对流传热.docx
《对流传热.docx》由会员分享,可在线阅读,更多相关《对流传热.docx(17页珍藏版)》请在冰豆网上搜索。
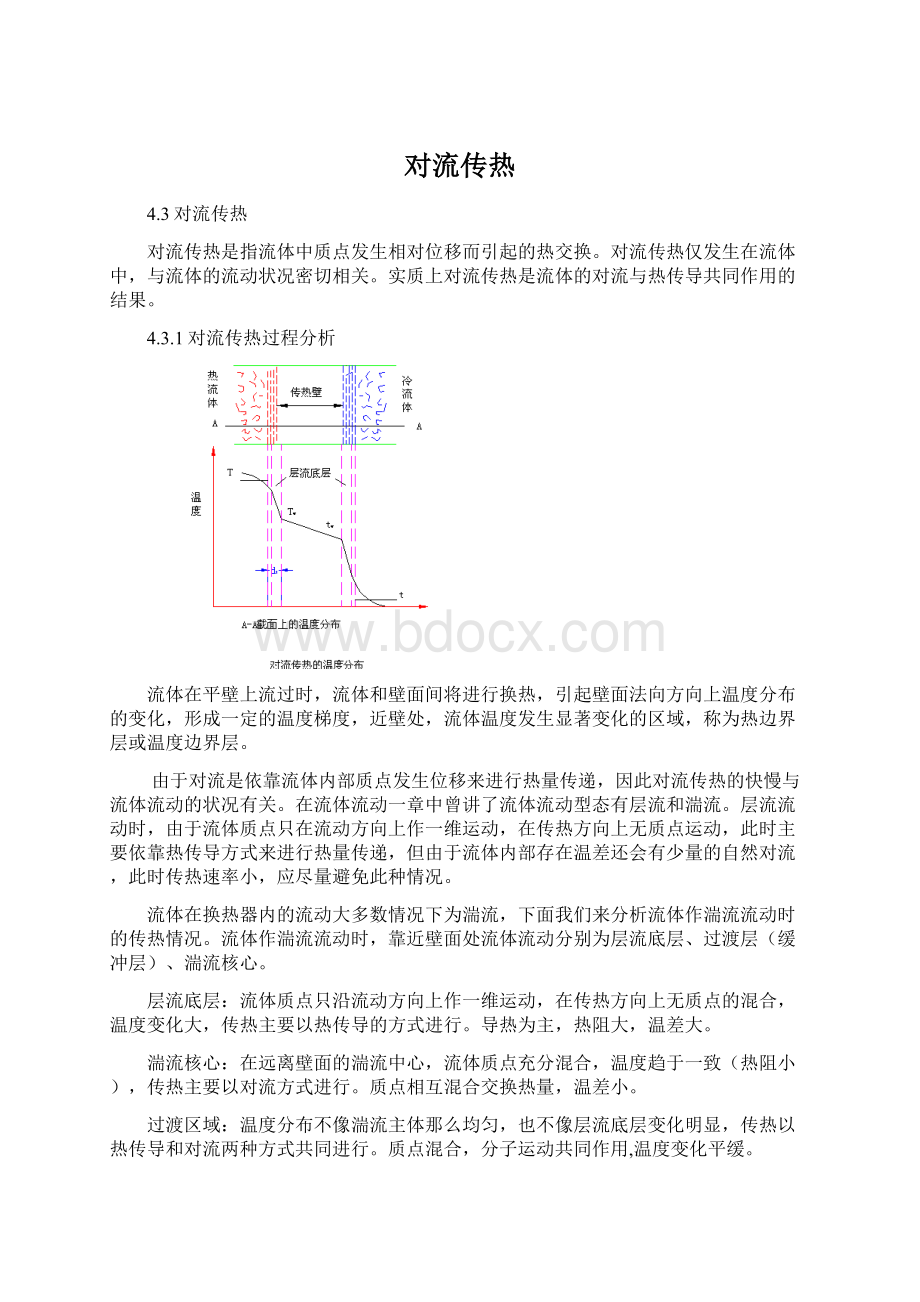
对流传热
4.3对流传热
对流传热是指流体中质点发生相对位移而引起的热交换。
对流传热仅发生在流体中,与流体的流动状况密切相关。
实质上对流传热是流体的对流与热传导共同作用的结果。
4.3.1对流传热过程分析
流体在平壁上流过时,流体和壁面间将进行换热,引起壁面法向方向上温度分布的变化,形成一定的温度梯度,近壁处,流体温度发生显著变化的区域,称为热边界层或温度边界层。
由于对流是依靠流体内部质点发生位移来进行热量传递,因此对流传热的快慢与流体流动的状况有关。
在流体流动一章中曾讲了流体流动型态有层流和湍流。
层流流动时,由于流体质点只在流动方向上作一维运动,在传热方向上无质点运动,此时主要依靠热传导方式来进行热量传递,但由于流体内部存在温差还会有少量的自然对流,此时传热速率小,应尽量避免此种情况。
流体在换热器内的流动大多数情况下为湍流,下面我们来分析流体作湍流流动时的传热情况。
流体作湍流流动时,靠近壁面处流体流动分别为层流底层、过渡层(缓冲层)、湍流核心。
层流底层:
流体质点只沿流动方向上作一维运动,在传热方向上无质点的混合,温度变化大,传热主要以热传导的方式进行。
导热为主,热阻大,温差大。
湍流核心:
在远离壁面的湍流中心,流体质点充分混合,温度趋于一致(热阻小),传热主要以对流方式进行。
质点相互混合交换热量,温差小。
过渡区域:
温度分布不像湍流主体那么均匀,也不像层流底层变化明显,传热以热传导和对流两种方式共同进行。
质点混合,分子运动共同作用,温度变化平缓。
根据在热传导中的分析,温差大热阻就大。
所以,流体作湍流流动时,热阻主要集中在层流底层中。
如果要加强传热,必须采取措施来减少层流底层的厚度。
4.3.2对流传热速率方程
对流传热大多是指流体与固体壁面之间的传热,其传热速率与流体性质及边界层的状况密切相关。
如图在靠近壁面处引起温度的变化形成温度边界层。
温度差主要集中在层流底层中。
假设流体与固体壁面之间的传热热阻全集中在厚度为δt有效膜中,在有效膜之外无热阻存在,在有效膜内传热主要以热传导的方式进行。
该膜既不是热边界层,也非流动边界层,而是一集中了全部传热温差并以导热方式传热的虚拟膜。
由此假定,此时的温度分布情况如下图所示。
建立膜模型:
式中
──总有效膜厚度;
──湍流区虚拟膜厚度;
──层流底层膜厚度。
使用傅立叶定律表示传热速率在虚拟膜内:
流体被加热:
流体被冷却:
设
,对流传热速率方程可用牛顿冷却定律来描述:
流体被加热:
流体被冷却:
式中Q’,Q──对流传热速率,W;
’,──对流传热系数,W/(m2·℃);
Twtw──壁温,℃;
T,t──流体(平均)温度,℃;
A──对流传热面积,m2。
牛顿冷却定律并非从理论上推导的结果,而只是一种推论,是一个实验定律,假设Q∝Dt。
对流传热一个非常复杂的物理过程,实际上由于有效膜厚度难以测定,牛顿冷却定律只是给出了计算传热速率简单的数学表达式,并未简化问题本身,只是把诸多影响过程的因素都归结到了当中──复杂问题简单化表示。
4.3.3影响对流传热系数的因素
对流传热是流体在具有一定形状及尺寸的设备中流动时发生的热流体到壁面或壁面到冷流体的热量传递过程,因此它必然与下列因素有关。
1.引起流动的原因
自然对流:
由于流体内部存在温差引起密度差形成的浮升力,造成流体内部质点的上升和下降运动,一般u较小,也较小。
强制对流:
在外力作用下引起的流动运动,一般u较大,故较大。
2.流体的物性
当流体种类确定后,根据温度、压力(气体)查对应的物性,影响较大的物性有:
r,m,l,cp。
的影响:
;的影响:
Re;cp的影响:
cpcp单位体积流体的热容量大,则较大;
的影响:
Re
3.流动型态
层流:
热流主要依靠热传导的方式传热。
由于流体的导热系数比金属的导热系数小得多,所以热阻大。
湍流:
质点充分混合且层流底层变薄,a较大。
;但Re动力消耗大。
4.传热面的形状、大小和位置
不同的壁面形状、尺寸影响流型;会造成边界层分离,产生旋涡,增加湍动,使a增大。
(1)形状:
比如管、板、管束等;
(2)大小:
比如管径和管长等;
(3)位置:
比如管子得排列方式(如管束有正四方形和三角形排列);管或板是垂直放置还是水平放置。
对于一种类型的传热面常用一个对对流传热系数有决定性影响的特性尺寸L来表示其大小。
5.是否发生相变
主要有蒸汽冷凝和液体沸腾。
发生相变时,由于汽化或冷凝的潜热远大于温度变化的显热(r远大于cp)。
一般情况下,有相变化时对流传热系数较大,机理各不相同,复杂。
4.3.4对流传热系数经验关联式的建立
由于对流传热本身是一个非常复杂的物理问题,现在用牛顿冷却定律把复杂简单表示,把复杂问题转到计算对流传热系数上面。
所以,对流传热系数大小的确定成为了一个复杂问题,其影响因素非常多。
目前还不能对对流传热系数从理论上来推导它的计算式,只能通过实验得到其经验关联式。
一、因次分析
由上面的分析:
a=f(u,l,m,l,cp,r,gbDt)
式中l———特性尺寸;
u———特征流速。
基本因次,共4个,长度L,时间T,质量M,温度q
变量总数:
共8个
因次分析之后,所得准数关联式中共有4个无因次数群(由p定理8-4=4)
因次分析结果如下:
Nusselt(努塞尔)待定准数(包含对流传热系数)
Reynolds(雷诺)表征流体流动型态对对流传热的影响。
Prandtl(普兰特)反映流体物性对对流传热的影响
Grashof(格拉斯霍夫)表征自然对流对对流传热的影响
(1)定性温度
由于沿流动方向流体温度的逐渐变化,在处理实验数据时就要取一个有代表性的温度以确定物性参数的数值,这个确定物性参数数值的温度称为定性温度。
定性温度的取法:
1)流体进出口温度的平均值tm=(t2+t1)/2;2)膜温t=(tm+tW)/2。
(2)特性尺寸
它是代表换热面几何特征的长度量,通常选取对流动与换热有主要影响的某一几何尺寸。
另外,实验范围是有限的,准数关联式的使用范围也就是有限的。
4.3.5无相变时对流传热系数的经验关联式
一、流体在管内的强制对流
1.圆形直管内的湍流
使用范围:
Re>10000,0.750
注意事项:
(1)定性温度取流体进出温度的算术平均值tm;
(2)特征尺寸为管内径di;
(3)流体被加热时,k=0.4,流体被冷却时,k=0.3;
上述n取不同值的原因主要是温度对近壁层流底层中流体粘度的影响。
当管内流体被加热时,靠近管壁处层流底层的温度高于流体主体温度;而流体被冷却时,情况正好相反。
对于液体,其粘度随温度升高而降低,液体被热时层流底层减薄,大多数液体的导热系数随温度升高也有所减少,但不显著,总的结果使对流传热系数增大。
液体被加热时的对流传热系数必大于冷却时的对流传热系数。
大多数液体的Pr>1,即Pr0.4>Pr0.3。
因此,液体被加热时,n取0.4;冷却时,n取0.3。
对于气体,其粘度随温度升高而增大,气体被加热时层流底层增厚,气体的导热系数随温度升高也略有升高,总的结果使对流传热系数减少。
气体被加热时的对流传热系数必小于冷却时的对流传热系数。
由于大多数气体的Pr<1,即Pr0.4通过以上分析可知,温度对近处层流底层内流粘度的影响,会引起近壁流层内速度分布的变化,故整个截面上的速度分布也将产生相应的变化。
(4)特征速度为管内平均流速。
以下是对上面的公式进行修正:
a.高粘度
要考虑壁面温度变化引起粘度变化对a的影响(m是在tm下;而mW是在tw下)。
在实际中,由于壁温难以测得,工程上近似处理为:
对于液体,加热时:
,冷却时:
b.过渡区
2300过渡区内流体比剧烈的湍流区内的流体的Re小,流体流动的湍动程度减少,层流底层变厚,a减小。
c.流体在弯管中的对流传热系数
先按直管计算,然后乘以校正系数f
式中d──管径;
R──弯管的曲率半径。
由于弯管处受离心力的作用,存在二次环流,湍动加剧,a增大。
d.非圆形直管内强制对流
采用圆形管内相应的公式计算,特征尺寸采用当量直径。
式中
此为近似计算,最好采用经验公式和专用式更为准确。
套管环隙:
式中d1、d2——分别为套管外管内径或内管外径。
适用范围:
d1/d2=1.65~17,
。
e.当l/d<60时则为短管,由于管入口扰动增大,a较大,乘上校正系数f。
2.圆形直管内的层流
特点:
1)物性特别是粘度受管内温度不均匀性的影响,导致速度分布受热流方向影响。
2)层流的对流传热系数受自然对流影响严重使得对流传热系数提高。
3)层流要求的进口段长度长,实际进口段小时,对流传热系数提高。
(1)Gr<25000时,自然对流影响小可忽略
适用范围:
Re<2300,
,l/d>60
定性温度、特征尺寸取法与前相同,mw按壁温确定,工程上可近似处理为:
对于液体,加热时:
,冷却时:
(2)Gr>25000时,自然对流的影响不能忽略时,乘以校正系数
在换热器设计中,应尽量避免在强制层流条件下进行传热,因为此时对流传热系数小,从而使总传热系数也很小。
例题:
有一列管换热器,由60根f25×2.5mm钢管组成,通过该换热器用饱和蒸汽加热管内流动的苯,苯由20°C加热至80°C,流量为13kg/s。
求:
(1)苯在管内的对流传热系数;
(2)如苯流量加大一倍,对流传热系数如何变化;(假设物性不发生变化)
(3)如苯在壳程流动,管内为饱和蒸汽,问对流传热系数的计算与前有何不同。
已知苯的物性:
例题:
一列管式换热器,由38根f25×2.5mm的无缝钢管组成,苯在管内流动,由20℃加热到80℃,苯的流量为8.32kg/s,外壳中通入水蒸气进行加热,求:
(1)管壁对苯的对流给热系数;
(2)管子换为f19×2mm管壁对苯的对流给热系数;
(3)当苯的流量提高一倍,对流给热系数变化如何?
已知苯的物性:
二、流体在管外的强制对流
流体可垂直流过单管和管束两种情况。
由于工业中所用的换热器多为流体垂直流过管束,由于管间的相互影响,其流动的特性及传热过程均较单管复杂得多。
故在此仅介绍后一种情况的对流传热系数的计算。
1.流体垂直流过管束
流体垂直流过管束时,管束的排列情况可以有直列和错列两种。
各排管的变化规律:
第一排管,直列和错列基本相同;第二排管,直列和错列相差较大;第三排管以后(直列第二排管以后),基本恒定;从图中可以看出,错列传热效果比直列好。
单列的对流传热系数用下式计算
适用范围:
5000(1)特性尺寸取管外径do,定性温度取法与前相同tm;
(2)流速u取每列管子中最窄流道处的流速,即最大流速。
(3)C,e,n取决于排列方式和管排数,由实验测定,具体取值。
对于前几列而言,各列的e,n不同,因此a也不同。
排列方式不同(直列和错列),对于相同的列,e,n不同,a也不同。
(4)对某一排列方式,由于各列的a不同,应按下式求平均的对流传热系数:
式中ai——各列的对流传热系数;
Ai——各列传热管的外表面积。
2.流体在换热器管壳间流动
一般在列管换热器的壳程加折流挡板,折流挡板分为圆形和圆缺形两种。
由于装有不同形式的折流挡板,流动方向不断改变,在较小的Re下(Re=100)即可达到湍流。
圆缺形折流挡板,弓形高度25%D,的计算式:
适用范围:
Re=2×103~106。
定性温度:
进、出口温度平均值;tw→μw。
特征尺寸:
(1)当量直径de
正方形排列:
正三角形排列:
(2)流速u根据流体流过的最大截面积Smax计算
式中h——相邻挡板间的距离;
D——壳体的内径。
提高壳程a的措施:
提高壳程ua,但hfµu2,hf;de¯a;加强壳程的湍动程度,如加折流挡板或填充物。
三、大空间的自然对流传热
所谓大空间自然对流传热是指冷表面或热表面(传热面)放置在大空间内,并且四周没有其它阻碍自然对流的物体存在,如沉浸式换热器的传热过程、换热设备或管道的热表面向周围大气的散热。
对流传热系数仅与反映自然对流的Gr和反映物性的Pr有关,依经验式计算:
Nu=C(GrPr)n
(1)特性尺寸对水平管取外径do,垂直管或板取管长和板高H。
(2)定性温度取膜温(tm+tw)/2。
(3)C,n=f(传热面的形状和位置,Gr,Pr),具体数值列在书表中。
4.3.6有相变时对流传热系数的经验关联式
一、蒸汽冷凝
蒸汽与低于其饱和温度的冷壁接触时,将凝结为液体,释放出气化热。
1.冷凝方式
蒸汽冷凝方式:
膜状冷凝,滴状冷凝。
膜状冷凝:
若冷凝液能润湿壁面,形成一层完整的液膜布满液面并连续向下流动。
滴状冷凝:
若冷凝液不能很好地润湿壁面,仅在其上凝结成小液滴,此后长大或合并成较大的液滴而脱落。
凝液润湿壁面的能力取决于其表面张力和对壁面的附着力大小。
若附着力大于表面张力则会形成膜状冷凝,反之,则形成滴状冷凝。
通常滴状冷凝时蒸汽不必通过液膜传热,可直接在传热面上冷凝,其对流传热系数比膜状冷凝的对流传热系数大5~10倍。
但滴状冷凝难于控制,工业上大多是膜状冷凝。
2.蒸汽在水平管外冷凝
计算公式:
式中n——水平管束在垂直列上的管子数;
r——汽化潜热(ts下),kJ/kg;
r——冷凝液的密度,kg/m3;
l——冷凝液的导热系数,W/(m.K);
m——冷凝液的粘度,Pa.s。
特性尺寸l:
管外径do;
定性温度:
膜温
,用膜温查冷凝液的物性r、l和m;潜热r用饱和温度ts查;此时认为主体无热阻,热阻集中在液膜中。
3.在竖直板或竖直管外的冷凝
当蒸汽在垂直管或板上冷凝时,冷凝液沿壁面向下流动,同时由于蒸汽不断在液膜表面冷凝,新的冷凝液不断加入,形成一个流量逐渐增加的液膜流,相应于液膜厚度加大,上部分为层流,当板或管足够高时,下部分可能发展为湍流。
对于冷凝液来说,临界Re=2100。
如图所示,从顶向底流动时,液膜d,a¯;当H一定高时,流动从层流过渡到湍流时,Re,层流底层d¯,a。
介绍de的计算方法。
式中S——冷凝液流过的截面积,m2;
b——润湿周边,m;
G——冷凝液的质量流量,kg/s;
M——单位长度润湿周边上冷凝液的质量流量,kg/s.m。
(1)层流时a的计算式
适用范围:
Re<1800
定性温度:
膜温
特征尺寸l:
管高或板高H
(2)湍流时a的计算式
(是否正确)
适用范围:
Re>1800
定性温度:
膜温
特征尺寸l:
管高或板高H
注:
Re是指板或管最低处的值(此时Re为最大)
4.冷凝传热的影响因素和强化措施
从前面的讲述中可知,对于纯的饱和蒸汽冷凝时,热阻主要集中在冷凝液膜内,液膜的厚度及其流动状况是影响冷凝传热的关键。
所以,影响液膜状况的所有因素都将影响到冷凝传热。
(1)流体物性的影响
冷凝液rm¯,则液膜厚度越小d¯Þa;冷凝液lÞa。
冷凝潜热r,同样的热负荷Q下冷凝液量小,则液膜厚度越小Þa。
以上的分析与前面讲的经验关联式一致。
在所有的物质中以水蒸汽的冷凝传热系数最大,一般为104/(m2.K)左右,而某些有机物蒸汽的冷凝传热系数可低至103W/(m2.K)以下。
(2)温度差影响
当液膜作层流流动时,Dt=ts-tW,Dt,则蒸汽冷凝速率加大,液膜增厚d,a¯。
(3)不凝气体的影响
上面的讨论都是对纯蒸汽而言的,在实际的工业冷凝器中,由于蒸汽中常含有微量的不凝性气体,如空气。
当蒸汽冷凝时,不凝气体会在液膜表面浓集形成气膜。
这样冷凝蒸汽到达液膜表面冷凝前,必须先以扩散的方式通过这层气膜。
这相当于额外附加了一热阻,而且由于气体的导热系数l小,使蒸汽冷凝的对流传热系数大大下降。
实验可证明:
当蒸汽中含空气量达1%时,a下降60%左右。
因此,在冷凝器的设计中,在高处安装气体排放口;操作时,定期排放不凝气体,减少不凝气体对a的影响。
(4)蒸汽流速与流向的影响
前面介绍的公式只适用于蒸汽静止或流速不大的情况。
蒸汽的流速对a有较大的影响,蒸汽流速较小u<10m/s时,可不考虑其对a的影响。
当蒸汽流速u>10m/s时,还要要考虑蒸汽与液膜之间的摩擦作用力。
蒸汽与液膜流向相同时,会加速液膜流动,使液膜变薄d¯,a;蒸汽与液膜流向相反时,会阻碍液膜流动,使液膜变厚d,a¯;但u时,会吹散液膜,a。
一般冷凝器设计时,蒸汽入口在其上部,此时蒸汽与液膜流向相同,有利于a。
(5)蒸汽过热的影响
蒸汽温度高于操作压强下的饱和温度时称为过热蒸汽。
过热蒸汽与比其饱和温度高的壁面接触(tW>ts),壁面无冷凝现象,此时为无相变的对流传热过程。
过热蒸汽与比其饱和温度低的壁面接触(tW冷却和冷凝。
整个过程是过热蒸汽首先在气相下冷却到饱和温度,然后在液膜表面继续冷凝,冷凝的推动力仍为Dt=ts-tW。
一般过热蒸汽的冷凝过程可按饱和蒸汽冷凝来处理,所以前面的公式仍适用。
但此时应把显热和潜热都考虑进来
,为过热蒸汽的比热和温度。
工业中过热蒸汽显热增加较小,可近似用饱和蒸汽计算。
(6)冷凝面的高度及布置方式
以减薄壁面上的液膜厚度为目的。
(7)强化传热措施
对于纯蒸汽冷凝,恒压下ts为一定值。
即在气相主体内无温差也无热阻,a的大小主要取决于液膜的厚度及冷凝液的物性。
所以,在流体一定的情况下,一切能使液膜变薄的措施将强化冷凝传热过程。
减小液膜厚度最直接的方法是从冷凝壁面的高度和布置方式入手。
如在垂直壁面上开纵向沟槽,以减薄壁面上的液膜厚度。
还可在壁面上安装金属丝或翅片,使冷凝液在表面张力的作用下,流向金属丝或翅片附近集中,从而使壁面上的液膜减薄;使冷凝传热系数得到提高。
二、液体沸腾时的对流传热系数
对液体加热时,液体内部伴有液相变为气相产生汽泡的过程称为沸腾。
按设备的尺寸和形状可分为:
大容器沸腾:
加热壁面浸入液体,液体被加热而引起的无强制对流的沸腾现象。
管内沸腾:
在一定压差下流体在流动过程中受热沸腾(强制对流);此时液体流速对沸腾过程有影响,而且加热面上气泡不能自由上浮,被迫随流体一起流动,出现了复杂的气液两相的流动结构。
工业上有再沸器、蒸发器、蒸汽锅炉等都是通过沸腾传热来产生蒸汽。
管内沸腾的传热机理比大容器沸腾更为复杂。
本节仅讨论大容器的沸腾传热过程。
♦气泡的生成和过热度
由于表面张力的作用,要求气泡内的蒸气压力大于液体的压力。
而气泡生成和长大都需要从周围液体中吸收热量,要求压力较低的液相温度高于汽相的温度,故液体必须过热,即液体的温度必须高于气泡内压力所对应的饱和温度。
在液相中紧贴加热面的液体具有最大的过热度。
液体的过热是新相——小气泡生成的必要条件。
♦粗糙表面的气化核心
开始形成气泡时,气泡内的压力必须无穷大。
这种情况显然是不存在的,因此纯净的液体在绝对光滑的加热面上不可能产生气泡。
气泡只能在粗糙加热面的若干点上产生,这种点称为气化核心。
无气化核心则气泡不会产生。
过热度增大,气化核心数增多。
气化核心是一个复杂的问题,它与表面粗糙程度、氧化情况、材料的性质及其不均匀性质等多种因素有关。
2.沸腾曲线
如图所示,以常压水在大容器内沸腾为例,说明Dt对的a影响。
(1)AB段,Dt=tW-ts,Dt很小时,仅在加热面有少量汽化核心形成汽泡,长大速度慢,所以加热面与液体之间主要以自然对流为主。
Dt<5°C时,汽化仅发生在液体表面,严格说还不是沸腾,而是表面汽化。
此阶段,a较小,且随Dt升高得缓慢。
(2)BC段,25°C>Dt>5°C时,汽化核心数增大,汽泡长大速度增快,对液体扰动增强,对流传热系数增加,由汽化核心产生的气泡对传热起主导作用,此时为核状沸腾。
(3)CD段,Dt>25°C进一步增大到一定数值,加热面上的汽化核心大大增加,以至气泡产生的速度大于脱离壁面的速度,气泡相连形成气膜,将加热面与液体隔开,由于气体的导热系数l较小,使a¯,此阶段称为不稳定膜状沸腾。
DE段,Dt>250°C时,气膜稳定,由于加热面tW高,热辐射影响增大,对流传热系数增大,此时为稳定膜状沸腾。
工业上一般维持沸腾装置在核状沸腾下工作,其优点是:
此阶段下a大,tW小。
从核状沸腾到膜状沸腾的转折点C称为临界点(此后传热恶化),其对应临界值Dtc、ac、qc。
对于常压水在大容器内沸腾时:
Dtc=25°C、qc=1.25×106W/m2。
3.沸腾传热的影响因素和强化措施
(1)流体物性
流体的m、l、s、r等有影响;l或r,a;m或s,a¯。
一般来说,有机物的m大,在同样的P和Dt下比水的a小;而且表面张力s小,润湿能力大的液体,有利于气泡形成和脱离壁面,a大。
措施:
在液体中加入少量添加剂,改变其表面张力s¯。
(2)温差Dt
从沸腾曲线可知,温差Dt是影响和控制沸腾传热过程的重要因素,应尽量控制在核状沸腾阶段进行操作。
(3)操作压力
提高操作压力P,相当于提高液体的饱和温度ts,使液体的m¯s¯,有利于气泡形成和脱离壁面,强化了沸腾传热,在同温差下,a增大。
(4)加热面的状况
加热面越粗糙,提供汽化核心多,越有利于传热。
新的、洁净的、粗糙的加热面,a大;当壁面被油脂玷污后,会使a下降。
此外,加热面的布置情况,对沸腾传热也有明显的影响。
例如在水平管束外沸腾时,其上升气泡会覆盖上方管的一部分加热面,导致平均a下降。
措施:
使加热面粗糙,用机加工或腐蚀等;
对于沸腾传热,由于过程的复杂性,虽然提出的经验式很多,但不够完善,至今还未总结出普遍适用的公式。
有相变时的a比无相变时的a大得多,热阻主要集中在无相变一侧流体,此时有相变一侧流体的a只需近似计算。