马来酸氯苯那敏片生产工艺规程.docx
《马来酸氯苯那敏片生产工艺规程.docx》由会员分享,可在线阅读,更多相关《马来酸氯苯那敏片生产工艺规程.docx(36页珍藏版)》请在冰豆网上搜索。
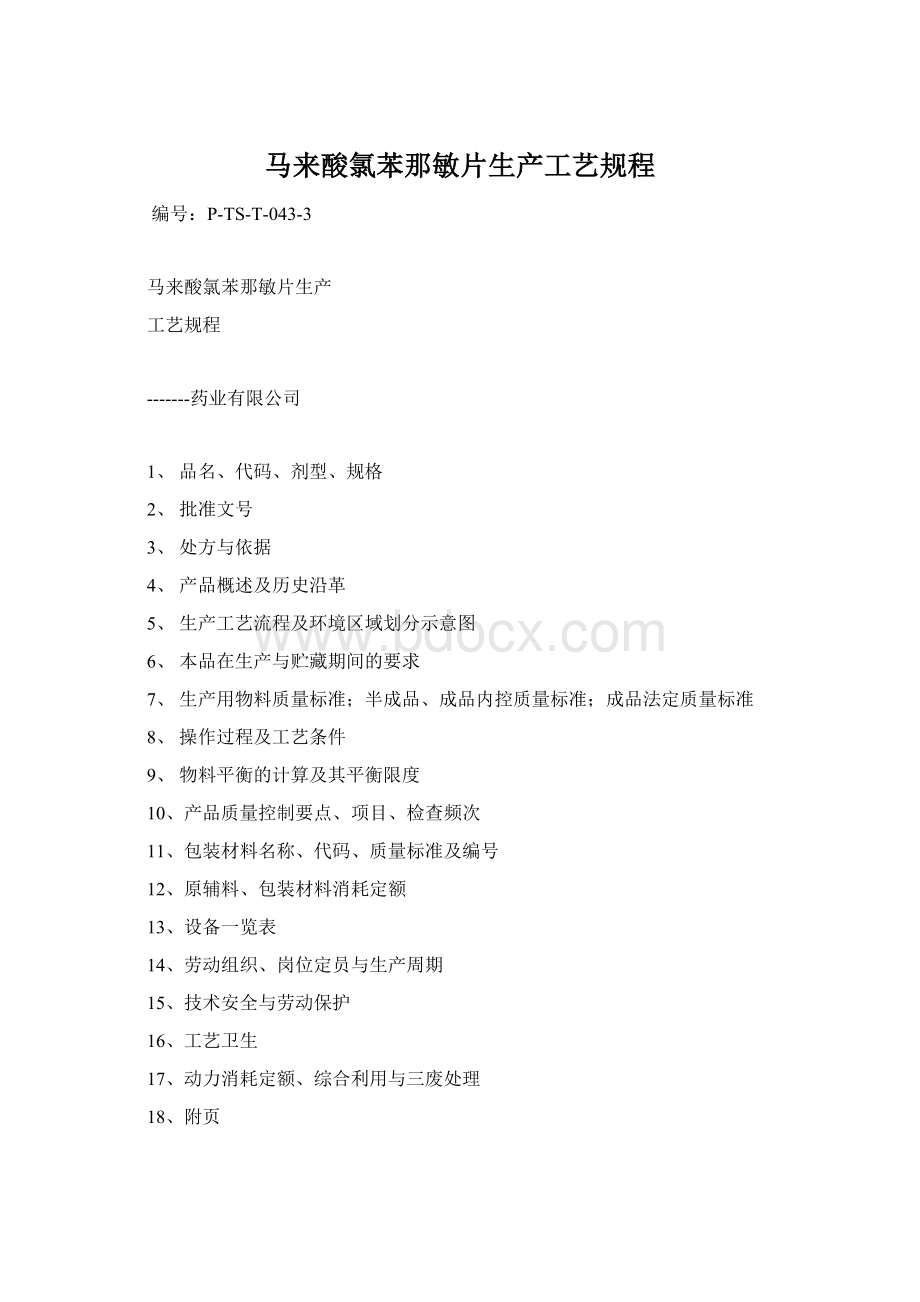
马来酸氯苯那敏片生产工艺规程
编号:
P-TS-T-043-3
马来酸氯苯那敏片生产
工艺规程
-------药业有限公司
1、品名、代码、剂型、规格
2、批准文号
3、处方与依据
4、产品概述及历史沿革
5、生产工艺流程及环境区域划分示意图
6、本品在生产与贮藏期间的要求
7、生产用物料质量标准;半成品、成品内控质量标准;成品法定质量标准
8、操作过程及工艺条件
9、物料平衡的计算及其平衡限度
10、产品质量控制要点、项目、检查频次
11、包装材料名称、代码、质量标准及编号
12、原辅料、包装材料消耗定额
13、设备一览表
14、劳动组织、岗位定员与生产周期
15、技术安全与劳动保护
16、工艺卫生
17、动力消耗定额、综合利用与三废处理
18、附页
药业有限公司GMP管理文件
工艺规程
文件名称:
马来酸氯苯那敏片生产工艺规程
文件类型:
TS
文件编码:
P-TS-T-043-2
起草:
2005年06月08日
审核:
2005年06月10日
批准:
2005年06月12日
执行日期:
2005年06月30日
修订依据:
(1)全面实施药品GMP管理工作;
(2)《中国药典》2010年版二部。
修订目的:
修订和增加部分内容,使生产工艺规程更加完善。
修订编码:
P-TS-T-043-3
修订人:
年月日
审核:
年月日
批准:
年月日
执行日期:
年月日
颁发部门:
生产技术部
分发部门:
固体制剂车间、生产技术部、质量管理部、生产总监、质量总监、验证委员会、总经理
目的:
建立马来酸氯苯那敏片生产工艺规程,明确马来酸氯苯那敏片生产过程的要求和内容,规范马来酸氯苯那敏片生产和质量管理,保证马来酸氯苯那敏片产品的质量。
范围:
马来酸氯苯那敏片生产的工艺过程。
责任人:
公司生产和质量管理人员,车间管理人员。
1、品名、代码、剂型、规格
1.1品名:
马来酸氯苯那敏片
1.2代码:
CG068
1.3剂型:
片剂
1.4规格:
4mg
2、批准文号
国药准字H41025423
3、处方与依据
3.1处方
原辅料名称
原辅料
代码
规格
1,000片
用量(kg)
实际生产执行配方用量
300万片(kg)
备注
马来酸氯苯那敏
YG057
80目
0.004
12
淀粉
FG004
120目
0.04
120
糊精
FG009
120目
0.03
90
羧甲淀粉钠
FG010
80目
0.0007
2.1
硬脂酸镁
FG003
80目
0.0007
2.1
乙醇
FY014
27%~29%
适量
72~81
3.2处方依据
中国药典2010年版二部
4、产品概述及历史沿革
4.1产品概述
本品每片含马来酸氯苯那敏4毫克。
辅料为:
淀粉、糊精、羧甲淀粉钠、硬脂酸镁。
4.1.1性状:
本品为白色片。
4.1.2适应症:
本品适用于皮肤过敏症;荨麻疹、湿疹、皮炎,药疹,皮肤瘙痒症、神经性皮炎、虫咬症、日光性皮炎。
也可用于过敏性鼻炎,药物及食物过敏。
4.1.3用法用量:
口服。
成人一次1片,一日3次。
4.1.4包装:
口服固体药用高密度聚乙烯瓶装,100片/瓶,1000片/瓶;聚氯乙烯固体药用硬片、药品包装用铝箔,24片×1板/盒。
4.1.5贮藏:
遮光,密封保存。
4.1.6有效期:
24个月。
4.2历史沿革
我公司马来酸氯苯那敏片于1982年4月12日经河南省卫生厅批准生产,批准文号为豫卫药准字(1982)32016号,执行标准为中国药典1977年版;1996年批准文号变更为豫卫药准字(1996)032016号;执行标准为中国药典1995年版;2003年7月1日经国家药品监督管理局重新注册为国药准字H41025423;执行标准为中国药典2000年版,2005年7月1日执行中国药典2005年版。
2010年10月1日,执行中国药典2010年版二部。
5、生产工艺流程及环境区域划分示意图
原辅料
↓
粉碎
↓
称量
↓
干混
27%~29%乙醇
↓←------------------┘
制软材
↓
制粒
↓
干燥
↓
整粒
硬脂酸镁
↓←------------------┘
总混
↓
冲模
——→
压片
↓
内包
←———
内包材
↓
外包
←———
外包材
↓
入库
洁净区
一般区
6、马来酸氯苯那敏片在生产与贮藏期间的要求
本品在生产与贮藏期间均应符合以下规定:
6.1本品生产所用原辅料均为药用级别。
6.2原辅料贮存间应保持清洁,符合相应的洁净级别。
6.3中间产品、包装材料与物料应定置存放;应悬挂物料状态卡,标明名称、规格、批号、数量等。
6.4不同物料之间应有一定的间隔,防止混淆。
6.5尽量缩短生产周期(正常生产周期8天)。
6.6为了提高本品稳定性,颗粒水分应控制在3.0%~5.0%,半成品与成品贮存过程中要遮光,密封保存。
7、生产用物料质量标准及成品法定质量标准;半成品、成品内控质量标准
7.1物料质量标准及成品法定质量标准(详见下列目录文件),马来酸氯苯那敏及马来酸氯苯那敏片法定质量标准视附页1
质量标准名称
质量标准编号
马来酸氯苯那敏质量标准
ZL-TS-Y-026-0
淀粉内控质量标准
ZL-TS-F-011-0
糊精内控质量标准
ZL-TS-F-012-0
羧甲淀粉钠内控质量标准
ZL-TS-F-031-0
乙醇内控质量标准
ZL-TS-F-007-0
硬脂酸镁内控质量标准
ZL-TS-F-013-0
纯化水内控质量标准
ZL-TS-F-002-0
马来酸氯苯那敏片质量标准
ZL-TS-T-001-0
7.2半成品内控质量标准
颗粒性状本品为白色颗粒
颗粒水分3.0~5.0%
含量5.4%~6.0%
溶出度限度应不低于标示量的75%
重量差异限度±7.0%
脆碎度<0.9%
7.3成品内控质量标准
性状本品为白色片
鉴别
(1)
(2)(3)应符合规定
溶出度限度应不低于标示量的75%
含量均匀度应符合规定
脆碎度<0.9%
含量94.0%~106.0%
微生物限度细菌数每1g不得过900个
霉菌数和酵母菌数每1g不得过90个
大肠埃希菌每1g不得检出
8、马来酸氯苯那敏片生产操作过程及工艺条件
8.1洁净区环境要求
洁净级别:
30万级;温度18~26℃;相对湿度:
45%~65%;压差:
洁净区与非洁净区之间的压差应不低于10Pa,相同洁净等级不同功能的操作间之间应保持适当的压差梯度。
8.2洁净区各工序(制粒、总混、压片、内包)生产前的准备
8.2.1凭生产指令,领料员到仓库领取合格的物料,按照物料进入洁净区程序进行清洁后进入洁净区。
8.2.2岗位操作人员严格按照口服固体制剂30万级洁净区更衣程序,洗手、消毒、更衣后进入洁净区。
8.2.3根据批生产指令,岗位负责人悬挂操作间、设备、容器等现行生产状态标示卡。
8.3洁净区各工序(制粒、总混、压片、内包)生产前的检查
8.3.1由班长或操作人员对下列项目进行检查:
(1)检查并记录操作间及相关辅助间的温度、相对湿度、压差是否符合要求,如有异常,应立即报告车间主任,由车间主任联系设备管理人员进行处理。
(2)岗位应有批生产指令。
(3)应有各岗位相关操作规程和空白记录、上批清场合格证副本。
将上批清场合格证副本附于本批生产记录之前。
(4)盛装物料的容器、操作间应处于“已清洁”状态;设备状态应完好,处于“已清洁”状态。
上述均应在有效期内,否则应重新消毒。
(5)计量器具的称量范围与待称物料的重量应相符;计量器具上应有“检定合格”标志。
并且在规定的有效期内。
(6)根据当天生产指令,对领入的物料进行称量前的复核,复核内容:
物料名称、批号、数量、有效期、生产厂家、外包装情况且无其他异常现象(如变色、异味)。
8.3.2质监员确认岗位有“清场合格证”且在有效期内,操作间、设备、设施等状态符合要求,且无与本次生产无关的物品后,方可批准进行生产。
8.4生产操作过程(制粒、总混、压片、内包)
8.4.1制粒工序生产操作
本工序的三维混合、粉碎过筛操作间与洁净走廊及相邻操作间应保持相对负压(>5Pa)。
8.4.1.1原辅料(马来酸氯苯那敏、淀粉、糊精、乙醇、羧甲淀粉钠、硬脂酸镁)根据生产指令进行核对后,经清外包去皮后,进入缓冲间进行消毒处理后(紫外线照射30分钟或75%酒精擦拭外壁)进入洁净区,存放于备料室。
8.4.1.2原辅料使用前岗位操作人员应目检,核对原辅料名称、数量、规格、批号、有效期、生产厂家等,应符合要求
8.4.1.3粉碎过筛:
8.4.1.3.1核对原料(马来酸氯苯那敏)名称、规格、批号与数量是否与工艺条件相符并做好记录。
8.4.1.3.2粉碎至规定细度。
8.4.1.3.3按工艺对物料的规格要求过筛80目。
8.4.1.3.4工艺条件:
(1)滤网、筛网每次使用前后应检查磨损和有无破裂情况。
(2)过筛和粉碎设备应有吸尘装置,含尘空气经处理后排放。
粉碎过筛室相对前室缓冲间应为负压。
(3)剩余的原料(马来酸氯苯那敏)应立即密闭退回备料室,并标明品名、规格、剩余量。
8.4.1.4称量、混合及单元投料量:
将处方中原辅料:
马来酸氯苯那敏12kg、糊精90kg、淀粉120kg、羧甲淀粉钠2.1kg称量后,根据《三维混合机标准操作规程》(P-OS-T-216-2)混合30分钟。
硬脂酸镁称量后在总混时加入。
将混合后的物料(222.0~224.1kg)分为3份(为单元投料量);上述物料称量分份后装入净料袋,挂上物料标示卡(标明名称、规格、批号、数量、操作人、复核人等),置暂存间分批存放备用。
称量时均一人称量,一人复核。
8.4.1.5湿润剂的制备:
制法:
取95%乙醇,加适量纯化水制成27%~29%乙醇。
8.4.1.6投料:
准备单元投料量物料,一人投料,一人复核,防止差错。
8.4.1.7制粒:
8.4.1.7.1确认投料完毕,根据《高效湿法混合制粒机操作规程》(P-OS-T-204-2)进行操作,要求主搅拌桨转速为150~180r/min(频率为25~30Hz),干混时间5分钟,干混结束后,加入27%~29%乙醇24.0~27.0kg搅拌10~15分钟,制成“握之成团,触之即散”的软材。
8.4.1.7.2在摇摆式颗粒机上装入18目不锈钢筛,安装时要松紧一致,保证颗粒均匀,将软材加入颗粒机的料斗内,一次加入量不能过多,以不超过料斗高度的2/3为宜,应缓缓加料,制成湿颗粒。
颗粒应显沉重,少细粉,整齐而无长条。
具体操作见《摇摆式颗粒机标准操作规程》(P-OS-T-222-2)。
8.4.1.7.3将湿颗粒平铺于料盘内,厚度约为10~15mm,装入烘车架上,推入热风循环烘箱中,关上烘箱门,根据《热风循环干燥烘箱标准操作规程》(P-OS-T-235-2)设定干燥温度55℃,启动风机,打开蒸汽阀门,进行加热干燥,干燥时间为240~270分钟。
8.4.1.7.4定期检查烘箱内的温度,控制在55℃±5℃,并根据颗粒干燥情况按要求翻料,翻料时应谨慎操作,动作幅度不能太大,以免洒落颗粒。
8.4.1.7.5物料干燥后,关闭加热开关,停止加热,待物料进行冷却后,关闭排风机。
8.4.1.7.6干燥结束后,用手紧握干粒,在手放松后颗粒不应粘结成团,手掌也不应有细粉粘附;或以食指和拇指取干粒捻搓时应粉碎,无潮湿感后,每个烘箱中分别随机在烘车架的上、中、下料盘中取样,用水分快速测定仪预测水分,符合中间产品水分规定(3.0%~5.0%)后出料,盛入洁净容器内,做好标识卡(标明品名、规格、批号、数量、质量等),转下道工序。
8.4.1.8记录:
生产操作时,同步填写生产记录,要求及时填写、内容真实、字迹清晰、易懂,不易擦掉。
8.4.1.9清场:
8.4.1.9.1生产结束后,操作人员根据《各工序清场管理规程》(P-MS-C-016-2)进行清场。
关闭设备电源,清理、清洁工作场所,根据《三维混合机清洁规程》(P-OS-T-001-2)、《摇摆式颗粒机清洁操作规程》(P-OS-T-010-2)和《高效湿法制粒机清洁规程》(P-OS-T-020-2)等清洁设备、工器具。
上交有关文件(各项记录、岗位SOP等),确保现场无与下一批产品生产不相关的文件。
8.4.1.9.2清场结束时,更换状态标示卡,及时悬挂操作间、设备等“已清洁”标示。
8.4.1.9.3质监员检查验收清场合格后,发放清场合格证正、副本(正本附于本批清场记录后,副本留在本岗位作为下次生产前本岗位已清洁合格的凭证,并纳入下次产品的批记录中)。
8.4.2总混工序生产操作
本工序与洁净走廊及相邻操作间保持相对负压(>5Pa)。
8.4.2.1物料(颗粒、辅料)使用前先目检,核对辅料名称、规格、批号、数量、生产厂家等,应符合要求,对处方进行计算复核后,进行操作。
8.4.2.2整粒:
8.4.2.3检查马来酸氯苯那敏片颗粒的品名、规格、批号、数量、质量等,应与物料标示卡一致。
质量应符合要求。
8.4.2.4将摇摆式颗粒机安装上筛网,根据《摇摆式颗粒机标准操作规程》(P-OS-T-222-2)进行操作,干颗粒加入机器内经过摆动作用通过16目筛网进行整粒。
整理后颗粒进行称重,得整理后颗粒214.0~218.0kg。
8.4.2.5总混:
将三维混合机料口运行到合适的位置,将整粒好的颗粒214.0~218.0kg,硬脂酸镁2.1kg装入混合机内,装量控制在容量800L的80%(640L)以内,根据《三维混合机标准操作规程》(P-OS-T-216-2)启动操作进行混合,时间要求20分钟,电机转速控制在400~600r/min范围内。
8.4.2.6出料:
将混合机出料口运行到合适的位置,打开出料口将混合好的颗粒放入洁净的容器内,准确称量各包装的重量,得总混后颗粒214.0~220.0kg,用药用低密度聚乙烯袋双层包装(内、外袋分别扎口,将物料标示卡在两袋中间放置)。
工作结束后,将颗粒送入中间站待验。
中控检验,合格后进行下道工序操作。
8.4.2.7记录:
生产操作时,同步填写生产记录,要求及时填写、内容真实、字迹清晰、易懂,不易擦掉。
8.4.2.8物料平衡:
生产结束后应进行物料平衡计算,如低于或超出正常范围(99.0%~100.0%),应立即上报车间主任,并分析发生的原因,按偏差处理程序进行处理。
8.4.2.9清场:
8.4.2.9.1生产结束后,操作人员根据《各工序清场管理规程》(P-MS-C-016-2)进行清场。
关闭设备电源,清理、清洁工作场所,根据《摇摆式颗粒机清洁操作规程》(P-OS-T-010-2)和《三维混合机清洁规程》(P-OS-T-001-2)等清洁设备、工器具。
上交有关文件(各项记录、岗位SOP等),确保现场无与下一批产品生产不相关的文件。
8.4.2.9.2清场结束时,更换状态标示卡,及时悬挂操作间、设备等“已清洁”标示。
8.4.2.9.3质监员检查验收清场合格后,发放清场合格证正、副本(正本附于本批清场记录后,副本留在本岗位作为下次生产前本岗位已清洁合格的凭证,并纳入下次产品的批记录中)。
8.4.2.10可能出现的异常情况的报告和处理:
(1)发现有质量问题时或有潜在的质量隐患时,应及时报告质量管理人员。
(2)首次生产时,当确认按工艺规定操作,中间产品仍不符合内控量标准时,应立即查找原因,并报告车间主任,车间主任报生产技术部、质量管理部及验证委员会,采取相应的补救措施,并申请对该操作系统及相关技术参数进行再验证。
(3)颗粒细粉太多:
①湿润剂用量少或软材太松,导致颗粒太疏松。
处理方法:
将本批物料粉碎后重新制粒,并报质量部门备案。
②筛网孔径太小造成颗粒细粉太多,处理方法:
更换合适的筛网目数,并报验证委员会。
(4)颗粒较硬,细粉太少:
粘合剂用量太多或制软材时软材搅拌时间长。
处理方法:
制粒工序减少粘合剂用量或减少制软材搅拌时间,并报验证委员会。
(5)混合不均有明显的润滑剂痕迹。
原因:
混合速度低,时间短。
处理方法:
调整速度,保证时间。
8.4.3压片工序生产操作
本工序与洁净走廊及其他操作间保持相对负压(>5Pa)。
8.4.3.1马来酸氯苯那敏片颗粒使用前先目检,核对物料品名、规格、批号、数量、生产日期等,应符合要求。
8.4.3.2根据颗粒重量计算片重,按颗粒含量定片重:
应压片重=0.004g/马来酸氯苯那敏颗粒百分含量,结合理论片重(g)=批颗粒总量(g)/投料量(片)。
实压片重应控制在内控标准规定的范围内。
8.4.3.3操作人员按工艺要求,到模具室领取直径为5.5mm的平斜冲,并填写领用记录,检查冲头冲模的规格是否与工艺要求一致,检查冲头冲模光洁度,有无凹槽、卷边、缺角、爆冲、磨损现象、长短是否一致,发现问题及时报告岗位负责人,并及时更换。
8.4.3.4操作人员将领取后的冲头冲模准确安装在压片机上,紧固冲模后,装上加料器、料斗等,转动压片机手轮,上下冲应灵活。
注油试机。
8.4.3.5将颗粒用不锈钢簸萁加入加料斗内,同时打开吸尘器,按计算的应压片重进行压片试生产,调节片子的平均重量,合格后,再调整压力至35~40KN,或两者交替调整,防止压力过大,片子硬度和重量均合格后,再对转速(一般控制在16~24r/min范围内)进行调整,然后再调整一次片子重量,防止转速提高片重有变化。
质监员取样检测平均片重、重量差异、脆碎度、崩解时限等,合格后开始进行生产。
8.4.3.6压片过程中操作人员必须每间隔15~20分钟取样一次,检查平均片重,并及时调整片重。
不定期检查外观质量,防止油污点、松得、裂片等的发生。
片子进入不锈钢筛中,筛下的颗粒性粉末及时加入待压颗粒内混均匀。
生产结束后清除机器上的细粉和小颗粒及落地料,统一收集,按尾料处理程序进行处理。
8.4.3.7合格的素片盛入双层药用低密度聚乙烯袋中(内、外袋分别扎口),称量后将物料卡(注明品名、规格、批号、数量、质量、操作人等)放在两袋中间,交中间站待验。
8.4.3.8记录:
生产操作时,同步填写生产记录,要求及时填写、内容真实、字迹清晰、易懂,不易擦掉。
8.4.3.9物料平衡
生产结束后应进行物料平衡计算,如收率低于或超出正常范围(98.0%~100.0%),应立即上报车间主任,并分析发生的原因,按偏差处理程序进行处理。
8.4.3.10清场
8.4.3.10.1生产结束后,操作人员根据《各工序清场管理规程》(P-MS-C-016-2)进行清场。
关闭设备电源,清理、清洁工作场所,根据《旋转式压片机清洁操作规程》(P-OS-T-015-2)清洁设备、工器具。
上交有关文件(各项记录、岗位SOP等),确保现场无与下一批产品生产不相关的文件。
8.4.3.10.2清场结束时,更换状态标示卡,及时悬挂操作间、设备等“已清洁”标示。
8.4.3.10.3质监员检查验收清场合格后,发放清场合格证正、副本(正本附于本批清场记录后,副本留在本岗位作为下次生产前本岗位已清洁合格的凭证,并纳入下次产品的批记录中)。
8.4.3.11压片时可能发生的困难及处理方法:
8.4.3.11.1松片
松片在压片操作中时常发生,片子置于中指与食指之间,如用拇指轻压即碎裂,或放入空瓶内,轻轻振摇即碎裂者称之为松片,究其原因可分以下几点:
(1)压片时压力不足。
由于压片时压力不足,不能使颗粒互相密切粘结,如适当加大压力,即可克服松片现象,但压力不可过大,以免导致片子崩解困难或产生裂片。
(2)冲头长短不齐。
调换冲头即可。
(3)因颗粒引起的松片
①粘合剂用量不足或选择不当导致所制得的颗粒质松,细粉较多,压片时即使加大压力亦不能克服,只有另选粘性更强的粘合剂重制颗粒。
②颗粒过于干燥。
喷洒60%乙醇水溶液混匀过筛即可。
(4)操作不当,例如由于粉末堵塞下冲而不能动,装的颗粒少。
8.4.3.11.2裂片
裂片亦称顶裂,即片子压成后,一经震动或放置后,即自片腰中部分裂成二片或三片的现象。
(1)压力过大:
压力过大,颗粒受压力增加,膨胀程度亦增加,粘合剂的结合力不能抑制其膨胀,故造成裂片,应减低压力处理。
(2)上冲与模孔不符合要求。
使用日久的冲模,日渐磨损,导致上冲与模孔吻合不正常,上冲带有尖锐向内的卷边,压力便不匀使片子的部分受压过大,而造成顶裂或模圈走样变形,其情况大致有三种:
①模孔内部倾斜,形成上大下小。
②模孔内径中部稍大,而两端小,则在片子顶击模孔时裂片。
③模孔内径中部较小而两端较大,则不易裂片。
(3)压片机转速过快,片子受压时间过短,使片子突然受压而紧缩,接着又突然发生膨胀而裂片。
8.4.3.11.3粘冲
一般发生在上冲,冲头或模孔粘有粉末或细粒时所压出之片子表面有凹痕或边缘现缺口,非但影响片子外观,亦常使主药含量不足,其原因为:
(1)新制冲头在用时表面不光滑或因冲头长久使用,或在保存及装入机体时不慎,而使冲头表面发生碰撞,导致冲头遭受损坏,易在压片过程中产生粘冲现象。
(2)颗粒中润滑剂用量不足。
润滑剂的主要作用,即为避免粘冲现象,故用量不足即可发生粘冲现象。
可加入足量的润滑剂,并混合均匀。
(3)颗粒不干或受潮:
颗粒干燥不好,其水分过高会出现粘冲,干颗粒受潮后可使润滑作用减低而发生粘冲现象。
处理方法:
可将湿颗粒再烘干后压片。
8.4.3.11.4重量差异增加:
压片过程中,重量差异不能超出药典所规定的限度方为合格,但在压片过程中,常发现重量差异增加,其原因为:
(1)加料斗与刮粉器不平衡:
多冲双轨旋转式压片机其前后各装有一只加料斗与刮粉器,如装时不平衡,则可造成一只加料斗中颗粒落下的速度快,而刮粉器上堆积的颗粒多;另一只加料斗中颗粒落下的速度较慢,而刮粉器上堆积的颗粒少,故易造成颗粒加入模孔时不平衡,而造成重量差异增加。
处理方法是:
可调整加料斗与刮粉器的位置,使两加料斗中颗粒相似,使颗粒能均匀地加入模内。
(2)加料斗中颗粒过少,或颗粒落下不匀:
加料斗中颗粒装量的多少,可影响其中颗粒落入刮粒器上颗粒的多少,如填入模孔中的量不足,致压出片重量减轻,故加料斗中的颗粒应保持足够的颗粒量(一般为加料斗容积的1/3以上)。
(3)加料斗堵塞。
在压片时如所用的颗粒细小,有粘性或过湿,可能系因加料斗装得过满,易使加料斗饲粒器堵塞,流动不畅,使填充模孔的数量不等,导致片重差异增加。
处理方法:
可将加料斗饲粒管稍加扩张,并在加颗粒时避免过满,防止堵塞。
(4)刮粉器堵塞。
颗粒中偶有棉纱头或药料等异物,混入颗粒而落于刮粉器时,亦能使加入模孔的颗粒减少,影响片重,若遇片重突然减轻时,应立即停车检查。
(5)产生片重变化的原因,绝大多数系由于压片机产生故障,或工作上疏忽所造成;故在压片过程中,应该做好机件保养工作,详细检查机件有无损害,并每隔一定时间(15~20分钟)称量一次平均片重。
8.4.