HDI板工具制作规范新20428.docx
《HDI板工具制作规范新20428.docx》由会员分享,可在线阅读,更多相关《HDI板工具制作规范新20428.docx(32页珍藏版)》请在冰豆网上搜索。
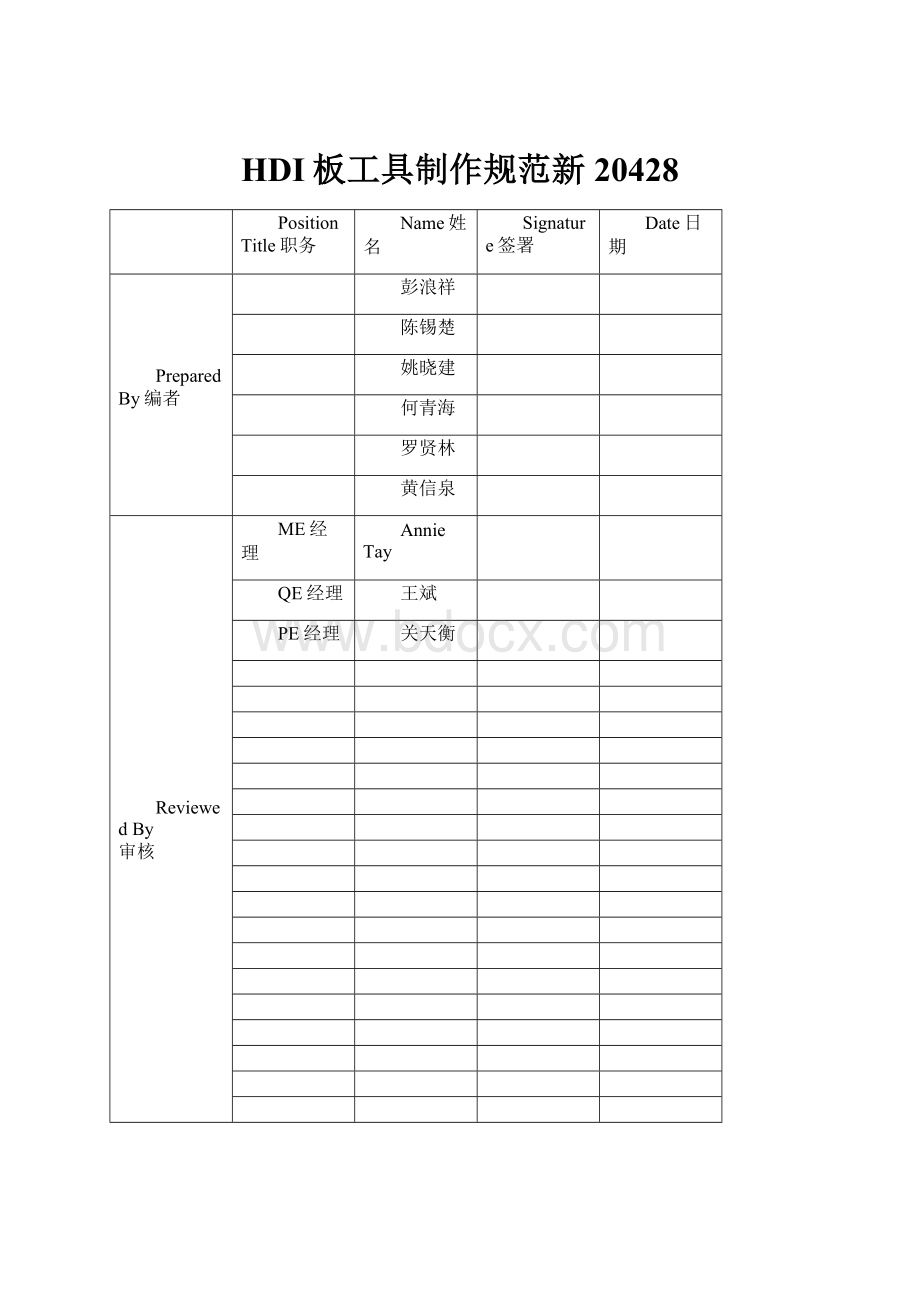
HDI板工具制作规范新20428
PositionTitle职务
Name姓名
Signature签署
Date日期
PreparedBy编者
彭浪祥
陈锡楚
姚晓建
何青海
罗贤林
黄信泉
ReviewedBy
审核
ME经理
AnnieTay
QE经理
王斌
PE经理
关天衡
ApprovedBy
批准
ManagementRepresentative
管理者代表
池俊如
EffectiveDate生效期
Version版本
RevisedBriefDescription修订简述
Revisedby修订者
7.1.2.4二阶HDI板铣边流程
(1)针对H孔介质使用PP的二阶HDI板,需在相应层激光钻孔后增加层压后处理铣边流程,单边铣2.5~3mm;
(2)PE-MI需在流程中设计此流程,从内层芯板开始,需要将板边加大或更改工具孔位置,板边工具孔离芯板板边距离需大于以下公式的计算值:
D=压板次数×(1.27mm或2.54mm)+使用1080介电层的层数×单边铣边宽度(mm)+2mm
7.2.4激光钻孔工序
7.2.4.1激光钻孔对位图形
(1)激光钻孔时根据板边的FiducialMark定位:
a.Mark图形为四个2.0mm通孔;激光层以通孔为中心周围直径10mm范围为全铜;
b.Mark尽量靠近内层图形,孔边距板边大于1mm;
c.FiducialMark设计时需考虑位置防反设计(防板放倒及放反)。
d.此2.0mm的孔由压板后X-Ray钻机钻出,因此内层必须设计X-Ray机识别的钻孔标靶图形(标靶图形设计在最内层即ThinCore层上,其它层对应位置开窗,具体要求参照X-Ray标靶设计方面的指示)。
a.激光钻孔时根据板边的FiducialMark定位,Mark图形为中间铜盘(CopperPad)为1.0mm,外环(Clearance)为3.0mm,如下图。
Mark图形附近无埋孔,保证埋孔离Mark盘边距大于5mm(若埋孔须树脂塞孔,则保证埋孔离Mark盘边距大于2mm,Mark尽量靠近内层图形,盘边距板边大于1mm。
FiducialMark摆放的位置需防反;
b:
一阶HDI板激光钻孔对位Mark设计4组,每个板角一组,分布如下图。
如果CFM采用LW或MW工艺,Mark图形需设计在第二层和第n-1层菲林上,两层的图形需错开摆放,其他菲林相应处做成Clearance;如果CFM采用SLW工艺,则需在CFM菲林设计4组Mark,每个板角一组。
其他菲林相应处无需做成Clearance;
c.二次一阶HDI板激光钻孔对位图形的设计思路同一阶HDI板;
d.二阶HDI板激光钻孔对位Mark:
所有的激光孔(包括次外层和外层HDI孔)根据第3和(n-2)层上设置的FiducialMark定位。
因此,须在第3和(n-2)层菲林上增加激光钻孔对位图形。
以典型的含阶梯式二阶HDI孔8层板为例,FiducialMark位于L3、L6层并相互错开,在L2、L4、L5、L7菲林相对应的位置做成直径为3.0mm的基材(或保证3.0mm范围内无铜)。
L27和L18的largewindow菲林以及外层菲林相对应位置做成直径为3.0mm的间隙;在蚀刻后确保Mark周围3.0mm范围内无铜。
对于填孔式二阶HDI孔的激光钻孔,若次层采用LW或MW方式,L2、L(n-1)层上激光钻孔的FiducialMark设置在L3、L(n-2)层上,外层采用LW或MW方式L1、Ln层上激光钻孔的FiducialMark也设置在L3、L(n-2)层上,但是当外层采用SLW方式,L1、Ln层上激光钻孔的FiducialMark设置在外层CFM菲林上;
(2)激光钻孔备用对位Mark
为防止激光钻孔对位图形异常,激光钻孔无法抓取,特在CFM菲林上设置备用图形。
图形设计为中间基材圈直径为1.0mm,而外层基材圈的间距为0.2mm,线宽为0.1mm,最外围的基材圈直径为3.0mm,次外层菲林上相应位置做铜盘直径为3.4mm,如下图(黑色为铜):
7.2.4.2激光孔对位检查及切片孔图形
(1)图形位置:
激光孔对位检查及切片孔图形用于检查激光钻孔位置与内层盘的准确性。
该图形设计布局在板的四角。
(2)菲林设计:
激光孔对位检查图形(如下图)用于检查激光钻孔位置与内层盘的准确性。
该图形设计布局在板的四角,靠近四角CFM蚀刻后对位精度检查图形旁。
L2和L(n-1)层上激光孔对位检查图形位于L3和L(n-2)层上,并且错开排列设置,其它内层和L2和L(n-1)Largewindow都开窗(48mil)。
在L2和L(n-1)层图形制作时相应位置设计作为L1和Ln层上激光孔对位检查图形,L1和LnLargewindow都开窗(48mil)。
…………………………………………………………………………………………………………………………
7.2.5.机械钻孔工序
7.2.5.1一钻钻孔采用标靶孔(ID孔)定位。
定位孔为5个直径为Φ3.175mm的孔,第1#和2#孔为钻孔定位孔,其中第3#孔为方向孔,4#及5#孔为备用ID孔,其位置分布如图7.2.5-1,ID孔由压板后X-Ray钻机钻出(其中备用孔正常时不用钻出),因此相应位置的内层(所有机械钻孔层以内的所有层上)需要设计X-Ray机识别的对位标靶图形;(譬如1+6+1的板,CS层的机械钻孔用ID孔的X-Ray标靶需要设计在L3/L4/L5/L6层上,外层的机械钻孔用ID孔的X-Ray标靶需要设计在L2/L3/L4/L5/L6/L7层上)
7.2.5.2对于有多次压合的板钻孔时,每次钻孔均需有一套独立的ID孔,且1#孔到两个长边(A与B)的距离均尽量不要大于10.5inch,否则会影响钻机效率;各套ID孔的孔之间距离不可小于5mm;
7.2.5.3二钻钻孔采用板边的二钻定位孔定位;二钻定位孔需要在一钻时设计出,且设计为非镀铜孔;
7.2.5.4在钻双面板(芯板直接钻孔)及盲孔板的内层芯板前,PE应先制作管位程序孔来确定生产板的位置,便于生产部钻出生产板上的定位孔然后利用生产板上定位孔定位,钻出其余孔。
另外对于双面板,由于PIN孔是钻房自己用打PIN机器钻的,因此没有方向孔,PE在钻带设计时需要增加一个方向孔,直接放入钻带中(方向孔的孔心Y方向要距离板边5mm,X方向距离中心1.5”—2.5”),PIN孔的位置设计要求如下图:
7.2.5.6在制作机械钻孔标靶孔程序时,最近的钻孔圆心到标靶孔的圆心间的距离应大于11.25mm;
……………………………………………………………………………………………………………………………
7.3.2CMF工序
7.3.2.1一阶/二次一阶/二阶HDI孔CFM开窗制作要求如下表:
H板类型
层次
H孔焊盘单边Ring
H孔底盘单边Ring
CFM
工艺
开窗尺寸
蚀刻后控制尺寸
流程选择
备注
一阶HDI板
外层
≥3.0
≥4.2
SLW
孔径+3.5mil
(孔径+3.5mil)~(孔径+4.5mil)
SES
≥4.5
3.0≤R<4.2
LW
孔径+6.5mil
(孔径+6.5mil)~(孔径+7.5mil)
SES
3.0≤R<4.5
3.0≤R<4.2
MW
孔径+5.0mil
(孔径+5.0mil)~(孔径+6.0mil)
SES
二次一阶HDI板
外层
≥3.0
≥4.2
SLW
孔径+3.5mil
(孔径+3.5mil)~(孔径+4.5mil)
SES
≥4.5
3.0≤R<4.2
LW
孔径+6.5mil
(孔径+6.5mil)~(孔径+7.5mil)
SES
3.0≤R<4.5
3.0≤R<4.2
MW
孔径+5.0mil
(孔径+5.0mil)~(孔径+6.0mil)
SES
次外层
≥3.0
≥4.2
SLW
孔径+3.5mil
(孔径+3.5mil)~(孔径+4.5mil)
DES
≥4.5
3.0≤R<4.2
LW
孔径+6.5mil
(孔径+6.5mil)~(孔径+7.5mil)
DES
3.0≤R<4.5
3.0≤R<4.2
MW
孔径+5.0mil
(孔径+5.0mil)~(孔径+6.0mil)
DES
两阶HDI板/阶梯式二阶盲孔
次外层
≥4.5
R≥3.0
LW
孔径+6.5mil
(孔径+6.5mil)~(孔径+7.5mil)
DES
3.0≤R<4.5
R≥3.0
MW
孔径+5.0mil
(孔径+5.0mil)~(孔径+6.0mil)
DES
外层
≥4.5
R≥3.0
LW
孔径+6.5mil
(孔径+6.5mil)~(孔径+7.5mil)
SES
3.0≤R<4.5
R≥3.0
MW
孔径+5.0mil
(孔径+5.0mil)~(孔径+6.0mil)
SES
两阶HDI板/填孔式二阶盲孔
次外层
≥4.5
R≥3.0
LW
孔径+6.5mil
(孔径+6.5mil)~(孔径+7.5mil)
DES
3.0≤R<4.5
R≥3.0
MW
孔径+5.0mil
(孔径+5.0mil)~(孔径+6.0mil)
DES
外层
≥4.5
R≥3.0
LW
孔径+6.5mil
(孔径+6.5mil)~(孔径+7.5mil)
SES
3.0≤R<4.5
R≥3.0
MW
孔径+5.0mil
(孔径+5.0mil)~(孔径+6.0mil)
SES
注:
(1).为满足间距要求,单孔单边切盘小于0.5mil时,则按整个焊盘尺寸计。
(2).如果客户要求外层铜厚≥35um的HDI板,基铜采用12um或减到12um,CFM采用SLW工艺,另如果客户要求外层基铜厚为12um,则CFM同样也采用SLW工艺。
7.3.2.2二阶HDI板的HDI孔CFM开窗原则和HDI孔盘尺寸要求
(1)二阶HDI板上若设计有一阶HDI孔,其L12和L23一阶HDI孔的最小孔径为4mil;而L13二阶HDI孔孔径设计必须为8mil。
(2)二阶HDI孔型结构选择原则
二阶HDI孔分为:
L13二阶HDI孔、阶梯式二阶HDI孔和填孔式二阶HDI孔。
阶梯式二阶HDI孔结构:
下层HDI孔为4mil,上层HDI孔为8mil构成的导通叠孔;填孔式二阶HDI孔结构:
下层为4mil并采取电镀铜填平工艺的一阶HDI孔,上层为4mil采取电镀铜填平工艺的一阶HDI孔或普通一阶HDI孔构成的导通叠孔。
通常若客户设计二阶HDI板结构中的二阶HDI孔上层孔径要求<8mil,或客户无孔径要求,但实际布线密度高,无法设计阶梯式二阶HDI孔时,应选择填孔式二阶HDI孔;否则优先考虑选择阶梯式二阶HDI孔及其生产工艺流程。
………………………………………………………………………………………………….
7.3.3激光钻孔工序
7.3.3.1激光介质的设计、使用规则如下:
(1)对激光孔底的铜厚≤Hoz的板,因内层铜薄流胶少介厚偏厚,稍有玻纤突出就会导致药水交换不良,形成单点铜薄甚至空洞,故设计需保证激光孔径≥5mil;
(2)一般情况下不要使用3313和2116(如客户有介电层厚度和阻抗要求,尽量说服客户更改设计),实在无法避免要使用时,激光孔径设计必须≥6mil;
(3)激光介质为1086、1080、1078或106,且设计完成介厚≤70um时,激光孔径可选择3mil,如果设计完成介厚>70um时,激光孔径可选择4mil或以上。
(4).二阶HDI板介质层种类要求:
L23、L(n-1)(n-2)介质层必须使用PP,L12、L(n-1)n介质层推荐使用1086PP、1080PP、1078PP、106PP、RCC70、RCC80。
7.3.3.2激光孔底铜厚设计要求
为防止HDI板因次外层板铜厚不足而导致激光击穿底铜的品质异常问题,现针对不同激光孔径的孔底铜厚要求如下:
对于3-5mil的激光孔,底铜(棕化后)铜厚不能小于12um,对于6-8mil的激光孔,对于内层无需镀铜增加铜厚的生产板,则必须采用1OZ铜箔,且要求确保棕化板的次外层铜厚在14um以上。
7.3.3.3HDI板激光钻孔制作程序
(1)激光钻带制作规范
a.激光钻带必须包括2部分:
对位程序和钻孔程序这两部分必须制作在同一个程序中(如下例子:
假设有两种孔径的盲孔):
程序头
M48
……
%
对位程序
T1(四个对位mark点)
X……Y……
X……Y……
X……Y……
X……Y……
钻孔程序
T2(钻孔-孔径1)
X……Y……
T3(钻孔-孔径2)
X……Y……
……
程序尾
T00
M30
b.激光钻孔指示上须注明不同刀具代表的是二阶还是一阶HDI孔,
b-1.一阶HDI孔注明为:
D12、D23分别表明只导通L1与L2层和导通L2与L3层;
b-2.二阶HDI孔注明为:
D123,表明同时导通L1、L2和L3层;
b-3.二阶HDI孔注明为:
D13,表明只导通L1和L3层。
…………依次类推。
(2)如果同一面上同时有一阶和二阶HDI孔,则分成不同的刀具号,做成同一钻带程序。
对于L123类HDI孔是采用D23和D123二次激光钻孔方式加工,D23和D123分别做在L2(n-1)和L1n激光钻带程序上。
(3)二阶HDI板中HDI孔激光孔确定原则
序号
激光孔类型
第一次激光钻孔的孔径
第二次激光钻孔的孔径
1
L123类阶梯式二阶HDI孔
4mil
8mil
2
L123类填孔式二阶HDI孔
4mil
4mil
(4)激光钻带制作注意事项
a.不同T对应不同的孔径,必须在生产指示中明确标注;
b.同一面上所有的刀具号必须做成同一个钻带程序;
c.激光钻带不允许进行Set平移。
d.对于激光孔,最外层的钻带不需要进行放缩,直接出1:
1钻带,而对于BU层钻带,需要根据相应的比例系数进行放缩,其对位标靶也需要同步放缩;
e.激光钻机机台标识:
最后一把刀末尾部分添加以下语句:
此坐标区域的CFM菲林需要开窗(设计为长条方式),内层对应地方需要设计为铜Pad.
............
M97,*
X……Y……
T00
M30
f.激光钻机钻字符需要的位置大小(字符将以7行4列的孔来表示出),假设镭射孔径为Dmm:
◆若D小于等于0.25mm时,字符高度为1.5+Dmm,宽度为0.75+D,字符间距约为:
0.5-D;
◆若D大于0.25mm时,字符高度为(1.2DX6+D)=8.2D,宽度为(1.2DX3+1)=4.6D,字符间距约为:
1.4D;
…………………………………………………………………………………………………………………………..
7.3.4机械钻孔工序
7.3.4.1二钻相关规定:
(1)若生产板有以下情况则需要二钻:
序号
情况描述
1
NPTH孔钻在铜面、焊盘上或离外层线路、焊盘太近(<5mil),无法移线/盘,干膜无法
封孔(允许露铜)或槽尺寸大于6x8mm超出干膜封孔能力;
2
板厚≥0.7mm,NPTH孔>6mm
3
板厚在0.5~0.7mm,NPTH孔>5.5mm
4
板厚≤0.5mm,NPTH孔>4.0mm
5
因客户有特殊要求,如有锥形孔;
(2)二钻流程一般放在锣板前;
(3)锣板定位孔在一钻程序中钻出;
(4)二钻方向:
应由材质均匀面钻向材质不均匀面,由铜面钻向基材面。
制作二钻程序时若两面均为铜面,则第二面此孔焊环必须保证6mil;若此板正反拼版且二钻处一面为铜一面为基材,则制作2个二钻程序及定位程序从铜面钻向非铜面;
7.3.4.2钻槽孔时的长度补偿:
(1)对于刀径<0.6mm的槽孔,在槽端孔的位置上加钻0.30mm的引导孔;
(2)当槽长<1.5倍槽宽,槽长补偿0.08mm;1.5倍槽宽≤槽长<1.8倍槽宽,槽长补偿0.05mm;当1.8倍槽宽≤槽长<2倍槽宽,槽长补偿0.03mm;当槽长≥2倍槽宽时,槽长无需补偿;
7.3.4.3当钻带中槽孔的槽长<2倍槽宽时,第二槽端孔坐标顺时针做旋转补偿,具体值见下表。
如右图,当程序需镜像时,即相应逆向补偿,槽孔程序采用G85指令,钻带输出时,以set为一个单位再配以循环指令加工;
槽孔宽度补偿
序号
槽宽
倍数(槽长/槽宽)
旋转补偿值
备注
1
>0.7mm
1.65<槽长/槽宽<2.0
0.02mm
●无需加预钻孔;
●槽长为补偿后值;
2
>0.7mm
≤1.65
0.040mm
3
≤0.7mm
1.65<槽长/槽宽<2.0
0.03mm
4
≤0.7mm
≤1.65
0.055mm
7.3.4.4连孔制作
(1)符合连孔制作的条件:
孔数两个,孔径ФD≥1.0mm,ФD与两孔中心距比值≤7/5;
(2)连孔制作要求:
连孔中心连线的中点加钻一个孔Фd,Фd大于公共弦长度约0.25mm至0.50mm,钻孔顺序为:
钻连孔→钻Фd→重钻连孔。
(3)钻孔孔壁到孔壁间距要求≥8mil。
(4)若孔径0.5≤ФD<1.0mm,且钻孔孔壁间距<8mil,应ICS询问客户接受改为槽孔制作。
7.3.4.5相交孔制作
对于两孔相交,又不符合连孔条件时,钻孔顺序为:
先钻小孔(孔1),再钻大孔(孔2),再用比孔1小2mil的直径重钻孔1,最后用比孔2小2mil的直径重钻孔2;
7.3.4.6邮票孔钻孔:
孔与孔之间距离最小要求12mil,每排孔留筋厚度总和要求≥板厚。
若单元内的只有靠邮票孔相连,则须有2排孔以上;若只有一排孔,总的筋厚要求>3mm。
7.3.4.7钻咀直径在钻孔表及钻带中表示时,统一标识到小数点后三位,其中整数位及小数点后前第1、2位表示直径,小数点后第3位表示为标识位,含义如下:
(1)尾数0:
普通圆孔钻咀;例如:
1.150表示直径1.15mm的普通孔钻咀;
(2)尾数1:
钻BGA区的钻咀;例如:
1.151表示直径1.15mm钻BGA的钻咀;对于生产板中含有BGA区域时,BGA处的孔需单独提出采用独立刀进行钻孔;
(3)尾数2:
坑槽(Slot)钻咀;例如:
1.152表示直径1.15mm的槽孔钻咀;
(4)尾数3:
钻邮票孔或槽引导孔钻咀;例如:
1.153表示直径1.15mm钻邮票孔或槽引导孔的钻咀;当板中有邮票孔或槽引导孔时,需要分刀钻出;
(5)尾数4:
T孔(特殊孔),制板层数大于等于10层且叠好钻孔加工时贯穿铜层总厚度超过16OZ的直径小于等于0.3mm的孔,例如:
0.254表示直径0.25mm的特殊孔;(若仅仅板边钻房测试孔符合此条件而单元内无孔符合时,则不需要单独提出此部分孔)
(6)¢0.505:
固定表示为钻钻机代码、操作员工代码、制板编号的0.5mm直径的钻咀;
(7)¢2.055:
固定用来在板边钻一个孔,用来判断区分底板,Z值设计为1.0mm;
7.3.4.8钻带制作时,每个板必须包含两个基本点钻带,一个为钻定位孔的程序,另一个为钻生产板的程序;钻带内钻咀排列时,第一把刀固定设计为钻板边工具孔的钻咀(3.175mm);从第二把刀开始由小到大排列钻其它孔;钻字唛设计在最后;
7.3.4.9钻嘴直径选择规则:
孔的类型
生产流程
钻孔刀径(D)与成品孔径中值(d)的关系(单位:
mm)
孔壁铜厚
常规能力刀径选择
特殊能力刀径选择(按中值选)
金属化孔
表面处理非喷锡
客户要求铜厚(min)
d+0.04+2.2×铜厚≤D≤d+0.09+2.2×铜厚
d+0.01+2.2×铜厚≤D≤d+0.06+2.2×铜厚(如两种孔径之间差0.2mm,需考虑电镀的Throwingpower,具体见制作规程电镀部分
非金属化孔
采取干膜盖孔或二钻工艺
对于圆孔,钻嘴直径应取中值偏上限;对于槽孔,钻嘴直径D≥d。
7.3.4.10钻机机台标识:
钻带中需要添加以下语句以加钻机器编号、操作员工代码、制板编号:
M97,*
X123456Y123456(123456字样为设计的钻字唛的坐标,设计在右下板边,固定采用0.5mm的钻咀)
设计时预留的10个字符的位置,字符所占位置如下(其中D为所使用的钻咀直径:
)
单个字符宽度=4.6D
字符间的间距=1.4D
单个字符高度=8.2D
.
7.3.4.11钻带输出时,采用公制3.3格式,输出零点采用定位ID孔中的下定位孔;若板需要进行放缩时,放缩中心点为板的正中心点;
7.3.4.12钻带中固定增加一把2.055mm的刀,其Z值设定为1mm,用于区分钻孔时的底板;
7.3.4.13钻带制作完成后,必须在板边加钻其比例系数,格式为L0.000000W0.000000;
7.3.4.14钻嘴使用以公制刀为主(直径0.2~6.35mm为正常钻嘴,直径6.4~6.95mm时需手动上钻嘴,直径4.05~6.95mm时需进行预钻孔,直径≥7mm时采用扩孔方式);特殊用刀(英制钻嘴、锥形钻嘴)时需提前通知相关部门备料和核算成本。
孔径范围
具体方法
预钻孔
¢4.05mm--6.95mm
1)预先使用规定尺寸的钻嘴进行钻孔;
2)再用与孔径相同尺寸的钻嘴钻孔。
见下表、下图:
D=钻嘴直径;预钻嘴径A=D/3;
扩孔
¢7.00mm--9.50mm
1)孔的中心先钻一个Ф3.175mm孔;
2)使用Ф3.175mm钻咀,编程采用G84钻孔;
¢9.55mm--12.80mm
1)孔的中心先钻一个Ф(D-6.35)mm孔(有预钻);
2)使用Ф3.175mm钻咀,编程采用G84钻孔;
¢12.85mm--14.05mm
1)孔的中心先钻一个Ф(D-7.60)mm孔(有预钻);
2)使用Ф3.85mm钻咀,编程采用G84钻孔;
¢14.10mm以上
1)孔的中心先钻一个Ф9mm孔(扩孔方式);
2)使用(D-9)/2mm钻咀,编程采用G84钻孔;
不同尺寸的大孔(直径为4.05-6.95mm)所对应的预钻孔的钻嘴直径及位置如下,如钻孔程序内无相应钻刀,则可适当改变钻刀直径Фd,保证4个Фd圈不相切,同时与大圈距离为0.2mm:
D(mm)
A(mm)
D(mm)
A(mm)
D(mm)
A(mm)
D(mm)
A(mm)
4.05
1.35
4.8
1.60
5.55
1.85
6.3
2.10
4.1
1.35
4.85
1.6