燃煤智能化管控系统可行性研究报告汇报.docx
《燃煤智能化管控系统可行性研究报告汇报.docx》由会员分享,可在线阅读,更多相关《燃煤智能化管控系统可行性研究报告汇报.docx(12页珍藏版)》请在冰豆网上搜索。
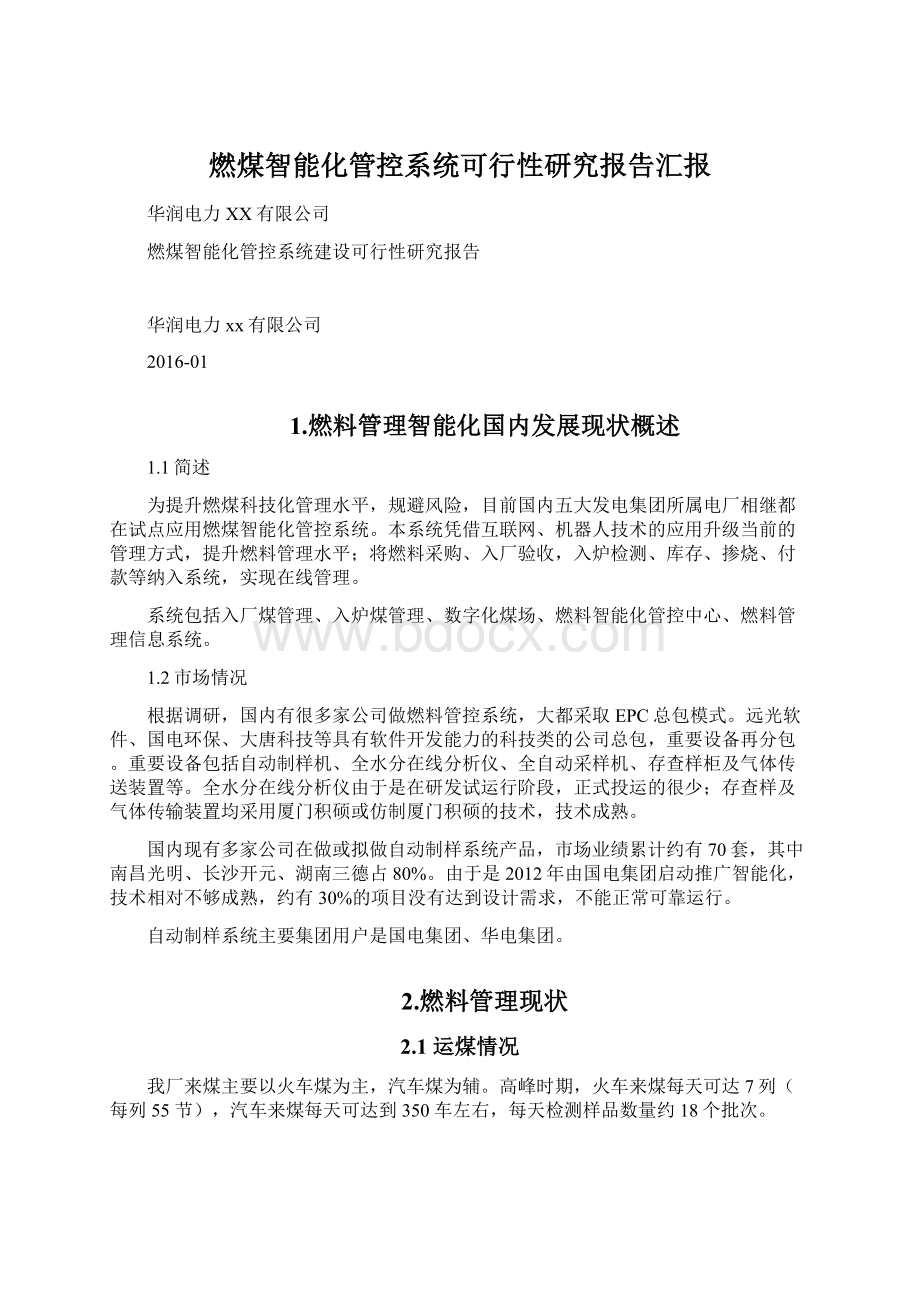
燃煤智能化管控系统可行性研究报告汇报
华润电力XX有限公司
燃煤智能化管控系统建设可行性研究报告
华润电力xx有限公司
2016-01
1.燃料管理智能化国内发展现状概述
1.1简述
为提升燃煤科技化管理水平,规避风险,目前国内五大发电集团所属电厂相继都在试点应用燃煤智能化管控系统。
本系统凭借互联网、机器人技术的应用升级当前的管理方式,提升燃料管理水平;将燃料采购、入厂验收,入炉检测、库存、掺烧、付款等纳入系统,实现在线管理。
系统包括入厂煤管理、入炉煤管理、数字化煤场、燃料智能化管控中心、燃料管理信息系统。
1.2市场情况
根据调研,国内有很多家公司做燃料管控系统,大都采取EPC总包模式。
远光软件、国电环保、大唐科技等具有软件开发能力的科技类的公司总包,重要设备再分包。
重要设备包括自动制样机、全水分在线分析仪、全自动采样机、存查样柜及气体传送装置等。
全水分在线分析仪由于是在研发试运行阶段,正式投运的很少;存查样及气体传输装置均采用厦门积硕或仿制厦门积硕的技术,技术成熟。
国内现有多家公司在做或拟做自动制样系统产品,市场业绩累计约有70套,其中南昌光明、长沙开元、湖南三德占80%。
由于是2012年由国电集团启动推广智能化,技术相对不够成熟,约有30%的项目没有达到设计需求,不能正常可靠运行。
自动制样系统主要集团用户是国电集团、华电集团。
2.燃料管理现状
2.1运煤情况
我厂来煤主要以火车煤为主,汽车煤为辅。
高峰时期,火车来煤每天可达7列(每列55节),汽车来煤每天可达到350车左右,每天检测样品数量约18个批次。
2.2设备及运行现状
2.3入厂计量
我厂火车煤入厂计量轨道衡2套,具备车号自动识别和动态计量数据功能,计量数据人工提交录入EAM系统;
汽车煤入厂重车衡3台、空车衡1台,IC卡刷卡称重,计量数据人工提交录入EAM系统。
2.4采样
入厂煤采样设备现有火车采样机4台,汽车采样机3台,入厂皮带中部采样机2台。
火车、汽车采样机均为全断面自动选点采样(需人工画框定位),自动打包(二期火车采样机不具备),在视频监控下人工装车、传送煤样。
入厂皮带中部采样机,因煤量小于800吨时,采样不符合采样标准,故仅作备用。
入炉煤有4台皮带中部煤流采样机,自动采集煤样,在视频监控下人工装车、传送煤样。
2.5制样
目前入厂煤和入炉煤制样均为人工方式,现场设备为传统破碎、缩分、粉碎等设备,且没有配套除尘设施,工作环境较恶劣。
2.6传送和存查样
制样、编码完成后,13mm、0.2mm样品由制样人员送到化验室。
存查样采用分散式管理,人工制样间旁设有存样室,存放3mm备查样,由经营策划部制样班负责;化验室另设有存样室,存放0.2mm分析煤样,由技术支持部化学专业负责。
存取方式均为人工,在视频监控下完成。
2.7化验
目前化验室具有较完善的化验设备。
化验数据人工录入EAM系统。
2.8燃料全价值寻优系统
软件平台、标准模块搭建正在有序进行中。
3.燃料管理系统建设组成
3.1入厂计量和采样
1、升级IC卡刷卡过衡称重,改为车辆自动识别,提高卸车效率;
3.2全自动制样机和在线全水份分析仪
流程图
3.2.1增设自动制样机1台、在线全水份分析仪1台、气动传输装置一套、存查样柜一套(按3000个存查单元考虑)、样瓶清洗机1台(离线)。
制样、全水份化验、送样、查样、弃样实现全自动,样瓶自动封装,机器编码,化验数据人工提交录入。
3.2.2因采样机数量多,布置分散,故只能采用离线方式。
3.2.3具体技术要求
3.2.3.1材料
a)金属结构中主要承接结构应符合GB/T700要求的碳素结构钢。
b)采用聚乙烯高分子材料的全密封结构或其他密封良好的皮带。
c)破碎元件(如:
牙板、锤头、辊筒、筛板、破碎腔等)需采用耐磨材料,其中牙板、锤头、辊筒表面硬度应不小于35HRC;筛板、破碎腔表面硬度应不小于20HRC。
d)筛板的材料厚度不小于3mm,破碎腔厚度不小于10mm。
e)皮带等密封盖板使用不锈钢材料,设计成方便打开的结构,并密封。
f)各下料口材料使用不锈钢材料。
g)轴类零件均应采用调质处理且全密封,位置应安装在设备腔体外侧,减少粉尘影响。
3.2.3.2煤样称重装置
(1)制样前的称重装置
将通过机采进料口或人工进料口得到的煤样储存在煤样称重装置内,对煤样进行称重,根据煤样重量自动调节缩分比,自动实现定质量缩分,称重后的煤样进入下一步流程制样。
(2)制样后的称重装置
制样后的样品封装后设置自动称重,并具备异常(样品重量低于国标要求)报警功能,煤样重量能够保存到上位机数据库中,方便自动识别读取。
3.2.3.3供料单元
a)各下料口的方圆节衔接处应进行双曲面处理,不能积煤。
b)供料方式应使煤流均匀、粒度离析达到最低程度。
c)供料速度可调,以使各阶段缩分器切割数达到GB/T19494和GB474规定的最少切割数以上。
d)供料厚度和宽度应与后继切割器匹配,使后者能完整地切割煤流。
e)对于皮带供料机,应有防止皮带跑偏装置和煤流整形及厚度调节装置。
f)煤样输送中无堆堵、黏附、洒漏。
g)给料皮带应安装带毛刷的动态刮板,并加弹簧压紧,保证清扫干净。
3.2.3.4破碎单元
(1)一级破碎机
一级破碎机进料口采用密封式设计,防止粉尘的飞扬,破碎机的主要性能参数:
a)进料粒度:
标称最大粒度≤100mm。
b)出料粒度:
6mm。
c)破碎能力:
≯1.5m3/h~5m3/h(矸石含量占30%以上)。
d)原煤水分适应性为:
全水分适应性为≤35%。
e)水分损失率:
≤0.5%。
f)过筛率:
≥95%。
g)破碎机的转速小于950转/min。
h)破碎机内不发生“饼煤”及粘附现象。
破碎机的破碎部件采用耐磨材料制作,锤头和筛板使用寿命应在9000小时以上,破碎机没有存煤现象,也没有堵煤和粘煤现象。
破碎机的振动不超标。
破碎机一般不发生堵煤现象,既使在水份较大的情况下产生堵煤时,也能方便地打开机壳进行处理。
为了保证系统能正常工作及由于大块不易破碎的物料进入破碎机而造成设备的损坏,破碎机设置可靠的电气、机械双重保护,以保证设备及人员的安全。
破碎机设计合理,方便打开清扫,不易破碎的杂物将被清除。
破碎机应有自动清扫防堵能力,能定期自动对碎煤板上遗留物料进行清理,防止煤样交叉污染。
(2)二级破碎机
二级破碎机主要参数要求:
a)进料粒度:
≤6mm。
b)出料粒度:
3mm。
c)破碎能力:
0.3m3/h~0.4m3/h(矸石含量占30%以上)。
d)原煤水分适应性为:
全水分适应性为≤35%。
e)水分损失率:
≤0.5%。
f)过筛率:
≥95%。
二级破碎机能保证破碎机出料粒度小于3mm,大于3mm的物料不超过5%。
投标方需满足破碎机的性能参数要求。
破碎机应有自动清扫防堵能力,能定期自动对碎煤板上遗留物料进行清理,防止煤样交叉污染。
(3)研磨装置
研磨装置能保证出料粒度≤0.2mm。
a)研磨介质及磨筒采用不锈钢材料制作,耐磨损、耐高温且不易腐蚀,机内与煤样接触部位不积料、不粘附、不跑漏、不对样料成分产生影响;采用有效措施减少振动,降低噪音,整机及振动棒等使用寿命长,维修方便,介质更换容易。
由于磨筒内研磨介质较多,物料研磨时无明显温升,确保物料无氧化现象。
b)采取两级冲洗研磨装置,制样完成后并进行吹扫清理,防止物料的交叉污染。
煤样制备环节具备空气吹扫,0.2mm煤样制备环节具有冲洗功能,防止煤样交叉污染。
c)将3mm煤样缩分出大于120g煤样全部进行研磨后,通过二分器缩分出两个0.2mm分析煤样进行封装。
d)研磨装置0.2mm分析煤样过筛率达到100%。
3.2.3.5缩分器
缩分器是将样品按标准规定的缩分比缩分成符合要求的二份或二份以上的预保留样品。
机械缩分器应符合GB/T19494.2-2004《煤炭机械化采样第2部分:
煤样的制备》及GB474-2008《煤样的制备方法》精密度及设备要求。
缩分比在无系统偏差和满足留样量与粒度的关系的前提下实现在线自动调节。
缩分器具有可靠性高,故障率低,维修方便,缩分精度高,缩分比调节范围大,工作可靠等特点。
缩分器的接料斗、弃料斗、样料管均采用不锈钢制作,以有效地防止粘煤和堵煤现象。
结构上采用全密封设计,防止水分损失以及煤粉外漏,缩分过程中,不得出现撒样,堵煤等现象。
(1)系统采用的一、二级机械缩分器为等质量缩分器,可按系统信息自动调整缩分频率,以满足不同总样量一致的要求,保证得到符合要求的样料质量。
(2)系统采用的三级缩分器为等比例缩分器,主要由料仓、标准二分器、溜管等组合而成,其中二分器符合现行的相关国家标准规定。
缩分器采用不锈钢制造,不变形、不脱焊、不粘附,缩分物料时缩分器整体震动,确保不堵料。
投标方在投标文件中具体阐述采用的缩分方式及实现的功能。
3.2.3.6煤样干燥装置
(1)如设置煤样干燥装置,煤样必须在取完全水分煤样后干燥。
红外或微波干燥方式,温度最高不能超过50℃(褐煤不超过40℃)。
可设定多个干燥阶段;
(2)采用微波等加热方式的投标方,应在投标文件附上实验数据,证明其不会对煤质理化性质产生影响;
(3)干燥单元的温度可实现50℃以下可调,控温精度在1℃。
(4)干燥单元能够实现对干燥时间的调控设置,调控精度在1分钟。
(5)可配置辅助设施(如空气循环装置)提高煤样的干燥速度,确保煤样达到空气干燥状态。
投标方在投标文件中具体阐述采用的干燥方式及实现的功能。
3.2.3.7弃料收集装置
(1)制样时所产生的弃料使用专用的输送设备,送到弃料收集装置中;
(2)弃料系统要求运行流畅,不影响设备的制样;
(3)具有弃样暂存功能,设备出现故障时能够方便取出。
(5)提供1.5吨电动密封翻斗车作为弃料小车,需列投标单价,费用包含在总价中。
4.3.8故障应急处理
(1)设备故障时,具有煤样暂存装置及应急取出装置或通道,且保证煤样信息不丢失。
(2)设备故障时,具有相应的报警装置。
(3)设备故障时,可自动取消与采样机的联动状态,避免出现工作流程的紊乱,造成混样现象。
3.2.3.9其他要求
(1)系统有扬尘的位置需配置除尘口,吸力能保持设备罩壳内部相对外面的微负压,确保除尘效果且不造成水分及煤样损失;
(2)系统在供料装置、缩分器、研磨装置安装吹扫装置,并配套负压吸尘;
(3)在溜料管、集料斗及给料装置等易堵煤位置安装振打装置;
(4)设备罩壳内合适位置加装温度测点,并将测点数据引入到控制屏上显示。
3.2.3.10自动封装、写码系统
(1)自动封装、写码一体化系统
整个工艺流程中,煤样一瓶一标识,不出现重复随机码,需有效防止错样、丢样现象的发生。
煤样写码后应有验码措施,保证能正确读取。
煤样瓶须满足气动传输的要求。
煤样瓶要求密封、防水、可清洗,满足全自动制样机封装标识需要,能适应三种煤样的需要。
封装、写码一体化系统能将全水分煤样、存查煤样、一般分析煤样封装,并根据智能化管理系统提供的煤质信息写码。
封装写码后的煤样只能通过终端识别系统解码才能识别煤质信息,杜绝人为因素干扰。
3.2.3.11自动封装、写码系统技术要求
(1)6mm全水分样、3mm存查样和0.2mm分析煤样全部使用瓶装方式,煤样量满足国标要求。
(2)投标方提供的煤样瓶称重、标识环节,需满足无法识别的煤样瓶能推离封装线,不得进入存查样柜。
(3)投标方提供的封装线要求有唯一的出口,且每个煤样瓶依次离开封装传输线,时间需控制可调。
(4)系统自动完成样品的封装、写码,全过程能有效避免人为因素的干扰。
(5)采用RFID芯片编码方式时,RFID芯片必须采用HF高频段芯片:
RFID芯片黏贴在气动传输厂家提供专用样瓶的瓶底。
工作频率:
13.56MHz;
支持协议:
ISO14443A;
读写距离:
1cm~3cm。
一条编码长度为16个字符,要求将煤样瓶16个字符的编码信息存储在2号扇区0号数据块。
RFID芯片的读取方式无密码认证。
(6)为了与气动传输装置配套使用,招标方保留是否采用投标方自动封装写码设备的最终决定权。
投标方请将自动封装写码系统单独投标。
(7)样瓶规格(煤样瓶由气动传输厂家提供)
(a)容量:
满足一次性封装全水样、存查样和分析样。
(b)存储煤量:
满足单瓶完成全水分煤样的封瓶且不能超过样瓶容量的四分之三。
(c)材质:
透明,阻燃,并确保密封效果。
3.2.3.12电气控制系统
(1)控制系统由可编程控制器(PLC)和上位机构成。
(2)核心部件选用可编程控制器(PLC),选用西门子,或同等进口品牌,性能可靠,安全稳定。
高低压电器选用西门子、施耐德及ABB三种品牌之一,电路标准化设计,确保设备运转效率。
(3)系统设有手动/自动二种方式供用户选择。
上位机选用工控机,确保电脑的防尘、防震、抗静电性能。
(4)上位机软件提供标准的通讯接口,与PLC及电厂燃料智能化集中管控系统相互通讯,实现故障、煤种、时间、班号、操作者、包装写码等信息显示。
(5)操作人员可通过上位机随时掌握现场情况,及时处理各种问题,也能根据实际需要进行设置操作,接受PLC传送的数据及各种有关的信息。
(6)上位机操作设置管理权限,将操作、维护、管理分开。
要求在管控中心实现对设备的远程控制。
(7)控制系统接收管控中心提供的车辆编号、矿点、煤种、煤样编码、启动指令、紧急停机指令等。
(8)控制系统反馈给管控中心以下数据:
制样时间、制样流水号、制样完成反馈、制样机故障信息等。
(9)投标方需免费提供与集中管控系统的接口软件。
管控中心可给制样装置控制系统发出总的启停指令,整个制样装置内部的启停顺序按照原设计工艺保留不变,由制样设备控制系统进行控制,若燃料智能化系统故障,原制样装置控制系统能正常独立工作。
(10)与气动传输装置智能上、下料仓开放接口,并形成互锁。
(11)工控计算机配置为:
IPC-610,6010VG/奔腾双核E7400,2.8GHz/2G/500G/DVD/K+M,23寸液晶显示屏。
(12)投标方提供的配电开关需含漏电保护。
3.2.3.13环保除尘系统
招标方负责提供全自动制样机水膜环保除尘主机,全自动制样间墙外1米为分界点,对接过程中,由安装慢的一方负责收口。
全自动制样间内的除尘管道及除尘沟盖板由投标方提供,除尘间内的设备由招标方提供。
请投标方在投标文件中将全自动制样机需要的除尘风量、除尘逻辑等详细列出,以便招标方设计水膜除尘主机和电气控制部分。
3.3燃料智能化管控中心
新建燃料智能化管控中心1套。
实现对计量、采、制样设备运行状况的实时控制和对现场节点的视频监控,同时也是燃料管理的展示中心。
保留煤化验自动化控制和化验设备运行状况监控实施的接口。
燃料管理敏感区域实施门禁管理,采用“指纹+密码”的开门方式。
因燃料全价值寻优系统正在建设,燃料管控系统不设置燃料数据收集分析系统。
3.4土建
在制样楼对面新建一座二层,建筑面积260㎡的“燃料管控中心”。
一层设置全自动制样机、在线全水自动分析仪,北侧外墙为落地玻璃。
二楼设置自动存查样柜和燃料管控中心。
4.方案论证
我公司采样机(9台)布置分散,如采用在线方式,则需新建2栋楼,新增2台全自动制样间,投资将增加450万,且不利于集中管控。
故采用离线方式。
燃煤全价值寻优系统正在建设,为了不重复建设,燃料管控系统不设置燃料信息分析部分。
作为下级系统接入EAM、燃煤全价值寻优系统,数据库对EAM、燃煤全价值寻优系统开放。
将燃煤智能管控系统布置在现有制样楼对面,实现燃料制样存查样的集中管理和控制,并与煤化验室进行无缝对接。
5.经济效益分析及建设费用核算
5.1效益分析
减少水分损失:
相对传统燃煤管理模式,按水分损失0.2%、标煤单价510元/吨,年用煤需求400万吨(2015年数据),需节省燃煤费用约400万元。
整个系统投资估算大约900万元,投资回收期为2.25年。
燃煤智能管控系统建成后,燃料采、制及煤样全水份化验工作自动进行,基本杜绝人为干涉,减少管理漏洞。
采、制样、计量设备的自动化,提高工作效率,降低人力成本、提高管理效率和管理质量。
在实行到厂结算的情况下,验收过程公平、公开,也大大提高企业形象和信用度。
5.2费用核算
项目
序号
建设内容
单位
数量
单价
(万元)
费用
(万元)
备注
硬件设备
1
车辆自动识别
套
4
10
40
2
在线全水自动测试系统
套
1
50
60
3
全自动制样机
套
1
180
180
含除尘系统。
(已立项并批复)
4
智能存查样柜
套
1
120
150
容量3000个单元(已立项并批复)
5
气动传输装置
套
1
50
50
传输距离约100米(实地测量后得出准确数值)(已立项并批复)
6
样瓶清洗装置
套
1
20
50
7
增加现有计量、采制设备数据采集远传
200
包括全厂计量、采制设备
监控中心
8
监控中心
套
1
100
50
软件
9
燃料采制集中管控系统
套
1
50
55
采样、计量设备、全自动制样机、气送系统、存查样系统等硬件设备的集中远程控制
土建
10
土建
M2
260
0.25
65
含装修
总计
900
已批复350万
6、总结
通过燃煤智能化管控系统建设,新增自动制样机、在线全水份分析仪等设备,并整合现有计量、采样、监控等设备,实行燃料集中管控,提高了管理水平,基本消除入厂验收过程中的人为干扰风险。
因涉及到总体设计、土建、控制、化验及设备改造等多个方面,且属定制化设计生产,建议采用EPC方式实施。