工程塑料在汽车上的应用下.docx
《工程塑料在汽车上的应用下.docx》由会员分享,可在线阅读,更多相关《工程塑料在汽车上的应用下.docx(7页珍藏版)》请在冰豆网上搜索。
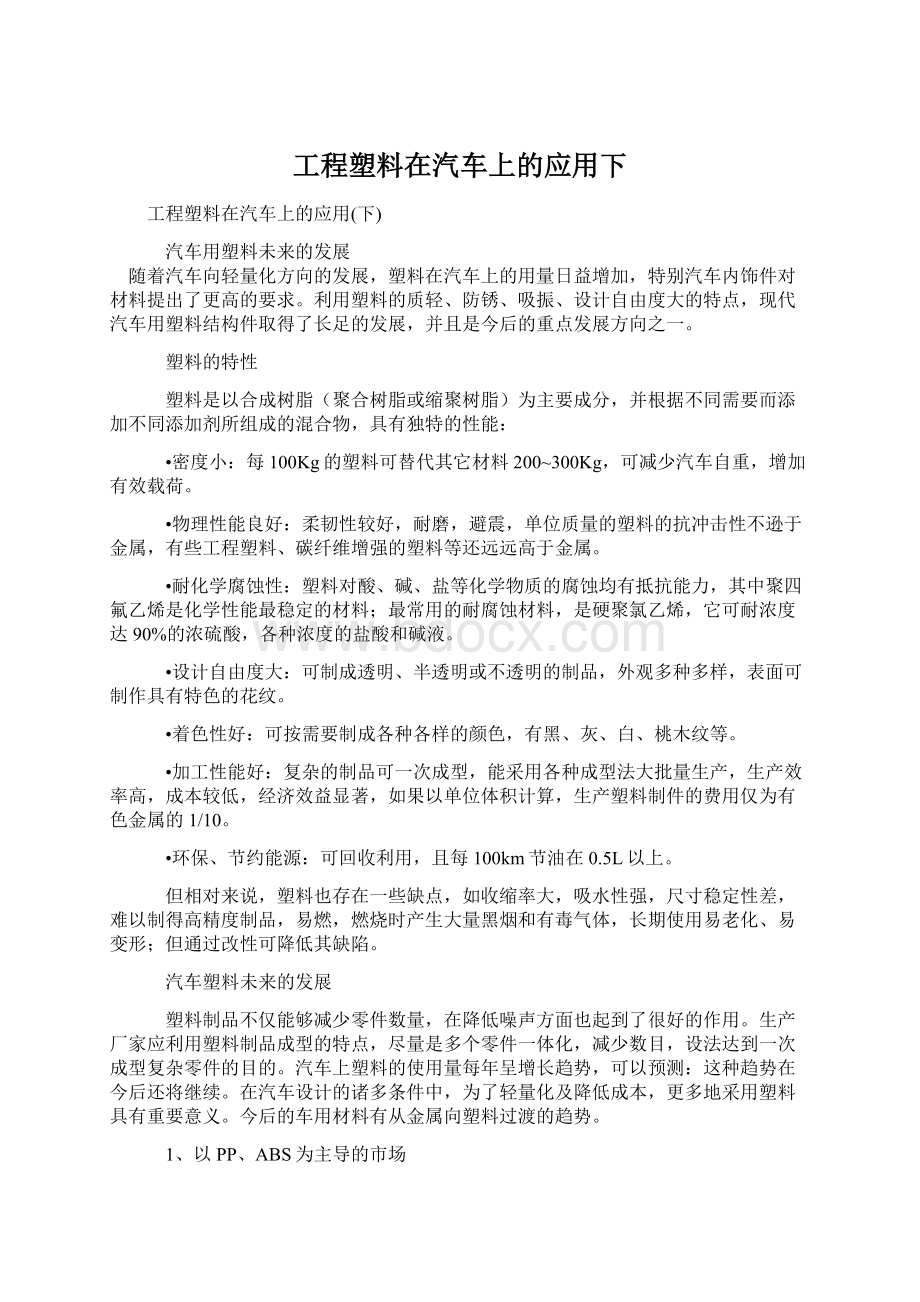
工程塑料在汽车上的应用下
工程塑料在汽车上的应用(下)
汽车用塑料未来的发展
随着汽车向轻量化方向的发展,塑料在汽车上的用量日益增加,特别汽车内饰件对材料提出了更高的要求。
利用塑料的质轻、防锈、吸振、设计自由度大的特点,现代汽车用塑料结构件取得了长足的发展,并且是今后的重点发展方向之一。
塑料的特性
塑料是以合成树脂(聚合树脂或缩聚树脂)为主要成分,并根据不同需要而添加不同添加剂所组成的混合物,具有独特的性能:
•密度小:
每100Kg的塑料可替代其它材料200~300Kg,可减少汽车自重,增加有效载荷。
•物理性能良好:
柔韧性较好,耐磨,避震,单位质量的塑料的抗冲击性不逊于金属,有些工程塑料、碳纤维增强的塑料等还远远高于金属。
•耐化学腐蚀性:
塑料对酸、碱、盐等化学物质的腐蚀均有抵抗能力,其中聚四氟乙烯是化学性能最稳定的材料;最常用的耐腐蚀材料,是硬聚氯乙烯,它可耐浓度达90%的浓硫酸,各种浓度的盐酸和碱液。
•设计自由度大:
可制成透明、半透明或不透明的制品,外观多种多样,表面可制作具有特色的花纹。
•着色性好:
可按需要制成各种各样的颜色,有黑、灰、白、桃木纹等。
•加工性能好:
复杂的制品可一次成型,能采用各种成型法大批量生产,生产效率高,成本较低,经济效益显著,如果以单位体积计算,生产塑料制件的费用仅为有色金属的1/10。
•环保、节约能源:
可回收利用,且每100km节油在0.5L以上。
但相对来说,塑料也存在一些缺点,如收缩率大,吸水性强,尺寸稳定性差,难以制得高精度制品,易燃,燃烧时产生大量黑烟和有毒气体,长期使用易老化、易变形;但通过改性可降低其缺陷。
汽车塑料未来的发展
塑料制品不仅能够减少零件数量,在降低噪声方面也起到了很好的作用。
生产厂家应利用塑料制品成型的特点,尽量是多个零件一体化,减少数目,设法达到一次成型复杂零件的目的。
汽车上塑料的使用量每年呈增长趋势,可以预测:
这种趋势在今后还将继续。
在汽车设计的诸多条件中,为了轻量化及降低成本,更多地采用塑料具有重要意义。
今后的车用材料有从金属向塑料过渡的趋势。
1、以PP、ABS为主导的市场
据英国应用信息(AMI)报告,到2000年为止,轿车零部件消耗的热塑性塑料仍然以年均超过6%的速度递增,而由于PP价格低廉且性能优越,所以汽车内外饰件的发展将以PP为主,现在市场上使用的PP零件占市场份额的42%,且可望以每年8%的速度增长,特别集中的汽车内饰方面。
2、应用范围正在扩大
塑料在汽车中的应用范围正在由内饰件向外饰件、车身和结构件扩展,今后的重点发展方向是开发结构件和外装件。
3、开发复合型材料
复合型材料在汽车零部件上的应用也越来越显示其强大的生命力。
汽车上使用复合材料的零件主要是仪表板、门护板、顶盖内护板、地毯、座椅及包裹架护板,它们基本上是由表皮(塑料、织物、地毯),隔音减振部分(泡沫或纤维)和骨架部分组成,这种形式的零件除满足一定的使用功能外,又使人感到舒适美观,而且由于该种材料生产工艺简单,成本低廉、适用性强而发展得比较迅速,它将是今后汽车内饰材料的主要发展方向。
4、工程塑料的需求量将逐年增大
工程塑料,尤其是高性能工程塑料因其具有良好的机械性能、综合力学性能,还有耐热、耐酸,寿命长,可靠性好,而越来越广泛地用于汽车工业,其前景非常好,例如发动机上的一些零部件像调速阀、机动盘、气流盘、水泵、输油管、皮带轮罩、冷却风扇、油门踏板等等已开始使用PA、PPS、PBT等注塑或吹塑成型。
5、玻璃纤维增强塑料的应用也有进一步扩大的趋势
玻璃纤维增强塑料俗称“玻璃钢”,具有质轻、比强度高、耐腐蚀、电绝缘、耐瞬时高温、传热慢、隔音、防水、易着色,能透过电磁波,成型方便,具有可设计性等优点,广泛用于生产保险杠、车顶盖、导流罩、电瓶托架、挡泥板、前脸部件、裙边部件及车身壳体等。
6、向安全性方面发展
在现今交通事故不断、乘客安全受到威胁的情况下,部分内饰零件的安全性检验己纳入议事日程。
比如,仪表板上表面的头部冲击试验;其下边缘的膝盖撞击试验;座椅靠背的身体冲击试验等,均要求被检验的内饰塑料不能碎裂,更不能碎片四溅或出瑰棱角伤人。
因此,汽车内饰零件不仅要求舒适美观,更要求能保护乘客安全。
塑料在汽车工业的应用
随着科技进步,汽车采用塑料是不可逆转的趋势,它对提高汽车效能、美观及轻量化的要求扮演愈来愈重要的角色。
目前,汽车用塑料已由普通的装饰用途,发展至制造结构性及功能性的部件,要求也不断提高,例如耐热、高强度及抗冲击性便是最常见的要求,一般处理的方法是采用复合材料或塑料合金。
目前,德国制造的汽车使用塑料平均约占用材的22%,是使用塑料最多的汽车工业国,而日本汽车使用的塑料则占用材的7.5%左右。
随着科技进步,汽车采用塑料是不可逆转的趋势,它对提高汽车效能、美观及轻量化的要求扮演愈来愈重要的角色。
目前,汽车用塑料已由普通的装饰用途,发展至制造结构性及功能性的部件,要求也不断提高,例如耐热、高强度及抗冲击性便是最常见的要求,一般处理的方法是采用复合材料或塑料合金。
目前,德国制造的汽车使用塑料平均约占用材的22%,是使用塑料最多的汽车工业国,而日本汽车使用的塑料则占用材的7.5%左右。
汽车内饰件包括仪表板、门内板、座椅、顶棚、门手柄等;外饰件包括保险杠、散热器格栅、档泥板、侧防撞条及灯类。
例如制造侧防撞条可用PVC制成的中空型材,并把金属芯材插入其中;在高级轿车上,则用反应注射成形法制造PUR防撞条;如考虑循环再造的问题,便可以使用改性PP。
事实上,由于改性PP及PE的性能较佳,其应用的发展正在加快。
据调查,目前汽车用外饰件的市场规模约19亿美元;而到2006年,其年均增长率可望达3.0%,届时的市场规模将达到22亿美元。
塑料外饰件采用五种主要的塑料,包括:
热固性塑料、TPE(热塑性弹性体)、工程树脂、日用热塑性塑料以及合金或半合金。
其中热固性塑料外饰件的市场最大,以5.6亿美元的规模占市场的三成左右,其市场增长也将是最快,在未来四年的年均增长率可望达4.4%。
工程树脂目前占汽车塑料外饰件的第二大市场,其2001年的市场规模约5亿美元,但预计未来五年的年均增长率将会是最低。
汽车保险杠是TPE的重要应用领域,其中又以TPO(热塑性聚烯烃)为主。
此外,汽车外壳的裙边模塑件、仪表透明罩、前大灯/信号灯的外壳以及车身内饰板等,也是使用塑料较多的部分,发展速度非常高。
纳米塑料更轻更强
纳米技术是近年全球的热门话题,无论在先进的航天工业,或是普通的纺织及塑料产品,都可以利用它来提升竞争力。
该技术的基本原理是,控制原子在物质中的排列,工程师可以利用这个特性,因应工作环境的要求,人为地把原子排列成最理想的状态。
例如纳米碳管轻巧及强度高,十分适合应用于航天工业。
纳米技术近年对塑料也有相当的贡献。
先进的TPO纳米材料具有重量轻、表现良好及经济效益高等优点。
此物料首次用于汽车外部件,便是在GM中型货车出现的复合部件,为一方便乘客上落的装置。
该部件的强度高及重量轻,在寒冬时的脆性较低。
由于没有额外使用添加剂,没有循环再造的问题。
纳米复合部件与传统TPO部件的体积相约,但由于所需的物料更少,因此成本较低。
纳米部件与热塑性塑料制品的生产程序一样,无需采用另类模具或考虑个别模具的设计。
制造纳米复合物时,只需在树脂加入固体以提高强度,其使用的粒子极细,厚度只有10-6mm;相对来说,加入纤维的TPO的平均厚度高出一千倍。
塑料车身板前景如何?
KermitWhitfield
2005版通用土星Relay微型厢车于去年秋季推向市场,该车型最值得注意的一点是-他没有了塑料车身板。
尽管土星长久以来一直在聚合物车身板应用领域拔得头筹,而其他所有的汽车厂商仍然在应用传统的压铸钢。
但是以前一度独立的土星(通用分公司)如今正越加紧密地回归通用的产品群,这意味着将会使用更多的钢材料。
在即将于新的平台上生产推出的大SUV和Roadster(双座敞篷车)中,也将确定使用钢材制造车身板(尽管土星在这个项目上对外保持沉默)。
这不得不让我们产生怀疑:
如果使用聚合物材料的推动力正在日益淡出人们的视野,那么塑料车身板还有前景么?
塑料的远去。
土星曾生产了三百多万辆配备塑料车身板的汽车,但是Relay车型却第一次采用全钢结构,而且这种情形还会不断发展下去。
来自塑料材料供应商的回答无疑是“当然”,而且充满信心。
事实上,他们如今对塑料材料的应用前景比过去更为乐观,这是因为他们综合市场、成本和技术各类因素,创造出更有利于塑料材料的应用环境,至少在某些特定的应用类型中,的确是这样的。
汽车上主要引人关注的易碰撞点是挡泥板和车身板。
据拜耳聚合物公司(BayerPolymers)预测,到2010年,美国和欧洲仅就热塑挡泥板一项的市场需求就将翻上一番。
而来自GE高新材料公司(GEAdvancedMaterials)车身板与玻璃装配部门全球项目总监MutsuoAoki先生更是指出,从2007年开始,“市场将发生爆炸性增长”。
这是什么原因?
根据Aoki先生的解释,汽车生产厂商,特别是位于如欧洲和日本等高能源成本地区的厂商,将日益对塑料车身板发生兴趣,因为塑料制车身板只有相应钢材料的一半重,这将有效减轻汽车重量,节省燃油。
而且,在欧洲,由于对汽车前卫式样的需求再加上行人安全立法的出台,塑料材料将更具优势,这是由于塑料给了设计者更多的设计自由,而且在发生汽车碰撞时,塑料也比钢材更具安全性。
塑料供应商期望在未来几年中塑材能在挡泥板市场中出现火爆。
但是,宝马公司并没有为此等待,他在其新型宝马6系列车型中并未曾使用GE高新材料公司的先进材料-NorylGTXresin。
而在北美,除了燃油价格较低和车型式样保守以外,还有另外一些因素阻碍了塑料应用。
其中最大的影响因素就是日趋小型化的生产运作以及日益扩大的车辆区别。
塑料供应商承认在高年产量的情况下,无法与钢材供应商竞争,这是由于大量塑料模具的高成本以及注塑模成型的高循环周期造成了单件成本高于压铸钢件。
但是,当年产量在8万件以下时,注塑成型塑料车身板的成本仍然低于大型级进冲压模的投资成本。
由于具备该类年产量的汽车制造厂商数目不断增多,对于塑料车身板的需求也日益增加。
当然,事实是,在美国不曾影响到塑料应用的钢材和汽油价格目前也在不断上升,因此汽车制造商也在其设计的新车型达到量产之前试图准确预测这些商品在未来几年的价格走向。
耐高温
对于塑料供应商来说,另一个令人乐观的原因是塑料材料的技术发展已大大引起了汽车制造商的兴趣。
多年来,塑料车身板的最大致命缺点(阿基里斯的脚踵)就是其无法承受汽车喷漆炉的高温而发生变形。
土星车解决这个问题的办法是,在进行总成装配前,将塑料车身板附着于立体模型架,然后进行低温电子喷涂工艺,但问题是,这项所谓“在线”工艺需要额外的空间和设备,并要在汽车制造厂中进行空间设计,这对于某些汽车制造商来说,并不愿意去做。
另一个解决办法则是,在室内或供应商处进行离线喷涂,但是这个方法有点冒险,这是因为可能存在颜色吻合度的差异问题。
拜耳聚合物公司车身外饰件分管经理DavidLoren先生称:
“整车制造商曾说过,‘要么给我们在线喷漆的方法,否则什么也别给。
’”现在,塑料供应商终于完成了这个目标,研制出了能承受在线喷漆所必需的200摄氏度高温环境的各种塑料材料。
能制造这类材料的公司有:
罗地亚工程塑料公司(RhodiaEngineeringPlastics)、拜耳聚合物公司(BayerPolymers)和GE高新材料公司(GEAdvancedMaterials)。
罗地亚工程塑料公司会计经理GaryKachin先生声称:
“在线喷漆能力能重振塑料车身板市场。
”
抗伸缩
塑料供应商另一个较少成功克服的难题是塑料车身板在极端温度中的伸缩问题。
塑料具有比钢更高的线性热膨胀系数(CLTE),因而需要更多的伸缩空间。
这就需要更宽的车身板间隙,而大多数汽车制造商出于精密配合的质量考虑并不希望如此。
这个问题理论上可以通过将挡泥板和车身板坚固固定于车门一侧并允许其向另一方向单向伸缩来得以改善。
但是,其实并不理想,因为车门是必须能双向伸缩的,所以匹配性并不佳。
因此,塑料需要在其配方中改变混合配比和增加矿物填充剂来减少其线性热膨胀系数,但是至今为止,仍然无法赶上钢材,也没有人相信能赶上。
GE高新材料公司的Aoki先生称,可以通过智能的设计弥补热膨胀系数上的差距,他指出他所在的公司正在拓展智能塑料车身板调试设计工作。
但是就如同土星一样,智能汽车的设计从头开始就以塑料为应用材料,但是汽车制造商并不愿意颠覆其已成熟的设计工艺来包容如聚合物车门这样的奇想。
事实上,塑料材料之所以重新走红挡泥板和车身板市场,主要的原因是可以取消一些特殊的处理工序。
至于横向车身板件,例如发动机罩、车顶板和车层盖等,在可以预见的未来将仍然由钢材主导市场。
这些大型板件需要很高的刚性,很小的变形度,而且能承受高温。
这些并不是热塑力所能达到的性能。
拜尔公司的Loren先生称,一些热塑材料,例如SMC,正在“慢慢开始涉入市场”。
但是,很明显,没有人认为这在短期内会占据很大的市场份额。
因此,回到我们文章最初关于塑料车身板的发展前途的问题,答案是:
有前途但是前途有限。
还记得通用土星商务车由于安装了塑料车身板,而显示出的侧边安全反弹性能么?
很好的主意,不是么?
但是显然,并没有被广泛普及。
现在的问题是:
该技术会否发展下去?
宝马汽车致力于塑料应用
邓美宝
在汽车讲求轻量化的时候,塑料在这领域找到它的用武之地。
无论是车身、内饰件以及外饰件等地方,都可以找到不同种类的塑料应用。
作为全球最大的汽车制造商之一,宝马(BMW)也因应潮流所趋,使用了大量的塑料。
宝马M3CSL汽车
宝马汽车在德国慕尼黑设有2家工厂,分别位于Landshut及Dingolfing,两厂共有员工超过26,000名,负责零部件制作、车款开发及组装工序,用于各款宝马汽车、摩托车以至一级方程式赛车。
Landshut工厂生产合金、塑料外饰件及内饰件,以及汽车传动轴和备用发动机;Dingolfing则以组装为主,特色之处是其组装线灵活性高,一条组装线可装配4款不同型号的宝马汽车。
公司运作性能及材料开发总监RudolfStauber博士指出,现时轿车对减重的要求越来越高,所以有必要多采用塑料或轻金属来取替以往的铁制部件。
以宝马7系为例,其总重量为1935千克,塑料部份占了14.5%。
虽然这个数字可能还不太高,但Stauber博士预测,2005年聚合物及弹性体在汽车的使用将超过20%。
除了减轻汽车的重量外,Stauber博士还指出了几项未来汽车的发展重点:
改善材料与环境的兼容性、提高司机及乘客的安全、提升实用价值,以及使用更多纳米技术。
宝马汽车现有使用的塑料大致包括热塑性塑料、热固性塑料、弹性体及热塑性弹性体等。
如,与厚钢板制成的同类部件相比,革新性热塑性塑料车身侧板重量更轻,两块前侧板可降低每车重量大约4公斤。
这一设计理念可进一步增强宝马6系车型的行驶动力性能。
另一重要的优点是,采用塑料部件,宝马设计师可继续确保宝马6系Coupe和敞篷车型侧板从头至尾的优美线条。
如果采用传统钢结构,不可能以同样方式将侧面装饰件整合于侧板内。
而且,热塑性塑料作为一种可逆向成型的材料,与钢质材料相比,在一些碰撞中如停车时可能造成的轻微碰撞不会造成严重影响。
碳纤维增强塑料应用
宝马塑料应用的一个重点发展项目是重量轻的复合材料—碳纤维增强塑料(CFP)。
宝马BMWFW25单壳式一级方程式赛车就是利用这种超强的轻质材料制成。
该材料的特点是:
1.CFP可大幅度减轻汽车重量,特别适合制作车体部件。
现代汽车中,车体占整车重量的15~20%,采用CFP塑料制成车体部件,其重量比铝材和钢材分别轻30%和50%以上。
即,这一先进材料可减轻整车重量达10%。
2.除了大幅度减轻整车重量之外,CFP塑料车体部件的最大优势在于其在碰撞时表现出优异的强度和刚度。
碳纤维厚度大约为0.007毫米,受力主要集中在纤维本身的定向流方向。
因此,可选择合理的排列,将纤维彼此层叠构建,从而优化CFP塑料的特色功能和特性,将其调整到预期的强度和负载条件。
3.CFP塑料的另一优势是可制成高度整合的超大型车体部件,这些部件如果用铝材或钢板制成,制作过程十分复杂。
这样,为车体设计和建造等方面提供了巨大优势,固定和支承等功能可直接整合于部件本体之中。
即使复杂的结构件或整车模块,均可用同一模具一体化制作,从而减少车体所需部件的数量。
通过Landshut厂CFP塑料专家、宝马研究革新中心专家和宝马公司汽车工程师的密切合作而开发和设计,宝马BMWM3CSL型汽车的车顶充分体现了采用轻质CFP增强车体结构的优势。
为了保证部件所需的稳定性之外,考虑材料的光洁度和外观,还采用了最佳的生产流程,以利用透明层漆面展现CFP材料的组织结构。
BMWM3CSL型汽车车顶在Landshut厂分三个生产阶段制成。
第一阶段中,将5层专用碳纤维层叠放置进行预成型。
这一阶段的重要要求,同时也是这一过程的一项重大革新,是确保碳纤维妥善排列,准确到位,具备合理的结构,提供车顶所需的稳定性和外观。
第二阶段是树脂压铸(RTM)注射工艺,将已预成型的多层碳纤维垫放入1,800吨压机,将透明型环氧树脂注射到材料之中。
然后,车顶在高温模具中硬化,最后,由机械手从模具中拆除,漆上透明漆。
这一新的生产流程在全球属首次系列化应用,它体现了两个特点:
首先,由于生产流程高度自动化,车顶制造所需的时间至少缩短了1/5。
其次,与钢质车顶相比,宝马M3CSL型汽车的车顶重量减轻了50%或6公斤。
仿真软件的应用
虚拟现实技术是设计中的重点技术,通过三维(3D)演示,使计算结果“有形化”,从而使整个开发队伍得到工作和结果的确实概念。
在研制车身蒙皮革新部件的过程中,宝马采用了最先进的仿真法。
如,在将塑料灌注于注射成型的车身侧板模具时,充分考虑了各种高温和机械因素,始终采用计算机辅助仿真程序。
由此,宝马公司塑料技术专家优化了各部件的功能特色和品质。
侧板注射成型模具
左右侧板采用热塑性材料通过注射成型工艺制成。
这一工艺中所用的注射成型模具,充分考虑了各个搭接点和工段,当然,也考虑了部件的复杂设计。
因此,这是当今汽车制造业中最复杂的模具。
侧板的特定外形和设计,要求采用至少9块滑动件,以形成水管、保险杠连接件、车门弯曲部分和轮罩法兰。
当中的挑战是,热塑性塑料要求严格控制模具内温度,连同滑动件一起,必须能在120℃高温下顺利移动。
另一要求是,必须确保宝马汽车保持高标准表面质量,不得留下模具或滑动件压印。
为了达到上述标准,宝马公司塑料技术专家自行开发了这一模具及其配套理念。
结果,开发出了一套三压板式模具,其中,第三压板作为专用刮板机架。
这一模具用于注射成型机上,能产生3200吨的闭模压力。
材料的总体收缩率为1.7%,模具内收缩率大约为1%。
清楚显示了极高的稳定力。
为防止滑动件在注射过程中移动,异型滑块必须精确设置和调整,公差在0.02~0.03毫米范围内。
注射成型之后,5轴式机械手将部件拆除,模具及围绕工件整个周边的搭接件不会对部件造成任何损伤。
然后,将注塑件从其它链段中切下,放置于冷却计上。
在下一工序中,一套全自动机械手将增强件由里向外粘贴在侧板内。
粘贴之前进