金属加与材料特性.docx
《金属加与材料特性.docx》由会员分享,可在线阅读,更多相关《金属加与材料特性.docx(17页珍藏版)》请在冰豆网上搜索。
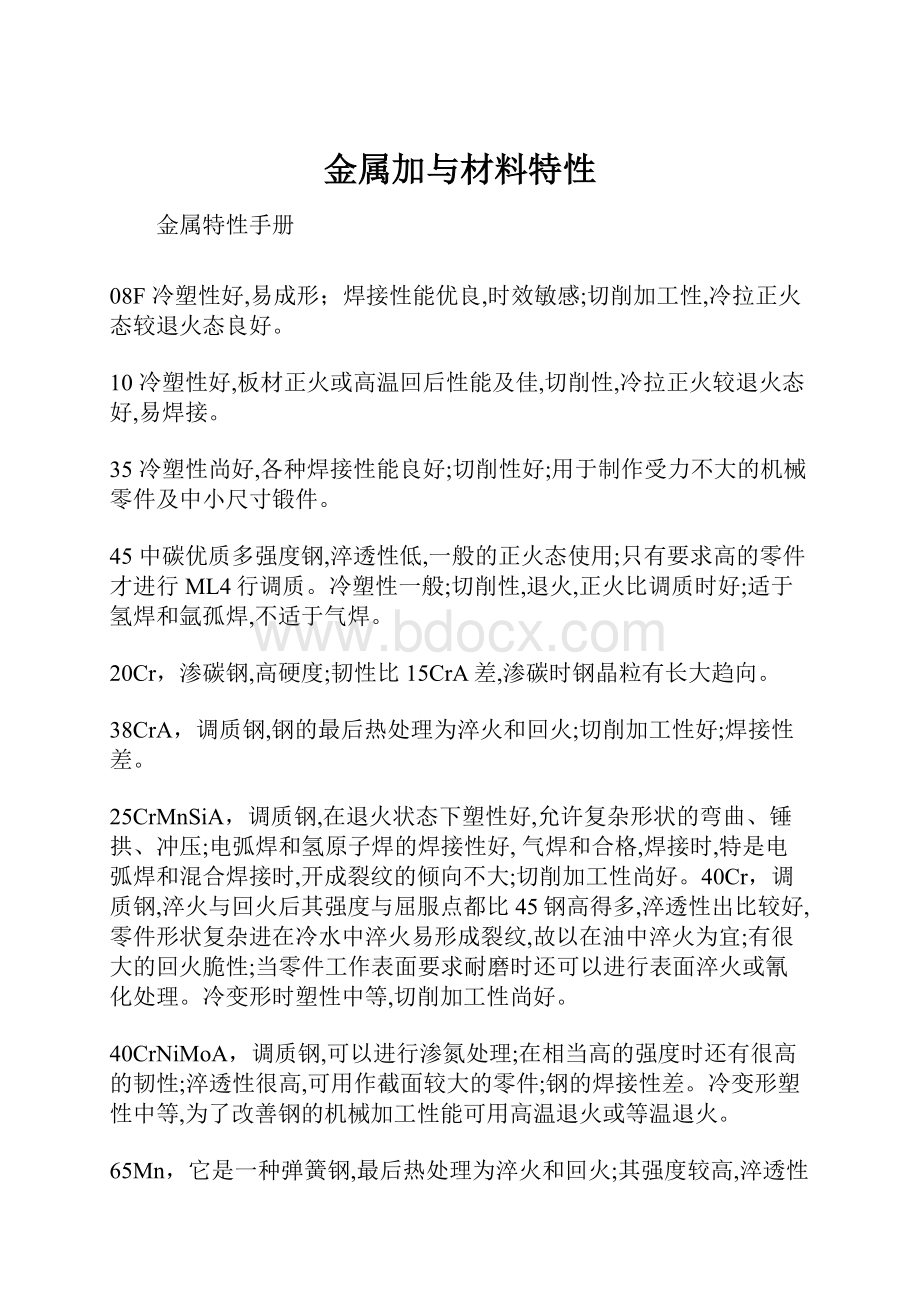
金属加与材料特性
金属特性手册
08F冷塑性好,易成形;焊接性能优良,时效敏感;切削加工性,冷拉正火态较退火态良好。
10冷塑性好,板材正火或高温回后性能及佳,切削性,冷拉正火较退火态好,易焊接。
35冷塑性尚好,各种焊接性能良好;切削性好;用于制作受力不大的机械零件及中小尺寸锻件。
45中碳优质多强度钢,淬透性低,一般的正火态使用;只有要求高的零件才进行ML4行调质。
冷塑性一般;切削性,退火,正火比调质时好;适于氢焊和氩孤焊,不适于气焊。
20Cr,渗碳钢,高硬度;韧性比15CrA差,渗碳时钢晶粒有长大趋向。
38CrA,调质钢,钢的最后热处理为淬火和回火;切削加工性好;焊接性差。
25CrMnSiA,调质钢,在退火状态下塑性好,允许复杂形状的弯曲、锤拱、冲压;电弧焊和氢原子焊的焊接性好,气焊和合格,焊接时,特是电弧焊和混合焊接时,开成裂纹的倾向不大;切削加工性尚好。
40Cr,调质钢,淬火与回火后其强度与屈服点都比45钢高得多,淬透性出比较好,零件形状复杂进在冷水中淬火易形成裂纹,故以在油中淬火为宜;有很大的回火脆性;当零件工作表面要求耐磨时还可以进行表面淬火或氰化处理。
冷变形时塑性中等,切削加工性尚好。
40CrNiMoA,调质钢,可以进行渗氮处理;在相当高的强度时还有很高的韧性;淬透性很高,可用作截面较大的零件;钢的焊接性差。
冷变形塑性中等,为了改善钢的机械加工性能可用高温退火或等温退火。
65Mn,它是一种弹簧钢,最后热处理为淬火和回火;其强度较高,淬透性较大,脱碳倾向小,但有过热敏感性,易出现淬火裂纹,并有回火脆性。
在退火状态下切削加工性尚好;焊接性好,冷变形塑性低,带材可供一般弯曲。
50CrVA,合金弹簧钢,钢的最后热处理为淬火和回火;热处理后具有较好的韧性,高的比例极限和强度极限,具有高的疲劳强度,的比值也较高,并有高的淬透性(与65Si2MnWA的淬透性相类似)与较低的过热敏感性;零件使用温度程300℃时,其弹性仍可保持。
钢的切削加工尚好,冷变形时塑性低,焊接性差。
2.棒材机械性能:
(抗拉强度)
状态抗拉强度硬度(HB)
08F热轧≤131
08F经热处理30183560——
10热轧————≤137
经热处理34213155——
热轧、锻制32183055——
冷拉45—850—≤187
冷拉钢退火30—2655—≤143
热轧————≤143
经热处理38232755——
热处理状态——————
20热轧————≤156
经热处理42252555——
供应状态39222250——
热处理状态——————
冷拉52—7.540—≤207
冷拉钢退火40—2150—≤163
25热轧—————≤170
经热处理462823509—
供应状态43241850——
热处理状态——————
冷拉55—740—≤217
冷拉钢退火42—1950—≤170
35热轧————≤187
经热处理543220457—
冷拉60—6.535—≤229
冷拉钢退火48—1545—≤187
3.板材机械性能:
牌号状态厚度抗拉强度
08FZ0.2~0.428~37
08FSP0.2~0.428~39
08FZSP4~60≥30
10Z0.2~0.430~42
10SP0.2~0.430~44
10ZSP0.2~0.4≥34
15Z0.2~4.034~46
15SP0.2~4.034~48
20Z0.2~4.036~50
20SP0.2~4.036~51
20ZSP4~60≥42
二、不锈钢材料特性:
1、铁素体型不锈钢:
其含Cr量高,具有良好而性及高温抗氧化性能。
2、奥氏体不锈钢:
典型牌号如/Cr18Ni9,/Cr18Ni9T1无磁性,耐蚀性能良好,
温强度及高温抗氧化性能好,塑性好,冲击韧性好,且无缺口效应,焊接性
优良,因而广泛使用。
这种钢一般强度不高,屈服强度低,且不能通过热
处理强化,但冷压,加工后,可使抗拉强度高,且改善其弹性,但其在高温下
冷拉获得的强度易化。
不宜用于承受高载荷。
3、马氏全不锈钢:
典型如2Cr13,GX-8,具磁性,消震性优良,导热性好,具高强度和屈服
极限,热处理强化后具良好综合机械性能。
加含碳量多,焊后需回为处理
以消除应力、高温冷却易形成8氏体,因此锻后要缓冷,并应立即进行回
火。
主要用于承载部件。
例:
10Cr18Ni9它是一种奥氏体不钢,淬火不能强化,只能消除冷作硬化和获
得良好的抗蚀,淬火冷却必须在水是进行,以保证得到最好的抗蚀性;在
900℃以下有稳定的抗氧化性。
适于各种方法焊接;有晶间腐蚀倾向,零
件长期在腐蚀介质、水中及蒸汽介质中工作时可能遭受晶界腐蚀破坏;
钢淬火后冷变形塑性高,延伸性能良好,但切削加工性较差。
1Cr18Ni9它是标准的18-8型奥氏体不锈钢,淬火炒能强化,但此时具有良
好的耐蚀性和冷塑性变形性能;钢因塑性和韧性很高,切削性较差;适
于各种方法焊接;由于含碳量较0Cr18ni9钢高,对晶界腐蚀敏感性较
焊接后需热处理,一般不宜作耐腐蚀的焊接件;在850℃以下空气介质
、以及750℃以下航空燃料燃烧产物的气氛中肯有较稳定的抗氧化性。
Cr13Ni4Mn9它属奥氏体不锈耐热钢,淬火不能强化,钢在淬火状态下塑性
很高,可时行深压延及其它类型的冷冲压;钢的切削加工性较差;用点焊
和滚焊焊接的效果良好,经过焊接后必须进行热处理;在大气中具有高
耐蚀性;易产晶界腐蚀,故在超过450的腐蚀介质是为宜采用;在750
~800℃以下的热空气中具有稳定的抗氧化性。
1Cr13它属于铁素体-马氏体型为锈钢,在淬火回火后使用;为提高零件的
耐磨性,疲劳性能及抗腐蚀性可渗氮、氰化;淬火及抛光后在湿性大气、
蒸汽、淡水、海水、和自来水中具有足够的抗腐蚀性,在室温下的硝酸
中有较好的安定性;在750℃温度以下具有稳定的抗氧化性。
退火状态
下的钢的塑性较高,可进行深压延钢、冲压、弯曲、卷边等冷加工;气焊
和电弧焊结果还满意;切削加工性好,抛光性能优良;钢锻造后冷并应立
即进行回火处理。
2Cr13它属于马氏体型不锈钢,在淬火回火后使用;为提高零件的耐
磨性耐腐蚀性、疲劳性能及抗蚀性可渗氮、氰化;淬火回火后钢的强度
、硬度均较
1Cr13钢高,抗腐蚀性与耐热性稍低;在700℃温度以下的空气介质中仍有稳
定的抗氧化性。
钢的焊接性和退火状态下塑性虽比不上1Cr13,但仍满
意;切削加工性好;抛光性能优良;钢在锻造后应缓冷,并立即进行回火
处理。
3Cr13它属于马氏体型不锈钢,在淬火回火后使用,耐腐蚀性和在700℃
以下的热稳定性均比1Cr13,2Cr13低,但强度、硬度,淬透性和热强性
都较高。
冷加工性和焊接性不良,焊后应立即热处理;在退火后有较好
的切削性;在锻造后应缓冷,并应立即进行回火处理。
9Cr18它属于高碳含铬马氏体不锈钢,淬火后具有高的硬度和耐磨性;对
海水,盐水等介质尚能抗腐蚀;钢经退火后有很好的切削性;由于会发生
硬化和应力裂纹,不适于焊接;为了避免锻后产生裂纹,必须缓慢冷却
(最好在炉中冷却),在热态下,将零件转放入700~725℃的炉中进行
回火处理。
三、铝合金:
强度/质量大,工艺性好,或用于压力制造及铸造,焊接,目前广泛用
于飞机、发动机各种结构上。
1、变形铝合金:
1.1防锈铝:
A1-Mn及A1-Mg系合金(LF21、LF2、LF3、LF6、LF10)
属于防锈铝,其特点是不能热处理强化,只能用冷作硬化强化,强度低、
塑性高、压力加工性良好,有良下的抗蚀性及焊接性。
特别适用于制
造受轻负荷的深压延零件,焊接零件和在腐蚀介质中工作的零件。
1.2硬铝:
LY系列合金元素要含量小的塑性好,强度低;如LY1,LY10,含金
元素及Mg,Cn适中者,强度、塑性中高;如LY11;金中Cn,Mg含量高
则强度高,可用于作承动构件;如LY12,LY2,LY4;
LC系列这超硬铝,强度高,但静疲劳性能差
LY11,LY17为耐热铝,高温强度不太多,但高温时蠕度强度高。
1.3锻铝:
LD2具有高塑性及腐蚀稳定性,易锻造,但强度较低;LD5,
LD6,LD10强度好,易于作高负载锻件及模锻件;LD7;LD8有较高
耐热性,用于高温零件,具有高的机械性能和冲压工艺性。
2、铸造铝合金:
1).低强度合金:
ZL-102;ZL-303
2).中强度合金:
ZL-101;ZL-103;ZL-203;ZL-302
3).中强度耐热合金:
ZL-401
4).高强度合金:
ZL-104;ZL-105
5).高强度耐热合金:
ZL-201;ZL-202
6).高强度耐蚀合金:
ZL301
模具制造的25个问题
1)选择模具钢时什么是最重要的和最具有决定性意义的因素?
成形方法-可从两种基本材料类型中选择。
A)热加工工具钢,它能承受模铸、锻造和挤压时的相对高的温度。
B)冷加工工具钢,它用于下料和剪切、冷成形、冷挤压、冷锻和粉末加压成形。
塑料-一些塑料会产生腐蚀性副产品,例如PVC塑料。
长时间的停工引起的冷凝、腐蚀性气体、酸、冷却/加热、水或储存条件等因素也会产生腐蚀。
在这些情况下,推荐使用不锈钢材料的模具钢。
模具尺寸-大尺寸模具常常使用预硬钢。
整体淬硬钢常常用于小尺寸模具。
模具使用次数-长期使用(>1000000次)的模具应使用高硬度钢,其硬度为48-65HRC。
中等长时间使用(100000到1000000次)的模具应使用预硬钢,其硬度为30-45HRC。
短时间使用(<100000次)的模具应使用软钢,其硬度为160-250HB。
表面粗糙度-许多塑料模具制造商对好的表面粗糙度感兴趣。
当添加硫改善金属切削性能时,表面质量会因此下降。
硫含量高的钢也变得更脆。
2)影响材料可切削性的首要因素是什么?
钢的化学成分很重要。
钢的合金成分越高,就越难加工。
当碳含量增加时,金属切削性能就下降。
钢的结构对金属切削性能也非常重要。
不同的结构包括:
锻造的、铸造的、挤压的、轧制的和已切削加工过的。
锻件和铸件有非常难于加工的表面。
硬度是影响金属切削性能的一个重要因素。
一般规律是钢越硬,就越难加工。
高速钢(HSS)可用于加工硬度最高为330-400HB的材料;高速钢+钛化氮(TiN)涂层,可加工硬度最高为45HRC的材料;而对于硬度为65-70HRC的材料,则必须使用硬质合金、陶瓷、金属陶瓷和立方氮化硼(CBN)。
非金属参杂一般对刀具寿命有不良影响。
例如Al2O3(氧化铝),它是纯陶瓷,有很强的磨蚀性。
最后一个是残余应力,它能引起金属切削性能问题。
常常推荐在粗加工后进行应力释放工序。
3)模具制造的生产成本由哪些部分组成?
粗略地说,成本的分布情况如下:
切削65%
工件材料20%
热处理5%
装配/调整10%
这也非常清楚地表明了良好的金属切削性能和优良的总体切削解决方案对模具的经济生产的重要性。
4)铸铁的切削特性是什么?
一般来说,它是:
铸铁的硬度和强度越高,金属切削性能越低,从刀片和刀具可预期的寿命越低。
用于金属切削生产的铸铁其大部分类型的金属切削性能一般都很好。
金属切削性能与结构有关,较硬的珠光体铸铁其加工难度也较大。
片状石墨铸铁和可锻铸铁有优良的切削属性,而球墨铸铁相当不好。
加工铸铁时遇到的主要磨损类型为:
磨蚀、粘结和扩散磨损。
磨蚀主要由碳化物、沙粒参杂物和硬的铸造表皮产生。
有积屑瘤的粘结磨损在低的切削温度和切削速度条件下发生。
铸铁的铁素体部分最容易焊接到刀片上,但这可用提高切削速度和温度来克服。
在另一方面,扩散磨损与温度有关,在高切削速度时产生,特别是使用高强度铸铁牌号时。
这些牌号有很高的抗变型能力,导致了高温。
这种磨损与铸铁和刀具之间的作用有关,这就使得一些铸铁需用陶瓷或立方氮化硼(CBN)刀具在高速下加工,以获得良好的刀具寿命和表面质量。
一般对加工铸铁所要求的典型刀具属性为:
高热硬度和化学稳定性,但也与工序、工件和切削条件有关;要求切削刃有韧性、耐热疲劳磨损和刃口强度。
切削铸铁的满意程度取决于切削刃的磨损如何发展:
快速变钝意味着产生热裂纹和缺口而使切削刃过早断裂、工件破损、表面质量差、过大的波纹度等。
正常的后刀面磨损、保持平衡和锋利的切削刃正是一般需要努力做到的。
5)什么是模具制造中主要的、共同的加工工序?
切削过程至少应分为3个工序类型:
粗加工、半精加工和精加工,有时甚至还有超精加工(大部分是高速切削应用)。
残余量铣削当然是在半精加工工序后为精加工而准备的。
在每一个工序中都应努力做到为下一个工序留下均匀分布的余量,这一点非常重要。
如果刀具路径的方向和工作负载很少有快速的变化,刀具的寿命就可能延长,并更加可预测。
如果可能,就应在专用机床上进行精加工工序。
这会在更短的调试和装配时间内提高模具的几何精度和质量。
6)在这些不同的工序中应主要使用何种刀具?
粗加工工序:
圆刀片铣刀、球头立铣刀及大刀尖圆弧半径的立铣刀。
半精加工工序:
圆刀片铣刀(直径范围为10-25mm的圆刀片铣刀),球头立铣刀。
精加工工序:
圆刀片铣刀、球头立铣刀。
残余量铣削工序:
圆刀片铣刀、球头立铣刀、直立铣刀。
通过选择专门的刀具尺寸、槽形和牌号组合,以及切削参数和合适的铣削策略,来优化切削工艺,这非常重要。
关于可使用的高生产率刀具,见模具制造用样本C-1102:
1
7)在切削工艺中有没有一个最重要的因素?
切削过程中一个最重要的目标是在每一个工序中为每一种刀具创建均匀分布的加工余量。
这就是说,必须使用不同直径的刀具(从大到小),特别是在粗加工和半精加工工序中。
任何时候主要的标准应是在每个工序中与模具的最终形状尽可能地相近。
为每一种刀具提供均匀分布的加工余量保证了恒定而高的生产率和安全的切削过程。
当ap/ae(轴向切削深度/径向切削深度)不变时,切削速度和进给率也可恒定地保持在较高水平上。
这样,切削刃上的机械作用和工作负载变化就小,因此产生的热量和疲劳也少,从而提高了刀具寿命。
如果后面的工序是一些半精加工工序,特别是所有精加工工序,就可进行无人加工或部分无人加工。
恒定的材料加工余量也是高速切削应用的基本标准。
恒定的加工余量的另一个有利的效应是对机床——导轨、球丝杠和主轴轴承的不利影响小。
8)为什么最经常将圆刀片铣刀作为模具粗加工刀具的首选?
如果使用方肩铣刀进行型腔的粗铣削,在半精加工中就要去除大量的台阶状切削余量。
这将使切削力发生变化,使刀具弯曲。
其结果是给精加工留下不均匀的加工余量,从而影响模具的几何精度。
如果使用刀尖强度较弱的方肩铣刀(带三角形刀片),就会产生不可预测的切削效应。
三角形或菱形刀片还会产生更大的径向切削力,并且由于刀片切削刃的数量较少,所以他们是经济性较差的粗加工刀具。
另一方面,圆刀片可在各种材料中和各个方向上进行铣削,如果使用它,在相邻刀路之间过渡较平滑,也可以为半精加工留下较小的和较均匀的加工余量。
圆刀片的特性之一是他们产生的切屑厚度是可变的。
这就使它们可使用比大多数其它刀片更高的进给率。
圆刀片的主偏角从几乎为零(非常浅的切削)改变到90度,切削作用非常平稳。
在切削的最大深度处,主偏角为45度,当沿带外圆的直壁仿形切削时,主偏角为90度。
这也说明了为什么圆刀片刀具的强度大——切削负载是逐渐增大的。
粗加工和半粗加工应该总将圆刀片铣刀,如CoroMill200(见模具制造样本C-1102:
1)作为首选。
在5轴切削中,圆刀片非常适合,特别是它没有任何限制。
通过使用良好的编程,圆刀片铣刀在很大程度上可代替球头立铣刀。
跳动量小的圆刀片与精磨的的、正前角和轻切削槽形相结合,也可以用于半精加工和一些精加工工序。
9)什么是有效切削速度(ve)和为什么它对高生产率非常重要?
切削中,实际或有效直径上的有效切削速度的基本计算总是非常重要。
由于台面进给量取决于一定切削速度下的转速,如果未计算有效速度,台面进给量就会计算错误。
如果在计算切削速度时使用刀具的名义直径值(Dc),当切削深度浅时,有效或实际切削速度要比计算速度低得多。
如圆刀片CoroMill200刀具(特别是在小直径范围)、球头立铣刀、大刀尖圆弧半径立铣刀和CoroMill390立铣刀之类的刀具(这些刀具请参见山特维克可乐满的模具制造样本C-1102:
1)。
由此,计算得到的进给率也低得多,这严重降低了生产率。
更重要的是,刀具的切削条件低于它的能力和推荐应用范围。
当进行3D切削时,切削时的直径在变化,它与模具的几何形状有关。
此问题的一个解决方案是定义模具的陡壁区域和几何形状浅的零件区域。
如果对每个区域编制专门的CAM程序和切削参数,就可以达到良好的折中和结果。
10)对于成功的淬硬模具钢铣削来说,重要的应用参数有哪些?
使用高速铣对淬硬模具钢进行精加工时,一个需遵守的主要因素是采用浅切削。
切削深度应不超过0.2/0.2mm(ap/ae:
轴向切削深度/径向切削深度)。
这是为了避免刀柄/切削刀具的过大弯曲和保持所加工模具拥有小的公差和高精度。
选择刚性很好的夹紧系统和刀具也非常重要。
当使用整体硬质合金刀具时,采用有最大核心直径(最大抗弯刚性)的刀具非常重要。
一条经验法则是,如果将刀具的直径提高20%,例如从10mm提高到12mm,刀具的弯曲将减小50%。
也可以说,如果将刀具悬伸/伸出部分缩短20%,刀具的弯曲将减小50%。
大直径和锥度的刀柄进一步提高了刚度。
当使用可转位刀片的球头立铣刀(见模具制造样本C-1102:
1)时,如果刀柄用整体硬质合金制造,抗弯刚性可以提高3-4倍。
当用高速铣对淬硬模具钢进行精加工时,选择专用槽形和牌号也非常重要。
选择像TiAlN这样有高热硬度的涂层也非常重要。
11)什么时候应采用顺铣,什么时候应采用逆铣?
主要建议是:
尽可能多使用顺铣。
当切削刃刚进行切削时,在顺铣中,切屑厚度可达到其最大值。
而在逆铣中,为最小值。
一般来说,在逆铣中刀具寿命比在顺铣中短,这是因为在逆铣中产生的热量比在顺铣中明显地高。
在逆铣中当切屑厚度从零增加到最大时,由于切削刃受到的摩擦比在顺铣中强,因此会产生更多的热量。
逆铣中径向力也明显高,这对主轴轴承有不利影响。
在顺铣中,切削刃主要受到的是压缩应力,这与逆铣中产生的拉力相比,对硬质合金刀片或整体硬质合金刀具的影响有利得多。
当然也有例外。
当使用整体硬质合金立铣刀(见模具样本C-1102:
1中的刀具)进行侧铣(精加工)时,特别是在淬硬材料中,逆铣是首选。
这更容易获得更小公差的壁直线度和更好的90度角。
不同轴向走刀之间如果有不重合的话,接刀痕也非常小。
这主要是因为切削力的方向。
如果在切削中使用非常锋利的切削刃,切削力便趋向将刀“拉”向材料。
可以使用逆铣的另一个例子是,使用老式手动铣床进行铣削,老式铣床的丝杠有较大的间隙。
逆铣产生消除间隙的切削力,使铣削动作更平稳。
12)仿形铣削还是等高线切削?
在型腔铣削中,保证顺铣刀具路径成功的最好方法是采用等高线铣削路径。
铣刀(例如球头立铣刀,见模具制造样本C-1102:
1)外圆沿等高线铣削常常得到高生产率,这是因为在较大的刀具直径上,有更多的齿在切削。
如果机床主轴的转速受到限制,等高线铣削将帮助保持切削速度和进给率。
采用这种刀具路径,工作负载和方向的变化也小。
在高速铣应用和淬硬材料加工中,这特别重要。
这是因为如果切削速度和进给量高的话,切削刃和切削过程便更容易受到工作负载和方向改变的不利影响,工作负载和方向的变化会引起切削力和刀具弯曲的变化。
应尽可能避免沿陡壁的仿形铣削。
下仿形铣削时,低切削速度下的切屑厚度大。
在球头刀中央,还有刃口崩碎的危险。
如果控制差,或机床无预读功能,就不能足够快地减速,最容易在中央发生刃口崩碎的危险。
沿陡壁的上仿形铣削对切削过程较好一些,这是因为在有利的切屑速度下,切屑厚度为其最大值。
为了得到最长的刀具寿命,在铣削过程中应使切削刃尽可能长时间地保持连续切削。
如果刀具进入和退出太频繁,刀具寿命会明显缩短。
这会使切削刃上的热应力和热疲劳加剧。
在切削区域有均匀和高的温度比有大的波动对现代硬质合金刀具更有利。
仿形铣削路径常常是逆铣和顺铣的混合(之字形),这意味切削中会频繁地吃刀和退刀。
这种刀具路径对模具质量也有不好的影响。
每次吃刀意味刀具弯曲,在表面上便有抬起的标记。
当刀具退出时,切削力和刀具的弯曲减小,在退出部分会有轻微的材料“过切削”。
13)为什么有的铣刀上必须有不同的齿距?
铣刀是多切削刃刀具,齿数(z)是可改变的,有一些因素可以帮助确定用于不同加工类型的齿距或齿数。
材料、工件尺寸、总体稳定性、悬伸尺寸、表面质量要求和可用功率就是与加工有关的因素。
与刀具有关的因素包括足够的每齿进给量、至少同时有两个齿在切削以及刀具的切屑容量,这些仅是其中的一小部分。
铣刀的齿距(u)是刀片切削刃上的点到下一个切削刃上同一个点的距离。
铣刀分为疏、密和超密齿距铣刀,大部分可乐满铣刀都有这3个选项,见模具制造样本C-1102:
1。
密齿距是指有较多的齿和适当的容屑空间,可以以高金属去除率切削。
一般用于铸铁和钢的中等负载铣削。
密齿距是通用铣刀的首选,推荐用于混合生产。
疏齿距是指在铣刀圆周上有较少的齿和有大的容屑空间。
疏齿距常常用于钢的粗加工到精加工,在钢加工中振动对加工结果影响很大。
疏齿距是真正有效的问题解决方案,它是长悬伸铣削、低功率机床或其它必须减小切削力应用的首选。
超密齿距刀具的容屑空间非常小,可以使用较高的工作台进给。
这些刀具适合于间断的铸铁表面的切削、铸铁粗加工和钢的小余量切削,例如侧铣。
它们也适合于必须保持低切削速度的应用。
铣刀还可以有均匀的或不等的齿距。
后者是指刀具上齿的间隔不相等,这也是解决振动问题的有效方法。
当存在振动问题时,推荐尽可能采用疏齿不等齿距铣刀。
由于刀片少,振动加剧的可能性就小。
小的刀具直径也可改善这种情况。
应使用能很好适应的槽形和牌号的组合——锋利的切削刃和韧性好的牌号组合。
14)为了获得最佳性能,铣刀应怎样定位?
切削长度会受到铣刀位置的影响。
刀具寿命常常与切削刃必须承担的切削长度有关。
定位于工件中央的铣刀其切削长度短,如果使铣刀在任一方向偏离中心线,切削的弧就长。
要记住,切削力是如何作用的,必须达到一个折中。
在刀具定位于工件的中央的情况下,当刀片切削刃进入或退出切削时,径向切削力的方向就随之改变。
机床主轴的间隙也使振动加剧,导致刀片振动。
通过使刀具偏离中央,就会得到恒定的和有利的切削力方向。
悬伸越长,克服所有可能的振动也就越重要。
1