚焊位置温度较高,温度过高会导致组件损毁;
溢锡会导致组件外观不良,并且会遮挡电池片,有损功率;
偏移(主栅线)会导致外观不良,并影响组件电流收集,遮挡部分电池片,影响组件功率;
锡渣及高点会导致外观不良,严重时会造成裂片,锡渣在两导电体间时可能引起组件内部短路;
焊疤会导致外观不良。
47、层压工序都有哪些注意点,可能会导致什么后果,如何监控,
答:
层压工序主要要注意以下几点:
一、层压工艺设置的正确性,不同EVA性能不同,层压工艺也不同,参数设置错误可能导致交联度超标,层压出现气泡、背板鼓包等,严格执行工艺文件;
二、层压温度、真空度达到要求,包括温度的稳定性,均匀性符合要求;抽真空速度、真空度达到要求;温度不稳定、不均匀会导致交联度超标,气泡问题,真空度不够可能导致气泡;温度的稳定性均匀性通过温度点检监控,真空度通过真空度表监控。
三、层压机的清洁,包括高温布的清洁,硅胶板的清洁;清洁不干净的后果是背板有凹槽,正面残胶难清洁;每炉及时对高温布进行清洁,每班对层压机硅胶板进行清洁。
四、进料、出料的动作,进料动作粗鲁可能导致裂片,隐裂,盖高温布动作不规范可能导致组件内部移位,出料动作不规范可能导致隐裂;规范操作。
48、层压半成品有哪些不良,怎么控制,
答:
层压工序半成品的不良主要有背板划伤、裂片、隐裂、背板凹槽、气泡、杂质、EVA缺胶、背板与EVA脱层、背板自身分层、汇流带变形、助焊剂发白、移位、色差、黑心片、污染片、汇流带漏焊等。
背板划伤,人为因素导致,规范组件堆放,规范削边、抬板、放板手法;
裂片、隐裂,裂片是由于焊接、层压导致,隐裂导致因素众多,与电池片来料,焊接,层压,均有关联,控制方法是严格控制来料,规范操作手法,焊接温度设置正确,放板、抬板轻拿轻放;
背板凹槽:
层压机清洁不干净,加强清洁,细致用心;
气泡:
与层压工艺设置、层压温度、真空度、物料存放环境、物料本身均有关系,气泡问题需要根据具体情况分析原因,有针对性的解决;
杂质;主要是加强员工自检解决,并控制车间环境,员工着装;
EVA缺胶:
与EVA来料、层压机温度均匀性有关;
背板与EVA分层:
一般是在户外使用过程中出现,层压工序背板与EVA分层与层压工艺和物料有关;
背板自身分层:
来料问题;
汇流带变形:
EVA及背板收缩导致,更改层压工艺参数及引出线方式可以改善;
助焊剂发白:
与烙铁头,助焊剂均有关系,及时更换烙铁头,助焊剂烘干,焊接手法规范均有改善;
移位:
组件未固定,或人为导致,对组件用胶带固定,员工在上板及盖高温布时尽量避免剧烈移动;
色差:
分选导致;
黑芯片、污染片:
来料原因;
汇流带漏焊:
员工操作失误导致
49、我司组件线前工段包括(准备)、(压带)、(串带)、(排板)四大工序。
准备工序分为(准
备玻璃)、(裁剪,,,,背板)、(裁剪折弯涂锡带)、(浸泡涂锡带)、(配片、激光划片)等五
项内容。
50、激光划片的深度为(电池片厚度的1/2至2/3)。
激光划片太浅会导致(掰片困难),划片
过深可能导致(电池片短路)。
51、裁剪EVA/背板必须在(准备车间)进行,裁剪出来的EVA/背板四角为(直角),出线孔的
长度比汇流带宽度宽(1—2mm),出线孔宽度(?
1mm)。
裁剪好的EVA无目视可见的(污迹),(杂
物)等附着在上面,且要在(24)小时内使用完,未裁剪的EVA需(装箱用胶布密封)、(遮光)
0保存在空气相对湿度(<60%),温度(<27C)的环境下。
裁剪好的背板无(划伤)痕迹,裁切处
(平直),无可视毛边。
52、EVA有(毛面)与(光面)之分,毛面可以(增大摩擦力,防止电池片移位);部分背板有
正反面之分,需要区分正反面的背板如果放反可能导致(背板与EVA/硅胶粘结强度下降,背板
的耐候性下降)。
53、裁剪好的涂锡带要求外观(光亮)、(平直),无(蛇形弯),整体为标准(矩形),涂锡带表
面无(刮伤),裁剪口不(倾斜),无(倒刺),若有倒刺必须压平。
需浸泡的涂锡带只限于(互
联条)及(串汇涂锡带),汇流带不需要进行浸泡。
每次浸泡数量不超过(,,,)根,浸泡时
0间约为(30)秒,烘烤温度为(50-60)C,烘烤时间约为(15-20)分钟,以涂锡带表面已经
烘烤(干燥),无(湿润液体残)留为宜。
54、配片包括(电性能)搭配,(颜色)搭配和(数量)搭配,原则上同一块组件的电池片(Pm)
要在同一等级,(Imp)也在同一档,同等级电池片缺少时,应选择Pm和Imp(尽可能接近要求)
的电池片补充。
同一组件内不应混有不同(颜色)分类的电池片,不能有明显(色差)。
不同电
流档电池片一起封装会导致(低电流电池片成为负载,降低功率输出,严重时影响组件使用寿
命)。
55、检查压带、串带焊接质量的方法是做(拉力测试)试验,测试工具(拉力计),测试结果正
面(>4N)背面(>3N)为合格。
56、压带工序温度控制要求为:
加热台温度控制范围为(45--50)?
之间,对于有铅焊接,快
客205H型号烙铁温度(345--365)?
之间,在能保证焊接效果的基础上温度尽可能(低)。
对
焊好的电池片进行检查,要求位置(适中),焊接(牢固),焊接表面(平整光滑),无(断片)、
(破损)、(焊渣)。
焊接温度过低会导致(虚焊),温度过高会(增加破片率)。
57、串带时快客205H型号烙铁头温度范围控制在(355--375)?
之间。
在距离电池片(12mm)
处开始(匀速)焊接,每条涂锡带的焊接时间为(3--5)S。
串带检查时电池串正面、反面不
良点有(虚焊)、(脱焊)、(掉线)、(破片)、(裂片)、(锡渣)、(高点)等。
58、摆片时将已清洁好的玻璃放在台面上,其(粗糙)面也叫(压花)面朝上,然后再将裁剪
好的EVA均匀的平铺在玻璃上,(光滑)面朝上,四周均匀超出玻璃边缘?
(4.5)mm。
59、排版检测时,将电池板放在测试台上,必须保证正面的电池片在(光源)范围内,用(红
色)笔接触电池板引出线(正)极,(黑色)笔接触电池板引出线(负)极。
测试中,万用表应调
节到(电压)档,读取测试值的有效值是在
(2)秒之内。
测试数值?
(0.55V*组件电池总数)
为合格。
60、我司《晶体硅太阳组件检验规范》的参考标准有(IEC61215)(IEC61730)(UL1703)。
61、晶体硅太阳组件检验规范中将太阳组件分为(合格)(不合格)两个等级。
2、、、62、组件电性能测试环境条件必须满足光强(1000)W/m光谱(AM1.5)、温度(25?
-2)
OC。
63、个体组件的电绝缘性能符合IEC61215标准。
即在组件边框与电路间施加(3000)V直流
电压,保持1分钟,然后将“电压调节”旋转到0V,10秒后再将电压调到(1000)V,保持2
分钟。
(旋转速度不能超过500V/S)如果红灯亮表示不合格,红灯不亮表示合格。
即在此过程中
若测试值超过0.05,表示不合格,若测试值没超过0.05,表示合格。
64、随意列举你知道的五项例行检验项目:
(室外暴露、冰雹冲击、湿冻、湿热、TC、热斑耐久、
紫外老化、盐雾测试、机械载荷等)。
65、每块组件上应该有的标志包括:
制造厂商或商标、产品名称及型号、(产品序列号)、主要
电性能参数(Pmax、Isc、Voc、Imp、Vmp)、(接地标识)、(引出端子或引线极性)、认证
标志。
66、电池片到边框之间的空白处允许面积(?
5mm?
)的异物(?
3处),但是异物位置到边框
的距离(?
10mm),所导致两电池串距离(?
1mm)。
67、杂质不能导致两片电池片之间的片距(?
0.5mm)。
68、玻璃标准:
线性气泡L?
3*〈0.5mm允许
(1)处,?
(2mm?
)且?
3处,各气泡之间最小间
距(?
0.6米).不允许有(开放气泡)。
69、背板材料同凸点高度(?
0.2mm),数量不超过(3)个/板.鼓点高度<0.2mm的不能密集出现。
70、电池边缘崩边和U形缺口,长度(?
2mm),深度(?
1mm),允许(2个)/片,(3个)/
板(崩边小片不过栅线)。
71、组件导电部分电池片、涂锡带等到玻璃边缘的距离(?
10mm)。
72、正面气泡距离玻璃边缘(?
5mm),气泡边缘到电池片边缘的距离(?
0.5)mm,其他空白处
?
(3个)/板.
73、如果条形码的位置正确,则条形码旋转(180度)可以接受。
74、边框拼缝间隙(?
0.5mm),长短边框上下平面错位(?
0.5mm).组件两对角线之差(?
3mm)75、边框与玻璃正面应无空胶,用0.3mm塞尺,塞入封间隙深度(?
5mm)。
76、边框B面露底划伤(?
5mm)?
(2)处,坑洼直径?
10mm、深度(?
0.5mm),数量(?
1
处),撞伤、擦伤在1米裸眼观察不明显。
77、接线盒安装位置符合设计要求,位置偏移小于(1cm)。
78、接线盒内清洁无杂物,无空胶。
电极插接可靠,承受(?
30N)拉力电极不脱出,输出极性
正确,引线之间间距根据接线盒内部确定,符合(IEC61730)电气安全要求。
79、用一级标准组件校准二级标准组件的周期为(每月)一次。
80、月校准过程中组件连续测试5次,其Pmax平均值在外校标定值Pamx(?
0.5%)以内。
81、日常生产过程的校准:
每
(2)小时测试二级标准组件,至少测试3次,其Pmax的平均
值在该标准组件标定值Pmax的(?
1%)以内,且怎样换算(测试值减标准值/标准值*100%)。
82、下打光(BSSA60)测试仪校准过程中怎样换算电压、电流修正系数(用标准值除以测试
值)。
83、下打光(BSSA60)测试仪准过程中电压温度系数=(电池片温度系数(-2.5mv)*电池组件电
池片总数量)正确填入后点击确定,此时测试系统将根据所测实际温度自动进行补尝、校准。
84、将标准电池组件置于测试仪台面中央位置,将组件测试线插接在测试仪测试插座上,红色
夹子接组件(正级),黑色夹子接组件(负极)。
85、下打光(BSSA60)测试仪测试完成后要导出数据首先点击(停止测量),然后再点击“摘
要到文件”;若忘记点击(停止测量),而进行了其他操作,则会导致系统反应缓慢。
86、我司使用的太阳电池组件测试仪DLSK-SOL3型、在测试前须将组件放入测试缓冲区,至少
2缓冲2小时。
在太阳能电池-组件测试系统的调试校准中要求标准光强达到(100)mw/cm,
22其误差范围允许在(99.9)mw/cm到(100.1)mw/cm之间。
87、标准组件用专用的不锈钢组件加保存,环境温度(18,T,28?
),相对湿度在
(40%-70%)之间,遮光保存,对当天使用的标准组件使用完毕后,清理干净放回存储架。
88、组件EL测试常见不良有(隐裂)、(黑栅)、(裂片)、(低效片)、(黑心片)等,EL测试不
良会导致(降低组件功率输出,严重的会直接缩短组件使用寿命)。
89、背板的结构由多层高分子薄膜经碾压黏合起来的复合膜,主要由三层组成:
含氟膜(或其
替代物)+PET层(或其替代物)+与EVA粘结层(有含氟膜、改性EVA、PE、PET等)。
90、背板的特点:
(ABCD)
A、优异的耐侯性B、低的水汽渗透率C、良好的电绝缘性D、一定的粘结强度91、EVA胶膜在未层压前是线性大分子,当受热时,交联剂分解,形成活性自由基,引发EVA
分子间反应形成网状结构。
从而提高EVA的力学性能、耐热性、耐溶剂性、耐老化性。
92、常见的EVA失效方式:
发黄、气泡、脱层。
93、EVA发黄由两个因素导致:
主要是添加剂体系相互反应发黄;其次EVA自身分子在氧气、
光照条件下,EVA分子自身脱乙酰反应导致发黄,所以EVA的配方决定其抗黄变性能的好坏。
94、脱层:
分与背板脱层(交联度不合格,与背板粘结强度差);与玻璃脱层(硅烷偶联剂缺陷,
玻璃脏污,硅胶封装性能差,交联度不合格)。
95、光伏行业对硅胶的总体性能要求:
具有弹性与应变能力、良好的电绝缘性能、良好的耐气
候性能、粘接、密封性能可靠不失效。
96、常见的硅胶失效方式:
自身老化、剥离强度差、剪切强度差、封装不良。
97、接线盒主要由上盖、密封圈(灌封接线盒无)、二极管、连接装置、散热装置(取决于接线
盒的设计)、盒体组成。
98、接线盒常见的失效方式二极管失效、接线盒材料老化、密封失效
99、在TPT/TPE原材料检验中TPE厚度要求>0.17mm;TPT厚度要求>0.32mm。
长宽尺寸与请购
单相符合,长度公差为?
2m,宽度公差为?
1mm,厚度均匀性?
5%
100、涂锡带原材料检验中厚度尺寸公差为?
0.02mm,宽度尺寸公差为?
0.2mm101、常用接线盒为QC(二极管有PVS1545和10SQ050两类)与MC(二极管为SB1240)
二、判断题
102、纠正措施是指为消除潜在的不合格的原因所采取的措施。
(×)
103、“清扫”就是在生产现场进行卫生大扫除。
(×)
104、当生产过程处于控制状态时,产品质量就不会发生波动。
(×)
105、顾客是接受产品的组织或个人,包括现实顾客和潜在顾客。
(?
)106、经过抽样检验判为合格的一批产品,都是合格品。
(×)
107、一洗硅片出漂洗槽后应尽量保持硅片表面湿润,防止硅酸钠不能随水一起甩掉,残
留在硅片上影响外观。
(?
)108、二次清洗后硅片表面可以有水膜,只需经过甩干后表面无水珠即可判定表面磷硅玻去除干
净(×)109、二次清洗后如硅片放置时间过长,表面会被氧化,从而影响PECVD效果(?
)
PECVD镀膜时,膜越厚薄膜的颜色越深,膜越浅薄膜颜色也越浅。
(?
)110、电池片正面电极极性为正,背面电极极性为负。
„„„„„„„„„„„(?
)111、STC是指“标准测试条件”„„„„„„„„„„„„„„„„„„„„(?
)112、Ipm是指“最大工作电流”;Rs指“并联电阻”。
„„„„„„„„„„(?
)113、CSG太阳电池产品的额定工作温度为:
―40?
,,90?
„„