液压管道安装工法概论.docx
《液压管道安装工法概论.docx》由会员分享,可在线阅读,更多相关《液压管道安装工法概论.docx(9页珍藏版)》请在冰豆网上搜索。
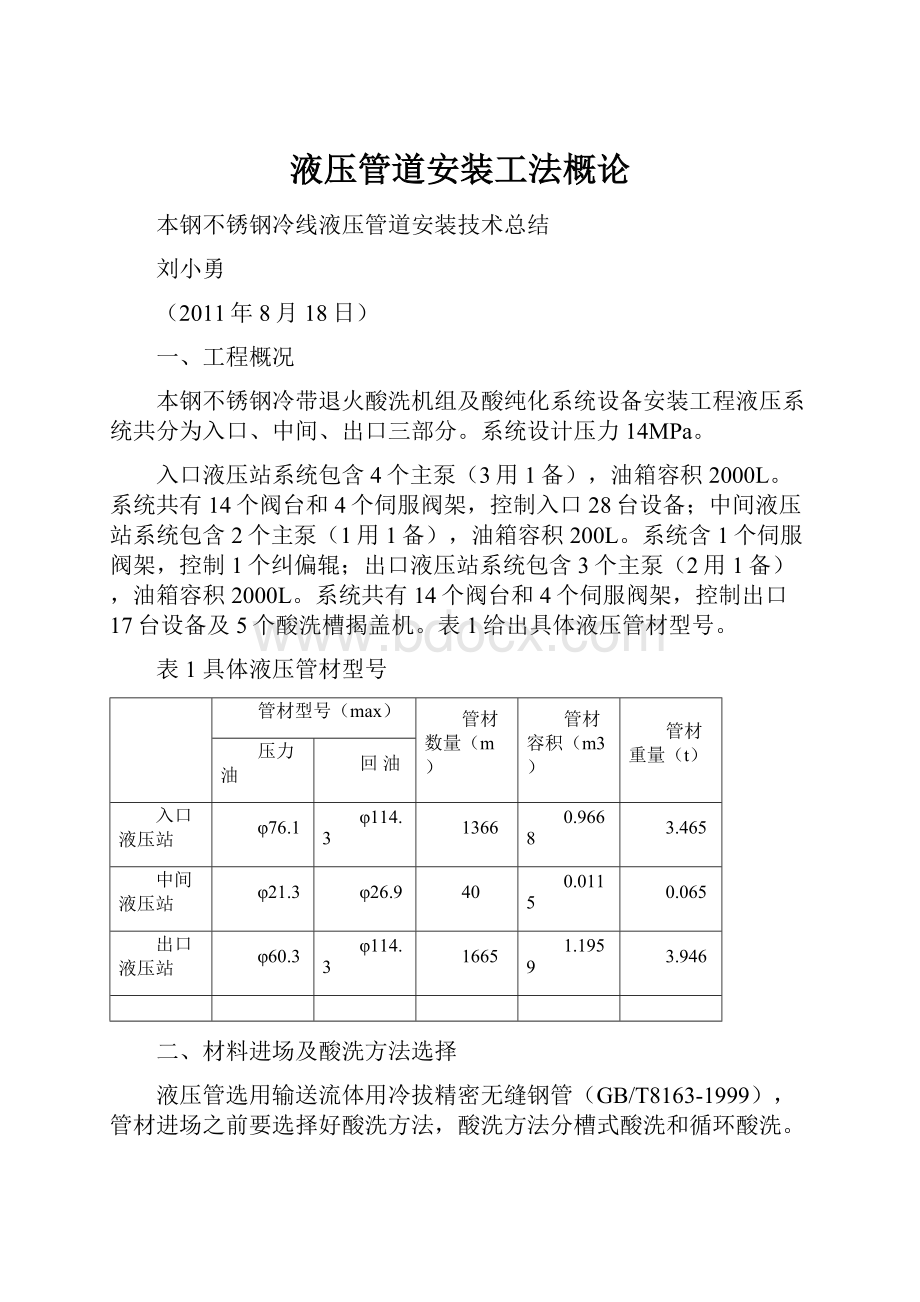
液压管道安装工法概论
本钢不锈钢冷线液压管道安装技术总结
刘小勇
(2011年8月18日)
一、工程概况
本钢不锈钢冷带退火酸洗机组及酸纯化系统设备安装工程液压系统共分为入口、中间、出口三部分。
系统设计压力14MPa。
入口液压站系统包含4个主泵(3用1备),油箱容积2000L。
系统共有14个阀台和4个伺服阀架,控制入口28台设备;中间液压站系统包含2个主泵(1用1备),油箱容积200L。
系统含1个伺服阀架,控制1个纠偏辊;出口液压站系统包含3个主泵(2用1备),油箱容积2000L。
系统共有14个阀台和4个伺服阀架,控制出口17台设备及5个酸洗槽揭盖机。
表1给出具体液压管材型号。
表1具体液压管材型号
管材型号(max)
管材数量(m)
管材容积(m3)
管材重量(t)
压力油
回油
入口液压站
φ76.1
φ114.3
1366
0.9668
3.465
中间液压站
φ21.3
φ26.9
40
0.0115
0.065
出口液压站
φ60.3
φ114.3
1665
1.1959
3.946
二、材料进场及酸洗方法选择
液压管选用输送流体用冷拔精密无缝钢管(GB/T8163-1999),管材进场之前要选择好酸洗方法,酸洗方法分槽式酸洗和循环酸洗。
槽式酸洗适合管径较大的短管、直管、容易拆卸、管路施工量小的场合,如泵站、阀站等液压装置内的配管及现场配管量小的液压系统。
槽式酸洗需要制作3个(8m*1.5m*1m)酸洗槽(一个酸洗、一个钝化、一个清洗),大约需要δ6钢板5t;循环酸洗是在安装好的液压管路中将液压元件断开或拆除,用软管、接管、冲洗盖板联接,构成冲洗回路,用酸泵将酸液打入回路中进行循环酸洗。
循环酸洗速度快、效果好、工序简单、操作方便,能减少对人体及环境的污染,缩短管路安装工期,并能避免槽式酸洗易发生装配时的二次污染问题,适合大型液压系统管路酸洗。
由于本工程液压主管道在隧道里支管道在地面上,隧道里非常潮湿,很难保证制安时不返锈,所以我们采用循环酸洗。
管材进场后首先进行除锈刷两边底漆处理。
三、管道加工
液压管道采用机械切割,切割表面必须平整。
管道煨弯采用冷弯,在专用煨管机上进行,以保证弯管质量。
管道弯制时检查壁厚,椭圆率不应超过8%(先确定煨管机最大可以煨弯多大管道,确定是否购买弯头)。
高压钢管弯曲半径应大于钢管外径的5倍(GB50235-2010),当弯曲半径过小时,会导致管路应力集中,降低管路强度。
表2给出钢管冷弯最小弯曲半径。
表2钢管冷弯最小弯曲半径(mm)
钢管外径D
14
18
22
28
34
42
48
60
76
89
114
弯曲半径R
70
100
135
150
200
250
300
360
450
540
350
四、管道敷设
管道敷设位置应便于装拆、检修,且不妨碍生产人员的行走,以及机电设备的运转、维护和检修;对于同排管道,应将各管的法兰、活接头等连接件相间错开100-200mm,便于装拆;管道外壁与相邻管道之管件边缘的距离应不小于10mm;在管道安装时应注意对阀台及管道内部保洁,管道安装间断期间应用丝堵或塑料布将管口包扎好,防止灰尘进入。
由于液压管道震动较大,塑料管夹安装必须规范。
管夹一般固定在预埋件上,管夹之间距离应适当,过小会造成浪费,过大将发生振动。
表3给出管夹间距离。
表3推荐管夹间距离(mm)
管子外径D
12~34
42~60
76~114
管夹间最大距离L
800
1000
1200
五、管道焊接
现场液压管道口径最大φ114,全部采用氩弧焊焊接一次成型,管道内充氩气保护。
为保证管道焊透,所有焊缝必须用机械加工法打V型坡口,且坡口间隙为0~2.5mm(GB50235-2010)。
如下图:
壁厚T(mm)
角度а(◦)
间隙C(mm)
钝边P(mm)
3-9
70±5
0~2.5
0~2
为保证焊接质量,尽量不采用固定焊口的形式,施焊前应对坡口附近宽20mm范围内的内外管壁进行清理,除净其上的油、水、漆、锈及毛刺等。
管道焊接完毕,应将焊缝表面熔渣及其两侧的飞溅清理干净,并作好记录。
本工程压力油管道对接焊缝质量不低于GB3323-87《钢熔化焊接对接接头射线照相和质量分级》中规定的Ⅱ级标准,采用射线探伤抽查15%焊缝检测;回油管道对接焊缝质量不低于GB3323-87《钢熔化焊接对接接头射线照相和质量分级》中规定的Ⅲ级标准,采用射线探伤抽查5%焊缝检测。
六、回路连接
本工程分两次酸洗,分别组成入口、出口两个回路。
组回路时断开液压缸、马达、油箱、阀台、伺服阀架、阀门等设备,接头处用胶布包扎好,保持清洁,断开部分采用钢管代替。
在每个回路上都增加临时阀门、取样点及压力表,以便于调节油泵输出的总流量在各回路中的分配,观察和掌握各回路的流量、压力、清洁程度等,增强冲洗效果。
油冲洗简单回路示意图如下:
油箱
阀台
阀台
压力表
过滤器
冲洗泵
进油管
回油管
回流
另外在管道敷设时最低点设置排水点,φ34以下采用锥密封活接头,φ34以上压力油管采用高压法兰,回油管采用普通对焊法兰,并在最高点设置排气孔,方法是增加DN15临时球阀。
由于出口揭盖机液压管道在+8米平台上,长度120m,压力油管径φ48,回油管径φ60,为了让酸洗时管道内充满酸液,在管道入口处增加一个+9m高的回形弯,如下图所示:
七、循环酸洗
循环酸洗前要进行仔细检查,检查回路连接是否正确,中和液排放地点是否明确,空压机系统、水源、液压油、冲洗用的液压站、加油小车、酸洗药品、安全劳动保护是否到位。
表4给出酸洗及油冲洗需用物品。
表4酸洗及油冲洗需用设备
名称
规格、型号
数量
单位
备注
耐酸泵
Q=100m/hP=0.38Mpa
1
台
酸洗槽
长2m*宽1m*高1.5m;钢板=8mm
2
个
一个中和用
电加热器
SRY2型,220v,4千瓦
8
只
溶液加热
空压机
6m3
1
台
压力表
1.6MpaY-100
2
个
夹布胶管
DN40
100
m
排废酸用
过滤芯
3μ;φ160*121*546
24
个
过滤芯
5μ;φ160*121*546
8
个
过滤芯
10μ;φ160*121*546
40
个
酸洗药品根据酸洗槽大小及回路容量计算,具体计算方法见(GB50231-98,附录十八表18.2中规定)。
表5给出出入口回路酸洗化学材料用量。
表5酸洗化学材料用量
名称
规格、型号
单位
数量
备注
盐酸
HCl,浓度30%
Kg
2100
入口950kg(浓度14%)
氨水
NH3H2O,浓度30%
Kg
300
入口120kg(浓度2%)
柠檬酸
C6H8O7,100%
Kg
300
入口120kg
烧碱
NaOH,100%
Kg
660
入口300kg
氢氟酸
HF
Kg
0.5
入口0.25kg
乌洛托品
(CH2)6N4
Kg
40
入口20kg
白猫洗洁精
1.5kg/桶
Kg
60
入口25kg
7.1回路吹扫
回路吹扫的目的是带出管内脏物。
在安装管道时,管内会残留一些如焊渣、氧化铁皮等脏物,脱开管道肓端法兰,敞开式吹扫,需逐个打开旁通回路进行吹扫。
主管路还需要用阀门或夹报纸放炮,将赃物吹扫出来。
7.2通水试漏
起动酸洗泵向回路充水,检查回水是否异常,同时可测量回路体积,参照此体积配备酸洗药品。
检查各回路的液流情况。
然后关闭阀门,使压力升至0.8~1Mpa,保压5—10min,检查泄漏并处理。
7.3管道脱脂
脱脂的目的是除去被清洗系统内各种油污,且可除去有机物等的物理附着物,使酸洗过程中的作用成分更完全、彻底的同清洗对象内表面接触,从而促进金属氧化物溶解,保证达到均一的酸洗效果。
起动泵循环,加入白猫洗洁精。
在脱脂液循环的同时,要检查各管道旁通处,管道三通处及最远点、最高点是否有液流循环,可用手触摸管子的温升情况,若管子温度上升,说明该处有循环,若管子温度不上升,说明此处无循环。
一旦不能循环,必须处理,可以采用增大泵输出流量的办法;若泵的流量不能再增大时,可以关闭部分大通径的旁通球阀,以使更大的压力顶出无循环处的空气,促成循环。
必须使所有管道内的液流都能循环,方可在脱脂后进行下一步的酸洗工序。
脱脂液循环30分钟之后,用压缩空气将脱脂液全部排掉,然后用清水冲洗至PH7。
7.4循环酸洗
循环酸洗的目的是利用酸洗液与管道焊接时产生的热影响区及焊皮进行化学和电化学反映,生成可溶性物质以除去污物的过程,同时为钝化创造条件。
循环酸洗是整个化学清洗过程的管件步骤。
起动泵循环,加入氢氟酸(清除氧化铁皮)、循环5分钟之后加入盐酸、乌洛托品(缓蚀剂),开始酸洗。
检查各管道旁通处、管道三通处,及最远点最高点是否有酸液循环,检查及处理办法同脱脂时检查与处理循环的步骤—样。
同时要检验酸的浓度,调整在7%范围内。
酸洗时间长短根据锈蚀情况来确定,一般2~6小时。
本项目入口冲洗了4小时,出口冲洗了6小时。
7.5中和处理
酸洗结束后,用压缩空气将管内大部分酸液排入中和槽,并打开临时排放阀,将残留液体排入胶桶中倒入中和槽,然后用清水冲洗管道至PH=7。
中和槽内加入氢氧化钠进行中和,至PH=7为止方可排放。
7.6钝化处理
当所有回流管的pH值=7时,立即加入柠檬酸,此量需要严格控制,一边加入柠檬酸,一边检测pH值,直至pH=2~3。
循环的时间为lh左右。
柠檬酸的功用就是在酸洗后由于水冲洗导致管内壁有返锈的倾向,以此弱酸来除去浮锈。
加入柠檬酸这一过程,也可认为这是酸洗的继续。
柠檬酸溶液循环一段时间,很清澈,呈浅黄色。
在柠檬酸循环后,加入氨水,氨水的用量也要严格控制,边加入,边检验pH值,直至pH=9.5,在加入氨水时,溶液的颜色发生变化,逐渐变深,呈现棕色,在加完氨水后.立即加入亚硝酸钠,由于亚硝酸钠易凝固,所以要充分溶解在溶液内后再倒入酸洗箱内循环。
钝化
温度在30℃~40℃为最佳。
钝化的目的就是在管内壁形成一层保护膜。
钝化液循环3h。
7.7管路吹扫
钝化后,用压缩空气将管内钝化液全部排出,并继续用压缩空气将管道吹干,同时打开所有排污阀,以彻底清除钝化液。
并逐个打开各阀台的旁通法兰,单独吹扫,直到整个回路再也没有钝化液。
十、循环油冲洗
酸洗完成后半小时内接着进行油冲洗工作。
油冲洗是个漫长过程,分为一次冲洗和精冲。
一次油冲洗就是对机组中间配管进行在线油冲洗,油冲洗时不经过任何阀件,冲洗油是本钢提供的正式工作油,冲洗装置选用临时专门冲洗装置,油冲洗过滤芯由我们项目部提供。
二次油冲洗就是在一次油冲洗合格后,拆除油冲洗临时装置,恢复管道连接,由正式工作泵对整个系统的进行油冲洗,此次冲洗油要经过系统中的油箱、阀台、过滤器和机体配管,但不经过液压缸执行机构,对于伺服阀必须用冲洗板代替。
一次油冲洗开始时一定要多组织人敲打管路,特别是弯头部分,这样可以加快冲洗时间,还要勤换滤芯,并时刻检测各监测点的清洁度。
油冲洗清洁度按甲方及监理要求达到(ISO4406-1999)标准17/15/12,对应(NAS1638)标准的6级精度要求。
分享:
分享到新浪Qing
0
喜欢