镁合金轧制工艺.docx
《镁合金轧制工艺.docx》由会员分享,可在线阅读,更多相关《镁合金轧制工艺.docx(23页珍藏版)》请在冰豆网上搜索。
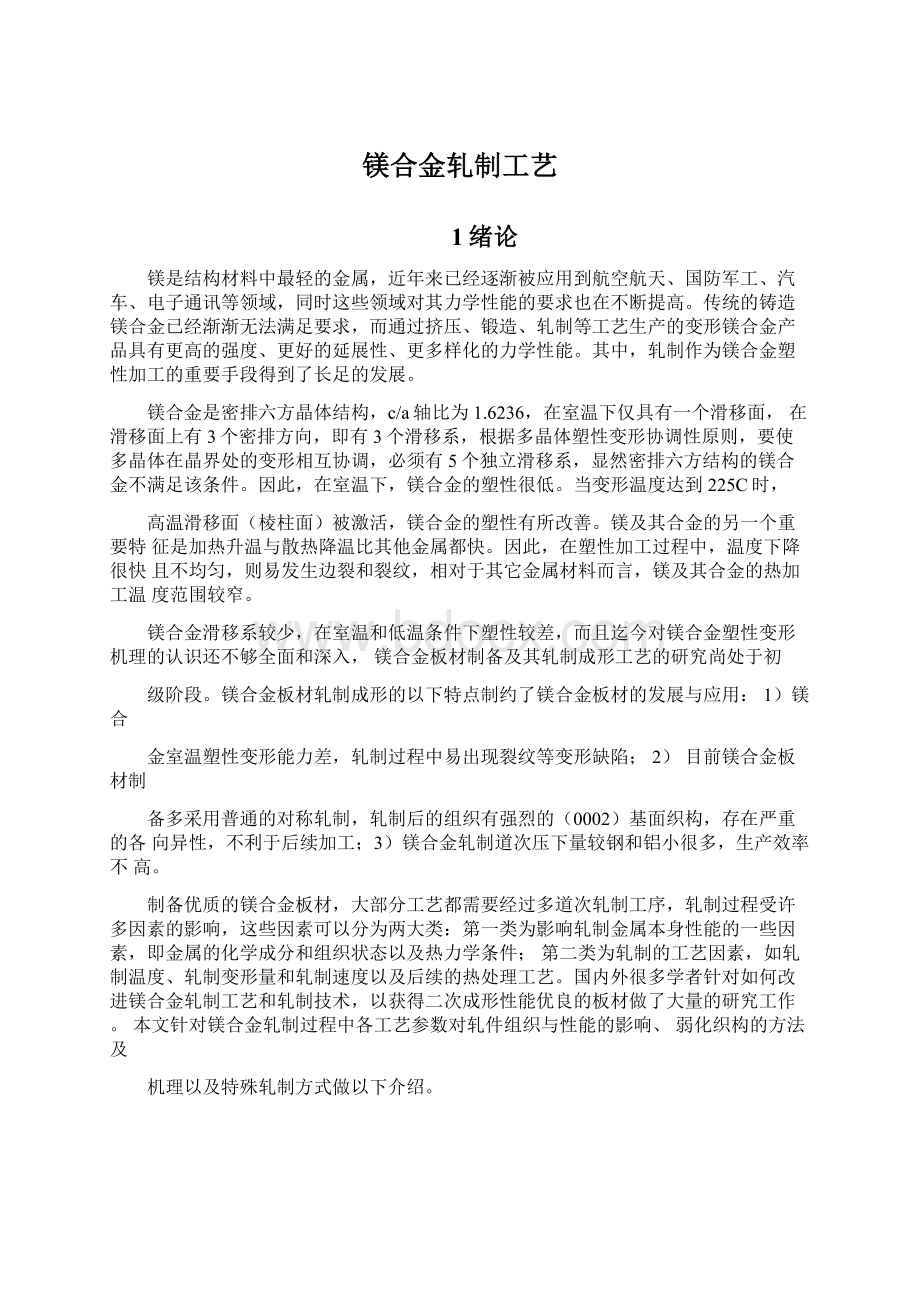
镁合金轧制工艺
1绪论
镁是结构材料中最轻的金属,近年来已经逐渐被应用到航空航天、国防军工、汽车、电子通讯等领域,同时这些领域对其力学性能的要求也在不断提高。
传统的铸造镁合金已经渐渐无法满足要求,而通过挤压、锻造、轧制等工艺生产的变形镁合金产品具有更高的强度、更好的延展性、更多样化的力学性能。
其中,轧制作为镁合金塑性加工的重要手段得到了长足的发展。
镁合金是密排六方晶体结构,c/a轴比为1.6236,在室温下仅具有一个滑移面,在滑移面上有3个密排方向,即有3个滑移系,根据多晶体塑性变形协调性原则,要使多晶体在晶界处的变形相互协调,必须有5个独立滑移系,显然密排六方结构的镁合金不满足该条件。
因此,在室温下,镁合金的塑性很低。
当变形温度达到225C时,
高温滑移面(棱柱面)被激活,镁合金的塑性有所改善。
镁及其合金的另一个重要特征是加热升温与散热降温比其他金属都快。
因此,在塑性加工过程中,温度下降很快且不均匀,则易发生边裂和裂纹,相对于其它金属材料而言,镁及其合金的热加工温度范围较窄。
镁合金滑移系较少,在室温和低温条件下塑性较差,而且迄今对镁合金塑性变形机理的认识还不够全面和深入,镁合金板材制备及其轧制成形工艺的研究尚处于初
级阶段。
镁合金板材轧制成形的以下特点制约了镁合金板材的发展与应用:
1)镁合
金室温塑性变形能力差,轧制过程中易出现裂纹等变形缺陷;2)目前镁合金板材制
备多采用普通的对称轧制,轧制后的组织有强烈的(0002)基面织构,存在严重的各向异性,不利于后续加工;3)镁合金轧制道次压下量较钢和铝小很多,生产效率不高。
制备优质的镁合金板材,大部分工艺都需要经过多道次轧制工序,轧制过程受许多因素的影响,这些因素可以分为两大类:
第一类为影响轧制金属本身性能的一些因素,即金属的化学成分和组织状态以及热力学条件;第二类为轧制的工艺因素,如轧制温度、轧制变形量和轧制速度以及后续的热处理工艺。
国内外很多学者针对如何改进镁合金轧制工艺和轧制技术,以获得二次成形性能优良的板材做了大量的研究工作。
本文针对镁合金轧制过程中各工艺参数对轧件组织与性能的影响、弱化织构的方法及
机理以及特殊轧制方式做以下介绍。
2轧制过程中的工艺参数
镁合金轧制过程中,轧制温度是关键参数。
Hosokawa等人对AZ31镁合金轧制的
研究表明,轧制温度在225〜400C范围内时,轧制压下量可达85.7%以上而不出现裂纹;200E以下时,成形性能则较差,易出现裂纹。
陈维平等研究了300,330,360C
3个轧制温度对AZ31镁合金组织和硬度的影响。
结果表明,在同一变形量下,随着轧制温度的升高,板材的晶粒呈长大趋势,硬度逐步下降,在330C轧制时,板材的综合性能较好。
镁合金散热较快,轧制过程中镁合金轧件与温度较低的轧辊直接接触,轧辊吸收较多热量,会降低镁合金的轧制性能。
轧制过程中轧辊温度的控制也对轧件性能有很大影响。
生产实践证明,若轧辊不预热,轧制过程中板材易产生表面裂纹和边裂;若轧辊内部温度较低,在轧制过程中仍要吸收大量的热,亦会降低合金的轧制性能。
因此,轧制前一般要先将轧辊预热至150C以上,在薄板轧制过程中则要保证轧辊温度维持在200〜250E范围内。
轧制变形量和轧制速度也是镁合金轧制过程中需考虑的两个重要参数。
变形量过
大时,可能产生边裂;而变形量过小时,不仅效率降低,还会影响板材的组织和性能。
镁合金一般采用多道次小压下量的轧制方式进行,冷轧条件下,AZ31镁合金的最大变形量可达15%但一般都采用道次压下量小于5%两次中间退火的总变形量小于25%的工艺。
然而近年来研究表明,在较高温度下也可进行大压下量轧制,大应变轧制是
制备具有细晶组织的AZ31镁合金板材的简单而有效的工艺,制备的AZ31薄板,晶粒尺寸为2〜5卩m。
2.1轧制温度
轧制温度对镁合金板材轧件的组织与性能有很大影响。
轧制温度过低时,高的应
力集中可导致孪晶形核和切变断裂;而温度过高时,晶粒容易长大而使板材热脆倾向增大。
因此,必须调整和控制好轧制温度以获得符合性能要求的轧件。
镁合金轧制按
照轧制温度可以分为:
高于再结晶温度的热轧,低于再结晶温度但高于冷轧温度的温轧以及冷轧。
AZ31BS合金熔点为650C,再结晶温度再熔,再结晶温度为270C
左右。
重庆大学汪凌云等通过控制轧制温度以及退火制度等,设计出较好的轧制工艺。
2.1.1实验
实验所用材料为AZ31BS合金板材。
热轧开轧温度为450C〜460C,终轧温度为260C〜300E,道次变形量控制在15%〜20%终轧压下量为5%〜10%采用测温仪随时测量板料温度,当板料温度低于260C时,对板材进行回炉加热,保温温度为430C〜450Eo温轧温度低于260C,温轧变形量控制在为25%〜30%温轧温度在再结晶温度以下而又高于冷轧温度。
这种方式能够在一定程度上提高材料的塑性,降低加工硬化。
冷轧阶段采用多道次小变形量的方法轧制板料。
单道次变形量控制在5鸠内,两次中
间退火间累计变形量不大于25%中间退火制度采用300E下保温1ho轧制时在轧辊上增加了轧辊控温装置,使得在轧制过程中轧辊的温度始终控制在100E〜160E左右。
实验时在热轧、温轧和冷轧终了时的板材进行了0°,45°和90°3个方向的取样并进行单向拉伸试验。
2.1.2组织与性能
2.1.2.1热车L
轧制得到的板料边裂很小,表面光洁度好。
当终轧温度低于260E,道次变形量
高于15%寸就出现了严重的边裂,甚至板材中部出现裂纹。
在热轧过程中增加了轧辊的控制装置,使轧辊温度始终保持在100E〜160E左右,同时将轧件多次反复加热,使轧件温度始终控制在热轧范围内,从而减小了裂纹的产生和发展。
图1为AZ31BS合金板材在300E终轧后的显微组织。
从图1可以看出,AZ31BS合金在300E轧制后,为均匀的再结晶组织。
平均晶粒直径为40卩m。
热轧后板材力学性能见表1o
图1AZ31B镁合金热轧板材显微组织
2.1.2.2温轧
温轧的目的是在一定的温度下(高于冷轧低于热轧),采用较大的变形量,从而
得到了抗拉强度比热轧后高的抗拉强度,厚度比热轧小的板材。
AZ31E镁合金典型的温轧工艺为:
温轧温度不大于260C,温轧变形量为25%-30%由于镁合金室温下塑性较差,为了保证压下量的需要,考虑到轧辊温度保持在100C〜160C左右,温轧的终轧温度在100C左右。
所以,温轧工艺的实施主要存在工艺温度范围窄、温度很难保证均匀的缺点,大规模生产时很难控制。
而且当温度低于300r时,采用大变形量轧制会出现严重的边裂,甚至中部也出现裂纹。
图2为AZ31B镁合金温轧后板材显微组织,其力学性能见表1。
图2AZ31B镁合金温轧板材显微组织
2.1.2.3冷轧
冷轧时采用小变形量多道次轧制,冷轧道次变形量一般为5%左右,总变形量约为
25%这样在轧制过程中不会出现严重的边裂和中部裂纹。
但是,当进一步增加变形
量时就出现严重的边裂和裂纹,这说明AZ31B镁合金板材在冷轧时的总变形量不能过大,最好控制在25%〜30流右。
图3为AZ31BS合金冷轧变形后的显微组织。
由图3可知,AZ31BS合金经过冷变形后组织“破碎”,尤其是晶界处的变形量较大,在金相试样侵蚀时很容易腐蚀而出现沟壑,在晶内则出现了大量的孪晶。
冷轧后,形成了加工硬化,延伸率降低,并且由于晶粒转动产生了大量变形织构,形成了各向异性。
冷轧AZ31B镁合金板材的力学性能见表1
图3AZ31B镁合金冷轧板材显微组织
轧后厚度
/mm
取向
/MPa
S/%
热轧
2.0
0°
225-230
17-18
热轧
2.0
45°
225-235
17-20
热轧
2.0
90°
230-235
17-19
温轧
1.6
0°
288
15
温轧
1.6
45°
285
16
温轧
1.6
90°
286
17
冷轧
1.0
0°
300
9
冷轧
1.0
45°
287
9
冷轧
1.0
90°
298
10
表1AZ31B镁合金板材力学性能
2.2轧制变形量
镁合金为密排六方结构,变相能力较差,轧制时道次变形量过大会导致出现裂纹。
冷轧时一般采用小变形量多道次轧制,道次变形量只有5%升高温度可以增加塑性,高温下轧制会发生动态再结晶,轧件可以承受较大的变形量。
重庆大学张丁非等研究了同一热轧温度下不同道次压下量以及不同道次轧制时轧件的组织性能的变化。
2.2.1实验
实验材料为AZ31镁合金板材,轧制前板坯的原始尺寸为100mM30mM16mm轧制前先将AZ31板材在400E下退火300min,随即进入双辊不可逆轧机进行不同压下量多道次的轧制实验。
每轧制一道次留样,并将留样淬火,将其他样品回炉保温5min
后进行下一道次的轧制,观察并记录不同变形率下轧制的表面质量。
轧制温度/r
道次压下量/mm
轧制道次
400
1
11
400
2
5
400
3
4
400
4
3
表2实验方案
2.2.2实验结果及分析
在400C不同压下量不同道次时轧制试样的宏观表面状况,裂纹从头部开始出现,
然后边裂紧接着发生,且每道次压下量越大,能够保证不开裂的道次数越少。
每道次压下量1mm轧制8个道次不会产生裂纹,累积变形量为50%。
每道次轧制压下量2mm轧制3个道次不会产生裂纹,累积变形量为37.5%。
而在每道次轧制压下量为3,4mm的情况下,仅能进行两个道次不开裂轧制,故AZ31镁合金不适合在单次变形量较大的
情况下轧制
轧制温度
/C
道次压下量
/mm
质量
表面、边部质量良好的道次
心部出现裂纹的道次
心部边部轧裂的道次
400
1
1-8
9-10
11
400
2
1-3
4
5
400
3
1-2
3
4
400
4
1-2
-
3
■rbhkii.mn
ti-"J•<11;Iuh山冷
50mim■>um
图4400C时每道次压下量为1mr的显微组织
(a)第2道次(b)第5道次(c)第8道次(d)第11道次
(1)边部组织
(2)心部组织
fill
I
14
*1
MidJk
■/
4'亠
.Ijr
■
戊
./F\fl\\
V
■
/■
g.
■
-4
••■
a.
ID
\
■
螢
■■
1
Zl
■■
■
・*
1i
*\
*
■
4
-
■I—•
r|.1b
_hF_
■&■—
1仆I«•*i•i-1■扃-4—■”呗"■■
024AH1012024hH10
「曲>卩富訴
图5每道次显微硬度和边部与心部晶粒尺寸的对比
(a)显微硬度;(b)晶粒尺寸
图4为400C条件下,每道次压下1mr时第2,5,8,11道次时边部和中间组织的金相图。
图2为每道次压下1mm时的显微硬度和不同道次中间与边部区域组织的晶粒尺寸的对比。
从图4结合图5(b)可以看出,在前4个道次,边部和中间组织的晶粒尺寸区别较明显,由于边部变形程度比中间大,故位错密度也较大,在较高的温度下,发生了回复再结晶,而中间的组织大多数尚存其原始形态。
第5〜8道次边部的再结晶组
织的晶粒发生了晶粒长大,而且长大的较均匀,同时中间的组织也由于累积变形量的增大而开始发生动态再结晶(见图4(c))。
第9到12道次,由于累积的应变量过大,内应力激增,应力集中在这些区域越来越严重,从而产生裂纹,并伴随着裂纹及附近区域晶粒的再结晶细化。
图4(d)显示了这种裂纹的产生情况。
从图5(b)可以看出,晶粒尺寸的变化是比较有规律的,都是先增大后减小,这是由于累积应变量的影响,由于每道次轧制后退火5min不足以消除内应力,从而累积。
由图5(b)还可知前7个道次轧制情况下,边部组织和中间组织的晶粒尺寸相差较大,组织较不均匀。
研究表
明:
组织越均匀晶粒越细小,材料的综合性能越好,而第8道次,边部组织和中间组
织的晶粒度相近分别为中间8.9卩m边部9.2卩m组织较均匀,显微硬度值为67高于平均值,而且从金相图可以看到明显的晶粒细化,故400E左右,每道次压下量为1mm
时,轧制到第8道次总变形量为50%是一个较好的轧制条件。
图6400C时每道次压下2m的显微组织
(a)第3道次(b)第6道次
(1)边部组织
(2)心部组织
图7每道次显微硬度和边部与心部晶粒尺寸的对比
(a)显微硬度;(b)晶粒尺寸图6为400C条件下,每道次轧制压下2m时第3,6道次时边部和中间组织的金相图。
图6是每道次压下2mr时的显微硬度和中间组织与边部区域组织的晶粒尺寸的对比。
从
图6(b)上可以看出在此条件下轧制时,各道次下组织都发生了明显的晶粒细化现象。
分析图6(a)可以看到组织不均匀,可能是再结晶晶粒与原始组织共存,和每道次压下量为1m相同的是,都会出现一个变形带,并且变形带上都是非常细小的等轴状再结晶晶粒,而且开裂也是从变形带区域开始。
从图6(b)可以看到已经出现裂纹,并且裂纹在细小晶粒区。
从图7(b)可以看出随着轧制道次的增加,轧制试样组织的晶粒尺寸是不断减小的,而且没有峰值。
相比较而言,在此条件下轧制,当第2道次,累积压下量为6mm变形率为25%,中间组织和边部组织都比较均匀且较细小,并且显微硬度较大(图7(a))是一个较合适的加工条件,虽然第3道次也没有裂纹产生,但第3道次的组织较不均匀,且硬度较低(图7(a)),而从第4道次开始就有大量裂纹产生。
图8400C时每道次压下3m的显微组织
(a)第1道次(b)第4道次
(1)边部组织
(2)心部组织
图9每道次显微硬度和边部与心部晶粒尺寸的对比
(a)显微硬度;(b)晶粒尺寸
图8为400C每道次压下3m时第1,4道次边部和中间组织的金相图,图9是每道次压下量3mr时的显微硬度和不同轧制道次下中间与边部区域组织的晶粒尺寸的对比。
从图9(b)可以看出第1,2道次,边部组织和中间组织都较不均匀,出现混晶现象(见图8(a)),再结晶晶粒与原始晶粒以及可能异常长大的晶粒同时存在(见图8(a))。
第3道次累积变形量为56.2%,由于变形量太大,一些组织的畸变能较大,发生再结晶时,形核率远远大于线长大速度G,故晶粒为非常细小的等轴状晶,晶粒尺寸只有4.54卩m而粗大晶粒有13.21卩m形成较多的细晶带,易形成裂纹。
故在道次压下3mr1的情况不适合轧制。
图10400°C时每道次压下4mr1的显微组织
(a)第1道次(b)第3道次
图11每道次显微硬度和边部与心部晶粒尺寸的对比
(a)显微硬度;(b)晶粒尺寸
图10为400C条件下每道次压下为4m时第1,3道次的金相图。
图11为道次压下量4m时的显微硬度和每道次下中间再结晶组织与边部区域组织的晶粒尺寸的对比,此条件下由于变形量太大,组织都很不均匀(见图10),而且形成较多的细晶带(见图7(b)),易开裂,故在单道次压下量为4m的情况下,由于变形量太大易产生裂纹,不适合轧制。
由图12可看出,在单道次压下量相同的情况下,随着轧制道次的增加,硬度值总
体上有上升的趋势,而且在上升过程中会出现一个反方向的峰值,这是因为:
在轧制
过程中再结晶的软化过程和加工硬化过程是同时进行的,随着变形量的增大,加工硬
化大于动态再结晶的软化,所以硬度值不断地增大。
在小变形量下,硬度值随着变形量的增大而增大,说明加工硬化的过程主要作用,但每条曲线都有一个凹点值,这个点是一个临界点,在这点附近主要是再结晶起作用。
70
■
•
W/
/
■
■
■Y
■
>心
L1//1/
■
■
%
一•丘
Pti呼%1min
F\f牌^
Perpuss3mrri