甲醇工艺.docx
《甲醇工艺.docx》由会员分享,可在线阅读,更多相关《甲醇工艺.docx(69页珍藏版)》请在冰豆网上搜索。
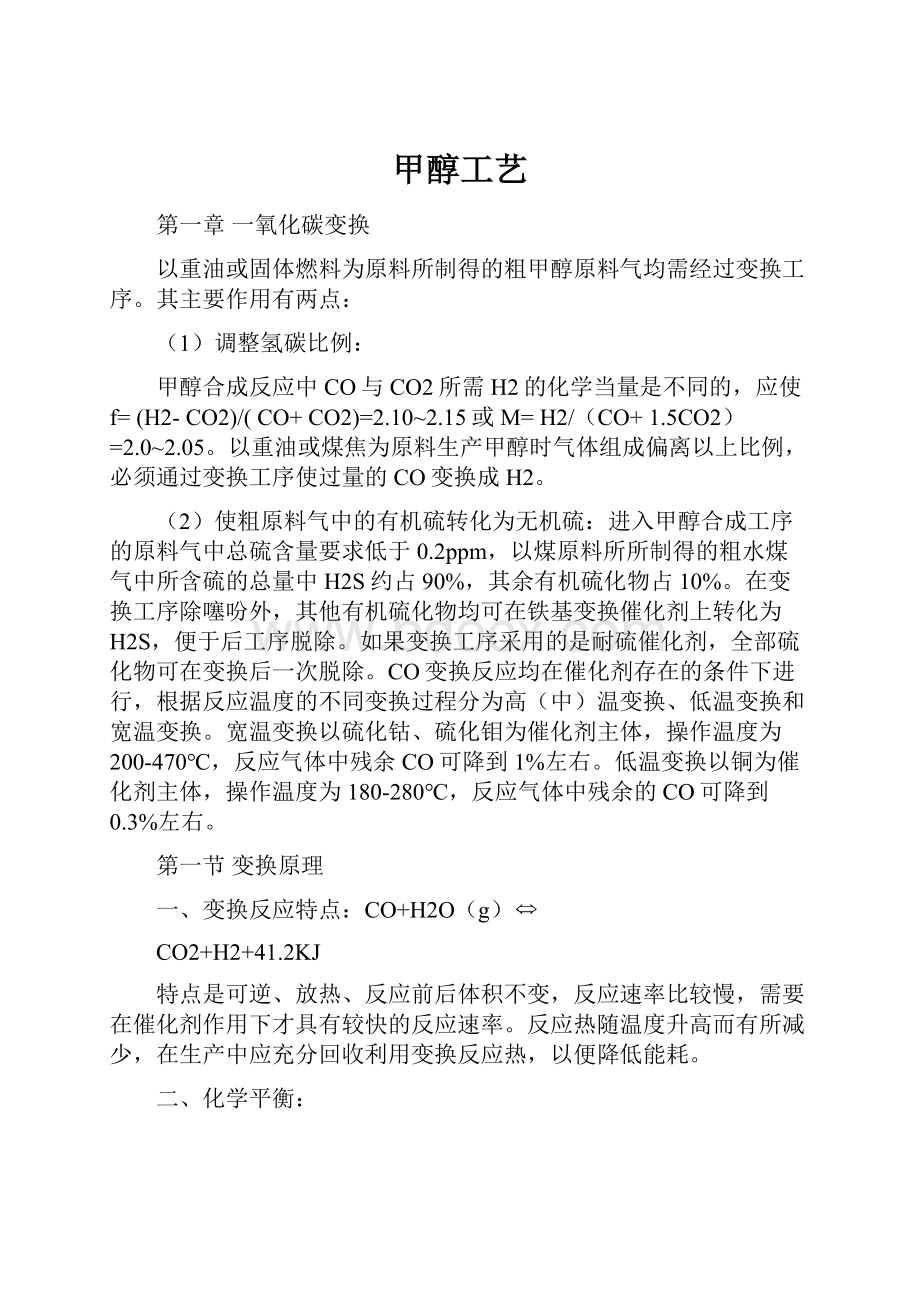
甲醇工艺
第一章一氧化碳变换
以重油或固体燃料为原料所制得的粗甲醇原料气均需经过变换工序。
其主要作用有两点:
(1)调整氢碳比例:
甲醇合成反应中CO与CO2所需H2的化学当量是不同的,应使f=(H2-CO2)/(CO+CO2)=2.10~2.15或M=H2/(CO+1.5CO2)=2.0~2.05。
以重油或煤焦为原料生产甲醇时气体组成偏离以上比例,必须通过变换工序使过量的CO变换成H2。
(2)使粗原料气中的有机硫转化为无机硫:
进入甲醇合成工序的原料气中总硫含量要求低于0.2ppm,以煤原料所所制得的粗水煤气中所含硫的总量中H2S约占90%,其余有机硫化物占10%。
在变换工序除噻吩外,其他有机硫化物均可在铁基变换催化剂上转化为H2S,便于后工序脱除。
如果变换工序采用的是耐硫催化剂,全部硫化物可在变换后一次脱除。
CO变换反应均在催化剂存在的条件下进行,根据反应温度的不同变换过程分为高(中)温变换、低温变换和宽温变换。
宽温变换以硫化钴、硫化钼为催化剂主体,操作温度为200-470℃,反应气体中残余CO可降到1%左右。
低温变换以铜为催化剂主体,操作温度为180-280℃,反应气体中残余的CO可降到0.3%左右。
第一节变换原理
一、变换反应特点:
CO+H2O(g)
CO2+H2+41.2KJ
特点是可逆、放热、反应前后体积不变,反应速率比较慢,需要在催化剂作用下才具有较快的反应速率。
反应热随温度升高而有所减少,在生产中应充分回收利用变换反应热,以便降低能耗。
二、化学平衡:
1、lgKp=
—1.782,平衡常数随温度的升高而减小。
2、变换率及其影响因素:
变换率表示变换反应进行的程度。
其定义是:
变换反应已转化的CO与变换前CO量之比。
在一定条件下当变换反应达到平衡时其变换率为平衡变换率,它是在该条件下变换率的最大值,体现了变换反应进行的最大限度。
实际生产中由于反应不可能达到平衡,实际变换率总是小于平衡变换率,需控制适宜的生产条件,使实际变换率尽可能接近平衡变换率。
影响平衡变换率的因素:
温度、压力、汽气比。
若要得到较高的变换率,应选择较低的操作温度。
由于变换反应是等摩尔反应,所以压力对变换反应化学平衡没有明显的影响。
实际生产中用汽气比表示水蒸汽用量,汽气比指入变换炉水蒸汽与干原料气的体积之比。
生产中从节能角度考虑,在确保CO变换率的前提下选择低的汽气比并在低温下变换以减少蒸汽消耗量。
三、变换反应速率:
CO变换反应属于气固相催化反应,若用[K]表示催化剂,变换过程表示如下:
[K]+H2O(g)=[K]O+H2
[K]O+CO=[K]+CO2
而第二步CO的氧化过程比第一步H2O(g)分子的吸附过程慢,是该反应的控制步骤。
影响反应速率的因素:
温度和压力
随着反应温度的升高,反应速率从上升到下降出现一个最大值,在气体组成和催化剂一定的情况下对应最大反应速率时的温度称为该条件下最佳温度或最适宜温度,而对应同一变换率的最适宜温度总是比平衡温度低几十度。
提高压力反应物体积缩小,单位体积中反应物分子数增多,反应物分子被催化剂吸附速率增大,反应物分子与被催化剂吸附原子碰撞的机会增多,加快反应速率。
第二节变换催化剂
低变催化剂属于经济型催化剂,一般用Cu-Zn-Al系催化剂,以采用氨络合物分解生产的催化剂性能较好,一般用小颗粒,还原后体积收缩率应小于10%,一般在5~6%为好。
宽温耐硫变换催化剂:
比如全“低变”流程,其优点有催化剂寿命长、汽耗低、有机硫转化率高达98%以上、设备材质要求低使用寿命长。
第三节宽温(耐硫)变换催化剂
通常应用的是Co-Mo系催化剂,既耐硫又有很宽的活性温区,一般在160-500℃之间。
一、Co-Mo系催化剂及其作用:
目前工业上用的Co-Mo系催化剂活性组分为CoO、MoO3,使用前需将它们硫化成CoS和MoS2。
我公司变换工序所用的催化剂是K8-11(宽变)和QCS-04(低变)。
其中K8-11组成为:
CoO:
3.6%;MoO3:
9.5%;Al2O3:
52.9%;助催化剂:
MgO22.4%;SiO211%。
Al2O3是结构型载体,加入碱金属可提高催化剂活性,起促进作用。
该催化剂有突出的耐硫和耐其他毒害的性能,可耐原料气中总硫到每Nm3几十克。
少量的NH3、HCN、C6H6等对Co-Mo系催化剂活性均无影响,且其强度好、遇水不粉化经硫化后强度还可以提高50%以上。
Co-Mo系催化剂寿命长,一般可用5年左右,有的可用到10年以上,并可再硫化以延长其寿命。
它可以用高空速、长寿命的特点折算每年耗用的费用反比其他催化剂费用低。
二、Co-Mo系催化剂及反硫化:
1、硫化
Co-Mo系宽温变换催化剂使用前呈氧化态,需经过硫化后才能有很好的催化活性。
硫化可用未脱硫的工艺气进行,工业上一般用干半水煤气中添加CS2为硫化剂。
硫化是一个放热过程,主要反应有:
CS2+4H2=2H2S+CH4+Q
MoO3+2H2S+H2=MoS2+3H2O+Q
CoO+H2S=CoS+H2O+Q
CoS+H2O=CoO+H2S+Q
加入CS2以低变炉的进口温度180-200℃为宜,并在床层低于250℃时再升温至硫化完全。
一般CS2用量按1m3催化剂150kg准备。
硫化在常压下进行,硫化过程需要20-50h。
硫化终点可由变换炉出口气体中总硫含量与入口处总硫含量接近时即可认为硫化结束。
采用快速硫化法可缩短硫化时间一半以上,其特点是在高空速下(300-500h-1)采用高浓度CS2(0.5-2%或20-70g/Nm3)并利用其氢解反应释放出的大量反应热在适当高温下(约425℃)进行强化硫化,硫化后的催化剂活性很好,使用时间较长。
2、反硫化
在一定的反应温度、蒸汽量、H2S浓度下会导致催化剂失活,即反硫化:
MoS2+2H2O=MoO2+2H2S-Q,在一定温度与汽气比下,要求有一定的H2S量,当H2S含量高于相应的数值时,就不会发生反硫化。
此浓度又称为最低H2S含量。
在催化剂使用后期要特别注意反硫化条件形成,一般在进口温度较低的情况下可防止反硫化反应的发生。
三、宽温变换催化剂的使用注意事项:
1、温度、汽气比
宽温变换催化剂进口温度是主要控制指标,在确保变换炉出口CO含量工艺指标范围内,并超过露点以上25℃的前提下,选择低的进口温度,一般在180-210℃,热点温度在210-240℃。
床层提温须遵循“慢提、少提”的原则,正常情况下,每年提温幅度不得大于5~10℃。
当汽气比小于1时,对变换率影响甚为敏感。
但宽温变换催化剂在低汽气比下仍有高的变换率。
为了防止反硫化发生不要提高操作温度与汽气比,稳定操作条件使脱硫后维持H2S浓度在30-60mg/Nm3。
2、在全低变流程中要特别注意原料气的质量,水质的净化,防止油水氯带入变换炉中。
全低变热点温度可高达约350℃,故H2S含量宜保持在0.5mg/Nm3需相应的调整原料气总硫含量并加强后工序脱硫。
第四节工艺条件选择
一、压力:
加压变换可加快反应速度和提高催化剂生产能力,从而可采用较大空速提高生产强度。
设备体积小,布置紧凑,投资较少。
湿变换气中水蒸汽冷凝温度高,有利于热能的回收利用。
但提高压力会使系统冷凝液酸度增大,设备腐蚀加重,如果变换过程所需蒸汽全部由外界加入新鲜蒸汽,加压变换会加大高压蒸汽负荷,减少蒸汽作功能力。
目前大中型氨厂变换压力一般为1.2-3.0MpaG。
二、温度:
(1)操作温度必须控制在催化剂的活性温度范围内。
反应开始时温度应高于催化剂活性温度20℃左右,且反应中严防超温。
一般反应开始温度为320-380℃,最高使用温度为530-550℃。
(2)使整个变换过程尽可能在接近最适宜温度的条件下进行。
由于最适宜温度随变换率升高而下降。
因此需要随着反应的进行及时移出反应热从而降低反应温度。
工业上采用多段床层间接冷却工艺,用原料气或饱和蒸汽进行段间换热,移走反应热。
段数越多,变换反应过程越接近最适宜温度曲线,但流程亦更为复杂。
三、蒸汽比例:
水蒸汽比例一般指蒸汽与原料气(或其中CO)的摩尔比。
增加蒸汽用量,可提高CO变换率,加快反应速度,防止副反应发生;但过量蒸汽不但经济上不合理,且催化剂床层阻力增加,CO停留时间加长,余热回收负荷增大。
四、最终变换率:
从制H2和气体净化角度考虑都需提高最终变换率,对以生产甲醇的工厂而言最终只要求H2/CO≈2.5即可,根据变换气中H2和CO体积百分含量求出最终变换率,如果高于最终变换率反而要消耗过多的蒸汽和催化剂而且也没有这个必要。
第五节工艺流程及主要设备
一、生产流程简述:
来自煤气化装置温度为199℃压力3.7MpaG的粗合成气,首先在粗煤气分离器S15101中分离夹带的水分,然后进粗煤气过滤器S15102A/B(一开一备),其中装有保护剂,可以将煤气中夹带的粉尘对催化剂有毒害的物质过滤掉。
过滤后的煤气分为三股:
一股流量约为总流量的25%与出低压废锅E15102的变换气混合以调节变换气中的氢碳比例;一股流量约为总流量的30%经过粗合成气换热器E15101与变换气换热到260℃进蒸汽混合器S15103与来自煤气化的48bar饱和蒸汽混合后进第一变换炉R15101进行变换反应。
出第一变换炉R15101的变换气温度为448℃,CO含量:
12.1%(mol,干基)。
出第一变换炉的变换气通过中压蒸汽过热器E15107将来自煤气化的饱和蒸汽过热到400℃,变换气则被冷却到389℃,然后经过粗合成气换热器E15101与进变换的煤气换热后,变换被冷却到342℃与另外一股流量约为总流量的45%的煤气混合进第二变换炉R15102继续进行变换反应,出第二变换炉R15102的变换气温度为436℃、CO含量:
8.5%(mol,干基)。
出第二变换炉R15102的变换气通过低压废锅E15102副产6.5bar饱和蒸汽约21.5t/h。
然后依次进入第二除盐水加热器E15103和第一除盐水加热器E15104回收热量后再在变换气水冷器E15105中被冷到40℃后去酸性气脱除工序。
来自第一变换气分离器S15106、第二变换气分离器S15107和第三变换气分离器S15108的工艺冷凝液减压到约34bar后进冷凝液闪蒸槽S15105,出冷凝液闪蒸槽的闪蒸汽去火炬,出冷凝液闪蒸槽的工艺冷凝液经冷凝液泵P15101A/B加压到45bar后送到煤气化装置。
催化剂升温和硫化采用氮气循环,宽变催化剂和低变催化剂分别升温和硫化。
流程示意图如下:
二、主要设备选型及说明:
1、第一变换炉(R15101):
选用热壁炉,1台,立式,炉体直径φ2000,高度4100
催化剂装填量(K8-11):
7.5m3
设计温度:
485℃
设计压力:
4.1MPaG
2、第二变换炉(R15102):
选用热壁炉,1台,立式,炉体直径φ3000高度8880
催化剂装填量(QCS-04):
43m3
设计温度:
475℃
设计压力:
4.1MpaG
3、变换气水洗塔(C15101):
1台,板式塔
直径φ2600高度6650
设计温度:
50℃
设计压力:
4.1MpaG
4、低压废锅(E15102):
1台,管壳式
直径φ1400/2400高度7930换热面积532.6㎡管内径×长度:
38.4×610
设计负荷:
11.78MW
设计温度:
180℃(壳)/420℃(管)
设计压力:
1(壳)/4.1(管)MpaG
5、蒸汽混合器(S15103)
1台,立式,
直径φ2000高度3900全容积14.5m3
设计温度:
320℃
设计压力:
4.1MpaG
6、冷凝液闪蒸槽(S15105)
1台,卧式
直径φ2400长度6000全容积31.2m3
设计温度:
150℃
设计压力:
4.1MpaG
7、电加热器(Z15101)
1台,直径φ1500高度7000
设计温度:
450℃
设计压力:
0.6MpaG
第二章酸性气体脱除(低温甲醇洗)
低温甲醇洗是50年代初德国林德公司和鲁奇公司联合开发的一种气体净化工艺。
该工艺以冷甲醇为吸收溶剂,利用甲醇在低温下对酸性气体溶解度极大的优良特性,脱除原料气中的酸性气体。
该工艺气体净化度高,选择性好,气体的脱硫和脱碳可在同一个塔内分段、选择性地进行。
低温甲醇洗工艺技术成熟,在工业上有着很好的应用业绩,被广泛应用于国内外合成氨、合成甲醇和其他羰基合成、城市煤气、工业制氢和天然气脱硫等气体净化装置中。
在国内以煤、渣油为原料建成的大型合成氨装置中也大都采用这一技术。
低温甲醇洗脱硫、脱碳技术特点如下:
(a)溶剂在低温下对CO2、H2S、COS等酸性气体吸收能力极强,溶液循环量小,功耗少。
(b)溶剂不氧化、不降解,有很好的化学和热稳定性。
(c)净化气质量好,净化度高,CO2<20ppm,H2S<0.1ppm。
(d)溶剂不起泡。
(e)具有选择性吸收H2S、COS和CO2的特性,可分开脱除和再生。
(f)溶剂廉价易得,但甲醇有毒,对操作和维修要求严格。
(g)该工艺技术成熟,目前全世界约有87套大中型工业化装置。
该工艺需从国外引进。
由于操作温度低,设备、管道需低温材料,且有部分设备需国外引进,所以投资较高。
(h)低温甲醇洗溶剂在低温(-50℃)下吸收,含硫酸气采用热再生,回收CO2采用降压解吸,脱碳采用气提再生,热耗很低。
虽然低温甲醇洗工艺投资较高,但与其它脱硫、脱碳工艺相比具有电耗低、蒸汽消耗低,溶剂价格便宜,操作费用低等优点。
特别是脱硫的净化度高,对甲醇生产十分有利,本工序采用低温甲醇洗工艺脱除酸性气体。
一、低温甲醇洗工艺原理
拉乌尔定律与亨利定律:
溶液中溶剂的蒸汽压不仅与溶液的性质有关,而且还与溶液中所溶解组分的浓度有关。
拉乌尔根据许多数据,发现稀溶液中溶剂的蒸汽压Pl与其液相中的摩尔分数Xl之间存在着下述关系:
Pl=Pl0Xl
Pl°——同一温度下纯溶剂的蒸汽压
Pl——溶液中溶剂的蒸汽压
Xl——溶液中溶剂的摩尔分数
溶液中溶剂的蒸汽压等于纯溶剂的蒸汽压与其摩尔分数的乘积,这就是拉乌尔定律。
设溶质的摩尔分数不X2,由于X1=1-X2,所以上式可改为:
Pl=Pl0(1-X2)
或者说X2=(Pl0-Pl)/Pl0
即溶剂蒸汽压下降的分数等于溶质的摩尔分数。
拉乌尔定律只适用于稀溶液或浓度很低的溶液。
由性质很相似的组份所构成的溶液,在所有浓度范围内,都符合拉乌尔定律。
亨利在研究气体在液体中溶解的规律时发现:
在一定温度和平衡状态下,一种气体在溶液里的溶解度和该气体的平衡分压成正比:
P2=KX2
X2——平衡时气体在液体中的摩尔分数
P2——平衡时液面上该气体的分压
K——常数(通过实验测定),与温度、总压、气体和溶剂的性质有关。
图中实线所示为非理想溶液中组份i的浓度Xi与蒸汽压Pi的关系。
当浓度很稀(Xi→0)或浓度很大(Xi→1)时,蒸汽压Pi和浓度Xi之间都呈现出线性关系,即非理想溶液的稀溶液段可以用亨利定律描述溶液中溶质的行为,而非理想溶液的浓溶液段则可用拉乌尔定律描述溶剂的行为。
一般来说,亨利系数K不等于该温度下溶质的蒸汽压。
在稀溶液中溶质若服从亨利定律,则溶剂必然服从拉乌尔定律。
亨利定律是化工吸收过程的依据。
吸收分离就是利用溶剂对气体混合物中各组分溶解度的不同选择性地把溶解度大的气体吸收,达到从气体混合物中除去或进一步回收这种气体的目的。
从上式可看出当溶质和溶剂一定时,在一定温度下,K为定值,气体的分压越大,则其在溶液中的溶解度就越大,所以增加气体压力有利于吸收。
从上式还可以看出,若在相同的气体分压下进行比较,K值越小,则溶解度越大,所以亨利常数K值的大小可以作为选择吸收剂的一个依据。
在应用亨利定律时须注意:
□亨利定律只适用于稀溶液。
当温度较高、压力较低时,应用亨利定律可以得到较为正确的结果。
□对于混合气体,当压力不大时,亨利定律对每一种气体都能分别适用。
□溶质在气相和溶液中的分子状态相同时亨利定律才适用。
低温甲醇洗在合成氨、甲醇合成生产净化工艺中的应用是以拉乌尔定律和亨利定律为理论依据的。
这两个定律只适用于稀溶液、压力不高的情况。
因此低温甲醇洗需采用经修正的亨利定律。
修正后的亨利定律主要考虑以下几点:
□修正了溶液浓度系数λ和平衡常数K的关系。
□由于范德华力的存在会引起溶质在溶剂中溶解度的下降。
□溶质溶于溶剂中后,也象溶剂一样会吸收其他组分。
低温甲醇洗吸收酸性气体以及溶液再生,解吸回收有用气体的理论基础就是各种气体在甲醇中的溶解度不同。
溶解度系数λ指气体分压为绝对大气压时的溶解度。
分压增加时,溶解度系数λ增大,温度较高时,分压对λ的影响不如温度低时显著。
根据气体在甲醇中溶解度的定义要从原料气中完全脱出某种气体组分,所需要的甲醇的最低流量如下式所示:
Smin=V/(Pλ)
Smin:
从原料气中完全脱除某一组份所需要的甲醇最低流量
V:
气体的流量
P:
原料气的总压
λ:
溶解气体组分的溶解度系数
由此可知原料气流量一定时,吸收气体组份所需的吸收剂流量与压力以及该组份的溶解度成反比。
所以吸收操作压力越高、原料气中待吸收的组份浓度越大,对吸收越有利。
从下图中可以看出,H2S、COS、CO2等酸性气体在低温甲醇中的溶解度明显增大,而对合成甲醇有用的气体如H2、CO及CH4等在甲醇中的溶解度随温度的下降增加很少,其中H2在甲醇中溶解度随温度降低反而减少。
从上图中可以看出低温下H2S的溶解度差不多比CO2大6倍,这样就可以选择性地从原料气中分别吸收CO2和H2S,同时通过解吸再生又可以分别加以回收。
又如低温下H2S、COS及CO2在甲醇中的溶解度与CO及H2相比至少要大100倍,而比CH4大50倍。
因此如果低温甲醇洗工艺是按脱除CO2进行设计的,则所有溶解度与CO2相当或比CO2溶解度更大的气体如C2H2、COS、H2S、NH3等及其他硫化物都将一起被脱除而原料气中有用的气体损失很少。
并且低温下甲醇的蒸汽压很小,这样溶剂损失也不大。
一般低温甲醇洗的操作温度为-30℃~-60℃。
低温下CO2在甲醇中的摩尔分率XCO2可按下式计算:
XCO2=0.425PCO2/PCO2°
因此CO2在甲醇中的溶解度SCO2(L/kg)可表示为:
SCO2=695.7PCO2/(2.35PCO2°—PCO2)
PCO2°:
同温度下液态CO2的蒸汽分压,KPa
PCO2:
CO2平衡分压,KPa
H2S在甲醇中的溶解度比CO2更大,可表示为:
SH2S=692PH2S/(1.9PH2S°—PH2S)(L/kg)
PH2S:
H2S平衡分压,KPa
PH2S°:
液态H2S的蒸汽分压,KPa。
可由下式确定:
PH2S°=6.583—973.5/T
当有CO2同时存在时,H2S的溶解度要减少,可表示为:
SH2S′=SH2S/(1+C×SCO22.4)
SCO2:
CO2在甲醇中的溶解度,L/Kg;
C:
与温度有关的常数,-25.6℃:
8×10-4;-50℃:
1.5×10-5;-78.5℃:
4×10-7;
COS在甲醇中的溶解度
COS在甲醇中的溶解度也遵从亨利定律,随着压力的增高而增加。
吸收气体中的CO2所需要的甲醇量足够完全地除净气体中的有机硫化物,如果只除去气体中的硫化物,那么应该考虑气体中COS的溶解度,因为COS是溶解度最低的硫化物组分。
H2、N2、CH4在甲醇中的溶解度:
由于变换气中H2的含量很高,在高压低温下脱除酸性气体时造成H2的损失仍是可观的。
各种气体在甲醇中的溶解热:
气体
H2S
CO2
COS
CS2
H2
CH4
溶解热
19.264
16.946
17.364
27.614
-3.826
3.349
H2S和CO2在甲醇中的溶解热不大,但其溶解度较大,因而仍有明显的温升,为了保持一定的吸收效率塔中需设置冷冻取走吸收放出的热量。
低温甲醇洗是一种典型的物理吸收过程。
物理吸收和化学吸收的根本不同点在于吸收剂与气体溶质分子间的作用力不同。
物理吸收中,各分子间的作用力为范德华力;而化学吸收中为化学键力。
这二者的区别构成它们在吸收平衡曲线、吸收热效应、温度对吸收的影响、吸收选择性以及溶液再生等方面的不同。
物理吸收中,气液关系开始时符合亨利定律,溶液中被吸收组分的含量基本上与其在气相中的分压成正比。
在化学吸收中,当溶液的活性组分与被吸收组分间的反应达到平衡以后,被吸收组分在溶液中的进一步溶解只能靠物理吸收。
物理吸收中,吸收剂的吸收容量随酸性组分分压的提高而增加,溶液循环量与原料气量及操作条件有关,操作压力提高,温度降低,溶液循环量减少;在化学吸收中,吸收剂的吸收容量与吸收剂中活性组分的含量有关,因此,在化学吸收中,溶液循环量与待脱除的酸性组分的量成正比,即与气体中酸性组分的含量关系很大,但与压力基本无关。
低温甲醇洗中,H2S、COS、CO2等酸性气体的吸收,吸收后溶液的再生以及CO、H2等溶解度低的有用气体的解吸曲线,其基础就是各种气体在甲醇中有不同的溶解度。
低温下,甲醇对酸性气体的吸收是很有利的。
当温度从20℃降到-40℃时,CO2的溶解度约增加6倍,吸收剂的用量也大约可减少6倍。
低温下,例如-40℃至-50℃时,H2S的溶解度又差不多比CO2大6倍,这样就有可能选择性地从原料气中脱除H2S,而在溶液再生时先解吸回收CO2。
低温下,H2S、COS、CO2在甲醇中的溶解度与CO、H2相比,至少要大100倍,与CH4相比,约大50倍。
因此,如果低温甲醇洗装置是按脱除CO2的要求设计的,则所有溶解度和CO2相当或溶解度比CO2大的气体,例如H2S、COS等以及其他硫化物都能一起脱除,而CO、H2、CH4等有用气体则损失较少。
通常,低温甲醇洗的操作温度为-30℃至-70℃,各种气体在-40℃时的相对溶解度,如下表所示:
-40℃(233K)时各种气体在甲醇中的相对溶解度
气体
气体的溶解度
H2溶解度
气体的溶解度
CO2溶解度
H2S
2540
5.9
COS
1555
3.6
CO2
430
1.0
CH4
12
CO
5
H2
1.0
N2
2.5
当气体中有CO2时,H2S在甲醇中的溶解度约比没有CO2时降低10%至15%。
溶液中CO2含量越高,H2S在甲醇中的溶解度的减少也越显著。
当气体中有H2存在时,CO2在甲醇中的溶解度就会降低。
当甲醇含有水分时,CO2的溶解度也会降低,当甲醇中的水分含量为5%时,CO2在甲醇中的溶解度与无水甲醇相比约降低12%。
下表所示不同温度和压力下CO2在甲醇中的溶解度(cm3CO2/g)℃
不同温度和压力下CO2在甲醇中的溶解度(cm3CO2/g),℃
压力
温度
-26℃
-36℃
-45℃
-60℃
备注
0.101Mpa
17.6
23.7
35.9
68.0
0.203Mpa
36.2
4.9
35.9
159.0
0.304Mpa
55.0
77.4
72.6
321.0
0.405Mpa
77.0
113.0
117.0
960.7
0.507Mpa
106.0
150.0
174.0
0.608Mpa
127.0
201.0
250.0
0.709Mpa
155.0
262.0
362.0
0.331Mpa
192.0
355.0
570
0.912Mpa
223.0
444.0