IR CONVEC air.docx
《IR CONVEC air.docx》由会员分享,可在线阅读,更多相关《IR CONVEC air.docx(16页珍藏版)》请在冰豆网上搜索。
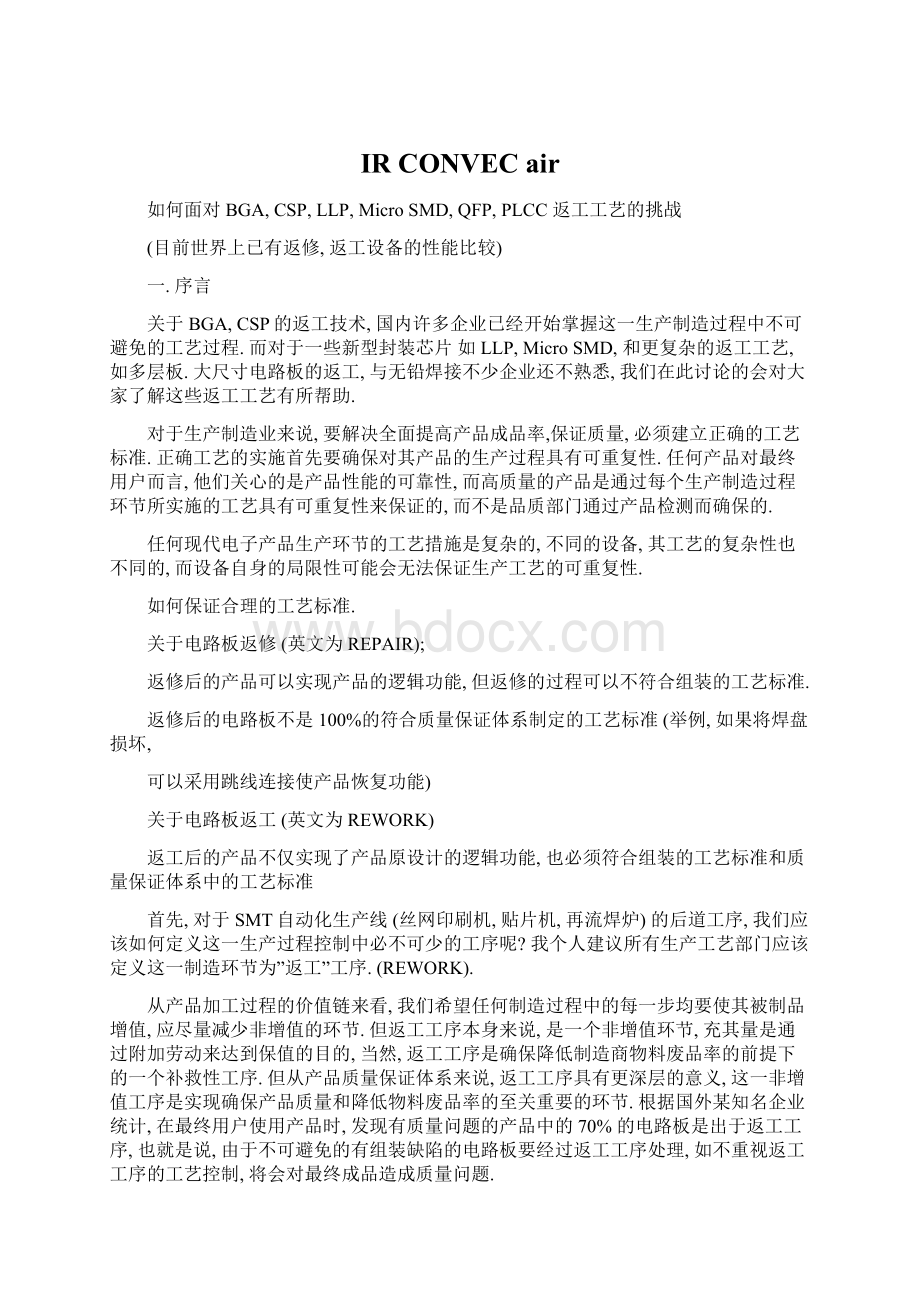
IRCONVECair
如何面对BGA,CSP,LLP,MicroSMD,QFP,PLCC返工工艺的挑战
(目前世界上已有返修,返工设备的性能比较)
一.序言
关于BGA,CSP的返工技术,国内许多企业已经开始掌握这一生产制造过程中不可避免的工艺过程.而对于一些新型封装芯片如LLP,MicroSMD,和更复杂的返工工艺,如多层板.大尺寸电路板的返工,与无铅焊接不少企业还不熟悉,我们在此讨论的会对大家了解这些返工工艺有所帮助.
对于生产制造业来说,要解决全面提高产品成品率,保证质量,必须建立正确的工艺标准.正确工艺的实施首先要确保对其产品的生产过程具有可重复性.任何产品对最终用户而言,他们关心的是产品性能的可靠性,而高质量的产品是通过每个生产制造过程环节所实施的工艺具有可重复性来保证的,而不是品质部门通过产品检测而确保的.
任何现代电子产品生产环节的工艺措施是复杂的,不同的设备,其工艺的复杂性也不同的,而设备自身的局限性可能会无法保证生产工艺的可重复性.
如何保证合理的工艺标准.
关于电路板返修(英文为REPAIR);
返修后的产品可以实现产品的逻辑功能,但返修的过程可以不符合组装的工艺标准.
返修后的电路板不是100%的符合质量保证体系制定的工艺标准(举例,如果将焊盘损坏,
可以采用跳线连接使产品恢复功能)
关于电路板返工(英文为REWORK)
返工后的产品不仅实现了产品原设计的逻辑功能,也必须符合组装的工艺标准和质量保证体系中的工艺标准
首先,对于SMT自动化生产线(丝网印刷机,贴片机,再流焊炉)的后道工序,我们应该如何定义这一生产过程控制中必不可少的工序呢?
我个人建议所有生产工艺部门应该定义这一制造环节为”返工”工序.(REWORK).
从产品加工过程的价值链来看,我们希望任何制造过程中的每一步均要使其被制品增值,应尽量减少非增值的环节.但返工工序本身来说,是一个非增值环节,充其量是通过附加劳动来达到保值的目的,当然,返工工序是确保降低制造商物料废品率的前提下的一个补救性工序.但从产品质量保证体系来说,返工工序具有更深层的意义,这一非增值工序是实现确保产品质量和降低物料废品率的至关重要的环节.根据国外某知名企业统计,在最终用户使用产品时,发现有质量问题的产品中的70%的电路板是出于返工工序,也就是说,由于不可避免的有组装缺陷的电路板要经过返工工序处理,如不重视返工工序的工艺控制,将会对最终成品造成质量问题.
返工的目的:
如前所述,返工过的电路板为了保证在质量上符合产品的原设计要求,采用相同的制造过程的工艺标准是必须的,使其确保返工的焊接具有过程控制的一致性.换句话说,保持产品的功能,参数,质量标准的一致性是与下述紧密相关的:
1.电路板结构设计合理性
2.电路板质量
3.助焊剂质量
4.焊膏质量
5.使用的返工设备性能
6.操作者技能
随着新型元器件的大量使用和生产过程中对质量的严格控制,人们越来越关心我们所使用的返工设备是否具有对焊接的各个温区在开放式加热条件下保持严格的过程控制.这种控制不单指设备自动化程度的高低,而是强调设备是否能对各种芯片,各种电路板进行有效的再流焊接的过程控制.如果设备本身对焊接过程缺乏可调控性,换句话说,设备本身并不具备焊接的全过程控制,在实际生产中则很难保持产品的一致性.
二.返工设备的主要加热特性要求
目前市场上的返修,返工设备品种较多,各种设备的组成与加热方式也有所区别.对这些设备的加热特性要求主要有:
1.芯片对中和贴片
●大部分设备采用光学系统,精度为0.001英寸
2.顶部加热方式
●要求可以自由控制升,降温斜率,加热体应具有低密度,热惰性小的性能
3.喷嘴结构
●要求温度均匀,对角线的温差deltaT小
4.底部加热方式
●要求能满足电路板对角线的温差小,加热体应具有低密度,热惰性小的性能.
5.降温过程
●要求可以控制降温斜率,这是取得再流焊区的必要条件
Reflow时间(30-60秒);无铅焊接reflow时间(15-30秒)
6.操作软件
●要求可以实现动态温度调整
7.各个稳区的风量调整
●要求可以调整风量,尤其对超小型芯片的焊接是重要的.如果不能调整风量,就难以自动控制升,降温斜率,很难在各个温区特别严格的过程控制.
以上功能组合形成系统后的优劣,决定了该系统能否正确完成对不同尺寸,不同层数,不同芯片的再流焊接曲线在各个温区的正确设立,并取得有效地焊接过程控制.最理想的设备应能最大限度地完成上述的主要的7项任务.
三.红外与热风加热方式的性能比较
现在,不同厂家采用的加热技术不同,以下是它们的比较:
厂家
顶部加热方式
底部加热方式
降温方式
热惰性比较
厂家ERSA
红外
红外
移动电路板
热惯性大
厂家PACE
热风
红外
外部风扇
热惯性大
厂家Z-VAC
热风
红外/散热器
顶部,底部同时降温
热惯性大
OK
热风/旁路降温(CoolingbyPass)
热风
顶部,底部同时降温
热惯性小
由上述的比较可以发现,目前厂家采用的加热方式主要有2种:
红外与热风.它们究竟有什么区别,以下稍作分析:
早在1992年美国OK国际公司就推出了第一台采用红外加热的返工系统,由于红外加热技术的局限性,产品推出后,只在全世界销售了仅5台后,OK公司决定开发独特的全热风加热系统以满足各种芯片,电路板的返工需求.此后一系列全热风返工产品面世,如BGA-2000,BGA-3000,BGA3500,APR-5000,APR-5000XL.
目前各个厂家采用了不同的加热方式技术,而只有美国OK公司的返工设备采用了与全自动再流焊炉所采用的全控制热风式加热技术.而其它厂家有的考虑了制造成本,或对电子组装技术的发展考虑不周,或受到自身技术的局限性而采取了红外加热(RedLightHeaters),或所谓暗红外加热技术(CeramicHeaters)
IR与全过程控制热风加热技术的性能比较:
IR红外加热全过程控制热风加热
加热器成本低,热量控制难度大容易控制热容量
升温,降温反应慢升温,降温快速反应
很难降温容易控制降温
芯片封装材质吸收热容量不同不受芯片材质影响
由于IR是点热源加热电路板易变形电路板均匀加热不易变形
对厚电路板加热不容易均匀对厚板子加热容易均匀
单芯片返工需满足的焊接条件:
芯片表面对角线温差:
有铅焊接一般要求芯片表面对
角线温差不大于10摄氏度
无铅焊接要求芯片表面对角线
温差不大于5摄氏度
为什么全热风加热优于红外加热系统
由于红外加热技术的致命缺陷是点加热源,红外直接对物体加热会造成热能量穿透芯片再达到焊球(如是BGA芯片),红外加热的能量输出是通过调节如照相机的光圈大小来控制.被加热芯片表面颜色不同,材质不同吸收热能量(红外线波长)也不同.制造商通常采用陶瓷材料加热体结构红外热源,业内称为陶瓷散热器CeramicHeaterRadiator.红外顶部加热会造成芯片壳体的温度大大高于焊脚的温度,如下图为德国某公司对BGA采用红外顶部加热产生的温度曲线.BGA芯片温度高达246.5C.而焊球温度为189C.这对芯片很容易造成过热损伤.
红色曲线为BGA封装温度
绿色曲线为PCB本温度
蓝色曲线为BGA焊点温度
下面是美国OK公司热风喷嘴中对44毫米正方形PBGA的温差测量曲线.由于OK公司采用了独特的喷嘴设计,采用RTD作为测温传感器,而其它厂家使用TC为传感器,由此看出,喷嘴内的温度是均匀的.
举例1.用红外加热焊接非正方形芯片
由于红外加热设备不采用喷嘴,几乎是对正方形面积的垂直加热,如果芯片是长方形的,相邻的元器件的焊点将不可避免的遭受二次溶锡
非正方形芯片
红外加热区域
红外同时加热相邻器件,热风喷嘴可以避免对相邻器件加热
红外加热能量分布
具有全热风加热的设备(美国OK公司的BGA-3592G,APR-5000,APR-5000XL),采用热风喷嘴的焊接,可以控制不影响相邻的元器件.
举例2.红外加热会同时加热芯片体和焊角
红外加热同时将QFP芯片体和焊脚同时加热,热风喷嘴可以只对焊脚加热
热风喷嘴可以设计为只对芯片管脚局部加热,避免对芯片体加热
具有全热风加热的设备(美国OK公司的BGA-3592G,APR-5000,APR-5000XL),可以只对芯片焊脚加热,而尽量降低芯片客体的热冲击.
举例3.红外加热会造成LLP芯片焊点同焊盘错位
LLP芯片焊接过程中形成”芯片自移动”(ChipSwimming)
由于红外加热对于芯片封装,焊脚,电路板很难形成均匀加热,并且很难控制其温度
的升温,降温斜率(单位时间内的升温,降温是取得再流焊接曲线的基本条件).因此下面的LLP芯片如采用红外加热焊接设备要取得正确焊接几乎是不可能的.
美国国家半导体公司的LLP封装为无焊脚,芯片中心为接地焊盘.因此要求单芯片返工设备必须具有完全的均匀加热和对升温,降温区的全过程控制
全热风加热的设备(美国OK公司的BGA-3592G,APR-5000,APR-5000XL)可以很好的控制LLP的可靠焊接(可参见美国国家半导体的网站,)
举例`4.红外加热很难在焊接塑料插接头
由于红外加热的热能量必须通过物体达到焊点(红外线不能象热风一样对流加热)
因此,对任何塑料接插件都会在焊接过程中造成插件变形.尤其对PLCC插座的焊接会造成变形,使芯片同插座不能形成可靠的接触
具有全热风加热的设备(美国OK公司的BGA-3592G,APR-5000,APR-5000XL),可以保证塑料插座的可靠焊接
举例5.红外加热不能焊接立体封装的芯片(模块式,采用多层间相同熔点焊接)
如下图所示,这是模块式封装电路,模快同电路板焊接,模块同屏蔽罩焊接.制造中
为了返工模块内芯片,必须只将屏蔽罩焊下,有时要求将整个模块焊下而不将屏蔽罩取下.实践证明采用红外顶部加热/红外底部加热,或热风顶部加热/红外底部加热
的设备几乎不能完成这类器件的返工.由于OK公司采用全热风加热系统,完成此类
选择性焊接是可行的.
具有全热风加热的设备(美国OK公司的BGA-3592G,APR-5000,APR-5000XL),可以完成这种极为复杂的焊接.
面对更高要求的返工工艺的挑战-无铅焊接
无铅焊接过程中,返工设备必须保证芯片表面温度,焊点温度,电路板底部的温度差小于10摄氏度.见下图.(比有铅焊接的要求高)
1.由于红外加热为高密度(CeramicHeaterRadiator)加热体,尽管加热系统采用了温度反馈控制,但加热体仍然会产生对芯片的温度过冲.即便将温度过冲控制到某种程度,
由于红外加热是辐射式加热如同暖气片加热,关断热源后,热能仍然会辐射到被加热
电路板上,因此采用红外加热的返修系统不能控制降温曲线,也就是说不能很好地控制再流焊区的形成.一般红外加热设备厂家均采用了非过程控制的解决方法,有的用户可能没有注意到由此产生的问题.为解决此问题,有的厂家采用当芯片完成再流焊时,将一个外接风扇启动给电路板降温.也有的采用当芯片完成再流焊时,将电路板从底部加热区上部移开.但这些方法并不能很好的解决此问题.
为了减少红外加热的不均匀性,一般BGA返修台的底部加热采用红外加热技术的生产厂家会在红外加热源的上面附加一个金属散热板来克服加热不均匀的缺陷(全金属板状,带孔金属网状),但加热仍然是靠辐射出红外波长传递能量的红外加热源.仍难以从根本上解决不均匀加热的问题.采用金属,陶瓷等高密度散热材料可以一定程度地改善加热的均匀性,由于热惰性大,降温有困难,因此,采用底部红外加热技术的设备不能很好的控制再流焊接区的形成.
2.因为芯片焊脚的温度永远高于整体电路板的温度,底部加热采用红外加热的不均匀性会造成电路板的变形,这一变形造成电路板上的其它元器件的焊点受到很大的变形应力,结果整个电路板在单芯片返工后的可靠性成为不可预测.对大尺寸电路板,多层板,带有大面积接地布线的电路板,采用红外加热技术的设备进行可靠焊接几乎是不可能的.
由于底部加热不均匀性造成的电路板翘变而形成的焊接桥连
3.红外加热很难形成正确的再流焊接曲线,而返工的定义是全焊接过程要符合原产品的生产制造工艺参数.对于不同的封装结构芯片,在进行单芯片返工时,使用设备必须具备灵活调整顶部,底部热能量的输出,从而获得最佳的温度再流焊接曲线.
无铅焊接工艺对使用设备的要求:
●设备需要有功率更大的底部加热体
●四个温度控制区
●较高的再流焊接温度(235摄氏度)
●较短的回流焊时间15-30秒(REFLOW)
●较小的温差(芯片体,芯片焊脚,PCB之间)
●快速的降温速率
由此可见,采用红外加热技术的设备由于存在不可克服的缺点,如升,降温慢,均匀性差,加热体热惰性大等自身利益技术的局限性,并不可能满足上述无铅焊接的基本要求.
下面的表格列出无铅焊接与有铅焊接的主要不同之处
下面的典型的无铅焊接温度&时间关系曲线.
下面是采用OK公司APR-5000对于44毫米正方形BGA进行无铅焊接实际曲线.
采用三个TC(热电藕)的测试结果:
TC1放在芯片壳体上
TC2放在芯片焊球上
TC3放在PCB的底部
曲线表明,在4个焊接温区,TC1,TC2,TC3之间的温度差始终保持在5-7摄氏度
总结
返工的核心问题是,如何实现最佳再流焊曲线
一旦电路板结构和板上元器件分布确定, 对于焊接而言, 这个电路板就只有一条最佳的再流焊接曲线来实现最佳的焊接.这就对工艺人员构成了直接的挑战.如何取得最佳焊接条件. 在返工过程中,由于使用的设备,附料等变量的局限性,工艺人员有时不得不作出各种折衷的选择.但是形成完善的工艺条件应该是质量保证的最高标准.
不论设备采用何种加热方式反馈控制电路, 单芯片返工设备对整个电路板而言是一个开放式加热设备,因此, 不同于再流焊炉是在全封闭状态下进行焊接过程控制.由于被返工芯片周围已经有了其它元器件,目前世界上的单芯片返修(无过程控制系统);和单芯片返工系统(全过程控制)均采用开放式加热系统.因此,(无论是红外(IR,DarkIR),散热板(HotPlate); 红外&散热板(IR&HotPlate)还是热风加热系统(ConvectionAir),都面临着同样的技术要求,即如何控制再流焊接曲线接近或重复批量生产中SMT再流焊炉的焊接曲线.
1.如何判断返工设备是否为全过程控制,只要鉴别在焊接过程的每个独立区域
●预热区
●温度饱和区
●再流焊区
●降温区
能否进行独立的升,降温控制和形成对元元器件均匀加热.这个技术指标应满足完成对不同的电路板和元器件的正确焊接.
参考文献:
PaulWood,BGA,CSPspecialistofOKInternationalUSA
OKInternational产品说明书, 技术支持文献
奥科电子实验数据, 图表.