铸造工艺设计基础.docx
《铸造工艺设计基础.docx》由会员分享,可在线阅读,更多相关《铸造工艺设计基础.docx(22页珍藏版)》请在冰豆网上搜索。
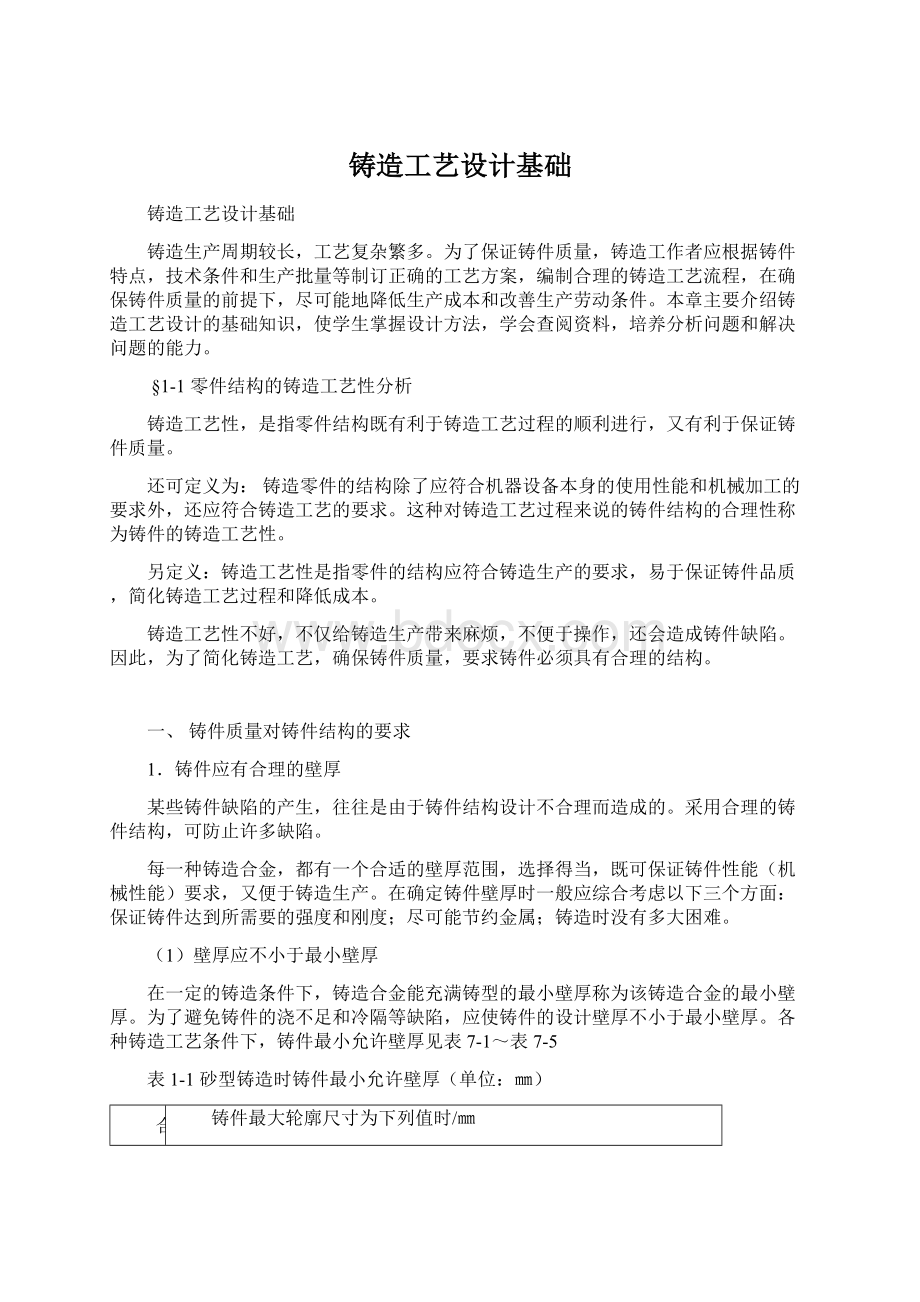
铸造工艺设计基础
铸造工艺设计基础
铸造生产周期较长,工艺复杂繁多。
为了保证铸件质量,铸造工作者应根据铸件特点,技术条件和生产批量等制订正确的工艺方案,编制合理的铸造工艺流程,在确保铸件质量的前提下,尽可能地降低生产成本和改善生产劳动条件。
本章主要介绍铸造工艺设计的基础知识,使学生掌握设计方法,学会查阅资料,培养分析问题和解决问题的能力。
§1-1零件结构的铸造工艺性分析
铸造工艺性,是指零件结构既有利于铸造工艺过程的顺利进行,又有利于保证铸件质量。
还可定义为:
铸造零件的结构除了应符合机器设备本身的使用性能和机械加工的要求外,还应符合铸造工艺的要求。
这种对铸造工艺过程来说的铸件结构的合理性称为铸件的铸造工艺性。
另定义:
铸造工艺性是指零件的结构应符合铸造生产的要求,易于保证铸件品质,简化铸造工艺过程和降低成本。
铸造工艺性不好,不仅给铸造生产带来麻烦,不便于操作,还会造成铸件缺陷。
因此,为了简化铸造工艺,确保铸件质量,要求铸件必须具有合理的结构。
一、铸件质量对铸件结构的要求
1.铸件应有合理的壁厚
某些铸件缺陷的产生,往往是由于铸件结构设计不合理而造成的。
采用合理的铸件结构,可防止许多缺陷。
每一种铸造合金,都有一个合适的壁厚范围,选择得当,既可保证铸件性能(机械性能)要求,又便于铸造生产。
在确定铸件壁厚时一般应综合考虑以下三个方面:
保证铸件达到所需要的强度和刚度;尽可能节约金属;铸造时没有多大困难。
(1)壁厚应不小于最小壁厚
在一定的铸造条件下,铸造合金能充满铸型的最小壁厚称为该铸造合金的最小壁厚。
为了避免铸件的浇不足和冷隔等缺陷,应使铸件的设计壁厚不小于最小壁厚。
各种铸造工艺条件下,铸件最小允许壁厚见表7-1~表7-5
表1-1砂型铸造时铸件最小允许壁厚(单位:
㎜)
合金种类
铸件最大轮廓尺寸为下列值时/㎜
﹤200
200-400
400-800
800-1250
1250-2000
﹥2000
碳素铸钢
低合金钢
高锰钢
不锈钢、耐热钢
灰铸铁
孕育铸铁
(HT300以上)
球墨铸铁
8
8-9
8-9
8-11
3-4
5-6
3-4
9
9-10
10
10-12
4-5
6-8
4-8
11
12
12
12-16
5-6
8-10
8-10
14
16
16
16-20
6-8
10-12
10-12
16~18
20
20
20-25
8-10
12-16
12-14
20
25
25
-
10-12
16-20
14-16
铸件最大轮廓为下列值时mm
铸造铝合金
﹤100
100-200
200-400
400-800
800-1250
3
4-5
5-6
6-8
8-12
表1-2熔模铸件的最小壁厚(单位:
㎜)
铸件尺寸
/㎜
最小壁厚/㎜
碳钢
高温合金
铝合金
铜合金
10~50
1.5~2.0
0.6~1.0
1.5~2.0
1.5~2.0
50~100
2.0~2.5
0.8~1.5
2.0~2.5
2.0~2.5
100~200
2.5~3.0
1.0~2.0
2.5~3.0
2.5~3.0
200~350
3.0~3.5
—
3.0~3.5
3.0~3.5
﹥350
4.0~5.0
—
3.5~4.0
3.5~4.0
表1-3金属型铸件的最小壁厚(单位:
㎜)
铸件尺寸
/㎜
最小壁厚/㎜
铝硅合金
铝镁合金、镁合金
铜合金
灰铸铁
铸钢
50×50
2.2
3
2.5
3
5
100×100
2.5
3
3
3
8
225×225
3
4
3.5
4
10
350×350
4
5
4
5
12
表1-4 压铸件的最小壁厚(单位:
㎜)
压铸件面积/㎝2
锌合金
铝合金镁合金
铜合金
﹤25
0.7~1.0
0.8~1.2
1.5~2.0
25~100
1.0~1.6
1.2~1.8
2.0~2.5
100~400
1.6~2.0
1.5~2.0
2.5~3.0
﹥400
2.0~2.5
2.0~2.5
3.0~3.5
(2) 铸件的临界壁厚
在铸件结构设计时,为了充分发挥金属的潜力,节约金属,必须考虑铸造合金的力学性能对铸件壁厚的敏感性。
厚壁铸件容易产生缩孔、缩松、晶粒粗大、偏析和松软等缺陷,从而使铸件的力学性能下降。
从这个方面考虑,各种铸造合金都存在一个临界壁厚。
铸件的壁厚超过临界壁厚后,铸件的力学性能并不按比例地随着铸件壁厚的增加而增加,而是显著下降。
因此,铸件的结构设计应科学地选择壁厚,以节约金属和减轻铸件重量。
在砂型铸造工艺条件下,各种合金铸件的临界壁厚可按最小壁厚的3倍来考虑。
铸件壁厚应随铸件尺寸增大而相应增大,在适宜壁厚的条件下,既方便铸造又能充分发挥材料的力学性能。
表7-5,表7-6给出砂型铸造各种铸造合金的临界壁厚。
表1-5砂型铸造各种铸造合金的临界壁厚(单位:
㎜)
合金种类与牌号
当铸件重量(㎏)为下列值时
0.1~2.5
2.5~10
﹥10
灰铸铁
HT100,HT150
HT200,HT250
HT300
HT350
8~10
12~15
12~18
15~20
10~15
12~15
15~18
15~20
20~25
12~18
25
25
可锻铸铁
KTH300-06 KTH390-8KTH350-10 KTH370-2
6~10
6~10
12~12
10~12
--
--
球墨铸铁
QT400-15 QT450-10
QT500-7 QT230-3
10
14~18
15~20
18~20
50
60
碳素铸钢
ZG200-400 ZG230-450
ZG270-500 ZG310-570
ZG340-640
18
15
15
25
20
20
--
--
--
铝合金
镁合金
锡合金
6~10
10~14
--
6~12
12~18
6~8
10~14
--
--
表1-6碳素铸钢件砂型铸造的临界壁厚(单位:
㎜)
含碳量
0.10
0.20
0.30
0.40
0.50
临界壁厚
11
13.5
18.5
25
39
(3) 铸件的内壁厚度
砂型铸造时,铸件内壁散热条件差,即使内壁厚度与外壁厚度相等,但由于它比外壁的凝固速度慢,力学性能往往要比外壁低,同时在铸造过程中易在内、外壁交接处产生热应力致使铸件产生裂纹。
对于凝固收缩大的铸造合金还易产生缩孔和缩松,因此铸件的内壁厚度应比外
壁厚度薄一些。
图1-1铸件内壁的合理结构 a,b)不合理 c)合理
表1-7砂型铸造各种铸造合金件内、外壁厚相差值
合金类别
铸铁
铸钢
铸铝
铸铜
铸件内壁比外壁厚度应减少的相对值%
10~20
20~30
10~20
15~20
注:
铸件内腔尺寸大的取下限
对于锻钢制造的轴类零件来说,增大直径便可提高承载能力。
但对铸件来说,随着壁厚的增加,中心部分晶粒粗大,承载能力并不随壁厚增加而成比例地增加。
因此,在设计较厚铸件时,不能把增加壁厚当作提高承载能力的唯一办法。
为了节约金属,减轻铸件重量,可以选择合理的截面形状,如承受弯曲载荷的铸件,可选用“T”型或“工”型截面。
采用加强筋也可减小铸件壁厚。
一般筋厚﹤内壁厚﹤外壁厚。
2.铸件壁应合理连接
铸件壁厚不均,厚薄相差悬殊,会造成热量集中,冷却不均,不仅易产生缩孔、缩松,而且易产生应力、变形和裂纹。
所以要求铸件壁厚尽量均匀,如图1-2(a)所示结构中壁厚不均,在厚的部分易形成缩孔,在厚薄连接处易形成裂纹。
改为1-2(b)结构后,由于壁厚均匀,即可防止上述缺陷产生。
也可用薄壁加加强筋结构。
加强筋的布置应尽量避免或减少交叉,防止习惯年成热节。
例如钳工划线平台,其筋条布置如图1-3所示。
铸件各部分壁厚不均现象有时不可避免, 此时应采用逐渐过渡的方式,避免截面突然变化。
接头断面的类型大致可分为L、V、K、T 和十字型五种。
在接头处,凝固速度慢,容易产生应力集中、裂纹、变形、缩孔、缩松等缺陷。
在接头形式的选用中,应优选L型接头,以减小与分散热节点及避免交叉连接。
逐渐过渡的形式与尺寸如表7-8所示。
由表可知,壁厚差别不很大时,采用圆弧过渡(); 壁厚差别很大时,采用L型过渡,在同等情况下,铸钢件的过渡尺寸比铸铁件要大。
两壁相交,其相交和拐弯处要作成圆角。
图1-2 均匀壁厚避免形成热节举例
3.结构斜度
进行铸件设计时,凡顺着拔模方向的不加工表面尽可能带有一定斜度以便于起模,便于操作,简化工艺。
铸件垂直度越小,斜度越大。
综合以上所述,为了保证铸件质量,铸件的合理结构为:
1) 壁厚力求均匀,减小厚大断面,防止形成热节。
办法是将厚大部位挖去一部分;图7-5
2) 内壁厚度应小于外壁。
因为内壁冷却慢,适当减薄(图7-6)。
3) 应有利于补缩和实现顺序凝固。
有些铸件铸锭厚度较大或厚度不均。
如果该件所用合金的体积收缩较大,则很容易形成缩孔、缩松。
此时应仔细审查零件结构,尽可能采取顺序凝固方式,让薄壁处先凝,厚壁处后凝,使在厚壁处易于安放冒口补缩,以防止缩孔、缩松。
图7-7
4) 注意防止发生翘曲变形。
细长杆状铸件,大平板铸件,增加加强筋及改变截面形状
床身一类的铸件,其截面形状不允许变化,为防止其变形可采用反挠度,即在模样上采取反变形量。
如果既不能设加强筋,又不能该变截面形状,只好采用人工失效方法消除应力减少变形。
5) 应避免水平方向出现较大平面。
大平面铸件的上部型砂时间受金属液体烘烤,容易造成夹砂。
解决的办法是倾斜浇注或设计成倾斜壁。
应避免铸件收缩时受到阻碍,否则会造成裂纹,对于收缩大的合金铸件尤其要注意这一点。
4.铸件结构设计原则
(1) 设计铸件壁厚时应考虑到合金的流动性;
流动性越好的合金,充型能力越强,铸造时就不容易产生浇不足、冷隔等缺陷,因此,能铸出的铸件最小壁厚尺寸也就越小。
(2)铸型型腔的形状与尺寸大小是根据铸件的形状与尺寸决定的。
不同的型腔形状和尺寸对液态金属的流动的阻力,散热情况是不同的,从而会导致液态金属在型腔内的流动与填充情况不同。
因此,铸件结构上应尽量避免突变性的转变、壁厚急剧的变化、细长结构、大的水平面、高度较大的凸台等。
(3)一个铸件在生产过程中是否出现缩孔、缩松、变形、热裂、冷裂等收缩类铸造缺陷,出现在哪个部位、严重程度如何,都与铸件结构密切相关。
由此可以得出指导铸件结构设计的原则:
1) 对凝固收缩大,容易产生集中缩孔的合金,如铸钢、球墨铸铁、可锻铸铁、黄铜、无锡青铜、铝硅共晶合金等,倾向于采用顺序凝固方式铸造。
这时在进行铸件结构设计时,应使铸件结构形式有利于顺序凝固。
2) 对溶液产生缩松的合金,如锡青铜、磷青铜等采用冒口补缩效果不大,常采用同时凝固方式来使缩松更分散些;对收缩较小的合金,如铸铁更倾向于采用同时凝固方式铸造。
这时铸件的结构应是壁厚均匀,尽量减少金属的聚集与消除热节。
对于一些结构形状复杂的大铸件,也可将其各部分按顺序或同时凝固方式设计。
3) 尽量使铸件结构有利于自由收缩,如尽量减少铸件的轮廓尺寸,减少突出部分,必要时可将一个铸件分成几个小铸件,然后用焊接或螺栓连接起来。
4) 尽量避免产生应力集中的形状,如不应有尖角、不同壁厚之间的连接要平缓。
5) 应考虑到各种铸造方法的工艺过程、凝固特点、铸型和型芯的特点。
尤其市使用金属铸型和型芯的铸造方法。
如金属型铸造、压力铸造,应便于铸件的抽芯和出芯。
二、从生产工艺考虑—简化工艺便于操作—角度对铸件结构提出的要求
铸件结构不仅应有利于保证铸件质量,防止和减少铸造缺陷,而且应保证造型、制芯、清理等操作的方便,以利于提高生产率和降低成本。
因此要求铸件要:
1 便于起模。
改进妨碍起模的凸台、凸缘,筋板和外表面侧凹。
2 减少和简化分型面
减少分型面的数目,既可减少砂箱数目,又能提高铸件尺寸精度。
曲面分型,工艺复杂,操作不便(制造模样和造型不方便),应尽量做成平直分型面。
3 改进铸件内腔结构,尽量减少砂芯数量
4 简化清理操作
5 增加结构斜度
铸件最好有结构斜度。
这样不仅起模方便,也提高铸件尺寸精度,甚至减少砂芯数量。
对那些不允许有结构斜度的铸件,在制造模样时,应做出角度很小的拔模斜度。
三、 组合铸件
有些大而复杂的铸件,受工厂条件限制,无法生产或虽能生产但质量难以保证,可用“一分为二”或“化整为零”。
即分成两个或两个以上的简单铸件,使复杂铸件分成简单件,大件变成小件,铸造完后再用螺栓或焊接方法连接起来。
这样做,不仅简化铸造过程,加工和运输也方便,并使原来无法生产的铸件得以生产。
§1-2铸造工艺方案的确定
铸造工艺方案包括造型、制芯、铸型种类、浇注位置和分型面等内容。
铸造工艺方案是否先进合理,对获得优质铸件、简化工艺过程、提高生产率、降低成本和改善劳动条件等起着决定作用。
一、造型方法的选择
1.按铸型种类分:
铸型种类
主要特点
应用情况
干型
水分少,强度高,透气性好,成本高,劳动条件差,不易实现机械化,自动化
结构复杂,质量要求高,单件,小批中大型铸件
湿型
不用烘干,成本低,劳动条件好,机械化造型应用最多;采用硼润土活化砂及高压造型,可以得到强度高、透气性较好的铸型
多用于单批或大批大量的中小件
自硬型
水玻璃砂型
强度高,硬化快,效率高,粉尘少,一般不须烘干
各种铸件均可应用,对大型铸件效率更高
树脂砂型
强度高,可自硬,精度高。
铸件易清理,生产效率高
大、中型钢、铁、铝、铜铸件单批或批量生产.
表面烘干型
(表面干型)
只将表面层烘干(烘干层厚度约为15~80㎜)具有干型的一些优点,避免和克服了干型的缺点
同干型相比,生产效率高,成本低,适用于铸件结构较复杂质量要求较高的单件、小批量生产的中、大型铸件
双快水泥砂型
利用快凝快硬的双快水泥作粘结剂制作铸型,具有自硬快的优点
生产效率高,劳动条件好,与水玻璃流态砂相比,铸铁件无缩沉和不粘砂,用于单件、成批生产的铸铁件
石灰石砂型
通常用水玻璃做粘结剂,吹CO2使之硬化或配制成水玻璃自硬砂,具有硅粉尘少,易清理,可消除工人矽肺病等
目前主要用于钢铸件的生产中。
应用于大型铸钢件时铸件有缩沉现象
2 按砂型紧实方式造型方法分:
1) 手工造型:
砂箱造型,脱箱造型,刮板造型,组芯地坑造型
2) 机器造型:
震击,震压,射压,抛砂,气流紧实等
3 按模样材料分:
金属模造型,塑料模造型,木模造型
一般中小型铸件应尽可能选用湿型,不用干型(大批量、机械化);大中型结构复杂、质量要求高的铸件用表面干型或干型;中大的铸型和砂芯可考虑用自硬性铸型,特别是对于大件铸型和砂芯更为合适。
二、浇注位置的确定
1.浇注位置:
浇注位置指浇注时铸件在铸型内所处的位置。
分型面:
指两半个铸型互相接触的表面。
一般先从保证铸件的质量出发来确定浇注位置,然后从工艺操作出发确定分型面。
2.选择浇注位置的主要原则
浇注位置的选择,决定于合金的种类、铸件结构及轮廓尺寸、铸件表面质量要求以及现有的生产条件。
选择浇注位置时,主要以保证铸件质量为前提,同时尽量做到简化造型工艺和浇注工艺。
选择浇注位置的主要原则有:
1)铸件的重要加工面、主要工作面和受力面,应尽量放在低部或侧面,以防止这些表面上产生砂眼、气孔、夹渣等铸造缺陷。
因为同一铸件,下边质量好,上边质量较差:
气孔、夹渣等铸造缺陷上边多,下边少,且下边补缩良好,组织细密。
如图图示车床床身导轨面是关键部位,不允许有任何缺陷,浇注时应把导轨面朝下。
齿轮的轮齿是重要加工面,应将其朝下以保持组织致密,防止铸造缺陷,如图1-22。
卷筒、缸筒等圆筒形铸件,关键部位是内外表面。
因不可能都朝下。
所以应采取立浇,即重要加工面都在侧面。
图1-23。
有时,加工面很多,无法都照顾到,势必使某一加工面朝上,此时,要将重要的加工面朝下,朝上的加工面应加大加工余来量。
如牛头刨床横船,上下面均有导轨,由于结构复杂不能平做立浇,只好将导轨加长,面积较大部分放在下边,上边导轨可加大加工余量或采取其它措施。
2)尽量使大平面朝下,并采取倾斜浇注,以避免夹砂、夹渣缺陷。
倾斜浇注及适当快浇,使金属液上升较快,辐射热不会长期地作用于整个表面上,而是不断地作用在“新的”表面上,使各处受热时间均小于夹砂形成的临界时间。
有时为了方便造型,采用“横做立浇”、“平做斜浇”的方法。
(图1-25)
3) 保证铸件有良好的液态金属导入位置,保证铸件充满。
较大而壁薄的铸件部分应朝下、侧立、或倾斜以保证金属液的充填。
浇注薄壁铸件时要求金属液到达薄壁处所经过的路程或所需的时间愈短愈好,使金属液在静压力的作用下平稳地充填好铸型的各部分。
铸件的薄壁部分应放在下边,以免发生浇不足、冷隔。
(图1-26)
4) 应该有利于顺序凝固和补缩。
薄壁部分在下,厚大部分在上,以便安放冒口和发挥冒口的补缩效果。
如果不能完全做到,起码也得把热节部分放在侧面。
厚大部分尽可能安放在上部位置,而对于中、下位置的局部厚大处采用冷铁或侧冒口等工艺措施解决其补缩问题。
(便于放侧冒口图1-27)
5) 尽量减少砂芯数目,使用砂芯时应保证砂芯定位稳固、排气通畅和下芯及检验方便。
尽可能避免出现吊砂、吊芯或悬臂芯。
吊砂在合箱、浇注时易造成塌箱;吊芯无支撑,不安全;悬臂芯定位不好,在金属液的冲击和浮力作用下,易发生偏斜。
较大的砂芯尽量使芯头朝下,挑担砂芯定位可靠。
浇注位置应有利于砂芯发的定位和稳固支撑,使排气通畅,避免使用吊芯、悬臂芯。
图1-28,1-29
6) 在大批量生产中,应使铸件的毛刺、飞边易于清除。
7)要避免厚实铸件冒口下面的主要工作面产生偏析。
8) 应使合箱位置、浇注位置和铸件的冷却位置相一致。
避免翻转铸型。
翻转铸型,不仅劳动量大,且易引起掉砂和芯子移动等弊病。
三、铸型分型面的选择
1.分型面:
指两半个铸型互相接触的表面。
(铸型组元之间的结合面)一般先从保证铸件的质量出发来确定浇注位置,然后从工艺操作出发确定分型面。
合理地选择分型面,对于简化铸造工艺,提高劳动生产率,降低生产成本,提高铸件质量都有直接的关系。
分型面的选择尽量与浇注位置一致,以避免合型翻转。
一般来说,要先确定浇注位置,而后选择分型面,但在分析了各种分型面的利弊之后,可能再次调整浇注位置。
2.从工艺操作方便出发,分型面确定原则:
1) 为了起模方便,分型面一般选在铸件最大截面上,且莫使模样在一箱内的高度过高。
图1-30所示的铸件中最大截面有两个,均可选做分型面,但第
(2)方案优于
(1)方案,可降低模样在下箱的高度。
2) 尽量把铸件的加工面和加工基准面放在同一半型内(同一砂箱中),目的是保证铸件尺寸精度。
图1-31所示的管子堵头,加工时以四方头中心线为基准,加工外螺纹,如果四方头和带螺纹的外圆不同心,则给加工带来困难,甚至无法加工。
3) 尽量减少分型面的数目、活块的数目。
多一个分型面,不仅操作不便,而且增加一个造成尺寸误差的因素,不利于提高铸件精度;多一个活块,多一次麻烦,多一个造成尺寸误差的因素。
当流水线生产用机器造型时,一般只允许有一个分型面,尽量不用活块,以砂芯代替活块,图1-32,1-33所示。
4) 分型面尽量选择平直分型面
平直分型面可简化造型过程、模型制造工作量,易于保证尺寸精度(图7-34)。
在实际生产中,必要时也可用曲面分型。
依铸件形状不同,选择不平分型面,如曲面、凸凹面、折面、圆铸面等。
曲面分型的实例见1-35。
5) 尽量减少砂芯数目。
芯子多,操作麻烦,铸件精度降低,且披缝多不易清理。
如图1-36所示接头铸件,若按a)图对称分型,则必须制作砂芯,但按b)图分型,内孔可用自带砂芯形成。
6) 便于下芯、合箱及检查型腔尺寸。
为此,尽量把主要砂芯放在下半箱中。
例如,中心距大于700㎜的减速箱盖,采用两个分型面的目的就是便于合箱时检查尺寸,才能保证铸件壁厚均匀。
图1-47。
§1-3铸造工艺参数的确定
在编制铸造工艺规程过程中,必须确定一些工艺数据,如收缩率、加工余量、拔模斜度等统称为工艺参数。
工艺参数选择的恰当与否,对铸件质量、尤其是尺寸精度、生产率、成本、原材料消耗等影响很大。
一、铸造收缩率
铸件凝固之后在固态下的收缩,将使铸件各部分尺寸小于模样尺寸。
为了使铸件冷至室温的尺寸等于铸件尺寸,模样尺寸应比铸件尺寸大一些。
加大的这部分尺寸,叫铸件收缩量。
一般以铸造收缩率表示。
铸造收缩率K=
×100%
K值主要与合金种类及具体成分有关,同时也与铸件收缩时受到的阻碍大小有关。
同一合金,同样成分,由于铸件结构、大小、厚薄不同,型砂的退让性不同,浇冒口类型及开设位置不同,砂箱结构及箱带的位置不同,铸件收缩率会有很大差异。
鉴于影响因素较多,很难准确确定K值大小。
只有通过试生产,多次划线,反复实验,才能准确测得。
一些常见铸造合金的K值如表1-7所示。
自由收缩指简单厚实铸件的收缩,除此之外的收缩均为受阻收缩。
同一铸件的轴向、径向或长宽高三个方向,其收缩值可能不一致,所以重要铸件应按不同方向分别确定K值。
K值还与铸型种类有关,湿型铸件收缩率应大于干型铸件收缩率。
表1-7常见合金的铸造收缩率
合金种类
铸造收缩率%
自由收缩
受阻收缩
灰铸铁、中小型铸件
特大型铸件
筒型铸件轴向
径向
1.0
0. 8
1. 0.9
2. 1.0
0.9
0.7
0.8
0.5
孕育铸铁HT25-47
HT35-61
1.0
1.5
0.8
1.0
白口铁
1.75
1.5
黑心可锻铸铁壁厚﹥25㎜
壁厚﹤25mm
0.75
1.0
0.5
0.75
球墨铸铁
1.0
0.8
铸钢 碳钢
含铬高合金钢
1.6~2.0
1.3~1.7
1.3~1.7
1.0~1.4
有色金属 锡青铜
无锡青铜
锌黄铜
铝硅合金
铝镁合金
镁合金
1.4
2.0~2.2
1.8~2