第5章蜗杆传动机构.docx
《第5章蜗杆传动机构.docx》由会员分享,可在线阅读,更多相关《第5章蜗杆传动机构.docx(18页珍藏版)》请在冰豆网上搜索。
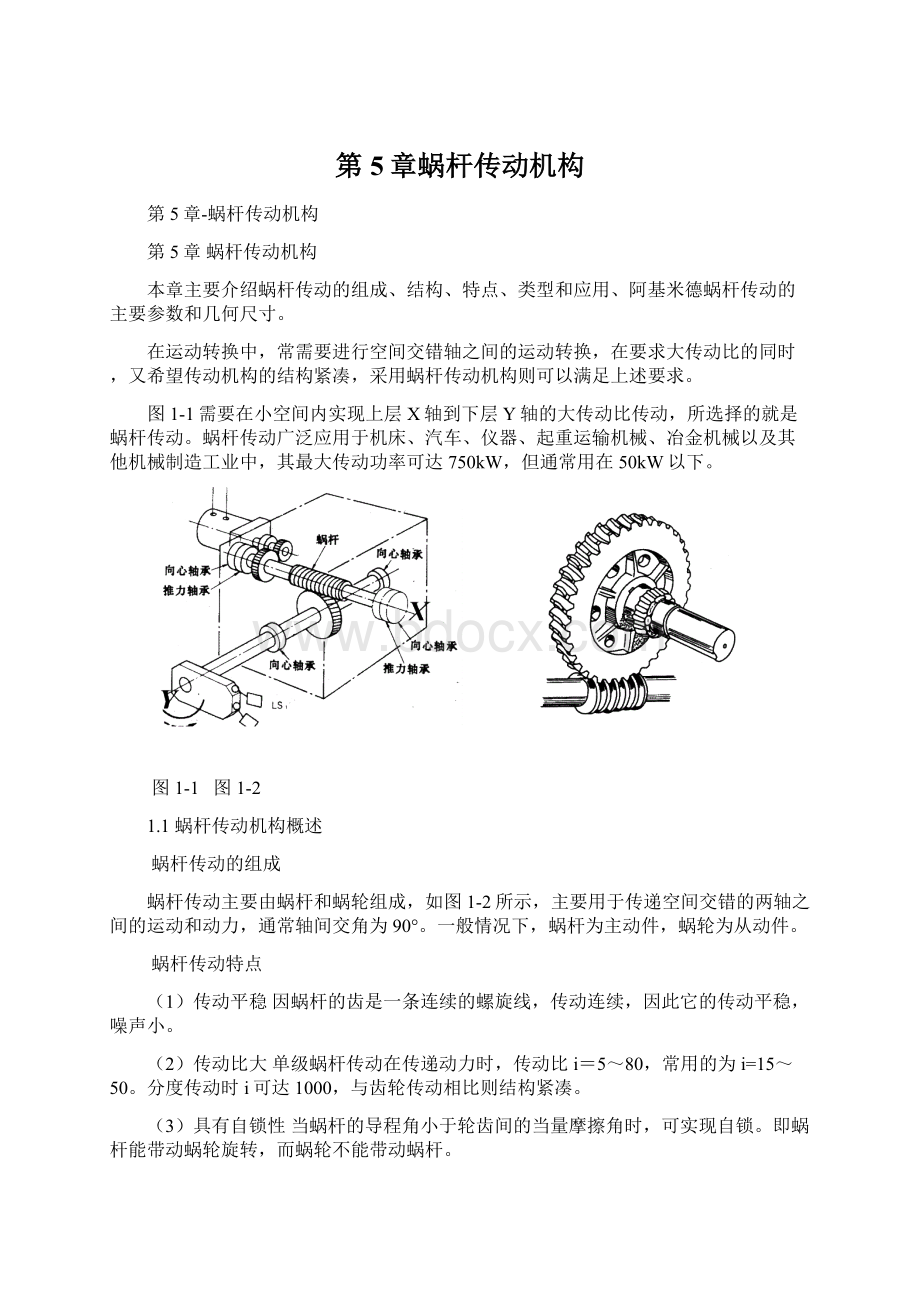
第5章蜗杆传动机构
第5章-蜗杆传动机构
第5章蜗杆传动机构
本章主要介绍蜗杆传动的组成、结构、特点、类型和应用、阿基米德蜗杆传动的主要参数和几何尺寸。
在运动转换中,常需要进行空间交错轴之间的运动转换,在要求大传动比的同时,又希望传动机构的结构紧凑,采用蜗杆传动机构则可以满足上述要求。
图1-1需要在小空间内实现上层X轴到下层Y轴的大传动比传动,所选择的就是蜗杆传动。
蜗杆传动广泛应用于机床、汽车、仪器、起重运输机械、冶金机械以及其他机械制造工业中,其最大传动功率可达750kW,但通常用在50kW以下。
图1-1图1-2
1.1蜗杆传动机构概述
蜗杆传动的组成
蜗杆传动主要由蜗杆和蜗轮组成,如图1-2所示,主要用于传递空间交错的两轴之间的运动和动力,通常轴间交角为90°。
一般情况下,蜗杆为主动件,蜗轮为从动件。
蜗杆传动特点
(1)传动平稳因蜗杆的齿是一条连续的螺旋线,传动连续,因此它的传动平稳,噪声小。
(2)传动比大单级蜗杆传动在传递动力时,传动比i=5~80,常用的为i=15~50。
分度传动时i可达1000,与齿轮传动相比则结构紧凑。
(3)具有自锁性当蜗杆的导程角小于轮齿间的当量摩擦角时,可实现自锁。
即蜗杆能带动蜗轮旋转,而蜗轮不能带动蜗杆。
(4)传动效率低蜗杆传动由于齿面间相对滑动速度大,齿面摩擦严重,故在制造精度和传动比相同的条件下,蜗杆传动的效率比齿轮传动低,一般只有0.7~0.8。
具有自锁功能的蜗杆机构,效率则一般不大于0.5。
(5)制造成本高为了降低摩擦,减小磨损,提高齿面抗胶合能力,蜗轮齿圈常用贵重的铜合金制造,成本较高。
蜗杆传动的类型
蜗杆传动按照蜗杆的形状不同,可分为圆柱蜗杆传动(图1-3a)、环面蜗杆传动(图1-3b)。
圆柱蜗杆传动除与图1-3a相同的普通蜗杆传动,还有圆弧齿蜗杆传动(图1-3c)。
圆柱蜗杆机构又可按螺旋面的形状,分为阿基米德蜗杆机构和渐开线蜗杆机构等。
圆柱蜗杆机构加工方便,环面蜗杆机构承载能力较高。
c)
图1-3
蜗杆传动的失效形式及设计准则
由于蜗杆传动中的蜗杆表面硬度比蜗轮高,所以蜗杆的接触强度、弯曲强度都比蜗轮高;而蜗轮齿的根部是圆环面,弯曲强度也高、很少折断。
蜗杆传动的主要失效形式有胶合、疲劳点蚀和磨损。
由于蜗杆传动在齿面间有较大的滑动速度,发热量大,若散热不及时,油温升高、粘度下降,油膜破裂,更易发生胶合。
开式传动中,蜗轮轮齿磨损严重,所以蜗杆传动中,要考虑润滑与散热问题。
蜗杆轴细长,弯曲变形大,会使啮合区接触不良。
需要考虑其刚度问题。
蜗杆传动的设计要求:
(1)计算蜗轮接触强度;
(2)计算蜗杆传动热平衡,限制工作温度,(3)必要时验算蜗杆轴的刚度。
蜗杆、蜗轮的材料选择
基于蜗杆传动的失效特点,选择蜗杆和蜗轮材料组合时,不但要求有足够的强度,而且要有良好的减摩、耐磨和抗胶合的能力。
实践表明,较理想的蜗杆副材料是:
青铜蜗轮齿圈匹配淬硬磨削的钢制蜗杆。
(1)蜗杆材料
对高速重载的传动,蜗杆常用低碳合金钢(如20Cr、20CrMnTi)经渗碳后,表面淬火使硬度达56~62HRC,再经磨削。
对中速中载传动,蜗杆常用45钢、40Cr、35SiMn等,表面经高频淬火使硬度达45~55HRC,再磨削。
对一般蜗杆可采用45、40等碳钢调质处理(硬度为210~230HBS)。
(2)蜗轮材料
常用的蜗轮材料为铸造锡青铜(ZCuSnl0Pl,ZCuSn6Zn6Pb3)、铸造铝铁青铜(ZCuAl10Fe3)及灰铸铁HTl50、HT200等。
锡青铜的抗胶合、减摩及耐磨性能最好,但价格较高,常用于vs≥3m/s的重要传动;铝铁青铜具有足够的强度,并耐冲击,价格便宜,但抗胶合及耐磨性能不如锡青铜,一般用于vs≤6m/s的传动;灰铸铁用于vs≤2m/s的不重要场合。
1.2蜗杆传动机构的基本参数和尺寸
蜗杆机构的正确啮合条件
1.中间平面我们将通过蜗杆轴线并与蜗轮轴线垂直的平面定义为中间平面,如图1-4所示。
在此平面内,蜗杆传动相当于齿轮齿条传动。
因此这个下面内的参数均是标准值,计算公式与圆柱齿轮相同。
图1-4
2.正确啮合条件根据齿轮齿条正确啮合条件,蜗杆轴平面上的轴面模数mx1等于蜗轮的端面模数mt2;蜗杆轴平面上的轴面压力角αx1等于蜗轮的端面压力角αt2;蜗杆导程角γ等于蜗轮螺旋角β,且旋向相同,即
mx1=mt2=m
αx1=αt2=α(1-1)
γ=β
基本参数
1.蜗杆头数z1,蜗轮齿数z2
蜗杆头数z1一般取1、2、4。
头数z1增大,可以提高传动效率,但加工制造难度增加。
蜗轮齿数一般取z2=28~80。
若z2<28,传动的平稳性会下降,且易产生根切;若z2过大,
蜗轮的直径d2增大,与之相应的蜗杆长度增加、刚度降低,从而影响啮合的精度。
2.传动比
(1-2)
3.蜗杆分度圆直径d1和蜗杆直径系数q
加工蜗轮时,用的是与蜗杆具有相同尺寸的滚刀,因此加工不同尺寸的蜗轮,就需要不同的滚刀。
为限制滚刀的数量,并使滚刀标准化,对每一标准模数,规定了一定数量的蜗杆分度圆直径d1。
蜗杆分度圆直径与模数的比值称为蜗杆直径系数,用表示,即
(1-3)
模数一定时,q值增大则蜗杆的直径d1增大、刚度提高。
因此,为保证蜗杆有足够的刚度,小模数蜗杆的q值一般较大。
4.蜗杆导程角γ
(1-4)
式中L—螺旋线的导程,L=z1px1=z1πm,其中px1为轴向齿距
通常螺旋线的导程角γ=3.5°~27°,导程角在(3.5°~4.5°)范围内的蜗杆可实现自锁,升角大时传动效率高,但蜗杆加工难度大。
蜗杆传动的基本尺寸计算
标准圆柱蜗杆传动的几何尺寸计算公式见表1-1。
蜗杆传动的结构
1.蜗杆的结构如图1-5,一般将蜗杆和轴作成一体,称为蜗杆轴。
2.蜗轮的结构如图1-6,一般为组合式结构,齿圈用青铜,轮芯用铸铁或钢。
图a为组合式过盈联接这种结构常由青铜齿圈与铸铁轮芯组成,多用于尺寸不大或工作温度变化较小的地方。
图b为组合式螺栓联接这种结构装拆方便,多用于尺寸较大或易磨损的场合。
图c为整体式主要用于铸铁蜗轮或尺寸很小的青铜蜗轮。
图d为拼铸式将青铜齿圈浇铸在铸铁轮芯上,常用于成批生产的蜗轮。
图1-5
a)b)c)d)
图1-6
表1-1标准普通圆柱蜗杆传动几何尺寸计算公式
名称
计算公式
蜗杆
蜗轮
齿顶高
ha=m
ha=m
齿根高
hf=1.2m
hf=1.2m
分度圆直径
d1=mq
d2=mz2
齿顶圆直径
da1=m(q+2)
da2=m(z2+2)
齿根圆直径
df1=m(q–2.4)
df2=m(z2–2.4)
顶隙
c=0.2m
蜗杆轴向齿距
蜗轮端面齿距
p=mπ
蜗杆分度圆柱的导程角
蜗轮分度圆上轮齿的螺
旋角
β=λ
中心距
a=m(q+z2)/2
蜗杆螺纹部分长度
z1=1、2,b1≥(1l十0.06z2)m
z1=4,b1≥(12.5十0.09z2)m
蜗轮咽喉母圆半径
rg2=a-da2/2
蜗轮最大外圆直径
z1=1、de2≤da2十2m
z1=2、de2≤da2十1.5m
z1=4、de2≤da2十m
蜗轮轮缘宽度
z1=1、2,b2≤0.75da1
z1=4,b2≤0.67da1
蜗轮轮齿包角
θ=2arcsin(b2/d1)
一般动力传动θ=70°-90°
高速动力传动θ=90°-130°
分度传动θ=45°-60°
表1-2蜗杆基本参数配置表
模数m
mm
分度圆直径d1
mm
蜗杆头数z1
直径系数q
m3q
模数m
mm
分度圆直径d1
mm
蜗杆头数z1
直径系数q
m3q
1
18
1
18.000
18
6.3
(80)
1,2,4
12.698
3175
1.25
20
1
16.000
31
112
1
17.798
4445
22.4
1
17.920
35
8
(63)
1,2,4
7.875
4032
1.6
20
1,2,4
12.500
51
80
1,2,4,6
10.000
5120
28
1
17.500
72
(100)
1,2,4
12.500
6400
2
18
1,2,4
9.000
72
10
1
17.500
8960
22.4
1,2,4,6
11.200
90
10
71
1,2,4
7.100
7100
(28)
1,2,4
1.000
112
90
1,2,4,6
9.000
9000
35.5
1
17.750
12
(112)
1
11.200
11200
2.5
(22.4)
1,2,4
8.960
10
160
1
16.000
16000
28
1,2,4,6
11.200
175
12.5
(90)
1,2,4
7.200
1062
(35.5)
1,2,4
1.200
222
112
1,2,4
8.960
17500
45
1
18.000
281
(10)
1,2,4
11.200
21875
3.15
(28)
1,2,4
8.889
278
200
1
16.000
31250
35.5
1,2,4,6
11.270
352
16
(112)
1,2,4
7.000
28672
(45)
1,2,4
1.286
447
10
1,2,4
8.750
35840
56
1
17.778
556
(180)
1,2,4
11.250
46080
4
(31.5)
1,2,4
7.875
504
250
1
15.625
64000
40
1,2,4,6
10.000
640
20
(10)
1,2,4
7.000
56000
(50)
1,2,4
12.500
800
160
1,2,4
8.000
64000
71
1
17.750
1136
(224)
1,2,4
11.200
89600
5
(40)
1,2,4
8.000
1000
315
1
15.750
126000
50
1,2,4,6
10.000
1250
25
(180)
1,2,4
7.200
112500
(63)
1,2,4
12.600
1575
200
1,2,4
8.000
125000
90
1
18.000
22500
(280)
1,2,4
11.200
175000
6.3
(50)
1,2,4
7.936
1984
400
1
16.000
250000
63
1,2,4,6
10.000
2500
注:
表中分度圆直径d1的数字,带( )的尽量不用;黑体的为γ<3°30′的自锁蜗杆。
蜗杆传动的受力分析
蜗杆传动的受力分析与斜齿圆柱齿轮的受力分析相似,齿面上的法向力Fn分解为三个相互垂直的分力:
圆周力Ft、轴向力Fa、径向力Fr,如图1-7。
蜗杆受力方向:
轴向力Fa1的方向由左、右手定则确定,图1-7为右旋蜗杆,则用右手握住蜗杆,四指所指方向为蜗杆转向,拇指所指方向为轴向力Fa1的方向;圆周力Ft1,与主动蜗杆转向相反;径向力Fr1,指向蜗杆中心。
蜗轮受力方向:
因为Fa1与Ft2、Ft1与Fa2、Frl与Fr2是作用力与反作用力关系,所以蜗轮上的三个分力方向,如图1-7所示。
Fa1的反作用力Ft2是驱使蜗轮转动的力,所以通过蜗轮蜗杆的受力分析也可判断它们的转向。
径向力Fr2指向轮心,圆周力Ft2驱动蜗轮转动,轴向力Fa2与轮轴平行。
力的大小可按下式计算:
(1-5)
式中—α=20︒
图1-7
1.3蜗杆传动的设计
蜗杆传动的强度计算方法
在中间平面内,蜗杆与蜗轮的啮合相当于齿条与斜齿轮啮合,因此蜗杆传动的强度计算方法与齿轮传动相似。
对于钢制的蜗杆,与青铜或铸铁制的蜗轮配对,其蜗轮齿面接触强度设计公式为:
(1-6)
式中,K为载荷系数,引入是为了考虑工作时载荷性质、载荷沿齿向分布情况以及动载荷影响,一般取K=1.1~1.3;T2(N⋅mm)为蜗轮上的转矩;z2为蜗轮齿数
[σH]为蜗轮许用接触应力,可查表1-3、表1-4获得。
表1-3锡青铜蜗轮的许用接触应力[σH]MPa
蜗轮材料
铸造方法
适用的滑动速度
vs/(m/s)
蜗杆齿面硬度
≤350HBS
>45HRC
ZCuSn10P1
砂 型
≤12
180
200
金属型
≤25
200
220
ZCuSn6Zn6Pb3
砂 型
≤10
110
125
金属型
≤12
135
150
表1-4铝铁青铜及铸铁蜗轮的许用接触应力[σH]MPa
蜗轮材料
蜗杆材料
滑动速度vs/(m/s)
0.5
1
2
3
4
6
8
ZCuAl10Fe3
淬火钢
250
230
210
180
160
120
90
HT150
HT200
渗碳钢
130
115
90
-
-
-
-
HT150
调质钢
110
90
70
-
-
-
-
*蜗杆未经淬火时,需将表中许用应力值降低20%。
蜗杆传动的热平衡计算
1.蜗杆传动时的滑动速度
蜗杆和蜗轮啮合时,齿面间有较大的相对滑动,相对滑动速度的大小对齿面的润滑情况、齿面失效形式及传动效率有很大影响。
相对滑动速度愈大,齿面间愈容易形成油膜,则齿面间摩擦系数愈小,当量摩擦角也愈小;但另一方面,由于啮合处的相对滑动,加剧了接触面的磨损,因而应选用恰当的蜗轮蜗杆的配对材料,并注意蜗杆传动的润滑条件。
滑动速度计算公式为
(1-7)
式中:
γ为普通圆柱蜗杆分度圆上的导程角
n1(r/min)为蜗杆转速
d1为普通圆柱蜗杆分度圆上的直径
2.蜗杆传动的效率
闭式蜗杆传动的功率损失包括:
啮合摩擦损失、轴承摩擦损失和润滑油被搅动的油阻损失。
因此总效率为啮合效率η1、轴承效率η2、油的搅动和飞溅损耗效率η3的乘积,其中啮合效率η1是主要的。
总效率为
η=η1η2η3(1-8)
当蜗杆主动时,啮合效率η1为:
式中:
γ为普通圆柱蜗杆分度圆上的导程角。
ρv为当量摩擦角,可按蜗杆传动的材料及滑动速度查表1-5得出。
由于轴承效率η2、油的搅动和飞溅损耗时的效率η3不大,一般取η2η3=0.95~0.96,
在开始设计时,为了近似地求出蜗轮轴上的转矩T2,则总效率η常按以下数值估取:
当蜗杆齿数z1=1时,总效率估取η=0.7;
当蜗杆齿数z1=2时,总效率估取η=0.8;
当蜗杆齿数z1=4时,总效率估取η=0.9;
表1-5当量摩擦系数fv当量摩擦角ρv
蜗轮材料
锡 青 铜
无 锡 青 铜
蜗杆齿面硬度
>45HRC
≤350HBS
>45HRC
滑动速度vs/(m/s)
fv
ρv
fv
ρv
fv
ρv
1.00
0.045
2°35′
0.055
3°09′
0.07
4°00′
2.00
0.035
2°00′
0.045
2°35′
0.055
3°09′
3.00
0.028
1°36′
0.035
2°00′
0.045
2°35′
4.00
0.024
1°22′
0.031
1°47′
0.04
2°17′
5.00
0.022
1°16′
0.029
1°40′
0.035
2°00′
8.00
0.018
1°02′
0.026
1°29′
0.03
1°43′
注:
1.蜗杆齿面粗糙度Ra=0.8~0.2。
2.蜗轮材料为灰铸铁时,可按无锡青铜查取fv、ρv
3.蜗杆传动的热平衡计算
由于蜗杆传动的效率低,因而发热量大,在闭式传动中,如果不及时散热,将使润滑油温度升高、粘度降低,油被挤出、加剧齿面磨损,甚至引起胶合。
因此,对闭式蜗杆传动要进行热平衡计算,以便在油的工作温度超过许可值时,采取有效的散热方法。
由摩擦损耗的功率变为热能,借助箱体外壁散热,当发热速度与散热速度相等时,就达到了热平衡。
通过热平衡方程,可求出达到热平衡时,润滑油的温度。
该温度一般限制在60~70℃,最高不超过80℃。
热平衡方程为:
式中:
P1(kW)为蜗杆传递的功率;
η为传动总效率;
A为散热面积,可按长方体表面积估算,但需除去不和空气接触的面积,凸缘和散热片面积按50%计算。
t0为周围空气温度,常温情况下可取20℃。
t1为润滑油的工作温度,一般限制在60~70℃,最高不超过80℃。
αt为箱体表面传热系数,其数值表示单位面积、单位时间、温差1℃所能散发的热量,根据箱体周围的通风条件一般取αt=10~17W/(m2℃),通风条件好时取大值。
由热平衡方程得出润滑油的工作温度t1为:
(1-9)
也可以由热平衡方程得出该传动装置所必需的最小散热面积Amin:
如果实际散热面积小于最小散热面积Amin,,或润滑油的工作温度超过80℃,则需采取强制散热措施。
蜗杆传动机构的散热
蜗杆传动机构的散热目的是保证油的温度在安全范围内,以提高传动能力。
常用下面几种散热措施:
1)在箱体外壁加散热片以增大散热面积;
2)在蜗杆轴上装置风扇(图1-8a);
3)采用上述方法后,如散热能力还不够,可在箱体油池内铺设冷却水管,用循环水冷却(图1-8b);
4)采用压力喷油循环润滑。
油泵将高温的润滑油抽到箱体外,经过滤器、冷却器冷却后,喷射到传动的啮合部位(图1-8c)。
图1-8
*普通圆柱蜗杆和蜗轮设计计算
设计时,通常给出传递的功率P1、传动比i和蜗杆转速n1及工作情况等条件。
设计步骤:
1.合理选择蜗杆及蜗轮的材料,并查表确定许用应力值。
2.按蜗轮齿面接触强度公式计算m3q,并查表确定模数m及蜗杆直径系数q值。
(1)选择蜗杆齿数,计算蜗轮齿数,并取整数。
(2)根据蜗杆齿数,估计总效率值,并计算蜗轮转矩。
(3)计算m3q,并查表确定模数m及蜗杆直径系数q值。
3.确定传动的基本参数并计算蜗杆传动尺寸。
4.按热平衡方程计算,给出适当的散热措施建议。
5.选择蜗杆蜗轮的结构,并画出工作图。
例:
试设计一混料机的闭式蜗杆传动。
已知:
蜗杆输入的传递功率P1=3kW、转速n1=130r/min、传动比i=26、载荷稳定。
解:
1.合理选择蜗杆及蜗轮的材料,并查表确定许用应力值。
由于转速较高,传递功率不大,所以蜗杆可采用45号钢,表面淬火,硬度为45~50HRC。
传动比大,则蜗轮也大,为节省有色金属,蜗轮齿圈用锡青铜ZCuSn6Zn6Pb3,砂型铸造,轮芯用铸铁HT200。
估计滑动速度vs<10m/s,由表1-3可查出蜗轮的许用接触应力[σH]=125MPa
2.按蜗轮齿面接触强度公式计算m3q,并查表1-3确定模数m及蜗杆直径系数q值。
(1)选择蜗杆齿数,计算蜗轮齿数,并取整数。
选择蜗杆齿数z1=2,根据传动比,计算蜗轮齿数z2=2×26=52
(2)根据蜗杆齿数,估计总效率值,并计算蜗轮转矩。
估计总效率值η=0.8,计算蜗轮转矩得
(3)计算m3q,并查表确定模数m及蜗杆直径系数q值。
取载荷系数K=1.2
由上式所得数据查表1-2,取m3q=3175mm3,则模数m=6.3mm、蜗杆直径系数q=12.698、蜗杆分度圆直径=80mm
3.确定传动的基本参数并计算蜗杆传动尺寸。
导程角
其它尺寸计算参考表1-2略。
4.按热平衡方程计算,给出适当的散热措施建议。
1)滑动速度计算公式为
式中:
γ为普通圆柱蜗杆分度圆上的导程角
n1为蜗杆转速,单位:
r/min
由滑动速度的数值可查表1-5,取当量摩擦角ρv=1°11’
计算啮合效率
轴承效率z2、油的搅动和飞溅损耗时的效率η3,一般取η2⋅η3=0.96,
则总效率η=0.84
由热平衡方程得出该传动装置所必需的最小散热面积Amin:
上式中取t0为周围空气温度,常温情况下可取20℃。
t1为润滑油的工作温度一般限制在60~70℃,最高不超过80℃。
取80℃代入计算。
αt为箱体表面传热系数,其数值表示单位面积、单位时间、温差1℃所能散发的热量,根据箱体周围的通风条件一般取αt=10~17W/(m2℃),通风条件好时取大值。
取αt=1W/(m2℃)
如果实际散热面积若小于最小散热面积Amin,或润滑油的工作温度一超过80℃,则需采取散热措施
5.选择蜗杆蜗轮的结构,并画出工作图。
略。
本章小结
1.概述
蜗杆传动通常用于传递空间交错成90°的两轴之间的运动和动力,具有传动比大、结构紧凑、传动平稳、可实现自锁、传动效率较低等特点。
2.普通圆柱蜗杆传动的主要参数
(1)中间平面的模数和压力角是标准的。
(2)蜗杆头数z1一般取1、2、4。
蜗轮齿数一般取z2=28~80。
(3)蜗杆分度圆直径要按表中数值取标准。
蜗杆分度圆直径与模数的比值称为蜗杆直径系数。
(4)蜗轮分度圆螺旋角恒等于蜗杆分度圆导程角,且蜗轮、蜗杆螺旋方向相同。
3.蜗杆传动正确啮合的条件
mx1=mt2=m
αx1=αt2=α
γ=β
4.蜗杆传动的失效形式
蜗杆传动的主要失效形式有胶合、疲劳点蚀和磨损。
5.蜗杆传动中蜗轮转动方向的判断
先用左、右手定则判断蜗杆轴向力Fa1的方向,则其反方向即为蜗轮的转动方向。
6.蜗杆传动的设计要求
(1)计算蜗轮接触强度
(2)计算蜗杆传动热平衡,限制工作温度
(3)必要时验算蜗杆轴的刚度。
思考题
1-1蜗杆传动的主要失效形式有哪几种?
选择蜗杆和蜗轮材料组合时,较理想的蜗杆副材料是什么?
1-2蜗杆传动有哪些特点?
1-3普通蜗杆传动的哪一个平面称为中间平面?
1-4蜗杆传动有哪些应用?
1-5蜗杆传动为什么要考虑散热问题?
有哪些散热方法?
1-6观察生活中,有哪些机器中应用了蜗杆传动机构?
铣床中有吗?
1-7试分析题图1-7蜗杆传动的中蜗轮的转动方向及蜗杆、蜗轮所受各分力的方向。
(a)(b)
题图1-7
习题
1-1设计一混料机的闭式蜗杆传动。
已知∶蜗杆输